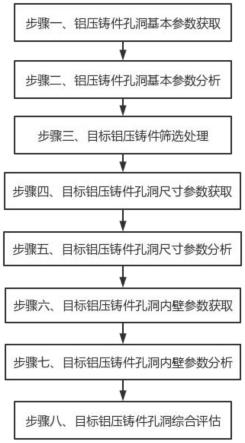
1.本发明涉及加工零件孔洞检测领域,涉及到基于机器视觉的铝合金机加工零件孔洞检测方法。
背景技术:2.随着科学技术的发展,铝合金机加工技术的使用越来越广泛,同时对铝合金机加工零件的质量要求也不断提高,特别是铝合金机加工零件孔洞的检测,要求十分严格,如果铝合金机加工零件的孔洞不符合要求,将直接影响到加工零件的使用,因此对铝合金机加工零件孔洞进行检测,具有重要意义。
3.现有的铝合金机加工零件孔洞检测方法存在一些弊端:一方面,在对加工零件的孔洞进行检测的时候,没有根据不合格孔洞的显著特征,如孔洞的形状或数量不匹配,对加工零件进行初次筛选并对筛选后的加工零件孔洞进行深度质检,进而加大了加工零件孔洞深度质检的对象范围,降低质检效率。
4.一方面,在对加工零件孔洞的尺寸进行检测时,质检的指标不够全面,没有对孔洞的直径、位置、深度和垂直度进行综合分析,孔洞的直径过大过小、位置偏移、深度过深过浅及洞孔打偏均会影响到后续加工零件与其配套零件的组装,使得加工零件的组装不贴合,甚至无法完成组装,进而使得加工零件孔洞尺寸质检结果的准确性和可靠性都比较低。
5.另一方面,缺乏对加工零件孔洞内壁的分析,如加工零件孔洞内壁的气孔和螺纹,加工零件孔洞内壁存在过多气孔,会降低加工零件的力学性能,影响加工零件的使用效果,同时降低加工零件的表面光泽度,加工零件孔洞内壁螺纹不规范,会使得加工零件的配套零件无法拧紧或造成螺纹损坏。
技术实现要素:6.针对上述问题,本发明提出了基于机器视觉的铝合金机加工零件孔洞检测方法,具体技术方案如下:基于机器视觉的铝合金机加工零件孔洞检测方法,包括如下步骤:步骤一、铝压铸件孔洞基本参数获取:获取铝合金机加工零件生产线上各铝压铸件表面孔洞的基本参数,将其记为各铝压铸件表面孔洞的基本参数,其中基本参数包括形状匹配度和数量。
7.步骤二、铝压铸件孔洞基本参数分析:根据各铝压铸件表面孔洞的基本参数,分析得到各铝压铸件的孔洞基本参数符合系数。
8.步骤三、目标铝压铸件筛选处理:根据各铝压铸件的孔洞基本参数符合系数,筛选孔洞基本参数合格的各铝压铸件,并将孔洞基本参数合格的各铝压铸件记为各目标铝压铸件。
9.步骤四、目标铝压铸件孔洞尺寸参数获取:获取各目标铝压铸件表面各孔洞的尺寸参数,其中尺寸参数包括直径、相对位置偏离度、深度和垂直度。
10.步骤五、目标铝压铸件孔洞尺寸参数分析:根据各目标铝压铸件表面各孔洞的尺
寸参数,分析得到各目标铝压铸件表面各孔洞的尺寸参数符合系数。
11.步骤六、目标铝压铸件孔洞内壁参数获取:获取各目标铝压铸件表面各孔洞的内壁参数,其中内壁参数包括气孔面积、气孔直径和螺纹规范度。
12.步骤七、目标铝压铸件孔洞内壁参数分析:根据各目标铝压铸件表面各孔洞的内壁参数,分析得到各目标铝压铸件表面各孔洞的内壁参数符合系数。
13.步骤八、目标铝压铸件孔洞综合评估:根据各目标铝压铸件表面各孔洞的尺寸参数符合系数和内壁参数符合系数,评估得到各目标铝压铸件表面各孔洞的合格指数,并进行处理。
14.在上述实施例的基础上,所述步骤一中获取各铝压铸件表面孔洞的基本参数,具体方法为:通过高清摄像机获取各铝压铸件的加工表面图像,根据各铝压铸件的加工表面图像,得到各铝压铸件加工表面图像中各孔洞区域,根据各铝压铸件加工表面图像中各孔洞区域,得到各铝压铸件表面孔洞的数量和形状匹配度,将其分别记为ai和bi,i表示第i个铝压铸件的编号,i=1,2,...,n。
15.在上述实施例的基础上,所述步骤二中分析得到各铝压铸件的孔洞基本参数符合系数,具体过程为:将各铝压铸件表面孔洞的数量ai和形状匹配度bi代入公式得到各铝压铸件的孔洞基本参数符合系数βi,其中a
标
表示数据库中存储的铝压铸件表面孔洞的标准数量,b
设
表示预设的铝压铸件表面孔洞形状匹配度的阈值,χ1、χ2分别表示预设的铝压铸件表面孔洞数量和孔洞形状匹配度的权重因子。
16.在上述实施例的基础上,所述步骤三的具体分析过程为:将各铝压铸件的孔洞基本参数符合系数与预设的合格铝压铸件对应的孔洞基本参数符合系数范围进行比对,若某铝压铸件的孔洞基本参数符合系数处于预设的合格铝压铸件对应的孔洞基本参数符合系数范围之内,表明该铝压铸件的孔洞基本参数合格,统计孔洞基本参数合格的各铝压铸件,将其记为各目标铝压铸件,反之,表明该铝压铸件的孔洞基本参数不合格,统计孔洞基本参数不合格的各铝压铸件,并将孔洞基本参数不合格的各铝压铸件放置至指定区域。
17.在上述实施例的基础上,所述步骤四中获取各目标铝压铸件表面各孔洞的直径和相对位置偏离度,具体方法为:根据各铝压铸件的加工表面图像,筛选得到各目标铝压铸件的加工表面图像,在各目标铝压铸件的加工表面图像中按照预设的坐标系构建方法构建二维坐标系;
18.按照预设的标记点选取原则在各目标铝压铸件加工表面图像中各孔洞圆周上进行各次标记点选取操作,得到各次标记点选取操作中各目标铝压铸件加工表面图像中各孔洞圆周上各标记点,将其记为各次标记点选取操作中各目标铝压铸件各孔洞圆周上各标记点,获取各次标记点选取操作中各目标铝压铸件各孔洞圆周上各标记点的坐标,将各次标记点选取操作中各目标铝压铸件各孔洞圆周上各标记点的坐标代入求圆方程,得到各次标记点选取操作中各目标铝压铸件各孔洞对应的圆方程,根据各次标记点选取操作中各目标铝压铸件各孔洞对应的圆方程,得到各次标记点选取操作中各目标铝压铸件各孔洞对应的直径和圆心坐标,对各次标记点选取操作中各目标铝压铸件各孔洞对应的直径进行平均值计算,得到各目标铝压铸件表面各孔洞的直径,将其记为j表示j个目标铝压铸件的编
号,j=1,2,...,m,g表示目标铝压铸件表面第g个孔洞的编号,g=1,2,...,h,对各次标记点选取操作中各目标铝压铸件各孔洞对应的圆心坐标进行平均值计算,得到各目标铝压铸件表面各孔洞的圆心坐标,将其记为
19.从数据库中提取铝压铸件加工表面的图纸,按照目标铝压铸件加工表面图像中二维坐标系的构建方法,在铝压铸件加工表面图纸中构建二维坐标系,获取铝压铸件加工表面图纸中各孔洞的圆心坐标,对铝压铸件加工表面图纸中各孔洞的圆心坐标进行设定比例的缩放,得到铝压铸件加工表面各孔洞的标准圆心坐标,将其记为(x
g标
,y
g标
),将各目标铝压铸件表面各孔洞的圆心坐标代入公式得到各目标铝压铸件表面各孔洞的相对位置偏离度其中ε表示预设的目标铝压铸件表面孔洞的相对位置偏离度的修正因子,δc
设
表示预设的目标铝压铸件表面孔洞圆心偏移距离的阈值。
20.在上述实施例的基础上,所述步骤四中获取各目标铝压铸件表面各孔洞的深度和垂直度,具体方式为:按照预设的深度检测点布设原则,在各目标铝压铸件表面各孔洞的洞口边沿布设各深度检测点,利用激光测距仪获取各目标铝压铸件表面各孔洞洞口边沿各深度检测点的深度,对各目标铝压铸件表面各孔洞洞口边沿各深度检测点的深度进行平均值计算,得到各目标铝压铸件表面各孔洞的深度,将其记为
21.按照预设的探测点布设原则,在各目标铝压铸件表面各孔洞的洞口边沿布设各探测点,作各目标铝压铸件表面各孔洞洞口边沿各探测点到孔洞底面的垂线,将其记为各目标铝压铸件表面各孔洞洞口边沿各探测点的内射线,获取各目标铝压铸件表面各孔洞洞口边沿各探测点的内射线与竖直基准线之间的夹角,将其记为各目标铝压铸件表面各孔洞洞口边沿各探测点对应的孔洞倾斜角,进一步分析得到各目标铝压铸件表面各孔洞的垂直度,将其记为
22.在上述实施例的基础上,所述步骤五中分析得到各目标铝压铸件表面各孔洞的尺寸参数符合系数,具体方法为:将各目标铝压铸件表面各孔洞的直径相对位置偏离度深度和垂直度代入公式得到各目标铝压铸件表面各孔洞的尺寸参数符合系数其中e表示自然常数,d
标
、f
标
分别表示数据库中存储的铝压铸件表面孔洞的标准直径和标准深度,δ
设
、φ
设
分别表示预设的目标铝压铸件表面孔洞的相对位置偏离度阈值和垂直度阈值,η1、η2、η3、η4分别表示预设的目标铝压铸件表面孔洞的直径、相对位置偏离度、深度和垂直度的权重因子。
23.在上述实施例的基础上,所述步骤六中各目标铝压铸件表面各孔洞的内壁参数,具体获取方法为:通过高倍显微镜获取各目标铝压铸件表面各孔洞的内壁显微图像,根据各目标铝压铸件表面各孔洞的内壁显微图像,得到各目标铝压铸件表面各孔洞的气孔面积
和气孔直径,将其分别记为和
24.根据各目标铝压铸件表面各孔洞的内壁显微图像,得到各目标铝压铸件表面各孔洞内壁的螺纹图像,进一步分析得到目标铝压铸件表面各孔洞的螺纹规范度,将其记为
25.在上述实施例的基础上,所述所述步骤七中分析得到各目标铝压铸件表面各孔洞的内壁参数符合系数,具体方法为:将各目标铝压铸件表面各孔洞的气孔面积气孔直径和螺纹规范度代入公式得到各目标铝压铸件表面各孔洞的内壁参数符合系数其中τ表示预设的目标铝压铸件表面孔洞的内壁参数符合系数修正因子,s
设
、l
设
、κ
设
分别表示预设的目标铝压铸件表面孔洞的允许气孔面积、允许气孔直径和螺纹规范度阈值,λ1、λ2、λ3分别表示预设的目标铝压铸件表面孔洞的气孔面积、气孔直径和螺纹规范度的权重因子。
26.在上述实施例的基础上,所述所述步骤八中具体分析过程为:将各目标铝压铸件表面各孔洞的尺寸参数符合系数和内壁参数符合系数代入公式得到各目标铝压铸件表面各孔洞的合格指数其中ψ1、ψ2分别表示预设的目标铝压铸件表面孔洞的尺寸参数符合系数和内壁参数符合系数的权重因子;
27.将各目标铝压铸件表面各孔洞的合格指数与预设的合格指数阈值进行比较,若某目标铝压铸件表面某孔洞的合格指数小于预设的合格指数阈值,则该目标铝压铸件孔洞不合格,筛选出孔洞不合格的各目标铝压铸件,并将孔洞不合格的各目标铝压铸件的编号发送至铝合金机加工零件质量管理部门。
28.相对于现有技术,本发明所述的基于机器视觉的铝合金机加工零件孔洞检测方法以下有益效果:
29.1.本发明提供的基于机器视觉的铝合金机加工零件孔洞检测方法,通过获取各铝压铸件表面孔洞的基本参数,分析得到各铝压铸件的孔洞基本参数符合系数,进一步筛选得到各目标铝压铸件,获取各目标铝压铸件表面各孔洞的尺寸参数和内壁参数,分析得到各目标铝压铸件表面各孔洞的尺寸参数符合系数和内壁参数符合系数,实现对铝压铸件孔洞的全面化、深度化检测,为铝压铸件的加工质量提供保障。
30.2.本发明提供的基于机器视觉的铝合金机加工零件孔洞检测方法,通过获取各铝压铸件表面孔洞的形状匹配度和数量,分析得到各铝压铸件的孔洞基本参数符合系数,根据各铝压铸件的孔洞基本参数符合系数,筛选得到孔洞基本参数合格的各目标铝压铸件,根据不合格孔洞的显著特征对加工零件进行初次筛选并对筛选后的加工零件孔洞进行深度质检,进而缩小加工零件孔洞深度质检对象范围,提高质检效率。
31.3.本发明提供的基于机器视觉的铝合金机加工零件孔洞检测方法,通过获取各目标铝压铸件表面各孔洞的直径、相对位置偏离度、深度和垂直度,分析得到各目标铝压铸件表面各孔洞的尺寸参数符合系数,从直径、位置、深度和垂直度对加工零件孔洞的尺寸进行综合分析,丰富尺寸质检指标的多样化,使得加工零件与其配套零件的组装更加贴合,进而
提高加工零件孔洞尺寸质检结果的准确性和可靠性。
32.4.本发明提供的基于机器视觉的铝合金机加工零件孔洞检测方法,通过获取各目标铝压铸件表面各孔洞的气孔面积、气孔直径和螺纹规范度,分析得到各目标铝压铸件表面各孔洞的内壁参数符合系数,实现对加工零件孔洞内壁的细致化分析,防止加工零件孔洞内壁存在气孔影响加工零件的力学性能、使用效果和表面光泽度,同时为加工零件与其配套零件的紧密组装提供保障。
附图说明
33.为了更清楚地说明本发明实施例的技术方案,下面将对实施例描述所需要使用的附图作简单地介绍,显而易见地,下面描述中的附图仅仅是本发明的一些实施例,对于本领域普通技术人员来讲,在不付出创造性劳动的前提下,还可以根据这些附图获得其他的附图。
34.图1为本发明的方法流程示意图。
具体实施方式
35.下面将结合本发明实施例中的附图,对本发明实施例中的技术方案进行清楚、完整地描述,显然,所描述的实施例仅仅是本发明一部分实施例,而不是全部的实施例。基于本发明中的实施例,本领域普通技术人员在没有作出创造性劳动前提下所获得的所有其它实施例,都属于本发明保护的范围。
36.请参阅图1所示,本发明提供的基于机器视觉的铝合金机加工零件孔洞检测方法,包括如下步骤:
37.步骤一、铝压铸件孔洞基本参数获取:获取铝合金机加工零件生产线上各铝压铸件表面孔洞的基本参数,将其记为各铝压铸件表面孔洞的基本参数,其中基本参数包括形状匹配度和数量。
38.作为一种优选方案,所述步骤一中获取各铝压铸件表面孔洞的基本参数,具体方法为:通过高清摄像机获取各铝压铸件的加工表面图像,根据各铝压铸件的加工表面图像,得到各铝压铸件加工表面图像中各孔洞区域,根据各铝压铸件加工表面图像中各孔洞区域,得到各铝压铸件表面孔洞的数量和形状匹配度,将其分别记为ai和bi,i表示第i个铝压铸件的编号,i=1,2,...,n。
39.需要说明的是,所述根据各铝压铸件的加工表面图像,得到各铝压铸件加工表面图像中各孔洞区域,具体方法为:利用图像处理技术,得到各铝压铸件加工表面图像中各像素点的灰度值,将各铝压铸件加工表面图像中相同灰度值对应的像素点所在区域进行拼接,得到各铝压铸件加工表面图像中各灰度区域,将各铝压铸件加工表面图像中各灰度区域的灰度值与预设的孔洞区域图像灰度值范围进行比较,若某铝压铸件加工表面图像中某灰度区域的灰度值属于预设的孔洞区域图像灰度值范围之内,则将该铝压铸件加工表面图像中该灰度区域记为孔洞区域,筛选出该铝压铸件加工表面图像中各孔洞区域,统计得到各铝压铸件加工表面图像中各孔洞区域。
40.需要说明的是,所述根据各铝压铸件加工表面图像中各孔洞区域,得到各铝压铸件表面孔洞的形状匹配度,具体过程为:根据各铝压铸件加工表面图像中各孔洞区域,得到
各铝压铸件加工表面图像中各孔洞区域轮廓,将各铝压铸件加工表面图像中各孔洞区域轮廓与数据库中存储的标准孔洞轮廓进行比对,得到各铝压铸件加工表面图像中各孔洞区域轮廓与标准孔洞轮廓的相似度,将其记为各铝压铸件加工表面图像中各孔洞的形状匹配度,将各铝压铸件加工表面图像中各孔洞的形状匹配度进行相互比较,将各铝压铸件加工表面图像中孔洞的最小形状匹配度记为各铝压铸件表面孔洞的形状匹配度。
41.步骤二、铝压铸件孔洞基本参数分析:根据各铝压铸件表面孔洞的基本参数,分析得到各铝压铸件的孔洞基本参数符合系数。
42.作为一种优选方案,所述步骤二中分析得到各铝压铸件的孔洞基本参数符合系数,具体过程为:将各铝压铸件表面孔洞的数量ai和形状匹配度bi代入公式得到各铝压铸件的孔洞基本参数符合系数βi,其中a
标
表示数据库中存储的铝压铸件表面孔洞的标准数量,b
设
表示预设的铝压铸件表面孔洞形状匹配度的阈值,χ1、χ2分别表示预设的铝压铸件表面孔洞数量和孔洞形状匹配度的权重因子。
43.步骤三、目标铝压铸件筛选处理:根据各铝压铸件的孔洞基本参数符合系数,筛选孔洞基本参数合格的各铝压铸件,并将孔洞基本参数合格的各铝压铸件记为各目标铝压铸件。
44.作为一种优选方案,所述步骤三的具体分析过程为:将各铝压铸件的孔洞基本参数符合系数与预设的合格铝压铸件对应的孔洞基本参数符合系数范围进行比对,若某铝压铸件的孔洞基本参数符合系数处于预设的合格铝压铸件对应的孔洞基本参数符合系数范围之内,表明该铝压铸件的孔洞基本参数合格,统计孔洞基本参数合格的各铝压铸件,将其记为各目标铝压铸件,反之,表明该铝压铸件的孔洞基本参数不合格,统计孔洞基本参数不合格的各铝压铸件,并将孔洞基本参数不合格的各铝压铸件放置至指定区域。
45.在本实施例中,本发明通过获取各铝压铸件表面孔洞的形状匹配度和数量,分析得到各铝压铸件的孔洞基本参数符合系数,根据各铝压铸件的孔洞基本参数符合系数,筛选得到孔洞基本参数合格的各目标铝压铸件,根据不合格孔洞的显著特征对加工零件进行初次筛选并对筛选后的加工零件孔洞进行深度质检,进而缩小加工零件孔洞深度质检对象范围,提高质检效率。
46.步骤四、目标铝压铸件孔洞尺寸参数获取:获取各目标铝压铸件表面各孔洞的尺寸参数,其中尺寸参数包括直径、相对位置偏离度、深度和垂直度。
47.作为一种优选方案,所述步骤四中获取各目标铝压铸件表面各孔洞的直径和相对位置偏离度,具体方法为:根据各铝压铸件的加工表面图像,筛选得到各目标铝压铸件的加工表面图像,在各目标铝压铸件的加工表面图像中按照预设的坐标系构建方法构建二维坐标系;
48.按照预设的标记点选取原则在各目标铝压铸件加工表面图像中各孔洞圆周上进行各次标记点选取操作,得到各次标记点选取操作中各目标铝压铸件加工表面图像中各孔洞圆周上各标记点,将其记为各次标记点选取操作中各目标铝压铸件各孔洞圆周上各标记点,获取各次标记点选取操作中各目标铝压铸件各孔洞圆周上各标记点的坐标,将各次标记点选取操作中各目标铝压铸件各孔洞圆周上各标记点的坐标代入求圆方程,得到各次标记点选取操作中各目标铝压铸件各孔洞对应的圆方程,根据各次标记点选取操作中各目标
铝压铸件各孔洞对应的圆方程,得到各次标记点选取操作中各目标铝压铸件各孔洞对应的直径和圆心坐标,对各次标记点选取操作中各目标铝压铸件各孔洞对应的直径进行平均值计算,得到各目标铝压铸件表面各孔洞的直径,将其记为j表示j个目标铝压铸件的编号,j=1,2,...,m,g表示目标铝压铸件表面第g个孔洞的编号,g=1,2,...,h,对各次标记点选取操作中各目标铝压铸件各孔洞对应的圆心坐标进行平均值计算,得到各目标铝压铸件表面各孔洞的圆心坐标,将其记为
49.从数据库中提取铝压铸件加工表面的图纸,按照目标铝压铸件加工表面图像中二维坐标系的构建方法,在铝压铸件加工表面图纸中构建二维坐标系,获取铝压铸件加工表面图纸中各孔洞的圆心坐标,对铝压铸件加工表面图纸中各孔洞的圆心坐标进行设定比例的缩放,得到铝压铸件加工表面各孔洞的标准圆心坐标,将其记为(x
g标
,y
g标
),将各目标铝压铸件表面各孔洞的圆心坐标代入公式得到各目标铝压铸件表面各孔洞的相对位置偏离度其中ε表示预设的目标铝压铸件表面孔洞的相对位置偏离度的修正因子,δc
设
表示预设的目标铝压铸件表面孔洞圆心偏移距离的阈值。
50.作为一种优选方案,所述步骤四中获取各目标铝压铸件表面各孔洞的深度和垂直度,具体方式为:按照预设的深度检测点布设原则,在各目标铝压铸件表面各孔洞的洞口边沿布设各深度检测点,利用激光测距仪获取各目标铝压铸件表面各孔洞洞口边沿各深度检测点的深度,对各目标铝压铸件表面各孔洞洞口边沿各深度检测点的深度进行平均值计算,得到各目标铝压铸件表面各孔洞的深度,将其记为
51.按照预设的探测点布设原则,在各目标铝压铸件表面各孔洞的洞口边沿布设各探测点,作各目标铝压铸件表面各孔洞洞口边沿各探测点到孔洞底面的垂线,将其记为各目标铝压铸件表面各孔洞洞口边沿各探测点的内射线,获取各目标铝压铸件表面各孔洞洞口边沿各探测点的内射线与竖直基准线之间的夹角,将其记为各目标铝压铸件表面各孔洞洞口边沿各探测点对应的孔洞倾斜角,进一步分析得到各目标铝压铸件表面各孔洞的垂直度,将其记为
52.需要说明的是,所述各目标铝压铸件表面各孔洞的垂直度,具体获取方法为:将各目标铝压铸件表面各孔洞洞口边沿各探测点对应的孔洞倾斜角进相互比较,筛选出各目标铝压铸件表面各孔洞对应的最大孔洞倾斜角,将其记为各目标铝压铸件表面各孔洞的倾斜角,将各目标铝压铸件表面各孔洞的倾斜角代入公式得到各目标铝压铸件表面各孔洞的垂直度其中表示预设的目标铝压铸件表面孔洞的垂直度修正因子,表示第j个目标铝压铸件表面第g个孔洞的倾斜角,j=1,2,...,m,g=1,2,...,h。
53.需要说明的是,所述各目标铝压铸件表面各孔洞的倾斜角的范围均为
54.步骤五、目标铝压铸件孔洞尺寸参数分析:根据各目标铝压铸件表面各孔洞的尺寸参数,分析得到各目标铝压铸件表面各孔洞的尺寸参数符合系数。
55.作为一种优选方案,所述步骤五中分析得到各目标铝压铸件表面各孔洞的尺寸参数符合系数,具体方法为:将各目标铝压铸件表面各孔洞的直径相对位置偏离度深度和垂直度代入公式得到各目标铝压铸件表面各孔洞的尺寸参数符合系数其中e表示自然常数,d
标
、f
标
分别表示数据库中存储的铝压铸件表面孔洞的标准直径和标准深度,δ
设
、φ
设
分别表示预设的目标铝压铸件表面孔洞的相对位置偏离度阈值和垂直度阈值,η1、η2、η3、η4分别表示预设的目标铝压铸件表面孔洞的直径、相对位置偏离度、深度和垂直度的权重因子。
56.在本实施例中,本发明通过获取各目标铝压铸件表面各孔洞的直径、相对位置偏离度、深度和垂直度,分析得到各目标铝压铸件表面各孔洞的尺寸参数符合系数,从直径、位置、深度和垂直度对加工零件孔洞的尺寸进行综合分析,丰富尺寸质检指标的多样化,使得加工零件与其配套零件的组装更加贴合,进而提高加工零件孔洞尺寸质检结果的准确性和可靠性。
57.步骤六、目标铝压铸件孔洞内壁参数获取:获取各目标铝压铸件表面各孔洞的内壁参数,其中内壁参数包括气孔面积、气孔直径和螺纹规范度。
58.作为一种优选方案,所述步骤六中各目标铝压铸件表面各孔洞的内壁参数,具体获取方法为:通过高倍显微镜获取各目标铝压铸件表面各孔洞的内壁显微图像,根据各目标铝压铸件表面各孔洞的内壁显微图像,得到各目标铝压铸件表面各孔洞的气孔面积和气孔直径,将其分别记为和
59.根据各目标铝压铸件表面各孔洞的内壁显微图像,得到各目标铝压铸件表面各孔洞内壁的螺纹图像,进一步分析得到目标铝压铸件表面各孔洞的螺纹规范度,将其记为
60.需要说明的是,所述根据各目标铝压铸件表面各孔洞的内壁显微图像,得到各目标铝压铸件表面各孔洞的气孔面积和气孔直径,具体过程为:利用图像处理技术,得到各目标铝压铸件表面各孔洞内壁显微图像的各灰度值,将各目标铝压铸件表面各孔洞内壁显微图像的各灰度值与预设的气孔图像灰度值范围进行比较,若某目标铝压铸件表面某孔洞内壁显微图像的某灰度值属于预设的气孔图像灰度值范围之内,则将该目标铝压铸件表面该孔洞内壁显微图像的该灰度值记为气孔灰度值,筛选出各目标铝压铸件表面各孔洞内壁显微图像的各气孔灰度值,获取各目标铝压铸件表面各孔洞内壁显微图像各气孔灰度值对应的区域,将其记为各目标铝压铸件表面各孔洞内壁各气孔区域;
61.获取各目标铝压铸件表面各孔洞内壁各气孔区域的面积,对各目标铝压铸件表面各孔洞内壁各气孔区域的面积进行累加,得到各目标铝压铸件表面各孔洞的气孔面积,获取各目标铝压铸件表面各孔洞内壁各气孔区域的长度,将各目标铝压铸件表面各孔洞内壁
各气孔区域的长度进行相互比较,将各目标铝压铸件表面各孔洞内壁的最大气孔区域长度记为各目标铝压铸件表面各孔洞的气孔直径。
62.需要说明的是,所述分析目标铝压铸件表面各孔洞的螺纹规范度,具体过程为:根据各目标铝压铸件表面各孔洞内壁的螺纹图像,得到各目标铝压铸件表面各孔洞内壁的螺纹轮廓,将各目标铝压铸件表面各孔洞内壁的螺纹轮廓与预设的铝压铸件孔洞内壁标准螺纹轮廓进行拟合,得到各目标铝压铸件表面各孔洞内壁的螺纹轮廓与预设的铝压铸件孔洞内壁标准螺纹轮廓的重合度,将其记为各目标铝压铸件表面各孔洞的螺纹规范度。
63.步骤七、目标铝压铸件孔洞内壁参数分析:根据各目标铝压铸件表面各孔洞的内壁参数,分析得到各目标铝压铸件表面各孔洞的内壁参数符合系数。
64.作为一种优选方案,所述步骤七中分析得到各目标铝压铸件表面各孔洞的内壁参数符合系数,具体方法为:将各目标铝压铸件表面各孔洞的气孔面积气孔直径和螺纹规范度代入公式得到各目标铝压铸件表面各孔洞的内壁参数符合系数其中τ表示预设的目标铝压铸件表面孔洞的内壁参数符合系数修正因子,s
设
、l
设
、κ
设
分别表示预设的目标铝压铸件表面孔洞的允许气孔面积、允许气孔直径和螺纹规范度阈值,λ1、λ2、λ3分别表示预设的目标铝压铸件表面孔洞的气孔面积、气孔直径和螺纹规范度的权重因子。
65.在本实施例中,本发明通过获取各目标铝压铸件表面各孔洞的气孔面积、气孔直径和螺纹规范度,分析得到各目标铝压铸件表面各孔洞的内壁参数符合系数,实现对加工零件孔洞内壁的细致化分析,防止加工零件孔洞内壁存在气孔影响加工零件的力学性能、使用效果和表面光泽度,同时为加工零件与其配套零件的紧密组装提供保障。
66.步骤八、目标铝压铸件孔洞综合评估:根据各目标铝压铸件表面各孔洞的尺寸参数符合系数和内壁参数符合系数,评估得到各目标铝压铸件表面各孔洞的合格指数,并进行处理。
67.作为一种优选方案,所述步骤八中具体分析过程为:将各目标铝压铸件表面各孔洞的尺寸参数符合系数和内壁参数符合系数代入公式得到各目标铝压铸件表面各孔洞的合格指数其中ψ1、ψ2分别表示预设的目标铝压铸件表面孔洞的尺寸参数符合系数和内壁参数符合系数的权重因子;
68.将各目标铝压铸件表面各孔洞的合格指数与预设的合格指数阈值进行比较,若某目标铝压铸件表面某孔洞的合格指数小于预设的合格指数阈值,则该目标铝压铸件孔洞不合格,筛选出孔洞不合格的各目标铝压铸件,并将孔洞不合格的各目标铝压铸件的编号发送至铝合金机加工零件质量管理部门。
69.以上内容仅仅是对本发明的构思所作的举例和说明,所属本技术领域的技术人员对所描述的具体实施例做各种各样的修改或补充或采用类似的方式替代,只要不偏离发明的构思或者超越本权利要求书所定义的范围,均应属于本发明的保护范围。