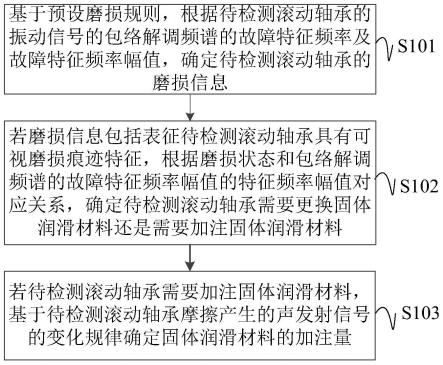
1.本技术涉及设备维护领域,特别是涉及一种基于信息融合的滚动轴承润滑脂加注管理方法。
背景技术:2.润滑材料检测是设备运行及维护工作的重要组成部分,其关系到设备正常运转,减少设备磨损,延长设备维修周期和使用寿命,降低生产成本与提高经济效益等一系列重要问题。轴承如滚动轴承作为机械设备中不可缺少的零部件,其可用于支撑机械旋转体,降低运动过程中的摩擦系数,并保证回转精度,轴承中通过加入润滑材料如润滑脂使相对运动部件接触面脱离,从而减小摩擦力。但是,为了保证轴承的性能,轴承内填充的润滑材料需要适量且污染较少,举例来说,若润滑脂量过少,易造成缺脂从而产生干摩擦,影响轴承使用寿命;若注脂量过多,不利于轴承散热,会导致轴承温度升高,润滑状态变坏;而润滑脂受金属磨屑污染,也会加剧轴承磨损。因此,检测轴承内的润滑材料的填充量以及污染状态是轴承运行过程中必不可少的工作。
3.对于滚动轴承内所填充的固体润滑材料的检测,相关技术通常是通过轴承外径和轴承宽度估算固体润滑材料的填充量,如通过轴承外径和轴承宽度估算润滑脂填充量,这种方法只适合新滚动轴承加注固体润滑材料或旧滚动轴承更换固体润滑材料,且其所确定的添加量存在较大的可调范围。当设备在运行中缺少固体润滑材料或者固体润滑材料被污染时,相关技术并无法指导固体润滑材料的定量化添加,也无法判断固体润滑材料的污染状态进而评价是否需要更换。
4.鉴于此,如何实现对滚动轴承内的固体润滑材料的填充量及污染状态精准检测,保障滚动轴承的稳定运行,降低滚动轴承运行的故障风险,是所属领域技术人员需要解决的技术问题。
技术实现要素:5.本技术提供了一种基于信息融合的滚动轴承润滑脂加注管理方法、装置、电子设备及可读存储介质,实现对滚动轴承内的固体润滑材料的填充量及污染状态精准检测,有利于保障滚动轴承的稳定运行,可有效降低滚动轴承运行的故障风险。
6.为解决上述技术问题,本发明实施例提供以下技术方案:
7.本发明实施例一方面提供了一种基于信息融合的滚动轴承润滑脂加注管理方法,包括:
8.基于预设磨损规则,根据待检测滚动轴承的振动信号的包络解调频谱的故障特征频率及故障特征频率幅值,确定所述待检测滚动轴承的磨损信息;
9.若所述磨损信息包括表征所述待检测滚动轴承具有可视磨损痕迹特征,根据磨损状态和所述包络解调频谱的故障特征频率幅值的特征频率幅值对应关系,确定所述待检测滚动轴承需要更换固体润滑材料还是需要加注固体润滑材料;
10.若所述待检测滚动轴承需要加注固体润滑材料,基于所述待检测滚动轴承摩擦产生的声发射信号的变化规律确定所述固体润滑材料的加注量。
11.可选的,所述根据待检测滚动轴承的振动信号的包络解调频谱的故障特征频率及故障特征频率幅值,确定所述待检测滚动轴承的磨损信息,包括:
12.获取待检测滚动轴承的振动信号;
13.根据所述振动信号的包络解调频谱的特征频率,确定所述待检测滚动轴承的磨损部件;
14.根据所述振动信号的包络解调频谱是否存在故障特征频率以及所述包络解调频谱中的故障特征频率幅值,确定所述磨损部件的磨损级别;
15.根据所述磨损部件和所述磨损级别生成磨损信息;
16.其中,所述磨损级别包括第一磨损级别、第二磨损级别和第三磨损级别;所述第一磨损级别用于表示所述待检测滚动轴承处于磨损初始阶段,具有不可视磨损痕迹;所述第二磨损级别用于表示所述待检测滚动轴承处于磨损中级阶段,具有可视磨损痕迹特征;所述第三磨损级别用于表示所述待检测滚动轴承已有金属颗粒剥落。
17.可选的,所述根据待检测滚动轴承的振动信号的包络解调频谱的故障特征频率及故障特征频率幅值,确定所述待检测滚动轴承的磨损信息之后,还包括:
18.若所述待检测滚动轴承为所述第一磨损级别,则判定所述待检测滚动轴承需要加注固体润滑材料。
19.可选的,所述根据磨损状态和所述包络解调频谱的故障特征频率幅值的特征频率幅值对应关系,确定所述待检测滚动轴承需要更换固体润滑材料还是需要加注固体润滑材料,包括:
20.预先基于所述待检测滚动轴承的包络解调频谱中所述磨损部件的特征频率信号在固体润滑材料以及传播距离上的衰减特性,确定所述磨损部件的最大容忍磨损程度对应的特征频率幅度阈值;
21.若所述包络解调频谱的故障特征频率幅值小于所述特征频率幅度阈值,则所述待检测滚动轴承需要加注固体润滑材料;
22.若所述包络解调频谱的故障特征频率幅值大于等于所述特征频率幅度阈值,则所述待检测滚动轴承需要更换固体润滑材料。
23.可选的,所述基于所述待检测滚动轴承的包络解调频谱中所述磨损部件的特征频率信号在固体润滑材料以及传播距离上的衰减特性,确定所述磨损部件的最大容忍磨损程度对应的特征频率幅度阈值,包括:
24.调用阈值计算关系式确定特征频率幅度阈值,所述阈值计算关系式为:
[0025][0026]
式中,ai为所述特征频率幅度阈值,α为信号衰减影响系数,a
i0
为所述待检测滚动轴承处于所述磨损中级阶段时的初始值,d为磨损部件至传感器的距离,μ为固体润滑材料的锥入度。
[0027]
可选的,所述根据待检测滚动轴承的振动信号的包络解调频谱的故障特征频率及故障特征频率幅值,确定所述待检测滚动轴承的磨损信息之后,还包括:
[0028]
若所述待检测滚动轴承为所述第三磨损级别,则判定所述待检测滚动轴承需要更换固体润滑材料。
[0029]
可选的,所述基于所述待检测滚动轴承摩擦产生的声发射信号的变化规律确定所述固体润滑材料的加注量之前,还包括:
[0030]
通过调整超声波接收装置的信号放大率,获取背景噪声;
[0031]
根据所述背景噪声的频率范围调整所述超声波接收装置,以通过避免背景噪声频率段来消除所述背景噪声对所述待检测轴承所发出的超声波信号的影响;
[0032]
按照预设加注调整量,依次向所述待检测滚动轴承填充相应的固体润滑材料,并在加注所述固体润滑材料之后,获取紧邻所述待检测轴承外圈的超声波传感器的超声波幅值信号;
[0033]
按照所述固体润滑材料的加注顺序,若存在当前次加注所述固体润滑材料后的超声波幅值在其上一次加注所述固体润滑材料后的超声波幅值与其下一次加注所述固体润滑材料后的超声波幅值之间,则根据当前次加注所述固体润滑材料后的超声波幅值确定表征所述待检测轴承处于目标润滑状态的固定基准线。
[0034]
可选的,所述基于所述待检测滚动轴承摩擦产生的声发射信号的变化规律确定所述固体润滑材料的加注量,包括:
[0035]
响应工况调整指令,调整所述待检测滚动轴承的当前运行工况与所述固定基准线的确定过程对应的运行工况相同;
[0036]
响应参数调整指令,调整所述超声波接收装置的信号放大率与所述固定基准线的确定过程对应的信号放大率相同;
[0037]
根据所述固定基准线确定所述待检测滚动轴承的当前加注量。
[0038]
本发明实施例另一方面提供了一种基于信息融合的滚动轴承润滑脂加注管理装置,包括:
[0039]
磨损程度检测模块,用于基于预设磨损规则,根据待检测滚动轴承的振动信号的包络解调频谱的故障特征频率及故障特征频率幅值,确定所述待检测滚动轴承的磨损信息;
[0040]
润滑状态判断模块,用于若所述磨损信息包括表征所述待检测滚动轴承具有可视磨损痕迹特征,根据磨损状态和所述包络解调频谱的故障特征频率幅值的特征频率幅值对应关系,确定所述待检测滚动轴承需要更换固体润滑材料还是需要加注固体润滑材料;
[0041]
定量化加注模块,用于若所述待检测滚动轴承需要加注固体润滑材料,基于所述待检测滚动轴承摩擦产生的声发射信号的变化规律确定所述固体润滑材料的加注量。
[0042]
本发明实施例还提供了一种电子设备,包括处理器,所述处理器用于执行存储器中存储的计算机程序时实现如前任一项所述基于信息融合的滚动轴承润滑脂加注管理方法的步骤。
[0043]
本发明实施例最后还提供了一种可读存储介质,所述可读存储介质上存储有计算机程序,所述计算机程序被处理器执行时实现如前任一项所述基于信息融合的滚动轴承润滑脂加注管理方法的步骤。
[0044]
本技术提供的技术方案的优点在于,基于滚动轴承磨损发生发展过程中振动信号的变化规律,根据包络解调频谱判断轴承磨损程度,基于轴承磨损程度确定滚动轴承所填
充的固体润滑材料是加注还是更换还是保持不变,实现对滚动轴承内的固体润滑材料的填充量及污染状态精准检测,有利于保障滚动轴承的稳定运行,降低滚动轴承运行的故障风险,有效延长滚动轴承的使用寿命;通过滚动轴承的固体润滑材料加注过程中声发射信号的变化规律确定所填充的固体润滑材料的加注量,实现定量化加注固体润滑材料,避免固体润滑材料超量或者不足,从而使每次加注后滚动轴承都处于最佳润滑状态,进一步延长滚动轴承的使用寿命。
[0045]
此外,本发明实施例还针对基于信息融合的滚动轴承润滑脂加注管理方法提供了相应的实现装置、电子设备及可读存储介质,进一步使得所述方法更具有实用性,所述装置、电子设备及可读存储介质具有相应的优点。
[0046]
应当理解的是,以上的一般描述和后文的细节描述仅是示例性的,并不能限制本技术。
附图说明
[0047]
为了更清楚的说明本发明实施例或相关技术的技术方案,下面将对实施例或相关技术描述中所需要使用的附图作简单的介绍,显而易见地,下面描述中的附图仅仅是本发明的一些实施例,对于本领域普通技术人员来讲,在不付出创造性劳动的前提下,还可以根据这些附图获得其他的附图。
[0048]
图1为本发明实施例提供的一种基于信息融合的滚动轴承润滑脂加注管理方法的流程示意图;
[0049]
图2为本发明实施例提供的另一种基于信息融合的滚动轴承润滑脂加注管理方法的流程示意图;
[0050]
图3为本发明实施例提供的基于信息融合的滚动轴承润滑脂加注管理装置的一种具体实施方式结构图;
[0051]
图4为本发明实施例提供的电子设备的一种具体实施方式结构图。
具体实施方式
[0052]
为了使本技术领域的人员更好地理解本发明方案,下面结合附图和具体实施方式对本发明作进一步的详细说明。显然,所描述的实施例仅仅是本发明一部分实施例,而不是全部的实施例。基于本发明中的实施例,本领域普通技术人员在没有做出创造性劳动前提下所获得的所有其他实施例,都属于本发明保护的范围。
[0053]
本技术的说明书和权利要求书及上述附图中的术语“第一”、“第二”等是用于区别不同的对象,而不是用于描述特定的顺序。此外术语“包括”和“具有”以及二者的任何变形,意图在于覆盖不排他的包含。例如包含了一系列步骤或单元的过程、方法、系统、产品或设备没有限定于已列出的步骤或单元,而是可包括没有列出的步骤或单元。下面详细的说明本技术的各种非限制性实施方式。
[0054]
首先参见图1,图1为本发明实施例提供的一种基于信息融合的滚动轴承润滑脂加注管理方法的流程示意图,本发明实施例可包括以下内容:
[0055]
s101:基于预设磨损规则,根据待检测滚动轴承的振动信号的包络解调频谱的故障特征频率及故障特征频率幅值,确定待检测滚动轴承的磨损信息。
[0056]
可以理解的是,如果滚动轴承磨损较为严重,会产生明显的金属颗粒物,在旋转离心力的作用下,金属颗粒物会镶嵌在滚动轴承的固体润滑材料中,并分布在轴承滚动体周围,如果此时添加固体润滑材料,会将金属颗粒物挤压至滚动轴承的旋转部件内,这样不仅无法改善滚动轴承的润滑条件,还会加剧磨损,甚至直接导致滚动轴承抱死。因此,判断滚动轴承磨损的严重程度是确定加注还是直接更换其内所填充的固体润滑材料的前提条件。基于此,本步骤即是检测滚动轴承的磨损程度,其中,预设磨损规则用于定义滚动轴承的磨损程度,磨损程度可按照磨损的严重程度进行分级别表示,如无磨损、第一磨损级别用于表示轻微磨损,第二磨损级别用于表示中度磨损等;当然,也可直接使用阶段表示,比如无磨损阶段、初级磨损阶段、中度磨损阶段、重度磨损阶段等,所属领域技术人员可根据实际进行灵活调整。滚动轴承磨损产生的金属颗粒物可来自于轴承的滚珠、内圈、外圈以及保持架,由于各部件材质、离测点的距离不同以及固体润滑材料导致的信号删减作用,不同部件磨损的严重程度不仅与检测信号的幅值大小相关,还与产生磨损的具体部件相关。例如:由于保持架悬空设置于轴承内部,完全被润滑脂覆盖,其产生磨损时检测信号衰减较大;而轴承外圈更接近测点并且直接刚性接触,信号衰减较小,相同幅值的保持架磨损故障往往比外圈磨损故障严重得多。因此,在判断滚动轴承磨损程度时,不仅需要考虑检测信号幅值的大小,还需要判断出产生磨损的具体部件,而判断磨损部件以及磨损程度是声发射信号无法完成的,需要结合振动信号进行判断。本实施例的预设磨损规则还建立了不同的磨损程度与滚动轴承的振动信号的频率特征之间的对应关系,而滚动轴承的不同部件的振动信号不同,这样便可通过分析振动信号直接定位至具体的磨损部件以及该磨损部件的磨损程度。
[0057]
待检测滚动轴承即为要确定是否进行固体润滑材料更换或加注或保持不变的轴承,该待检测滚动轴承的振动信号可采用任何一种振动信号采集设备进行获取,本技术对此不作任何限定。待检测滚动轴承中所填充的润滑材料多种多样,如液体的润滑材料,但本实施例适用于对待检测滚动轴承的柔性的固体润滑材料的检测,所谓柔性的固体润滑材料是指其不同于液体固体润滑材料如润滑油,但其形状可变,如润滑脂。磨损信息用于表示待检测轴承的哪个部件发生了磨损且磨损的程度是否严重。
[0058]
s102:若磨损信息包括表征待检测滚动轴承具有可视磨损痕迹特征,根据磨损状态和包络解调频谱的故障特征频率幅值的特征频率幅值对应关系,确定待检测滚动轴承需要更换固体润滑材料还是需要加注固体润滑材料。
[0059]
在上述步骤确定磨损信息之后,对于没有磨损的情况,无需更换也无需加注固体润滑材料;对于处于初始磨损阶段的轴承,也即只有轻微的磨损,磨损部件上的磨损痕迹肉眼不可见,此时,只需要加注固体润滑材料,即可使待检测滚动轴承处于最佳的润滑状态。对于具有肉眼可见的磨损痕迹也即具有可视磨损痕迹特征的磨损阶段,该阶段由于不确定磨损是否产生金属颗粒以及所产生的金属颗粒是否会影响待检测滚动轴承的稳定运行,不确定固体润滑材料是否被严重污染,所以需要通过进一步检测来确定是加注还是更换。为了确定待检测滚动轴承内的固体润滑材料是需要更换还是加注,本实施例预先构建磨损状态和特征频率幅值的对应关系,滚动轴承的各部件如外圈、滚珠、内圈和保持架,特征频率的获取方法属于公知常识,可根据轴承设计参数计算或根据轴承型号查询,获取不同磨损状态下的特征频率幅值,便可构建不同部件的磨损状态和特征频率幅值的对应关系,用户
可预先定义需要进行更换固体润滑材料的磨损状态,若达到该磨损状态或磨损超过该状态,即判定需要进行更换;若没有达到该磨损状态,则只需要进行加注。基于上个步骤所得到的磨损信息需要确定待检测滚动轴承内的固体润滑材料是更换还是加注,通过分析待检测滚动轴承的振动信号的包络解调频谱得到故障特征频率幅值,通过故障特征频率幅值与磨损状态和特征频率幅值的对应关系来确定磨损部件的磨损状态,进而便可确定更换还是加注。
[0060]
s103:若待检测滚动轴承需要加注固体润滑材料,基于待检测滚动轴承摩擦产生的声发射信号的变化规律确定固体润滑材料的加注量。
[0061]
在前两个步骤确定需要加注固体润滑材料之后,本步骤通过分析待检测滚动轴承摩擦产生的声发射信号的变化规律来确定所需加注固体润滑材料的量。声发射信号基于声发射现象产生,所谓声发射现象是指润滑材料缺乏或者被污染时,轴承各部件之间的摩擦往往产生频率极高的声波,利用声发射信号判断润滑材料加注过程中的润滑状态。对待检测滚动轴承加注固体润滑材料时,随着加注量增加,待检测滚动轴承各相对运动部件之间的油膜逐渐建立起来,由摩擦形成的超声波幅值逐渐降低;各部件之间的油膜建立起来以后,若继续加注固体润滑材料如润滑脂会导致固体润滑材料过量,由于固体润滑材料散热系数较低,待检测滚动轴承旋转产生的热量不能及时散出,会导致待检测滚动轴承的温度升高,较高的温度会降低油脂的黏性,导致已经建立起来的油膜破坏,从而加剧待检测滚动轴承各部件之间的摩擦,使由摩擦形成的超声波幅值反而增大。因此,用待检测滚动轴承摩擦产生的声发射现象来评价固体润滑材料加注量,可以找出最佳的固体润滑材料加注量,并进行定量化的分析。
[0062]
在本发明实施例提供的技术方案中,基于滚动轴承磨损发生发展过程中振动信号的变化规律,根据包络解调频谱判断轴承磨损程度,基于轴承磨损程度确定滚动轴承所填充的固体润滑材料是加注还是更换还是保持不变,实现对滚动轴承内的固体润滑材料的填充量及污染状态精准检测,有利于保障滚动轴承的稳定运行,降低滚动轴承运行的故障风险,有效延长滚动轴承的使用寿命;通过滚动轴承的固体润滑材料加注过程中声发射信号的变化规律确定所填充的固体润滑材料的加注量,实现定量化加注固体润滑材料,避免固体润滑材料超量或者不足,从而使每次加注后滚动轴承都处于最佳润滑状态,进一步延长滚动轴承的使用寿命。
[0063]
在上述实施例中,对于如何执行步骤s101并不做限定,本实施例还给出待检测滚动轴承的磨损信息的一种可选的确定方式,可包括如下内容:
[0064]
获取待检测滚动轴承的振动信号;根据振动信号的包络解调频谱的特征频率,确定待检测滚动轴承的磨损部件;根据振动信号的包络解调频谱是否存在故障特征频率以及包络解调频谱中的故障特征频率幅值,确定磨损部件的磨损级别;根据磨损部件和磨损级别生成磨损信息。
[0065]
其中,磨损级别可包括第一磨损级别、第二磨损级别和第三磨损级别;第一磨损级别用于表示待检测滚动轴承处于磨损初始阶段,具有不可视磨损痕迹;第二磨损级别用于表示待检测滚动轴承处于磨损中级阶段,具有可视磨损痕迹特征;第三磨损级别用于表示待检测滚动轴承已有金属颗粒剥落。相应的,若待检测滚动轴承为第一磨损级别,则判定待检测滚动轴承需要加注固体润滑材料。若待检测滚动轴承为第二磨损级别,则基于上述实
施例的s102步骤判断待检测滚动轴承需要加注固体润滑材料还是直接更换固体润滑材料。若待检测滚动轴承为第三磨损级别,则判定待检测滚动轴承需要更换固体润滑材料。
[0066]
在本实施例中,滚动轴承正常运行时,振动幅值较小,解调波形无冲击信号,包络解调频谱中无轴承故障特征频率,此时油膜将滚动轴承相对运动部件之间进行了有效的隔离,无需添加固体润滑材料如润滑脂。滚动轴承的磨损故障发展可分为四个阶段:磨损初始阶段、第二阶段、第三阶段和第四阶段,对应的磨损程度分别为轻微、中度、严重和危急,各个阶段特点不同,滚动轴承磨损严重程度也不一样。滚动轴承磨损故障初始阶段也即第一磨损级别(轻微),振动幅值较小、产生噪声,解调波形可见非常短的冲击,包络解调频谱无明显故障特征频率,频率范围5khz-40khz,此时存在肉眼不可见的微小磨损,磨屑对固体润滑材料如润滑脂的性能几乎无影响,此时加注润滑脂可改善润滑条件,使轴承重归正常运行状态;滚动轴承故障第二阶段也即第二磨损级别(中度),存在摩擦和较小的冲击,包络解调频谱可见故障特征频率,频率范围1khz-5khz,此时滚动轴承存在肉眼可见的磨痕,包络解调频谱中故障特征频率的幅值越大磨损越严重,甚至有金属颗粒掉落,该阶段需要确定剥落金属颗粒物对固体润滑材料如润滑脂性能的影响,判断是加注还是更换固体润滑材料如润滑脂,从而改善滚动轴承润滑条件,延长轴承使用寿命;滚动轴承处于第三阶段也即第三磨损级别(严重),超高频幅值持续增大,出现由冲击产生的谐波和由载荷周期性变化调制形成的边频成分,可见轴承故障特征频率出现峰值;滚动轴承故障第四阶段也即第三磨损级别(危急),超高频幅值下降,周期性振动下降,背景噪声明显升高,形成“干草堆”,继续发展,其特征频率将完全消失,频谱更像是旋转松动模式。第三、第四阶段轴承有较大金属颗粒剥落,为避免突发事件,需更换轴承。由此可见,当滚动轴承的振动信号的包络解调频谱中无高频成分也不存在故障特征频率时,滚动轴承处于正常运行状态,无需加注固体润滑材料;当滚动轴承磨损故障处于初始阶段时,轴承没有明显的点蚀,只需进行润滑脂加注;当滚动轴承磨损故障处于第二阶段时,需要按照上述实施例的s102进行更换还是加注的判断;当滚动轴承处于第三、第四阶段时,存在较大的金属颗粒剥落,滚动轴承已损坏,此时应尽快更换轴承。
[0067]
为了便于实施,基于上述实施例,可基于不同部件的磨损状态和特征频率幅值的对应关系确定需要进行更换时的磨损状态也即最大容忍磨损程度所对应的特征频率幅值,本实施例称为特征频率幅度阈值,只需要通过比较两个数值便可实现待检测滚动轴承需要更换固体润滑材料还是需要加注固体润滑材料的判断,可包括下述内容:
[0068]
预先基于待检测滚动轴承的包络解调频谱中磨损部件的特征频率信号在固体润滑材料以及传播距离上的衰减特性,确定磨损部件的最大容忍磨损程度对应的特征频率幅度阈值;
[0069]
若包络解调频谱的故障特征频率幅值小于特征频率幅度阈值,则待检测滚动轴承需要加注固体润滑材料;
[0070]
若包络解调频谱的故障特征频率幅值大于等于特征频率幅度阈值,则待检测滚动轴承需要更换固体润滑材料。
[0071]
对于s102步骤,待检测滚动轴承处于包络解调频谱可见故障特征频率以及频谱中尚未出现轴承故障特征频率之间,可根据滚动轴承包络解调频谱中各部件特征频率信号在固体润滑材料以及传播距离上的衰减特性,采用包络解调频谱中故障特征频率幅值的大小
来判断磨损的严重程度。固体润滑材料越硬,传感器距离声发射源越近,信号衰减越小,为了提高固体润滑材料的状态检测精度,本实施例可调用阈值计算关系式确定本实施例的特征频率幅度阈值,阈值计算关系式可表示为:
[0072][0073]
式中,ai为特征频率幅度阈值,α为信号衰减影响系数,由信号传播的材料性能确定,可根据材料材质查询;a
i0
为待检测滚动轴承处于磨损中级阶段时的初始值,由现有标准确定;d为磨损部件至传感器的距离;μ为固体润滑材料的锥入度,该值与材料硬度成反相关关系,由固体润滑材料的稠度号确定,固体润滑材料的锥入度与稠度号的对应关系可如表1所示:
[0074]
表1固体润滑材料的锥入度与稠度号的对应关系
[0075]
稠度号锥入度范围状态000#445~475液态00#400~430接近液态0#355~385极软1#310~340非常软2#265~295软3#175~205中4#130~160硬5#85~115非常硬
[0076]
例如:对于型号为nu220ecp的某电机滚动轴承,其采用7008航空润滑脂,稠度号3#,设备材料为铸铁,通过调用阈值计算关系式计算滚动轴承的各部件存在明显金属剥落时对应的特征频率域值如表2所示:
[0077]
表2包络解调频谱中特征频率幅值与部件磨损状态的对应关系
[0078][0079]
当待检测滚动轴承磨损故障处于第二阶段,对于振动信号中的各特定部件如外圈、滚珠、内圈和保持架,当包络解调频谱中故障特征频率幅值小于表2中相应的特征频率幅度阈值时,应加注固体润滑材料如润滑脂;当包络解调频谱中故障特征频率幅值大于等于表2中相应的特征频率幅度阈值时,应更换固体润滑材料。
[0080]
其它滚动轴承也可以根据轴承型号以及安装部位确定包络解调频谱中特征频率幅值与部件磨损状态的对应关系。另外,滚动轴承各部件特征频率的获取方法属于公知常识,可根据轴承设计参数计算或根据轴承型号查询,此处便不在赘述。
[0081]
上述实施例对如何定量化实现对固体润滑材料的加注,本实施例还给出一种可选
的实施方式,可包括:
[0082]
通过调整超声波接收装置的信号放大率,获取背景噪声;
[0083]
根据背景噪声的频率范围调整超声波接收装置,从而避开背景噪声频率段,进而可用于消除背景噪声对待检测轴承所发出的超声波信号的影响;
[0084]
按照预设加注调整量,依次向待检测滚动轴承填充相应的固体润滑材料,并在加注固体润滑材料之后,获取紧邻待检测轴承外圈的超声波传感器的超声波幅值信号;
[0085]
按照固体润滑材料的加注顺序,若存在当前次加注固体润滑材料后的超声波幅值在其上一次加注所述固体润滑材料后的超声波幅值与其下一次加注固体润滑材料后的超声波幅值之间,则根据当前次加注所述固体润滑材料后的超声波幅值确定表征待检测轴承处于目标润滑状态的固定基准线。
[0086]
进一步的,为了提高固定基准线的精度,重复上述步骤多次,得到多个位于前一次和后一次加注固体润滑材料后的超声波幅值之间的当前次加注固体润滑材料后的目标超声波幅值,若这多个目标超声波幅值之间的波动小于预设阈值如5%,则根据多个目标超声波幅值的平均值确定该固定基准线。
[0087]
在本实施例中,在对滚动轴承加注固体润滑材料如润滑脂时,随着固体润滑材料的加注量增加,滚动轴承各相对运动部件之间的油膜逐渐建立起来,由摩擦形成的超声波幅值逐渐降低;各部件之间的油膜建立起来以后,若继续加注固体润滑材料会导致固体润滑材料过量,由于固体润滑材料如润滑脂散热系数较低,滚动轴承旋转产生的热量不能及时散出,会导致滚动轴承的温度升高,较高的温度会降低固体润滑材料的黏性,导致已经建立起来的油膜破坏,从而加剧滚动轴承各部件之间的摩擦,使由摩擦形成的超声波幅值反而增大。因此,用滚动轴承摩擦产生的声发射信号来监测润滑脂的加注过程,可以使润滑脂加注量处于最佳状态,并可进行定量化分析。
[0088]
本实施例通过滚动轴承固体润滑材料加注过程中声发射信号幅值的变化规律进行定量化加注过程为:调整超声波接受装置的信号放大率,获取背景噪声,用于排除背景噪声对声发射信号的影响;将超声波传感器紧贴离轴承外圈最近的位置,调整接受频率范围监测轴承超声波幅值,按照预设加注调整量慢慢加入少量的固体润滑材料,等待直至超声波幅值稳定:
①
若超声波幅值较加注之前降低,则需继续增加少量固体润滑材料,直到超声波值略有升高时,说明滚动轴承已经达到了最佳润滑状态,立即停止添加固体润滑材料;此时超声波的测量值可用于确定轴承在下一次润滑过程中是否需要润滑的参考值,收集三个及以上数据后,若数值波动小于5%,其测量平均值可用于确定该固定基准线。
②
若超声波值较加注之前有所升高,则停止添加固体润滑材料。
[0089]
在固定基准线确定之后,上述实施例的s103的一种可选的实施过程可为:响应工况调整指令,调整待检测滚动轴承的当前运行工况与固定基准线的确定过程对应的运行工况相同;响应参数调整指令,调整超声波接收装置的信号放大率与固定基准线的确定过程对应的信号放大率相同;根据固定基准线确定待检测滚动轴承的当前加注量。
[0090]
在本实施例中,调整设备至与之前固体润滑材料加注时运行工况相同;调整超声波接受装置的放大率与之前加注时相同,将超声波传感器紧贴离轴承外圈最近的位置,获取超声值读数并与基线对比;添加固体润滑材料,使测量值尽可能地接近该固定基准线时,固体润滑材料加注完毕。若更换滚动轴承或固体润滑材料型号后应重新测定该固定基准
线。
[0091]
由上可知,本实施例通过声发射信号的变化规律固定固体润滑材料的加注基线后,使润固体润滑材料的加注过程有据可依,实现了定量化加注,实用性更好,普适性更强。
[0092]
为了使所属领域技术人员更加清楚明白本技术的技术方案,本技术还提供了一个示意性例子,本实施例的待检测滚动轴承为型号为nu220ecp的滚动轴承,其内填充的固体润滑材料为7008航空润滑脂,结合图2,对该滚动轴承的润滑脂的检测过程可包括:
[0093]
对滚动轴承进行振动监测分析,获取滚动轴承的振动信号,根据振动信号的包络解调频率谱中的故障特征频率及幅值判断是否存在明显金属剥落,若存在,则直接更换润滑脂。若不存在,则判断包络解调频率谱中是否存在35khz左右高频成分,如存在,则滚动轴承正常运行,无需更换润滑脂也无需加注润滑脂,若存在,则调整超声波接受装置的信号放大率,获取背景噪声,以排除背景噪声的影响。将超声波传感器紧贴离轴承外圈最近的位置,监测轴承超声波幅值为45db,慢慢加入少量的润滑脂,等待直至超声波幅值稳定,发现超声波幅值降为41.9db,继续加注润滑脂,润滑脂加注量与超声波幅值对应关系如表3所示。
[0094]
表3润滑脂加注量与声发射信号幅值对应关系
[0095]
次数0123456加注量(g)20202020202020声发射信号幅值(db)45.041.939.236.834.732.833.6
[0096]
由表3可知,第五次加注后声发射信号幅值最小,记录本次幅值。
[0097]
当然,为了提高加注精准度,在加注过程中,每次加注量可以不一样,比如开始加注时一次加注量可以小一些,然后根据超声波幅值的变化情况调整每次的加注量。该滚动轴承后两次加注采用相同的办法,记录声发射信号最小幅值分别为32.5db和33.1db,三次加注声发射信号最小幅值波动小于5%,求取测量平均值为32.8db用于固定基线。基线固定后下一次如需加注润滑脂时,以32.8db为基线,当声发射信号幅值大于32.8db时,应添加润滑脂至声发射信号幅值接近32.8db为止。为便于工程应用,偏离基线可根据轴承型号和设备运行情况设置为一个阈值,例如该设备规定偏离基线20%时,表明需要添加润滑脂,那么当声发射信号幅值大于32.8
×
(1+20%)=39.4db时,表明需要添加润滑脂,按上述步骤完成润滑脂加注即可。
[0098]
本实施例基于滚动轴承磨损发生发展过程中振动及声发射信号的变化规律,利用振动信号判断磨损部件以及磨损程度,利用声发射信号判断润滑脂加注过程中的润滑状态,通过融合振动包络解调谱特征频率幅值和声发射信号强度变化规律指导滚动轴承润滑脂管理,避免了盲目性加注或更换以及加注过程带来的风险,并且实现了定量化管理,便于推广应用,具体有益效果如下:
[0099]
基于滚动轴承磨损发生发展过程中振动信号的变化规律,根据包络解调频谱中特征频率幅值的大小判断轴承磨损程度,根据轴承磨损程度确定润滑脂应采取的管理措施(加注、更换、保持不变),延长了轴承使用寿命,避免了润滑脂在添加过程中存在的风险;通过滚动轴承润滑脂加注过程中声发射信号的变化规律指导润滑脂加注,使每次加注后滚动轴承都处于最佳润滑状态,避免润滑脂过量或者不足;通过声发射信号的变化规律固定润滑脂加注基线后,使润滑脂加注过程有据可依,实现了定量化加注,便于推广应用。
[0100]
需要说明的是,本技术中各步骤之间没有严格的先后执行顺序,只要符合逻辑上的顺序,则这些步骤可以同时执行,也可按照某种预设顺序执行,图1-图2只是一种示意方式,并不代表只能是这样的执行顺序。
[0101]
本发明实施例还针对基于信息融合的滚动轴承润滑脂加注管理方法提供了相应的装置,进一步使得方法更具有实用性。其中,装置可从功能模块的角度和硬件的角度分别说明。下面对本发明实施例提供的基于信息融合的滚动轴承润滑脂加注管理装置进行介绍,下文描述的基于信息融合的滚动轴承润滑脂加注管理装置与上文描述的基于信息融合的滚动轴承润滑脂加注管理方法可相互对应参照。
[0102]
基于功能模块的角度,参见图3,图3为本发明实施例提供的基于信息融合的滚动轴承润滑脂加注管理装置在一种具体实施方式下的结构图,该装置可包括:
[0103]
磨损程度检测模块301,用于基于预设磨损规则,根据待检测滚动轴承的振动信号的包络解调频谱的故障特征频率及故障特征频率幅值,确定待检测滚动轴承的磨损信息;
[0104]
润滑状态判断模块302,用于若磨损信息包括表征待检测滚动轴承具有可视磨损痕迹特征,根据磨损状态和包络解调频谱的故障特征频率幅值的特征频率幅值对应关系,确定待检测滚动轴承需要更换固体润滑材料还是需要加注固体润滑材料;
[0105]
定量化加注模块303,用于若待检测滚动轴承需要加注固体润滑材料,基于待检测滚动轴承摩擦产生的声发射信号的变化规律确定固体润滑材料的加注量。
[0106]
可选的,在本实施例的一些实施方式中,上述磨损程度检测模块301还可用于:获取待检测滚动轴承的振动信号;根据振动信号的包络解调频谱的特征频率,确定待检测滚动轴承的磨损部件;根据振动信号的包络解调频谱是否存在故障特征频率以及包络解调频谱中的故障特征频率幅值,确定磨损部件的磨损级别;根据磨损部件和磨损级别生成磨损信息;其中,磨损级别包括第一磨损级别、第二磨损级别和第三磨损级别;第一磨损级别用于表示待检测滚动轴承处于磨损初始阶段,具有不可视磨损痕迹;第二磨损级别用于表示待检测滚动轴承处于磨损中级阶段,具有可视磨损痕迹特征;第三磨损级别用于表示待检测滚动轴承已有金属颗粒剥落。
[0107]
作为上述实施例的一种可选的实施方式,上述磨损程度检测模块301可进一步用于:若待检测滚动轴承为第一磨损级别,则判定待检测滚动轴承需要加注固体润滑材料。
[0108]
作为上述实施例的另一种可选的实施方式,上述磨损程度检测模块301还可进一步用于:预先基于待检测滚动轴承的包络解调频谱中磨损部件的特征频率信号在固体润滑材料以及传播距离上的衰减特性,确定磨损部件的最大容忍磨损程度对应的特征频率幅度阈值;若包络解调频谱的故障特征频率幅值小于特征频率幅度阈值,则待检测滚动轴承需要加注固体润滑材料;若包络解调频谱的故障特征频率幅值大于等于特征频率幅度阈值,则待检测滚动轴承需要更换固体润滑材料。
[0109]
作为上述实施例的另一种可选的实施方式,上述磨损程度检测模块301还可进一步用于:调用阈值计算关系式确定特征频率幅度阈值,所述阈值计算关系式为:
[0110][0111]
式中,ai为特征频率幅度阈值,α为信号衰减影响系数,a
i0
为待检测滚动轴承处于磨损中级阶段时的初始值,d为磨损部件至传感器的距离,μ为固体润滑材料的锥入度。
[0112]
作为上述实施例的再一种可选的实施方式,上述磨损程度检测模块301还可进一步用于:若待检测滚动轴承为第三磨损级别,则判定待检测滚动轴承需要更换固体润滑材料。
[0113]
可选的,在本实施例的另一些实施方式中,所述装置例如还可以包括基线确定模块,用于通过调整超声波接收装置的信号放大率,获取背景噪声;根据背景噪声的频率范围调整超声波接收装置,从而避开背景噪声频率段,进而可用于消除背景噪声对待检测轴承所发出的超声波信号的影响;按照预设加注调整量,依次向待检测滚动轴承填充相应的固体润滑材料,并在加注固体润滑材料之后,获取紧邻待检测轴承外圈的超声波传感器的超声波幅值信号;按照所述固体润滑材料的加注顺序,若存在当前次加注所述固体润滑材料后的超声波幅值在其上一次加注所述固体润滑材料后的超声波幅值与其下一次加注所述固体润滑材料后的超声波幅值之间,则根据当前次加注所述固体润滑材料后的超声波幅值确定表征待检测轴承处于目标润滑状态的固定基准线。
[0114]
作为上述实施例的一种可选的实施方式,上述定量化加注模块303还可用于:响应工况调整指令,调整待检测滚动轴承的当前运行工况与固定基准线的确定过程对应的运行工况相同;响应参数调整指令,调整超声波接收装置的信号放大率与固定基准线的确定过程对应的信号放大率相同;根据固定基准线确定待检测滚动轴承的当前加注量。
[0115]
本发明实施例所述基于信息融合的滚动轴承润滑脂加注管理装置的各功能模块的功能可根据上述方法实施例中的方法具体实现,其具体实现过程可以参照上述方法实施例的相关描述,此处不再赘述。
[0116]
由上可知,本发明实施例实现了对滚动轴承内的固体润滑材料的精准检测,有利于保障滚动轴承的稳定运行,可有效降低滚动轴承运行的故障风险。
[0117]
上文中提到的基于信息融合的滚动轴承润滑脂加注管理装置是从功能模块的角度描述,进一步的,本技术还提供一种电子设备,是从硬件角度描述。图4为本技术实施例提供的电子设备在一种实施方式下的结构示意图。如图4所示,该电子设备包括存储器40,用于存储计算机程序;处理器41,用于执行计算机程序时实现如上述任一实施例提到的基于信息融合的滚动轴承润滑脂加注管理方法的步骤。
[0118]
其中,处理器41可以包括一个或多个处理核心,比如4核心处理器、8核心处理器,处理器41还可为控制器、微控制器、微处理器或其他数据处理芯片等。处理器41可以采用dsp(digital signal processing,数字信号处理)、fpga(field-programmable gate array,现场可编程门阵列)、pla(programmable logic array,可编程逻辑阵列)中的至少一种硬件形式来实现。处理器41也可以包括主处理器和协处理器,主处理器是用于对在唤醒状态下的数据进行处理的处理器,也称cpu(central processing unit,中央处理器);协处理器是用于对在待机状态下的数据进行处理的低功耗处理器。在一些实施例中,处理器41可以集成有gpu(graphics processing unit,图像处理器),gpu用于负责显示屏所需要显示的内容的渲染和绘制。一些实施例中,处理器41还可以包括ai(artificial intelligence,人工智能)处理器,该ai处理器用于处理有关机器学习的计算操作。
[0119]
存储器40可以包括一个或多个计算机可读存储介质,该计算机可读存储介质可以是非暂态的。存储器40还可包括高速随机存取存储器以及非易失性存储器,比如一个或多个磁盘存储设备、闪存存储设备。存储器40在一些实施例中可以是电子设备的内部存储单
元,例如服务器的硬盘。存储器40在另一些实施例中也可以是电子设备的外部存储设备,例如服务器上配备的插接式硬盘,智能存储卡(smart media card,smc),安全数字(secure digital,sd)卡,闪存卡(flash card)等。进一步地,存储器40还可以既包括电子设备的内部存储单元也包括外部存储设备。存储器40不仅可以用于存储安装于电子设备的应用软件及各类数据,例如:执行基于信息融合的滚动轴承润滑脂加注管理方法过程中的程序的代码等,还可以用于暂时地存储已经输出或者将要输出的数据。本实施例中,存储器40至少用于存储以下计算机程序401,其中,该计算机程序被处理器41加载并执行之后,能够实现前述任一实施例公开的基于信息融合的滚动轴承润滑脂加注管理方法的相关步骤。另外,存储器40所存储的资源还可以包括操作系统402和数据403等,存储方式可以是短暂存储或者永久存储。其中,操作系统402可以包括windows、unix、linux等。数据403可以包括但不限于基于信息融合的滚动轴承润滑脂加注管理结果对应的数据等。
[0120]
在一些实施例中,上述电子设备还可包括有显示屏42、输入输出接口43、通信接口44或者称为网络接口、电源45以及通信总线46。其中,显示屏42、输入输出接口43比如键盘(keyboard)属于用户接口,可选的用户接口还可以包括标准的有线接口、无线接口等。可选地,在一些实施例中,显示器可以是led显示器、液晶显示器、触控式液晶显示器以及oled(organic light-emitting diode,有机发光二极管)触摸器等。显示器也可以适当的称为显示屏或显示单元,用于显示在电子设备中处理的信息以及用于显示可视化的用户界面。通信接口44可选的可以包括有线接口和/或无线接口,如wi-fi接口、蓝牙接口等,通常用于在电子设备与其他电子设备之间建立通信连接。通信总线46可以是外设部件互连标准(peripheral component interconnect,简称pci)总线或扩展工业标准结构(extended industry standard architecture,简称eisa)总线等。该总线可以分为地址总线、数据总线、控制总线等。为便于表示,图4中仅用一条粗线表示,但并不表示仅有一根总线或一种类型的总线。
[0121]
本领域技术人员可以理解,图4中示出的结构并不构成对该电子设备的限定,可以包括比图示更多或更少的组件,例如还可包括实现各类功能的传感器47。
[0122]
本发明实施例所述电子设备的各功能模块的功能可根据上述方法实施例中的方法具体实现,其具体实现过程可以参照上述方法实施例的相关描述,此处不再赘述。
[0123]
由上可知,本发明实施例实现了对滚动轴承内的固体润滑材料的精准检测,有利于保障滚动轴承的稳定运行,可有效降低滚动轴承运行的故障风险。
[0124]
可以理解的是,如果上述实施例中的基于信息融合的滚动轴承润滑脂加注管理方法以软件功能单元的形式实现并作为独立的产品销售或使用时,可以存储在一个计算机可读取存储介质中。基于这样的理解,本技术的技术方案本质上或者说对现有技术做出贡献的部分或者该技术方案的全部或部分可以以软件产品的形式体现出来,该计算机软件产品存储在一个存储介质中,执行本技术各个实施例方法的全部或部分步骤。而前述的存储介质包括:u盘、移动硬盘、只读存储器(read-only memory,rom)、随机存取存储器(random access memory,ram)、电可擦除可编程rom、寄存器、硬盘、多媒体卡、卡型存储器(例如sd或dx存储器等)、磁性存储器、可移动磁盘、cd-rom、磁碟或者光盘等各种可以存储程序代码的介质。
[0125]
基于此,本发明实施例还提供了一种可读存储介质,存储有计算机程序,该计算机
程序被处理器执行时如上任意一实施例所述基于信息融合的滚动轴承润滑脂加注管理方法的步骤。
[0126]
本说明书中各个实施例采用递进的方式描述,每个实施例重点说明的都是与其它实施例的不同之处,各个实施例之间相同或相似部分互相参见即可。对于实施例公开的硬件包括装置及电子设备而言,由于其与实施例公开的方法相对应,所以描述的比较简单,相关之处参见方法部分说明即可。
[0127]
专业人员还可以进一步意识到,结合本文中所公开的实施例描述的各示例的单元及算法步骤,能够以电子硬件、计算机软件或者二者的结合来实现,为了清楚地说明硬件和软件的可互换性,在上述说明中已经按照功能一般性地描述了各示例的组成及步骤。这些功能究竟以硬件还是软件方式来执行,取决于技术方案的特定应用和设计约束条件。专业技术人员可以对每个特定的应用来使用不同方法来实现所描述的功能,但是这种实现不应认为超出本发明的范围。
[0128]
以上对本技术所提供的一种基于信息融合的滚动轴承润滑脂加注管理方法进行了详细介绍。本文中应用了具体个例对本发明的原理及实施方式进行了阐述,以上实施例的说明只是用于帮助理解本发明的方法及其核心思想。应当指出,对于本技术领域的普通技术人员来说,在不脱离本发明原理的前提下,还可以对本技术进行若干改进和修饰,这些改进和修饰也落入本技术权利要求的保护范围内。