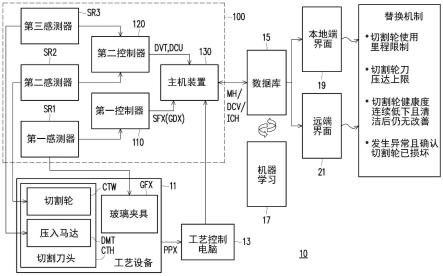
1.本发明涉及一种检测系统,且特别涉及一种切割轮的状态检测系统及切割轮的状态检测方法。
背景技术:2.在使用玻璃基板的工艺中,需要对玻璃基材应用切割工艺,以使玻璃基板呈现所需的大小。但是,于切割工艺中,切割轮可能因为撞击、老化等因素而出现崩齿损坏的现象。但是,一般的切割轮的更换方式为人为检测异常、或达到更换刀轮里程数(例如25000米)即更换。然而,通过人力进行切割轮的检查,较费时,效率不佳,并且异常风险的管控不易。并且,在切割轮尚未损坏时因达到里程数更换,会增加刀具成本。
技术实现要素:3.本发明提供一种切割轮的状态检测系统及切割轮的状态检测方法,可实时监控切割输的状态,以预测切割轮的健康度,借此使生产成本最佳化,以及降低切割轮异常的风险。
4.本发明的切割轮的状态检测系统包括,包括第一感测器、第一控制器、第二感测器、第三感测器、第二控制器以及主机装置。第一感测器配置于玻璃夹具上,以检测玻璃夹具的气压缸开合状态信号。第一控制器耦接第一感测器,以基于气压缸开合状态信号提供夹具状态信号。第二感测器配置于具有切割轮的切割刀头上,以检测切割刀头的震动。第三感测器配置于驱动切割轮的压入马达,以检测压入马达的电流。第二控制器耦接第二感测器及第三感测器,以基于切割刀头的震动提供切割刀头的震动数据且基于压入马达的电流提供压入马达的电流数据。主机装置耦接第一控制器及第二控制器,主机装置基于夹具状态信号接收震动数据及电流数据,并且通过一切割轮健康度模型分析震动数据及电流数据,以提供包含切割轮的至少一健康度预估的一切割轮健康度信息。
5.本发明的切割轮的状态检测方法,包括下列步骤。经由配置于玻璃夹具上的第一感测器检测玻璃夹具的气压缸开合状态信号,以提供夹具状态信号。经由配置于具有切割轮的切割刀头上的第二感测器及第三测器提供切割刀头的震动数据及驱动切割轮的压入马达的电流数据。经由主机装置基于夹具状态信号接收震动数据及电流数据。通过切割轮健康度模型分析震动数据及电流数据,以提供包含切割轮的至少一健康度预估的一切割轮健康度信息。
6.基于上述,本发明实施例的切割轮的状态检测系统及切割轮的状态检测方法,通过第二感测器及第三感测器实时监控切割刀头的震动及压入马达的电流,以获取切割时的震动数据。接着,对切割时的震动数据进行分析以产生包含切割轮的至少一健康度预估的切割轮健康度信息。因此,由于切割轮健康度信息是通过系统实时产生的,因此可以实时监控切割轮的状态。
7.为让本发明的上述特征和优点能更明显易懂,下文特举实施例,并配合说明书附
图作详细说明如下。
附图说明
8.图1为依据本发明一实施例的工艺设备监控系统的系统示意图。
9.图2为依据本发明一实施例的切割轮的切割轮健康度信息的模拟示意图。
10.图3为依据本发明一实施例的电流数据的分析示意图。
11.图4为依据本发明一实施例的震动数据的分离示意图。
12.图5为依据本发明一实施例的切割轮的状态检测方法的流程图。
13.附图标记说明:
14.10:工艺设备监控系统
15.11:工艺设备
16.13:工艺控制电脑
17.15:数据库
18.17:机器学习模块
19.19:本地端界面
20.21:远端界面
21.100:状态检测系统
22.110:第一控制器
23.120:第二控制器
24.130:主机装置
25.cth:切割刀头
26.ctw:切割轮
27.dcu:电流数据
28.dcv:震动特征数据
29.dmt:压入马达
30.dvt:震动数据
31.dvtx:经切割的震动数据
32.gdx:气量数据
33.gfx:玻璃夹具
34.mh:切割轮健康度模型
35.ich:切割轮健康度信息
36.pct:切割期间
37.pnc:非切割期间
38.ppx:工艺参数
39.sfx:夹具状态信号
40.sr1:第一感测器
41.sr2:第二感测器
42.sr3:第三感测器
43.s510-s550:步骤
具体实施方式
44.除非另有定义,本文使用的所有术语(包括技术和科学术语)具有与本发明所属领域的普通技术人员通常理解的相同的含义。将进一步理解的是,诸如在通常使用的字典中定义的那些术语应当被解释为具有与它们在相关技术和本发明的上下文中的含义一致的含义,并且将不被解释为理想化的或过度正式的意义,除非本文中明确地这样定义。
45.应当理解,尽管术语“第一”、“第二”、“第三”等在本文中可以用于描述各种元件、部件、区域、层及/或部分,但是这些元件、部件、区域、及/或部分不应受这些术语的限制。这些术语仅用于将一个元件、部件、区域、层或部分与另一个元件、部件、区域、层或部分区分开。因此,下面讨论的“第一元件”、“部件”、“区域”、“层”或“部分”可以被称为第二元件、部件、区域、层或部分而不脱离本文的教导。
46.这里使用的术语仅仅是为了描述特定实施例的目的,而不是限制性的。如本文所使用的,除非内容清楚地指示,否则单数形式“一”、“一个”和“该”旨在包括复数形式,包括“至少一个”。“或”表示“及/或”。如本文所使用的,术语“及/或”包括一个或多个相关所列项目的任何和所有组合。还应当理解,当在本说明书中使用时,术语“包括”及/或“包括”指定所述特征、区域、整体、步骤、操作、元件的存在及/或部件,但不排除一个或多个其它特征、区域整体、步骤、操作、元件、部件及/或其组合的存在或添加。
47.图1为依据本发明一实施例的工艺设备监控系统的系统示意图。请参照图1,在本发明实施例中,工艺设备监控系统10包括工艺设备11、工艺控制电脑13、数据库15、机器学习模块17、本地端界面19、远端界面21及切割轮ctw的状态检测系统100。工艺设备11例如至少包括具有切割轮ctw的切割刀头cth、驱动切割轮ctw且配置于切割刀头cth上的压入马达dmt以及用于固定玻璃基材的玻璃夹具gfx,其中压入马达dmt控制切割轮ctw对玻璃基材的压入程度,但没有主动带动切割轮ctw进行转动。
48.切割轮的状态检测系统100包括第一感测器sr1、第一控制器110、第二感测器sr2、第三感测器sr3、第二控制器120以及主机装置130。第一感测器sr1配置于玻璃夹具gfx上以检测玻璃夹具gfx的气量数据gdx,其中气量数据gdx可包含指示玻璃夹具gfx的气压缸(未示出)的开合状态的气压缸开合状态信号。第一控制器110耦接第一感测器sr1以基于气量数据gds(或者基于气压缸开合状态信号)提供夹具状态信号sfx。
49.第二感测器sr2配置于具有切割轮ctw的切割刀头cth上,以检测切割刀头cth的震动。第三感测器sr3配置于驱动切割轮ctw的压入马达dmt,以检测压入马达dmt的电流。第二控制器120耦接第二感测器sr2及第三感测器sr3以基于切割刀头cht的震动提供切割刀头cht的震动数据dvt且基于压入马达dmt的电流提供压入马达dmt的电流数据dcu。
50.主机装置130耦接第一感测器110及第二感测器120,主机装置130基于夹具状态信号sfx接收震动数据dvt及电流数据dcu,基于电流数据dcu判断至少一面板长边与至少一面板短边的一切割顺序是否符合一预设顺序,基于切割顺序符合预设顺序通过切割轮健康度模型mh分析震动数据dvt及电流数据dcu,以提供包含切割轮ctw的至少一健康度预估的切割轮健康度信息ich。
51.图2为依据本发明一实施例的切割轮的切割轮健康度信息的模拟示意图。请参照图1及图2,在本实施例中,切割轮健康度信息ich可存储于数据库中,以通过本地端界面19及远端界面21传达切割轮ctw的健康度给本地端的操作人员以及远端的系统管理人员。本
地端的操作人员可自行或根据系统管理人员的通知进行相关的替换机制,例如确认切割轮的使用是否达到里程限制(例如50,000米);切割轮刀压是否达上限(如0.1牛顿(0.1n));切割轮健康度连续低下(如50%一小时)且清洁后仍无改善;以及,发生异常且确认切割轮已损坏。
52.因此,由于切割轮健康度信息ich是通过系统实时产生的,因此可以实时监控切割轮的状态。如果监控到切割轮健康度异常低落,即可立即停机进行排查,有效避免切割轮的异常影响面板的切割品质。并且,可使用切割轮的健康度指标取代传统的切割距离(里程)来管理与衡量切割轮的使用标准。此外,使用切割轮的健康度来作为切割轮是否更换的指标,可以让每一把切割轮都使用到自身体质的极限,有效避免浪费的发生。再者,使用切割轮的健康度来作为切割轮是否更换的指标,也可以有效的避免临时发生的切割轮的异常影响产品品质。
53.请再参照图1,在本实施例中,预设顺序基于来自具有切割刀头cht的工艺设备11的至少一工艺参数ppx所判定。进行步来说,工艺参数ppx包括对玻璃基材施加的至少一切割压力、至少一切割位置、至少一切割位移量、至少一切割速度、至少一切割起始等待时间以及至少一切割结束等待时间,因此主机装置130可通过工艺参数ppx借此判断切割轮ctw的预设切割顺序。
54.并且,在本发明实施例中,主机装置130基于夹具状态信号sfx与夹具临界值的比较判断是否接收震动数据dvt及电流数据dcu。换言之,主机装置130可基于夹具状态信号sfx与夹具临界值的比较判断玻璃夹具gfx是否夹持玻璃基材,在玻璃夹具gfx夹持玻璃基材时才接收接收震动数据dvt及电流数据dcu,反之,则不接收接收震动数据dvt及电流数据dcu。
55.在本发明实施例中,主机装置130分析电流数据dcu以判断切割轮ctw压入玻璃基材的至少一切割期间pct及切割轮ctw未压入玻璃基材的至少一非切割期间pnc。举例来说,主机装置130对电流数据dcu进行移动平均,基于移动平均后的电流数据dcu判断至少一切割期间pct及至少一非切割期间pnc。并且,主机装置130可更基于工艺设备11提供的一切割起始等待时间及一切割结束等待时间判断至少一切割期间pct及至少一非切割期间pnc。
56.接着,主机装置130基于至少一切割期间pct获取震动数据dvt以产生至少一震动特征数据dcv,并且分析至少一震动特征数据dcv以提供切割轮健康度信息ich。在本发明实施例中,主机装置130可以对至少一切割期间pct内的震动数据dvt进行带通滤波,接着对至少一切割期间pct内经带通滤波的震动数据dvt进行基本统计特征提取、傅里叶转换、小波包特征提取、以及希尔伯特-黄转换(hilbert-huang transform)的至少其一来进行特征提取,以产生震动特征数据dcv。
57.在本发明实施例中,基本统计特征提取包括一最大值提取、一最小值提取、一平均值提取、一中位数提取、标准差一提取、一方差提取、一偏态提取、一峰度提取的其中之一。
58.在本发明实施例中,主机装置130对至少一切割期间pct内的震动数据dvt的数据长度来判断各个切割期间pct的一切割动作的切割方向并进行标记对应的震动特征数据dcv。并且,主机装置130将基于至少一工艺参数ppx标记至少一震动特征数据dcv。
59.在本发明实施例中,主机装置130可通过一物联网(iot)与第一感测器110及第二感测器120进行通信。并且,主机装置130采用离群值检测(outlier detection)演算法清理
切割轮健康度信息ich中的至少一离群数据。
60.在本发明实施例中,主机装置130将至少一震动特征数据dcv储于至一数据库15,以经由机器学习模块17基于存储于数据库15的多个过去的震动特征数据dcv建立切割轮健康度模型mh。进步一来说,切割轮健康度模型mh的训练与预测流程包括:针对每一次的工艺动作的震动特征数据dcv进行进行标记,标记的条件为当下使用的切割轮为“正常刀轮”或是“异常刀轮”;使用数据扩增技术让正常数据与异常数据的震动特征数据dcv的数量比例相等;依照切割轮转速(通过切割速度换算),挑选适合的频域特征,例如0.5倍频、1倍频、2倍频、3倍频、4倍频、5倍频等等;挑选切割方向相同的震动特征数据dcv,确保不会因为方向的关系造成差异性过大;使用序列向前选择(sequential feature selection)进行特征筛选;并且,使用机器学习模块17,让人工智能(artificial intelligence,ai)学习切割轮ctw在不同切割状态下的震动特征数据dcv,借此训练出具有预测切割轮状态的能力的切割轮健康度模型mh。
61.在在本发明实施例中,可使用分散式超参数最佳化技术(distributed hyperparameter optimization)得到最大化的曲线下面积(area under the curve,auc)分数的切割轮健康度模型mh。
62.预测结果会依照人工智能(例如切割轮健康度模型mh)所带出的相似度来转换为切割轮ctw的健康度预估,作为评估切割轮ctw的效度的指标。机器学习模块17的数据来源为存储已完成数据前处理的震动特征数据dcv的数据库15。机器学习模块17会不断的检测是否有新的震动特征数据dcv产生,如果有的话会依照条件进行预测并输出结果至数据库15存储,提供后续的视觉化与设备调整使用。
63.图3为依据本发明一实施例的电流数据的分析示意图。请参照图1及图3,在本实施例中,(a)部分为电流数据dcu,(b)部分为移动平均后的电流数据dcu,(c)部分为标示出进行切割的时段。根据(c)部分,可将进行切割的时段标示为切割期间pct,而其他时段标示为非切割期间pnc。其中,切割期间pct及非切割期间pnc可基于工艺设备11提供的切割起始等待时间及切割结束等待时间来校准。
64.图4为依据本发明一实施例的震动数据的分离示意图。请参照图1及图4,在本实施例中,当夹具状态信号sfx转态时(例如上升至高电平),主机装置130接收震动数据dvt及电流数据dcu(如(a)部分所示)。接着,依据电流数据dcu判断切割期间pct及非切割期间pnc(如图3所示)。其中,非切割期间pnc中的震动数据dvt会被遮罩,亦即仅会获取切割期间pct的震动数据dvt,因而产生多个经切割的震动数据dvtx。主机装置130可对经切割的震动数据dvtx进行处理来产生震动特征数据dcv。
65.图5为依据本发明一实施例的切割轮的状态检测方法的流程图。请参照图5,在本实施例中,切割轮的状态检测方法包括下列步骤。在步骤s510中,经由配置于玻璃夹具上的第一感测器检测玻璃夹具的气量数据(亦即气压缸开合状态信号),以提供夹具状态信号。在步骤s520中,经由配置于具有切割轮的切割刀头上的第二感测器及第三感测器提供切割刀头的震动数据及驱动切割轮的压入马达的电流数据。在步骤s530中,经由主机装置基于夹具状态信号接收震动数据及电流数据。在步骤s540中,经由主机装置基于电流数据判断至少一面板长边与至少一面板短边的切割顺序是否符合预设顺序。在步骤s550中,经由主机装置基于切割顺序符合预设顺序通过切割轮健康度模型分析震动数据及电流数据,以提
供包含切割轮的至少一健康度预估的切割轮健康度信息。其中,在步骤s510-s550的顺序为用以说明,本发明实施例不以此为限。并且步骤s510-s550的细节可参照图1至图4实施例所示,在此则不再赘述。
66.综上所述,本发明实施例的切割轮的状态检测系统及切割轮的状态检测方法,通过第二感测器及第三感测器实时监控切割刀头的震动及压入马达的电流,以获取切割时的震动数据。接着,对切割时的震动数据进行分析以产生包含切割轮的至少一健康度预估的切割轮健康度信息。因此,由于切割轮健康度信息是通过系统实时产生的,因此可以实时监控切割轮的状态。在切割轮健康度异常低落的情况下,可立即停机进行排查,以有效避免切割轮的异常影响面板的切割品质。并且,使用切割轮的健康度来作为切割轮是否更换的指标,可以让每一把切割轮都使用到自身体质的极限,有效避免浪费的发生。
67.虽然本发明已以实施例公开如上,然其并非用以限定本发明,任何所属技术领域中技术人员,在不脱离本发明的构思和范围内,当可作些许的变动与润饰,故本发明的保护范围当视权利要求所界定者为准。