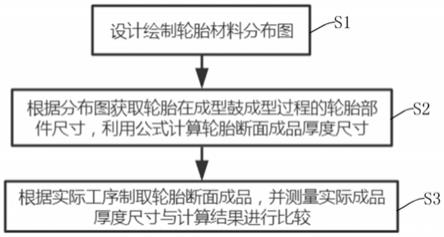
[0001]
本发明涉及轮胎技术领域,特别涉及一种确定轮胎断面成品厚度尺寸的设计方法。
背景技术:[0002]
轮胎制造过程中,准确设计确定轮胎尺寸极为重要。根据轮胎在成型时不同部件材料在不同位置的伸张情况而进行的设计,考虑到钢丝的伸张与帘布伸张因为材料的差异而无法统一设计,故需要分开进行,胎面尺寸因为全部是胶料,可直接根据模具沟深的到成品公式进行设计。
[0003]
现有技术的不足之处在于,目前无法直接得到成品轮胎的断面厚度尺寸,基本上都是根据材料分布图绘制后进行图纸的测量而设计,并没有考虑胶料压缩、材料的拉伸等因素,会导致设计值和实际测量值有较大的差异,给生产带来较大的影响,需要反复修订施工,造成时间和成本的浪费。轮胎断面厚度尺寸设计初始值与实际测量值不能有效的进行应对的问题。
技术实现要素:[0004]
本发明的目的克服现有技术存在的不足,为实现以上目的,采用一种确定轮胎断面成品厚度尺寸的设计方法,以解决上述背景技术中提出的问题。
[0005]
一种确定轮胎断面成品厚度尺寸的设计方法,包括:
[0006]
s1、设计绘制轮胎材料分布图;
[0007]
s2、根据分布图获取轮胎在成型鼓成型过程的轮胎部件尺寸,利用公式计算轮胎断面成品厚度尺寸;
[0008]
s3、根据实际工序制取轮胎断面成品,并测量实际成品厚度尺寸与计算结果进行比较。
[0009]
作为本发明的进一步的方案:所述s2根据分布图获取轮胎在成型鼓成型过程的轮胎部件尺寸,利用公式计算轮胎断面成品厚度尺寸的具体步骤包括:
[0010]
s21、根据获取的轮胎部件尺寸,通过公式计算帘线的伸张值;
[0011]
s22、根据帘线的伸张值的计算结果,利用伸张率公式计算胎体帘布层伸张率以及带束层伸张率;
[0012]
s23、通过上述结果计算胎冠、肩部以及胎侧部位成品厚度。
[0013]
作为本发明的进一步的方案:所述所述帘线的伸张值公式:δ=pi
l
/l=pi
l
/(b
s
+(d
g-d
b
));
[0014]
帘布层伸张率公式:η=(dia+(2*d’*δ)/(1-a))/d
g
;
[0015]
带束层伸张率公式:η’=(dia+(2*d’)/(1-a))/d
g’;
[0016]
其中,δ为帘线的伸张值、η为帘布层伸张率、η’为带束层伸张率、dia为轮胎着合直径、d’为成品所在位置尺寸、a=0.03为胶料压缩率、d
g
为一段成型鼓直径、d
g’为带束层成型鼓直径、pi
l
为帘线内周长、d
b
为钢丝圈内直径、b
s
为一段鼓宽、l为半成品帘布长度。
[0017]
作为本发明的进一步的方案:所述s23通过上述结果计算胎冠、肩部以及胎侧部位成品厚度的具体步骤包括:
[0018]
获取帘布层以及带束层半成品部件厚度,并根据所述胎体帘布层伸张率、带束层伸张率分别计算帘布层成品厚度和带束层成品厚度;
[0019]
获取模具沟深以及沟底基部胶尺寸,并根据帘布层成品厚度和带束层成品厚度计算胎冠及肩部总厚度以及胎侧部位成品厚度。
[0020]
作为本发明的进一步的方案:所述帘布层成品厚度公式:ga=ga0/η;
[0021]
带束层成品厚度公式:ga’=ga0’
/η’;
[0022]
其中,ga为帘布层成品厚度、ga’为带束层成品厚度、ga0为帘布层半成品部件厚度、η为胎体帘布层伸张率、ga0’
为带束层半成品部件厚度、η’为带束层伸张率。
[0023]
作为本发明的进一步的方案:所述胎冠及肩部总厚度公式:ga总=ga+ga’+(gm*0.97+tg);
[0024]
其中,ga总为胎冠及肩部总厚度、ga为帘布层成品部件厚度、gm为模具沟深、tg为沟底基部胶尺寸。
[0025]
作为本发明的进一步的方案:所述胎侧部位成品厚度公式:ga-1
=ga1/η;
[0026]
其中,ga-1
为胎侧部位成品厚度、ga1为半成品部件厚度、η为帘布层伸张率。
[0027]
与现有技术相比,本发明存在以下技术效果:通过采用上述的技术方案,根据一段成型胎体的伸张、二段带束层的伸张、不同高度位置的尺寸,同时根据模具沟深的到成品经验公式计算,然后计算出实际断面的厚度尺寸,可较大幅度降低反复修订施工的频率,有利于生产效率的提升。无需反复修订施工,极大的节约了时间和成本。
附图说明
[0028]
下面结合附图,对本发明的具体实施方式进行详细描述:
[0029]
图1为本发明公开的设计方法的步骤示意图;
[0030]
图2为本发明公开的设计方法的轮胎胎体断面示意图;
[0031]
图3为本发明公开的设计方法的胎体成型时帘线形态示意图;
[0032]
图4为本发明公开的设计方法的帘布层厚度示意图;
[0033]
图5为本发明公开的设计方法的带束层厚度示意图;
[0034]
图6为本发明公开的设计方法的胎冠胶厚度示意图;
[0035]
图7为本发明公开的设计方法的胎冠及肩部总厚度示意图;
[0036]
图8为本发明公开的设计方法的胎侧部位厚度示意图。
具体实施方式
[0037]
下面将结合本发明实施例中的附图,对本发明实施例中的技术方案进行清楚、完整地描述,显然,所描述的实施例仅仅是本发明一部分实施例,而不是全部的实施例。基于本发明中的实施例,本领域普通技术人员在没有做出创造性劳动前提下所获得的所有其他实施例,都属于本发明保护的范围。
[0038]
请参考图1,本发明实施例中,一种确定轮胎断面成品厚度尺寸的设计方法,包括:
[0039]
s1、通过设计绘制轮胎材料分布图。
[0040]
s2、根据分布图获取轮胎在成型鼓成型过程的轮胎部件尺寸,利用公式计算轮胎断面成品厚度尺寸的具体步骤包括:根据获取的轮胎部件尺寸,通过公式计算帘线的伸张值。根据帘线的伸张值计算结果,胎体帘布层伸张率以及带束层伸张率。通过上述结果计算胎冠、肩部以及胎侧部位成品厚度。
[0041]
s3、根据实际工序制取轮胎断面成品,并测量实际成品厚度尺寸与计算结果进行比较。
[0042]
其中,所述轮胎部件尺寸包括帘线内周长pi
l
、一段鼓宽b
s
、钢丝圈内直径d
b
、半成品帘布长度l以及一段成型鼓直径d
g
。
[0043]
具体实施方式:
[0044]
帘线的伸张值δ:
[0045]
请参考图2,图示黑线为轮胎帘线内周长pi
l
。
[0046]
请参考图3,轮胎制造的聚酯材料本身具有一定伸张,在轮胎成型的过程中,特别是胎体伸张的时候,帘线也会受到一定的拉伸,在设计时需要先考虑。帘线的伸张主要是轮胎在成型鼓上时的长度到成品轮胎时的长度变化,为方便计算以及准确度,会以轮胎帘线内周长pi
l
为基数进行。根据轮胎部件尺寸以及帘线的伸张值公式计算帘线的伸张值δ。
[0047]
帘线的伸张值公式:δ=pi
l
/l=pi
l
/(b
s
+(d
g-d
b
));其中,δ为帘线的伸张值。
[0048]
进一步的,利用所述帘线的伸张值δ分别计算胎体帘布层伸张率以及带束层伸张率。
[0049]
胎体帘布层伸张率η:
[0050]
请参考图3,胎体在成型的过程中会因为充气和定型的原因进行一定程度的膨胀和拉伸,这个时候不仅帘线会受到一定的拉伸,胶料同样会受到一定的压缩和拉伸,不同部位的受拉伸程度也不同,因此要加入部件部位定位尺寸。
[0051]
带束层伸张率η’:
[0052]
请参考图4和图5,由于带束层的材料是钢丝,在成型过程中几乎不受拉伸,膨胀变形的主要原因是由于角度的变化导致,因此材料的伸张值为1,认为不做变化,故在公式中去除δ,同时考虑到冠带层是缠绕在带束层上,变化可认可为一致,最终确定为两者保持一致的设计方法。
[0053]
帘布层伸张率公式:η=(dia+(2*d’*δ)/(1-a))/d
g
;
[0054]
带束层伸张率公式:η’=(dia+(2*d’)/(1-a))/d
g’;
[0055]
其中,η为帘布层伸张率、η’为带束层伸张率、dia为轮胎着合直径、d’为成品所在位置尺寸、a=0.03为胶料压缩率、d
g
为一段成型鼓直径、d
g’为带束层成型鼓直径。
[0056]
请参考图6、图7和图8,进一步根据帘布层伸张率、带束层伸张率以及帘布层和带束层半成品部件厚度,计算帘布层成品厚度和带束层成品厚度,最后得出胎冠、肩部以及胎侧部位成品厚度。胎侧部位的厚度计算同冠部帘布层的计算公式相同,不用考虑带束层和冠带层的影响,仅是需要将胎侧胶的半成品厚度加入到总的半成品厚度中即可。
[0057]
帘布层成品厚度公式:ga=ga0/η;
[0058]
带束层成品厚度公式:ga’=ga0’
/η’;
[0059]
其中,ga为帘布层成品厚度、ga’为带束层成品厚度、ga0为帘布层半成品部件厚度、η为胎体帘布层伸张率、ga0’
为带束层半成品部件厚度、η’为带束层伸张率。
[0060]
胎冠及肩部总厚度公式:ga总=ga+ga’+(gm*0.97+tg);
[0061]
其中,ga总为胎冠及肩部总厚度、ga为帘布层成品部件厚度、gm为模具沟深、tg为沟底基部胶尺寸。
[0062]
胎侧部位成品厚度公式:ga-1
=ga1/η;
[0063]
其中,ga-1
为胎侧部位成品厚度、ga1为半成品部件厚度、η为帘布层伸张率。
[0064]
以下为本发明公开的设计方法的工作原理及工作过程:
[0065]
请参考下表,图表为设计方法得到的断面测量结果表。从断面测试结果表可以看出,本发明的设计方法得到的ga更能匹配断面实际的测量值。
[0066]
[0067]
其中,ga总为新设计方法计算值;ga测为实际断面测量值;ga原为原始方法设定值。y为表示与实际断面测量值相符合;n为表示与实际断面测量值不符合。
[0068]
本发明的有益效果:可以不通过多次试做解决轮胎断面厚度尺寸设计初始值与实际测量值不能有效的进行应对的问题,减少资源浪费,提高效率。
[0069]
尽管已经示出和描述了本发明的实施例,对于本领域的普通技术人员而言,可以理解在不脱离本发明的原理和精神的情况下可以对这些实施例进行多种变化、修改、替换和变型,本发明的范围由所附权利要求及其等同物限定,均应包含在本发明的保护范围之内。