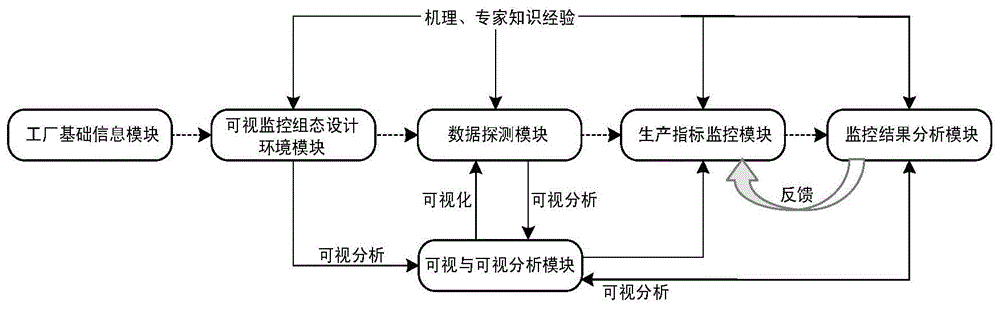
本发明涉及生产指标监控
技术领域:
,尤其涉及一种基于组态的生产指标可视化监控系统及方法。
背景技术:
:生产指标可视化监控系统是工业过程中数据联系最为频繁的环节,也是直接体现工业过程最终产品的质量与产量的窗口;目前国内关于生产指标可视化监控系统及方法的研究和应用为数不多且功能单一。“201711283037.x(一种选矿生产指标可视化分析系统与方法)”实现对选矿生产各工序指标的整合和配置并对指标异常进行分析可视。“201811009657.9(一种选矿生产指标的关联关系可视化系统及方法)”实现了对选矿生产指标间关联关系的分析,以及对生产指标间时序变化关系的分析,最终将所分析的生产指标间的关系可视。“201811010246.1(一种基于工艺流程的选矿生产指标可视化监控系统及方法)”提供了基于生产工艺流程的生产指标可视化组态设计,支持实时数据、历史数据、历史数据统计特性的可视化方案,能够为生产指标监控配置生产指标监控算法,实现对生产指标的监控。以上专利主要包括对选矿生产指标异常的监控并提供报警处理,对生产指标间的关系进行可视分析,201811010246.1主要提供了生产工艺流程组态工具,并对指标数据进行实时、历史监控;多视图可视仅限于对指标的分类监控。但上述专利缺少对各工艺流程的完整逻辑结构,缺少对生产指标数据的探测,对生产指标的可视化方案局限于显示实时数据和历史数据,多视图监控局限于指标分类层面,同时也没有涉及对监控结果的分析以及反馈。技术实现要素:本发明要解决的技术问题是针对上述现有技术的不足,提供一种基于组态的生产指标可视化监控系统及方法,实现对生产指标的可视化监控。为解决上述技术问题,本发明所采取的技术方案是:一方面,本发明提供一种基于组态的生产指标可视化监控系统,包括工厂基础信息模块、可视监控组态设计环境模块、数据探测模块、可视与可视分析模块、生产指标监控模块及监控结果分析模块;所述工厂基础信息模块用于对工厂基础信息进行建模,实现工厂对基础信息的管理;所述可视监控组态设计环境模块用于构建基于工厂基础信息模块的各个工艺流程,利用生产工艺流程的逻辑关系,构建各工序的流程及其子流程,并配置各工序及其子工序的设备、生产指标、报警事件、生产工艺规则约束、专家经验知识和算法约束;所述可视与可视分析模块用于提供生产指标可视化和可视化分析方案,此模块不仅包括实时数据、历史数据及统计特性的可视化,还支持指标数据对比分析、生产指标关联关系的可视化分析及生产指标多视图的可视化;所述数据探测模块用于探测生产指标数据之间的关系;所述生产指标监控模块用于实现可视监控组态设计环境模块构建完成的工艺流程的可视化监控,结合专家经验、知识和数据探测模块分析得出的生产指标数据之间的关系、借助于可视与可视分析模块对指标的可视分析,根据实际需求对配置关键指标进行监控;所述监控结果分析模块用于分析生产指标监控过程中出现的未被监控到的新的异常和故障,同时监控和收集生产指标监控模块中的报警记录,通过逐一分析报警记录信息,追溯设备、指标异常或故障的原因,利用数据探测模块对历史数据进行探测分析,并结合机理、专家知识经验重新配置生产指标监控模块中的监控指标,从而实现对生产指标监控异常的有效反馈,实现对生产指标监控的动态调整,使得生产指标可视化监控系统具备动态演化能力;所述可视监控组态设计环境模块包括图元库子模块、绘制面板子模块、功能栏子模块、项目工序子模块、配置子模块和第一工序库子模块;所述生产指标监控模块包括第二工序库子模块、生产指标监控与配置子模块、工序监控子模块、报警记录子模块。优选地,所述工厂基础信息模块包括组织结构基础信息管理单元、工序流程基础信息管理单元、设备档案基础信息管理单元、指标档案基础信息管理单元、计量单位基础信息管理单元、物料基础信息管理单元和人员档案基础信息管理单元;所述组织结构基础信息管理单元用于管理工厂内部各个部门之间层次和职能结构信息;所述工序流程基础信息管理单元用于管理各个工艺流程以及其子工序流程;所述设备档案基础信息管理单元用于管理各个工艺流程中所涉及的所有设备信息;所述指标档案基础信息管理单元用于管理各个工艺流程中所涉及的所有指标信息;所述计量单位基础信息管理单元用于管理设备、指标的度量单位;所述物料基础信息管理单元用于管理生产过程中涉及的物料信息;所述人员档案基础信息管理单元用于管理生产过程中涉及的人员信息。优选地,所述图元库子模块包括常见图元节点和连接线的形状,及根据需求自定义的图元和连接线形状;所述绘制面板子模块通过鼠标拖拽方式将图元库中节点拖至绘制面板中,并配置端点、锚点及工序状态;所述功能栏子模块包括保存、导入、后退、前进、清除、缩放和刷新功能;所述保存功能用于将新构建的工艺流程或子流程保存到数据库或以文本格式保存到本地;所述导入功能用于将本地文件转换为文本格式导入到绘制面板;所述后退功能用于后退到上一个操作时的界面状态;所述前进功能用于恢复后退功能的操作;所述清除功能用于清空当前绘制面板;所述缩放功能用于放大或缩小当前绘制面板,既能概览整个的工艺流程,也能放大局部具体查看各个子流程;所述刷新功能用于初始化整个绘制面板;所述项目工序子模块用于显示当前所配置的项目的各工序及子工序,并在各工序名称后面用不同颜色的五角星表示目前各工序的设计状态;所述配置子模块包括工序配置子模块和指标配置子模块,用于配置选定工序的基础信息、工序事件、工序指标、约束条件,并通过鼠标进行各个工序节点间的连线,同时在连线上配置各工序之间输入输出指标类型;所述第一工序库子模块用来管理已经构建好的通用基础工序单元,以用于快速构建新的工艺流程图,从而提高基础工序组件的复用性和重用性。优选地,所述数据探测模块用于探测指标数据之间的关系,具体包括指标间关联关系的探测、指标间时序变化关系的探测、指标间主元变量的探测及指标数据与维度之间的双向关联关系的探测;所述指标间关联关系的探测通过皮尔逊相关系数和信息熵分析指标间的关联关系,包括输入与输入指标之间、输入与输出指标之间、输出与输出指标之间的关系;所述皮尔逊相关系数用于分析指标间线性关系;所述信息熵用于分析指标间非线性关系;所述指标间时序变化关系的探测是指通过皮尔逊相关系数分析生产指标之间的延迟相关性,即生产指标之间是否间隔一段采样时间而具有相关性;所述指标间主元变量的探测通过主成分分析及基于核函数的主成分分析将影响待测指标的指标集从高维投影到低维,实现对生产指标的降维。优选地,所述实时数据可视化用于反应当前生产运行状态是否正常,生产相关指标是否达到预期目的;采用图表、实时数据曲线的方式进行可视化;所述历史数据及统计特性可视化用于反应指标在一段时间内的历史趋势并对历史数据的统计特性进行可视化,并通过时间滑窗的形式灵活的查看不同时间段的历史数据;同时提供移动、放缩、悬浮提示框、刷新的交互操作;所述指标数据对比分析可视化通过同时展示不同量纲的多维数据,采用平行坐标图的形式进行表示;所述平行坐标图显示多个维度的数据,每个坐标轴表示一个维度,每个维度表示一个生产指标;所述生产指标关联关系可视化用于显示生产指标之间的关联关系,输入指标和输入指标、输出和输出指标之间关系使用散点图表示;过程指标与运行指标之间的关联关系,采用图论中的二分图表示;所述二分图是指将过程指标和运行生产指标分别看成两个独立的点集,通过两个点集的映射关系表征两个集合中点的关联关系;所述生产指标多视图可视化根据指标的所属工序和指标类型进行分类,设计多视图可视化方案,提供多视图交互技术;每一个工序和指标类别都对应一个视图,其中,工序为主视图,指标分类为子视图,嵌入到工序视图中;操作员点击具体工序以导航进入该工序查看详细信息,此时,其余工序视图通过缩放技术进行缩小,显示为缩略图;同时在该工序下点击具体的子工序导航进入该工序的子工序查看详细信息;在已选择工序或者子工序下,操作员点击具体分类指标,查看该工序或者子工序下该分类指标视图里面的指标详细信息,此时其余指标类别视图通过缩放技术进行缩小,显示为缩略图。优选地,所述第二工序库子模块用于显示当前所有的工序流程,包括各级子工序,用来帮助用户导航到具体的工序;操作员通过点击相应的工序,工序监控子模块会同步导航到该工序,以显示该工序的工艺流程;所述生产指标监控与配置子模块用于显示与配置各工序的指标以及对指标配置可视化方案,操作员能够在可视监控组态设计环境模块已配置指标的基础上,根据实际需求过滤出各工序关键指标,并通过配置功能配置各工序关键指标,实现对各工序关键指标的监控;同时对各个指标配置可视化方案以便进行可视化监控;所述工序监控子模块用于显示第二工序库子模块中所点击的工序,触发可视监控组态设计环境模块定义该工序的约束条件、工序事件、工序状态,工序点击事件,操作员通过双击查看子过程的实时状态;同时监控该工序已配置监控指标的实时数据曲线和历史数据曲线,并显示该工序下各指标已配置的可视化方案,通过可视分析更高效的监控生产指标;所述报警记录子模块用于显示当前时段的报警信息,每条报警记录包括报警时间,报警所在的工序名称,故障设备名称和异常指标名称;在设备名称、指标名称前提供符号提示。另一方面,本发明还提供一种基于组态的生产指标可视化监控方法,包括以下步骤:步骤1、通过工厂基础信息模块收集、录入工厂的生产基础信息,构建基础信息单元并将其存储至数据库,实现工厂对基础信息的管理;所述基础信息的管理包括组织结构基础信息管理、工序流程基础信息管理、设备档案基础信息管理、指标档案基础信息管理、计量单位基础信息管理、物料基础信息管理、人员档案基础信息管理。步骤2、通过使用工厂基础信息模块中的基础信息管理单元,构建各生产流程可视监控组态设计环境,具体方法为:步骤2.1、从图元库中选择需要构建的基础图元,点击所选图元将其拖到工艺流程绘制面板;步骤2.2、根据实际生产工艺流程绘制组态界面,并配置各个工序的端点、锚点、工序状态信息;步骤2.3、在工序配置子模块配置工序基础信息、工序事件、约束条件属性,并通过鼠标绘制各个工序间的有向连线,表示实际生产中的流程;步骤2.4、在指标配置子模块为各工序配置指标、并配置指标类型,包括输入指标、输出指标、输入输出指标、被控量和控制量;步骤2.5、在已有指标类型的基础上添加算法,并通过选择框的形式选择不同的算法进行建模;步骤2.6、通过功能栏子模块的保存功能钮,将配置完成的工序保存至本地数据库并显示到项目工序子模块,项目工序子模块显示当前项目工序流程,不同的标识颜色表示目前该工序的设计状态,红色表示配置完成,绿色表示配置未完成,黄色表示未配置;步骤2.7、同时将配置完成的工序保存至工序库,集中管理已经构建完成的通用基础工序单元,从而提高基础工序组件的复用性和重用性;步骤2.8、将绘制并配置完成的流程图保存为文本格式数据,然后将数据保存至本地数据库或导出为文本文件保存至本地;步骤3、在可视监控组态设计环境模块的基础上,应用数据探测模块探测指标数据之间的关系,具体方法为:步骤3.1、探测指标间的关联关系,包括输入与输入指标之间、输入与输出指标之间、输出与输出指标之间的关系;通过皮尔逊相关系数分析指标间的线性关联关系,通过互信息分析指标间的非线性相关关系;步骤3.1.1、使用皮尔逊相关系数分析指标间线性关联关系,如果分析结果表明指标间线性关系强,则指标间存在线性相关性,如果分析结果表明指标间不存在线性关系,转到步骤3.1.2,探测指标间是否存在非线性关系;步骤3.1.2、通过互信息分析指标间非线性相关关系;步骤3.2、探测指标间时序变化关系,通过皮尔逊相关系数分析生产指标之间的延迟相关性,即生产指标之间是否间隔一段采样时间而具有相关性;步骤3.3、探测指标间的潜变量,从而通过使用潜变量代替原始的指标变量,实现对指标的降维;使用主成分分析和基于核函数的主成分分析方法分别探测线性指标间潜变量和非线性指标间的潜变量;利用步骤3.1的结论,如果指标数据间是线性关系,则转到步骤3.3.1,如果指标数据间是非线性关系,则转到步骤3.3.2;步骤3.3.1、利用主成分分析探测指标间的潜变量,利用主成分分析求解出指标数据的特征值并按其值从大到小进行排列,选择其中最大的k个,使得这k个主成分占全部主成分的百分比超过设定的阈值,使用这k个特征值对应的主元即潜变量代替原始指标,实现对原始指标数据的降维;步骤3.3.2、利基于核函数的主成分分析提取非线性特征,通过非线性函数将指标集映射到高维线性特征空间,然后在高维空间中使用主成分分析方法计算其主元成分,实现对原始指标数据的降维;步骤3.4、将经过数据探测模块分析得到的结果通过可视与可视分析模块中可视化功能以更直观的方式展示出来;步骤4、以可视监控组态设计环境模块中已配置的生产指标为基础,借助数据探测模块分析得出的指标间各类关系,利用可视与可视分析模块对生产指标数据进行可视分析,以辅助人们从可视的角度去理解指标数据间的关系,具体方法为:步骤4.1、采用图表或实时数据曲线的方式表示实时数据,反应当前生产运行状态是否正常,生产相关指标是否达到预期目的;步骤4.2、采用历史数据曲线的方式表示历史数据,并通过时间滑窗的形式灵活的查看不同时间段的历史数据趋势,同时提供交互操作,包括移动、放缩、悬浮提示框、刷新;步骤4.3、采用平行坐标图表示指标数据对比分析,同时展示不同量纲的多维数据;步骤4.3.1、通过平行坐标图显示多个维度的数据,每个坐标轴表示一个维度;步骤4.3.2、每个维度表示一个生产指标,通过对每个维度设置不同单位来描述不同数量级的数据;步骤4.3.3、每个维度显示该指标数据的当前值,通过设置上下限,反应该指标当前的运行状态,若超出限制值有报警提示,异常指标数据所在的坐标轴显示为红色;步骤4.3.4、在正常工况下,每个生产指标均在上下限范围内,平行坐标图的整体轮廓大致相同,若整体轮廓出现异常形状,表示工况异常;操作员通过观察图形的整体轮廓,判断生产运行情况;步骤4.4、借助二分图的方法,采用桑基图的方式表示生产指标关联关系;步骤4.4.1、在二分图中,将过程指标和运行指标分别看成两个独立的点集,通过两个点集的映射关系表征两个集合中点的关联关系;步骤4.4.2、将二分图中的映射关系平移到桑基图中,左侧颜色条代表过程指标,右侧颜色条代表影响过程指标的运行指标;步骤4.4.3、通过对左右两侧的颜色条设置不同的颜色来区分不同的指标;左侧各个颜色条流向右侧,表示右侧指标影响左侧指标的因素;步骤4.4.4、根据步骤3筛选出的关键指标以及各个过程指标与运行指标间关系,计算各工序指标对过程指标影响的贡献率,确定图中各个指标的比例关系;步骤4.4.5、提供交互操作,当鼠标悬浮于左侧某个过程指标所在区域时,单独显示影响该指标的左侧指标,并显示百分比以表示对该指标的影响程度;步骤4.5、采用多视图交互技术实现指标多视图监控的可视;步骤4.5.1、每一个工序对应一个主视图,每一个指标分类对应一个子视图;步骤4.5.2、将指标分类视图嵌入到工序视图中;步骤4.5.3、操作员点击具体工序导航进入该工序,该工序视图通过缩放技术进行放大并显示详细信息,此时其余工序视图通过缩放技术进行缩小,显示为缩略图;步骤4.5.4、在该工序中,点击具体分类指标,该分类视图通过缩放技术进行放大并显示该类别指标,此时其余工序视图通过缩放技术进行缩小,显示为缩略图;步骤5、在生产指标监控模块中配置监控运行参数,具体方法为:步骤5.1、参考数据探测模块和可视与可视分析模块分析得出的指标数据间的关系,借助可视与可视分析模块中各可视化方案所呈现的信息,直观显示生产指标间关联关系和重要程度,为配置监控指标提供依据;步骤5.2、结合专家知识经验,补充因系统分析不全面所遗漏的指标,配置生产指标监控模块的参数;步骤5.3、在生产指标监控模块中构建生产指标监控运行环境,配置监控运行参数;步骤5.3.1、通过第二工序库子模块显示当前所有的工序流程,包括各级子工序;步骤5.3.2、通过点击第二工序库子模块中的工序,工序监控子模块同步导航到该工序,显示该工序的工艺流程;选中相应工序时,触发可视监控组态设计环境模块定义的该工序的约束条件、工序事件、工序状态,工序点击事件;步骤5.3.3、根据实际需求在生产指标监控与配置子模块中对各工序配置所要监控的关键指标,以及对该工序已配置的指标配置可视化方案;步骤5.3.4、通过双击查看该工序的子过程的实时状态;显示该工序已配置的所有指标,指标的实时数据曲线、历史数据曲线;同时显示各个可视化方案,便于监控分析已配置指标;步骤5.3.5、通过报警记录子模块显示当前时段的报警信息,每条信息包括故障时间、故障工序名称、故障设备名称及异常指标名称;并分析出设备故障类型和指标异常类型,如设备停歇、指标超上限、指标超下限;步骤6、通过监控结果分析模块分析生产指标监控过程的中出现的未处理的异常和故障;步骤6.1、通过监控结果分析模块分析正在监控的工艺流程中未知故障;步骤6.2、同时监控和收集生产指标监控模块中的报警记录,通过逐一分析报警记录信息,追溯设备、指标异常或故障的原因;步骤6.3、利用数据探测模块对历史数据进行探测分析;步骤6.4、结合机理、专家知识经验重新配置生产指标监控模块中监控指标;步骤6.5、最终实现对生产指标监控异常的有效反馈,实现对生产指标监控的动态调整。采用上述技术方案所产生的有益效果在于:本发明提供的一种基于组态的生产指标可视化监控系统及方法,实现了对工厂逻辑结构、基础信息的管理,设计了可视监控组态设计环境模块,组态生产工艺流程,实现了对生产指标监控的完全可配置性。同时,实现了对各类生产专家的知识和经验的集成,以及探测数据之间的各类关系,辅助用户进行指标监控,使得对生产过程的监控更加精准和高效。通过可视分析技术支持多种可视化方案,帮助用户探测和了解数据;通过多视图交互技术实现了系统自动生成指标概览视图和不同等级的嵌套视图,方便用户在不同视图之间进行交互。此外,还实现了对正在运行的工艺流程中未知故障的分析,重新配置关键生产指标再监控,能够及时实现有效的反馈,从而实现对生产指标监控的动态调整,使得生产指标可视化监控系统具备动态演化能力。附图说明图1为本发明实施例提供的一种基于组态的生产指标可视化监控系统的结构框图;图2为本发明实施例提供的一种基于组态的生产指标可视化监控方法的流程图。具体实施方式下面结合附图和实施例,对本发明的具体实施方式作进一步详细描述。以下实施例用于说明本发明,但不用来限制本发明的范围。本实施例以选矿三选厂为例,使用本发明的一种基于组态的生产指标可视化监控系统及方法实现对该选矿三选厂的生产指标进行监控。一种基于组态的生产指标可视化监控系统,如图1所示,包括:工厂基础信息模块、可视监控组态设计环境模块、数据探测模块、可视与可视分析模块、生产指标监控模块和监控结果分析模块。其中,工厂基础信息模块用于对工厂基础信息的建模,有助于操作员高效的创建工艺流程,实现工厂对基础信息的管理。该模块包括组织结构基础信息管理单元、工序流程基础信息管理单元、设备档案基础信息管理单元、指标档案基础信息管理单元、计量单位基础信息管理单元、物料基础信息管理单元、人员档案基础信息管理单元。所述组织结构基础信息管理单元用于管理工厂内部各个部门之间层次和职能结构信息;所述工序流程基础信息管理单元用于管理各个工艺流程以及其子工序流程;所述设备档案基础信息管理单元用于管理各个工艺流程中所涉及的所有设备信息;所述指标档案基础信息管理单元用于管理各个工艺流程中所涉及的所有指标信息。所述计量单位基础信息管理单元用于管理设备、指标的度量单位;所述物料基础信息管理单元用于管理生产过程中涉及的物料信息;所述人员档案基础信息管理单元用于管理生产过程中涉及的人员信息。可视监控组态设计环境模块用于构建基于工厂基础信息模块的各个工艺流程,利用生产工艺流程的逻辑关系,构建各工序的流程及其子流程,并配置各工序及子工序的设备、生产指标、报警事件、生产工艺规则约束、专家经验知识和算法约束。包括图元库子模块、绘制面板子模块、功能栏子模块、项目工序子模块、配置子模块及第一工序库子模块。所述图元库子模块,包括常见图元节点和连接线的形状,也可根据需求自定义图元和连接线形状并添加至图元库中。所述绘制面板子模块,通过鼠标拖拽方式将图元库中节点拖至绘制面板中,并配置端点、锚点、工序状态。所述功能栏子模块包括保存、导入、后退、前进、清除、缩放、刷新功能;所述保存功能用于将新构建的工艺流程或子流程保存到数据库或以文本格式保存到本地;所述导入功能用于将本地文件转换为文本格式导入到绘制面板或者导入到数据库;所述后退功能用于后退到上一个操作时的界面状态;所述前进功能用于恢复后退功能的操作;所述清除功能用于清空当前绘制面板;所述缩放功能用于放大或缩小当前绘制面板,既能概览整个的工艺流程,也能放大局部具体查看各个子流程;所述刷新功能用于初始化整个页面。所述项目工序子模块用于显示当前所配置的项目的各工序及子工序,各工序名称后面用不同颜色的五角星表示目前各工序的设计状态,红色表示配置完成,绿色表示配置未完成,黄色表示未配置;所述配置子模块包括工序配置子模块和指标配置子模块,用于配置选定工序的基础信息、工序事件、工序指标和约束条件,并通过鼠标指进行各个工序节点间的连线,同时在连线上配置各工序之间输入输出指标类型。所述第一工序库子模块用来管理已经构建好的通用基础工序单元,以用于快速构建新的工艺流程图,从而提高基础工序组件的复用性和重用性。数据探测模块用于探测指标数据之间的关系;包括指标间关联关系探测、指标间时序变化关系探测、指标间主元变量探测和指标数据与维度之间的双向关联关系探测。所述指标间关联关系探测是指通过皮尔逊相关系数、信息熵分析指标间关联关系,包括输入与输入指标之间、输入与输出指标之间、输出与输出指标之间的关系;所述皮尔逊相关系数用于分析指标间线性关系;所述信息熵用于分析指标间非线性关系。所述指标间时序变化关系探测是指通过皮尔逊相关系数分析生产指标之间的延迟相关性,即生产指标之间是否间隔一段采样时间而具有相关性。所述指标间主元变量探测是指通过主成分分析(principalcomponentanalysis,即pca)和基于核函数的主成分分析(kernelprincipalcomponentanalysis,即kpca)将影响待测指标的指标集从高维投影到低维,实现对生产指标的降维。所述主成分分析是指通过线性空间变换求取主成分变量,将高维空间变量投影到低维主成分空间;所述基于核函数的主成分分析用于非线性特征提取,通过非线性函数将指标集映射到高维空间再实现pca。可视与可视分析模块用于提供生产指标可视化和可视化分析方案,此模块不仅包括实时数据、历史数据的可视化,还支持指标数据对比分析、生产指标关联关系可视分析和生产指标多视图可视化。所述实时数据用于反应当前生产运行状态是否正常,生产相关指标是否达到预期目的。采用图表、实时数据曲线的方式进行可视化。所述历史数据及统计特性用于反应指标在一段时间内的历史趋势并对历史数据的统计特性进行可视化,通过时间滑窗的形式灵活的查看不同时间段的历史数据。同时提供交互操作,包括移动、放缩、悬浮提示框、刷新。所述指标数据对比分析是指同时展示不同量纲的多维数据,采用平行坐标图的形式。所述平行坐标图显示多个维度的数据,每个坐标轴表示一个维度,每个维度表示一个生产指标。所述生产指标关联关系可视化用于显示生产指标之间的关联关系,输入指标和输入指标、输出和输出指标之间关系使用散点图表示;过程指标与运行指标之间的关联关系,采用图论中的二分图表示。所述二分图是指将过程指标和运行生产指标分别看成两个独立的点集,通过两个点集的映射关系表征两个集合中点的关联关系。所述生产指标多视图可视化是指根据指标的所属工序和指标类型进行分类,设计多视图可视化方案,提供多视图交互技术。每一个工序和指标类别都对应一个视图,其中工序为主视图,指标分类为子视图,嵌入到工序视图中。操作员可点击具体工序以导航进入该工序查看详细信息,此时其余工序视图通过缩放技术进行缩小,显示为缩略图;同时在该工序下可以点击具体的子工序导航进入该工序的子工序查看详细信息;在已选择工序或者子工序下,操作员同样可点击具体分类指标,查看该工序或者子工序下该分类指标视图里面的指标详细信息,此时其余指标类别视图通过缩放技术进行缩小,显示为缩略图。生产指标监控模块用于实现可视监控组态设计环境模块构建完成的工艺流程的可视化监控,结合专家经验、知识和数据探测模块分析得出的指标数据的关系、借助于可视与可视分析模块对指标的可视分析,根据实际需求配置关键指标进行监控,包括第二工序库子模块、生产指标监控与配置子模块、工序监控子模块、报警记录子模块。所述第二工序库子模块主要显示当前所有的工序流程,包括各级子工序,其目的主要用来帮助用户导航到具体的工序,操作员可通过点击相应的工序,工序监控面板会同步导航到该工序,以显示该工序的工艺流程;所述生产指标监控与配置子模块用于显示与配置各工序的指标以及对指标配置可视化方案,操作员能够在可视监控组态设计环境模块已配置指标的基础上,根据实际需求过滤出各工序关键指标,并通过配置功能配置各工序关键指标,实现对各工序关键指标的监控;同时对各个指标配置上可视化方案以便进行可视化监控;所述工序监控子模块用于显示工序库中所点击的工序,触发可视监控组态设计环境模块定义该工序的约束条件、工序事件、工序状态,工序点击事件,操作员可通过双击查看子过程的实时状态;同时能监控该工序已配置监控指标的实时数据曲线和历史数据曲线,并显示该工序下各指标已配置的可视化方案,通过可视分析更高效的监控生产指标。所述报警记录子模块用于显示当前时段的报警信息,每条报警记录包括报警时间,报警所在的工序名称,故障设备名称和异常指标名称;在设备名称、指标名称前提供符号提示,红色圆圈表示设备停歇、黄色圆圈表示设备温度过高或消耗原料过量、红色上箭头表示指标超上限、绿色下箭头表示指标超下限。监控结果分析模块用于分析生产指标监控过程的中出现的未被监控到的新的异常和故障,如设备故障、质量指标检验不合格等;同时监控和收集生产指标监控模块中的报警记录,通过逐一分析报警记录信息,追溯设备、指标异常/故障的原因,利用数据探测模块对历史数据进行探测分析并结合机理、专家知识经验重新配置生产指标监控模块中监控指标,从而实现对生产指标监控异常的有效反馈,实现对生产指标监控的动态调整,使得生产指标可视化监控系统具备动态演化能力。一种基于组态的生产指标可视化监控方法,如图2所示,包括以下步骤:步骤1、收集、录入选矿三选厂的基础信息,构建该厂基础信息单元并将其存储至数据库,实现该厂对基础信息的管理。具体包括组织结构基础信息管理、工序流程基础信息管理、设备档案基础信息管理、指标档案基础信息管理、计量单位基础信息管理、物料基础信息管理、人员档案基础信息管理。组织结构基础信息管理是对选矿三选厂的能源、设备、物料、成本等部门之间的层次和职能的管理。工序流程基础信息管理是对选矿三选厂所有工序及各工序子流程的管理,包括悬浮压滤、空气压缩站、悬浮焙烧炉等;设备档案基础信息管理是对选矿三选厂所有设备信息的管理,包括高压辊磨机、压滤机、离心空压机等;指标档案基础信息管理是对选矿三选厂所有指标信息的管理,包括底流泵出口流量、底流泵频率、炉前压滤水分、磁选机作业率等;计量单位基础信息管理是对选矿三选厂所有设备和指标计量单位的管理,包括%、吨、倍、gj、kg/t、h等;物料基础信息管理是对选矿三选厂生产过程涉及的物料信息的管理;人员档案基础信息管理是对选矿三选厂生产过程中工作人员信息的管理;步骤2、使用工厂基础信息模块中的选矿三选厂基础信息管理单元,构建该厂生产流程可视监控组态设计环境,具体方法为:步骤2.1、从图元库中选择悬浮焙烧炉工序的基础图元,点击所选图元将其拖到工艺流程绘制面板;步骤2.2、根据实际选矿三选厂的生产工艺流程绘制组态界面的流程图,并配置悬浮焙烧炉工序的端点、锚点、工序状态等信息;步骤2.3、在工序配置子模块配置悬浮焙烧炉工序的基础信息(字体颜色设置为黑色、字号设置为小四、文字字体设置为宋体)、工序事件(鼠标单击表示进入悬浮焙烧炉的子流程、鼠标双击表示选悬浮焙烧炉工序,对该工序进行指标配置、鼠标悬浮显示悬浮焙烧炉工序的相关备注)、约束条件(规则:给矿量65±10t/h、给矿水12±5m3/h、分益浓度50±5%、排矿水48±8m3/h、磨矿浓度80±2%、旋给浓度50±10%、旋给压力125±35kpa)等属性;步骤2.4、在指标配置子模块配置悬浮焙烧炉工序的指标,并配置指标类型,包括输入指标、输出指标、输入输出指标、被控量和控制量;本实施例中,悬浮焙烧炉工序配置的指标包括:强磁精矿产量、选矿综精sio2、三磁精品位、强磁矿仓、一次一流回收率及弱精品位;步骤2.5、在悬浮焙烧炉工序已有指标类型的基础上,通过选择框添加算法;本实施例中,添加的算法为自回归滑动平均模型(autoregressivemovingaveragemodel,即arma);步骤2.6、点击功能栏子模块的保存按钮,将配置完成的悬浮焙烧炉工序保存至数据库,其名称显示到项目工序子模块的目录中,项目工序子模块显示悬浮焙烧炉工序流程,不同的标识颜色表示目前该工序的设计状态,悬浮焙烧炉工序的标识呈红色表示配置完成;步骤2.7、同时将配置完成的悬浮焙烧炉工序保存至工序库,集中管理已经构建完成的通用基础工序单元,从而提高基础选矿各工序组件的复用性和重用性;步骤2.8、按照步骤2.1至步骤2.7依次配置选矿三选各个工序,包括悬浮压滤、空气压缩站、除盐水站,并通过鼠标绘制各个工序间的有向连线,表示实际选矿三选生产中的流程,将其保存为json格式数据,可将数据保存至数据库或导出为json文件保存至本地。步骤3、在可视监控组态设计环境模块的基础上,应用数据探测模块探测指标数据之间的关系。本实施例中,选取的生产指标数据如表1所示:表1生产指标数据步骤3.1、探测指标间关联关系,包括输入与输入指标之间、输入与输出指标之间、输出与输出指标之间的关系。通过皮尔逊相关系数分析指标间线性关联关系,通过互信息分析指标间非线性相关关系。本实施例中,选取表1中部分生产指标,包括选矿综精产量(湿重)、弱磁精矿产量,综合块矿率、弱精品味、块1#和废石1#矿量。步骤3.1.1、使用皮尔逊相关系数分析指标间线性关联关系,如果分析结果表明指标间线性关系强,则认为指标间存在线性相关性,如果分析结果表明指标间不存在线性关系,转到步骤3.1.2,探测指标间是否存在非线性关系;步骤3.1.2、通过互信息分析指标间非线性相关关系。本实施例中,表1中选取的指标经线性关联关系探测,得出结果如表2所示。选矿综精产量(湿重)与弱磁精矿产量的皮尔逊相关系数为0.926,表示两指标有极强的正相关;综合块矿率与弱磁精矿产量的皮尔逊相关系数为-0.023,表示两指标有较弱的负相关。表2生产指标间的线性关联关系探测结果步骤3.2、探测指标间时序变化关系,通过皮尔逊相关系数分析生产指标之间的延迟相关性,即生产指标之间是否间隔一段采样时间而具有相关性。本实施例中,选取表1部分生产指标,包括选矿综精产量和选矿综精sio2。经延时相关关系探测,选矿综精sio2延时选矿综精产量t时刻的相关系数,探测结果如表3所示。当选矿综精sio2延时t=5时,皮尔逊相关系数为0.54786,选矿综精产量与选矿综精sio2相关性最大。表3生产指标之间的延迟相关性的探测结果t=0t=1t=2t=3t=4t=5t=6t=7t=80.428860.018410.271330.113790.379440.547860.200340.310050.42422步骤3.3、探测指标间的潜变量,通过潜变量代替原始的指标变量,实现对指标的降维。使用主成分分析pca和基于核函数的主成分分析kpca方法分别探测线性指标间潜变量和非线性指标间的潜变量。本实施例中,选取的生产指标包括3-1球磨机电流、3-1旋流器给矿压力、3-1旋流器给矿浓度、3-1旋流器给矿流量、3-1#泵运转频率、3-1球磨排矿水阀门开度、3-1球磨给矿水阀门开度和3-2旋流器给矿压力。生产指标数据如表4所示。通过步骤3.1,得出指标数据间是线性关系,相关系数矩阵如表5所示,进行以下线性指标间潜变量的探测。表4生产指标数据表5相关系数矩阵进行主成分pca分析,得到特征值,从大到小依次为:145.56、21.53、5.44、3.66、1.03、0.67、0.28、-5.41,前两个特征值(145.56+21.53/(145.56+21.53+5.44+3.66+1.03+0.67+0.28-5.41)>0.9),表明该组变量之间线性相关性非常强,可以用前两个特征值(145.56、21.53)对应的主元来代替原始的8个指标,实现对指标的降维。步骤3.4、将经过数据探测模块分析得到的结果通过可视与可视分析模块中的可视化功能以更直观的方式展示出来。步骤4、以可视监控组态设计环境模块已配置的生产指标为基础,借助数据探测模块分析得出的指标间各类关系,利用可视与可视分析模块对指标数据进行可视分析,辅助人们从可视的角度去理解选矿生产指标数据间的关系,具体方法为:步骤4.1、采用图表或实时数据曲线的方式表示实时数据,反应当前生产运行状态是否正常,生产相关指标是否达到预期目的;本实施例中,实时数据选取综合生产指标中的选矿综精产量(湿重);步骤4.2、采用历史数据曲线的方式表示历史数据,并通过时间滑窗的形式灵活的查看不同时间段的历史数据趋势,同时提供交互操作,包括移动、放缩、悬浮提示框、刷新;本实施例中,历史数据选取综合生产指标中的选矿综精产量(湿重),数据时间选择2018-5-1至2018-5-7。步骤4.3、采用平行坐标图表示指标数据对比分析,能够同时展示不同量纲的多维数据;本实施例中,选取指标选矿综精产量(湿重)、综合块矿率、选矿综精水分、选矿综精sio2、测算烧结矿品味和选矿综精cao进行指标数据对比分析。步骤4.3.1、通过平行坐标图显示多个维度的数据,每个坐标轴表示一个维度;步骤4.3.2、选矿综精产量(湿重)、综合块矿率、选矿综精水分、选矿综精sio2、测算烧结矿品味、选矿综精cao各表示一个维度,通过对指标设置不同单位来描述不同数量级的数据;步骤4.3.3、每个维度显示该指标数据的当前值,通过设置上下限,反应该指标当前的运行状态;本实施例中,选矿综精产量(湿重)的指标范围为260t至350t,在2018-4-2019:28指标数据值为355t有超上限报警提示,选矿综精产量(湿重)所在的坐标轴显示为红色;步骤4.3.4、在正常工况下,选矿综精产量(湿重)、综合块矿率、选矿综精水分、选矿综精sio2、测算烧结矿品味、选矿综精cao应均在上下限范围内,平行坐标图的整体轮廓应大致相同,若整体轮廓出现异常形状,表示工况异常,操作员可通过观察图形的整体轮廓,判断生产运行情况;步骤4.4、借助二分图方法,采用桑基图的方式表示生产指标关联关系;步骤4.4.1、在二分图中,将过程指标和运行指标分别看成两个独立的点集,通过两个点集的映射关系表征两个集合中点的关联关系;步骤4.4.2、将二分图中的映射关系平移到桑基图中,左侧颜色条代表过程指标,右侧颜色条代表影响过程指标的运行指标;本实施例中,选取指标:选矿综精cao、选矿综精sio2、测算烧结矿品味、综合块矿率、选矿综精水分为过程指标;选取指标一次溢流回收率、平环尾矿品位、弱尾品位、强精sio2、弱磁精品位为运行指标。步骤4.4.3、通过对左右两侧的颜色条设置不同的颜色来区分不同的指标;左侧各个颜色条流向右侧,表示右侧指标影响左侧指标的因素;步骤4.4.4、根据步骤3筛选出的关键指标以及各个过程指标与运行指标间关系,计算各运行指标对过程指标影响的贡献率,确定图中各个运行指标的比例关系;步骤4.4.5、提供交互操作,当鼠标悬浮于左侧选矿综精sio2所在区域时,单独显示影响该指标的运行指标;本实施例中,弱精品位的贡献率为57%、强精sio2的贡献率为8%、山磁精品位的贡献率为7%、一次溢流回收率的贡献率为7%。步骤4.5、采用多视图交互技术实现选矿生产指标的多视图可视化;本实施例中,涉及的工序包括悬浮压滤、空气压缩站、悬浮焙烧炉、酿造间、悬浮磨选车间等;指标分类包括设备指标、质量指标、工艺指标、成本指标、计量指标、能源指标;步骤4.5.1、将每一个工序对应一个主视图,每一个指标分类对应一个子视图;步骤4.5.2、将指标分类视图嵌入到工序视图中;步骤4.5.3、操作员点击悬浮焙烧炉时能够导航进入该工序,该工序视图通过缩放技术进行放大并显示该工序下已配置指标的实时数据和历史数据,此时其余工序视图通过缩放技术进行缩小,显示为缩略图移到界面最右侧;步骤4.5.4、在悬浮焙烧炉工序中,选择设备指标分类的同时筛选出该工序下已配置指标中的设备指标,该分类视图通过缩放技术进行放大并显示筛选出的设备指标的实时数据和历史数据,此时其余工序视图通过缩放技术进行缩小,显示为缩略图移到子界面的最右侧;步骤5、在生产指标监控模块中配置选矿三选工艺流程监控运行参数,具体方法为:步骤5.1、参考步骤3和步骤4分析得出的选矿生产指标数据间的关系,借助步骤4中各可视化方案所呈现的信息,直观显示选矿生产指标间关联关系和各指标的重要程度,为配置监控指标提供依据;步骤5.2、结合专家知识经验,补充因系统分析不全面所遗漏的指标,配置生产指标监控模块的参数;本实施例中,根据步骤3得出强精sio2对选矿综精sio2的贡献率为8%,但是在步骤2.6并没有配置该指标,在此将强精sio2配置到悬浮焙烧炉工序中;步骤5.3、构建选矿生产指标监控运行环境;步骤5.3.1、通过第二工序库子模块显示选矿三选厂各工序流程,包括各级子流程;步骤5.3.2、点击第二工序库子模块中的悬浮焙烧炉工序,工序监控子模块同步导航到该工序,并显示该工序的工艺流程;选中悬浮焙烧炉工序时,触发可视监控组态设计环境模块定义的该工序的约束条件、工序事件、工序状态,工序点击事件;步骤5.3.3、根据实际需求在生产指标监控与配置子模块中对悬浮焙烧炉工序配置所要监控的关键指标,以及对该工序已配置的指标配置可视化方案;本实施例中,配置的指标为强精sio2、强磁精矿产量、选矿综精sio2、三磁精品位、强磁矿仓、一次一流回收率、弱精品位,配置的可视化方案为实时数据和历史数据可视化方案;步骤5.3.4、通过双击悬浮焙烧炉工序查看子过程的实时状态;能够显示悬浮焙烧炉工序已配置的所有指标,包括强精sio2、强磁精矿产量、选矿综精sio2、三磁精品位、强磁矿仓、一次一流回收率、弱精品位,显示各指标的实时数据曲线、历史数据曲线;同时显示各个可视化方案,便于监控分析已配置指标;步骤5.3.5、通过报警记录子模块显示当前时段的报警信息,每条信息包括故障时间、故障工序名称、故障设备名称、异常指标名称;并分析出设备故障类型和指标异常类型,如设备停歇、指标超上限、指标超下限;本实施例中,报警记录显示在2018-09-22,悬浮压滤工序中1-3-1磁选机设备的#6电流数据在11:38分超指标上限。步骤6、通过监控结果分析模块分析生产指标监控过程的中出现的未处理的异常和故障。步骤6.1、通过监控结果分析模块分析正在监控的工艺流程中未知故障,如设备停歇、指标质量检验不合格等;步骤6.2、监控和收集生产指标监控模块中的报警记录,通过逐一分析报警记录信息,追溯设备、指标异常/故障的原因;步骤6.3、利用数据探测模块对历史数据进行探测分析;步骤6.4、结合机理、专家知识经验重新配置生产指标监控模块中监控指标;步骤6.5、最终实现对生产指标监控异常的有效反馈,实现对生产指标监控的动态调整。最后应说明的是:以上实施例仅用以说明本发明的技术方案,而非对其限制;尽管参照前述实施例对本发明进行了详细的说明,本领域的普通技术人员应当理解:其依然可以对前述实施例所记载的技术方案进行修改,或者对其中部分或者全部技术特征进行等同替换;而这些修改或者替换,并不使相应技术方案的本质脱离本发明权利要求所限定的范围。当前第1页12