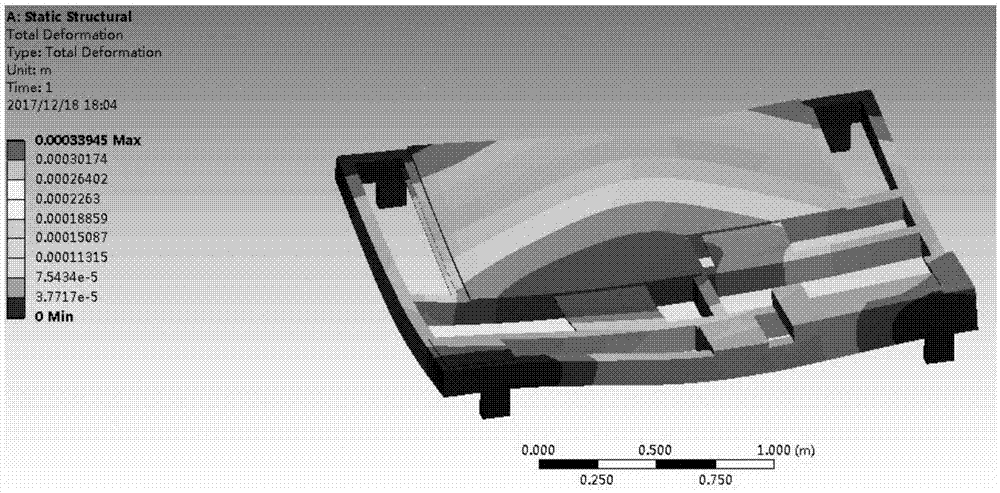
本发明涉及聚氨酯浇注机
技术领域:
,具体涉及一种浇注机底座轻量化设计方法。
背景技术:
随着我国聚氨酯工业的发展,聚氨酯弹性体浇注机也随之兴起。据不完全统计,目前国内国产设备市场占有率百分之九十以上,基本替代了进口设备,完全能满足快速发展的国内市场需求。而降低浇注机生产成本势在必行。浇注机轻量化技术是在确保机身刚度和浇注精度的前提下,减轻机身重量,降低浇注机加工成本及操作困难度。而底座作为二组份浇注机主要承载部件,更是浇注机轻量化设计的重点。国内外机械结构的轻量化研究主要集中在两方面:一是通过改变结构材料降低自重,二是改变结构形式。前者不能降低生产成本,因而多采用后者实现结构轻量化设计。浇注型聚氨酯在工业化生产中一般采用两步法生产,采用如图1所示的浇注机,包括浇注机机头1,主机2,转臂装置3,a料罐4,b料罐5,a模温机6,b模温机7,电控柜8,清洗罐9和抽真空装置10。第一步合成的预聚体作为a组份和扩链剂b组份分别装在a料罐4和b料罐5两个罐体内,由系统的温控系统提供了两种原料的不同的温度,利用单独的计量系统,把原料从罐体按照一定的比例输送到混合机头,在混合机头内搅拌头的高速旋转下,物料在混合器中被剪切、拉伸,实现混合反应,反应过程中伴随着热量传输,物料的粘度也在改变,反应后的物料从混合腔出口流出,通过管道浇注入制品模具,浇注完成后,浇注阀把物料从进料管切换到回流管,返回料罐,而混合腔在物料排完后,通过机头清洗阀向混合腔注入清洗剂清洗混合腔,完成一个浇注过程。浇注机底座为空间薄壁梁结构,主要由矩形钢管,钢板(密度ρ=7.84x10^3kg/m^3,弹性模量e=2.068x10^5mpa,泊松比μ=0.3)焊接而成,该底座所受载荷主要为垂直底座平面的集中载荷,根据车架结构和设计计算模型的准确性原则,在建立参数化模型时对其进行部分简化,去除一些对分析结果影响较小的几何特征。对导入ansysworkbench的三维模型定义材料属性,选用workbench平台默认的三维实体单元solid186,自由网格化分,网格尺寸定为3mm,得到底座结构有限元模型,如图2所示,共生成节点1036704个,单元549601个。技术实现要素:本发明的目的是针对上述不足,提出了一种通过采用三维设计软件对浇注机底座进行参数化建模,将模型导入workbench中进行有限元分析后确定设计变量、目标函数、状态变量进行优化设计,从而既能减轻整体重量,又能满足工作强度的浇注机底座轻量化设计方法。本发明具体采用如下技术方案:一种浇注机底座轻量化设计方法,基于ansyaworkbench对浇注机底座参数化建模,将模型导入ansyaworkbench中进行有限元分析,经分析后确定设计变量、目标函数、状态变量进行优化设计,具体包括:几何模型的建立:将浇注机底座的三维模型导入ansysworkbench,并定义三维模型的材料属性,选用ansysworkbench平台默认的三维实体单元solid186进行自由网格化分,网格尺寸为3mm,得到底座结构有限元模型;结构优化:按照实际载荷大小与加载方式计算得到浇注机底座结构工况载荷与位移约束,对有限元模型进行力的加载和边界条件设置;在正常工况下对浇注机底座进行有限元分析,最大等效应力位于浇注机底座的支腿与框架横梁连接处,最大等效应力σmax=61mpa<σs,最大位移位于浇注机底座的中间横梁与a料罐计量泵电机托板连接处,最大位移ξmax=0.34mm;通过静力学分析后的浇注机底座有限元模型和分析结果看,底座在正常工况下所受应力较小,底座强度存在较大设计余量,并且出现明显应力集中现象,因此在浇注机底座中间横梁与a料罐计量泵电机托板连接处增加一支腿,体重比之前增加2.8kg;轻量化设计,根据优化结果重新建模,进行力学性能分析,并和原底座结构力学性能进行对比,得出优化设计效果,将已验证的底座模型导入shapeoptimization模块进行拓扑优化设计,设计中底座在正常工况下所施加的载荷和约束与静力学分析相同,根据减重需求,将优化目标设置为减重50%。优选地,所述几何模型的建立过程中,共生成1036704个节点,549601个单元。优选地,所述结构优化中,在正常工况下对浇注机底座进行有限元分析过程中,所用材料的屈服极限σs=235mpa。本发明具有如下有益效果:该浇注机底座轻量化设计方法对浇注机底座有限元模型进行静力学分析,并根据分析结果对浇注机底座进行结构上的改进,在底座底部增加一个支腿,能够在不明显增加底座质量的前提下极大地提高底座刚度。根据静力学分析结果,对底座进行拓扑优化及尺寸优化两级轻量化设计,使底座质量共减轻了185.43kg,降幅为31.5%,实现了轻量化目标。附图说明图1为浇注机整体结构示意图;图2为ansysworkbench生成的底座结构有限元模型;图3为底座正常工况结构示意图;图4a为底座静力学分析应力云图;图4b为底座静力学分析应力云图;图5a为浇注机底座改进前结构示意图;图5b为浇注机底座改进后结构示意图;图6a为浇注机底座改进后应力分布云图;图6b为浇注机底座改进后应力分布云图;图7为浇注机底座的优化结果示意图;图8为修改后拓扑优化模型静力学分析结果示意图;图9a为浇注机底座尺寸优化后的应力云图;图9b为浇注机底座尺寸优化后的每一次迭代承载梁厚度变化图;图9c为浇注机底座尺寸优化后的每一次迭代托板厚度变化图;图9d为浇注机底座尺寸优化后的每一次迭代底座总质量变化图。其中,1为浇注机机头,2为主机,3为转臂装置,4为a料罐,5为b料罐,6为a模温机,7为b模温机,8为电控柜,9为清洗罐,10为抽真空装置,11为材料可去除部分,12为保留材料部分。具体实施方式下面结合附图和具体实施例对本发明的具体实施方式做进一步说明:如图2所示,一种浇注机底座轻量化设计方法,基于ansyaworkbench对浇注机底座参数化建模,将模型导入ansyaworkbench中进行有限元分析,经分析后确定设计变量、目标函数、状态变量进行优化设计,具体包括:几何模型的建立:将浇注机底座的三维模型导入ansysworkbench,并定义三维模型的材料属性,选用ansysworkbench平台默认的三维实体单元solid186进行自由网格化分,网格尺寸为3mm,得到底座结构有限元模型,共生成1036704个节点,549601个单元;如图3-5b所示,结构优化:按照实际载荷大小与加载方式计算得到浇注机底座结构工况载荷与位移约束,对有限元模型进行力的加载和边界条件设置;在正常工况下对浇注机底座进行有限元分析,所用材料的屈服极限σs=235mpa,最大等效应力位于浇注机底座的支腿与框架横梁连接处,最大等效应力σmax=61mpa<σs,最大位移位于浇注机底座的中间横梁与a料罐计量泵电机托板连接处,最大位移ξmax=0.34mm;通过静力学分析后的浇注机底座有限元模型和分析结果看,底座在正常工况下所受应力较小,底座强度存在较大设计余量,并且出现明显应力集中现象,为提高底座结构合理性,避免因应力集中造成的疲劳损坏,使减重效果更明显,在浇注机底座中间横梁与a料罐计量泵电机托板连接处增加一支腿,体重比之前增加2.8kg;通过静力学分析后的底座有限元模型和分析结果看,底座在正常工况下所受应力较小,底座强度存在较大设计余量,并且出现明显应力集中现象。如图6a和6b所示,改进后的底座结构模型所施加的载荷与位置约束,除增加一个支腿的位置约束外,其余与改进前保持一致,对模型网格划分和静力学分析。底座结构改进后应力集中现象有所改善,最大应力为27mpa,比之前有大幅降低。最大位移0.09mm,有明显减少。轻量化设计,拓扑优化以材料分布为优化对象,主要优化结构的拓扑结构,对底座拓扑优化的传统做法是:直接在底座结构的基础上进行拓扑计算,对拓扑结果建议删除的地方,减少结构尺寸,对拓扑结果建议保留的地方,增加结构厚度或宽度,以此增加底座结构刚度。根据优化结果重新建模,进行力学性能分析,并和原底座结构力学性能进行对比,得出优化设计效果。根据优化结果重新建模,进行力学性能分析,并和原底座结构力学性能进行对比,得出优化设计效果,将已验证的底座模型导入shapeoptimization模块进行拓扑优化设计,设计中底座在正常工况下所施加的载荷和约束与静力学分析相同,根据减重需求,将优化目标设置为减重50%。优化结果如图7所示,材料可去除部分11和保留材料部分12,根据底座实际功能及装配要求,对红色区域进行材料去除处理,根据优化结果对底座结构进行修改,修改后拓扑优化模型静力学分析结果如图8。根据实际情况和拓扑优化结果修改后,底座模型最大应力23.8mpa没有超过需用应力范围,底座结构经过拓扑优化,修改后的质量由改进结构后的591.4kg减少到514.9kg,减重76.5kg降幅12.9%,初步完成了底座的轻量化,由于仍存在设计余量,可用尺寸优化方法对底座进行小范围的精确轻量化设计。尺寸优化是结构优化设计方法中最简单直接的,主要是改变单元结构尺寸达到优化设计目的。设计变量通常取零件厚度或截面尺寸等,约束条件为满足零件条件的多性能指标。浇注机底座结构是根据经验设计确定的,按照设计要求,结构尺寸不能做大幅改变。因此,选取底座主要承载梁矩形管的壁厚d3及保温箱托板厚度t6作为设计变量,将底座总质量最小作为目标函数,将底座结构正常工况下最大应力σmax(不能超过所用材料的屈服极限σs=235mpa)及最大位移ξmax(不能超过垂直方向上位移许用值ξ,本文取ξ=5mm)设置为状态变量,在ansysworkbench中对相应变量参数化设置。在进行优化设计时,对底座模型采用与之前相同的边界条件设置,优化前后各设计变量的取值如表1所示。表1优化前后各设计变量取值设计变量约束下限约束上限初始值优化后承载梁矩形管壁厚d3(mm)11086.015保温箱托板厚度t6(mm)116.51510.03最大应力σmax(mpa)023523.828.612最大位移ξmax(mm)050.090.103底座总质量m(kg)——————————514.94403.17在优化算法中选用系统默认的筛选法对底座模型优化设计,在ansysworkbench中设置相应设计变量变化范围后,对模型尺寸优化,得到三组参考数据,根据实际情况选取一组最优数据,表1,可知拓扑优化后的底座模型经过尺寸优化,质量降低了111.8kg,降幅为21.7%,最大应力有所提升但并没超过材料的屈服极限,且存在设计余量,最大位移也未超过许用位移值。因此,浇注机底座模型经过拓扑优化及尺寸优化二级优化设计后,底座总质量由原本的588.6kg降为403.17kg,共减轻了185.43kg,降幅为31.5%,轻量化效果明显。尺寸优化后应力分布云图和每一次迭代各厚度的变化如图9a-9d所示。本文采用样机试制的方法验证轻量化设计结果的可行性。为保证实验结果的有效性,按照现有二组份聚氨酯浇注机技术要求设计制作了一台聚氨酯浇注机样机,其中底座尺寸按照优化后的结果加工制作,将样机投入生产应用,结果表明优化后的浇注机底座强度完全可以满足聚氨酯浇注机正常工作使用,实验结果充分说明优化设计结果合理性,为浇注机新产品开发提供了参考。对底座有限元模型进行静力学分析,并根据分析结果对底座进行结构上的改进,在底座底部增加一个支腿,能够在不明显增加底座质量的前提下极大地提高底座刚度。根据静力学分析结果,对底座进行拓扑优化及尺寸优化两级轻量化设计,使底座质量共减轻了185.43kg,降幅为31.5%,实现了轻量化目标。样机试制验证优化设计结果的可行性。当然,上述说明并非是对本发明的限制,本发明也并不仅限于上述举例,本
技术领域:
的技术人员在本发明的实质范围内所做出的变化、改型、添加或替换,也应属于本发明的保护范围。当前第1页12