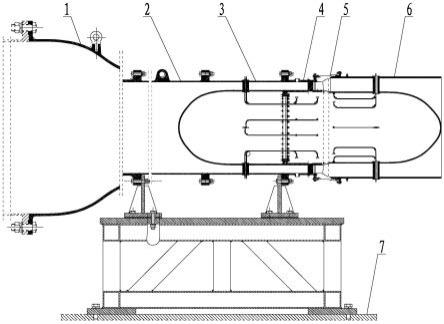
1.本发明涉及航空发动机零部件试验技术,尤其涉及一种航空发动机低压涡轮导向器流量检测试验段结构,适用于用于航空发动机涡轮导向器流量函数试验。
背景技术:2.涡轮导向器流量函数试验器主要用于获取导向器流量函数随进出口总静压膨胀比和冷气状态参数的变化曲线,验证导向器流通能力并获得冷气状态参数对导向器流量函数特性的影响规律。由于进气马赫数、进气攻角对涡轮导向器的前后温度、气流流场、发动机流量及功率、转速、耗油率等都有直接影响,关系发动机工作的稳定性、压气机与涡轮的匹配性等。因此,对发动机涡轮导向器函数流量测量是一项必不可少的工作,每一件涡轮导向器在装机交付前都必须进行流量函数专项试验,以确定涡轮导向器排气面积与流量的合格性。
3.现有技术中有文献公开关于低压涡轮导向器试验相关技术,如公开号为cn113607420a公开了一种低压涡轮导向器环吹试验安装结构及试验方法,利用整流叶栅将气流偏离轴向一定角度,同时对低压涡轮导向器引入冷气,满足发动机实际工作中低压涡轮导向器进口气流角及其表面实际的流动状态,解决了气流直接作用在低压涡轮导向器的低导叶片前缘的问题,改善气流在低压涡轮导向器局部分离的同时还提高了低压涡轮导向器的气动性能,而且增加试验数据的可靠性。
4.发动机低压涡轮导向器装机前均需进行流量检测试验,该试验主要获取不同试验状态下进出口总压、总温、静压、气流角等的径向分布曲线。发动机低压涡轮导向器前为高压涡轮,流出高压涡轮的高温燃气以一定攻角进入低压涡轮导向器。以往低压涡轮导向器流量检测试验段未考虑高压涡轮出口气流预旋角度影响。目前涡轮导向器流量检测试验段没有成熟的设计经验,进气收敛段多采用直筒设计,流场品质较差。且导向器多是采用轴向进气,对试验结果有一定程度的影响,导致流量检测结果偏小。
技术实现要素:5.本发明的主要目的是提出一种航空发动机低压涡轮导向器流量检测试验段结构,旨在解决上述技术问题。
6.为实现上述目的,本发明提出一种航空发动机低压涡轮导向器流量检测试验段结构,包括低压涡轮导向器,在低压涡轮导向器的进气端设置有进气测量机匣,在进气测量机匣的进气端设置有进气整流段,在进气整流段的进气端设置有进口直管,在进口直管的进气端设置有进气收敛段,在低压涡轮导向器的出气端设置有排气测量机匣;所述进气收敛段的内流道型面采用维氏曲线;在进气测量机匣的内、外机匣之间环形分布设置有整流叶栅,用于改变进气方向并将气流导引至低压涡轮导向器。
7.优选的,所述进气收敛段的设计步骤包括:
8.步骤一:确定收敛段进口截面半径hi和收敛段出口截面半径h0;
9.步骤二:设置步长x;
10.步骤三:按下式确定不同步长对应的点,进行拟合可得收敛段维氏曲线部分;
[0011][0012]
式中:hi—收敛段进口截面半径;
[0013]
h0—收敛段出口截面半径;
[0014]
h—轴向距离x处的截面高度;
[0015]
l为收敛段维氏曲线部分总长。
[0016]
优选的,所述进气收敛段的进口和出口分别一体成型设置有平直过渡段。
[0017]
优选的,进气收敛段的内流道型面粗糙度不低于ra3.2;所述平直过渡段的长度为70mm。
[0018]
优选的,在所述进气收敛段上设置有吊耳。
[0019]
优选的,所述进气整流段包括进气整流段外支撑、以及同轴设置在进气整流段外支撑内部的整流帽罩;进气整流段外支撑的内壁面与整流帽罩的外周面间隔设置形成进气流道;进气整流段外支撑与整流帽罩之间通过支板连接。
[0020]
优选的,在进气整流段外支撑的两端分别设置有法兰边,进气端的法兰边与所述进口直管连接,出气端的法兰边与进气测量机匣的外机匣连接;在整流帽罩尾端内壁上行设置有进气整流段内支撑;所述进气整流段内支撑与进气测量机匣的内机匣连接。
[0021]
优选的,所述进气测量机匣包括进气测量机匣外机匣、以及同轴设置在进气测量机匣外机匣内部的进气测量机匣内机匣,所述整流叶栅一端与进气测量机匣外机匣连接,另一端与进气测量机匣内机匣连接;进气测量机匣外机匣与进气测量机匣内机匣之间间隔设置形成进气流道;在进气测量机匣外机匣的外周面上环形布置有总温总压测点;在进气测量机匣内机匣的内壁面上位于整流叶栅的前、后环形布置有两排进口静压测点。
[0022]
优选的,利用进气测量机匣测量后,根据下式低压涡轮导向器前总压进行修正:
[0023][0024]
式中:p1*—整流叶栅栅前总压;
[0025]
p2*—整流叶栅栅后总压;
[0026]
p1—整流叶栅栅前静压;
[0027]
p2—整流叶栅栅后静压;
[0028]
γ=1.4。
[0029]
优选的,所述排气测量机匣包括排气机匣外机匣、以及同轴设置在排气机匣外机匣内的排气机匣内机匣;排气机匣外机匣与排气机匣内机匣之间间隔设置形成排气流道;在排气机匣内机匣的尾端设置有出口整流帽罩;所述排气机匣外机匣与排气机匣内机匣之间设置有多个排气机匣支板;在排气机匣外机匣的外壁面、以及排气机匣内机匣的内壁面分别设置有出口静压测点。
[0030]
由于采用了上述技术方案,本发明的有益效果如下:
[0031]
(1)本发明中进气收敛段的内流道型面采用维氏曲线,可以有效地提高流场均匀性和轴向静压梯度,提高了进气流场品质;另外,通过在低压涡轮导向器前设置一排环形整流叶栅,可以改变进气方向,进而改变进气攻角,将气流导引至低压涡轮导向器,进而保证进气方向与发动机产品一致。
[0032]
(2)本发明通过在整流叶栅的栅前栅后布置两排静压测点,对低压涡轮导向器前总压进行修正,提高流量检测准确性。
附图说明
[0033]
为了更清楚地说明本发明实施例或现有技术中的技术方案,下面将对实施例或现有技术描述中所需要使用的附图作简单地介绍,显而易见地,下面描述中的附图仅仅是本发明的一些实施例,对于本领域普通技术人员来讲,在不付出创造性劳动的前提下,还可以根据这些附图示出的结构获得其他的附图。
[0034]
图1为本发明所提供的航空发动机低压涡轮导向器流量检测试验段结构示意图;
[0035]
图2为本发明中进气收敛段的结构示意图;
[0036]
图3为本发明中进气收敛段的维氏收缩曲线图;
[0037]
图4为本发明中进气整流段的结构示意图;
[0038]
图5为本发明中进气测量机匣的结构示意图;
[0039]
图6为本发明中排气测量机匣的结构示意图。
[0040]
附图标号说明:1、进气收敛段;101、平直过渡段;102、吊耳;2、进口直管;3、进气整流段;301、整流帽罩;302、进气整流段外支撑;303、支板;304、进气整流段内支撑;4、进气测量机匣;401、总温总压测点;402、整流叶栅;403、进气测量机匣外机匣;404、进口静压测点;405、进气测量机匣内机匣;5、低压涡轮导向器;6、排气测量机匣;601、出口静压测点;602、排气机匣支板;603、排气机匣外机匣;604、排气机匣内机匣;605、出口整流帽罩;7、支撑平台。
具体实施方式
[0041]
下面将结合本发明实施例中的附图,对本发明实施例中的技术方案进行清楚、完整地描述,显然,所描述的实施例仅仅是本发明的一部分实施例,而不是全部的实施例。基于本发明中的实施例,本领域普通技术人员在没有作出创造性劳动前提下所获得的所有其他实施例,都属于本发明保护的范围。
[0042]
需要说明,本发明实施例中所有方向性指示(诸如上、下、左、右、前、后
……
)仅用于解释在某一特定姿态(如附图所示)下各部件之间的相对位置关系、运动情况等,如果该特定姿态发生改变时,则该方向性指示也相应地随之改变。
[0043]
结合图1所示,一种航空发动机低压涡轮导向器流量检测试验段结构,包括低压涡轮导向器5,在低压涡轮导向器5的进气端设置有进气测量机匣4,在进气测量机匣4的进气端设置有进气整流段3,在进气整流段3的进气端设置有进口直管2,在进口直管2的进气端设置有进气收敛段1,在低压涡轮导向器5的出气端设置有排气测量机匣6;所述进气收敛段1的内流道型面采用维氏曲线;在进气测量机匣4的内、外机匣之间环形分布设置有整流叶栅402,用于改变进气方向并将气流导引至低压涡轮导向器5。
[0044]
进气收敛段1用于将稳压箱中气流引入;进口直管2起到连接进气收敛段1和进气整流段3的作用;进气测量机匣4用于低压涡轮导向器5进口测试受感部布置并测取进口相关气动参数;排气测量机匣6用于低压涡轮导向器5出口测试受感部布置以及测取出口相关气动参数。
[0045]
在本实施例中,进气收敛段1的内流道型面采用维氏曲线,相比于常见的收敛段收缩曲线采用的双三次曲线或五次方曲线,维氏曲线在流场均匀性和轴向静压梯度等方面更为优越,提高了进气流场品质;另外,通过在低压涡轮导向器5前设置一排环形整流叶栅402,可以改变进气方向,进而改变进气攻角,将气流导引至低压涡轮导向器5,进而保证进气方向与发动机产品一致。
[0046]
结合图2及图3所示,所述进气收敛段1的设计步骤包括:
[0047]
步骤一:确定收敛段进口截面半径hi和收敛段出口截面半径h0;
[0048]
步骤二:设置步长x;
[0049]
步骤三:按下式确定不同步长对应的点,进行拟合可得收敛段维氏曲线部分;
[0050][0051]
式中:hi—收敛段进口截面半径;
[0052]
h0—收敛段出口截面半径;
[0053]
h—轴向距离x处的截面高度;
[0054]
l为收敛段维氏曲线部分总长。
[0055]
结合图2所示,所述进气收敛段1的进口和出口分别一体成型设置有平直过渡段101,避免进出口产生流场波动,提高流场品质。
[0056]
在本实施例中,整个进气收敛段1采用铸件,铸造完成在机床进一步加工至要求精度。进气收敛段1的内流道型面粗糙度不低于ra3.2;所述平直过渡段101的长度为70mm,进气收敛段1的厚度15mm。
[0057]
结合图2所示,在所述进气收敛段1上设置有吊耳102,方便吊车起吊安装。
[0058]
结合图4所示,所述进气整流段3包括进气整流段外支撑302、以及同轴设置在进气整流段外支撑302内部的整流帽罩301;进气整流段外支撑302的内壁面与整流帽罩301的外周面间隔设置形成进气流道;进气整流段外支撑302与整流帽罩301之间通过支板303连接。
整流帽罩301将进气转入试验件环形流道,整流帽罩301前端的曲面设计保证了流场品质,减小流动过程中压力损失,避免产生激波等干扰;进气整流段外支撑302起到联接进气测量机匣4的外机匣、以及连接进口直管2的作用,并与整流帽罩301共同形成进气流道;支板303起到联接进气整流段内外支撑302和整流帽罩301的作用,要求其具有足够的结构刚度,不至于在在气动力作用下产生变形。
[0059]
进一步地,在进气整流段外支撑302的两端分别设置有法兰边,进气端的法兰边与所述进口直管2连接,出气端的法兰边与进气测量机匣4的外机匣连接;另外,法兰边对进气整流段外支撑302在连接之后还形成框架结构,进一步加强进气整流段外支撑302的刚性。在整流帽罩301尾端内壁上行设置有进气整流段内支撑304;所述进气整流段内支撑304与进气测量机匣4的内机匣连接。进气整流段内支撑304既起到连接作用,还能起到支撑作用。
[0060]
结合图5所示,所述进气测量机匣4包括进气测量机匣外机匣403、以及同轴设置在进气测量机匣外机匣403内部的进气测量机匣内机匣405,所述整流叶栅402一端与进气测量机匣外机匣403连接,另一端与进气测量机匣内机匣405连接;进气测量机匣外机匣403与进气测量机匣内机匣405之间间隔设置形成进气流道,流道表面粗糙度ra1.6;在进气测量机匣外机匣403的外周面上环形布置有总温总压测点401用于测取外壁面总温、总压;总温总压测点401设置在轴向距离整流叶栅402前缘1.5倍整流叶栅402叶片中径弦长的轴向投影位置处;由于流经整流叶栅402的气流存在一定压力损失,因此在进气测量机匣内机匣405的内壁面上位于整流叶栅402的前、后环形布置有两排进口静压测点404,用于测取内壁面静压,修正环向整流叶栅402结构产生的总压损失。整流叶栅402前的进口静压测点404的轴向与总温总压测点401的探针进气口保持一致,整流叶栅402后的进口静压测点404尽量靠近低压涡轮导向器5。进气测量机匣内机匣405用于联接试验件鼓筒结构,应具有足够的结构刚度,保证试验过程中试验件稳固。
[0061]
在本实施例中,利用进气测量机匣4测量后,根据下式低压涡轮导向器5前总压进行修正:
[0062][0063]
式中:p1*—整流叶栅栅前总压;
[0064]
p2*—整流叶栅栅后总压;
[0065]
p1—整流叶栅栅前静压;
[0066]
p2—整流叶栅栅后静压;
[0067]
γ=1.4。
[0068]
结合图6所示,所述排气测量机匣6包括排气机匣外机匣603、以及同轴设置在排气机匣外机匣603内的排气机匣内机匣604;排气机匣外机匣603与排气机匣内机匣604之间间隔设置形成排气流道,排气流道表面粗糙度ra1.6;在排气机匣内机匣604的尾端设置有出口整流帽罩605;所述排气机匣外机匣603与排气机匣内机匣604之间设置有多个排气机匣
支板602;在排气机匣外机匣603的外壁面、以及排气机匣内机匣604的内壁面分别设置有出口静压测点601用于测取出口静压,出口静压测点601轴向距低压涡轮导向器5叶片尾缘1.5倍叶片中径弦长轴向投影。排气机匣支板602用于支撑排气测量机匣6的内、外机匣,保证稳固,根据排气气流角成一定角度焊接,避免出口产生激波影响。排气机匣外机匣603用于联接试验件外机匣出口,应具有足够的结构刚度,保证试验过程中试验件稳固。排气机匣内机匣604用于联接试验件鼓筒结构,应具有足够的结构刚度,保证试验过程中试验件稳固。出口整流帽罩605的尾端型面设计为曲面,使得排气流道呈扩张趋势,保证排气通畅。
[0069]
结合图1所示,航空发动机低压涡轮导向器流量检测试验段结构还包括支撑平台7,支撑平台7上设置有安装座分别与进口直管2、进气整流段3连接,支撑平台7起到支撑整个试验装段的作用。
[0070]
以上所述仅为本发明的优选实施例,并非因此限制本发明的专利范围,凡是在本发明的发明构思下,利用本发明说明书及附图内容所做的等效结构变换,或直接/间接运用在其他相关的技术领域均包括在本发明的专利保护范围内。