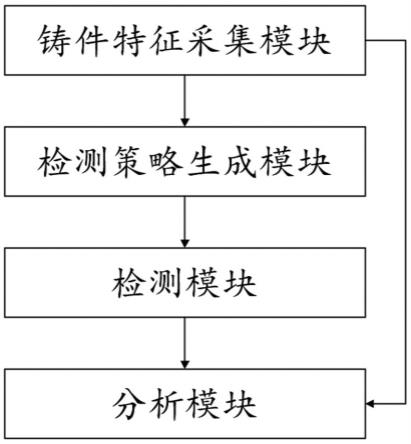
一种铸件缺陷检测控制系统
1.技术领域
2.本发明涉及机器视觉检测技术领域,具体为一种铸件缺陷检测控制系统。
背景技术:3.铸件是通过铸造的方式获取的一种金属件,其通过冶炼的液态金属注入至预先准备好的铸型中,经金属冷却成型及打磨抛光后获得具有特定形状及特定尺寸的零部件;在金属铸造的过程中,由于材料的原因、铸型的原因及环境的因素,或导致铸造出的铸件存在一定的缺陷。
4.现有的对铸件进行质量检测的方式包括尺寸检测、重量监测及表面缺陷检测,其中,传统的表面缺陷的检测主要通过目测的方式,判断铸件中存在的明显缺陷,进而对铸件的质量进行判断;而随着视觉检测计ai技术的快速发展,通过计算机识别铸件的图像信息并通过对图像信息的分析来对铸件表面的缺陷进行判断,进而能够实现铸件的自动化检测过程。
5.现有的对铸件视觉识别的方法在检测平面上存在的缺陷时具有较优的识别准确度,但在检测立体结构时,摄像头采集的清晰度会受到距离的影响,进而导致部分平面采集的图像不够清晰,进而影响缺陷识别的准确度,同时对于金属铸件而言,光照强度大小的不同也会影响铸件对光线的反射状态,因此,固定的光线强度在采集不同深度铸件表面的图像信息时,难以保证铸件的每个表面都能得到最佳的照射光线,进而影响对铸件表面缺陷的识别。
技术实现要素:6.本发明的目的在于提供一种铸件缺陷检测控制系统,解决以下技术问题:如何实现对铸件不同表面缺陷检测的准确性。
7.本发明的目的可以通过以下技术方案实现:一种铸件缺陷检测控制系统,所述系统包括:铸件特征采集模块,用于采集标准铸件的模型信息;检测策略生成模块,用于根据模型信息生成检测策略;所述检测策略生成的步骤为:s1、根据模型信息获得铸件所有的检测平面;s2、根据铸件所有的检测平面获取各个检测平面对应的补光强度及焦距信息;s3、采用对应的补光强度及焦距信息对各个检测平面进行检测,生成检测策略;检测模块,用于按照检测策略获取铸件各个检测平面的图像信息;分析模块,用于根据铸件各个检测平面的图像信息与标准图像信息进行比对,分析出铸件是否故障及故障类型。
8.于一实施例中,所述分析模块的工作过程为:ss100、对铸件各个检测平面的图像信息进行灰度化处理,形成灰度图像;ss200、采用边缘检测算法识别出灰度图像中的特征轮廓信息;ss300、通过将特征轮廓信息与标准图像信息中的标准轮廓信息进行比对,判断铸件是否故障及故障类型。
9.于一实施例中,步骤ss300包括:ss301、获取特征轮廓信息中特征轮廓中心坐标点f,将f与标准轮廓信息中的坐标点集合r进行比对:若,则判断f对应的特征轮廓为异常区域;若,进行步骤ss302;若r中存在f无对应的元素,则判断该元素对应的区域为缺陷区域;ss302、获取f对应的特征轮廓区域的面积s及周长c;将面积s与预设面积区间进行比对,将周长c与预设周长区间进行比对:若且,则判断该特征轮廓区间正常;否则,判断该特征轮廓为异常区域;ss303、判断异常区域的缺陷类型。
10.于一实施例中,所述异常区域中心点的获取方式为:建立xy坐标轴,选取异常区域沿x轴方向中心线与异常区域沿y轴方向中心线的重合点作为特征轮廓中心坐标点f。
11.于一实施例中,步骤s303中判断的过程包括:将异常区域与标准轮廓信息进行重合度比对,获得重合百分比p;若p=100%,则判断异常区域中心点对应标准轮廓信息中的特征类型:若对应特征类型为实体,则判断缺陷类型为塌型;若对应特征类型为孔体,则判断缺陷类型为飞边;若,为预设阈值,则判断缺陷类型为变形;若 >p,则判断缺陷类型为凹陷。
12.于一实施例中,当缺陷类型判断为凹陷时,通过异常轮廓特征值x判断凹陷的具体类型;异常轮廓特征值x的计算公式为:;当时,判断凹陷为圆形凹陷;当时,判断凹陷为异型凹陷;当时,判断凹陷为裂纹凹陷;其中, 及为预设阈值。
13.于一实施例中,所述检测模块包括摄像头及补光灯;
步骤s2中,补光强度获取的过程为:获取各个检测平面距离摄像头的距离l,将距离l输入至光照强度函数中获取光照强度lux(l);其中,lux(l)=,其中, 为预设系数。
14.于一实施例中,步骤s2中,焦距信息获取的过程为:以距离l作为摄像头的焦距。
15.于一实施例中,根据每种缺陷类型所在的检测平面及对应的坐标对缺陷类型进行统计;根据统计结果判断铸件的风险位置点。
16.本发明的有益效果:(1)本发明能够针对各个检测平面确定对应的补光强度并调整正确的焦距,之后再通过检测模块采集铸件不同检测平面的图像信息,进而能够获取到各个检测平面更加清晰的图像信息;将图像信息与各个检测平面对应的标准图像信息进行比对,进而能够更加准确的判断出各个检测平面是否存在铸件缺陷的问题。
17.(2)本发明通过对铸件各个检测平面的图像信息进行灰度化处理,再通过边缘检测算法识别出灰度值变化量较大的像素点,形成特征轮廓信息,通过将特征轮廓信息与标准图像信息中的标准轮廓信息进行比对,进而能够对特征轮廓信息对应的特征进行判断,确定铸件是否存在故障及故障类型。
18.(3)本发明通过光照强度函数获得对应的补光强度并通过距离l获得焦距,能够获得适用于检测平面最佳的补光光照强度及摄像头焦距,进而能够提高识别的准确性。
19.(4)本发明通过风险位置点的指示,能够协助工艺人员对铸件的铸型及铸造工艺进行对应的调整,便于前期试生产过程的进行。
附图说明
20.下面结合附图对本发明作进一步的说明。
21.图1是本发明铸件缺陷检测控制系统概要框图;图2是本发明检测策略生成的步骤流程图;图3是本发明分析模块工作过程的步骤流程图。
具体实施方式
22.下面将结合本发明实施例中的附图,对本发明实施例中的技术方案进行清楚、完整地描述,显然,所描述的实施例仅仅是本发明一部分实施例,而不是全部的实施例。基于本发明中的实施例,本领域普通技术人员在没有作出创造性劳动前提下所获得的所有其它实施例,都属于本发明保护的范围。
23.请参阅图1、图2所示,在一个实施例中,提供了一种铸件缺陷检测控制系统,系统包括:铸件特征采集模块,用于采集标准铸件的模型信息;检测策略生成模块,用于根据模型信息生成检测策略;检测策略生成的步骤为:
s1、根据模型信息获得铸件所有的检测平面;s2、根据铸件所有的检测平面获取各个检测平面对应的补光强度及焦距信息;s3、采用对应的补光强度及焦距信息对各个检测平面进行检测,生成检测策略;检测模块,用于按照检测策略获取铸件各个检测平面的图像信息;分析模块,用于根据铸件各个检测平面的图像信息与标准图像信息进行比对,分析出铸件是否故障及故障类型。
24.通过上述技术方案,通过采集标准铸件的模型信息,再通过模型信息确定铸件的各个检测平面及各个检测平面距离检测模块的距离信息,进而能够针对各个检测平面确定对应的补光强度并调整正确的焦距,之后再通过检测模块采集铸件不同检测平面的图像信息,进而能够获取到各个检测平面更加清晰的图像信息;将图像信息与各个检测平面对应的标准图像信息进行比对,进而能够更加准确的判断出各个检测平面是否存在铸件缺陷的问题。
25.上述技术方案中,检测平面的确定根据铸件的模型来进行确定,例如,当铸件从竖直方向的视角往下注视时,若看到的特征均在一个平面上时,则检测平面即为该平面,当看到的特征在多个平面上时,则分别针对每个平面设置检测平面,当看到的特征是曲面时,此时根据曲面的整体高度杆特定距离设定检测平面,因此,针对不同的结构类型,均能获得对应的检测平面。
26.作为本发明的一种实施方式,请参阅附图图3所示,分析模块的工作过程为:ss100、对铸件各个检测平面的图像信息进行灰度化处理,形成灰度图像;ss200、采用边缘检测算法识别出灰度图像中的特征轮廓信息;ss300、通过将特征轮廓信息与标准图像信息中的标准轮廓信息进行比对,判断铸件是否故障及故障类型。
27.通过上述技术方案,本实施例提供了一种特征轮廓信息与标准图像信息中的标准轮廓信息进行比对的一种实施方式,具体的,首先对铸件各个检测平面的图像信息进行灰度化处理,此过程能够减少后续识别过程中的运算量,之后再通过边缘检测算法识别出灰度值变化量较大的像素点,形成特征轮廓信息,通过将特征轮廓信息与标准图像信息中的标准轮廓信息进行比对,进而能够对特征轮廓信息对应的特征进行判断,确定铸件是否存在故障及故障类型。
28.上述技术方案中,灰度化处理的过程通过最大值灰度化、平均灰度化及加权平均值灰度化等常见的灰度化处理的方法实现,边缘检测算法可采用现有技术中的识别算法,例如roberts边缘检测算法、差分边缘检测算法等实现。
29.作为本发明的一种实施方式,步骤ss300包括:ss301、获取特征轮廓信息中特征轮廓中心坐标点f,将f与标准轮廓信息中的坐标点集合r进行比对:若,则判断f对应的特征轮廓为异常区域;若,进行步骤ss302;若r中存在f无对应的元素,则判断该元素对应的区域为缺陷区域;ss302、获取f对应的特征轮廓区域的面积s及周长c;将面积s与预设面积区间进行比对,将周长c与预设周长区间
进行比对:若且 ,则判断该特征轮廓区间正常;否则,判断该特征轮廓为异常区域;ss303、判断异常区域的缺陷类型。
30.通过上述技术方案,本实施例提供了一种进行比对的具体方法,首先根据特征轮廓的结构信息确定其唯一的特征轮廓中心坐标点f,将f与标准轮廓信息中的坐标点集合r进行比对,显然,当f
∉
r时,说明该特征轮廓区域不属于铸件本身的结构,因此将其判断为异常区域;当f∈r时,通过特征轮廓区域的结构特征进行进一步分析,具体的,通过获取f对应的特征轮廓区域的面积s及周长c,通过面积及周长的特征来对特征轮廓区域进行判断,显然,当且时,说明此特征轮廓区域的面积和周长均在预设的区间内,均处于合理的误差范围内,因此判断该特征轮廓区间正常;当面积或周长任一项不在对应的区间内时,说明此特征区域轮廓与标准轮廓信息中对应的轮廓产生了偏差,即判断异常区域产生缺陷,因此判断此特征轮廓为异常区域,之后再根据异常区域的特征判断其具体的缺陷类型,进而能够确定铸件存在的缺陷种类,便于对其进行统计管理。
31.上述技术方案中,预设面积区间及预设周长区间均根据特征轮廓中心坐标点对应标准轮廓信息中轮廓实际面积及周长面积分别添加合理的误差范围确定,在此不作详述;坐标点集合r中的元素为带有偏差范围的区间,因此,当特征轮廓中心坐标点f落入对于的区间内,视为特征轮廓中心坐标点f∈r。
32.作为本发明的一种实施方式,所述异常区域中心点的获取方式为:建立xy坐标轴,选取异常区域沿x轴方向中心线与异常区域沿y轴方向中心线的重合点作为特征轮廓中心坐标点f。
33.通过上述技术方案,本实施例提供了一种确定特征轮廓中心坐标点f的方法,具体地,在检测模块的检测区域建立xy坐标轴,分别选取异常区域沿x轴方向中心线与异常区域沿y轴方向中心线的重合点作为特征轮廓中心坐标点f,其中,异常区域沿x轴方向中心线指的是异常区域轮廓在x轴投影的中心线,异常区域沿y轴方向中心线指的是异常区域轮廓在y轴投影的中心线,通过此种方式选取特征轮廓中心坐标点f,能够通过点位核对的方式提前判断出该特征轮廓是否为异常区域,提高异常区域识别的效率。
34.作为本发明的一种实施方式,步骤s303中判断的过程包括:将异常区域与标准轮廓信息进行重合度比对,获得重合百分比p;若p=100%,则判断异常区域中心点对应标准轮廓信息中的特征类型:若对应特征类型为实体,则判断缺陷类型为塌型;若对应特征类型为孔体,则判断缺陷类型为飞边;若,为预设阈值,则判断缺陷类型为变形;若 ,则判断缺陷类型为凹陷。
35.通过上述技术方案,本实施例提供了一种判断具体缺陷类型的方法,具体地,首先将异常区域与标准轮廓信息进行比对,当异常区域完全落入至标准轮廓信息中某个轮廓中时,根据标准轮廓信息中的特征类型进行判断,当对应特征类型为实体,此时p=100%且面积
和周长均与对应标准不对应,因此说明缺陷类型为塌型,若对应特征类型为孔体,说明异常区域轮廓相对较小,因此判断缺陷类型为飞边;当时,说明异常区域与标准轮廓信息中某个轮廓发生了位置偏差,因此说明缺陷类型为变形;当 时,说明该异常区域相对独立存在,因此说明缺陷类型为局部凹陷,因此,通过对异常区域的比对分析,能够初步确定具体的缺陷类型。
36.需要说明的是,标准轮廓信息中的特征类型根据标准铸件的模型信息预先获得;上述方案中重合度比对的方法为将异常区域的中心点与标准轮廓信息中对应轮廓的中心点重合;p为异常区域落入标准轮廓信息对应轮廓的比值。
37.作为本发明的一种实施方式,当缺陷类型判断为凹陷时,通过异常轮廓特征值x判断凹陷的具体类型;异常轮廓特征值x的计算公式为:;当时,判断凹陷为圆形凹陷;当时,判断凹陷为异型凹陷;当时,判断凹陷为裂纹凹陷;及为预设阈值。
38.进一步地,本实施例还能根据异常轮廓特征值x判断凹陷的具体类型,其中,x为面积与周长数值的比值,面积s及周长c均进行了标准化统一量纲,当x较大时,说明周长相对较小,面积较大,因此异常区域为圆形凹陷几率较大;当x较小时,说明周长相对较大,面积较小,因此异常区域为裂纹凹陷几率较大,当时,判断凹陷为不规则凹陷类型,即异型凹陷。
39.上述技术方案中,预设阈值 及均通过实验分析数据拟合运算获得。
40.作为本发明的一种实施方式,检测模块包括摄像头及补光灯;步骤s2中,补光强度获取的过程为:获取各个检测平面距离摄像头的距离l,将距离l输入至光照强度函数中获取光照强度lux(l);其中,,其中, 为预设系数。
41.通过上述技术方案,本实施例中的检测模块通过摄像头获取铸件表面的图像信息,通过补光灯来对图像采集过程进行辅助,其中,步骤s2中补光强度获取的过程通过距离来进行确定,具体的,通过公式来过获取光照强度, 为预设系数,根据补光灯的性能确定,l为检测平面距离摄像头的距离,因此通过补光光照强度的运算过程,能够获得最佳的光照强度。
42.上述技术方案中的距离l获取方式为:获取检测平面距离检测基准面的距离,再通过摄像头距离检测基准面的距离减去检测平面距离检测基准面的距离来确定,其中,摄像头距离检测基准面的距离为固定值,检测平面距离检测基准面的距离根据标准铸件的模型信息获得。
43.作为本发明的一种实施方式,步骤s2中,焦距信息获取的过程为:以距离l作为摄像头的焦距。
44.进一步地,本实施例根据获取的距离l作为焦距,进而能够更加准确的获取各个检测平面的图像信息,提高缺陷识别的准确度。
45.作为本发明的一种实施方式,根据每种缺陷类型所在的检测平面及对应的坐标对缺陷类型进行统计;根据统计结果判断铸件的风险位置点。
46.通过上述技术方案,本实施例能够对多个铸件的缺陷类型进行统计,并通过缺陷类型较多类型对应的坐标点确定铸件最容易出现缺陷的风险位置点,因此通过风险位置点的指示,能够协助工艺人员对铸件的铸型及铸造工艺进行对应的调整,便于前期试生产过程的进行。
47.以上对本发明的一个实施例进行了详细说明,但所述内容仅为本发明的较佳实施例,不能被认为用于限定本发明的实施范围。凡依本发明申请范围所作的均等变化与改进等,均应仍归属于本发明的专利涵盖范围之内。