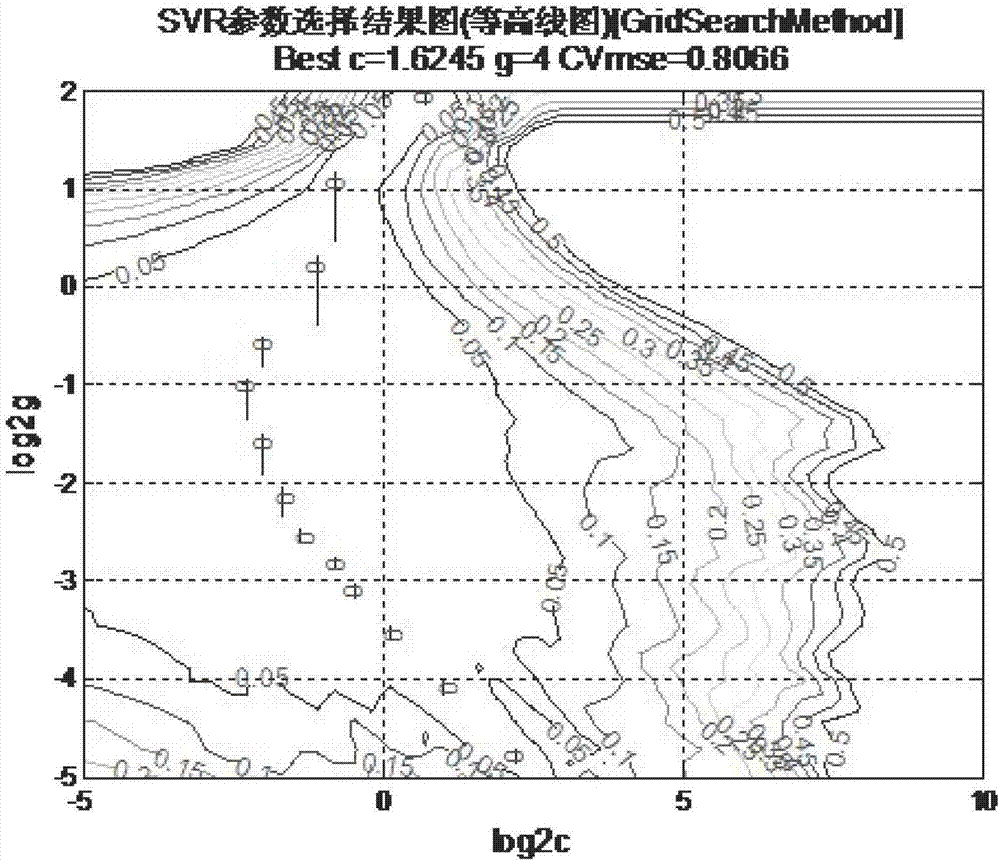
本发明属于sgcc板料复杂弯曲成形工艺领域,尤其涉及一种基于k折交叉验证法的支持向量机近似模型优化方法。
背景技术:
:随着汽车在生活、生产领域的迅速普及与更新,车窗升降板作为调节汽车窗口的重要活动零件,其装配性能和使用性能的好坏直接决定了车窗活动的平稳性和顺滑度,同时也在很大程度上影响人们的体验感受。由于车窗升降板的结构相对于其他大型覆盖件和结构件而言,具有形状复杂、曲率变化大、零件装配尺寸要求高的特点,导致在实际生产过程中为了获得质量上佳的零件,需要尽可能地减小零件回弹,避免造成零件尺寸精度的下降。现阶段,在对冲压件进行回弹分析时,有较为成熟的解析求解法,但是只有在分析形状相对简单、容易成形的零件才有用,比如常见的u型件和v型件等。一旦涉及到形状复杂、特征较多的异形件时,解析求解法则无用武之地。同时有研究发现,在试验条件下的回弹量理论计算值均偏大,且平均相对误差高达88%,所以仅仅依靠理论公式的解析计算来预测零件回弹量是远远不可行的,甚至会给出错误的预测结果,误导实际应用。技术实现要素:本发明要解决的技术问题是:提供一种基于k折交叉验证法的支持向量机近似模型优化方法,能够避免出现像传统交叉验证法出现的存在费时、效率低的缺点,提高支持向量机的学习能力及收敛速度,增加了对支持向量机模型参数选择的准确性和可靠性,以解决上述现有技术中存在的问题。本发明采取的技术方案为:一种基于k折交叉验证法的支持向量机近似模型优化方法,该方法包括以下步骤:(1)确定支持向量机的核函数类型:选择径向基函数作为支持向量机模型的核函数;(2)确定径向基函数的惩罚因子c和核参数σ:取惩罚参数的变化范围为c∈[2-5,210],核参数的取值范围为σ∈[2-5,22];(3)确定优化目标和优化变量:将零件成形后发生回弹的最大位移量作为优化目标,记为yi=(blankmovement)i,根据使用要求,在不发生破裂等不可修复性缺陷的前提下,最大位移量需小于ymin=0.5mm;优化变量为板料厚度a、冲压速度b和摩擦因数c;(4)确定样本获取的方法:采用拉丁超立方抽样方法获取100组优化变量试验数据,并通过dynaform平台分别进行车窗升降板的冲压成形有限元数值模拟和结果分析;(5)确定k折交叉验证法的k值:取k=5,即将上述试验数据分成5组,其中1组作为验证集,其余4组作为测试集,并取验证集的均方差作为评判该模型的误差;(6)数据归一化处理:采用z-score标准化法对数据进行归一化处理,将不同量纲、数量级的优化变量均归于[-1,1]区间内;(7)建立优化模型:将c和σ的选择区间用幂函数表达,区间端点为幂函数的指数,采用k折交叉验证算法进行支持向量机回归模型的参数寻优,构建支持向量机近似模型。优选的,上述步骤(3)的优化变量在初始成形工艺参数的基础上对每个参数的初始值以80%和120%的比例计算最大值和最小值,从而确定优化区间。优选的,上述步骤(7)中模型迭代寻优后获得的最优成形工艺参数是c=1.6245,σ=4,均方差mse=0.8066,平均误差0.0538。本发明的有益效果:与现有技术相比,本发明效果如下:(1)本发明通过k折交叉验证方法构建支持向量机近视模型,能够避免出现像传统交叉验证法出现的存在费时、效率低的缺点,提高支持向量机的学习能力及收敛速度,增加了对支持向量机模型参数选择的准确性和可靠性;(2)本发明采用拉丁超立方抽样方法针对100组成形工艺参数和对应质量指标的初始样本数据中后20组测试集模拟数据和预测数据值进行折线图对比和误差分析,经过数值模拟与分析验证后得出优化结果的3d视图和等高线视图,将前80能够较大程度上降低零件回弹量(零件回弹的最大位移量)和svm预测集的回弹值对比,验证该参数下支持向量机的回归预测精度。将测试集的回弹值(最大位移量)与预测集的回弹值进行对比,计算两者之间的误差和平均误差来定量描述通过k折交叉验证法优化支持向量机核参数模型的优劣情况;(3)本发明通过数据挖掘手段对涉及到的数据进行归一化处理,消除各个数据指标之间的单位和量纲差异,以避免直接将成形参数和数值模拟的回弹结果输入至matlab的编辑界面内,由于系统的数据精度造成较小数值的参数湮灭,比如板料厚度、摩擦因素和最大位移量,无法进行后续的数学建模工作,将总共100组的成形工艺参数和对应质量指标的初始样本数据通过数据归一化处理,方可进行下面的数学建模、模型优化和工艺参数优化等工作,从而对零件的质量进行综合性的对比和评价;(4)通过z-score标准化方法将成形工艺参数和优化目标数据进行归一化,使样本数据归一后满足正态分布,实现的是样本坐标分布。附图说明图1为k折交叉验证法优化svm参数c和σ的3d结果图;图2为k折交叉验证法优化svm参数c和σ的等高线结果图;图3为训练集回弹最大位移量(cv-svm);图4为测试集回弹最大位移量(cv-svm)。具体实施方式下面结合附图及具体的实施例对本发明进行进一步介绍。实施例:如图1-图4所示,一种基于k折交叉验证法优化支持向量机近似模型参数方法,该方法包括以下步骤:(1)针对svm对非线性回归问题的应用确定核函数与核参数取值范围。由于使用支持向量机进行非线性回归分析时,需要将作为样本的试验数据投射到具有高维特征的空间,此过程需要通过核函数(kernelfunction)才能实现。针对特定的问题,选择与其相匹配的核函数是决定支持向量机回归精度的重要因素。选取径向基函数作为核函数时,影响近似模型复杂程度的参数种类相对于其他核函数而言要少很多,而且径向基函数在样本数据在不同维度的的映射处理有着显著优势。所以本发明把径向基函数作为支持向量机对工艺优化进行非线性回归分析预测的核函数。为了有效控制支持向量机的学习能力和泛化能力,进行交叉验证时,取惩罚参数的变化范围为c∈[2-5,210],核参数的取值范围为σ∈[2-5,22],k折取为5;(2)建立数学模型,确定优化目标与约束条件:由于本研究的分析对象为异形弯曲件车窗升降板,为了确保零件在后期进行装配的整体精度,把零件成形后发生回弹的最大位移量(blankmovement)作为优化目标,记为yi=(blankmovement)i,根据使用要求,在不发生破裂等不可修复性缺陷的前提下,最大位移量小于ymin=0.7mm即可满足装配使用条件。零件成形前后的最大位移量可在回弹后处理界面下直接显示。本发明未选择零件不同截面弯曲角变化量(△θ)作为优化目标是因为该零件在装配过程主要考虑整体尺寸,细节尺寸对装配精度的影响程度不大;miny=f(a,b,c)=yi为了选取最佳的成形工艺参数,需要在初始成形工艺参数的基础上选择参数取值的变化区间,本发明采取的区间确定方法是在对每个参数的初始值以80%和120%的比例计算最大值和最小值,结果如表1所示。表1成形工艺参数的取值区间优化变量下限平均值上限材料厚度a/mm0.81.01.2冲压速度b/mm·s-1400050006000摩擦因数c0.1000.1250.150根据约束区间设置目标函数的束条件。(3)编写拉丁超立方抽样所需的程序,通计算机的操作抽取100组试验数据作为成形工艺方案,并分别在dynaform平台进行数值模拟,获取了对应参数下的回弹数据。将样本数据中的1~80组作为构建支持向量机非线性回归近似模型的训练样本,其余20组为测试样本用来检验该近似模型的精确度。lhsdesign函数的抽样计算模型如下:n=100;p=1;xa=0.8+(1.2-0.8)*lhsdesign(n,p);xb=4000+(6000-4000)*lhsdesign(n,p);xc=0.100+(0.150-0.100)*lhsdesign(n,p);x=[xaxbxc]式中,n——需要获得的样本个数;p——表示变量数;xa——材料厚度(程序运行时用字母a代替);xb——冲压速度(程序运行时用字母b代替);xc——摩擦因数(程序运行时用字母c代替);x——参数组合。针对零件成形过程,将拉丁超立方抽样方法获得的100组成形工艺参数在dynaform平台下进行冲压分析数值模拟,获取板料移动位移(blankmovement)作为回弹量分配训练集和测试集,如表2所示。表2100例车窗升降板弯曲成形的工艺参数及回弹量统计表(3)为避免成形工艺参数单位不一致和量纲差距过大容易引起“大数据吞食小数据”的数据湮灭现象的产生,通过z-score标准化方法对以上100组数据样本进行归一化处理,将上述通过拉丁超立方抽样方法获取的100组关于车窗升降板冲压成形工艺参数及回弹量进行z-score标准化处理,得到的部分数据如表3所示。表3100组经z-score标准化处理得到的部分试验数据(4)通过k折交叉验证法优化支持向量机非线性回归近似模型参数,在matlab软件中编写k折交叉验证的运行程序,为了区别系统代码和程序代码,将程序中的所有c和σ分别用c和g替代(下同),同时将c和σ的选择区间用幂函数表达,区间端点为幂函数的指数,进行支持向量机回归模型的参数寻优。通过k折交叉验证法优化svm参数,寻优结束后,最终得到的优化结果为:bestc=1.6245,bestg=4,均方差mse=0.8066,优化结果的3d视图和等高线视图分别见图1-图2所示。80组训练集的回弹值(零件回弹的最大位移量)和svm预测集的回弹值对比情况如图3所示,从图中可知,除了第23组的数值偏差明显较大,其余组的拟合程度较好。为了验证该参数下支持向量机的回归预测精度,通过20组的测试集对进行检测,数值模拟的回弹值和svm预测集的回弹值对比情况如图4所示。将测试集的回弹值(最大位移量)与预测集的回弹值进行对比,如表4所示,计算两者之间的误差和平均误差来定量描述通过k折交叉验证法优化支持向量机核参数模型的优劣情况。表4cv-svm测试集回弹值与预测集回弹值的误差对比分析通过对20组测试集模拟数据和预测数据进行折线图对比和误差分析,明确了k折交叉验证法优化支持向量机核参数后的模型虽然在预测集上的表现上佳,但对于测试集的预测精度有所欠缺,除了81~87、90、95和100号数据的拟合精度较高,其他编号的数据误差较大,但平均误差仅为0.0538,在一定程度上还是实现了对车窗升降板成形后回弹量的预测。结果分析(1)针对svm对非线性回归问题的应用,采用径向基函数作为核函数,惩罚因子取值范围为c∈[2-5,210」,核参数取值范围为σ∈[2-5,22」;(2)在matlab平台下编写拉丁超立方抽样所需的程序,通计算机的操作抽取100组试验数据作为成形工艺方案,并分别在dynaform平台进行数值模拟,获取了对应参数下的回弹数据。将样本数据中的1~80组作为构建支持向量机非线性回归近似模型的训练样本,其余20组为测试样本用来检验该近似模型的精确度;(3)为避免成形工艺参数单位不一致和量纲差距过大容易引起“大数据吞食小数据”的数据湮灭现象的产生,通过z-score标准化方法对以上100组数据样本进行归一化处理,分布区间为[-1,1];(4)采用k折交叉验证法确定支持向量机的惩罚因子c和核参数σ时,取k=5;(5)利用matlab平台下运行优化程序后的结果表示为:bestc=1.6245,bestg=4,均方差mse=0.8066,平均误差0.0538,构建了cv-svm支持向量机非线性回归预测模型。以上所述,仅为本发明的具体实施方式,但本发明的保护范围并不局限于此,任何熟悉本
技术领域:
的技术人员在本发明揭露的技术范围内,可轻易想到变化或替换,都应涵盖在本发明的保护范围之内,因此,本发明的保护范围应以所述权利要求的保护范围为准。当前第1页12