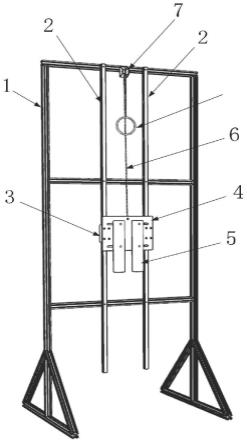
1.本发明属于岩土工程技术领域,具体涉及一种可以实现多锤同时冲击的落锤加载装置。
背景技术:2.强夯是利用重锤自由下落、以巨大的冲击能量作用于地基,克服土颗粒间的多种阻力,实现地基加固的一种有效方法。国内外学者采用物理模型试验对单点强夯的加固效果和加固机理进行了深入的研究。
3.与强夯单点冲击荷载作用不同,直升机在着陆过程中,多个轮胎同时接触场地,对场地土体同时施加冲击荷载,即荷载的作用特点为多点同时作用冲击荷载。由于直升机轮胎之间距离较近,冲击荷载作用时间短,这种多点同时冲击具有显著的时效性,且引起的附加应力会产生叠加。为研究直升机着陆过程中多点同时冲击的效应,进行物理模型试验时,务必保证多个落锤同时作用在场地土体上。现用于岩土模型试验的落锤加载装置均采用单个落锤加载的形式,无法模拟直升机着落过程产生的多点冲击荷载,不能满足工程实际的需求;并且,现有落锤加载装置大多存在操作繁琐或体积过大的问题,使用时费时费力。
技术实现要素:4.针对上述问题,本发明提供了一种可以实现多个落锤同时冲击的落锤加载装置,可实现两个及以上落锤同时下落,施加多点同时作用的冲击荷载,各落锤之间的间距也可进行调整。
5.本发明提供一种可实现多锤同时冲击的落锤加载装置,包括加载架、导轨、滑块、连接板、落锤、绳索与定滑轮。
6.所述加载架整体呈龙门架结构,架设于地面上。同时在加载架两侧中部及下部之间安装有中部横梁与底部横梁。加载架中所用杆件均采用铝合金异形截面杆,截面整体呈圆角正方形,包括沿杆件轴向设计的中心支柱、沿杆件轴向设计的四个圆角l形外壁,以及沿杆件轴向设计的连接支撑。其中,四个外壁设置于中心支柱外围,分别位于一个正方形四角处,截面共同构成圆角正方形结构,且周向上相邻外壁间不相接。中心支柱与各个外壁之间设置连接支撑,通过连接支撑将中心支柱与四个外壁间连接组成整体结构;且连接支撑设计为由三块板构成的y形截面结构。其中两个板a分别与l形外壁的两壁面垂直固连;另一个板b与中心支柱固连;通过上述对支撑架1中杆件的设计,使杆件周向四面处形成沿杆件轴向的六边形截面滑槽,用于设置六边形螺母。
7.导轨为两条竖直设置,安装于整个加载架前侧中部。两条导轨上滑动安装有滑块,两个滑块与连接板固定。
8.连接板顶部设计有绳索固定孔,与绳索一端相连,绳索绕过加载架顶端定滑块后另一端连接把手。连接板上设计有多组沿左右方向等间隔设计有多组条形孔,每组条形孔为两个,沿左右方向,分别设计于连接板上下位置。上述每组条形孔对应安装一个落锤,使
每组中两个条形孔分别与落锤上的螺孔对应,通过螺栓由连接板后侧穿过两个条形孔后与落锤上的螺纹孔拧紧,实现落锤在连接板上的固定。
9.本发明使用过程为:
10.步骤1:根据落锤数量需求选择对应数量的多组条形孔的连接板,将落锤以预设的间距固定在连接板上,并将滑块安装至连接板上。
11.步骤2:按照需求将加载架移动至指定位置,将导轨安装固定在加载架上。
12.步骤3:将安装有落锤的连接板通过其后侧滑块滑入导轨内,将绳索绕过定滑轮。
13.步骤4:通过下拉绳索,将连接板及落锤提升至需求高度,且通过导轨上沿轴向设计的刻度判断高度是否达到要求,随后开始进行落锤试验。
14.步骤5:实验完成后将连接板及落锤滑出导轨存放即可。
15.本发明具有如下优点:
16.(1)本发明可实现多锤同时冲击的落锤加载装置,主要用于岩土工程领域的物理模型试验,可以实现两个及以上落锤同时下落,施加多点同时作用的冲击荷载;
17.(2)本发明可实现多锤同时冲击的落锤加载装置,可以实现两个及以上落锤之间的间距调节,且操作简便;
18.(3)本发明可实现多锤同时冲击的落锤加载装置,落锤尺寸、样式可根据用户需求进行定制,落锤更换简便,适用于多种场合;
19.(4)本发明可实现多锤同时冲击的落锤加载装置,加载架采用铝合金空心截面杆,整体重量较轻,便于操作。
附图说明
20.图1为本发明可实现多锤同时冲击的落锤加载装置整体结构示意图;
21.图2为本发明可实现多锤同时冲击的落锤加载装置中加载架结构示意图;
22.图3为本发明可实现多锤同时冲击的落锤加载装置中加载架的杆件截面示意图;
23.图4为本发明可实现多锤同时冲击的落锤加载装置中加载架的杆件内螺母安装示意图;
24.图5为本发明可实现多锤同时冲击的落锤加载装置中导轨截面示意图;
25.图6为本发明可实现多锤同时冲击的落锤加载装置中滑块截面示意图;
26.图7为本发明可实现多锤同时冲击的落锤加载装置中导轨与滑块配合方式示意图;
27.图8为本发明可实现多锤同时冲击的落锤加载装置中滑块正面结构示意图;
28.图9为本发明可实现多锤同时冲击的落锤加载装置中滑块侧面结构示意图;
29.图10为本发明可实现多锤同时冲击的落锤加载装置中连接板结构示意图;
30.图11为本发明可实现多锤同时冲击的落锤加载装置中落锤安装方式块截面示意图。
31.图中:
32.1-加载架
ꢀꢀꢀꢀꢀꢀꢀꢀꢀꢀꢀꢀꢀꢀꢀꢀ
2-导轨
ꢀꢀꢀꢀꢀꢀꢀꢀꢀꢀꢀꢀꢀꢀꢀꢀꢀꢀ
3-滑块
33.4-连接板
ꢀꢀꢀꢀꢀꢀꢀꢀꢀꢀꢀꢀꢀꢀꢀꢀ
5-落锤
ꢀꢀꢀꢀꢀꢀꢀꢀꢀꢀꢀꢀꢀꢀꢀꢀꢀꢀ
6-绳索
34.7-定滑轮
ꢀꢀꢀꢀꢀꢀꢀꢀꢀꢀꢀꢀꢀꢀꢀꢀ
101-立柱
ꢀꢀꢀꢀꢀꢀꢀꢀꢀꢀꢀꢀꢀꢀꢀꢀ
102-底座
35.103-顶梁
ꢀꢀꢀꢀꢀꢀꢀꢀꢀꢀꢀꢀꢀꢀꢀꢀ
104-中部横梁
ꢀꢀꢀꢀꢀꢀꢀꢀꢀꢀꢀꢀ
105-底部横梁
36.106-中心支柱
ꢀꢀꢀꢀꢀꢀꢀꢀꢀꢀꢀꢀ
107-外壁
ꢀꢀꢀꢀꢀꢀꢀꢀꢀꢀꢀꢀꢀꢀꢀꢀ
108-连接支撑
37.109-滑槽
ꢀꢀꢀꢀꢀꢀꢀꢀꢀꢀꢀꢀꢀꢀꢀꢀ
110-六边形螺母
ꢀꢀꢀꢀꢀꢀꢀꢀꢀꢀ
201-导轨凹进部分
38.202-导轨凸起部分
ꢀꢀꢀꢀꢀꢀꢀꢀ
301-滑块凹进
ꢀꢀꢀꢀꢀꢀꢀꢀꢀꢀꢀꢀ
302-滑块凸起
39.401-绳索固定孔
ꢀꢀꢀꢀꢀꢀꢀꢀꢀꢀ
402-连接孔
ꢀꢀꢀꢀꢀꢀꢀꢀꢀꢀꢀꢀꢀꢀ
403-条形孔
具体实施方式
40.下面结合附图对本发明作进一步详细说明。
41.本发明可实现多锤同时冲击的落锤加载装置,该落锤加载装置主要由加载架1、导轨2、滑块3、连接板4、落锤5、绳索6与定滑轮7组成,如图1所示。
42.所述加载架1整体呈龙门架结构,如图2所示,具有左右两侧立柱101、两侧立柱101底端固定的底座102以及顶梁103,各杆件间均通过角钢及螺栓连接。加载架1通过两侧底座102架设于地面上。同时在加载架1两侧立柱101中部及下部还安装有与顶梁103平行的中部横梁104与底部横梁105,与顶梁103配合用来安装导轨2。
43.上述加载架1中所用杆件均采用铝合金异形截面杆,如图3所示,截面整体呈圆角正方形,边长30mm;包括沿杆件轴向设计的中心支柱106、沿杆件轴向设计的四个圆角l形外壁107,以及沿杆件轴向设计的连接支撑108。其中,四个外壁107设置于中心支柱106外围,分别位于一个正方形四角处,截面共同构成圆角正方形结构,且周向上相邻外壁107间不相接。中心支柱106与各个外壁107之间设置连接支撑108,通过连接支撑108将中心支柱106与四个外壁107间连接组成整体结构;且连接支撑108设计为由三块板构成的y形截面结构;其中两个板a分别与l形外壁107的两壁面垂直固连;另一个板b与中心支柱106固连。
44.上述中心支柱106为截面为边长12mm的正方形,中部沿轴向开有通孔,以减轻加载架1整体重量;且设计周向四条棱处与连接支撑108相连。连接支撑108中两个板a设计厚度为1mm,板b设计厚度为1.4mm;外壁107厚度设计为1mm。
45.通过上述对支撑架1中杆件的设计,使杆件周向四面处形成沿杆件轴向的六边形截面滑槽109,且滑槽109两侧的连接支撑中相对的板a平行,形成一个矩形空槽部分,用于设置六边形螺母110,通过相对的板a限制六边形螺母110的周向转动,保证六边形螺母110仅可沿滑槽109在杆件轴向上滑动,如图4所示;该六边形螺母110用于各杆件间的连接角钢固定,以及后续导轨2的固定;固定时仅需将要固定的部件通过螺栓与六边形螺母110配合定位后,将六边形螺母110由杆件一端插入滑槽109的矩形空槽部分内,滑动到指定位置后,由于六边形螺母110旋转被限制,通过转动螺栓即可实现部件与杆件间的固定。
46.所述导轨2为两条,垂直于顶梁103设置,安装于整个加载架1前侧中部。两条导轨2通过轴向上的三个连接位,配合螺钉分别与顶梁103、中部横梁104及底部横梁105固定,实现两条导轨2与加载架1间的固定。两条导轨2上滑动安装有滑块3。
47.上述导轨2左右两侧具有沿轴向上的导轨凹进部分201,整体截面呈工字型,如图5所示;同时在导轨2上,位于导轨凹进部分201前方的左右两侧,沿导轨2轴向各设计一条导轨凸起部分202。如图6所示,滑块3后侧面设计有导轨配合槽301,该导轨配合槽301相对侧壁上由内向外分别设计有与导轨凸起部分202及导轨凹进部分201配合的滑块凹进301及滑块凸起302。由此,通过滑块3上滑块凹进301和滑块凸起302分别与导轨凸起部分202及导轨
凹进部分201配合,将滑块3由导轨2一侧划入导轨2,实现两者间的滑动配合连接,如图7所示。通过上述设计可有效防止滑块3在滑动过程中由导轨2上脱落。
48.上述滑块3前侧面周向上设计有四个螺孔,作为连接板安装孔303,用于安装连接板4,如图8所示。
49.上述导轨2及滑块3采用hgh 25h型线性导轨滑块,单个滑块3在三个方向上的容许静力矩mr=0.56kn
·
m、m
p
=0.57kn
·
m、m
γ
=0.57kn
·
m,因此使得连接板4上安装的落锤5偏心引起的弯矩不超过滑块3的容许弯矩值时不会对导轨2造成损害。
50.所述连接板4上用来安装落锤5,整体呈长方形板状结构,如图9所示。连接板4顶部靠近顶边处中心位置开孔,作为绳索固定孔401。连接板4前侧面左右两侧各设计有4个连接孔402,分别与前述两个滑块3上的四个连接板安装孔303配合,由螺栓穿过,将连接板4固定于两个滑块3上,使连接板4可沿导轨2上下滑动;且上述连接孔402外围设计有与连接孔凹槽,使螺栓拧紧后,螺栓头部嵌入凹槽内部,不高于连接板4表面,不影响落锤5在连接板4上的安装。
51.连接板4上沿左右方向等间隔设计有n组条形孔403,每组条形孔403为两个,沿左右方向,分别设计于连接板4上下位置。上述每组条形孔403对应安装一个落锤5,使每组中两个条形孔403分别与落锤5上的螺孔对应,通过螺栓由连接板4后侧穿过两个条形孔403后与落锤5上的螺纹孔拧紧,实现落锤5在连接板4上的固定,如图10所示。通过松开螺栓,使落锤5可沿条形孔403左右移动,实现多个落锤5左右间距的调节,相邻两落锤5之间的间距调节范围设计为0~160mm。在进行实验室可通过落锤5在连接板4上的对称布置可减小滑块3所承受的弯矩。
52.上述落锤5的尺寸、样式可根据用户需求进行定制,只需在制作落锤5时在落槌上预留用于与连接板4上条形孔403配合安装的螺纹孔即可,由此使得落锤更换简便,适用于多种场合。
53.所述绳索6为尼龙绳,末端安装有把手,绳索6绕过顶梁103中心位置安装的定滑轮7,前端与连接板4顶部绳索固定孔401相连固定。由此通过手持把手拉动绳索6,实现连接板4及其上安装的落锤5的高度提升;通过松开把手实现落锤5的释放。若实验过程中落锤5数量过多,无法动过拉动把手提升多落锤高度,可添加一小型卷扬机,去掉绳索6末端把手,将绳索6末端连接至卷扬机即可。
54.本发明可实现多锤同时冲击的落锤加载装置可进行土工模型试验,在使用时可根据所需落锤5数量选择相应的连接板4进行安装。试验过程如下:
55.步骤1:根据落锤5数量需求n选择具有n组条形孔403的连接板4,将落锤5以预设的间距固定在连接板4上,并将滑块3安装至连接板4上。
56.步骤2:按照需求将加载架1移动至指定位置,将导轨3安装固定在加载架1上。
57.步骤3:将安装有落锤5的连接板4通过其后侧滑块3划入导轨2内,将绳索6绕过定滑轮7。
58.步骤4:通过下拉绳索6末端把手,将连接板4及落锤5提升至一定高度,具体高度根据试验要求确定,且通过导轨2上沿轴向设计的刻度判断高度是否达到要求,随后开始进行落锤试验。
59.步骤5:实验完成后将连接板4及落锤5滑出导轨2,妥善存放即可。
60.试验过程中,如需调节落锤5之间的间距,可将连接落锤5的螺栓拧松,此时落锤5可沿连接板4上的条形孔403水平移动,移动至合适位置后将连接落锤5螺栓拧紧即可。