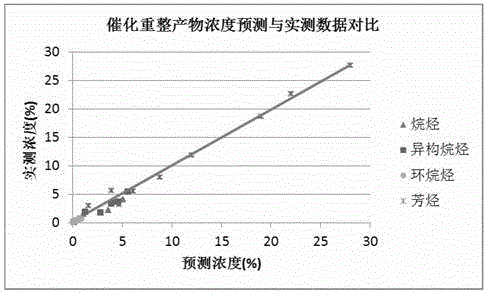
本发明属于石油炼制及石油化工生产
技术领域:
,具体涉及一种分子水平的实时优化方法。
背景技术:
:实时优化(英文全称RealTimeOptimization,英文缩写RTO)是炼油和石化企业实现计划——调度——操作——控制一体化优化的关键环节。基于实时优化可以将生产计划、调度排产、操作优化、操作控制整体贯通,真正做到优化目标从上到下、从全局到局部的层层分解和闭环控制。实时优化能够根据生产条件、市场因素、企业计划的变化而实时调整生产方案,使得整个生产持续保持在最优状态(如图1所示)。基于实时优化技术,在不增加重大设备投资的情况下,可以充分发挥现有生产装置的运行潜力,有效提高主要技术经济指标,有效实现增产、节能、降耗的目标,为企业创造新增利润。因此,实时优化是炼油和石化企业实现计划调度操作化一体化优化不可或缺的关键一环。原油的分子成分复杂,含有超过20万个分子组分,即使是较轻的汽油、柴油产品也有300多个分子。但目前企业由于无法详细掌握原油、半成品产物和成品产物的具体分子构成,企业大多基于化验得出的宏观物性数据(如干点、闪点、硫含量、芳烃含量等),结合经验对装置进行管理,未从分子角度了解原料及产物成分,并针对不同分子组成设计对应的精细化生产方案,实现分子水平的优化排产、调度和操作。目前,炼油和石化装置模拟和优化研究大多基于集总方法(将动力学性质相似的组分用一个虚拟组分代替,然后构造这些集总组分的反应网络的方法),对炼油及化工生产过程中原料分子详细构成和分子层级本征动力学机理没有深入运用。这种基于经验模型或集总模型的方法,只在经验数据所覆盖的条件范围内有一定的准确度;当原料发生变化,或反应条件超出历史数据覆盖范围时,其精确度会受很大影响,导致优化效果不佳,甚至导致损失的产生,因此很难用于全局优化和实时优化。而基于原料详细分子组成和分子层级本征动力学机理的实时优化方法能够从分子水平来认识石化生产过程,更准确预测产品性质,并且其使用范围更为广泛,在原料或反应条件发生较大变化时仍然能够具备很高的精确度。与基于集总模型的实时优化方法相比,分子水平的实时优化方法具有更准确、更可靠、适用范围更广等优势。技术实现要素:本发明为了实现炼油和石化装置的实时优化,使得装置连续的保持在最优状态,提升经济效益并降低能耗,提出了一种分子水平的实时优化方法。该方法基于原油分子数据库和模型预测的产物分子组成数据,准确掌握每套炼油和石化装置原料和产物的详细分子组成,基于分子层级本征动力学反应机理,把握炼油与石化生产工艺最基础的原理,使得实时优化系统所适用的范围更为广泛、更为准确。从而,本发明提供了一种针对炼油或石化装置的分子水平的实时优化(RTO)方法,包括如下步骤:(1)获取生产装置的原料及产物的宏观性质;(2)获取原料的详细分子组成;(3)根据原料的分子组成,预测产物的分子组成;(4)根据预测的产物的分子组成,计算产物的宏观性质;(5)将步骤4中所预测的产物宏观性质,与步骤1中获取的实际的产物宏观性质进行比对,校正动力学模型中的参数;(6)根据优化的动力学模型,运用优化算法,计算最优生产方案;(7)将步骤(6)产生的最优生产方案部署至生产装置;(8)生产装置进入稳态后,重复步骤(1)-(7),进行下一次循环;整个系统不断循环,使得生产持续保持在最优状态。其中步骤(1)中,可以通过在线分析仪器实时获取生产装置的原料及产物的宏观性质。所述的在线分析仪器可以是质谱、气相色谱、气相色谱-质谱联用、核磁共振、近红外光谱或其他任何化学分析仪器中的一种或多种联用。所述宏观性质包括但不限于密度、馏程、碳含量、硫含量、氮含量、残碳、闪点等物理化学性质。其中步骤(2)中,可以根据步骤原料宏观性质,比对原料分子数据库,获取原料的详细分子组成。所述原料分子数据库可以是由已知原料的宏观性质组成的数据库。在一个特定的实施例中,根据申请号为CN201610705619.1的专利申请中公开的方法,例如根据该专利申请的权利要求1-8中任意一项所述的方法,来确定原料的详细分子组成。原油的分子成分复杂,含有超过20万个分子组分。在本发明中,优选使用100个以上的分子,例如100-200000个分子,更优选使用500个、1000个、5000个、10000个或50000个以上的分子来描述原料的详细分子组成。在一些特定的实施方式里,使用1-10万个分子组成描述原料的成分。在一些特定的实施方式里,使用2-10万个、2-5万个或2-3万个分子组成描述原料的成分。其中步骤(3)中,可以根据步骤(2)获取的原料详细分子组成,运用分子层级本征动力学模型和过程模型,预测产物分子组成。典型的本征动力学模型可以是本领域已知的。在本发明中,分子层级本征动力学模型针对原料详细分子组成构建反应网络,从而能基于原料详细分子组成,通过本征动力学模型,精确预测产物的分子组成。其中步骤(4)中,可以运用物性算法模型计算产物宏观性质,产物宏观性质的计算基于产物每个分子成分的相关性质进行加权求和或应用混合因子进行调整。其中预测产物的宏观性质包括但不限于密度、馏程、碳含量、硫含量、氮含量、残碳、闪点等。典型的物性算法模型可以是本领域已知的。在本发明中,物性计算模型基于详细分子组成计算产物与原料的宏观性质:首先,根据每个组成分子的详细结构计算其物理化学性质;其次,根据原料与产品中每个分子的浓度,通过加权求和或运用混合因子调整计算混合物的宏观性质。其中步骤(6)中,可以基于当前原料组成、市场条件、企业规划、设备约束等条件计算最优生产方案,最优生产方案的优化目标可以是最大化经济效益、最小化能耗、最大化某种产物产量中的一种或多种。其中步骤(7)中,所述的部署具体为将最优生产方案在线部署至先进控制系统(APC);APC系统接收到指令后在线部署至集散控制系统(DCS),从而控制生产装置。进一步,本发明提供了一种针对炼油和石化装置的分子水平的实时优化方法,其特征在于,包含以下步骤:(1)通过在线分析仪器实时获取生产装置的原料及产物的宏观性质,包括但不限于密度、馏程、碳含量、硫含量、氮含量、残碳、闪点等;(2)根据步骤(1)中在线分析仪器所获取的原料宏观性质,比对原料分子数据库,获取原料的详细分子组成,使用100-200000个分子组成描述原料的成分;(3)根据步骤(2)中获取的原料详细分子组成,运用分子层级本征动力学模型和过程模型,预测产物分子组成,其中分子层级本征动力学模型针对原料详细分子组成构建反应网络;(4)根据步骤(3)中所预测的产物分子组成,运用物性算法模型计算产物宏观性质,包括但不限于密度、馏程、碳含量、硫含量、氮含量、残碳、闪点,产物宏观性质的计算基于产物每个分子成分的相关性质进行加权求和或应用混合因子进行调整;(5)将步骤(4)中所预测的产物宏观性质,与步骤1中在线分析仪器测量的产物宏观性质进行比对,并校正动力学模型中的参数,使得模型预测准确;(6)在完成步骤(5)的模型校正后,运用优化算法,计算出当前原料组成、市场条件、企业规划、设备约束等条件下最优的生产方案,此处优化的目标可以是最大化经济效益、最小化能耗、最大化某种产物产量中的一种或多种;(7)将步骤(6)所产生的最优生产方案在线部署至APC系统;(8)APC系统接收到步骤(7)的指令后在线部署至DCS系统,控制生产装置;(9)生产装置进入稳态后,重复步骤(1)-(8),进行下一次循环,整个系统不断循环,使得生产持续保持在最优状态。另一方面,本发明也提供了用于实施上述方法的专用装置。具体而言,本发明的装置包含了炼油或石化生产装置,在线分析装置,模型计算系统,先进控制系统(APC),集散控制系统(DCS)。其中模型计算系统可以包括根据物性确定分子组成的模型系统、根据原料分子组成预测产物分子组成的分子层级本征动力学模型系统和过程模型系统、根据预测的产物组成计算产物物性的物性算法模型系统和/或优化算法系统;其中模型计算系统可以将生产方案在线部署至APC系统;APC可以将指令进一步部署至DCS系统;DCS系统能够控制生产装置。从而,本发明的方法在每个环节均围绕原料与产物的详细分子组成构建。首先本方法首次使用2-3万个或更多的分子来描述原料与产品的分子组成,而现有的方法通常使用400个以内的集总组分或虚拟组分来描述原料与产品。分子层级本征动力学模型也是基于原料的详细分子组成构建,所形成的反应网络代表了分子反应的本征特性。而现有方法多基于集总模型,形成的反应网络为表征反应网络。本方法的本征反应网络与现有方法的表征反应网络相比,具有适用性更广、延展性更佳、准确度更高等优点。本方法的物性计算模型同样基于详细分子组成计算产物与原料的宏观性质:首先,根据每个组成分子的详细结构计算其物理化学性质;其次,根据原料与产品中每个分子的浓度,通过加权求和或运用混合因子调整计算混合物的宏观性质。而现有方法多基于集总组分或虚拟组分的物理化学性质计算原料与产物的宏观性质,在应对混合效应时无法抓住分子构成的本质规律,而多采用经验模型调整的方法。正是因为本方明所有的步骤均围绕详细的分子组成构建,因此本发明与现有技术相比所具有的优点主要包括以下方面:1.通过分子水平的实时优化使得优化方向更为准确,有效降低错误判断优化方向的风险,使得优化方案更为有效;2.基于详细分子组成与分子层级本征动力学机理的实时优化方法不受原料组成和反应条件的约束,能够适用于更广的原料组成与反应条件,使得运用本发明方法的调试期大大缩短,更迅速的产生优化效果;3.通过分子管理,能够获取详细的产物分子组成,并可获取更丰富的性质数据,预测和优化能力更为完整;4.基于分子水平的实时优化系统,其原料和产物都用详细的分子组成描述,因此可获知不同生产装置之间的流股分子组成,使得不同生产装置可联合优化,并可进一步构建连贯的炼油厂和石化厂全流程优化模型。附图说明图1、炼油和石化企业实时优化(RTO)架构图。图2、实时优化(RTO)流程图。图3、本发明应用于催化重整装置实时优化时的在线色谱分析仪结构配置。图4、实时优化系统对催化重整装置反应温降的预测与实测数据对比。图5、实时优化系统对催化重整反应装置产物浓度的预测与实测数据对比。图6、本方法实施常减压装置实时优化的流程图。图7、本方法使用20万个原油分子与现有方法使用400个原油分子在预测产品物性准确度上的对比。具体实施方式下面通过具体实施方式对本发明作进一步详细的描述。【实施例1】本发明运用在催化重整装置上的实施例。1.以一套催化重整装置为实施对象,采用在线色谱分析仪作为在线检测仪器,实时检测原料及产物的宏观性质,包括饱和烃、非饱和烃、甲苯、二甲苯等物质的含量;图3显示了本实施例所使用的在线色谱分析仪的结构配置。2.根据步骤1中在线色谱分析仪所获取的原料宏观性质,比对重整原料分子数据库,获取原料的详细分子组成。重整原料分子组分中含量在0.05%以上的有正构烷烃、异构烷烃、五元环烷烃、六元环烷烃、芳烃等共计243个分子组分。3.根据步骤2中获取的重整原料详细分子组成,运用催化重整分子层级本征动力学模型,预测产品分子组成。动力学模型包括针对243个主要分子的脱氢芳化、烷烃环化、烷烃异构化等共计569种反应。图5显示了本实时优化系统对烷烃、异构烷烃、环烷烃、芳烃产物浓度的预测结果,生产条件范围跨度近100°C,平均误差在1.5%以内。4.根据步骤3中所预测的催化重整产物分子组成,运用物性算法模型计算其性质,包括饱和烃、非饱和烃、甲苯、二甲苯等物质的含量。5.将步骤4中所预测的产物宏观性质,与步骤1中在线色谱分析仪测量的产物宏观性质进行比对,并校正催化重整反应动力学模型中的参数,使得模型预测准确。6.在完成步骤5的模型校正后,运用优化算法,计算出当前原料组成、市场条件、企业规划、设备约束等条件下最优的生产方案,包括反应温度、配料比等。此处优化的目标可以是最大化整体效益、最小化能耗、最大化芳烃收率或重整汽油收率中的一种或多种。7.将步骤6所产生的最优生产方案在线部署至催化重整装置的APC系统。8.APC系统接收到步骤7的指令后在线部署至DCS系统,控制催化重整生产装置的温度与配料比等参数。9.生产装置进入稳态后,重复步骤1-8,进行下一次循环。整个系统不断循环,使得生产持续保持在最优状态。实验结果:表1展示了步骤2中确定的详细分子组成中的部分分子结构。由于数量较大,未将全部分子结构列出。图4显示了通过实时优化系统预测的催化重整装置反应温降与实测温降的对比,操作温度范围跨度为50°C,准确度高达98%以上。图5显示了本实时优化系统对烷烃、异构烷烃、环烷烃、芳烃产物浓度的预测结果,生产条件范围跨度近100°C,平均误差在1.5%以内。本实施例特有的效果在于实时优化是基于详细的原料与产物分子组成,并结合了分子层级本征动力学模型。在现有的催化重整模拟与优化方法中,通常采用几个或几十个集总虚拟组分。而本实施例则用243个分子组分详细描述碳数在1-12的重整原料及产物分子组成。针对这243个分子组分,运用分子层级本征动力学模型的569个化学反应描述原料到产物的反应机理。本发明结合详细的分子组成与本征动力学模型,能够准确的预测243个分子组成的产率,而现有方法只能粗略的预测几十个集总产物的产率。对产物分子的详细预测能够从根本上掌握产物的各种性质,为精准的实时优化提供了基础。基于分子层级本征动力学模型和详细分子组成的实时优化系统,其延展性也大大超出目前已有的方法。目前已有的方法通常只能覆盖5-10°C的催化重整生产条件范围,而本方法可覆盖100°C以上的生产范围,延展性提升10倍以上。延展性和准确性也使得本发明方法能够在更宽的范围内实施优化,寻找全局最优解,而现有方法只能在有限的条件范围内进行局部优化。本实施例高度结合分子数据库、软件、硬件三个环节,使得实时优化系统更为完整,与基于集总模型或经验模型的优化系统相比,所作出的优化决策也更为科学和准确。图3显示了本实施例所使用的在线色谱分析仪的结构配置。表1包含了本发明催化重整原料及产物分子数据库中部分常见的分子化学结构。图4显示了通过实时优化系统预测的催化重整装置反应温降与实测温降的对比,操作温度范围跨度为50°C,准确度高达98%以上。图5显示了本实时优化系统对烷烃、异构烷烃、环烷烃、芳烃产物浓度的预测结果,生产条件范围跨度近100°C,平均误差在1.5%以内。表1、本发明所使用的催化重整原料及产物分子数据库中部分常见的分子化学结构。【实施例2】本发明运用在常减压蒸馏装置上的实施例。1.以一套常压蒸馏与减压蒸馏联合装置为实施对象,采用在线近红外光谱分析仪或核磁共振分析仪作为在线检测仪器,实时检测原料及产物的性质。检测对象包括原油、常顶油、常一线、常二线、常三线、减一线、减二线、减三线、减四线等流股,检测性质包括密度、馏程、干点、粘度、残碳、硫含量等。2.根据步骤1中在线近红外光谱分析仪或核磁共振分析仪所获取的原油性质,比对原油分子数据库,获取原料的详细分子组成。原油分子数据库包含近20万个分子,描述原油从初馏点到终馏点所有馏程范围的分子组分,涵盖液化石油气、石脑油、汽油、煤油、柴油、润滑油、重油、减压渣油等馏分。运用这20万个分子中的约2-3万个分子描述各个特定的原油。表2了显示本方法所使用的部分原油分子结构。3.根据步骤2中获取的原油详细分子组成,运用常减压切割模型,对常减压装置塔顶和各侧线的出口产物进行模拟,预测塔顶和各侧线产物分子组成。4.根据步骤3中所预测的各流股分子组成,运用物性算法模型计算其性质,包括密度、馏程、干点、粘度、残碳、硫含量等。表3展示了本方法能够预测的原油及常减压装置各出口流股的31种物性。5.将步骤4中所预测的产物物性,与步骤1中在线近红外光谱分析仪或核磁共振分析仪测量的各流股物性进行比对,并校正常减压切割模型的参数,使得模型预测准确。6.在完成步骤5的模型校正后,运用优化算法,计算出当前原料组成、市场条件、企业规划、设备约束等条件下最优的生产方案,包括常压炉、减压炉的预热温度,各侧线切割温度、回流比等。此处优化的目标可以是最大化整体效益、最小化能耗、最大化某侧线流率中的一种或多种。7.将步骤6所产生的最优生产方案在线部署至常减压装置的APC系统。8.APC系统接收到步骤7的指令后在线部署至DCS系统,控制常减压装置的温度与回流比等参数。9.生产装置进入稳态后,重复步骤1-8,进行下一次循环。整个系统不断循环,使得生产持续保持在最优状态。图6为本方法实施常减压装置实时优化的流程图。图7显示了本方法使用20万个原油分子与现有集总方法在预测产品物性准确度上的对比。表2、本方法所使用的部分原油分子结构编号性质名称编号性质名称1密度(20°C)17三环芳香烃(%)2C18四环及以上芳香烃(%)3H19硫化物(%)4S20胶质(%)5N21沥青质(%)6O22Fe(%)7K值23Ni(%)8粘度(cP@50°C)24V(%)9闪点25实沸点曲线(°C)10凝点26分子量11残碳(%)27不饱和度(DBE)12总酸值28Z-值13蜡含量29辛烷值(RON)14饱和烃(%)30溶解度参数((cal/mol)^0.5)15一环芳香烃(%)31芳香性(%)16二环芳香烃(%)表3、本方法能够预测的原油及常减压装置各出口流股的31种物性。本实施例特有的效果在于实时优化是基于详细的原油分子组成,原油分子数据库包括20万个分子,每个原油由2-3万个分子描述,而现有集总方法通常只包括400个以内的分子,在精细程度上有大幅提升。图6为本方法实施常减压装置实时优化的流程图。表2显示本方法所使用的部分原油分子结构。本方法与现有方法比较所具有的第二个优势在于,详细的原油分子组成为常减压装置的后续生产装置提供了详细的原料分子数据,比如催化重整装置、催化裂化装置、加氢精制和加氢裂化装置、延迟焦化装置等。现有的方法则无法为这些装置提供详细的原料分子数据。本方法的第三个优势在于其见效周期的缩短和效率的提升。在常减压装置所处理的原油发生变化时,本方法可及时调整原油分子数据,与现有方法比,可将校正时间缩短80%以上,大幅降低见效周期。本方法的第四个优势在于其延展性强,可以在更宽范围的生产条件内进行优化。现有的方法只能准确预测10°C左右的温度区间,而本方法可准确预测超过50°C的生产条件跨度范围。图7显示了本方法使用20万个原油分子与现有方法使用400个原油分子在预测产品物性准确度上的对比。本方法的第五个优势在于能够提供更为详细的原料与产物性质。基于对原油及各侧线流股详细分子组成的掌握,可准确预测各流股的31种宏观性质,而现有方法只能预测10-15种宏观性质。表3展示了本方法能够预测的原油及常减压装置各出口流股的31种物性。。当前第1页1 2 3