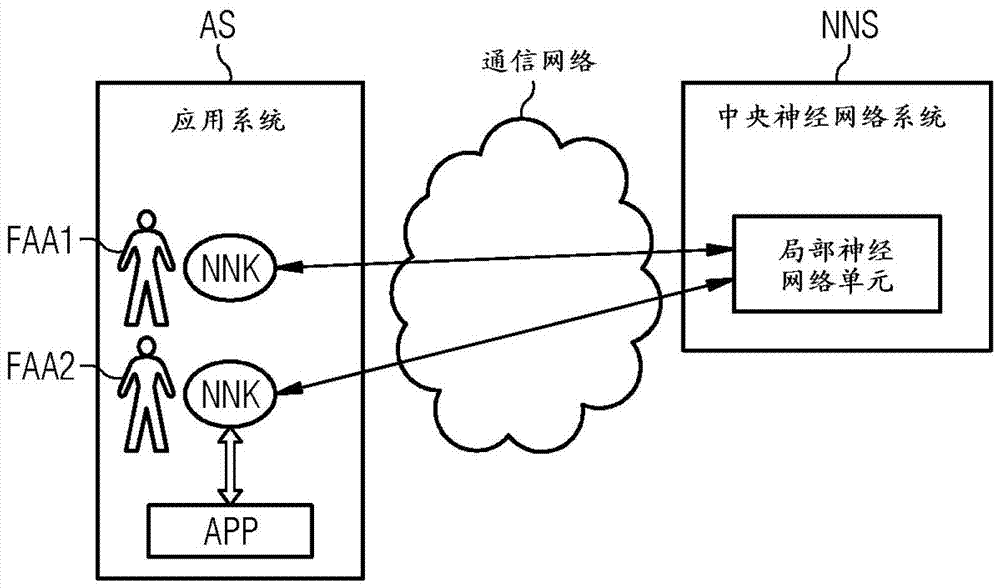
本发明涉及生产工厂中故障状态自动恢复的方法和系统。
背景技术:众所周知,在根据ISA(InternationalStandardAssociation,国际标准协会)S-95标准的现有技术中,一种管理和控制通过ERP(EnterpriseResourcePlanning,企业资源计划)计划的并通过车间生产的制造过程的方法提供了用于实施上述计划的制造过程并且控制车间里的对应生产步骤的MES(ManufacturingExecutingSystem,制造执行系统)。具体的,ERP是一种用于计划企业的业务资源的包括硬件装置和对应软件应用的系统,企业的业务资源即物料供应、人力资源管理、采购、订单、利润、财务、库存控制、客户管理等等,而词语“车间”被用于表示例如通过测量每一台机器每小时生产的工件数量或者机器的运行参数、生产的工件的质量等等,而支持对制造过程中涉及的单个机器的控制的系统。MES是处于上层ERP和下层车间之间的提供计算机和软件工具的中间层,包括用于管理生产订单的软件工具(从ERP接收生产请求)、和用于生产建模的软件工具(支持选择和管理制造过程中涉及的资源的设计阶段,以便在要求的时间限制内实现计划的制造过程,所述资源即雇员、机器和物料)。MES基于定义了软件工具如何在车间层实施生产以及如何与车间层通信的ISAS95标准。更具体的,S95基本上基于由多个顺序的处理阶段表示的制造过程,其中,每一个顺序的处理阶段包括在车间层顺序执行的多个操作。执行上述MES软件工具包括通过激活顺序的处理阶段并顺序执行对应的多个操作而管理制造过程。更具体的,为了完成制造过程,对于多个处理阶段,管理生产订单的软件工具基本上是重复下面的步骤:激活多个顺序的处理阶段并等待其结束。在这种情况下,与相应顺序处理阶段对应的多个软件工具要在相应顺序处理阶段的持续时间内执行。在MES环境中,可以观察到存在下面的巨大需求:避免由生产过程中实际涉及的生产资源的意外错误事件而导致生产停工期。因而,希望尽快检测到系统故障的出现并提供合适的解决方案,以便使系统从错误事件中恢复。此外,当对生产过程进行了适当的观测时,系统的错误事件经常是可预测的。因而,通常根据对来自特定于资源的应用的信息的分析来执行对错误的检测,以不断检验是否发生了相对于预期状态的显著偏离。通常,这种方案在故障恢复过程中可能遇到许多问题。具体的,人力分析复杂生产环境中的大量数据几乎是不可能的,这通常导致减少为用于错误检测而收集的数据。另外,给出判断的过程和对来自应用的信息的分析可能花费生产过程所不能接受的非常长的时间。进一步的,错误问题的分析及其解决方案的寻找可能涉及许多技术专家(即技术支援小组、软件架构师、软件设计者和开发者),这也可能延迟判断并相应地增加判断的成本。在相关文献中,几种解决方案使用知识库系统检测应用中的错误和故障(例如,T.Sorsa,H.N.Koivo和H.Koivisto的“Neuralnetworksinprocessfaultdiagnosis”,IEEETrans.Syst.,Man.andcyberm.,vol.21,no.4,p815-825,1991”),但是,当前软件产品和校正系统都不能够解决上述问题。
技术实现要素:因而,本发明的目的是提供生产工厂中故障状态自动恢复的方法和系统,该方法和系统不需要太多的资源来确定合适的恢复计划,在消除可预见的停工时间方面对于停工时间管理有积极影响。根据本发明,通过一种生产工厂中故障状态自动恢复的方法来实现该目的,该方法包括:a)提供多个生产资源;b)提供制造执行系统,该制造执行系统包括设计层的将可利用的生产资源模型化为工厂模型的生产建模器和根据多个生产订单调度对被模型化的生产资源的操作的生产调度器,并包括执行层的根据生产调度执行生产过程的生产控制器和检测故障状态并响应于一个或多个故障状态自动决定校正操作的故障和/或机会管理器;c)对于至少一种生产资源,运行用于操作该生产资源的应用和故障分析代理,该故障分析代理初始在设计层向故障和/或机会管理器提供多个分类的错误状态,在执行层相对于分类的错误状态检测代表对生产资源的操作的操作数据,并且在出现错误状态的情况下向故障和/或机会管理器转发错误事件;d)通过故障和/或机会管理器收集错误事件并通过神经网络系统分析错误事件,以便指定至少一个错误事件的错误类别;以及e)根据指定的错误类别,通过故障和/或机会管理器决定为该错误类别确定的校正操作,并向故障分析代理转发校正操作,以便对生产资源和生产资源的应用分别执行该校正操作。对于系统,根据本发明,上述目的是通过生产工厂中故障状态自动恢复系统来实现的,该系统包括:a)多个生产资源;b)制造执行系统,包括设计层的将可利用的生产资源模型化为工厂模型的生产建模器和根据多个生产订单调度对被模型化的生产资源的操作的生产调度器,并包括执行层的根据生产调度执行生产过程的生产控制器和检测故障状态并响应于一个或多个故障状态自动决定校正操作的故障和/或机会管理器;c)用于对至少一种生产资源运行操作该生产资源的应用和故障分析代理的多个计算装置,该故障分析代理初始在设计层向故障和/或机会管理器提供多个分类的错误状态,在执行层相对于分类的错误状态检测代表对生产资源的操作的操作数据,并且在出现错误状态的情况下向故障和/或机会管理器转发错误事件;d)故障和/或机会管理器,用于收集错误事件并通过神经网络系统分析错误事件,以便指定至少一个错误事件的错误类别;以及e)根据指定的错误类别,故障和/或机会管理器决定为该错误类别确定的校正操作,并向故障分析代理转发校正操作,以便对生产资源和生产资源的应用分别执行该校正操作。这样,上述方法和系统包括自动数据收集分析技术,包括对将会发生的错误事件聚类,其中,通过软件助理触发错误事件的自动恢复,软件助理在执行错误恢复算法的过程中不涉及人的干预。因而,上述方法和系统使用故障分析代理,以便根据神经网络系统检测到的关键错误主动改变应用的行为。因而,生产系统一直保持正确的运行状态。故障分析代理起到双重角色。收集检测的特定于资源的软件应用的大量异质数据,以及在某些方面需要校正的时候作用于这些应用以便校正异常行为。附图说明下面参照附图更加详细地介绍本申请的例子:图1示出包括用于自动错误恢复的装置的制造执行系统的架构示意图;图2示出在图1中使用的自动错误恢复系统的第一实施方式的示意图;以及图3示出在图1中使用的自动错误恢复系统的第二实施方式的示意图。具体实施方式图1示出由上层2的ERP(企业资源计划)计划的并由下层6的车间生产的制造过程的管理和控制系统的架构示意图,其中,中间层4的MES(制造执行系统)用于实施计划的制造过程并控制在车间的对应生产步骤。具体的,ERP是一种用于计划企业的业务资源的包括硬件装置和对应的软件应用的系统,企业的业务资源即物料供应、人力资源管理、采购、订单、利润、财务、库存控制、客户管理等等,而词语“车间”被用于表示例如通过测量每一台机器每小时生产的工件数量或者机器的运行参数、生产的工件的质量等等,而支持对制造过程中涉及的单个机器R的控制的系统。软件MES控制台位于中间层4,在上层2的ERP和下层6的车间之间提供计算机和软件工具,包括用于管理生产订单的软件工具(从ERP接收生产请求)和包括各种软件模块的软件工具。通常,PM(productionmodeler,生产建模器)支持选择和管理制造过程中要涉及的资源R(即雇员、机器和物料)的设计阶段,以便在要求的时间限制内实现计划的制造过程。制造过程本身则通过PS(productionscheduler,生产调度器)(使用在设计层输入生产建模器PM的数据)进行调度。为了执行生产过程,上述MES软件工具包括PC(productioncontroller,生产控制器),生产控制器PC激活顺序的处理阶段并执行对应的多个操作。上述MES控制台现在被扩展,以便还提供生产工厂中故障状态自动恢复的系统。目前,包括多种生产资源R、B,其中R示例性表示任何种类的资源,B表示用于向生产过程(例如食品制造)提供热水的锅炉。MES控制台包括设计层的将可利用的生产资源R、B模型化为工厂模型的生产建模器PM,和根据多个生产订单调度对模型化的生产资源R、B的操作的生产调度器PS。在执行层,包括生产控制器PC,以便根据生产调度执行生产过程。还包括FAM(faultand/oropportunitymanager,故障和/或机会管理器),以便检测故障状态并响应于一个或多个故障状态自动决定校正操作。进一步的,还包括用于对至少一种生产资源B运行操作该生产资源B的应用程序和FAA(faultanalysisagent,故障分析代理)的多个计算装置,故障分析代理FAA初始在设计层向故障和/或机会管理器FAM提供多个分类的错误状态,故障分析代理FAA在执行层相对于分类的错误状态来检验代表对生产资源B的操作的操作数据,并且在出现错误状态的情况下,故障分析代理FAA向故障和/或机会管理器FAM转发错误事件。故障和/或机会管理器FAM收集错误事件,并且通过神经网络系统NNK分析错误事件,以便指定至少一个错误事件的错误类别。根据指定的错误类别,故障和/或机会管理器FAM决定为该错误类别确定的校正操作,并且向故障分析代理FAA转发该校正操作,以便分别对生产资源B和生产资源B的应用执行校正操作。在当前的例子中,锅炉B包括FD(fillinglevelmeter,充填液位计)、TD(temperaturedetector,温度检测计)以及PD(powerconsumptiondetector,功耗检测计)。故障分析代理FAA定期分析这三个检测器的数据,以便确定运行锅炉B的应用是否在正常工作。图2示出当前系统的故障自动恢复机制的第一实施方式。一方面,执行要分析的应用App的AS(applicationsystem,应用系统)具有多个故障分析代理FAA1、FAA2。在操作开始时,这些故障分析代理FAA1、FAA2向中央神经网络系统NNS传输特定于应用的神经网络知识NNK。在例如锅炉应用的操作过程中,故障分析代理FAA1、FAA2分析数据,并根据已经作为神经网络知识NNK的一部分传输到中央神经网络系统NNS的分类的错误状态检验这些数据。在出现错误状态的情况下,故障分析代理FAA转发错误事件到作为中央神经网络系统NNS的一部分的故障和/或机会管理器FAM。中央神经网络系统NNS通过它的故障和/或机会管理器FAM收集错误事件,并通过它的神经网络逻辑分析错误事件,以便指定至少一种错误事件的错误类别,并且根据神经网络逻辑得到预定的校正操作。然后,故障和/或机会管理器FAM向被分析的应用App的故障分析代理FAA转发由神经网络逻辑推导的错误类别、以及为推导的错误类别确定的校正操作。故障分析代理FAA然后自动地执行对生产资源B的应用App的校正操作。对于锅炉B,加热操作可以被切换到更高能耗或更低能耗。例如,不断产生的水垢可能降低加热元件的效率,但考虑到仍可达到的热梯度,在预定的能耗阈值内这是可以容忍的。这样,该系统提供了自动数据收集和分析以对错误分类。然后,通过故障分析代理FAA触发自动错误恢复,故障分析代理FAA直接作用于不正常的应用App以便校正App的异常行为。故障分析代理FAA分析的消息可以包括两类。第一类消息是特定应用参数,例如应用调度的关键错误(例如由于数据库连接断开),或者对于资源和/或资源的应用App的异常行为的报警。第二类是通用系统参数,例如网络连接状态、CPU负载、私有存储使用情况、句柄(handle)使用情况等等。现有技术中,管理错误状态的工作流程要求软件代理能够一周7天每天24小时向技术支持小组提供已适当筛选的信息。技术支持小组是否能在非常短的时间内向生产工厂的操作者提供合适的解决方案,实质上取决于错误情形的复杂度和问题的重要性。明显的,当错误情形的解决方案需要各种专家的介入时,停工时间更长。根据本发明,由神经网络通过它的错误和/或机会管理器执行这种错误情形的分析,错误和/或机会管理器使用“学会的”神经网络知识NNK分析错误消息来确定潜在的问题,并提供可能的解决方案,经由故障分析代理FAA在相应应用App上自动执行该解决方案。因而,使得所述多个故障分析代理FAA能够直接影响相应应用的行为,以便控制整个生产系统的状态保持无故障状态。图3现在示出当前系统的故障自动恢复机制的第二实施方式,其与在图2中示出的实施方式相比只有少许修改。这个实施方式提供分布式神经网络系统,其中,故障和/或机会管理器FAM在本地使用存储的知识DK,并在要被分析的应用App的应用系统AS内执行。主要优点可以在于:因为例如故障分析代理FAA可以是可互换的,并且局部神经网络系统的停工不会影响在MES内运行的所有应用(除了那些在包含局部神经网络系统的局部应用系统内运行的应用以外),所以分布式神经网络系统内在地更加牢固。