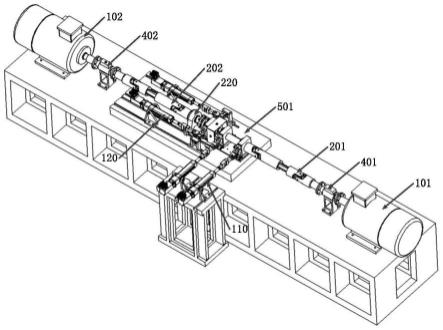
1.本技术涉及弹性联轴器疲劳测试技术领域,具体涉及一种用于联轴器的疲劳试验装置及疲劳试验方法。
背景技术:2.联轴器又称联轴节,是传动系统中连接驱动轴与从动轴用于传递动力的关键装置,主要用来将不同机构中的主动轴和从动轴牢固地联接起来一同旋转。联轴器可分为刚性联轴器和挠性联轴器两大类,其中挠性联轴器又可分为无弹性元件挠性联轴器和有弹性元件挠性联轴器,无弹性元件挠性联轴器只具有补偿两轴线相对位移的能力,但不能缓冲减振,常见的有滑块联轴器、齿式联轴器、万向联轴器和链条联轴器等;有弹性元件挠性联轴器因含有弹性元件,除具有补偿两轴线相对位移的能力外,还具有缓冲和减振作用,常见的有弹性套柱销联轴器、弹性柱销联轴器、梅花形联轴器、轮胎式联轴器、蛇形弹簧联轴器和簧片联轴器等。然而有弹性元件挠性联轴器其在安装或长期使用过程中往往会存在径向、角向及轴向偏差,长时间处于不对中状态下运行容易引起联轴器元件的疲劳破坏。
3.目前现有技术中针对联轴器的安装误差所引起的疲劳损伤问题设计出了一些关于联轴器的故障模拟试验装置,例如模拟联轴器径向误差的实验装置、模拟联轴器角向误差的实验装置等,通过这些装置得到径向、角向及轴向偏差,模拟联轴器的安装误差,从而对联轴器的疲劳寿命进行评估。然而在工程实际应用中,联轴器一般会与转子、轴承等连接为一套传动系统,且在系统固定处会设置弹性隔振装置,使传动系统处于柔性支撑中,因此在联轴器运行时会受到其他动部件的影响发生动态不对中,这种动态不对中会导致联轴器的弹性元件受到外部激励而发生振动,并与静态不对中导致的振动相耦合。例如在飞机、船舶等大型设备的任务剖面中由于发动机输出功率会随不同的工况要求而变化,这可能会使某一时段传动系统动态不对中导致的振动频率较为接近联轴器固有频率,因此联轴器的倍频振动会更加突出,结合系统的全生命周期,这种共振产生的振动应力会时联轴器中的弹性元件产生累计损伤,最终可能导致其发生振动疲劳破坏。
4.因此,为更全面地评估联轴器的疲劳寿命,其动态不对中所造成的振动导致联轴器中的弹性元件疲劳破坏不可忽视,从而亟需设计一种用于联轴器的疲劳试验装置。
技术实现要素:5.本技术提供一种用于联轴器的疲劳试验装置及疲劳试验方法,以为更全面地评估联轴器的疲劳寿命。
6.本技术第一方面提供一种用于联轴器的疲劳试验装置,该疲劳实验装置包括:加载系统、连接系统以及数据测量系统;
7.所述加载系统包括驱动变频电机、径向角向加载机构、轴向加载机构、负载变频电机,在无负载的情况下所述径向角向加载机构的水平方向与轴向加载机构的水平方向垂直,且所述径向角向加载机构用于对弹性联轴器试件施加径向与角向的载荷,所述轴向加
载机构用于对弹性联轴器试件施加轴向的载荷;
8.所述连接系统包括第一滑杆十字万向联轴器、第二滑杆十字万向联轴器以及传动轴组件,所述第一滑杆十字万向联轴器通过传动轴组件分别与所述驱动变频电机和弹性联轴器试件连接,所述第二滑杆十字万向联轴器通过传动轴组件分别与负载变频电机和弹性联轴器试件连接;
9.所述数据测量系统用于测量传动轴组件上的扭力、所述径向角向加载机构上的径向力和角度、所述轴向加载机构的轴向力以及弹性联轴器试件的位移。
10.优选地,所述径向角向加载机构包括第一加载装置、第二加载装置、第一关节轴承、径向加载轴承座、滑块、导轨底盘以及转盘轴承;
11.所述第一加载装置与第二加载装置的结构相同,均由第一电缸和第一电缸底座组成,所述第一电缸底座用于支撑和固定所述第一电缸;
12.所述径向加载轴承座和所述第一关节轴承设置有两组,每组中均为所述径向加载轴承座均为单边同侧与所述第一关节轴承连接,无负载的情况下两个所述第一关节轴承相互平行且轴线与所述径向加载轴承座的传动轴垂直,所述第一加载装置与其中一个所述第一关节轴承连接,所述第二加载装置与另一个所述第一关节轴承连接;
13.所述滑块设置有两组,每个所述滑块与对应位置的所述径向加载轴承座连接,且所述滑块在力的作用下沿着所述导轨底盘上表面的导轨滑动;所述转盘轴承装设在所述导轨底盘的下表面,用于所述导轨底盘在力的作用下转动。
14.优选地,所述轴向加载机构包括第三加载装置、第四加载装置、第二关节轴承、轴向加载轴承座、轴承座支撑架、直线运动轴承组件以及固支轴承座组件,所述连接系统包括第三传动轴;
15.第三加载装置和第四加载装置的结构相同,均由第二电缸和第二电缸底座组成,所述第二电缸底座用于支撑和固定所述第二电缸;
16.所述轴向加载轴承座的两侧各连接一个所述第二关节轴承,无负载的情况下两个所述第二关节轴承以及直线运动轴承组件的轴线相互平行,所述第三加载装置与其中一个所述第二关节轴承连接,所述第四加载装置与另一个所述第二关节轴承连接;
17.所述轴承座支撑架设置有两个,分别位于所述轴向加载轴承座的两侧,用于减小轴向运动时所述轴向加载轴承座的摩擦力;
18.所述第三传动轴通过所述固支轴承座组件进行径向轴向约束,所述固支轴承座组件用于平衡径向力与力矩;
19.所述直线运动轴承组件装设在所述轴向加载轴承座上,所述直线运动轴承组件通过第三传动轴与固支轴承座组件连接,所述直线运动轴承组件用于释放所述轴向加载机构的轴向自由度且使得所述第二滑杆十字万向联轴器不受轴向力影响。
20.优选地,所述数据测量系统包括第一扭力传感器、第二扭力传感器、第一径向力传感器、第二径向力传感器、第一轴向力传感器、第二轴向力传感器、电涡流位移传感器以及角度传感器;
21.所述第一扭力传感器设置在所述第一滑杆十字万向联轴器上,所述第二扭力传感器设置在所述第二滑杆十字万向联轴器上,所述第一径向力传感器设置在所述第一加载装置上,所述第二径向力传感器设置在所述第二加载装置上,所述第一轴向力传感器设置在
所述第三加载装置上,所述第二轴向力传感器设置在所述第四加载装置上,所述电涡流位移传感器设置在弹性联轴器试件加持处,所述角度传感器设置在所述导轨底盘上。
22.优选地,所述第一电缸底座通过调心滚子轴承与所述第一电缸连接;
23.两个所述第一电缸的作动端均利用过渡螺栓将所述第一径向力传感器和第二径向力传感器分别与各匹配的所述第一关节轴承固定,所述第一关节轴承的头部铰接于所述径向加载轴承座的加载端;
24.所述径向加载轴承座内部设置有双列角接触球轴承以及与双列角接触球轴承连接的第一传动轴,外部底面的凹槽内安装所述滑块,所述滑块安设在所述导轨底盘的轨道上。
25.优选地,所述直线运动轴承组件包括导轨安装法兰盘、导轨支座法兰盘、导轨轴、直线运动球轴承以及卡簧;
26.所述导轨轴与所述直线运动球轴承分别使用所述卡簧固定于所述导轨安装法兰盘与所述导轨支座法兰盘之间;
27.所述轴承座支撑架主体呈h状,在h状主体的横梁上设置有滚动直线滚针导轨支承。
28.优选地,所述第二电缸底座通过调心滚子轴承与所述第二电缸连接;
29.两个所述第二电缸的作动端均利用过渡螺栓将第一轴向力传感器和第二轴向力传感器分别与各匹配的所述第二关节轴承固定,所述第二关节轴承的头部铰接于所述轴向加载轴承座的加载端;
30.所述轴向加载轴承座内部设置有双列角接触球轴承以及与双列角接触球轴承连接的第二传动轴,通过螺栓与花键将第二传动轴与所述导轨轴安装法兰盘固定;
31.所述第三传动轴用于连接所述第二滑杆十字万向联轴器、所述固支轴承座组件和所述导轨支座法兰盘。
32.优选地,该疲劳实验装置还包括支撑系统;
33.所述支撑系统包括滑槽试验平台,用于各系统之间的调节与固定;
34.所述固支轴承座组件主要包括轴承座、双列深沟球轴承,其中双列深沟球轴承与所述第三传动轴连接,轴承座底部固支于所述滑槽试验平台,力与力矩均通过所述轴承座固支端进行平衡。
35.本技术第二方面一种联轴器的疲劳试验方法,该疲劳试验方法应用于上述任意一项所述的用于联轴器的疲劳试验装置,该疲劳试验方法主要步骤如下:
36.s1试件装夹:将弹性联轴器试件夹持于所述连接系统中,通过第一滑杆十字万向联轴器、第二滑杆十字万向联轴器以及传动轴组件,分别与驱动变频电机和负载变频电机连接,利用杠杆百分表对装置中的连接位置进行同轴度检测;
37.s2正式试验:将数据测量系统中传感器的扭力、径向力和角度进行清零,启动驱动变频电机至试验额定转速,再次对扭力值进行平衡清零;通过反馈的扭力信号控制负载变频电机使扭矩达到试验设定值,待传动系统稳定后,采集测量系统开始采集各项数据,并根据对传动系统在任务剖面的振动测试数据或仿真结果,选取相应工况下的外部激励状态对各加载设备进行控制;
38.s3信号采集:采集测量系统采集弹性联轴器试件的位移、扭力、径向力和角度数
据,将位移数据的时域信号进行傅里叶变换(fft)提取特征值,检测频率变化;
39.s4试验结束:试验到指定循环数而弹性联轴器试件未发生破坏停止实验;或在正常试验过程中,当弹性联轴器试件的固有频率下降0.5~1.5%时,即认为产生疲劳裂纹停止实验;或弹性联轴器试件裂纹未产生在危险部位,则该弹性联轴器试件作报废处理,停止实验。
40.优选地,所述选取相应工况下的外部激励状态对各加载设备进行控制包括如下步骤:
41.a)弹性联轴器径向振动疲劳试验工况
42.利用径向角向加载机构对弹性联轴器试件施加径向力,该径向力在控制系统中协调加载时需要满足在弹性联轴器试件处的力矩为零,其计算公式如下:
43.径向力方程:fr=f
12-f
11
44.力矩方程:f
11
(l
11
+l
12
)=f
12
l
12
45.将径向力方程带入力矩方程
46.f
11
(l
11
+l
12
)-(fr+f
11
)l
12
=0
47.可得
[0048][0049]
上述公式中,a为常数,其中f
11
、f
12
分别为径向角向加载机构中施加两个径向力,ι
11
、ι
12
分别为两个径向力至弹性联轴器试件的距离;
[0050]
则在加载控制系统中通过上述关系式输入径向力fr,即可实现对径向角向加载机构的协调加载,使弹性联轴器试件仅受径向力的激励作用,利用载荷谱可实现弹性联轴器径向载荷的动态施加;
[0051]
b)弹性联轴器角向振动疲劳试验工况
[0052]
角向疲劳是指弹性联轴器试件中弹性元件受绕z轴交变力矩(mz)影响下的疲劳性能,为实现弹性联轴器试件仅受角向激励影响,可利用径向角向加载机构对弹性联轴器试件施加大小相等、方向相反的载荷,其计算公式如下:
[0053]
径向力方程:f
11
=f
12
[0054]
力矩方程:mz=f
11
(l
11
+l
12
)-f
12
l
12
[0055]
可得
[0056]mz
=f
11
l
11
[0057]
上述公式中f
11
、f
12
分别为径向角向加载机构中施加两个径向力,ι
11
、ι
12
分别为两个径向力至弹性联轴器试件的水平距离,在施加一对力偶过程中,不会对弹性联轴器试件产生附加剪力,通过协调控制两个径向力的载荷和方向,可实现弹性联轴器试件角向疲劳载荷的动态施加;
[0058]
c)弹性联轴器轴向振动疲劳试验工况
[0059]
使用轴向加载机构施加大小相等、方向相同的载荷,其计算公式如下:
[0060]
轴向力方程:f
x
=f
21
+f
22
[0061]
力矩方程:f
21
l
21
=f
22
l
22
[0062]
其中
[0063]f21
=f
22
,l
21
=l
22
[0064]
上述公式中f
21
、f
22
分别为轴向加载机构中施加两个轴向力,ι
21
、ι
22
分别为两个轴向力至弹性联轴器试件中轴线的垂直距离。
[0065]
由以上技术方案可知,本技术提供一种用于联轴器的疲劳试验装置及疲劳试验方法具有以下有益效果:
[0066]
(1)本发明的疲劳试验装置在各工况加载过程中,通过部件间的相互作用形成自平衡机构,同时使用软连接的形式将驱动与负载装置连入试验系统,使驱动与负载装置仅传递扭矩而不受其他作用力的影响发生过载,保证了试验过程的安全性;
[0067]
(2)相较于直接改变驱动电机水平位置或角度的方式,本发明对被试件所受外部载荷采用两点协调加载的方式,使径向力及扭矩可单独作用于被试件,可更好地对被试件进行单一受力影响的疲劳性能评估;
[0068]
(3)本发明的疲劳试验装置可对弹性联轴器施加三个方向外部激励的作用,实现了工程应用中传动系统在弹性支撑下发生动态不对中振动状态的模拟,对于复杂的多方向耦合工况,结合本装置各机构能够独立加载的特点,通过各方向激励载荷的迭加能进行同相位、同比例或非同相位、非同比例等条件下的多轴振动疲劳性能试验研究;
[0069]
(4)利用疲劳试验装置调节灵活、控制系统精确的特点,在安装被试件过程中可预留径向、角向或轴向安装误差,使本发明亦可作为模拟联轴器故障的试验系统,通过采集典型的联轴器故障信号,应用于故障监测系统的研究。
附图说明
[0070]
为了更清楚地说明本技术实施例或现有技术中的技术方案,下面将对实施例中所需要使用的附图作简单地介绍,显而易见地,下面描述中的附图仅仅是本技术的一些实施例,对于本领域普通技术人员来讲,在不付出创造性劳动的前提下,还可以根据这些附图获得其他的附图。
[0071]
图1为本技术的用于联轴器的疲劳试验装置的立体结构示意图;
[0072]
图2为本技术径向角向加载机构、轴向加载机构以及部分传动轴组件的剖面示意图;
[0073]
图3为本技术的一种径向角向加载机构的结构示意图;
[0074]
图4为本技术的一种轴向加载机构的结构示意图;
[0075]
图5为本技术的一种直线运动轴承组件的结构示意图;
[0076]
图6为本技术的一种轴承座支撑架的结构示意图;
[0077]
图7为本技术的一种径向加载工况载荷传递示意图;
[0078]
图8为本技术的一种角向加载工况载荷传递示意图
[0079]
图9为本技术的一种轴向加载工况载荷传递示意图。
具体实施方式
[0080]
本技术第一方面提供一种用于联轴器的疲劳试验装置,该疲劳实验装置的结构可参阅图1所示的示意图,其具体结构包括:加载系统100、连接系统200以及数据测量系统400;所述加载系统100包括驱动变频电机101、径向角向加载机构110、轴向加载机构120、负
载变频电机102,在无负载的情况下所述径向角向加载机构110的水平方向与轴向加载机构120的水平方向垂直,且所述径向角向加载机构110用于对弹性联轴器试件300施加径向与角向的载荷,所述轴向加载机构120用于对弹性联轴器试件300施加轴向的载荷;所述连接系统200包括第一滑杆十字万向联轴器201、第二滑杆十字万向联轴器202以及传动轴组件,所述第一滑杆十字万向联轴器201通过传动轴组件分别与所述驱动变频电机101和弹性联轴器试件300连接,所述第二滑杆十字万向联轴器202通过传动轴组件分别与负载变频电机102和弹性联轴器试件300连接;所述数据测量系统400用于测量传动轴组件上的扭力、所述径向角向加载机构110上的径向力和角度、所述轴向加载机构120的轴向力以及弹性联轴器试件300的位移。
[0081]
径向角向加载机构110、轴向加载机构120以及部分传动轴组件配合后可参图2所示的示意图,其中所述径向角向加载机构110的具体结构可参考图3所示的示意图,具体结构包括第一加载装置、第二加载装置、第一关节轴承113、径向加载轴承座114、滑块115、导轨底盘116以及转盘轴承117;所述第一加载装置与第二加载装置的结构相同,均由第一电缸111和第一电缸底座112组成,所述第一电缸底座112用于支撑和固定所述第一电缸111;所述滑块115与所述径向加载轴承座114连接,所述滑块115设置有两组,每个所述滑块115与对应位置的所述径向加载轴承座114连接,且所述滑块115在力的作用下沿着所述导轨底盘116上表面的导轨滑动;所述转盘轴承117装设在所述导轨底盘116的下表面,用于所述导轨底盘116在力的作用下转动;所述径向加载轴承座114和所述第一关节轴承113设置有两组,每组中均为所述径向加载轴承座114均为单边同侧与所述第一关节轴承113连接,即所述径向角向加载机构110中的径向加载机构包括两个径向加载轴承座114,每个加载轴承座114都是在单边同侧连接对应的关节轴承和电缸,使用时在无负载的情况下两个所述第一关节轴承113相互平行且轴线与所述径向加载轴承座114的传动轴垂直,所述第一加载装置与其中一个所述第一关节轴承113连接,所述第二加载装置与另一个所述第一关节轴承113连接。所述第一电缸底座112通过调心滚子轴承与所述第一电缸111连接;两个所述第一电缸111的作动端均利用过渡螺栓将所述第一径向力传感器403和第二径向力传感器404分别与各匹配的所述第一关节轴承113固定,所述第一关节轴承113的头部铰接于所述径向加载轴承座114的加载端;所述径向加载轴承座114内部设置有双列角接触球轴承以及与双列角接触球轴承连接的第一传动轴211,外部底面的凹槽内安装所述滑块115,所述滑块115安设在所述导轨底盘116的轨道上。
[0082]
径向角向加载机构110的具体工作原理如下:径向角向加载机构110中的电缸组件为两套型号与连接方式均相同的电缸组件,通过滑块115、导轨底盘116与转盘轴承117的组合形式释放了径向与角向的自由度,当两个电缸同时施加大小相等、方向相反的力时,两套加载装置会发生相对于其连线中点的微小转动,则可视为作用于加载装置连线中点的一对力偶,使弹性联轴器试件300仅受到角向力矩的影响,当两个电缸分别施加一组力,使相对于弹性联轴器试件300连接位置的力矩为零,所受径向力为两个电缸加载值之差时,则可认为弹性联轴器试件300仅受到径向力作用。
[0083]
所述轴向加载机构120的结构可参阅图4所示的示意图,其具体结构包括第三加载装置、第四加载装置、第二关节轴承123、轴向加载轴承座124、轴承座支撑架125、直线运动轴承组件126以及固支轴承座组件(220),所述连接系统(200)包括第三传动轴(213);第三
加载装置和第四加载装置的结构相同,均由第二电缸121和第二电缸底座122组成,所述第二电缸底座122用于支撑和固定所述第二电缸121;所述轴向加载轴承座124的两侧各连接一个所述第二关节轴承123,无负载的情况下两个所述第二关节轴承123以及直线运动轴承组件126的轴线相互平行,所述第三加载装置与其中一个所述第二关节轴承123连接,所述第四加载装置与另一个所述第二关节轴承123连接;所述轴承座支撑架125设置有两个,分别位于所述轴向加载轴承座124的两侧,用于减小轴向运动时所述轴向加载轴承座124的摩擦力;所述第三传动轴213通过所述固支轴承座组件220进行径向轴向约束,所述固支轴承座组件220用于平衡径向力与力矩;所述直线运动轴承组件126装设在所述轴向加载轴承座124上,所述直线运动轴承组件126通过第三传动轴213与固支轴承座组件220连接,所述直线运动轴承组件126用于释放所述轴向加
[0084]
具体而言,所述直线运动轴承组件126的结构可参阅图5所示的示意图,具体包括导轨安装法兰盘1261、导轨支座法兰盘1262、导轨轴1263、直线运动球轴承1264以及卡簧1265;所述导轨轴1263与所述直线运动球轴承1264分别使用所述卡簧1265固定于所述导轨安装法兰盘1261与所述导轨支座法兰盘1262之间;所述轴承座支撑架125可参阅图6所示示意图,其主体呈h状,在h状主体的横梁上设置有滚动直线滚针导轨支承1251。另外,所述第二电缸底座122通过调心滚子轴承与所述第二电缸121连接;两个所述第二电缸121的作动端均利用过渡螺栓将第一轴向力传感器405和第二轴向力传感器406分别与各匹配的所述第二关节轴承123固定,所述第二关节轴承123的头部铰接于所述轴向加载轴承座124的加载端;所述轴向加载轴承座124内部设置有双列角接触球轴承以及与双列角接触球轴承连接的第二传动轴212,通过螺栓与花键将第二传动轴212与所述导轨轴安装法兰盘1261固定;所述第三传动轴213用于连接所述第二滑杆十字万向联轴器202、所述固支轴承座组件220和所述导轨支座法兰盘1262。
[0085]
所述轴向加载机构120中的电缸组件为两套型号与连接方式均相同的电缸组件,通过两个电缸的同步加载实现对弹性联轴器试件300轴向载荷的施加,同时由于直线运动轴承组件126的使用,在该机构后段的固支轴承座组件220与第二滑杆十字万向联轴器202均不受轴向力的影响。
[0086]
进一步说明所述数据测量系统包括第一扭力传感器401、第二扭力传感器402、第一径向力传感器403、第二径向力传感器404、第一轴向力传感器405、第二轴向力传感器406、电涡流位移传感器407以及角度传感器408;所述第一扭力传感器401设置在所述第一滑杆十字万向联轴器201上,所述第二扭力传感器402设置在所述第二滑杆十字万向联轴器202上,所述第一径向力传感器403设置在所述第一加载装置上,所述第二径向力传感器404设置在所述第二加载装置上,所述第一轴向力传感器405设置在所述第三加载装置上,所述第二轴向力传感器406设置在所述第四加载装置上,所述电涡流位移传感器407设置在弹性联轴器试件300加持处,所述角度传感器408设置在所述导轨底盘116上。
[0087]
该疲劳实验装置还包括支撑系统500;所述支撑系统500包括滑槽试验平台501,用于各系统之间的调节与固定。径向角向加载机构110在对弹性联轴器试件300施加径向力时,此径向力会通过直线运动轴承组件126传递至机构后段,为保证试验装置不发生大变形偏转影响试验结果,在装置中需安装一组固定组件将所述第三传动轴213进行径向轴向约束,故在机构后段设置了一组固支轴承座组件220用于平衡径向力与力矩,所述固支轴承座
组件220主要包括轴承座221、双列深沟球轴承222,其中双列深沟球轴承222与所述第三传动轴213连接,轴承座221底部固支于滑槽试验平台501,力与力矩均通过轴承座221固支端进行平衡。
[0088]
力与力矩均的平衡关系如下:
[0089]
(1)径向加载工况的载荷示意图可参考图7所示的示意图,该工况下装置平衡方程为:
[0090]
力平衡公式:f
31
=f
12-f
11
[0091]
力矩平衡公式:f
12
(l
12
+l
31
)-f
11
(l
11
+l
12
+l
31
)=m
31
[0092]f12
(l
12
+l
31
)-f
11
(l
11
+l
12
+l
31
)=m
31
[0093]
因施加径向力时需保证弹性联轴器处的力矩为零,即
[0094]f12
l
12-f
11
(l
11
+l
12
)=0
[0095]
可得
[0096]
(f
12-f
11
)l
31
=m
31
[0097]
上述公式中,f
11
、f
12
分别为径向角向加载机构中施加两个径向力,ι
11
、ι
12
分别为两个径向力至弹性联轴器试件的距离,m
31
为固支轴承座组件的力矩,ι
31
为固支轴承座组件的力矩至弹性联轴器试件的距离。
[0098]
(2)角向加载工况的载荷示意图可参考图8所示的示意图,径向角向加载机构110在施加一对力偶时,径向力为一对平衡力,力矩则通过轴向加载机构120中的两个电缸进行平衡,该工况下装置平衡方程为:
[0099]
力平衡公式:f
11
=f
12
,f
21
=f
22
[0100]
力矩平衡公式:f
11
l
11
=2f
21
l
21
[0101]
在图8中,f
11
、f
12
分别为径向角向加载机构中施加两个径向力,ι
11
、ι
12
分别为两个径向力至弹性联轴器试件的距离;f
21
、f
22
分别为轴向加载机构中施加两个轴向力,ι
21
、ι
22
分别为两个轴向至弹性联轴器试件的距离。
[0102]
(3)轴向加载工况的载荷示意图可参考图9所示的示意图,轴向加载机构120在施加轴向力时,利用双列角接触球轴承能够传递较大轴向力的特点,使该载荷传递至径向角向加载机构110中的导轨底盘116,并通过固支于支撑平台的转盘进行平衡。该工况下装置平衡方程为:
[0103]
力平衡公式:f
21
+f
22
=f2[0104]
f2=f1[0105]
可得
[0106]
力矩平衡公式:f
21
l
21
=f
22
l
22
[0107]
上述公式中,f
21
、f
22
分别为轴向加载机构中施加两个轴向力,ι
21
、ι
22
分别为两个轴向至弹性联轴器试件的距离,f2为f
21
和f
22
的合力,f1为第一传动轴所受的力。
[0108]
本技术第二方面提供一种联轴器的疲劳试验方法,该疲劳试验方法应用于上述任意一项所述的用于联轴器的疲劳试验装置,该疲劳试验方法主要步骤如下:
[0109]
s1试件装夹:将弹性联轴器试件夹持于所述连接系统中,通过第一滑杆十字万向联轴器、第二滑杆十字万向联轴器以及传动轴组件,分别与驱动变频电机和负载变频电机连接,利用杠杆百分表对装置中的连接位置进行同轴度检测。
[0110]
另外试验系统安装完成后,在弹性联轴器试件的水平与垂直位置安装电涡流位移传感器,导轨底盘的中心安装角度传感器分别用于测量位移与旋转角度的信号
[0111]
s2正式试验:将数据测量系统中传感器的扭力、径向力和角度进行清零,启动驱动变频电机至试验额定转速,再次对扭力值进行平衡清零;通过反馈的扭力信号控制负载变频电机使扭矩达到试验设定值,待传动系统稳定后,采集测量系统开始采集各项数据,并根据对传动系统在任务剖面的振动测试数据或仿真结果,选取相应工况下的外部激励状态对各加载设备进行控制;
[0112]
s3信号采集:采集测量系统采集弹性联轴器试件的位移、扭力、径向力和角度数据,将位移数据的时域信号进行傅里叶变换(fft)提取特征值,检测频率变化。
[0113]
电涡流位移传感器采集的位移数据为时域信号,为能够更加清晰地对振动疲劳试验进行监测,在控制系统中需将时域信号进行傅里叶变换(fft)提取特征值,监测频率变化;通过第一扭力传感器与第二扭力传感器的测量值可得出在不同试验工况条件下弹性联轴器试件对传动效率的影响;对于在径向角向加载机构加载过程中会发生大变形的弹性联轴器试件可根据导轨底盘上的角度传感器测量值对载荷进行修正。
[0114]
s4试验结束:试验到指定循环数而弹性联轴器试件300未发生破坏停止实验;或在正常试验过程中,当弹性联轴器试件的固有频率下降0.5~1.5%时(优选1%),即认为产生疲劳裂纹停止实验;或弹性联轴器试件裂纹未产生在危险部位,则该弹性联轴器试件作报废处理,停止实验。
[0115]
在弹性联轴器实验之前还可以将弹性联轴器试件安装至固定工装中,使用锤击法单独测试联轴器结构的固有频率,记录各方向频响曲线;根据模态试验的夹持方式,在有限元软件中建立联轴器动力学模型,进行模态分析,提取共振频率与振型,依据仿真计算与模态试验的对比结果,验证有限元模型的准确性,最后将所建立的联轴器模型接入传动系统的有限元模型中进行分析,确定结构危险部位。
[0116]
所述选取相应工况下的外部激励状态对各加载设备进行控制包括如下步骤:
[0117]
a)弹性联轴器径向振动疲劳试验工况
[0118]
利用径向角向加载机构对弹性联轴器试件施加径向力,该力在控制系统中协调加载时需要满足在弹性联轴器试件处的力矩为零,其计算公式如下:
[0119]
径向力方程:fr=f
12-f
11
[0120]
力矩方程:f
11
(l
11
+l
12
)=f
12
l
12
[0121]
将径向力方程带入力矩方程
[0122]f11
(l
11
+l
12
)-(fr+f
11
)l
12
=0
[0123]
可得
[0124][0125]
上述公式中,a为常数,其中f
11
、f
12
分别为径向角向加载机构中施加两个径向力,ι
11
、ι
12
分别为两个径向力至弹性联轴器试件的距离;
[0126]
则在加载控制系统中通过上述关系式输入径向力fr,即可实现对径向角向加载机构的协调加载,使弹性联轴器试件仅受径向力的激励作用,利用载荷谱可实现弹性联轴器径向载荷的动态施加;
[0127]
b)弹性联轴器角向振动疲劳试验工况
[0128]
角向疲劳是指弹性联轴器试件中弹性元件受绕z轴交变力矩(mz)影响下的疲劳性能,为实现弹性联轴器试件仅受角向激励影响,可利用径向角向加载机构对弹性联轴器试件施加大小相等、方向相反的载荷,其计算公式如下:
[0129]
径向力方程:f
11
=f
12
[0130]
力矩方程:mz=f
11
(l
11
+l
12
)-f
12
l
12
[0131]
可得
[0132]mz
=f
11
l
11
[0133]
上述公式中f
11
、f
12
分别为径向角向加载机构中施加两个径向力,ι
11
、ι
12
分别为两个径向力至弹性联轴器试件的水平距离,在施加一对力偶过程中,不会对弹性联轴器试件产生附加剪力,通过协调控制两个径向力的载荷和方向,可实现弹性联轴器试件角向疲劳载荷的动态施加;
[0134]
c)弹性联轴器轴向振动疲劳试验工况
[0135]
使用轴向加载机构施加大小相等、方向相同的载荷,其计算公式如下:
[0136]
轴向力方程:f
x
=f
21
+f
22
[0137]
力矩方程:f
21
l
21
=f
22
l
22
[0138]
其中
[0139]f21
=f
22
,l
21
=l
22
[0140]
上述公式中f
21
、f
22
分别为轴向加载机构中施加两个轴向力,ι
21
、ι
22
分别为两个轴向力至弹性联轴器试件中轴线的垂直距离。
[0141]
以上结合具体实施方式和范例性实例对本技术进行了详细说明,不过这些说明并不能理解为对本技术的限制。本领域技术人员理解,在不偏离本技术精神和范围的情况下,可以对本技术技术方案及其实施方式进行多种等价替换、修饰或改进,这些均落入本技术的范围内。本技术的保护范围以所附权利要求为准。