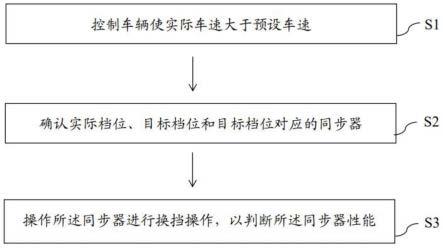
1.本技术涉及车辆性能测试技术领域,尤其涉及一种车辆变速箱同步器性能的测试方法及车辆。
背景技术:2.随着汽车产业的进一步发展,市场竞争愈发激烈,市场对产品性能要求越来越严格,产品种类也更加多样化,为此在新产品开发时要更好地满足客户需求。车辆变速箱同步器的功能是在保证转速同步的条件下完成换档,可避免换档打齿、换档冲击的产生,同步器主要由接合套、同步环等组成。
3.相关技术一般采用台架试验对同步器的性能进行测试,但需要制定专用的同步器测试台架,台架方案十分复杂。
技术实现要素:4.有鉴于此,本技术实施例期望提供一种车辆变速箱同步器性能的测试方法及车辆,能够通过评估同步器换档的最大同步转速设计边界参数验证同步器的性能。
5.为达到上述目的,本技术实施例一方面提供一种车辆变速箱同步器性能的测试方法,包括:
6.控制车辆使实际车速大于预设车速;
7.确认实际档位、目标档位和目标档位对应的同步器;
8.操作所述同步器进行换档操作,以判断所述同步器性能。
9.一些实施例中,在第一试验场内控制所述车辆起步,在第二试验场内操作所述同步器进行换档操作,所述第二试验场与所述第一试验场相连,其中,所述第一试验场的附着系数大于所述第二试验场的附着系数。
10.一些实施例中,所述第一试验场为平铺的雪地路面或为附着系数大于等于0.2的平铺路面,所述第二试验场为平铺的冰地路面或为附着系数小于等于0.15的平铺路面。
11.一些实施例中,若当所述车辆的实际车速大于所述预设车速,所述车辆还未达到所述第二试验场,则所述车辆滑行至所述第二试验场,在所述第二试验场内所述车辆的实际车速大于或等于所述预设车速。
12.一些实施例中,操作所述同步器进行换档操作的步骤,具体包括:
13.点刹制动所述车辆使实际档位的变速箱的输入轴转速等于第一预设转速;
14.制动踩到底或控制离合器分离,操作所述同步器换至中位;
15.当目标档位的所述变速箱的输入轴转速等于第二预设转速,控制所述同步器换至目标档位位置。
16.一些实施例中,控制车辆使实际车速大于预设车速的步骤之前,所述测试方法包括:
17.将所述车辆调整为预设状态后启动所述车辆。
18.一些实施例中,所述车辆的预设状态包括:关闭esc/abs功能及tcu对abs相关功能诊断。
19.一些实施例中,所述测试方法包括:
20.获取所述车辆的实际车速、所述变速箱的档位信号、发动机转速、所述变速箱输入轴转速以及换档控制机构位置信号;
21.分析出目标档位对应的所述同步器同步端与被同步端两侧最大同步转速差对应的档位车速。
22.一些实施例中,所述同步器最大同步转速差为第一预设值工况下,换档操作次数大于等于2。
23.本技术实施例又一方面提供一种测试变速箱同步器性能的车辆,所述车辆包括:
24.发动机;
25.变速箱,包括离合器和用于换档的同步器,所述变速箱与所述发动机通过所述离合器驱动连接;
26.变速箱控制单元,用于获取所述变速箱的输入轴转速、实际档位、目标档位以及所述离合器的观测扭矩;
27.车载控制器,用于接收所述变速箱控制单元获取的信号,计算所述同步器的同步端转速、被同步端转速和换档残余力矩,进行所述同步器运动状态分析。
28.本技术实施例提供的车辆变速箱同步器性能的测试方法,通过控制车辆以足够高的车速,能够进行制动和换档操作,并设定能够使同步器在同步作用下实现最大同步转速差的变化的档位变化,即从实际档位切换至目标档位,再通过观察车辆换档时同步器的运行状态,来判断同步器的性能。如此,能够实现最大同步转速差变化,为换档系统开发和控制提供能够设计采用的最大同步转速差,同时也能利用最大同步转速差的变化来评估同步器的同步环碳条的粘附性能。
附图说明
29.图1为本技术实施例提供的一种双离合器变速箱的结构示意图;
30.图2为本技术实施例提供的一种双离合器变速箱d1档传力路线的结构示意图;
31.图3为本技术实施例提供的一种双离合器变速箱r档传力路线的结构示意图;
32.图4为本技术实施例提供的一种锁环式同步器的结构示意图;
33.图5为本技术实施例提供的一种车辆变速箱同步器性能的测试方法的流程示意图;
34.图6为本技术实施例提供的一种试验场地的示意图;
35.图7为本技术实施例提供的在单个输入轴之间的换档同步过程的示意图;
36.图8为本技术实施例提供的在内外输入轴之间的换档同步过程的示意图;
37.图9为本技术实施例提供的一种车辆变速箱同步器性能的测试方法的具体流程示意图。
38.附图标记说明
39.双离合器变速箱10;外输入轴101;内输入轴102;档位齿轮103;齿轮选择器104;第一离合器105;第二离合器106;同步器20;齿毂201;滑块202;齿套203;同步环204;结合齿
205;锁销206。
具体实施方式
40.需要说明的是,在不冲突的情况下,本技术中的实施例及实施例中的技术特征可以相互组合,具体实施方式中的详细描述应理解为本技术宗旨的解释说明,不应视为对本技术的不当限制。
41.常见变速箱种类有:手动变速箱、自动变速箱、半自动变速箱、双离合变速箱(dual clutch transmission,缩写为dct)以及无级变速箱。其中,dct能够实现快速换档,还具有较高的传动效率,然而其在换档过程中容易出现明显的顿挫感且散热困难,因此需要提高制造加工的精度。
42.参阅图1,以某种结构的双离合变速箱10(以下简称dct)为例,圆套中的数字1~6、r代表档位,两个离合器单独运转,第一离合器105控制偶数档,即二档、四档和六档,第二离合器106控制奇数档,即一档、三档、五档和倒档。dct的中央是一个由两个部分构成的动力输入轴,利用双变速输入轴构造使奇数档和偶数档分离,其中外输入轴101为中空轴,用于为二档和四档提供动力;内输入轴102嵌套在外输入轴101中,用于为一档、三档和五档提供动力。
43.在dct的换档过程中,首先需要控制离合器制动,使发动机与变速箱断开连接,中断输送到变速箱的动力,然后操作换档杆实现档位切换,在这个过程中,涉及到齿形选择器104与不同档位齿轮103的切换与结合,而同步器20能够利用摩擦消除齿轮间的转速差,让齿轮在结合之前相匹配,从而实现被同步端与同步端的同步,以防止磨齿。
44.参阅图2和图3,以某种结构的dct为例,图2为d1档动力路线示意图,图3为r档动力路线示意图。以d1档切换至r档为例,在d1档行驶过程中,动力从外输入轴is1输入,通过5档齿轮和同步器sc耦合,动力经内输入轴is2轴齿轮、2档齿轮传递到第一输出轴os1,再由第一输出轴os1输出动力;在d1档切换至r档的换档过程中,同步器s1从与2档齿轮耦合切换至中位,同步器s2从中位同步至r档齿轮耦合,此时动力传递路线为外输入轴is1、5档齿轮、同步器sc、6档齿轮、内输入轴is2轴齿轮、2档齿轮、r档齿轮、第二输出轴os2,由于中间多了一个r档齿轮,所以传递方向较之前的相反,第一输出轴os1、第二输出轴os2与差速器输出端耦合转向相同。
45.现有的常见同步器种类有:常压式、惯性式以及自行增力式,其中,惯性式又包括锁环式和锁销式,在现有的轿车市场中,大多数汽车都采用锁环式同步器。参阅图4,锁环式同步器20包括有齿毂201、滑块202、结合齿203、同步环204、齿套205、锁销206和碳条层207。在换档过程中,同步环204与结合齿203所在的摩擦锥面摩擦,利用摩擦传力使得结合齿两端转速同步。
46.需要注意的是,在同步器转速同步作用下同步转速差的变化过程中,同步器的同步性能能够反映同步环碳条粘附性能。具体地,同步器转速同步作用下同步转速差越大,同步器产生的摩擦力矩和滑摩功也就越大,会导致同步环工作环境温度升高和所受的应力增大。当同步环工作环境温度过高时,同步环表面碳附摩擦层材料会被损坏,从而导致同步器丧失摩擦同步功能。因此,在动态进行同步器在不同转速差下的测试中,同步器的同步性能受同步环碳条粘附性能的影响,可以根据同步环碳条的损坏程度评估同步环碳条的粘附性
能。
47.有鉴于此,本技术实施例均以采用锁环式同步器20的dct车型为例,参阅图5,本技术实施例一方面提供一种车辆变速箱同步器性能的测试方法,测试方法包括以下步骤:
48.s1:控制车辆使实际车速大于预设车速;
49.s2:确认实际档位、目标档位和目标档位对应的同步器;
50.s3:操作同步器进行换档操作,以判断同步器性能。
51.本技术实施例提供的测试方法,通过给予车辆以足够的车速,以使车辆有足够高的车速,能够进行制动和换档操作,并设定能够使同步器在同步作用下实现最大同步转速差的变化的档位变化,即从实际档位切换至目标档位,再通过观察车辆换档时,同步器的运行状态及输入轴转速变化率,来判断同步器性能。如此,能够实现最大同步转速差变化,为换档系统开发和控制提供能够设计采用的最大同步转速差,同时也能利用最大同步转速差的变化来评估同步环碳条的粘附性能。
52.下面详细介绍各步骤的具体实施方式。
53.s1:控制车辆使实际车速大于预设车速。
54.可以理解的是,使实际车速大于预设车速,是为了让车辆有足够高的车速,能够进行制动和换档操作。
55.预设车速是根据变速箱构型条件、车速与测试的同步器在不同档位间的传动比换算关系以及换档过程中同步器的最大同步转速差确定的。例如,在前进档(drive,缩写为d档)切换至倒档(reverse,缩写为r档)的情况下,预设车速的理论估算方法为,在忽略换档时间情况下,认为换档前后车速相同,将该车速定为v,则换档前变速箱的输入轴的转速n1=v/id,id为d档传动比,换档后变速箱的输入轴的转速n2=v/ir,ir为r档传动比,同步器转速差为换档前后输入轴的转速的矢量差值。同时,同步器转速差与车速存在线性的对应关系,通过同步器设计的最大同步转速差可以反算得预设的最大车速,即预设车速。
56.s2:确认实际档位、目标档位和目标档位对应的同步器。
57.实际档位是指控制车辆加速直至实际车速大于预设车速时,所对应的当前档位;通过将实际档位切换至对应档位,能够实现同步器转速同步作用下最大同步转速差的变化,该对应档位即为目标档位。
58.实际档位与目标档位是根据变速箱的换档功能设定的,根据不同的行车情况,同一实际档位对应不同的目标档位。例如,一种行车情况为车辆从低档向高档变换档位时,如驻车档(park,缩写为p档)摘出挂到d1档时,d1档为实际档位,则d2档为目标档位;另一种行车情况为车辆从高档向低档变换档位时,如从高档降到d1档时,d1档为实际档位,则r档为目标档位。
59.s3:操作同步器进行换档操作,以判断同步器性能。
60.具体的,通过控制车辆从实际档位切换至目标档位,完成换档操作,从而在同步器同步作用下实现最大同步转速差的变化,并通过测试驾驶员观察同步器是否完成挂档,且输入轴转速变化率是否异常来判断同步器性能。如果同步器完成挂档,且输入轴转速变化率没有异常,则同步器性能良好;如果同步器没有完成挂档,且输入轴转速变化率异常,则同步器性能有待改善或调整换档系统开发和控制提供最大同步转速设计边界参数。
61.一些实施例中,操作同步器进行换档操作的s3步骤,具体包括:
62.s31:点刹制动车辆使实际档位的变速箱的输入轴转速等于第一预设转速。
63.可以理解的是,点刹制动是为了确保车辆直线行驶,不会失去稳定性,同时,制动能够实现离合器分离、减少同步工况承受驱动端传递扭矩的影响。
64.第一预设转速是指变速箱的输入轴换档过程中的初始转速。使实际档位的变速箱的输入轴转速降至第一预设转速,是为了控制测试过程中的初始同步转速,以保证在测试过程中能实现最大同步转速差的变化。
65.s32:制动踩到底或控制离合器分离,操作同步器换至中位。
66.可以理解的是,同步器是通过齿毂201与档位齿轮结合齿203相结合传递扭矩的,其未结合状态下叫做同步器的中位。制动踩到底或控制离合器分离,并操作同步器换至中位,能够使目标档位对应的输入轴与传动系解耦,从而减少同步器换档时的负载,降低同步惯量同步过程中解锁和拨环的同步力矩降低。
67.s33:当目标档位的变速箱的输入轴转速等于第二预设转速,控制同步器换至目标档位位置。
68.同步器换至目标档位位置对应车辆从实际档位切换至目标档位,第二预设转速是第一预设转速通过一定的比例关系得出的,车辆从实际档位切换至目标档位,且输入轴转速由第一预设转速变为第二预设转速,通过控制测试过程中的最终同步转速,能够在同步器同步作用下实现最大同步转速差的变化。
69.需要注意的是,第一预设转速和第二预设转速是根据试验设计的同步转速差、变速箱构型、同步器至轮端的速比条件综合计算可以得到。在同步器所涉及的台架稳态测试中,所具体涉及的转速计算、车速计算等在相关技术中以得到广泛成熟应用,在此不加以赘述。
70.具体地,点刹制动车辆使目标档位的变速箱的输入轴转速等于第二预设转速,再将制动踩到底或控制离合器分离,控制同步器换至目标档位位置。在将控制同步器换至目标档位位置的过程中,需要测试驾驶员注意车辆是否出现挂档故障报错、转速变化率异常的情况。如果出现上述情况,则说明同步器功能出现异常,试验不成功;如果出现上述情况,并能够完成挂档,则说明同步器功能正常,且成功完成一次试验测试流程。
71.一些实施例中,参阅图7,当换档操作是在变速箱的单个输入轴的档位之间进行,实际档位切换至目标档位为单个输入轴之间的换档,即奇数档之间的切换或偶数档之间的切换。例如,当从实际档位d3档切换至目标档位d1档时,两个档位皆位于变速箱的内输入轴上,因此两档切换时的转速变化都在内输入轴上。在换档过程中,使d3档的内输入轴转速等于第一预设转速,再操作同步器换至中间位置,然后控制车辆制动减速,使d1档的内输入轴转速等于第二预设转速,控制同步器换至目标档位位置,在此过程中,变速箱的内输入轴转速从第一预设转速降至第二预设转速,实现了最大转速差的变化。
72.一些实施例中,参阅图8,当换档操作是在变速箱的内外输入轴的档位之间进行,实际档位切换至目标档位为内外输入轴之间的换档,即奇数档与偶数档之间相互切换。例如,当从实际档位d1档切换至目标档位r档时,d1档位于变速箱的外输入轴上,r档档位于变速箱的内输入轴上,因此两档切换时的转速变化分别作用于内输入轴和外输入轴上。在换档过程中,使d1档的外输入轴转速等于第一预设转速,再操作同步器换至中间位置,然后控制车辆制动减速,使r档的内输入轴转速等于第二预设转速,控制同步器换至目标档位位
置,在此过程中,变速箱的内外输入轴相互交替作用,转速从内输入轴的第一预设转速降至外输入轴的第二预设转速,实现了最大转速差的变化。
73.参见图6,本技术实施例的车辆变速箱同步器性能的测试在试验场内进行。试验场包括第一试验场和第二试验场,例如,第二试验场两端分别连接有第一实验场,其中,第一试验场的附着系数大于第二试验场的附着系数。
74.一些实施例中,车辆变速箱同步器性能的测试方法,具体为在第一试验场内控制车辆起步,在第二试验场内操作同步器进行换档操作。也就是说,在第一试验场内控制车辆起步,并控制车辆使实际车速大于预设车速,在从第一试验场进入第二试验场前,需要确认实际档位、目标档位和目标档位对应的同步器,最后,从第一试验场进入第二试验场,并在第二试验场内操作同步器进行换档操作。
75.需要注意的是,使实际车速大于预设车速是为了确保车辆在进入第二试验场前有足够高的车速,然后在第二试验场内操作同步器进行换档操作过程中,能够完成制动和换档操作。
76.需要说明的是,由于路面附着系数越高,车辆可以利用的驱动力或制动力越大。车辆在第一试验场内需要完成起步加速的操作,对路面附着系数的要求较低,而车辆在第二试验场内操作同步器进行换档操作时,需要排出其他因素的影响,营造极限情况,以得到在设计的极限情况下同步器性能的设计极限,对路面附着系数的要求较高。因此,第一试验场的附着系数大于第二试验场的附着系数,第一试验场的附着系数需要满足车辆正常运行;第二试验场的附着系数则需要尽最大可能的消除变速箱传动轴系传递的扭矩,最大限度地降低传动系负载,如此,能够减少同步器在换档过程中传递扭矩。
77.具体地,一些实施例中,第一试验场为平铺的雪地路面或为附着系数大于等于0.2的平铺路面,第二试验场为平铺的冰地路面或为附着系数小于等于0.15的平铺路面。
78.一些实施例中,若当车辆的实际车速大于预设车速,车辆还未达到第二试验场,则车辆滑行至第二试验场,在第二试验场内车辆的实际车速大于或等于预设车速。
79.具体地,在第一试验场内控制车辆使实际车速大于预设车速之后会出现三种情况,其一为车辆刚好达到第二试验场,则车辆以实际车速大于预设车速进入第二试验场;其二为车辆还未达到第二试验场,控制车辆滑行至第二试验场,此时车辆的实际车速大于或等于预设车速;其三为车辆还未达到第二试验场,控制车辆滑行,在滑行的过程中车辆的实际车速小于预设车速,则需要重新控制车辆使实际车速大于预设车速,并使车辆以实际车速大于预设车速进入第二试验场。
80.需要注意的是,车辆的显示设备上有人机交互模块,可以显示出车速信号的数值,测试驾驶员能够通过目视车速信号的数值,判断车辆实际车速是否大于或等于预设车速;测试驾驶员在测试过程中,能够通过目视实地情况,判断车辆是否从第一试验场达到第二试验场。
81.一些实施例中,控制车辆使实际车速大于预设车速的步骤之前,测试方法包括:将车辆调整为预设状态后启动车辆。
82.可以理解的是,为了应对第二试验场附着系数较低而可能导致车辆打滑的情况,需要将影响车辆加速、换档、同步器两端的力矩的相关设备进行调整。如此,使车辆调整为预设状态,以保证车辆在第二试验场内的正常行驶。
83.具体地,一些实施例中,车辆的预设状态包括:关闭汽车电子稳定控制系统(electronic stability controller,esc)或防抱死制动系统(antilock brake system,abs)功能及远程信息控制单元(telematics control unit,tcu)对abs相关功能诊断。在附着系数较低的场地行驶时,遇到打滑工况,esc会向tcu发送限扭请求,影响加速和换档功能;制动力矩分配也会产生阻力矩,影响同步器两端的力矩,如此,能够实现车辆的平稳运行;关闭abs诊断后,abs无法向tcu发送车速和轮速信号,能够保证车辆的正常操作,tcu如未关闭abs诊断,将按照变速箱跛行策略,离合器打开,车辆无法加速行驶。
84.一些实施例中,测试方法包括获取车辆的实际车速、变速箱的档位信号、发动机转速、变速箱输入轴转速以及换档控制机构位置信号;分析出目标档位对应的同步器同步端与被同步端两侧最大同步转速差对应的档位车速。
85.可以理解的是,档位车速是指测试方法中为试验设计的、用于考核同步器最大同步转速差对应的车速或验证最大同步转速差时不断调整和验证的车速,即为预设车速、第一预设转速对应的车速和第二预设转速对应的车速。在实际测试的过程中,车辆的加速、观察车速、目标轴转速、换档操作都围绕着档位速度展开。此外,第一预设转速为车速与同步器起始档位对应的速比的乘积、第二预设转速为车速与同步器目标档位对应的速比的乘积,同步转速差为第一预设转速与第二预设转速的差值,制定同步器的同步转速差与设计的换档车速有关。
86.在所述的测试方法的试验设计中,车辆的实际车速、变速箱的档位信号、发动机转速、变速箱输入轴转速为计算同步器两端最大同步转速差所需要的信息,获取上述信息用于分析目标档位对应的同步器同步端与被同步端两侧最大同步转速差对应的档位车速。然后根据计算获取的同步器所能承受的最大同步转速差,以评估同步器的同步性能,同时获取换档系统开发和控制能够设计采用的最大同步转速差。
87.需要注意的是,在实际测试的过程中,因关闭了esc/abs,参考全球定位系统(global positioning system,gps)作为换档的车速,参考变速箱的档位信号、发动机转速、变速箱输入轴转速、换档控制机构位置信号作为换档开始与结束观测的信息,发动机转速信号主要用于判断换档时的转速是否超出了发动机超转速断油转速,超出该转速下的换档没有实际意义。
88.一些实施例中,同步器最大同步转速差为第一预设值工况下,换档操作次数大于等于2。
89.具体地,在成功完成一次试验测试流程后,需要再次重复至少一次试验测试流程,在同步器最大同步转速差为第一预设值工况下,完成换档操作。如此,能够减少试验测试误差,排出其他因素干扰,确保测试结果的准确性。
90.一些实施例中,参阅图9,车辆变速箱同步器性能的测试方法具体流程为:
91.p1:车辆进入第一试验场,将车辆调整为预设状态后启动车辆,以保证车辆在打滑工况下能够正常行驶。
92.p2:控制车辆使实际车速大于预设车速,以保证车辆有足够高的车速能够进行制动和换档操作。
93.p3:确认实际档位、目标档位和目标档位对应的同步器,以保证能够实现同步器转速同步作用实现最大同步转速差的变化。
94.p4:完成上述操作后,判断车辆是否进入第二试验场,若车辆没有进入第二试验场,则执行p5步骤;若车辆进入第二试验场,则执行p7步骤。
95.p5:控制车辆滑行,在车辆滑行的过程中,车辆会逐渐减速,同时车辆会不断接近第二试验场。
96.p6:判断车辆实际车速是否小于预设车速,若车辆实际车速小于预设车速,则执行p2步骤;若车辆实际车速不小于预设车速,则执行p4步骤。
97.p7:点刹制动车辆,使实际档位的变速箱的输入轴转速等于第一预设转速,控制测试过程中的初始同步转速,以保证在测试过程中能实现最大同步转速差的变化。
98.p8:制动踩到底或控制离合器分离,操作同步器换至中位,以使目标档位对应的输入轴与传动系解耦,从而减少同步器换档时的负载,降低同步惯量同步过程中解锁和拨环的同步力矩降低。
99.p9:点刹制动车辆,使实际档位的变速箱的输入轴转速等于第二预设转速,控制测试过程中的最终同步转速,以实现最大同步转速差的变化。
100.p10:制动踩到底或控制离合器分离,操作同步器换至目标档位位置,实现再最大同步转速差的变化下的换档操作。
101.p11:判断换档过程中同步器是否完成换档,且转速变化率是否异常。
102.p12:获取车辆的实际车速、变速箱的档位信号、发动机转速、变速箱输入轴转速以及换档控制机构位置信号,再通过车载控制器接收变速箱控制单元获取的信号。
103.p13:分析出目标档位对应的同步器同步端与被同步端两侧最大同步转速差对应的档位车速、计算同步器的同步端转速、被同步端转速和换档残余力矩。
104.p14:根据计算获取的同步器所能承受的最大同步转速差,以评估同步器的同步性能,同时获取换档系统开发和控制能够设计采用的最大同步转速差。
105.p15:通过观测在最大同步转速差的变化下同步环碳条的损坏程度评估同步环碳条的粘附性能,即在最大同步转速差的变化下同步环碳条的损坏程度越小,同步环碳条的粘附性能越好。
106.本技术实施例另一方面,提供一种测试变速箱同步器性能的车辆,车辆包括发动机、变速箱、变速箱控制单元(transmission control unit,tcu)和车载控制器。变速箱包括离合器和用于换档的同步器,变速箱与发动机通过离合器驱动连接;变速箱控制单元用于获取变速箱的输入轴转速、实际档位、目标档位以及离合器的观测扭矩;车载控制器用于接收变速箱控制单元获取的信号,计算同步器的同步端转速、被同步端转速和换档残余力矩,进行同步器运动状态分析。
107.本技术提供的各个实施例/实施方式在不产生矛盾的情况下可以相互组合。以上所述仅为本技术的较佳实施例而已,并不用于限制本技术,对于本领域的技术人员来说,本技术可以有各种更改和变化。凡在本技术的精神和原则之内,所作的任何修改、等同替换、改进等,均应包含在本技术的保护范围之内。