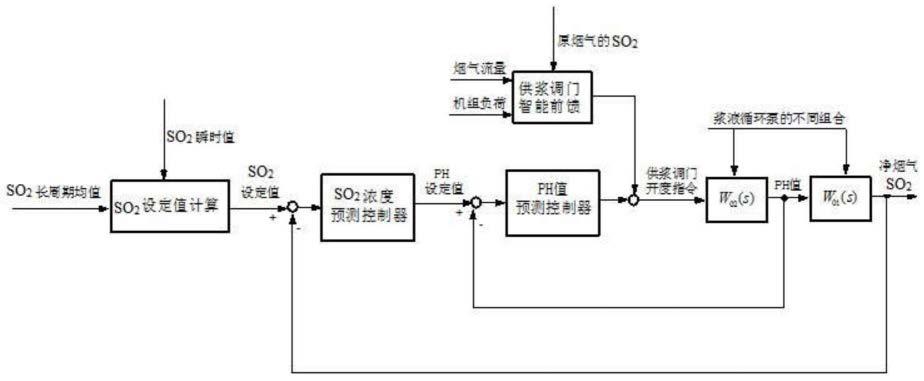
1.本发明属于燃煤发电技术领域,具体涉及一种火电机组启停过程多目标一体化控制系统及控制方法。
背景技术:2.目前国内大型火电机组启停过程中的脱硫控制系统(fgd),普遍对烟气so2浓度、吸收塔ph值以及合理的浆液循环泵运行组合问题是割裂处理的,整个fgd仅设计一套吸收塔ph值控制回路(通过供浆调门进行控制),当机组工况发生变化造成净烟气so2浓度不能满足要求时,运行人员只能根据经验设定合适的ph值和启动浆液循环泵来进行调整。同时由于吸收塔ph值属于非常典型的大滞后被控对象(时间常数达到1200s~1600s),dcs内基于pid算法设计的ph值控制回路运行性能很差,基本无法满足正常的控制需求。上述状况使得目前fgd系统的自动水平很低,几乎完全依靠运行人员的手动调节,大部分运行时间内fgd系统未处于最佳运行工况,造成较高的厂用电率和石灰石消耗量,同时易出现净烟气so2超标而遭到环保考核。因此,有必要为火电机组启停过程的脱硫系统进行优化控制。
技术实现要素:3.本发明的目的是提供一种火电机组启停过程多目标一体化控制系统及控制方法,在满足环保考核要求的前提下,通过优化控制系统的调整,使整体fgd脱硫系统始终保持在最佳运行工况。
4.技术方案:为实现上述发明目的,本发明采用如下技术方案:
5.一种火电机组启停过程多目标一体化控制系统,包括净烟气so2浓度控制模块、浆液ph值控制模块和浆液循环泵运行组合调度模块;所述净烟气so2浓度控制模块用于根据净烟气so2浓度设定值与实测值之间的偏差,通过实时调整脱硫塔中浆液ph值,控制净烟气so2浓度到设定值;所述浆液ph值控制模块用于将净烟气so2浓度控制模块中得到的浆液ph值作为设定值,通过实时调整供浆调门的开度,控制浆液ph值;所述浆液循环泵运行组合调度模块,以净烟气so2浓度和浆液循环泵电耗为输出的数学模型,在确保电耗最低,且so2浓度和ph值在允许范围的前提下,通过粒子群约束优化算法,获得浆液循环泵的最佳运行组合。
6.用上述火电机组启停过程多目标一体化控制系统进行火电机组启停过程多目标一体化控制的方法,该方法包括如下步骤:
7.浆液循环泵运行组合调度模块,首先建立以机组负荷、烟气流量、原烟气so2浓度、浆液循环泵运行组合、吸收塔ph值为输入变量,以净烟气so2浓度和浆液循环泵电耗为输出的数学模型,在确保电耗最低,且so2浓度和ph值在允许范围的前提下,通过采用粒子群约束优化算法,获得浆液循环泵的最佳运行组合,并将最佳运行组合的算法结果发送给净烟气so2浓度控制模块、浆液ph值控制模块,然后净烟气so2浓度控制模块用于根据净烟气so2浓度设定值与实测值之间的偏差,通过实时调整脱硫塔中浆液ph值,控制净烟气so2浓度到
设定值;所述浆液ph值控制模块用于将净烟气so2浓度控制模块中得到的浆液ph值作为设定值,通过实时调整供浆调门的开度,控制浆液ph值。
8.进一步地,所述寻找浆液循环泵的最优运行组合,使浆液循环泵的电耗最低所使用的目标函数j:
[0009][0010]
其中,e为浆液泵的电耗,它是浆液循环泵的运行组合的函数,由粒子群约束优化算法确定;c是so2的上限值,[k1,k2]是浆液ph值的允许范围。
[0011]
进一步地,所述so2的上限值c取35mg/m3。
[0012]
有益效果:与现有技术相比,本发明针对燃煤火电机组启停fgd系统运行调整的三个核心问题(净烟气so2浓度控制、吸收塔ph值控制、浆液循环泵运行组合),提出了一种火电机组启停过程多目标一体化控制系统,在满足环保考核要求的前提下,通过优化控制系统的调整,使脱硫系统始终保持在最佳运行工况。
附图说明
[0013]
图1是本发明的控制原理图。
具体实施方式
[0014]
为了使本发明要解决的技术问题、技术方案和有益效果更加清楚,下面结合附图及具体实施例进行详尽的描述。
[0015]
本发明公开了一种火电机组启停过程多目标一体化控制系统,并在国内某电厂应用,如图1所示,本发明实施例公开的一种火电机组启停过程多目标一体化控制系统,包括净烟气so2浓度控制模块、浆液ph值控制模块和浆液循环泵运行组合调度模块;所述净烟气so2浓度控制模块用于根据净烟气so2浓度设定值与实测值之间的偏差,通过实时调整脱硫塔中浆液ph值,控制净烟气so2浓度到设定值;所述浆液ph值控制模块用于将净烟气so2浓度控制模块中得到的浆液ph值作为设定值,通过实时调整供浆调门的开度,控制浆液ph值;所述浆液循环泵运行组合调度模块,以净烟气so2浓度和浆液循环泵电耗为输出的数学模型,在确保电耗最低,且so2浓度和ph值在允许范围的前提下,通过粒子群约束优化算法,获得浆液循环泵的最佳运行组合。
[0016]
用上述火电机组启停过程多目标一体化控制系统进行火电机组启停过程多目标一体化控制的方法,该方法包括如下步骤:
[0017]
浆液循环泵运行组合调度模块,首先建立以机组负荷、烟气流量、原烟气so2浓度、浆液循环泵运行组合、吸收塔ph值为输入变量,以净烟气so2浓度和浆液循环泵电耗为输出的数学模型,在确保电耗最低,且so2浓度和ph值在允许范围的前提下,通过采用粒子群约束优化算法,获得浆液循环泵的最佳运行组合,并将最佳运行组合的算法结果发送给净烟气so2浓度控制模块、浆液ph值控制模块,然后净烟气so2浓度控制模块用于根据净烟气so2浓度设定值与实测值之间的偏差,通过实时调整脱硫塔中浆液ph值,控制净烟气so2浓度到设定值;所述浆液ph值控制模块用于将净烟气so2浓度控制模块中得到的浆液ph值作为设定值,通过实时调整供浆调门的开度,控制浆液ph值。
[0018]
进一步地,所述寻找浆液循环泵的最优运行组合,使浆液循环泵的电耗最低所使用的目标函数j:
[0019][0020]
其中,e为浆液泵的电耗,它是浆液循环泵的运行组合的函数,由粒子群约束优化算法确定;c是so2的上限值,[k1,k2]是浆液ph值的允许范围。
[0021]
所述so2的上限值c取35mg/m3。
[0022]
通过采用受约束的非线性粒子群优化算法实施整个寻优计算,最终可获得浆液循环泵的最优运行组合,使浆液循环泵的电耗最低,同时满足对so2的有效控制。
[0023]
以上实施例仅为本发明的优选实施例,仅用于更加清楚地说明本发明方法,并非对本发明作任何其他形式的限制,应当指出的是,对于本领域一般技术而言,在不背离本发明原理和精神的前提下对其所做出的任何显而易见的改动,都应该包含在本发明的权利要求的保护范围内。
技术特征:1.一种火电机组启停过程多目标一体化控制系统,其特征在于,包括净烟气so2浓度控制模块、浆液ph值控制模块和浆液循环泵运行组合调度模块;所述净烟气so2浓度控制模块用于根据净烟气so2浓度设定值与实测值之间的偏差,通过实时调整脱硫塔中浆液ph值,控制净烟气so2浓度到设定值;所述浆液ph值控制模块用于将净烟气so2浓度控制模块中得到的浆液ph值作为设定值,通过实时调整供浆调门的开度,控制浆液ph值;所述浆液循环泵运行组合调度模块,以净烟气so2浓度和浆液循环泵电耗为输出的数学模型,在确保电耗最低,且so2浓度和ph值在允许范围的前提下,通过粒子群约束优化算法,获得浆液循环泵的最佳运行组合。2.一种用权利要求1所述火电机组启停过程多目标一体化控制系统进行火电机组启停过程多目标一体化控制的方法,其特征在于,该方法包括如下步骤:浆液循环泵运行组合调度模块,首先建立以机组负荷、烟气流量、原烟气so2浓度、浆液循环泵运行组合、吸收塔ph值为输入变量,以净烟气so2浓度和浆液循环泵电耗为输出的数学模型,在确保电耗最低,且so2浓度和ph值在允许范围的前提下,通过采用粒子群约束优化算法,获得浆液循环泵的最佳运行组合,并将最佳运行组合的算法结果发送给净烟气so2浓度控制模块、浆液ph值控制模块,然后净烟气so2浓度控制模块用于根据净烟气so2浓度设定值与实测值之间的偏差,通过实时调整脱硫塔中浆液ph值,控制净烟气so2浓度到设定值;所述浆液ph值控制模块用于将净烟气so2浓度控制模块中得到的浆液ph值作为设定值,通过实时调整供浆调门的开度,控制浆液ph值。3.根据权利要求2所述的火电机组启停过程多目标一体化控制的方法,其特征在于,所述寻找浆液循环泵的最优运行组合,使浆液循环泵的电耗最低所使用的目标函数j:其中,e为浆液泵的电耗,它是浆液循环泵的运行组合的函数,由粒子群约束优化算法确定;c是so2的上限值,[k1,k2]是浆液ph值的允许范围。4.根据权利要求3所述的火电机组启停过程多目标一体化控制的方法,其特征在于,所述so2的上限值c取35mg/m3。
技术总结本发明公开一种火电机组启停过程多目标一体化控制系统及控制方法。本发明的控制系统包括净烟气SO2浓度控制模块、浆液pH值控制模块和浆液循环泵运行组合调度模块;净烟气SO2浓度控制模块用于根据净烟气SO2浓度设定值与实测值之间的偏差,控制净烟气SO2浓度到设定值;浆液pH值控制模块用于将净烟气SO2浓度控制模块中得到的浆液PH值作为设定值,通过实时调整供浆调门的开度,控制浆液pH值;所述浆液循环泵运行组合调度模块通过粒子群约束优化算法,获得浆液循环泵的最佳运行组合。本发明通过优化控制系统的调整,使整体FGD脱硫系统始终保持在最佳运行工况。始终保持在最佳运行工况。始终保持在最佳运行工况。
技术研发人员:潘喜良 林松青 李耀亮 刘鹏峰 李雷 戴海鹏 黄学辉 杜武荣 徐超群 游联欢 詹新民
受保护的技术使用者:华能罗源发电有限责任公司
技术研发日:2022.02.22
技术公布日:2022/6/14