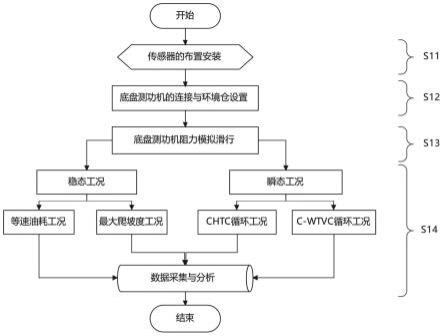
1.本发明属于整车冷却性能试验方法领域,具体涉及一种基于底盘测功机和环境仓的热管理试验方法及系统。
背景技术:2.热管理是考量整车对实际环境耐受程度的一个重要指标,同时也为降低油耗提供数据支持,一般整车热管理试验通常在实际道路上进行,由于对其试验工况条件比较严苛,整车道路热管理试验所需试验环境极限,存在驾驶安全性差,试验过程中存在安全隐患;由于是在室外道路,环境因素不可控,具体指气温、环境湿度、风速等不可控,并且由于环境因素无法控制,同一工况试验环境一致性差,同样的环境条件试验数据可重复性验证程度不高。
3.现有技术中,cn201410444352.6公开了一种车辆热平衡能力室内测试装置及方法,该文件包括底盘测功机、配备温度控制系统的环境仓、冷却风机和温度数据采集系统;该文件对整车进行发动机进、出水,散热器进、出水以及环境温度等传感器的安装,并通过温度数据采集系统进行调试,确保所有传感器的数据有效、稳定。将带有传感器的整车开到底盘测功机上,并进行对中,使用底盘测功机的固定装置对整车进行非驱动轮或车身的固定,使冷却风机出风口面对整车进气格栅,调整冷却风机到进气格栅的距离为0.6-1米。调整环境仓的温度控制为热平衡测试所需温度。待整车浸车超过4小时后,启动发动机,进行热车。该文件的底盘测功机按照车辆最大总质量加载,调整底盘测功机为恒车速模式,通过对整车变速箱以及传动比进行计算,得出发动机最大扭矩点转速所对应的车速,并调整到位。发动机油门全开,同时观察温度数据采集系统的发动机出水温度是否稳定,并记录最后稳定的15分钟的数据,稳定要求为温度变化率0.5℃/10分钟。该文件基于最大功率点、最大扭矩点的发动机进出水温度,散热器进出水温度,来对整车发动机及冷却系统的匹配及要求进行测试。该文件虽然在室内环境进行试验,但是该文件进行测试时,无法匹配出道路滑行的阻力及阻力系数,也无法参考迎面风速等多种参数对样车的影响,进而造成试验结果数据的误差较大,无法满足试验要求,无法为整车开发提供数据保障。
技术实现要素:4.本发明提供一种基于底盘测功机和环境仓的热管理试验方法,方法可以解决整车道路热管理试验存在的驾驶安全性差、试验环境和试验条件不可控、试验数据重复性差等问题。
5.方法包括:
6.s11,安装试验所需的温度传感器、压力传感器和流量计;
7.s12,将试验样车固定在底盘测功机上,连接传感器与数采系统并调试,确认数据传输与采集无误后开启环境仓,环境仓设置温度为32℃至37℃;
8.s13,试验样车与底盘测功机预热结束后再进行滑行试验,基于道路滑行所提供阻
力f=av2+bv+c,将道路滑行阻力系数a、b、c分别输入底盘测功机,迎面风机风速v按照v=n2v2+n1v+n0设置车速v跟随,此时样车置于空挡状态,由底盘测功机自动将样车拖至100km/h,然后自由滑至速度为0km/h,滑行三次,滑行结束后检查滑行数据曲线一致性并选择三组中滑行所需时间误差在
±
3%以内且误差最小的一组;
9.s14,滑行结束后进行稳态试验工况和瞬态试验工况来测试整车热管理性能。
10.进一步需要说明的是,方法中,待环境仓设置温度为32℃至37℃并稳定后开始对试验样车与底盘测功机进行预热;
11.预热方式为试验样车在底盘测功机上行驶至最高车速的80%进行至少30分钟,后桥温度达到后桥齿轮油最大许用温度的60%;
12.若两个连续试验工况进行时,后桥温度满足后桥齿轮油最大许用温度的60%则无需热车。
13.进一步需要说明的是,s11中每个温度测点均有安装2个温度传感器,并且温度传感器为k型热电偶式,每个压力测点至少安装1个压力传感器。
14.进一步需要说明的是,s14中进行等速油耗试验时试验样车达到固定挡位固定车速后应稳住油门踏板,使车速不超过
±
0.1km/h的浮动,待发动机出水温度与冷却水流量稳定1分钟后且发动机出水温度温差≤
±
0.5℃时开始记录数据。
15.进一步需要说明的是,等速油耗测试为试验样车每行驶固定相同距离记录一组数据,一个速度点记录至少三组有效数据,每个速度点记录数据时行驶固定距离需相同,三组百公里油耗数据不超过1%为有效,实时记录发动机系统参数、各测点温度和压力数据、流量计流量、燃油温度。
16.进一步需要说明的是,s14中使用底盘测功机进行最大爬坡度试验,底盘测功机以坡度0.2%依次递增坡度,在油门到底后调节坡度变化的幅度以至目标转速不变;
17.待发动机出水温度与冷却水流量稳定1分钟后且发动机出水温度温差≤
±
0.5℃时开始记录数据,实时记录发动机系统参数、各测点温度和压力、流量计流量、燃油温度、车速以及坡度。
18.进一步需要说明的是,s14中整车热管理试验进行稳态工况时选择等速油耗测试和最大爬坡度测试,瞬态工况时选择chtc、c-wtvc循环工况。
19.进一步需要说明的是,s14中瞬态工况选择chtc、c-wtvc循环工况,且试验过程中实时记录发动机参数数据、水温、冷却水流量、传感器各测点温度和压力参数、油耗、油温,瞬态试验循环工况试验数据,并记录三组百公里油耗不超过1%为有效数据。
20.本发明还提供一种基于底盘测功机和环境仓的热管理试验系统,系统包括:温度传感器、压力传感器、流量计、预热器、底盘测功机以及测试终端机;
21.测试终端机设有can采集模块、数据存储模块、数据分析模块以及数据显示模块;
22.数据采集模块分别与温度传感器、压力传感器以及流量计连接,接收试验过程的温度信息、压力信息以及水流量信息;
23.can采集模块与整车控制器连接,获取试验样车在试验过程中的数据信息;
24.底盘测功机用于固定试验样车,底盘测功机基于f=av2+bv+c提供道路滑行阻力,将道路滑行阻力系数a、b、c,迎面风机风速v按照v=n2v2+n1v+n0设置车速v跟随,此时样车置于空挡状态,由底盘测功机自动将样车拖至100km/h,然后自由滑至速度为0km/h,滑行三
语言或类似的程序设计语言。程序代码可以完全地在试验终端机上执行,作为一个独立的软件包执行。本发明试验终端机还可以是远程计算机,通过任意种类的网络——包括局域网(lan)或广域网(wan)——连接到试验设备进行远程试验操作。
39.这样,本发明利用基于底盘测功机和环境仓相配合,通过建立试验条件,试验工况,利用传感器监控、数据传输等技术,实现可以准确模拟该样车匹配的道路行驶阻力,可以实时记录该车试验时的各种参数,为整车开发提供数据保障,提高开发效率。
40.下面将结合本发明实施例中的附图1至2,对本发明实施例中的技术方案进行清楚、完整地描述,显然,所描述的实施例仅仅是本发明一部分实施例,而不是全部的实施例。
41.这里,需要说明的是试验样车c状态检查。样车检查根据样车检查表:样车配置与试验大纲一致、磨合里程、外观、轮胎、发动机油位、防冻液液位、燃油箱油位、尿素液位、有无漏液、发动机状况、空调、点烟器、挡泥板、配重块、电瓶、行驶检查。
42.需要进一步说明的是,磨合里程需满足标准要求。轮胎:完好,磨损正常,气压满足技术要求。配重块根据试验要求在样车驱动桥上方配重2-4吨载荷。行驶检查:园区至少行驶20分钟,发动机变速器、驱动桥、转向装置、制动装置运行正常。
43.以下将给出一种可能的实施例对其具体的实施方案进行非限制性阐述。整车热管理试验方法的步骤如下:
44.步骤s11:安装试验所需的温度传感器、压力传感器和流量计。其中温度测点包括发动机进、出水温度,中冷器进出、气温度,空滤后进气温度,环境温度,后桥温度;压力测点包括发动机进、出气压力,中冷器进出、气压力,膨胀水箱压力,空滤后进气压力、排气背压。
45.本发明的实施例中,确保试验数据准确性和保险性,每个温度测点均在同一位置安装2个温度传感器,并且温度传感器为k型热电偶式,每个压力测点至少安装1个压力传感器,同时可根据需求增加温度与压力测点,不可在此基础上减少测点。
46.步骤s12:试验样车c固定在底盘测功机b上,连接传感器与数采系统并调试,确认数据传输与采集无误后开启环境仓a,环境仓a设置温度为32℃至37℃,优选地温度为35℃。待环境仓a温度达到35℃并稳定后开始对试验样车c与底盘测功机b进行预热,预热方式为试验样车c在底盘测功机b上行驶至最高车速的80%进行至少30分钟,同时后桥温度达到后桥齿轮油最大许用温度的60%。
47.步骤s13:试验样车c与底盘测功机b预热结束后首先进行滑行试验,基于道路滑行所提供阻力f=av2+bv+c,将道路滑行阻力系数a、b、c分别输入底盘测功机b,迎面风机d风速v按照v=n2v2+n1v+n0设置车速v跟随,此时试验样车c置于空挡状态,由底盘测功机b自动将样车拖至100km/h,然后自由滑至速度为0km/h,滑行三次且数据有效,滑行结束后检查滑行数据曲线一致性并选择三组中滑行所需时间误差在
±
3%以内且误差最小的一组。
48.步骤s14:滑行结束后进行稳态试验工况和瞬态试验工况来测试整车热管理性能。
49.本发明的试验方法在试验前进行热车,进行稳态工况时选择等速油耗试验、最大爬坡度试验。
50.本发明在进行等速油耗试验时,试验样车c状态为固定挡位、固定车速、固定坡度,试验样车c达到试验所需挡位和车速时,试验驾驶员稳住油门踏板,使车速不超过
±
0.1km/h的浮动,实时监控试验样车c发动机水温、风扇转速、冷却水流量、所布置传感器各测点参数、油耗、油温,待发动机出水温度与冷却水流量稳定后开始记录数据,等速油耗测试为试
验样车c每行驶固定相同距离记录一组数据,一个速度点记录至少三组有效数据,百公里油耗不超过1%为有效;在进行最大爬坡度试验时,使用固定挡位与固定转速,先将试验样车c提高至固定挡位和固定转速,通过给底盘测功机b输入坡度以0.2%递增,试验驾驶员增大油门开度以维持转速不变,直到油门开度达到100%,调节坡度至转速与车速均稳定后停止调节,实时监控试验样车c各数据参数,直到发动机出水温度与冷却水流量稳定时开始记录数据,试验样车c行驶固定距离记录一组数据,只需记录一组。进行瞬态试验工况时选择chtc、c-wtvc循环工况,由试验驾驶员根据循环工况路谱行驶,实时记录发动机数据、水温、冷却水流量、传感器各测点参数、油耗、油温,瞬态试验循环工况试验数据需记录三组有效数据,百公里油耗不超过1%为有效。
51.传感器数据由数据采集模块进行采集,整车参数与发动机参数由can采集模块进行采集,各数据由数据存储模块存储并由数据分析模块进行分析,最终得出结论。
52.本发明提供的基于底盘测功机和环境仓的热管理试验方法及系统可以将试验过程数据信息以及试验结果信息进行归档存储。
53.配置试验过程数据信息以及试验结果信息操作界面,使试验人员在系统中添加未储存,或未进行配置的试验数据信息;或对已储存的试验数据信息进行修改,或删除。试验结果数据可以基于柱状图,或曲线图,或数据列表进行显示供操作人员参考使用。
54.本发明能够对试验过程数据信息以及试验结果信息进行汇总,方便试验人员进行查阅,试验过程监控效率有效的得到提升。还能够对试验数据高效率地收集、存储,并进行处理,使用多维空间描述整个试验过程。提高车辆试验的质量和效能,及时发现在车辆在试验过程中的数据异常,以提高试验过程管理水平和效率,控制车辆制作过程风险,从而实现试验全过程监督、管理和控制的及时性和科学性。
55.以下是本公开实施例提供的基于底盘测功机和环境仓的热管理试验系统的实施例,该系统与上述各实施例的基于底盘测功机和环境仓的热管理试验方法属于同一个发明构思,在基于底盘测功机和环境仓的热管理试验系统的实施例中未详尽描述的细节内容,可以参考上述基于底盘测功机和环境仓的热管理试验方法的实施例。
56.如图3所示,系统包括:温度传感器、压力传感器、流量计、预热器、底盘测功机以及试验终端机;
57.试验终端机设有数据采集模块、can采集模块、控制模块、数据存储模块、数据分析模块以及数据显示模块;
58.数据采集模块分别与温度传感器、压力传感器以及流量计连接,接收试验过程的温度信息、压力信息以及水流量信息;
59.can采集模块与整车控制器连接,获取试验样车在试验过程中的数据信息;
60.底盘测功机用于固定试验样车,底盘测功机基于f=av2+bv+c提供道路滑行阻力,将道路滑行阻力系数a、b、c,迎面风机风速v按照v=n2v2+n1v+n0设置车速v跟随,此时样车置于空挡状态,由底盘测功机自动将样车拖至100km/h,然后自由滑至速度为0km/h,滑行三次,滑行结束后检查滑行数据曲线一致性并选择三组中滑行所需时间误差在
±
3%以内且误差最小的一组;
61.预热器用于将环境仓温度加热至32℃至37℃;
62.数据存储模块用于储存试验过程数据信息以及试验结果信息;
63.数据分析模块用于对试验过程数据信息进行分析,得出最终试验结论;
64.数据显示模块用于显示试验过程数据信息以及试验结果信息。
65.数据采集模块采集的信息包括:发动机进、出水温度,中冷器进出、气温度,空滤后进气温度,环境温度,后桥温度;压力测点包括发动机进、出气压力,中冷器进出、气压力,膨胀水箱压力,空滤后进气压力、排气背压。
66.本发明涉及的基于底盘测功机和环境仓的热管理试验系统相比于道路试验,在环境仓内基于底盘测功机的整车热管理试验具有驾驶安全性高、同一试验工况状态完全可控,试验环境条件可控性强、试验数据精确并且数据重复性验证便捷的优点,底盘测功机可以准确模拟该样车匹配的道路行驶阻力,可以实时记录该车试验时的各种参数,为整车开发提供数据保障,提高开发效率。
67.本发明涉及的热管理试验系统中所公开的实施例描述的各示例的单元及算法步骤,能够以电子硬件、计算机软件或者二者的结合来实现,为了清楚地说明硬件和软件的可互换性,在上述说明中已经按照功能一般性地描述了各示例的组成及步骤。这些功能究竟以硬件还是软件方式来执行,取决于技术方案的特定应用和设计约束条件。专业技术人员可以对每个特定的应用来使用不同方法来实现所描述的功能,但是这种实现不应认为超出本发明的范围。
68.对所公开的实施例的上述说明,使本领域专业技术人员能够实现或使用本发明。对这些实施例的多种修改对本领域的专业技术人员来说将是显而易见的,本文中所定义的一般原理可以在不脱离本发明的精神或范围的情况下,在其它实施例中实现。因此,本发明将不会被限制于本文所示的这些实施例,而是要符合与本文所公开的原理和新颖特点相一致的最宽的范围。