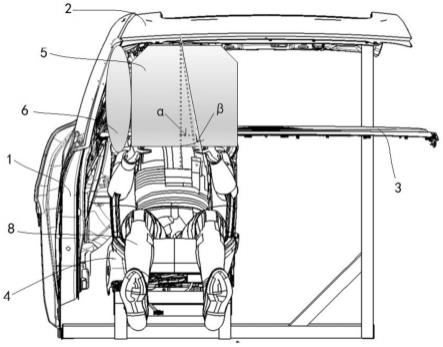
1.本发明涉及车辆可靠性试验技术领域,更具体地,涉及一种顶棚安全气囊和侧气帘耦合点爆试验装置及试验方法。
背景技术:2.目前国内汽车,乃至世界汽车,副驾驶位安全气囊往往会选择安装在仪表板上的布置方案,选择顶棚安全气囊的车型非常少。副驾驶位的安全气囊,不论是传统方案仪表板气囊,还是新型的顶棚安全气囊,都具备保护副驾驶位乘员的作用,所以针对新的在副驾驶位的顶棚安全气囊的试验验证方法,目前都是参考原来的布置在仪表板上的安全气囊的经验来确定。但是因为两者的紧固方式不同,布置位置不同,与内饰件的配合关系也差别非常大,所以开发顶棚安全气囊的试验方法和装置,需要根据其自身的独特属性,建立专属于顶棚安全气囊的试验方法和装置。
3.目前ciasi的碰撞测试机构,已经针对国内的碰撞测试方法进行了更新,原来64公里小偏置的碰撞只撞击主驾侧进行碰撞测试,后续规则会更新到随机选择主驾侧还是副驾侧进行碰撞测试。撞击副驾侧的碰撞试验,需要副驾驶位的正面气囊和侧气帘同时点爆,保护乘员的头部安全。传统的安装在仪表板上的副驾驶位安全气囊,侧气帘点爆后a柱向外推出,对其影响很小,故而没有安排试验进行针对仪表板气囊和侧气帘的耦合试验进行验证;但是新的顶棚安全气囊固定在顶盖横梁,顶棚遮阳板区域,顶棚安全气囊点爆可能会引发遮阳板转动,侧气帘点爆a柱会向外推出,顶棚安全气囊容易受到a柱的推动,遮阳板可能会影响侧气帘姿态,因此需要通过发明新的实验方法和装置来提前验证风险。
技术实现要素:4.本发明针对现有技术中存在的技术问题,提供一种顶棚安全气囊和侧气帘耦合点爆试验装置及试验方法,填补了顶棚安全气囊与侧气帘配合的试验空白;试验装置可反复使用,缩减了试验验证的成本。
5.根据本发明的第一方面,提供了一种顶棚安全气囊和侧气帘耦合点爆试验装置,包括仿形结构件、顶棚安全气囊、侧气帘和点爆控制单元,所述仿形结构件模拟被测车型的车内结构,所述顶棚安全气囊和侧气帘模拟被测车型的安装方式安装在仿形结构件内,顶棚安全气囊和侧气帘的点爆线束分别与所述点爆控制单元连接,所述点爆控制单元与外部信号源通信连接。
6.在上述技术方案的基础上,本发明还可以作出如下改进。
7.可选的,所述仿形结构件包括被测车型的右侧围钣金、顶盖钣金和安装型材,所述右侧围钣金和顶盖钣金模拟被测车型的装配关系固定安装在所述安装型材的外侧,所述安装型材的内侧还设有多个安装位,被测车型的仪表板、副驾驶位座椅、顶棚安全气囊、遮阳板、侧气帘、a/b/c立柱上下饰板、前后排安全拉手按照被测车型的装配关系安装在所述安装型材内侧的安装位上,所述顶棚安全气囊和侧气帘的点爆线束引出、并连接到所述点爆
控制单元的信号输出端。
8.可选的,试验装置还包括分布在仿形结构件外侧的图像采集单元,用于采集试验过程中多个视角的图像信息。
9.可选的,所述图像采集单元包括分别设置在仿形结构件的x向和y向的多个相机,多个所述相机用于采集试验过程中多个视角的试验图像。
10.可选的,所述仿形结构件上设有相机定位参考点,每个相机相对于所述参考点的坐标位置固定设置。
11.根据本发明的第二方面,基于上述的一种顶棚安全气囊和侧气帘耦合点爆试验装置的试验方法,提供一种顶棚安全气囊和侧气帘耦合点爆试验方法,包括:
12.选择试验环境温度类型,将试验装置置于选定的温度环境中直到达到预设的静置时间,根据被测车型的安全气囊点爆策略向点爆控制单元输出规定的顶棚安全气囊和侧气帘的点爆时刻;
13.在预设的点爆时刻,同时点爆顶棚安全气囊和侧气帘,通过多个视角的图像信息获取顶棚安全气囊、侧气帘、仿形结构件和/或周边环境件的状态信息;
14.根据顶棚安全气囊、侧气帘、仿形结构件和/或周边环境件的状态信息分析试验结果是否合格。
15.可选的,所述试验环境温度类型至少包括高温环境、常温环境和低温环境。
16.可选的,通过多个视角的图像信息获取顶棚安全气囊的状态信息,包括:
17.根据图像信息提取顶棚安全气囊的缝纫线并计算得到所述缝纫线的曲率,将所述缝纫线的曲率与预设的曲率阈值相比对,若所述缝纫线的曲率不大于预设的曲率阈值,则判断顶棚安全气囊已充满。
18.可选的,所述根据顶棚安全气囊、侧气帘、仿形结构件和/或周边环境件的状态信息分析试验结果是否合格,包括:
19.根据顶棚安全气囊的展开状态判断顶棚安全气囊有无破损,根据侧气帘的展开状态判断侧气帘有无破损;
20.根据顶棚安全气囊的展开状态沿时间轴的变化得到顶棚安全气囊的展开速度,根据侧气帘的展开状态沿时间轴的变化得到侧气帘的展开速度;根据对应试验环境温度类型下的展开速度阈值,判断顶棚安全气囊的展开速度和/或侧气帘的展开速度是否合格。
21.可选的,所述根据顶棚安全气囊、侧气帘、仿形结构件和/或周边环境件的状态信息分析试验结果是否合格,还包括:
22.根据顶棚安全气囊的展开速度和侧气帘的展开速度判断侧气帘是否先于顶棚安全气囊展开;
23.在顶棚安全气囊与侧气帘的展开状态下,基于整车坐标系,以副驾驶位座椅的z向中心线为参考铅垂线,以顶棚安全气囊的上边缘中心点和下边缘的中心点连线作为考核线,计算参考铅垂线与考核线之间的夹角得到考核角度,若所述考核角度在角度合格阈值范围内,则判断顶棚安全气囊展开方向合格;若所述考核角度在角度偏差阈值范围内,则判断顶棚安全气囊展开方向可接受;若所述考核角度不在角度合格阈值范围和角度偏差阈值范围内,则判断顶棚安全气囊5展开方向不合格。
24.本发明提供的一种顶棚安全气囊和侧气帘耦合点爆试验装置及试验方法,通过将
顶棚安全气囊、侧气帘和车内环境件按照被测车型的装配关系装配到仿形结构件上,以模拟被测车型的车内环境。通过外部信号源的安全气囊点爆策略向点爆控制单元输出顶棚安全气囊和侧气帘同时点爆的控制信号,实现车内顶棚安全气囊和侧气帘同时点爆的场景模拟,可以实现顶棚安全气囊和侧气帘配合一起点爆的耦合静态点爆试验。通过该试验装置进行模拟试验,可在设计阶段演示各种顶棚安全气囊设计方案与车辆环境的兼容性,以预知各种顶棚安全气囊设计方案可能存在的安全隐患,填补了顶棚安全气囊与侧气帘配合的试验空白。利用顶棚安全气囊和侧气帘的耦合子系统试验,可以提前验证整车在64公里小偏置碰撞后的配合效果,且本试验验证的成本远远低于实车验证测试的成本,试验装置可反复使用,进一步缩减了试验验证的成本。通过本试验装置与试验方法进行顶棚安全气囊和侧气帘耦合点爆试验,相比于整车碰撞试验,试验周期更短,缩减了设计开发周期,减小了整车开发时间成本。
附图说明
25.图1为本发明提供的一种顶棚安全气囊和侧气帘耦合点爆试验装置侧视图;
26.图2为本发明提供的一种顶棚安全气囊和侧气帘耦合点爆试验装置主视图;
27.图3为本发明提供的一种顶棚安全气囊和侧气帘耦合点爆试验装置中某一实施例中相机布设位置示意图;
28.图4为本发明实施例中顶棚安全气囊充满状态与未充满状态对比示意图;
29.图5为本发明实施例中顶棚安全气囊展开方向示意图;
30.图6为本发明提供的一种顶棚安全气囊和侧气帘耦合点爆试验方法流程图。
31.附图中,各标号所代表的部件列表如下:
32.1、右侧围钣金,2、顶盖钣金,3、安装型材,4、副驾驶位座椅,5、顶棚安全气囊5,501、缝纫线,6、侧气帘,7、相机,8、假人。
具体实施方式
33.下面结合附图和实施例,对本发明的具体实施方式作进一步详细描述。以下实施例用于说明本发明,但不用来限制本发明的范围。
34.图1为本发明提供的一种顶棚安全气囊和侧气帘耦合点爆试验装置的侧视图,图2为本发明提供的一种顶棚安全气囊和侧气帘耦合点爆试验装置的主视图。如图1及图2所示,本发明提供的一种顶棚安全气囊和侧气帘耦合点爆试验装置,包括仿形结构件、顶棚安全气囊5、侧气帘6和点爆控制单元,所述仿形结构件模拟被测车型的车内结构,所述顶棚安全气囊5和侧气帘6模拟被测车型的安装方式安装在仿形结构件内,顶棚安全气囊5和侧气帘6的点爆线束分别与所述点爆控制单元连接,所述点爆控制单元与外部信号源通信连接。由于顶棚安全气囊5以及侧气帘6作为车辆发生危险碰撞时的安全保护措施,在正常状态下,其隐藏与车体内,不必展示出来,因此图1及图2中未示出顶棚安全气囊5以及侧气帘6。按照整车装配关系,在正常状态下,顶棚安全气囊5收缩设置在车辆副驾驶座上前方的结构件内,侧气帘6则收缩设置于车辆副驾驶位右侧上方的结构件内,本实施例基于这样的装配关系将顶棚安全气囊5以及侧气帘6收缩安装在仿形结构件上,由于其收缩后体积较小,因此图1及图2中未将其展示出。
35.可以理解的是,基于背景技术中的缺陷,本发明实施例提出了一种顶棚安全气囊和侧气帘耦合点爆试验装置。通过将顶棚安全气囊5、侧气帘6和车内环境件按照被测车型的装配关系装配到仿形结构件上,以模拟被测车型的车内环境。在使用本试验装置进行试验时,通过外部信号源的安全气囊点爆策略向点爆控制单元输出顶棚安全气囊5和侧气帘6同时点爆的控制信号,实现车内顶棚安全气囊5和侧气帘6同时点爆的场景模拟,可以实现顶棚安全气囊5和侧气帘6配合一起点爆的耦合静态点爆试验。通过该试验装置进行模拟试验,可在设计阶段演示各种顶棚安全气囊5设计方案与车辆环境的兼容性,以预知各种顶棚安全气囊5设计方案可能存在的安全隐患,填补了顶棚安全气囊5与侧气帘6配合的试验空白。利用顶棚安全气囊5和侧气帘6的耦合子系统试验,可以提前验证整车在64公里小偏置碰撞后的配合效果,且采用本试验装置验证的成本远远低于实车验证测试的成本,本试验装置可反复使用,进一步缩减了试验验证的成本。通过本试验装置进行顶棚安全气囊和侧气帘耦合点爆试验,相比于整车碰撞试验,试验周期更短,缩减了设计开发周期,减小了整车开发时间成本。
36.在一种可能的实施例方式中,如图1及图2所示,所述仿形结构件包括被测车型的右侧围钣金1、顶盖钣金2和安装型材3,所述右侧围钣金1和顶盖钣金2模拟被测车型的装配关系固定安装在所述安装型材3的外侧,所述安装型材3的内侧还设有多个安装位,被测车型的仪表板、副驾驶位座椅4、顶棚安全气囊5、遮阳板、侧气帘6、a/b/c立柱上下饰板、前后排安全拉手按照被测车型的装配关系安装在所述安装型材3内侧的安装位上,所述顶棚安全气囊5和侧气帘6的点爆线束引出、并连接到所述点爆控制单元的信号输出端。
37.可以理解的是,本实施例中提取了原开发车型的完整右侧围钣金1和完整顶盖钣金2,以更加准确地模拟被测车型的车内环境。在右侧围钣金1和顶盖钣金2的结构基础上,配合开发用于支撑右侧围钣金1和顶盖钣金2的安装型材3。其中安装型材3开发时,除了考虑结构支撑性,还需针对开发的被测车型的各种车内环境件(例如内饰件)的匹配安装位置,需要考虑预留空间以及多个安装位。本试验装置涉及到的环境件主要是与顶棚安全气囊5和侧气帘6相关联的部件,例如仪表板、副驾驶位座椅4、遮阳板、a/b/c立柱上下饰板、前后排安全拉手等。安装型材3的优化设计,降低了整体的占用空间和重量,同时匹配车内各环境件,使顶棚安全气囊5与侧气帘6点爆后,能更加贴合实车的车内环境,使试验结果更加准确。
38.在一种可能的实施例方式中,试验装置还包括分布在仿形结构件外侧的图像采集单元,用于采集试验过程中多个视角的图像信息。
39.可以理解的是,在试验过程中可通过对多个视角的图像信息进行特征提取并分析得到试验结果。获得的图像信息还可记录试验过程,便于后续回放并分析试验不合格原因,利于后续对被测车型设计方案的改进。
40.在一种可能的实施例方式中,所述图像采集单元包括分别设置在仿形结构件的x向和y向的多个相机7,多个所述相机7用于采集试验过程中多个视角的试验图像。
41.如图3所示为其中一种优选的实施例中对顶棚安全气囊和侧气帘耦合点爆试验装置中相机7布设位置示意图,此图的视角为俯视视角。如图3所示,中间框代表本实施例的试验装置,基于整车坐标系,沿车辆x向在车前车后分别设置相机7,以采集试验过程中正面视角和背面视角的图像信息;沿车辆y向在车辆副驾驶位一侧设置相机7,以采集试验过程中
侧面视角的图像信息,通过各个视角连续的图像信息变化,记录整个试验过程,从而对试验结果进行分析,也使得可通过图像信息追溯试验失败原因。
42.在一种可能的实施例方式中,所述仿形结构件上设有相机定位参考点,每个相机7相对于所述参考点的坐标位置固定设置。
43.由于在采用本试验装置进行试验时,可能涉及到需对顶棚安全气囊5与侧气帘6的多个装配设计方案进行验证,因此可能在完成一轮试验验证后需要拆卸下测试完成的顶棚安全气囊5和/或侧气帘6,以进行下一轮试验的顶棚安全气囊5与侧气帘6的装配。为了获得更加准确与可靠的试验结果以及便于对各个设计方案的试验过程进行比对,最好是在同一个视角进行图像信息采集。在这个过程中,为了防止顶棚安全气囊5和/侧气帘6的拆装过程中由于仿形结构件发生位移(位置变化或者角度偏转)导致图像信息采集视角不一致,如图3所示,根据经验在仿形结构件上设置一个参考点,通过这个参考点的坐标来计算各个相机7与参考点之间的相位位置,每次测试前确认各个相机7与参考点的相对位置,即可保证每次试验时采集图像信息的视角相同,增加试验的可靠性。参考点的选择可根据试验条件灵活选择,例如副驾驶作为的车窗位置、前挡风玻璃位置等。例如,图3中,将副驾驶位的车窗上某一点作为参考点,假设参考点、各相机位于整车坐标系内的同一xy平面,即假设参考点、各相机位于同一高度,假设在xy平面内参考点坐标为(0,0,),侧视角相机沿y向到参考点的距离为cmm,沿x向到参考点的距离为dmm,因此侧视角相机到参考点的相对坐标为(c,d);正面视角相机沿y向到参考点的距离为b mm,沿x向到参考点的距离为a mm,因此侧视角相机到参考点的相对坐标为(b,a);背面视角相机沿y向到参考点的距离为e mm,沿x向到参考点的距离为f mm,因此侧视角相机到参考点的相对坐标为(e,f)。同理的,若参考点、各相机位于并不位于同一平面,各相机相对于参考点进行坐标计算基于三维坐标,其计算方式与上述二维平面内相对坐标计算方式雷同,此处不再赘述。
44.基于上述的一种顶棚安全气囊和侧气帘耦合点爆试验装置,本实施例还提供一种顶棚安全气囊和侧气帘耦合点爆试验方法。如图6所示为本实施例的试验方法流程图,本试验方法包括:
45.选择试验环境温度类型,将试验装置置于选定的温度环境中直到达到预设的静置时间,根据被测车型的安全气囊点爆策略向点爆控制单元输出规定的顶棚安全气囊5和侧气帘6的点爆时刻;
46.在预设的点爆时刻,同时点爆顶棚安全气囊5和侧气帘6,通过多个视角的图像信息获取顶棚安全气囊5、侧气帘6、仿形结构件和/或周边环境件的状态信息;
47.根据顶棚安全气囊5、侧气帘6、仿形结构件和/或周边环境件的状态信息分析试验结果是否合格。
48.可以理解的是,通过本实施例提供的顶棚安全气囊和侧气帘耦合点爆试验方法,可以通过外部信号源的安全气囊点爆策略向点爆控制单元输出顶棚安全气囊5和侧气帘6同时点爆的控制信号,实现各种环境温度条件下车内顶棚安全气囊5和侧气帘6同时点爆的场景模拟,可以实现顶棚安全气囊5和侧气帘6配合一起点爆的耦合静态点爆试验。通过该模拟试验,可在设计初期阶段演示各种顶棚安全气囊5设计方案与车辆环境的兼容性,以预知各种顶棚安全气囊5设计方案可能存在的安全隐患,填补了顶棚安全气囊5与侧气帘6配合的试验空白。
49.在一种可能的实施例方式中,所述试验环境温度类型至少包括高温环境、常温环境和低温环境。例如,高温环境温度为85℃,常温环境为23℃,低温环境为-35℃。通过进行不同环境温度类型下的试验,可模拟车辆在不同气候条件下的性能,例如研究顶棚安全气囊5和侧气帘6在不同气候环境下同时点爆的可靠性,以开发出更适合某类气候条件的顶棚安全气囊5与侧气帘6的装配方案。本实施例中,依次将仪表板、副驾驶位座椅4、顶棚安全气囊5、遮阳板和右侧侧气帘6、a/b/c立柱上下饰板、前后排安全拉手按照车型的装配关系,正确装配到仿形结构件的安装型材3上,副驾驶位座椅4上放置模拟假人8;其中顶棚安全气囊5和右侧侧气帘6需要各自单独引出点爆线束连接到点爆控制单元;根据试验需求,选择高温85℃、常温23℃、低温-35℃中的某一预期试验环境温度;整个装配好顶棚安全气囊5、侧气帘6和车辆内饰件的试验装置(模拟车身)放入对应温度环境中,保存4小时;保存时间满4小时后,根据车辆开发目前的安全气囊点爆策略,输入规定的顶棚安全气囊5和右侧侧气帘6的点爆时刻,进行点爆,以完成试验。
50.在一种可能的实施例方式中,通过多个视角的图像信息获取顶棚安全气囊5的状态信息,包括:
51.根据图像信息提取顶棚安全气囊5的缝纫线501并计算得到所述缝纫线501的曲率,将所述缝纫线501的曲率与预设的曲率阈值相比对,若所述缝纫线501的曲率不大于预设的曲率阈值,则判断顶棚安全气囊5已充满。
52.如图4所示,从侧视角展示的顶棚安全气囊5充满状态和未充满状态的对比示意图。图4(a)中,三角形部分为顶棚安全气囊5充满的状态,连接三角形内角的线条为气囊的缝纫线501,当顶棚安全气囊5充满的状态下,由于气囊充气膨胀,缝纫线501受到气囊内部高压的作用,被绷直形成近似于直线的状态。而图4(b)中,气囊未充满的状态下,由于气囊内部压力不足以将缝纫线501绷直形成直线,因此缝纫线501呈不规则的弯曲状态。通过对点爆后顶棚安全气囊5的图像进行缝纫线501的特征提取,通过判断缝纫线501的曲率是否合格,即可判断缝纫线501是否绷直,从而判断顶棚安全气囊5是否充满。
53.在一种可能的实施例方式中,所述根据顶棚安全气囊5、侧气帘6、仿形结构件和/或周边环境件的状态信息分析试验结果是否合格,包括:
54.根据顶棚安全气囊5的展开状态判断顶棚安全气囊5有无破损,根据侧气帘6的展开状态判断侧气帘6有无破损;
55.根据顶棚安全气囊5的展开状态沿时间轴的变化得到顶棚安全气囊5的展开速度,根据侧气帘6的展开状态沿时间轴的变化得到侧气帘6的展开速度;根据对应试验环境温度类型下的展开速度阈值,判断顶棚安全气囊5的展开速度和/或侧气帘6的展开速度是否合格。
56.可以理解的是,在进行顶棚安全气囊5与侧气帘6进行同步点爆的试验中,需首先判断顶棚安全气囊5以及侧气帘6展开的有效性,若二者有其一未正常展开,均判定试验结果为不合格。基于正常展开状态才进一步判断顶棚安全气囊5是否充满。如图4所示可以看到,当顶棚安全气囊5展开状态下,其形状特征明显,因此可通过对图像信息进行气囊的特征提取,通过判断顶棚安全气囊5和/或侧气帘6的面积和/或形状,从而判断顶棚安全气囊5和/或侧气帘6是否正常展开。
57.由于对试验过程进行了图像信息采集,连续的图像信息记载了顶棚安全气囊5和
侧气帘6的展开状态随时间轴变化的过程,因此可通过对连续的图像信息进行分析,计算得到气囊的展开速度。
58.本实施例中,判断顶棚安全气囊5完全展开的条件,高温85℃试验温度下,需要满足9ms内露白,50ms内充满的要求;常温23℃试验温度下,需要满足10ms内露白,55ms内充满的要求;低温-35℃试验温度下,需要满足12ms内露白,65ms内充满的要求。
59.因为顶棚安全气囊5与侧气帘6是作为车辆碰撞过程中对车内人员的生命安全进行保障的安全措施,其展开速度极大地决定了这个安全措施的有效性,因此评估顶棚安全气囊5与侧气帘6的展开速度具有重要意义。
60.在一种可能的实施例方式中,所述根据顶棚安全气囊5、侧气帘6、仿形结构件和/或周边环境件的状态信息分析试验结果是否合格,还包括:
61.根据顶棚安全气囊5的展开速度和侧气帘6的展开速度判断侧气帘6是否先于顶棚安全气囊5展开;
62.在顶棚安全气囊5与侧气帘6的展开状态下,基于整车坐标系,以副驾驶位座椅4的z向中心线为参考铅垂线,以顶棚安全气囊5的上边缘中心点和下边缘的中心点连线作为考核线,计算参考铅垂线与考核线之间的夹角得到考核角度,若所述考核角度在角度合格阈值范围内,则判断顶棚安全气囊5展开方向合格;若所述考核角度在角度偏差阈值范围内,则判断顶棚安全气囊5展开方向可接受;若所述考核角度不在角度合格阈值范围和角度偏差阈值范围内,则判断顶棚安全气囊5展开方向不合格。如图5所示,本实施例中设置角度合格阈值α为10
°
、角度偏差阈值β为15
°
,若测得的考核角度不大于10
°
,则判定顶棚安全气囊5展开方向合格;若测得的考核角度大于10
°
且不大于15
°
,则根据实际情况判断顶棚安全气囊5展开方向可接受;若测得的考核角度大于15
°
,则判定考核角度不合格,进一步判断顶棚安全气囊5展开方向不合格。
63.可以理解的是,本实施例涉及的顶棚安全气囊5与侧气帘6同时点爆的情况大多见于车辆受到侧向撞击的情况。而车辆在行驶过程中受到侧向撞击的时候,对人体的伤害首先来自于车辆侧向,然后由于惯性,人员受到来自于车辆正面的撞击伤害,因此需保证侧气帘6具有相对于顶棚安全气囊5更快的反应速度,以达到对车内人员可靠的保护效果。由于侧气帘6先于顶棚安全气囊5展开后,为了达到更加全面的保护效果,侧气帘6与顶棚安全气囊5紧密贴合、存在一定的空间干涉,侧气帘6膨胀会将顶棚安全气囊5朝向主驾驶位推出。为了保障副驾驶位座椅4前方的顶棚安全气囊5达到可靠的保护效果,需对顶棚安全气囊5展开后的偏离角度进行限制,即通过本实施例的方法考验顶棚安全气囊5的展开方向。
64.根据周边环境件的状态信息分析试验结果是否合格,用于判断顶棚安全气囊5和侧气帘6的周边环境件的可靠性。试验过程中,周边环境件合格的条件需满足:无内饰件出现脱落、破碎和飞溅,周边环境件不导致顶棚安全气囊5和右侧侧气帘6的卡滞,例如遮阳板不应阻碍顶棚安全气囊5的展开、遮阳板不应与侧气帘6发生干涉等。
65.本发明提供的一种顶棚安全气囊和侧气帘耦合点爆试验装置及试验方法,通过将顶棚安全气囊5、侧气帘6和车内环境件按照被测车型的装配关系装配到仿形结构件上,以模拟被测车型的车内环境,相比于实车试验,明显降低了实车试验占用空间和重量,有利于试验的反复进行。通过外部信号源的安全气囊点爆策略向点爆控制单元输出顶棚安全气囊5和侧气帘6同时点爆的控制信号,实现车内顶棚安全气囊5和侧气帘6同时点爆的场景模
拟,可以实现顶棚安全气囊5和侧气帘6配合一起点爆的耦合静态点爆试验。通过该试验装置进行模拟试验,可在设计阶段演示各种顶棚安全气囊5设计方案与车辆环境的兼容性,以预知各种顶棚安全气囊5设计方案可能存在的安全隐患,给出了试验的操作方法和指导,同时也给出了试验结果的验收和考核方式,填补了顶棚安全气囊5与侧气帘6配合的试验空白。利用顶棚安全气囊5和侧气帘6的耦合子系统试验,可以提前验证整车在64公里小偏置碰撞后的配合效果,且本试验验证的成本远远低于实车验证测试的成本,试验装置可反复使用,进一步缩减了试验验证的成本。通过本试验装置与试验方法进行顶棚安全气囊和侧气帘耦合点爆试验,相比于整车碰撞试验,试验周期更短,缩减了设计开发周期,减小了整车开发时间成本。
66.需要说明的是,在上述实施例中,对各个实施例的描述都各有侧重,某个实施例中没有详细描述的部分,可以参见其它实施例的相关描述。
67.尽管已描述了本发明的优选实施例,但本领域内的技术人员一旦得知了基本创造概念,则可对这些实施例作出另外的变更和修改。所以,所附权利要求意欲解释为包括优选实施例以及落入本发明范围的所有变更和修改。
68.显然,本领域的技术人员可以对本发明进行各种改动和变型而不脱离本发明的精神和范围。这样,倘若本发明的这些修改和变型属于本发明权利要求及其等同技术的范围之内,则本发明也意图包括这些改动和变型在内。