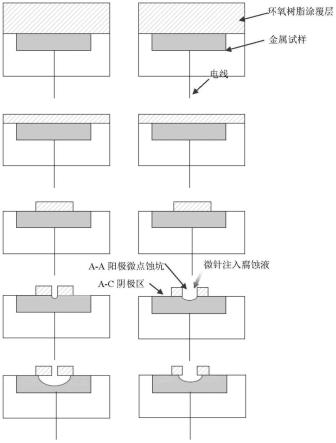
1.本发明涉及一种研究不锈钢材料耐点蚀性能的方法,具体涉及一种模拟单一点蚀坑发展研究不锈钢材料耐点蚀性能的方法,属于金属腐蚀领域。
背景技术:2.点蚀是在不锈钢表面局部形成一定的小孔或锈斑的一种腐蚀形式,其在侵蚀性环境中很容易发生,并会经过不断发展引起危害性极大的事故,对国民经济造成损失。点腐蚀的特点在于不锈钢外表面生成点蚀坑的随机性,具体表现为:发生点蚀时间的随机性,发生点蚀部位的随机性,发生点蚀数量的随机性,亚稳态点蚀稳态转变的随机性。因此点蚀的研究始终是材料腐蚀领域的一个难点,当前迫切需要一种研究点蚀行为的新方法,以有效研究点腐蚀的发展规律,这对预防点腐蚀的发生,减小点腐蚀对金属设备运行安全性影响具有重要意义。
3.常见的点蚀研究方法主要分为两大类,第一类为针对点蚀敏感性及影响点蚀因素的研究,主要有化学浸泡法、极化曲线测量法、电化学噪声法等。该类方法材料表面生成点蚀坑数量庞大,没有特定点蚀研究对象。第二类为对点蚀发展机理的研究,一般为对单一点蚀坑发展的研究,该类方法所产生的点蚀脱离实际环境,与真实点蚀坑的发展过程有较大差异。当前缺乏一种与真实点蚀坑发展过程相近的,具有特定点蚀研究对象的单一点蚀坑研究方法。且针对2cr13马氏体不锈钢这种材料的耐点蚀性能分析方法(利用单一点蚀坑的耐点蚀性能分析方法来研究该材料发展机理)也未见报道。
技术实现要素:4.针对现有技术的不足,本发明的目的是提供一种研究不锈钢材料耐点蚀性能的方法,该方法是具有特定点蚀研究对象的单一点蚀坑研究方法,与真实点蚀坑发展过程相近。
5.为了实现上述目的,本发明的技术方案是:
6.一种研究不锈钢材料耐点蚀性能的方法,即制备同时具有活化态阳极和两侧钝化态阴极的工作电极,构建可自催化发展的闭塞点蚀坑体系,然后将工作电极浸泡在nacl溶液中,根据浸泡时间的不同,研究不锈钢点蚀坑的发展规律。具体方法为:
7.(1)先制备不锈钢电化学试样,在电化学试样的工作面上涂覆液态环氧树脂,凝固后打磨,然后在试样表面钻孔至试样工作面表面金属层,制得工作电极a;
8.(2)对工作电极a,以长边为基准,以钻孔部位为中心,两侧各去除部分涂覆层,暴露出部分钝化态金属,将暴露出的钝化态金属部位标记为a-c,即阴极;然后将工作电极a放入3.5%nacl溶液中,恒电位极化,使a-c部位得到稳定钝化层;
9.(3)采用硫化胶涂覆a-c部位,然后将工作电极a放入3.5%nacl溶液中,恒电位极化,使工作电极a钻孔部位的钝化膜破裂,裸露出活化态金属,形成微点蚀坑,此部位标记为a-a,即阳极;
10.(4)将a-c部位硫化胶去除干净,然后将工作电极a再次放入3.5%nacl溶液中浸
泡,并将腐蚀液注射入a-a阳极点蚀坑凹槽;
11.(5)根据浸泡时间的不同,研究不锈钢点蚀坑的发展规律。
12.进一步,步骤(1)中液态环氧树脂包括质量比为100:7:10的环氧树脂、邻苯二甲酸二乙酯、乙二胺。
13.进一步,步骤(1)中打磨环氧树脂厚度至400-600μm;钻孔直径为200-1200μm,优选为500-1000μm。
14.进一步,步骤(2)中恒电位极化的电位确定方法为先制备不锈钢丝状电极并进行动电位极化,获得极化曲线,然后根据极化曲线确定自腐蚀电位ecorr和点蚀电位eb,最后根据公式计算得到恒电位极化的电位ec,公式为:ec=ecorr+(0.6
±
0.2)
×
(eb-ecorr)v,极化时间为5min。
15.进一步,步骤(3)中恒电位极化的电位确定方法为先制备不锈钢丝状电极并进行动电位极化,获得极化曲线,然后根据极化曲线确定点蚀电位eb,最后根据公式计算得到恒电位极化的电位ea,公式为:ea=eb+(1
±
0.2)v,极化时间为5s。
16.进一步,步骤(4)中腐蚀液的制备方法为:先制备不锈钢丝状电极,然后对丝状电极进行动电位极化,获得极化曲线,确定丝状电极在该环境下的点蚀电位eb,再根据点蚀电位确定恒电位极化的电位下限,最后利用恒电位极化制备一维点蚀坑并得到酸性腐蚀液。具体方法为:
17.(1)取丝状不锈钢试样,以顶面为工作面,在试样尾部焊接上导线,然后用绝缘的环氧树脂镶嵌到pvc管中,得到丝状电极;
18.(2)将丝状电极工作面进行打磨,清洗,采用传统三电极体系在五口瓶中进行实验,以饱和甘汞电极作为参比电极,铂电极作为辅助电极,连接gamry电化学工作站与丝状电极,对丝状电极进行动电位极化,获得动电位极化曲线,确定丝状电极在该环境下的点蚀电位eb;再根据公式计算得到恒电位极化的电位ea,公式为:ea=eb+(1
±
0.2)v;
19.(3)采用相同方法制备丝状电极,对丝状电极恒电位极化,得到由丝状电极整体腐蚀构成腐蚀坑底部,环氧树脂构成腐蚀坑坑壁的一维点蚀坑;
20.(4)恒电位极化结束后,保持丝状电极位置不变,实验环境不变,继续浸泡;经过长时间的浸泡,一维点蚀坑不断向下腐蚀,一维点蚀坑内得到酸性腐蚀液及腐蚀产物。
21.进一步,动电位极化采用0.5mv/s的扫描速度,动电位极化初始电位为-1.0v(sce),终止电位扫描至过钝化区。
22.进一步,所述不锈钢材料为2cr13马氏体不锈钢。
23.本发明研究不锈钢材料耐点蚀性能的方法的过程示意图如图1所示。
24.本发明的有益效果:
25.真实点蚀发展环境包括:温度、点蚀坑发展时材料本身所处溶液环境、点蚀坑内酸性溶液、点蚀坑内活化的金属坑底及坑壁、点蚀坑上影响离子扩散的pit cover(坑盖)。因此本发明采用特定点蚀研究方法,即在电极试样表面涂覆一层涂覆层后,钻孔,然后去除工作电极部分涂覆层,暴露部分钝化态金属(阴极a-c)并进行恒电位极化,再涂覆阴极a-c并进行恒电位极化,形成微点蚀坑(阳极a-a),最后将阴极a-c涂覆层去除,在a-a阳极点蚀坑凹槽内注入酸性腐蚀液并浸泡发展,使所形成的点蚀坑发展过程与真实点蚀坑更贴切,从而得到最接近真实2cr13材质的点蚀坑,有利于研究2cr13马氏体不锈钢这种材料在真实腐
蚀环境中的点蚀发展规律,而现有点蚀研究方法绝大多数不能研究点蚀在真实的自然环境的发展。
26.本发明能够得到最接近2cr13马氏体不锈钢材质在真实腐蚀环境中所形成的点蚀坑,点蚀坑特征为开口小,内部大。其中点蚀坑上方的涂覆层作为点蚀坑盖(pit cover),与真实点蚀坑的pit cover起相同作用。
27.本发明制备同时具有活化态阳极和两侧钝化态阴极的工作电极,构建可自催化发展的闭塞点蚀坑体系的体系b(闭塞自催化的大阴极小阳极的模拟点蚀坑),在浸泡过程中,涂覆层下的金属以钻孔部位为圆心,不断向四周腐蚀,涂覆层构成的点蚀坑盖的作用会越发明显,与真实点蚀坑的特征很接近。
28.本发明体系为可控单一闭塞点蚀坑,能够得到接近真实2cr13点蚀坑形态,可用于研究2cr13马氏体不锈钢在该环境下的点蚀发展规律,以评估该不锈钢的耐腐蚀性能。
附图说明
29.图1为本发明方法的过程示意图。
30.图2为丝状电极的照片。
31.图3为丝状电极的动电位极化曲线。
32.图4为一维点蚀坑浸泡所得酸性腐蚀液及腐蚀产物烘干所得底部盐膜成分分析结果。
33.图5为丝状电极制备酸性腐蚀液及腐蚀产物过程示意图。
34.图6为本发明制备点蚀坑的示意图。
35.图7为本发明制备的点蚀坑沿点蚀坑中心纵截面扫描电镜照片(去除涂覆层)。
36.图8为真实点蚀坑沿点蚀坑中心纵截面扫描电镜照片。
37.图9为两种点蚀坑开口尺寸对点蚀发展的影响。
具体实施方式
38.以下结合实施例对本发明的具体实施方式作进一步详细说明。
39.实施例1、酸性腐蚀液的制备
40.1.1实验仪器及丝状电极的制备过程:
41.本实验用于监测试样电位的仪器为美国gamry电化学工作站,采用传统三电极体系在五口瓶中进行实验,采用饱和甘汞电极(sce)作为参比电极,铂电极作为辅助电极。试样为丝状,所用材料为2cr13,尺寸为:1mm
×
1mm
×
15mm,工作面为1mm
×
1mm一面,丝状试样的尾部用焊锡焊接上导线,然后用绝缘的液态环氧树脂镶嵌到pvc管中,待冷却凝固后得到丝状电极(如图2所示)。配制液态环氧树脂时,各原料配比为:环氧树脂:邻苯二甲酸二乙酯:乙二胺=100:7:10(质量比)。在配制时要注意绕一个方向匀速搅拌,防止配制好的液态环氧树脂中有过多气泡,影响点蚀坑截面试样的观察。
42.1.2测量丝状电极腐蚀成一维点蚀坑的恒电位极化所需电位:
43.(1)在广口瓶中使用实验室药品和去离子水按要求配制好质量浓度3.5%的nacl溶液。
44.试样在试验前打磨:在金相预磨机上依次用180、360、600、800号砂纸打磨丝状电
极工作面,并用酒精轻轻冲洗制备好样品,干燥。
45.(2)将质量浓度3.5%nacl溶液倒入五口瓶中,把饱和甘汞电极和铂电极放入五口瓶中合适的位置,使用水浴锅加热,并将温度保持在30℃,将丝状电极放入到溶液中。
46.(3)连接gamry电化学工作站与丝状电极,对丝状电极动电位极化,获得动电位极化曲线,整个曲线可分为4个区域:活化溶解区、活化-钝化过渡区、钝化区和过钝化区。
47.在对丝状电极进行动电位极化前,先在质量浓度3.5%nacl溶液中浸泡30min左右,在浸泡过程中监测丝状电极的开路电位(ocp),在此过程中,丝状电极电位会从较低电位逐渐变正,表示电极表面逐渐生成一层膜,此过程保证动电位极化曲线测试结果的准确。待开路电位稳定后,开始动电位极化曲线的测量。
48.动电位极化曲线测试采用0.5mv/s的扫描速度,动电位极化初始电位为-1.0v(sce),终止电位为-0.1v(sce)。
49.动电位极化曲线如图3所示,由图可知,丝状电极的自腐蚀电位ecorr=-0.68v(sce)。在电位区间-0.5v~-0.2v时电流密度发生激烈的波动,表示为不锈钢丝状电极表面钝化膜的破裂与再次钝化,电位超过-0.2v(sce)时,电流密度逐渐增大不再波动,表示电极表面钝化膜发生逐渐不可恢复的破裂。根据gb/t17899-1999不锈钢点蚀电位测量方法,将阳极电流密度达到100μa/cm2最正的电位值作为点蚀电位eb,2cr13的点蚀电位eb=-0.18v(sce)。即超过点蚀电位,试样表面将开始发生点蚀。为确保恒电位极化时,阳极区域钝化膜发生不可恢复的破裂,且不会反应太剧烈而难以控制,对阳极进行恒电位极化的电位ea下限不可低于点蚀电位eb,该电位的选择通常以点蚀电位为基准再加约(1
±
0.2)v,即ea=eb+(1
±
0.2)v,因此本发明对阳极进行恒电位极化的电位ea选取在+0.82v(sce)。
50.根据动电位极化测得的极化曲线还得到对阴极进行恒电位极化的电位ec,即钝化电位,钝化电位的选取在极化曲线钝化区内,一般约为ecorr+(0.6
±
0.2)
×
(eb-ecorr),即ec=ecorr+(0.6
±
0.2)
×
(eb-ecorr)v,ec范围在-0.48~-0.28v(sce),因此本发明钝化电位选取在-0.4v(sce)。
51.1.3酸性腐蚀液的获得
52.所用试样仍为上述2cr13相同材质丝状电极。
53.(1)试样在试验前打磨:在金相预磨机上依次用180、360、600、800号砂纸打磨丝状电极工作面,并用酒精轻轻冲洗制备好样品,干燥。
54.(2)将质量浓度3.5%nacl溶液倒入五口瓶中,把饱和甘汞电极和铂电极放入五口瓶中合适的位置,使用水浴锅加热,并将温度保持在30℃,将丝状电极放入到溶液中。
55.(3)连接gamry电化学工作站与丝状电极,对丝状电极进行恒电位极化,电位为+0.82v(sce),极化时间为15s,本次极化过程保持丝状电极工作面水平朝上,防止在制备酸性腐蚀液及腐蚀产物过程中,腐蚀液外溢,得到由丝状电极整体腐蚀构成腐蚀坑底部,环氧树脂构成腐蚀坑坑壁的一维点蚀坑。
56.(4)恒电位极化结束后,保持丝状电极位置不变,温度、溶液等实验环境不变,在该环境下浸泡28天。经过长时间的浸泡,一维点蚀坑不断向下腐蚀,一维点蚀坑内得到酸性腐蚀液及腐蚀产物。酸性腐蚀液及腐蚀产物(酸液和腐蚀产物的混合物)主要成分为金属溶解产生的fe和cr的阳离子以及点蚀坑底部的一层含有cl的盐膜,酸性腐蚀液及腐蚀产物ph低于浸泡环境质量浓度3.5%nacl溶液的ph(如图4所示)。
57.丝状电极制备酸性腐蚀液及腐蚀产物过程示意图如图5所示。
58.实施例2、研究不锈钢材料耐点蚀性能的方法
59.1、将尺寸为20mm
×
10mm
×
6mm的2cr13金属试样采用上述环氧树脂封装方法制备普通电化学试样,工作面为20mm
×
10mm一侧截面。然后将电化学试样工作面朝上,在电化学试样工作面整体二次涂覆液体环氧树脂,厚度约为2~3mm。厚度更厚不方便下一步的打磨,更薄也可以,但是手工操作难以达到很薄。待液体环氧树脂凝固后,再将环氧树脂涂覆层采用1000目砂纸打磨至500μm左右。涂覆层500μm厚度即代表后续所得阳极部位模拟点蚀坑的初始深度约为500μm,该深度可作为点蚀坑内各种离子向点蚀坑外扩散的障碍,该深度也可以保证坑内可以注入足够的酸性腐蚀液及腐蚀产物;若涂覆层所剩的厚度太薄,如100μm,难以注入足够的酸性腐蚀液及腐蚀产物,导致体系b的阳极点蚀坑难以腐蚀。在试样中心钻圆孔,钻孔尺寸为500μm(直径)。点蚀坑开口会影响点蚀坑内各种离子向外扩散的难度,开口过大极容易导致点蚀坑的发展停滞,开口过小不利于酸性腐蚀液的注入,也会导致后期难以观察。钻孔部位为试样正中。钻孔时避免触碰工作电极表面,仅暴露出工作电极表面金属层即可。此步骤得到工作电极a。
60.2、对工作电极a,以长边为基准,以钻孔部位为中心,两侧各去除部分涂覆层,暴露出部分钝化态金属,将暴露出的钝化态金属部位标记为a-c(阴极);以图1中的工作电极a为例,以20mm的长边为基准,以钻孔部位为中心,两侧各去除5mm的涂覆层,从而使两侧各暴露出5mm长度的钝化态金属;将工作电极a放入质量浓度3.5%nacl溶液(30℃)中,于-0.4v(sce)恒电位极化5min,使a-c部位得到稳定钝化层;
61.3、采用硫化胶涂覆a-c部位,涂覆的原因为对阳极部位a-a在+0.82v(sce)恒电位极化时,如果不涂覆a-c部位将对该部位同样产生极化作用导致a-c部位腐蚀。硫化胶干燥后将工作电极a在质量浓度3.5%nacl溶液中(30℃)在+0.82v(sce)恒电位极化5s,使工作电极钻孔部位的钝化膜破裂,裸露出活化态金属,形成微点蚀坑,此部位记为a-a(阳极)。此时,极化时间过短得不到活化态金属,时间过长容易导致微点蚀坑过深。本发明的目的是为了得到真实的自然情况下的点蚀坑,而不是极化形成的点蚀坑,极化时间过长会导致得到的点蚀坑偏离真实点蚀坑形貌。本发明极化时间保证得到的微点蚀坑开口尺寸近似等于涂覆层所钻小孔的尺寸,该小孔的直径,即为体系b在浸泡自催化发展时的点蚀坑开口尺寸。
62.4、将a-c部位硫化胶去除干净,再次暴露出a-c部位,这样在质量浓度3.5%nacl溶液中阴阳极同时接触溶液才是一个体系,然后将工作电极a再次放入质量浓度3.5%nacl溶液中,电极工作面水平朝上,防止注入a-a阳极点蚀坑凹槽的溶液外溢,并将酸性腐蚀液注射入a-a阳极点蚀坑凹槽;此时,工作电极a同时具有活化态的阳极a-a,和两侧钝化态的阴极a-c,满足闭塞点蚀坑自催化发展的条件:点蚀坑内裸露的活化态金属a-a,点蚀坑内保持点蚀坑内金属始终处于活化态的酸性腐蚀性溶液,a-a周围环氧树脂层构成扩散屏障阻碍点蚀坑内离子迁移,以及点蚀坑周围钝化态的金属作为阴极a-c。
63.此时的体系为一个可自催化发展的闭塞点蚀坑体系,称为体系b。
64.5、共制备12个独立的体系b,将其在同上试验环境的质量浓度3.5%nacl溶液中浸泡,浸泡周期分别为0天、6天、12天和30天(每个周期3个体系),在酸洗后测量点蚀坑深度,取其平均值为体系b浸泡n天的平均深度,得到该钻孔尺寸的点蚀坑的发展规律。
65.本发明方法可得到最接近真实2cr13马氏体不锈钢材质在质量浓度3.5%nacl溶
液中的点蚀坑,点蚀坑特征为开口小,内部大。其中点蚀坑上方的涂覆层作为点蚀坑盖(pit cover),与真实点蚀坑的pit cover起相同作用(如图6所示)。本发明的体系b(闭塞自催化的大阴极小阳极的模拟点蚀坑)在浸泡过程中,涂覆层下的金属以钻孔部位为圆心,不断向四周腐蚀,涂覆层构成的点蚀坑盖的作用会越发明显,与真实点蚀坑的特征很接近(如图7和图8所示)。
66.实施例3、研究不锈钢材料耐点蚀性能的方法
67.本实施例的方法同实施例2,不同之处在于改变钻孔尺寸为1000μm,得到另一钻孔尺寸点蚀坑发展规律。
68.两种钻孔尺寸的模拟点蚀坑体系b点蚀坑增加的深度和时间的关系对比图见图9。由图可知,本实验条件下,相同的材料,不同点蚀坑开口,所形成的点蚀坑的发展过程均与真实点蚀坑非常接近。其中点蚀坑开口小,点蚀坑内溶液ph更低,腐蚀性更强,点蚀坑扩展更快。
69.注:图中所示的深度为体系b点蚀坑发展到该时间周期的深度减去浸泡前的平均深度。