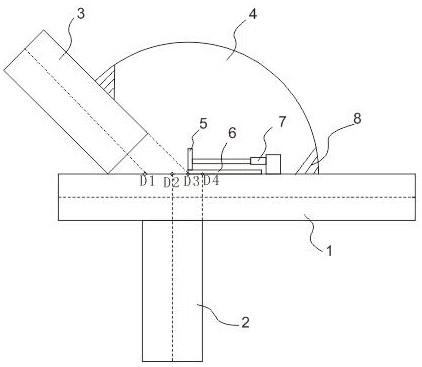
1.本发明涉及船用设备检测技术领域,具体而言,涉及一种船舶船舭部位三心对位检测方法及装置。
背景技术:2.船舶在航行过程中受到波浪冲击,会产生较大的弯曲应力,因此在船舶建造过程中十分重视钢板装配及焊接过程中的中心线对齐问题,特别是船体舭部区域,其设有横向、纵向和斜向钢板三块交汇钢板,且斜向钢板与横向钢板之间的夹角为135
°
或45
°
,且要求横向、纵向和斜向钢板的三心对位准确。
3.在传统的三心对位精度检验过程中,船厂在每个产品开工前都需要专用的角度样板,产品完成后样板无法再次利用。由于不同产品的样板不能够通用,由于横向、纵向和斜向钢板三种板位置不同,板厚不同,要精确测量每条船板则需制作出20至30块样板,利用效率比较低,或是采用滑块移动的方式进行刻度调节,但是针对不同板厚均需要人工调整,且螺栓等活动件较多,操作不便,检测效率较低且不易管理,并且使用通用样板只能确定是否对正,测量与检验精度不高。
技术实现要素:4.本发明旨在至少克服现有技术中存在的上述缺陷,提供了一种船舶船舭部位三心对位检测方法及装置,对于不同的船舶及不同部位,可以通用一个扇形样板,制作方便易于管理,检测快捷且检验精度比较高。
5.本发明通过以下方法实现:一种船舶船舭部位三心对位检测方法,其包括如下过程:s1: 制作一个弦心角为135
°
的扇形样板,并在扇形样板上设置一个沿水平方向滑动的标尺且标尺最初与扇形样板的圆心对正;s2:将扇形样板放置在船舭部位,使扇形样板的一条弦放置在船舭部位横向钢板上,扇形样板的另一条弦与船舭部位斜向钢板贴紧,并将扇形样板固定不动;s3:将船舭部位横向钢板厚度y、纵向钢板厚度x及斜向钢板厚度z分别通过pc输入给计算单元;s4:计算单元计算出移动距离,并通过pc控制驱动装置动作,驱动标尺沿着横向移动距离,若此时标尺的标记点向下的投影刚好与纵向钢板外侧边向上的延长线与横向钢板上表面的交点重合,则说明船舶船舭部位三心对位合格。
6.进一步,横向钢板厚度y、纵向钢板厚度x及斜向钢板厚度z由设计文件获得。
7.优化的,横向钢板厚度y、纵向钢板厚度x及斜向钢板厚度z由超声波厚度测量仪测量获得。
8.进一步,计算出的值若为正值,则驱动装置驱动标尺向右移动,计算出的值若为负值,则驱动装置驱动标尺向左移动。
9.一种船舶船舭部位三心对位检测装置,其包括扇形样板、标尺、pc、计算单元及驱动装置,所述扇形样板弦心角为135
°
,所述标尺滑动的安装在扇形样板上,驱动装置驱动标尺水平往复直线运动,所述pc用于接收船舭部位横向钢板厚度y、纵向钢板厚度x及斜向钢板厚度z值,并将数据传输给计算单元,计算单元计算出移动距离的值,pc控制驱动装置驱动标尺水平往复移动距离。
10.优化的,驱动装置为直线马达。
11.进一步,船舭部位横向钢板厚度y、纵向钢板厚度x及斜向钢板厚度z值根据设计文件直接由pc输入传输给计算单元。
12.优化的,还设有超声波厚度测量仪与pc连接,超声波厚度测量仪对船舭部位横向钢板厚度y、纵向钢板厚度x及斜向钢板厚度z值进行检测,并将数据传输给pc。
13.进一步,扇形样板的两端在内外两侧分别固定安装有扇形磁片。
14.优化的,扇形磁片与扇形样板在扇形磁片的下部粘接。
15.本发明的有益效果:本发明提供的一种船舶船舭部位三心对位检测方法及装置,将三心对位的数学原理与数控模块进行结合,仅需要输入三心对位钢板厚度即可计算出标尺移动距离,并自动输出至驱动装置,驱动标尺移动至指定位置,进行三心对位精度检验。结构简单,仅需一个通用的扇形样板,即可完成不同船舶船舭部位三心对位的检测,检测方便快捷且精度高。
附图说明
16.图1为本发明结构示意图。
17.图2为检测控制框图。
18.图中:1. 横向钢板,2. 纵向钢板,3. 斜向钢板,4. 扇形样板,5. 标尺,6. 轨道,7. 驱动装置,8. 扇形磁片。
具体实施方式
19.为了能够更清楚地理解本发明的上述目的、特征和优点,下面结合附图和具体实施方式对本发明进行进一步的详细描述。
20.一种船舶船舭部位三心对位检测方法,其包括如下过程:s1:制作一个弦心角为135
°
的扇形样板,并在扇形样板上设置一个沿水平方向滑动的标尺且标尺最初与扇形样板的圆心对正;s2:将扇形样板放置在船舭部位,使扇形样板的一条弦放置在船舭部位横向钢板上,扇形样板的另一条弦与船舭部位斜向钢板贴紧,并将扇形样板固定不动;s3:将船舭部位横向钢板厚度y、纵向钢板厚度x及斜向钢板厚度z分别通过pc输入给计算单元;
s4:计算单元计算出移动距离,并通过pc控制驱动装置动作,驱动标尺沿着横向移动距离,若此时标尺的标记点向下的投影刚好与纵向钢板外侧边向上的延长线与横向钢板上表面的交点重合,则说明船舶船舭部位三心对位合格。
21.进一步,横向钢板厚度y、纵向钢板厚度x及斜向钢板厚度z由设计文件获得,通常横向钢板厚度y、纵向钢板厚度x及斜向钢板厚度z是按照设计文件制作的,所以直接引用设计文件的厚度即可,无需再进行测量,使测量过程更加简单优化。
22.优化的,横向钢板厚度y、纵向钢板厚度x及斜向钢板厚度z由超声波厚度测量仪测量获得,现场测量后再将数据输入给计算模块,使检测结果精度更高,避免了制作误差的影响。
23.进一步,计算出的值若为正值,则驱动装置驱动标尺向右移动,计算出的值若为负值,则驱动装置驱动标尺向左移动,即向远离斜向钢板的方向移动。
24.一种船舶船舭部位三心对位检测装置,其包括扇形样板4、标尺5、pc、计算单元及驱动装置7,所述扇形样板弦心角为135
°
,所述标尺滑动的安装在扇形样板上,驱动装置驱动标尺水平往复直线运动,具体可以在扇形样板上固定安装一个轨道6,将标尺卡装在轨道上,由驱动装置驱动标尺沿着轨道移动。
[0025] pc用于接收船舭部位横向钢板1厚度y、纵向钢板2厚度x及斜向钢板3厚度z值,并将数据传输给计算单元,计算单元计算出移动距离的值,pc控制驱动装置驱动标尺水平往复移动距离。
[0026]
优化的,驱动装置为直线马达,使标尺移动的距离控制更加精确。
[0027]
进一步,船舭部位横向钢板厚度y、纵向钢板厚度x及斜向钢板厚度z值根据设计文件直接由pc输入传输给计算单元。
[0028]
优化的,还设有超声波厚度测量仪与pc连接,超声波厚度测量仪对船舭部位横向钢板厚度y、纵向钢板厚度x及斜向钢板厚度z值进行检测,并将数据传输给pc。
[0029]
进一步,扇形样板的两端在内外两侧分别固定安装有扇形磁片8。设置扇形磁片的目的:一是增大扇形样板端部与横向钢板及斜向钢板的接触面积,防止样板倾斜导致监测数据失准。二是借助磁力使扇形样板与被检测位置钢板紧密垂直贴合,不再依靠人手辅助保持垂直贴合,防止人为因素导致样板不够垂直,并且不会妨碍标尺的移动。三是保护样板的端部,避免磨损,发生磨损后更换扇形磁片即可。
[0030]
优化的,扇形磁片与扇形样板在扇形磁片的下部粘接。配置扇形磁片数量为4块,具体半径可以优化为30mm左右,厚度为10mm左右。粘贴位置为弧形样板端部。粘贴时,粘合剂涂抹位置为扇形磁片下半部分,进行点状涂抹,不进行连续的面状涂抹,涂抹面积不超过扇形磁片总面积的40%,可以方便在磁片破损或者磨损后更换。
[0031]
更换磁片的方法:由于扇形磁片的下半部分涂抹粘合剂,上半部分没有涂抹粘合剂,因此使用螺丝刀从扇形磁片的上半部分撬动,即可将磁片与扇形样板分离。完成分离
后,将样板上残留的胶渍清洗干净,待表面无水渍残留后,将更换的磁片涂抹粘合剂,完成黏贴即可。
[0032]
本发明保护的船舶船舭部位三心对位检测装置,假设斜向钢板与扇形样板贴合面的延长线与横向钢板上表面的交点为d3,纵向钢板内侧面向上的延长线与横向钢板上表面的交点为d4,纵向钢板中心线向上的延长线与横向钢板上表面的交点为d2,斜向钢板中心线向下的延长线与横向钢板上表面的交点为d1,则根据几何关系,且由于斜向钢板与横向钢板之间的夹角为135
°
,假设船舭部位横向钢板、纵向钢板及斜向钢板三心对位,即三块钢板的中心线相交于一点,则有:d3d4+d1d3=d1d2+d2d4
ꢀꢀꢀꢀ
(1)d1d3=
ꢀꢀꢀꢀꢀꢀꢀꢀꢀꢀꢀꢀꢀꢀꢀꢀꢀꢀ
(2)d1d2=
ꢀꢀꢀꢀꢀꢀꢀꢀꢀꢀꢀꢀꢀꢀꢀꢀꢀꢀꢀ
(3)d2d4=
ꢀꢀꢀꢀꢀꢀꢀꢀꢀꢀꢀꢀꢀꢀꢀꢀꢀꢀꢀ
(4)d3d4=
ꢀꢀꢀꢀꢀꢀꢀꢀꢀꢀꢀꢀꢀꢀꢀ
(5)若三心对位,将扇形样板放置在船舭部位,使扇形样板的一条弦放置在船舭部位横向钢板上,扇形样板的另一条弦与船舭部位斜向钢板贴紧时,扇形样板的圆心位置应该与d3重合,则标尺向右移动距离,那么标尺的位置应该与d4重合,若不重合,说明三块钢板的中心线没有相交于一点,三心对位不准确。
[0033]
综上所述,本发明提供的一种船舶船舭部位三心对位检测方法及装置,将三心对位的数学原理与数控模块进行结合,仅需要分别输入三心对位钢板的厚度,即可通过计算模块自动计算出标尺移动的距离,并通过pc控制驱动装置驱动标尺移动相应的距离,根据标尺是否与相应的点重合就可以精确检测出船舶船舭部位的三块钢板是否三心对位。其检测结果比较精准,而且结构简单,仅需一个通用的扇形样板,即可完成不同船舶船舭部位三心对位的检测,检测方便快捷,可以实现自动控制。
[0034]
以上所述仅为本发明的优选实施例而已,并不用于限制本发明,对于本领域的技术人员来说,本发明可以有各种更改和变化。凡在本发明的精神和原则之内,所作的任何修改、等同替换、改进等,均应包含在本发明的保护范围之内。