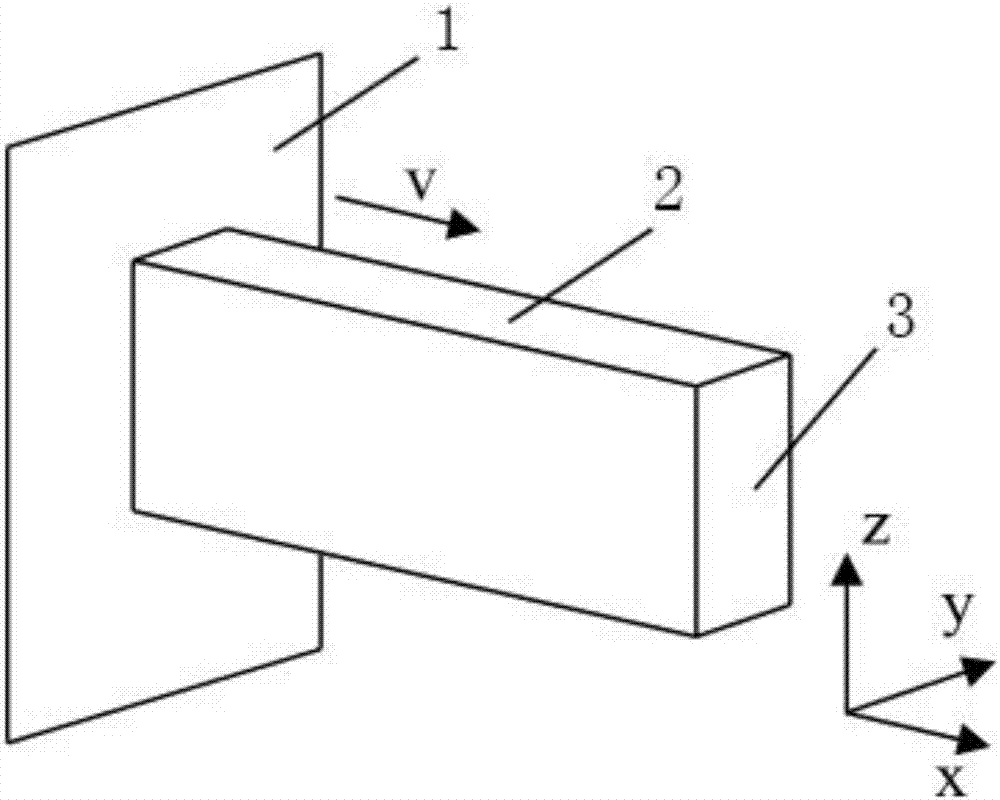
本发明涉及一种属于汽车被动安全领域的建立方法,更确切地说,本发明涉及一种汽车碰撞简化参数化有限元模型的建立方法。
背景技术:
:汽车被动安全性是指汽车在发生交通事故时,车辆能够有效地保护车内乘员或车外行人免受伤害或尽量降低伤害程度的性能。为了提高汽车的被动安全性,必须合理设计车体结构使其在发生碰撞时能产生合理的变形并充分吸收碰撞能量。在车体结构的设计及优化过程中,目前广泛采用实车试验与有限元仿真分析相结合的方法。有限元仿真分析通过计算机进行虚拟碰撞试验,得到车体的变形过程及碰撞响应,进而进行车体结构设计及改进。由于有限元法可以减少实车试验次数,提高开发效率并大大节省开发成本,因而应用广泛。传统的汽车整车碰撞有限元模型中车体零部件主要用壳单元和体单元模拟,模型中单元数量庞大,即便使用高性能计算机,每次计算通常也需要几个小时。当设计方案较多或结构改进时往往需要对有限元模型进行反复修改的设计与验证,同时这需要耗费大量的模型修改及计算时间,使得整个开发过程耗时耗力。为了减小模型规模,缩短方案求解时间,简化的有限元模型得到了广泛应用,主要思想均是采用其他形式的单元代替整车详细有限元模型,考虑到简化模型的精度要求,目前,存在的简化模型中的单元形式主要为壳单元与梁单元所组成的混合单元,虽然该类型的简化模型能在一定程度上减少虚拟试验求解时间,但是由于壳单元的存在,还是达不到理想的求解速度。因此,需要一种新型的简化参数化有限元模型,该模型在满足计算精度的前提下,采用梁单元作为唯一的替代单元,对整车详细有限元模型进行简化,该新型简化模型与整车详细有限元模型及梁、壳混合单元组成的简化模型相比其可以缩短求解时间,并且该新型的简化有限元模型通过对结构特性的参数化,实现只需对简化模型中若干参数的调整即可达到对结构方案的改进设计,从而省去了传统结构改进的结构三维模型建立、网格划分、材料及厚度定义等一系列步骤,进而可以在结构初期设计阶段的性能优化和验证,指导后续的结构详细设计。技术实现要素:本发明所要解决的技术问题是克服了现有技术存在汽车车体结构抗撞性设计及改进时,采用传统的详细有限元模型消耗大量修改和计算时间的问题,提供了一种汽车碰撞简化参数化有限元模型的建立方法。为解决上述技术问题,本发明是采用如下技术方案实现的:所述的汽车碰撞简化参数化有限元模型的建立方法的步骤如下:1)建立车体拓扑结构;2)提取部件截面参数;3)提取部件刚度特性并参数化;4)模拟部件碰撞特性;5)验证简化参数化有限元模型。技术方案中所述的建立车体拓扑结构是指:1)获取汽车的详细有限元模型:在汽车的设计阶段工程师会建立汽车的详细有限元模型,本步骤要找到汽车设计阶段所建立的详细有限元模型;为建立汽车碰撞简化参数化有限元模型做准备;2)建立车体的一维梁单元拓扑模型:利用详细有限元模型中各个二维壳单元和三维体单元部件的几何位置,利用hypermesh软件依次提取出每个部件两个端面的几何中心点,并将这两个中心点作为一维梁单元的始末节点,建立出车体的一维梁单元拓扑模型;3)建立车体拓扑结构模型。技术方案中所述的提取部件截面参数是指:1)依据截面面积相等的原则将安全部件的截面等效成矩形,依次计算出截面的长、宽和厚度;2)ls-dyna中的*section_beam关键字常用来模拟一维梁单元的截面特性,在*section_beam中依次填入每一个安全部件的截面尺寸及梁单元三个方向的惯性矩,用来模拟安全部件的截面属性。技术方案中所述的提取部件刚度特性并参数化是指:1)提取压溃刚度特性并参数化:(1)加载工况为刚性壁障(1)以1m/s的恒定速度沿x方向冲击后端面固定的部件(2),使部件2完全压溃;(2)利用hypermesh软件建立压溃部件有限元仿真模型,利用ls-dyna软件计算获得压溃力-压溃量曲线;(3)根据吸能量相等原则将压溃力-压溃量曲线简化并参数化,参数化后的曲线可以用fx、fp、fm、dm、de和dx六个参数表示,其中:fx.极限压溃力,单位.kn;fp.压溃力峰值,单位.kn;fm.平均压溃力,单位.kn;dm.峰值力所对应的压溃量,单位.mm;de.有效压溃量,单位.mm;dx.极限压溃量,单位.mm。2)提取弯曲刚度特性并参数化:(1)加载工况为约束部件一个端面上所有节点的自由度,在另一个端面的几何中心处建立节点刚体并与该端面的上的所有节点刚性连接,给节点刚体施加0.157rad/ms的转动角速度,使部件产生绕y轴的弯曲变形;(2)利用hypermesh软件建立弯曲部件有限元仿真模型,利用ls-dyna软件计算获得弯曲力矩-转角曲线;(3)根据吸能量相等原则将弯曲力矩-转角曲线简化并参数化,参数化后的曲线可以用mx、mp、mm、θm、θe和θx六个参数表示,其中:mx.极限弯曲力矩,单位.n·m;mp.弯曲力矩的峰值,单位.n·m;mm.平均弯曲力矩,单位.n·m;θm.峰值力矩所对应的转角,单位.rad;θe.有效弯曲角度,单位.rad;θx.极限弯曲角度,单位.rad。技术方案中所述的模拟部件碰撞特性是指:(1)整个模拟过程用ls-dyna完成,对于每个代替压溃部件和弯曲部件的简化梁单元,其材料用ls-dyna中相应的*mat_force_limited材料来模拟,选择好材料后进入编辑界面依次输入材料密度、弹性模量及泊松比;(2)最后将利用提取部件刚度特性并参数化步骤中的第(1)步骤获得的压溃部件简化参数化的压溃力-压溃量曲线以及利用提取部件刚度特性并参数化中的第(2)步骤获得的弯曲部件简化参数化的弯曲力矩-转角曲线赋予该材料,变形部件模拟完成;(3)汽车发生碰撞过程中有些部件是不发生变形的,对于代替非变形部件的梁单元,用ls-dyna中的*mat_elastic材料来模拟,依次输入材料密度、弹性模量、泊松比及屈服极限,非变形的部件模拟完成。技术方案中所述的验证简化参数化有限元模型。(1)利用ls-dyna对汽车碰撞简化参数化有限元模型进行碰撞仿真后将得到四条曲线,分别为吸能量曲线、加速度曲线、速度曲线以及位移曲线;(2)通过对比汽车碰撞简化参数化有限元模型与整车详细有限元模型相应曲线的差异即能验证新建立的汽车碰撞简化参数化有限元模型是否合格。与现有技术相比本发明的有益效果是:1.本发明所述的汽车碰撞简化参数化有限元模型的建立方法可以准确模拟出汽车碰撞的关键响应(吸能量、加速度、速度、位移)以及关键部件(吸能盒、前纵梁等)的变形过程。2.本发明所述的汽车碰撞简化参数化有限元模型的建立方法中的汽车碰撞简化参数化有限元模型计算快速且修改方便,与详细有限元模型相比,大大节约了结构设计及改进所耗费的时间,提高了开发效率,适合在车体结构抗撞性设计阶段进行大规模快速设计及优化。3.本发明所述的汽车碰撞简化参数化有限元模型的建立方法应用到汽车抗撞性结构设计初期使子结构的刚度特性修改方便快捷,省去了建立详细壳单元模型的繁琐,利用汽车碰撞简化参数化有限元模型快速获得碰撞波形,验证由目标分解得到的子结构性能目标的合理性和正确性附图说明下面结合附图对本发明作进一步的说明:图1为本发明所述的汽车碰撞简化参数化有限元模型的建立方法的流程框图;图2为本发明所述的汽车碰撞简化参数化有限元模型的建立方法中提取压溃刚度特性的加载示意图;图3为本发明所述的汽车碰撞简化参数化有限元模型的建立方法中简化并参数化的压溃力-压溃量曲线示意图;图4为本发明所述的汽车碰撞简化参数化有限元模型的建立方法中提取弯曲刚度特性的加载示意图;图5为本发明所述的汽车碰撞简化参数化有限元模型的建立方法中简化并参数化的弯曲力矩-转角曲线示意图;图6为本发明所述的汽车碰撞简化参数化有限元模型的建立方法的实施例中m6型乘用车详细有限元模型结构图;图7为本发明所述的汽车碰撞简化参数化有限元模型的建立方法的实施例中建立的m6型乘用车正面碰撞简化梁单元模型拓扑结构图;图8为本发明所述的汽车碰撞简化参数化有限元模型的建立方法的实施例中m6型乘用车前端前纵梁详细有限元模型结构图;图9为本发明所述的汽车碰撞简化参数化有限元模型的建立方法的实施例中详细有限元模型与简化梁单元模型吸能量曲线对比;图10为本发明所述的汽车碰撞简化参数化有限元模型的建立方法的实施例中详细有限元模型与简化梁单元模型加速度曲线对比;图11为本发明所述的汽车碰撞简化参数化有限元模型的建立方法的实施例中详细有限元模型与简化梁单元模型速度曲线对比;图12为本发明所述的汽车碰撞简化参数化有限元模型的建立方法实施例中详细有限元模型与简化梁单元模型位移曲线对比。图中:1.刚性壁障,2.车体部件,3.部件后端,4.前纵梁第一段,5.前纵梁第二段。具体实施方式下面结合附图对本发明作详细的描述:本发明的整个建模过程将用到hypermesh软件,hypermesh软件是美国altair公司的产品,是世界领先的、功能强大的cae应用软件包,也是一个创新、开放的企业级cae平台,它集成了设计与分析所需的各种工具,具有无与伦比的性能以及高度的开放性、灵活性和友好的用户界面。本发明在模型的仿真计算过程中将用到ls-dyna软件,ls-dyna程序是功能齐全的几何非线性、材料非线性和接触非线性程序。它以lagrange算法为主,兼有ale和euler算法;以显式求解为主,兼有隐式求解功能;以结构分析为主,兼有热分析、流体-结构耦合功能;以非线性动力分析为主,兼有静力分析功能(如动力分析前的预应力计算和薄板冲压成型后的回弹计算)是军用和民用相结合的通用结构分析非线性有限元程序。参阅图1,本发明所述的汽车碰撞简化参数化有限元模型的建立方法的步骤如下:1.建立车体拓扑结构本发明所述的车体拓扑结构,即车身中主要骨架件的空间位置,对应到汽车碰撞简化参数化有限元模型,即为模型中一维梁单元始末节点的空间位置。本发明提及的一维梁单元、二维壳单元、三维体单元等等都是hypermesh软件中模型的单元类型。1)获取汽车的详细有限元模型:在汽车的设计阶段工程师会建立汽车的详细有限元模型,本发明将以汽车设计阶段所建立的详细有限元模型为依据来建立汽车碰撞简化参数化有限元模型;2)建立车体的一维梁单元拓扑模型:利用详细有限元模型中各个二维壳单元和三维体单元部件的几何位置,利用hypermesh软件依次提取出每个部件两个端面的几何中心点,并将这两个中心点作为一维梁单元的始末节点,建立出车体的一维梁单元拓扑模型;2.提取部件截面参数本发明所述的部件截面参数包括一维梁单元的截面形状和惯性矩。汽车车身中典型安全部件的截面常为矩形、单帽形、双帽形,在车体结构设计初期,为了计算和修改方便,通常将截面都等效为矩形,在后期详细设计时考虑加工工艺、连接的需要,再将截面形状进一步细化为单帽形、双帽形等。本发明依据截面面积相等的原则将安全部件的截面等效成矩形,依次计算出截面的长、宽和厚度。ls-dyna中的*section_beam关键字常用来模拟一维梁单元的截面特性,本发明在*section_beam中依次填入每一个安全部件的截面尺寸及梁单元三个方向的惯性矩,用来模拟安全部件的截面属性。3.提取部件刚度特性并参数化车体发生碰撞变形时有些部件的变形为压溃,称之为压溃部件;有些部件的变形为弯曲,称之为弯曲部件。所以模型要与车体碰撞特性保持一致就必须提取其压溃刚度特性和弯曲刚独度特性。压溃刚度特性和弯曲刚度特性分别用压溃力-压溃量曲线和弯曲力矩-转角曲线表征。刚度特性是利用详细有限元模型进行仿真计算获得的,具体方法如下:1)提取压溃刚度特性并参数化:对于发生压溃变形的部件,其刚度特性为压溃力-压溃量曲线,本发明将利用有限元仿真软件hypermesh以及ls-dyna在一定的加载工况下进行仿真计算提取出部件的压溃刚度特性。参阅图2,图2为提取压溃部件的压溃刚度特性的加载示意图,加载工况为刚性壁障1以1m/s的恒定速度沿x方向冲击后端面固定的部件2,使部件2完全压溃。利用hypermesh软件建立压溃部件有限元仿真模型,利用ls-dyna软件计算获得压溃力-压溃量曲线。参阅图3,图3为简化并参数化的压溃力-压溃量曲线示意图,根据吸能量相等原则将压溃力-压溃量曲线简化并参数化,参数化后的曲线可以用fx、fp、fm、dm、de和dx六个参数表示。各参数的具体含义如表1所示:表1压溃力-压溃量曲线中各参数含义符号含义单位fx极限压溃力knfp压溃力峰值knfm平均压溃力kndm峰值力所对应的压溃量mmde有效压溃量mmdx极限压溃量mm2)提取弯曲刚度特性并参数化:对于发生弯曲变形的部件,其刚度特性为弯曲力矩-转角曲线,本发明将利用有限元仿真软件hypermesh以及ls-dyna在一定的加载工况下进行仿真计算提取出部件的弯曲刚度特性。参阅图4,图4为弯曲部件有限元仿真加载示意图,加载工况为约束部件一个端面上所有节点的自由度,在另一个端面的几何中心处建立节点刚体并与该端面的上的所有节点刚性连接,给节点刚体施加0.157rad/ms的转动角速度,使部件产生绕y轴的弯曲变形。利用hypermesh软件建立弯曲部件有限元仿真模型,利用ls-dyna软件计算获得弯曲力矩-转角曲线。参阅图5,图5为简化并参数化的弯曲力矩-转角曲线示意图,根据吸能量相等原则将弯曲力矩-转角曲线简化并参数化,参数化后的曲线可以用mx、mp、mm、θm、θe和θx六个参数表示。各参数的具体含义如表2所示:表2弯曲力矩-转角曲线中各参数含义4.拟模部件碰撞特性(1)模拟部件碰撞特性解释:本发明所述的模拟部件碰撞特性即是将前面得到的刚度特性曲线以及相应的材料属性赋予简化参数化模型中的梁单元。(2)模拟部件碰撞特性方法:整个模拟过程用ls-dyna完成,对于每个代替压溃部件和弯曲部件的简化梁单元,其材料用ls-dyna中相应的*mat_force_limited材料来模拟,选择好材料后进入编辑界面依次输入材料密度、弹性模量及泊松比,最后将利用步骤3中的第(1)获得的压溃部件简化参数化的压溃力-压溃量曲线以及利用步骤3中的第(2)获得的弯曲部件简化参数化的弯曲力矩-转角曲线赋予该材料,变形部件模拟完成。汽车发生碰撞过程中有些部件是不发生变形的,对于代替非变形部件的梁单元,用ls-dyna中的*mat_elastic材料来模拟,依次输入材料密度、弹性模量、泊松比及屈服极限,非变形的部件模拟完成。5.验证简化参数化有限元模型(1)验证目的:经过前面四个步骤,汽车碰撞简化参数化有限元模型建立完成,具体的模型形状如图7所示。这一步将利用ls-dyna软件对模型进行碰撞仿真,目的是检验新建立的汽车碰撞简化参数化有限元模型能否很好的模拟已有的整车详细有限元模型的碰撞特性。(2)验证方法:利用ls-dyna对汽车碰撞简化参数化有限元模型进行碰撞仿真后将得到四条曲线,分别为吸能量曲线、加速度曲线、速度曲线以及位移曲线,通过对比汽车碰撞简化参数化有限元模型与整车详细有限元模型相应曲线的差异即能验证新建立的汽车碰撞简化参数化有限元模型是否合格。实施例本发明接下来结合实施例介绍本发明所述的汽车碰撞简化参数化有限元模型的建立方法。实施例中选取m6型乘用车的详细有限元模型为基础,建立其正面碰撞的简化参数化有限元模型,m6型乘用车的详细有限元模型如图6所示。1.建立车体拓扑结构以及提取部件截面参数(1)建模分析:对于乘用车正面碰撞时变形主要集中在整车前部,而中后部基本没有发生变形。因此本实施例所建立的简化梁单元模型主要建模对象将从前端结构中选取。车身构件在冲击载荷作用下,主要产生轴向压溃及局部弯曲两种变形方式。(2)建立车体拓扑结构以及模拟部件惯性特征过程:利用hypermesh软件中的梁单元来构建车体拓扑,梁单元在hypermesh中的形状为一条线段,每个梁单元都相当于车体的一部分子结构。汽车正面碰撞过程中前纵梁起主要的吸能和传力作用,本发明以前纵梁为例,新建一个梁单元来模拟车体详细有限元模型前纵梁子结构,将车体前纵梁截面等效成矩形,确定好前纵梁截面矩形的长宽数值后赋给*section_beam关键字。如此反复为车体的各个子结构建立新的梁单元来模拟,建立的汽车正面碰撞简化梁单元模型拓扑结构如图7所示,可以看到拓扑结构反映了整车骨架件的布置情况。2.提取部件刚度特性并参数化1)提取压溃刚度特性并参数化:本实施例采用有限元法提取子结构刚度特性,有限元模型的加载工况如图2所示。以车体前端前纵梁第一段为例,前纵梁第一段形状如图8中4号部件所示,利用hypermesh软件建立前纵梁第一段有限元仿真模型,利用ls-dyna软件计算获得压溃力-压溃量曲线。刚性壁障以1m/s的恒定速度撞击后端约束的前纵梁第一段,使前纵梁第一段能够完全压溃,提取出前纵梁第一段与壁障之间的碰撞力以及前纵梁第一段自身的压溃量。参阅图3,图3为简化并参数化的压溃力-压溃量曲线示意图,根据吸能量相等原则将压溃力-压溃量曲线简化并参数化。车体结构其他压溃部件刚度特性的提取方法同上,最终得到车体前端主要安全结构的压溃刚度特性如表3所示。表3车体前端部分子结构的刚度特性2)提取弯曲刚度特性并参数化:汽车正面碰撞过程中前纵梁第二段后端由于受到发动机的阻挡作用产生弯曲变形,是正面碰撞中的主要弯曲部件,前纵梁第二段形状如图8中5号部件所示,本发明以前纵梁第二段为例,利用hypermesh软件建立前纵梁第二段的有限元仿真模型,约束前纵梁第二段一端所有节点的自由度,在另一个端面的几何中心处建立节点刚体并与该端面的上的所有节点刚性连接,给节点刚体施加0.157rad/ms的转动角速度,使前纵梁产生绕y轴的弯曲变形。利用ls-dyna软件计算获得弯曲力矩-转角曲线。参阅图5简化并参数化的弯曲力矩-转角曲线示意图,根据吸能量相等原则将弯曲力矩-转角曲线简化并参数化,得到前纵梁第二段的弯曲刚度特性,如表4所示。表4提取弯曲刚度特性的曲线结果3.模拟部件碰撞特性碰撞特性模拟分为三类部件分别为压溃部件、弯曲部件、非吸能部件。(1)压溃部件模拟:对于主要吸能部件,压溃子结构本实施例采用ls-dyna中带有非线性轴向压溃特性的梁单元模拟,材料类型为*mat_force_limited(*mat29),并将2步骤中的第(1)中得到的压溃部件简化参数化的压溃力-压溃量曲线赋予该材料。(2)弯曲部件模拟:对于弯曲变形中产生的塑性铰本实施例采用非线性弹簧单元模拟,材料类型为*mat_nonlinear_plastic_discrete_beam(*mat68),并将步骤2步骤中的第(2)获得的弯曲部件简化参数化的弯曲力矩-转角曲线赋予该材料。(3)非吸能部件模拟:对于非主要吸能部件,只要模拟出其惯性特性即可,本实施例采用简单梁单元模拟,材料类型为*mat_elastic(*mat1),保证质量与详细模型一致。4.验证简化参数化有限元模型汽车正面碰撞简化参数化有限元模型已经建立完成,模型的外形参考图7。将建立的汽车正面碰撞简化参数化有限元模型利用ls-dyna软件进行碰撞仿真计算,得到模型的吸能量曲线、加速度曲线、速度曲线以及位移曲线,将这四条曲线与详细有限元模型仿真计算得到的四条曲线进行对比来验证简化参数化有限元模型,参阅图9至图12。从图中可以看出,简化梁单元模型和详细有限元模型的最终吸能量分别为130j、128kj,误差很小,对于概念分析模型,这种可误差是可以接受的。简化梁单元模型与详细有限元模型的碰撞加速度、速度和位移随时间的变化趋势一致性很高,但也存在一定的偏差。主要是由于梁单元模型除变形大、吸能量多的主要吸能部件外其余部件均被简化为弹性材料,不发生塑性变形,整体刚度大,碰撞时间短,回弹快,碰撞波形峰值大。通过上述分析表明,简化梁单元模型能够反映整车的碰撞过程,碰撞响应以及关键结构的变形。此外,简化梁单元模型计算100ms所用的cpu时间仅为2min,便于在结构设计初期进行快速计算获得碰撞波形,用来验证子结构的性能分解是否合理,以快速实现能量管理和载荷路径分解。当前第1页12