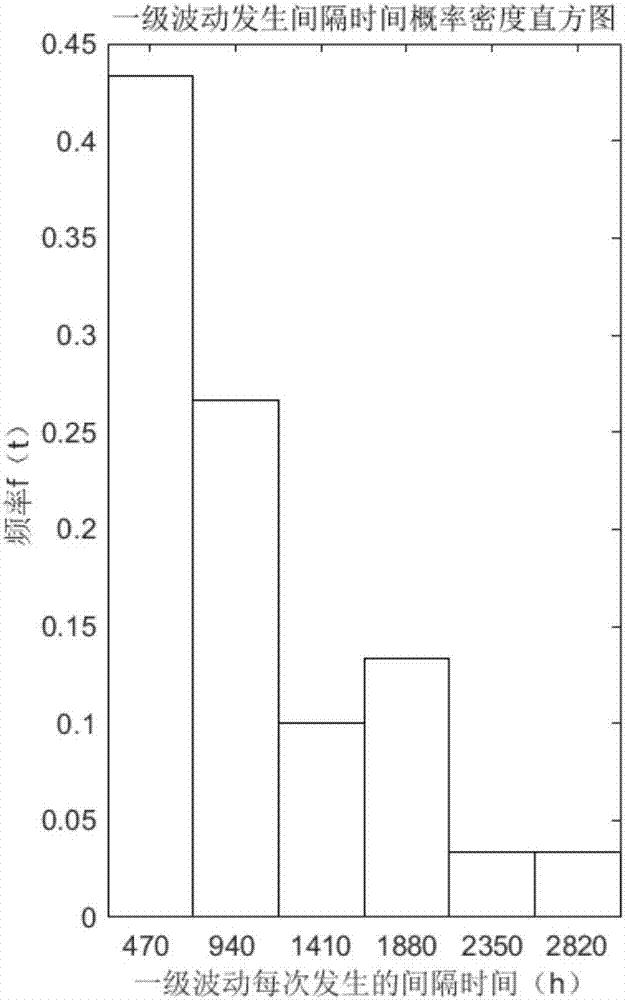
本发明涉及一种生产线
技术领域:
的评价方法,更确切地说,本发明涉及一种离散型生产线产能波动过程及其影响度评价方法。
背景技术:
:生产线性能评价是生产线设计阶段一项至关重要的工作,其评价结果反映所设计生产线的生产性能,既可指导生产线生产计划和维护策略的制定,又是生产线设计者对现有方案进行优化设计的依据。目前,评价生产线性能的常用指标有生产率、在制品水平、产品通过时间、各工位饥饿率和堵塞率等,但现有研究多局限于其稳态表现,较少考虑到生产线运行的不稳定性所导致的产能波动,然而生产线是一个复杂多变的系统,生产线上设备、人员众多,任何设备故障、人员操作不当等都会引起产能波动,因此生产管理人员在制定生产组织方案前,需要预先对生产线的产能进行充分合理的评价,综合了解生产线的平均生产能力和产能波动性,才能制定出合理的生产计划、生产调度方案以及生产线维护策略,使企业效益最大化。在实际生产过程中,生产组织人员为减小生产线的产能波动对企业生产效益造成的影响,需要了解生产线的产能波动规律及其影响程度,从而及时开展生产调度和生产线维护等工作。然而现有评价产能波动性的方法只能评价生产线产能的总体波动性能,不能评价生产线的产能波动的过程,并且现有评价技术无法使生产组织者明确不同程度的产能波动对生产组织工作造成的影响,所以其评价结果无法为生产线组织人员制定具体生产组织方案提供依据,导致生产组织者只得凭借经验定性感知生产线在生产过程中可能出现的波动情况,并制定相应的生产调度和生产线维护策略,然而这种经验方法缺乏理论依据,制定出的生产组织方案难以切合生产线实际运行情况,不利于企业实现生产效益最大化。对于生产线产能波动性对订单交货期的影响方面的研究,目前研究人员普遍认为产能的波动服从正态分布,并通过统计或估计生产线产能的均值和方差来评价其波动性,这种方法只能大致体现生产线产能的波动范围,其评价结果只能协助生产管理者预计产品交货期的可能范围,无法指导其制定最佳交货期。技术实现要素:本发明所要解决的技术问题是为克服现有技术无法评价生产线产能波动的过程,也无法评价产能波动过程对企业生产组织工作和订单交货期的影响,导致生产组织者在针对生产线的产能变动情况制定具体生产组织计划时缺乏客观依据的问题,提供了一种离散型生产线产能波动过程及其影响度评价方法。为解决上述技术问题,本发明是采用如下技术方案实现的:所述的一种离散型生产线产能波动过程及其影响度评价方法的步骤如下:1)收集生产线运行数据;2)划分生产线的产能波动等级;3)处理生产线运行数据并绘制直方图;4)评价生产线的产能波动过程;5)评价生产线产能波动过程的影响度;6)应用生产线产能波动过程及其影响度的评价结果制定具体生产组织计划。技术方案中所述的收集生产线运行数据是指:1)记录离散型生产线上产出的所有合格品的下线时刻t,对于已投产的生产线和仍处于设计阶段尚未建成的生产线,生产组织人员可以分别通过以下两种方式获取生产线运行数据:(1)对于已投产的生产线,生产组织者可以跟踪生产线的现场运行情况,依次记录生产线上所有合格品的下线时刻t;(2)对于仍处于设计阶段尚未建成的生产线,生产组织者依据生产线的设计参数即生产线上工位数,各工位内的设备数,各工位内设备间的串、并联组织形式,各设备的操作时间、故障率、修复率和可用度,生产线上缓存区的位置和容量设置以及生产线上各设备间的物料转移策略,利用PlantSimulation仿真软件建立生产线仿真模型,通过运行生产线仿真模型依次记录所有合格品的下线时刻t;2)将所记录的生产线上产出的所有合格品的下线时刻t利用公式(1)进行计算,获得生产线上每件合格品的产出间隔时间:Δt=tn-1-tnn=1,2,3……;(1)Δt:每件合格品的产出间隔时间,以下称为单件产出间隔时间,单位:小时;tn:生产线产出第n件合格品的时刻,单位:小时;n:生产线产出合格品的编号。技术方案中所述的划分生产线的产能波动等级是指:生产线处于稳态无故障运行时,单件产出间隔时间应为定值T0,或者在T0上下出现微小浮动,当其值偏离T0较大时,即认为生产线的生产能力出现波动,为表示产能的波动程度,本发明将生产线的单件产出间隔时间Δt划分为6个区段,每个区段标记为一个产能波动等级,具体划分标准如下:1)零级波动的划分标准:单件产出间隔时间Δt小于生产线消化即加工完一个转运单位的产品所需的时间,Δt<T0×C(2)Δt:每件合格品的产出间隔时间,以下称为单件产出间隔时间,单位:小时;T0:生产线处于稳态无故障运行时的平均产出间隔时间,单位:小时;C:一个转运单位的容量;此时认为生产线处于正常无波动生产状态,故将此区段标定为零级波动;2)一级波动的划分标准:单件产出间隔时间Δt大于等于生产线消化一个转运单位的产品所需的时间,且小于生产线完全消化生产线上最小缓存区内所有在制品所需的时间,T0×C≤Δt<T0×Bmin(3)Bmin:生产线上所有缓存区中容量最小的缓存区的容量;通常认为这种情况为较常发生的停产,对生产组织过程造成的影响程度较小;3)二级波动的划分标准:单件产出间隔时间Δt大于等于生产线完全消化生产线上最小缓存区内所有在制品所需的时间,且小于等于其完全消化生产线上最大缓存区内所有在制品所需的时间,T0×Bmin≤Δt<T0×Bmax(4)Bmax:生产线上所有缓存区中容量最大的缓存区的容量;通常认为二级波动对生产组织过程造成一定的影响,如排除生产故障时除涉及线上工作人员外还需涉及设备管理、维修部门的协助;4)三级波动的划分标准:单件产出间隔时间Δt大于等于生产线完全消化生产线上最大缓存区内所有在制品所需的时间,且小于等于其完全消化生产线上最大缓存区内所有在制品数的两倍所需的时间,T0×Bmax≤Δt<T0×(2×Bmax)(5)通常认为三级波动对生产组织过程造成的影响程度高,此级波动对生产组织过程造成的影响除二级波动所提到的方面外,还会导致库存水平调整、产品保养成本升高这类相对严重的问题;5)四级波动的划分标准:单件产出间隔时间Δt大于等于生产线完全消化生产线上最大缓存区内所有在制品数的两倍所需的时间,且小于等于其完全消化生产线上最大缓存区内所有在制品数的三倍所需的时间,T0×(2×Bmax)≤Δt<T0×(3×Bmax)(6)生产线发生较长时间停产,四级波动的发生往往需要设备厂家协助排查故障,同时车间需要及时调整库存以保证按时完成任务,此时对生产组织工作造成较大影响;6)五级波动的划分标准:单件产出间隔时间Δt大于等于生产线完全消化生产线上最大缓存区内所有在制品数的三倍所需的时间,Δt≥T0×(3×Bmax)(7)此时认为生产线发生严重故障,整条生产线需要停产排查。技术方案中所述的处理生产线运行数据并绘制直方图是指:将划分生产线的产能波动等级步骤得到的各级产能波动数据进行统计处理,计算各级波动的发生频率及其每次发生的间隔时间,并绘制各级波动发生间隔时间的概率密度直方图和累积分布直方图:1)统计各级波动发生的频次Ni,并利用公式(8)计算各级波动发生的频率:ki:i级波动的发生频率;Ni:i级波动的发生频次;N:生产线运行时间内发生的单件产出间隔时间总数,即生产线产出的合格品总数;2)统计各级波动发生的间隔时间,并绘制各级波动发生间隔时间的概率密度直方图和累积分布直方图;(1)统计各级波动发生的间隔时间,即除零级波动外的各级波动内部每次发生时刻的时间间隔,如:第一次发生一级波动的时刻和第二次发生一级波动的时刻的时间差,计算公式为公式(9):TBLi(j)=ti(j+1)-ti(j)i=1,2…5(9)TBLi(j):i级波动的第j个间隔时间,单位:小时;ti(j):第j次发生i级波动的时刻,单位:小时;(2)将各级波动发生间隔时间的统计结果进行分组统计:利用斯特奇斯公式计算分组数目和组距,统计各组内发生该等级波动的频次和频率;(3)将上述统计结果绘制成各级波动发生间隔时间的概率密度直方图和累积分布直方图。技术方案中所述的评价生产线的产能波动过程是指:1)拟合各级波动发生间隔时间的概率分布函数fi(t),步骤如下:(1)识别候选分布:根据各级波动发生间隔时间的概率密度直方图和累积分布直方图估计各级波动发生间隔时间服从的分布形式;(2)采用最小二乘法针对所有候选分布进行参数估计,并使用相关系数检验法检验参数正确性,要求显著性水平α=0.05,最终确定各级波动发生间隔时间的概率密度函数fi(t);2)绘制各级波动发生间隔时间的概率密度分布函数的曲线,生产组织者根据该分布曲线对生产线的各级产能波动出现的时间间隔分布情况产生直观认识;3)利用公式(10)计算各个波动等级发生的平均间隔时间MTBLi,将其作为生产线产能波动过程的定量评价指标:MTBLi:i级波动发生的平均间隔时间,单位:小时;fi(t):i级波动发生间隔时间所服从的概率分布函数。技术方案中所述的评价生产线产能波动过程的影响度是指:1)评价生产线各级产能波动对企业内部生产组织工作的影响度IPOi:由于生产组织人员制定生产调度和生产线维护的计划时需要考虑各级波动对生产组织工作的不同影响程度,从而确定开展生产组织工作的优先顺序,因此本发明提出利用公式(11)计算各级波动对企业内部生产组织工作的影响度IPOi,这里主要考虑了各级波动的波动程度、重要程度和发生频率对生产组织工作产生的影响:IPOi:i级波动对企业内部生产组织工作的影响度;i级波动重要度参数;θi:i级波动的波动程度,取i级波动所对应的停产区间的中值,量纲为1;ki:i级波动的发生频率。2)评价生产线产能波动过程对企业订单交货期的影响度IDT。技术方案中所述的i级波动的重要度参数的具体获得步骤为:1)选择至少3名企业内部经验丰富的生产组织工作者对各级波动的发生对产品调度、人员调度、库存管理、交货期和生产成本的影响程度进行评价,求各因素的评价结果的平均值,得到各级产能波动对上述各因素的影响度的评价值s1i、s2i、s3i、s4i、s5i;2)管理者根据企业实际生产组织情况确定各影响因素的权重ω1、ω2、ω3、ω4、ω5;3)根据公式(12)计算各级波动初始重要度参数s1i:i级波动的发生对产品调度的影响程度;ω1:产品调度因子的权重;s2i:i级波动的发生对人员调度的影响程度;ω2:人员调度因子的权重;s3i:i级波动的发生对库存管理的影响程度;ω3:库存管理因子的权重;s4i:i级波动的发生对交货期的影响程度;ω4:交货期因子的权重;s5i:i级波动的发生对生产成本的影响程度;ω5:生产成本因子的权重;4)由于公式中参数ki的数量级通常为10-4,所以利用公式(13)对公式(12)中的各级波动初始重要度参数进行标准化处理得到各级波动重要度参数式中:级波动重要度参数;级波动初始重要度参数。技术方案中所述的评价生产线产能波动过程对企业订单交货期的影响度IDT是指:依据划分生产线的产能波动等级与处理生产线运行数据并绘制直方图步骤中各级产能波动的统计结果计算生产线波动性对企业订单交货期的影响度IDT,公式为(14):IDT:生产线波动过程对企业订单交货期的影响度;T0:生产线处于稳态无故障运行时的平均产出间隔时间,单位:小时;ki:i级波动的发生频率;TTRi:i级波动所对应的停产区间的中值,单位:小时。技术方案中所述的应用生产线产能波动过程及其影响度的评价结果制定具体生产组织计划是指:1)在制定生产调度方案和生产线维护计划时,管理人员应综合考虑各级产能波动发生的间隔时间MTBLi和各级产能波动对企业生产组织工作的影响度IPOi,以明确各级波动可能的发生时刻及其重要程度,从而确定生产组织工作的优先级,进而制定出更加切合生产线实际运行情况且符合企业生产效益的生产组织方案;2)在制定生产计划时,管理人员可以依据产能波动过程对企业对外部交货期的影响度指标IDT,结合公式(15)计算得到订单的最佳交货期DT:DT=Q×T0×IDT(15)DT:订单的最佳交货期,单位:小时;Q:生产线生产的合格品总数,制定生产计划时应代入计划生产的合格品数;T0:生产线处于稳态无故障运行时的平均产出间隔时间,单位:小时;IDT:生产线波动过程对企业订单交货期的影响度。与现有技术相比本发明的有益效果是:1.本发明所述的一种离散型生产线产能波动过程及其影响度评价方法以生产线自身的实际组织情况为依据将其产能波动程度划分为六个等级,这种产能波动等级的划分方法针对性强,切合生产线自身的实际运行与组织情况;2.本发明所述的一种离散型生产线产能波动过程及其影响度评价方法解决了现有技术无法评价生产线产能波动的过程的缺陷,定量评价了既定生产线的产能波动过程,评价结果能够为生产组织者在针对既定生产线的产能变动情况制定生产调度方案和生产线维护策略时提供具体、量化的依据,从而使其制定的生产组织计划切合生产线的实际运行情况;3.本发明所述的一种离散型生产线产能波动过程及其影响度评价方法定量评价了生产线各级产能波动对企业内部生产组织工作的影响度,使生产组织者明确何种程度的波动对生产组织工作造成的影响程度最大,从而协助其确定生产组织工作的优先级;4.本发明所述的一种离散型生产线产能波动过程及其影响度评价方法在所划分的产能波动等级的基础上,评价了生产线产能波动过程对企业订单交货期的影响度,该评价指标可直接指导企业制定订单的最佳交货期。附图说明下面结合附图对本发明作进一步的说明:图1为本发明所述的一种离散型生产线产能波动过程及其影响度评价方法的流程框图;图2为一级产能波动发生间隔时间的概率密度直方图;图3为一级产能波动发生间隔时间的累积概率分布直方图;图4为一级产能波动发生间隔时间的概率密度拟合曲线;图5为一级产能波动发生间隔时间的累积概率分布拟合曲线。具体实施方式下面结合附图对本发明作详细的描述:下面结合附图对一种离散型生产线产能波动过程及其影响度评价方法作详细说明:本发明提供了一种离散型生产线产能波动过程及其影响度评价方法,首先收集生产线上的运行数据,然后针对离散型生产线的具体组织情况划分产能波动等级,之后根据产能波动等级的划分依据将所收集的生产线运行数据进行分类和处理,随后评价了离散型生产线的产能波动过程,其后评价了各等级产能波动对企业内部生产组织工作的影响程度和生产线的产能波动过程对企业订单交货期的影响度。本方法的评价结果既能使生产组织工作者定量地了解生产线产能的波动过程,又能使其明确各级产能波动对企业生产组织工作的影响程度的大小,以便为其制定生产调度方案和生产线维护策略提供具体依据,此外还能指导生产线组织者制定订单的最佳交货期。本发明所述的一种离散型生产线产能波动过程及其影响度评价方法的步骤如下:1.收集生产线运行数据:记录离散型生产线上产出的所有合格品的下线时刻,并计算生产线上产出每件合格品的间隔时间,将其作为生产线波动性评价方法的输入数据;1)记录生产线上产出的所有合格品的下线时刻:记录离散型生产线上产出的所有合格品的下线时刻t,对于已投产的生产线和仍处于设计阶段尚未建成的生产线,生产组织人员可以分别通过以下两种方式获取生产线运行数据:(1)跟踪记录现场数据:对于已投产的生产线,生产组织者可以跟踪生产线的现场运行情况,依次记录生产线上所有合格品的下线时刻t;(2)先建立仿真模型再运行仿真模型并记录仿真数据:对于仍处于设计阶段尚未建成的生产线,生产组织者可以依据生产线的设计参数,即生产线线上工位数,各工位的设备数及设备间的串、并联组织形式,各设备的操作时间、故障率、修复率和可用度,缓存容量设置,物料转移策略,利用PlantSimulation仿真软件建立生产线仿真模型,该软件中文名称为工厂仿真,是工厂生产、物流仿真领域的常用软件,通过运行生产线仿真模型依次记录所有合格品的下线时刻t;2)计算生产线上产出每件合格品的间隔时间:将所记录的生产线上产出的所有合格品的下线时刻t利用公式(1)进行计算,获得生产线上每件合格品的产出间隔时间:Δt=tn-1-tnn=1,2,3……;(1)Δt:每件合格品的产出间隔时间,以下称为单件产出间隔时间,单位:小时;tn:生产线产出第n件合格品的时刻,单位:小时;n:生产线产出合格品的编号;2.划分生产线的产能波动等级:生产线处于稳态无故障运行时,单件产出间隔时间应为定值T0,或者在T0上下出现微小浮动,当其值偏离T0较大时,即认为生产线的生产能力出现波动,因此为表示产能的波动程度,本发明将生产线的单件产出间隔时间Δt划分为6个区段,每个区段标记为一个产能波动等级,具体划分标准如下:1)零级波动的划分标准:单件产出间隔时间Δt小于生产线消化(即加工完)一个转运单位的产品所需的时间,所述的一个转运单位是指各工位间一次性转移在制品数的最小单位,例如当生产线用托盘来转移所加工的产品时,各工位间一次性转移在制品数的最小单位为一托盘,根据托盘的规格,一个托盘内可以放置多件产品;Δt<T0×C(2)T0:生产线处于稳态无故障运行时的平均产出间隔时间,单位:小时;C:一个转运单位的容量;此时认为生产线处于正常无波动生产状态,故将此区段标定为零级波动;2)一级波动的划分标准:单件产出间隔时间Δt大于等于生产线消化一个转运单位的产品所需的时间,且小于生产线完全消化生产线上最小缓存区内所有在制品所需的时间,所述的最小缓存区是指容量最小的缓存区,一个缓存区可以由多个转运单位组成,例如当转运单位为托盘时,缓存区内可以设置1个托盘或多个托盘,所述的最小缓存区即指所设置托盘数最少的缓存区;T0×C≤Δt<T0×Bmin(3)Bmin:生产线上所有缓存区中容量最小的缓存区的容量;通常认为这种情况为较常发生的停产,对生产组织过程造成的影响程度较小;3)二级波动的划分标准:单件产出间隔时间Δt大于等于生产线完全消化生产线上最小缓存区内所有在制品所需的时间,且小于等于其完全消化生产线上最大缓存区内所有在制品所需的时间,T0×Bmin≤Δt<T0×Bmax(4)Bmax:生产线上所有缓存区中容量最大的缓存区的容量;通常认为二级波动对生产组织过程造成一定的影响,如排除生产故障时除涉及线上工作人员外还需涉及设备管理、维修部门的协助;4)三级波动的划分标准:单件产出间隔时间Δt大于等于生产线完全消化生产线上最大缓存区内所有在制品所需的时间,且小于等于其完全消化生产线上最大缓存区内所有在制品数的两倍所需的时间,T0×Bmax≤Δt<T0×(2×Bmax)(5)通常认为三级波动对生产组织过程造成的影响程度高,此级波动对生产组织过程造成的影响除二级波动所提到的方面外,还会导致库存水平调整、产品保养成本升高这类相对严重的问题;5)四级波动的划分标准:单件产出间隔时间Δt大于等于生产线完全消化生产线上最大缓存区内所有在制品数的两倍所需的时间,且小于等于其完全消化生产线上最大缓存区内所有在制品数的三倍所需的时间,T0×(2×Bmax)≤Δt<T0×(3×Bmax)(6)此时生产线发生较长时间停产,除上述影响外,四级波动的发生往往需要设备厂家等协助排查故障,同时车间需要及时调整库存以保证按时完成任务,此时对生产组织工作造成较大影响;6)五级波动的划分标准:单件产出间隔时间Δt大于等于生产线完全消化生产线上最大缓存区内所有在制品数的三倍所需的时间,Δt≥T0×(3×Bmax)(7)此时认为生产线发生严重故障,整条生产线需要停产排查;3.处理生产线运行数据并绘制直方图:将步骤2得到的各级产能波动数据进行统计处理,计算各级波动的发生频率及其每次发生的间隔时间,并绘制各级波动发生间隔时间的概率密度直方图和累积分布直方图;1)统计各级波动发生的频次Ni,并利用公式(8)计算各级波动发生的频率:ki:i级波动的发生频率;Ni:i级波动的发生频次;N:生产线运行时间内发生的单件产出间隔时间总数,即生产线产出的合格品总数;2)统计各级波动发生的间隔时间:统计各级波动发生的间隔时间,即除零级波动外的各级波动内部每次发生时刻的时间间隔,如:第一次发生一级波动的时刻和第二次发生一级波动的时刻的时间差,计算公式为公式(9):TBLi(j)=ti(j+1)-ti(j)i=1,2…5(9)TBLi(j):i级波动的第j个间隔时间,单位:小时;ti(j):第j次发生i级波动的时刻,单位:小时;3)绘制各级波动发生间隔时间的概率密度直方图和累积分布直方图:(1)将各级波动发生间隔时间的统计结果进行分组统计:利用斯特奇斯公式计算分组数目和组距,统计各组内发生该等级波动的频次和频率;(2)参阅图2与图3,将上述统计结果绘制成各级波动发生间隔时间的概率密度直方图和累积分布直方图;4.评价生产线的产能波动过程:首先利用步骤3的统计结果拟合各级波动发生间隔时间的概率分布函数fi(t),再绘制各级波动发生间隔时间的概率分布函数曲线,使生产组织者直观、定性地了解各级波动出现间隔时间的分布情况;然后,依据fi(t)计算各级波动发生的平均间隔时间MTBLi,将其作为生产线产能波动过程的定量评价指标,使生产组织者定量把握生产线的产能波动过程;1)拟合各级波动发生间隔时间的概率分布函数fi(t),步骤如下:(1)识别候选分布:参阅图2与图3,根据各级波动发生间隔时间的概率密度直方图和累积分布直方图估计各级波动发生间隔时间可能服从的分布形式;(2)采用最小二乘法针对所有候选分布进行参数估计,并使用相关系数检验法检验参数正确性(显著性水平α=0.05),最终确定各级波动发生间隔时间的概率密度函数fi(t);2)绘制各级波动发生间隔时间的概率分布图:参阅图4与图5,绘制各级波动发生间隔时间的概率密度函数和累积概率密度函数曲线,生产组织者可根据该分布曲线对生产线的各级产能波动出现的时间间隔分布情况产生直观认识;3)利用公式(10)计算各个波动等级发生的平均间隔时间MTBLi,将其作为生产线产能波动过程的定量评价指标:MTBLi:i级波动发生的平均间隔时间,单位:小时;fi(t):i级波动发生间隔时间所服从的概率分布函数;5.评价生产线产能波动过程的影响度:1)评价生产线各级产能波动对企业内部生产组织工作的影响度IPOi:由于生产组织人员制定生产调度和生产线维护的策略时需要考虑各级波动对生产组织工作的不同影响程度,从而确定生产组织工作的优先顺序,因此本发明提出利用公式(11)计算各级波动对企业内部生产组织工作的影响度IPOi,这里主要考虑了各级波动的波动程度、重要程度和发生频率对生产组织工作产生的影响:IPOi:i级波动对企业内部生产组织工作的影响度;i级波动重要度参数;θi:i级波动的波动程度,取i级波动所对应的停产区间的中值,量纲为1;ki:i级波动的发生频率;对于五级产能波动,由于该级波动的单件产出间隔时间划分区间为Δt≥T0×(3×Bmax),此区间为半开放式的,因此设定θ5取该区间内的所有Δt的值中最常出现的值。上述i级波动的重要度参数的具体获得步骤为:(1)选择至少3名企业内部经验丰富的生产组织工作者对各级波动的发生对产品调度、人员调度、库存管理、交货期和生产成本的影响程度进行评价,求各因素的评价结果的平均值,得到各级产能波动对上述各因素的影响度的评价值s1i、s2i、s3i、s4i、s5i;(2)管理者根据企业实际生产组织情况确定各影响因素的权重ω1、ω2、ω3、ω4、ω5;(3)根据公式(12)计算各级波动初始重要度参数s1i:i级波动的发生对产品调度的影响程度;ω1:产品调度因子的权重;s2i:i级波动的发生对人员调度的影响程度;ω2:人员调度因子的权重;s3i:i级波动的发生对库存管理的影响程度;ω3:库存管理因子的权重;s4i:i级波动的发生对交货期的影响程度;ω4:交货期因子的权重;s5i:i级波动的发生对生产成本的影响程度;ω5:生产成本因子的权重;(4)由于公式(11)中参数ki的数量级通常为10-4,所以利用公式(13)对公式(12)中的各级波动初始重要度参数进行标准化处理得到各级波动重要度参数2)评价生产线产能波动过程对企业订单交货期的影响度IDT:依据步骤2、3中各级产能波动的统计结果计算生产线波动过程对企业订单交货期的影响度IDT,公式为(14):TTRi:i级波动所对应的停产区间的中值,单位:小时;对于五级产能波动,设定TTR5采用与上述θ5相同的取值依据——通过观察该区间内的所有Δt的值,TTR5取最常出现得值。6.应用生产线产能波动过程及其影响度的评价结果制定具体生产组织计划:1)在制定生产调度方案和生产线维护计划时,管理人员应综合考虑各级产能波动发生的间隔时间MTBLi和各级产能波动对企业生产组织工作的影响度IPOi,以明确各级波动可能的发生时刻及其重要程度,从而确定生产组织工作的优先级,进而制定出更加切合生产线实际运行情况且符合企业生产效益的生产组织方案;2)在制定生产计划时,管理人员可以依据产能波动过程对企业对外部交货期的影响度指标IDT,结合公式(15)计算得到订单的最佳交货期DT:DT=Q×T0×IDT(15)DT:订单的最佳交货期,单位:小时;Q:生产线生产的合格品总数,制定生产计划时应代入计划生产的合格品数;T0:生产线处于稳态无故障运行时的平均产出间隔时间,单位:小时;IDT:生产线波动过程对企业订单交货期的影响度。实施例:本发明以某企业的某条已建成但尚未投产的机械加工生产线为例。1.收集生产线的运行数据:本实施例中的生产线尚未投产,故首先建立该生产线的仿真模型,通过运行仿真模型记录生产线上每件产品的下线时刻t,随即利用其计算生产线上每件合格产品的单件产出间隔时间Δt:依据生产线的设计参数,即生产线上工位数,各工位的设备数及设备间的串、并联组织形式,各设备的操作时间、故障率、修复率和可用度,缓存容量设置,物料转移策略,利用PlantSimulation生产仿真软件建立该生产线的仿真模型,设定仿真模型运行时间为3年,记录期间所有合格品的下线时刻t,并利用公式(1)计算单件产出间隔时间Δt,统计结果如表1所示(表1中前3件合格品产出于该生产线的预热阶段,不计入考虑范围):表1单件产出间隔时间统计表合格品编号n下线时刻t(h)单件产出间隔时间Δt(h/件)10.62330.623320.65440.031130.69610.041740.73110.035050.76890.037860.80390.035070.84170.0378………71641526279.88240.031171641626279.92410.041771641726279.95520.031171641826279.99680.04172.划分生产线的产能波动等级:观察该生产线运行数据可知,该生产线处于稳态无故障运行时的平均无故障间隔时间T0=0.036h,且该生产线使用的托盘容量为5,最小缓存区可容纳6个托盘,最大缓存区可容纳12个托盘,即:C=5,Bmin=30,Bmax=60,依据公式(2)(3)(4)(5)(6)(7)将该生产线的产能波动等级划分如下:零级波动:Δt<0.2h;一级波动:0.2h≤Δt<1h;二级波动:1h≤Δt<2h;三级波动:2h≤Δt<4h;四级波动:4h≤Δt<6h;五级波动:Δt≥6h;3.处理生产线运行数据并绘制直方图:统计各级波动的发生频率及其发生的间隔时间,并绘制各级波动发生的间隔时间的概率密度直方图和累积分布直方图;1)利用公式(8)统计各级波动的发生频率:2)统计各级波动发生的间隔时间:利用公式(9)统计各级波动发生的间隔时间TBLi(j),以一级波动为例,统计结果如表2:表2一级波动发生的间隔时间统计表一级波动发生次序j一级波动发生时刻t1(j)(h)一级波动发生的间隔时间TBLi(j)(h)1475.8732159475.87322733.942334258.06913892.253498158.311242294.5737051402.320253993.1075741698.533964540.414799547.307277097.9760672557.5613………2721193.5947342.74392821882.1410688.54632922611.7735729.63253023333.5103721.73683)绘制各级波动发生间隔时间的概率密度直方图和累积分布直方图:(1)将各级波动发生间隔时间的统计结果进行分组统计:利用斯特奇斯公式计算分组数目和组距,统计各组内发生该等级波动的频次和频率,以一级产能波动为例:一级波动发生的间隔时间数为30,所以根据斯特奇斯方法将一级波动发生间隔时间分为6组,组距为470h,统计如表3:表3一级波动发生间隔时间分组统计表间隔时间区间(h)频次频率累积频率0-470130.43330.4333470-94080.26670.7000940-141030.10000.80001410-188040.13330.93331880-235010.03330.96672350-282010.03331(2)根据表3统计结果,参照图2、图3绘制各级波动发生间隔时间的概率密度直方图和累积分布直方图;4.评价生产线的产能波动过程:首先利用步骤3的统计结果拟合各级波动发生间隔时间的概率分布函数fi(t);绘制函数图像,使生产组织者对生产线的各级产能波动发生的间隔时间的分布情况产生直观、定性的认识;再依据fi(t)计算各级产能波动发生的平均间隔时间MTBLi,作为生产线产能波动过程的定量评价指标,使生产组织者定量把握生产线的产能波动过程;1)拟合各级波动发生间隔时间的概率密度函数:(1)识别候选分布,由图2与图3观察发现一级波动发生间隔时间的分布符合weibull分布或指数分布,由于weibull分布的形状参数β=1时即为指数分布,所以认为一级波动发生间隔时间的分布符合weibull分布,对于其他各级波动发生间隔时间的分布函数使用相同方法识别候选分布;(2)采用最小二乘法对weibull分布进行参数估计,并利用相关系数检验法检验参数正确性(显著性水平α=0.05),最终确定各级波动发生间隔时间的概率密度函数fi(t):一级波动发生间隔时间的概率密度函数:二级波动发生间隔时间的概率密度函数:三级波动发生间隔时间的概率密度函数:四级波动发生间隔时间的概率密度函数:五级波动发生间隔时间的概率密度函数:2)绘制各级波动发生间隔时间的概率分布图:参阅图4与图5,绘制各级波动的概率密度分布拟合曲线和累积分布拟合曲线,生产组织者可根据该分布曲线对生产线的各级产能波动出现的时间间隔分布情况产生直观认识;3)由公式(10)计算各级波动发生的平均间隔时间,并将其作为生产线产能波动过程的定量评价指标,计算结果为:MTBL1=879hMTBL2=683hMTBL3=807hMTBL4=2921hMTBL5=3562h5.评价生产线产能波动过程的影响度:1)评价生产线各级产能波动对企业内部生产组织工作的影响度IPOi:(1)将4名生产组织工作者对该生产线各级产能波动对企业产品调度、人员调度、库存管理、交货期和生产成本的影响程度的评价结果的平均值s1i、s2i、s3i、s4i、s5i进行统计,统计结果如表4:表4各级产能波动对各影响因素的影响度评价结果(2)由该企业管理者根据企业实际生产组织情况对上述5个影响因素的权重进行分配,分配结果为:ω1=0.2;ω2=0.1;ω3=0.2;ω4=0.2;ω5=0.3;(3)根据公式(12)与(13)计算各级产能波动的重要度参数结果如表5所示:表5各级产能波动的重要程度参数计算结果(4)综合考虑生产线各级产能波动的波动程度、重要程度和发生频率对生产组织工作产生的影响,利用公式(11)评价各级波动对企业内部生产组织工作的影响度IPOi,评价结果如表6:表6产能波动性对企业内部生产组织工作的影响度的评价结果由于五级波动的单件产出间隔时间划分区间为Δt≥6h,通过观察该区间内的所有Δt的值,θ5取Δt最常出现的值8。2)评价生产线产能波动性对该企业订单交货期的影响度IDT:由表1观察可知该生产线稳态运行时的平均产出间隔时间为T0=0.036h,根据步骤2划分的产能波动等级区间和步骤3统计出的各级波动的频率ki,利用公式(14)评价该生产线产能波动性对该企业对外部交货期的影响度IDT:由于五级波动的单件产出间隔时间划分区间为Δt≥6h,TTR5采用与上述θ5相同的取值依据——通过观察该区间内的所有Δt的值,8最常出现,故取TTR5=8h。6.应用生产线产能波动过程及其影响度的评价结果的制定具体生产组织计划:1)由MTBLi评价结果可知,该生产线自正式投产起,平均约每880h发生一次一级波动,每680h发生一次二级波动,每800h发生一次三级波动,以此类推;此外,由各级波动对企业生产组织工作的影响度指标IPOi可知,该生产线发生三级波动对该企业生产组织工作造成的影响程度最大,其次是五级波动,然后是二级波动,一级波动造成的影响程度很小;因此,生产组织人员应着重关注平均每800h出现一次的三级波动,以及平均每3600h出现一次的五级波动和平均每680h出现一次的二级波动,并力求在其发生前制定生产调度方案和生产线维护计划,以免该等级的产能波动出现时出现生产人员、产品及设备调度不当的情况,同时提前制定应对措施还可减少产能波动对企业生产效益造成的损失;2)假设该生产线接到订单,并计划生产合格品5000件,则在制定生产计划时,管理人员可依据该生产线产能波动过程对外部交货期的影响度评价指标IDT,结合公式(15)计算得到订单交货期DT(假设该生产线每天运行24h):DT=Q×T0×IDT≈190h而该生产线理想交货期DT′为:DT′=Q×T0=180h对比DT与DT′,显然考虑了生产线产能的波动性所得到的结果DT更符合生产线实际生产能力,因此本方法计算得到的DT对交货期的制定更具参考价值,应将其设置为该订单的最佳交货期。当前第1页1 2 3