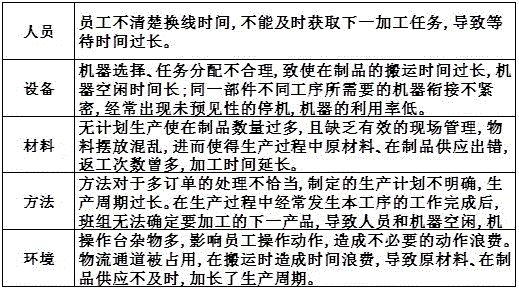
本发明涉及车间控制计划
技术领域:
,具体是基于智能优化算法的双层式生产计划优化控制方法。
背景技术:
:现在的工厂在生产中,订单由销售部进行选择确认后,下发到生产部由计划人员依照经验手工分割成子订单之后编制成生产计划,按照日期顺序下发纸质生产通知单到仓库进行配料,再下发到车间内冲压、折弯等各个工艺组别进行生产。而目前大多厂内车间没有车间调度人员,生产计划的执行主要依靠厂长与各工艺组组长进行沟通,由各组组长组织组内工人进行生产。由于多品种订单式生产模式具有产品种类多、零件加工工序多等特点,计划人员订单分割经验有限、编制生产计划效率低、准确度不高,加上厂内各层次计划比较粗放,车间内部信息流动不畅,导致工人无法实时了解订单中产品数量以及各组组内生产进度等信息,工作具有盲目性,经常出现订单无法按时完成,各班组频繁加班赶工的现象。同时,也存在一下问题:1、员工不清楚换线时间,不能及时获取下一加工任务,导致等待时间过长;2、机器选择、任务分配不合理,致使在制品的搬运时间过长,机器空闲时间长,同一工件不同工序所需的及其衔接不紧密,经常出现未预见性的停机,机器利用率低;3、无计划生产使制品数量过多,且缺乏有效的现场管理;4、制定的生产计划不明确,生产周期过长,在生产过程中经常发生本工序的工作完成后,班组无法确定要加工的下一件产品,导致人员机器空闲。因此,本发明提供一种基于智能优化算法的双层式生产计划优化控制方法来解决上述问题。技术实现要素:针对上述情况,为克服现有技术之缺陷,本发明提供一种基于智能优化算法的双层式生产计划优化控制方法,有效的解决了现在工厂无生产计划,生产计划简陋导致生产效率低下的问题。本发明包括所述的基于智能优化算法的双层式生产计划优化控制方法包括以下两层:第一层:订单排序,以交货期优先为原则,保证订单的总罚费最小,对订单进行排序,生成厂内的生产计划,第二层为车间调度,以最大完工时间最小化与机器利用率最大为目标,考虑了实际生产中的主要因素,对订单制定详细的车间生产计划。第二层:利用遗传算法求解多时间约束的车间调度模型,具体的包括一下几步:第一步:数据的获取与处理,需获取的数据包括工件的加工时间、换模或准备时间、工件移动时间,其获取手段采用秒表测方式;第二步:编码和解码,具体的包括机器选择和工序排序两个子问题,其采用遗传算法实现编码与解码;第三步:适用度函数,把机器利用率和最大完工时间最小化影响着目标函数:f=f1*0.6+f1*f2*0.4其中f为适用度,f1为最大完工时间,f2为机器的利用率,两者在目标中所占权重为6:4;第四步:求得初始解。优选的,所述的第一层订单排序的问题建模如下:ki-1+ti-1*70%=ki(4-1)其中(4-1)表示订单与订单之间的并行度为30%,(4-2)表示随着订单内产品数量的增加,单个产品的加工时间呈指数形式减少,a、b、c对于不同类型的产品而不同。(4-3)xi=0表示订单i无提前或拖期,xi=1表示订单i产生提前期,xi=2表示订单i产生拖期,(4-4)表示目标函数为总罚费最小;具体求解方式如下:规则:奇数位按照交货期早的进行排序,偶数位随机生成;自适应权重计算公式:其中,wamx,wmin分别表示w的最大值与最小值,f表示当前微粒的目标函数值,favg表示当前所有微粒的平均目标值,,fmin表示当前所有微粒的最小目标值。因惯性权重随着微粒的目标函数值变化而自动改变,故称自适应权重;迭代公式:为了使得优良的解得到更大的搜索空间,较差的减少内存的消耗采用自适应变邻域的方式进行对每个粒子生成不同的邻域搜索空间,具体如下:ns=(nsmax-nsmin)*(f-fmin)/(fmax-fmin)优选的,为进一步加强微粒的全局搜索能力,混合变邻域粒子群算法的伪代码如下:输入:接受的订单输出:订单排序1生成初始种群2fori=1:nind*ninia3a:按照交期随机混合生成初始粒子4end5fori=nind*ninia+1:nind6b:随机生成初始粒子7end8计算适应度9粒子惯性w权重更新10粒子学习因子c1,c2更新11粒子邻域搜索范围ns更新12fori=1:maxgen13粒子速度更新;14粒子位置更新15粒子进行自适应变邻域搜索16计算适应度17粒子惯性w权重更新18粒子学习因子c1,c2更新19粒子邻域搜索范围ns更新20end21返回最好的粒子优选的,第二层的利用遗传算法求解多时间约束的车间调度模型的具体模型需符合一下条件:(1)同一机器在同一时刻只能允许加工一个工件;(2)同一工件在同一时刻只能被一台机器加工,且工件一旦开始加工就不能中断;(4)每个工件工序的加工顺序有先后之分,即每一道工序加工完成后会立即被送到下一道工序加工所选用的机器,此时该道工序方可加工;(5)工序加工时间会因所选择的加工机器的不同而不同,加工时间是已知的;(6)同一个工件相邻两道工序在不同机器间移动时,移动时间因相邻两道工序所选择的加工机器的不同而不同,并且机器间的移动时间是给定的。(7)不同工序因选择的加工机器不同而导致换模时间不同,并且机器的换模时间是给定的。(8)所有工件第一道工序在零时刻都可以被机器加工,机器只能在设定时间才可以用于加工,并且机器的开工时间是给定的。优选的,第二层车间调度模型的求解采用以下公式:其中,ti是机器i可以开始加工的时间;ojh是工件j的第h道工序,并定义oj(h-1)为第ojh的上一道工序,oj’h’表示为ojh所在机器的前一道工序;fjh表示工件j的第h道工序加工完成时间;tijh表示工件j的第h道工序在机器i上加工时所需要的时间;ti’j’表示为工件j的第h道工序的辅助时间;sijh表示为工件j的第h道工序在机器i上的加工开始时间;cijh表示为工件j的第h道工序在机器i上的加工结束时间;dctimejhi表示为工件j的第h道工序在机器m上的换模时间;movetimejhie表示为工件j的第h道工序在机器mi和机器me之间工件的移动时间;cj表示为工件j的完工时间;cmax表示为所有工件完工时间中的最大完工时间。本发明针对现在工厂无生产计划,生产计划简陋导致生产效率低下的问题做出新的生产计划优化控制方法,解决了厂内多订单生产中出现的交货期延长,生产周期长,机器利用率低,在制品量多等问题,可取得良好的经济效果和社会效益。附图说明图1为本发明交货期延长统计表。图2为本发明订单的生产周期表。图3为本发明机器时间分布表。图4为本发明机器利用率示意图。图5为本发明制品数量统计图。图6为本发明两层生产计划示意图。图7为本发明2018上半年订单排序示意图。图8为本发明顶板在不同机器上秒表测时表。图9为本发明各工件在不同机器的加工时间表。图10为本发明各机器换模或准备时间。图11为本发明工件移动距离表。图12为本发明甘特图。图13为本发明机器加工计划表。图14为本发明工件加工计划表图15为本发明机器利用率示意图。图16为本发明改善后的订单生产周期表。具体实施方式有关本发明的前述及其他技术内容、特点与功效,在以下配合参考附图1至图16对实施例的详细说明中,将可清楚的呈现。以下实施例中所提到的结构内容,均是以说明书附图为参考。下面将参照附图描述本发明的各示例性的实施例。实施例一,本发明为基于智能优化算法的双层式生产计划优化控制方法,其特征在于,所述的基于智能优化算法的双层式生产计划优化控制方法包括一下两层:第一层:订单排序,以交货期优先为原则,保证订单的总罚费最小,对订单进行排序,生成厂内的生产计划,第二层为车间调度,以最大完工时间最小化与机器利用率最大为目标,考虑了实际生产中的主要因素,对订单制定详细的车间生产计划,然而只有第一层订单排序虽然排列出当前的应做订单顺序,但是依然有部分订单延期,而且订单的生产计划并不详细,不能够具体到每台机器应该在哪个时间做哪个工件的哪个工序,为了解决此问题,建立了利用遗传算法求解多时间约束的车间调度模型;第二层:利用遗传算法求解多时间约束的车间调度模型,具体的包括一下几步:第一步:数据的获取与处理,在车间调度模型中,需要有不同的工件在不同的机器上加工的时间、工件在不同机器上进行加工的换模或准备时间、工件在不同机器之间的移动时间,故需获取的数据包括工件的加工时间、换模或准备时间、工件移动时间,其获取手段采用秒表测方式;第二步:建立模型与编码解码,具体的包括机器选择和工序排序两个子问题,其中机器选择子问题是用来解决每道加工工序在可选机器集中选择哪台机器进行加工,工序排序子问题是解决于工件工序在机器上的加工顺序,其采用遗传算法实现编码与解码,具体的,针对于编码过程中对两个子问题的编码,采用分段编码:即染色体有a/b两个部分,分别代表着模型的两个子问题,a部分表示每道工序选择的机器,b部分表示机器上的工序编码;当编码解码结束后可以得到活动调度,为了使调度结果更加的符合实际,便引入了移动时间,换模时间,开工时间,把机器的换模或准备时间与工件的移动时间相比较较大者作为辅助时间,在机器形成调度后,对每个工序之间,机器之间进行空闲时间检索,用辅助时间与空闲之间对比,若空闲时间大于辅助时间,则不进行调整,若空闲时间小于辅助时间,则对形成的调度进行处理;第三步:适用度函数,因在模型中仅仅考虑机器利用率或者最大完工时间最小化产生的调度都很片面,故需要使机器利用率和最大完工时间最小化同时影响着目标函数:f=f1*0.6+f1*f2*0.4(4-7)其中f为适用度,f1为最大完工时间,f2为机器的利用率,两者在目标中所占权重为6:4;第四步:求得初始解,具体的,种群的初始化在算法中是一个重要的问题,初始解对于算法在运行过程中求解的速度和质量有很大的作用,因此在生成初始化解的时候不仅要保证解多样性,也要保证解的质量性,多样性指初始解覆盖的解空间大,搜索的空间范围广;质量性是指生成的初始解较为接近于最优解;为了满足这两个要求,按照以下三种方式生成初始解:(1)随机生成法:机器部分:每个工序随机在可选择加工机器集中选择一个;工序部分:随机的产生工件的加工顺序;(2)最小时间选择:机器部分:选择当前工序可选择加工机器集中最小加工时间的机器;工序部分:随机的产生工件的加工顺序;(3)剩余加工时间最大优先选择法:机器部分:每个工序随机在可选择加工机器集中选择一个;工序部分:选择当前工件剩余总加工时间最大的工件。实施例二,在实施例一的基础上,所述的第一层订单排序的问题建模如下:有n个订单在工厂内进行加工,每个订单内只有一种产品,数量为mi,每种产品的单个加工时间随着订单内产品数量的增多而减少,其中第i个订单的加工时间为ti。第i订单的交货期为wi;ki表示第i个订单的开始加工时间;ei表示第i个订单的结束加工时间;订单与订单之间的并行度为30%。以交货期为优先原则,订单提前或拖期交货都将产生罚费,根据厂内实际生产更倾向于提前生产,故设置提前或拖期的权数为1:2,以最小罚费cmin为目标函数:ki-1+ti-1*70%=ki(4-1)其中(4-1)表示订单与订单之间的并行度为30%,(4-2)表示随着订单内产品数量的增加,单个产品的加工时间呈指数形式减少,a、b、c对于不同类型的产品而不同。(4-3)中xi=0表示订单i无提前或拖期,xi=1表示订单i产生提前期,xi=2表示订单i产生拖期,(4-4)表示目标函数为总罚费最小;具体求解方式如下:规则:奇数位按照交货期早的进行排序,偶数位随机生成,此规则的设定将原来随机生成的初始粒子变为按照一定规则生成初始粒子,使结果更优,需注意的是,为了使初始粒子具有多样性,保留了一半的随机初始粒子;自适应权重计算公式:非线性的动态惯性权重系数可使算法的全局搜索能力和局部改良能力更优,其中,wmax,wmin分别表示w的最大值与最小值,f表示当前微粒的目标函数值,favg表示当前所有微粒的平均目标值,,fmin表示当前所有微粒的最小目标值。因惯性权重随着微粒的目标函数值变化而自动改变,故称自适应权重,当个微粒目标值陷入局部最优时,惯性权重增大,加强搜索能力;对于目标函数值优于平均目标值的微粒,其惯性权重减小,保留该微粒;迭代公式,对于学习因子进行同步变化,设置学习因子,c1和c2的取值范围为[cmin,cmax],第t次迭代公式如下:为了使得粒子群算法的运行效率更高,局部搜索的能力更强,我们在其中加入了邻域搜索算法,其中为了使得优良的解得到更大的搜索空间,较差的减少内存的消耗采用自适应变邻域的方式进行对每个粒子生成不同的邻域搜索空间,具体如下:ns=(nsmax-nsmin)*(f-fmin)/(fmax-fmin)实施例三,在实施例二的基础上,为进一步加强微粒的全局搜索能力,混合变邻域粒子群算法的伪代码如下:输入:接受的订单输出:订单排序1生成初始种群2fori=1:nind*ninia3a:按照交期随机混合生成初始粒子4end5fori=nind*ninia+1:nind6b:随机生成初始粒子7end8计算适应度9粒子惯性w权重更新10粒子学习因子c1,c2更新11粒子邻域搜索范围ns更新12fori=1:maxgen13粒子速度更新;14粒子位置更新15粒子进行自适应变邻域搜索16计算适应度17粒子惯性w权重更新18粒子学习因子c1,c2更新19粒子邻域搜索范围ns更新20end21返回最好的粒子实施例四,在实施例一的基础上,为了使模型更加符合生产过程中的实际需要,建立了考虑换模时间和工件移动时间的多目标柔作业车间调度模型,具体的,n个工件要在m台机器上加工,每个工件包含的工序数可以是一道工序也可以是多道工序。每道工序只能被一台机器加工,该机器是其可选机器集中的任意一台机器。因考虑到实际情况,机器可以在不同的时刻开始加工。当一道工序加工完毕后会进入下一道工序,若相邻的两道工序加工机器不是同一机器,则要考虑机器的换模时间和工件的移动时间,若为同一机器则只需考虑机器的换模时间。为不同工序选择合适的加工机器、合理地安排工件的加工顺序,优化目标为考虑多时间约束的车间调度模型最大完工时间最小化和机器的利用率最高,此时第二层的利用遗传算法求解多时间约束的车间调度模型的具体模型需符合一下条件:(1)同一机器在同一时刻只能允许加工一个工件;(2)同一工件在同一时刻只能被一台机器加工,且工件一旦开始加工就不能中断;(4)每个工件工序的加工顺序有先后之分,即每一道工序加工完成后会立即被送到下一道工序加工所选用的机器,此时该道工序方可加工;(5)工序加工时间会因所选择的加工机器的不同而不同,加工时间是已知的;(6)同一个工件相邻两道工序在不同机器间移动时,移动时间因相邻两道工序所选择的加工机器的不同而不同,并且机器间的移动时间是给定的。(7)不同工序因选择的加工机器不同而导致换模时间不同,并且机器的换模时间是给定的。(8)所有工件第一道工序在零时刻都可以被机器加工,机器只能在设定时间才可以用于加工,并且机器的开工时间是给定的。实施例五,在实施例四的基础上,第二层车间调度模型的求解采用以下公式:ti’j’=max(dctimejhi,movetimejhie(4-9)cej(h-1)+ti′j′<cejh(4-10)其中,公式(4-5)表示目标函数表达式,即最大完工时间最小化;(4-6)表示机器的均利用率的表达式,即机器的平均利用率最高,式(4-7)表示工序加工的完成时间等于工序开始时间与工序加工时间之和;式(4-8)表示机器的资源约束;式(4-9)表示选取对应的换模时间与移动时间中的较大者作为辅助时间;式(4-10)表示如果工序所在机器的开始加工时间(空隙开始时间)小于上一道工序的辅助时间,则受辅助时间约束;否则(空隙开始时间大于上道工序结束时间),加工工序受当前加工机器的资源约束。式(4-11)表示为工件的第一道工序开始加工的时间受机器开工时间的约束;j={j1,j2,j3,…,jg,…jn}为工件,jg是第g个工件(g=1,2,3,…,n);m={m1,m2,m3,…,mi,…,mm}为机器,mi是第i台机器(i=1,2,3,…,m);ti是机器i可以开始加工的时间;ojh是工件j的第h道工序,并定义oj(h-1)为第ojh的上一道工序,oj’h’表示为ojh所在机器的前一道工序;fjh表示工件j的第h道工序加工完成时间;tijh表示工件j的第h道工序在机器i上加工时所需要的时间;ti’j’表示为工件j的第h道工序的辅助时间;sijh表示为工件j的第h道工序在机器i上的加工开始时间;cijh表示为工件j的第h道工序在机器i上的加工结束时间;dctimejhi表示为工件j的第h道工序在机器m上的换模时间;movetimejhie表示为工件j的第h道工序在机器mi和机器me之间工件的移动时间;cj表示为工件j的完工时间;cmax表示为所有工件完工时间中的最大完工时间。本发明还提供了一种在具体场景中本发明的具体计算方法:生产现状a工厂主要生产各类活动文件柜,订单由销售部进行选择确认后,下发到生产部由计划人员依照经验手工分割成子订单之后编制成生产计划,按照日期顺序下发纸质生产通知单到仓库进行配料,再下发到车间内冲压、折弯等各个工艺组别进行生产。目前厂内车间没有车间调度人员,生产计划的执行主要依靠厂长与各工艺组组长进行沟通,由各组组长组织组内工人进行生产。由于多品种订单式生产模式具有产品种类多、零件加工工序多等特点,计划人员订单分割经验有限、编制生产计划效率低、准确度不高,加上厂内各层次计划比较粗放,车间内部信息流动不畅,导致工人无法实时了解订单中产品数量以及各组组内生产进度等信息,工作具有盲目性,经常出现订单无法按时完成,各班组频繁加班赶工的现象。总结出交货期延长的主要原因,参考图1;问题分析由于七月份是厂内的生产高峰期,故选取七月一号到七月三号下单的的五个订单为例,进行生产周期的分析,计算出订单的生产周期,参考图2,从中可以得出7月1日和7月3日下单的5个订单的生产周期在12-16天之间,有三个订单出现延期交货情况。最长延期天数为14.93天,最短延期天数为4.49天。据了解,在订单数较多、订单产品数量较大的情况下,订单延期交货情况更为严重。选取一周的时间从加工、换模、修理、待机四个方面统计机器使用情况,做出堆积图和扇形图分别参考图3、图4,根据图3可知,各个机器的利用率不一致,机器利用率低、长时间待机问题普遍存在,折弯组的机器利用率最低,只有36.47%;根据图4可知,综合所有机器的使用情况,发现在一天之内机器加工时间占比不到50%,待机的时间达到了27.87%,机器的利用率低使得产品部件不能及时加工,从而影响订单的生产周期,也反映出工厂对多订单的生产模式不能制定出合理的生产计划;在某个时间点,清点了工厂内不同工作区的不同部件的数量并制作了统计图,参考图5,由图5可知每个部件在下料区的在制品数量最多,达到16573件,占比约23.46%。但却会出现有些部件下料不足,如背板、左侧板、右侧板。主要原因为下发到车间各工艺组的生产通知单只包含下单日期、与客户约定的交货期、订单号、产品型号、数量等信息,并没有具体到每个工艺组各部件生产总量等信息。比如冲压组每天要冲压多少个面板,都要靠各个组长根据经验估算数量后通知组内工人,在实际生产过程中工人对于具体生产数量具有很大的不确定性,这样就会导致前后工序在制品衔接不畅,出现断料、人等机器、机器等人的情况,生产过程中停滞待工的时间较长。从上述问题可以发现,目前工厂内最大的问题为生产计划不合理,没有合理的订单排序与详细的车间级计划。工厂目前在排单计划的过程中出现有些订单做的过早,而有些订单做的过晚的情况,导致一些需要出货的产品无法及时的完成加工,而一些当前无需加工的订单却在加工的现状。且订单在进行加工的过程中出现了订单中产品部件生产混乱,进而导致生产周期长、在制品量多与机器利用率低等问题。第一层订单排序模型构建与验证基于上述问题分析,设计出一种两层式的生产计划排序结构,参考图6;至此,问题分析完成,进入方法使用阶段,先对第一层订单排序模型构建与求解,根据本发明中第一层的建模与求解方法(实施例二和实施例三中的计算方法),得出厂内2018年上半年的订单排序表,参考图7;经过订单的排序,可以准确的定位并筛选出当前需要优先做的订单,确定其余的订单应该在哪个时间段进行生产,通过排序,可以判断出当有加急订单产生时,加工该订单是否会影响其余订单的交货期。如此排列出当前的应做订单顺序,但是依然有部分订单延期,而且订单的生产计划并不详细,不能够具体到每台机器应该在哪个时间做哪个工件的哪个工序,故进行本发明的第二层。第二层车间调度模型的构建为了使模型更加符合生产过程中的实际需要,建立了考虑换模时间和工件移动时间的多目标柔作业车间调度模型。n个工件要在m台机器上加工,每个工件包含的工序数可以是一道工序也可以是多道工序。每道工序只能被一台机器加工,该机器是其可选机器集中的任意一台机器。因考虑到实际情况,机器可以在不同的时刻开始加工。当一道工序加工完毕后会进入下一道工序,若相邻的两道工序加工机器不是同一机器,则要考虑机器的换模时间和工件的移动时间,若为同一机器则只需考虑机器的换模时间。为不同工序选择合适的加工机器、合理地安排工件的加工顺序,优化目标为考虑多时间约束的车间调度模型最大完工时间最小化和机器的利用率最高;假设以下条件:(1)同一机器在同一时刻只能允许加工一个工件;(2)同一工件在同一时刻只能被一台机器加工,且工件一旦开始加工就不能中断;(4)每个工件工序的加工顺序有先后之分,即每一道工序加工完成后会立即被送到下一道工序加工所选用的机器,此时该道工序方可加工;(5)工序加工时间会因所选择的加工机器的不同而不同,加工时间是已知的;(6)同一个工件相邻两道工序在不同机器间移动时,移动时间因相邻两道工序所选择的加工机器的不同而不同,并且机器间的移动时间是给定的;(7)不同工序因选择的加工机器不同而导致换模时间不同,并且机器的换模时间是给定的;(8)所有工件第一道工序在零时刻都可以被机器加工,机器只能在设定时间才可以用于加工,并且机器的开工时间是给定的。数据获取与处理车间调度模型中,需要有不同的工件在不同的机器上加工的时间、工件在不同机器上进行加工的换模或准备时间、工件在不同机器之间的移动时间。工件的加工时间采用秒表时间研究的方法,对常规的产品进行工时测量,为了便于描述和计算,我们将某一个订单中的469件产品做为一件产品进行批量处理。以产品的顶板为例,顶板在生产的过程中需要经过下料、冲压、折弯、点焊和喷粉等工序,不同的工序可采用的机器不同,加工的时间也不同,每个工序的不同机器分别选取了15组具有代表性的数据进行分析,分析结果参考图8。其中:ucl=平均值+3×标准差;lcl=平均值-3×标准差正常时间=观测时间×评定系数标准时间=正常时间×(1+宽放率)宽放率为人的生理宽放和作业宽放,取宽放率为15%按照上述方法测出了全部的数据,参考图9。换模或准备时间同样采取了秒表测时的方法对工厂内的机器换模或准备时间进行测时,参考图10。工件的移动时间根据厂内的布局、工件在机器与机器之间移动路线进行实地测试,采取秒表测时的方法得出结果,参考图11。数据代入及分析遗传算法的具体参数为:个体数目40;最大遗传代数:100;代沟:0.9;交叉率:0.8;变异率:0.6。按照实际的生产过程设定机器的开工时间为:机器剪板机1剪板机2激光切1激光切2转塔冲冲压组1冲压组2冲压组3折弯点焊电焊1氩焊喷粉开工时间00120120120360360360480600720840960把上述得到的数据以及参数代入到模型中得到甘特图,具体参考图12;其中白色的部分代表着工件的移动或者是机器的换模时间,其余部分为工件的加工时间。如白色的101部分代表着工件1的第一道工序的辅助时间,阴影的101部分代表着工件1的第一道工序加工时间,对其在1上表示着在剪板机一上加工,其余的如此读取。由此得到单个订单在未包装前的生产周期为2519.98分钟,按厂内一天正常工作时间8个小时来算,在未包装前的生产周期为5.24天,加上产品的包装时间为订单的生产周期为5.89天;并生成及其加工计划表图13和工件加工计划表图14;根据重排的生产计划计算出机器利用率,参考图15,得出机器的平均利用率达到了79.21%。把上个订单在机器上的完成时间作为下个订单的开始时间,得出订单生产周期的汇总表,参考图16,可以看出订单全部如期交货。效果评价经过两层式的生产计划排列结构,解决了厂内多订单生产中出现的交货期延长,生产周期长,机器利用率低,在制品量多等问题。经过订单的排序,产生的主计划可以明确出是否可以插单,哪个订单在哪个时间段内生产等问题,建立考虑换模时间和工件移动时间的多目标作业车间调度模型有效的解决了厂内生产过程中由于车间调度不合理造成的生产周期长、机器的利用率低、在制品量多等问题。订单的生产周期从之前的13.72天降低到6.3天,生产周期降低了7.42天,机器整体利用率由之前的49.41%提升到79.39%,机器的整体利用率提升了29.98%订单的交货延期交货问题可以解决。整个工厂内产能将会提升30%以上。厂内目前的年生产产品按35000台来算,可以提升到45500台;按照厂内目前每年的营业额约为五千万,大约每年的营业额可以再增加一千五百万。由于钢制家具生产基地的生产模式大多相同,故此种车间生产计划模式可以推广到整个钢制家具的生产基地,取得良好的经济效果和社会效益。本发明针对现在工厂无生产计划,生产计划简陋导致生产效率低下的问题做出新的生产计划优化控制方法,解决了厂内多订单生产中出现的交货期延长,生产周期长,机器利用率低,在制品量多等问题,可取得良好的经济效果和社会效益。当前第1页12