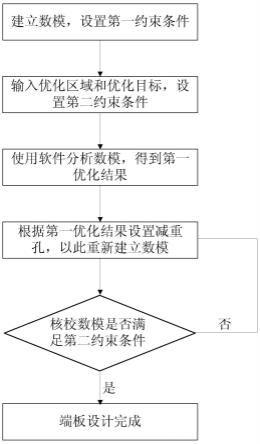
1.本发明涉及新能源汽车技术领域,尤其涉及一种电池模组端板设计方法。
背景技术:2.在新能源汽车领域,汽车的续航能力在产品竞争力中具有非常重要的地位,而降低电池模组端板的重量从而提高电池包的能量密度比则是一个提升汽车续航能力的有效途径。
3.目前主流的电池模组端板在设计时主要的参考指标是端板的结构强度,只要满足端板的强度在电芯循环的寿命到达末期时足够不至于失效、端板的最大变形不会挤压到周边线束部件等条件即可,而不会对端板的轻量化设计作过多要求。因此如何在满足对强度的约束条件下,对端板进行轻量化设计是业内更优选的追求目标。
技术实现要素:4.有鉴于此,本发明提供了一种在满足强度要求的同时进行轻量化设计的电池模组端板设计方法,其包括以下步骤:
5.步骤s1:根据电池模组端板和侧板的数模建立第一仿真分析模型,设置约束电池模组端板和侧板的第一约束条件;
6.步骤s2:输入优化区域及优化目标,设置用于约束优化目标的第二约束条件;
7.步骤s3:根据第一约束条件和第二约束条件,使用分析软件对第一仿真分析模型、优化区域和优化目标进行优化分析,得到第一优化结果;
8.步骤s4:根据第一优化结果在优化区域内设置减重孔,然后在第一仿真分析模型的基础上根据设置的减重孔建立第二仿真分析模型;
9.步骤s5:根据第二约束条件,使用分析软件对第二仿真分析模型进行校核分析,判断第二仿真分析模型是否满足第二约束条件,若第二仿真分析模型满足第二约束条件,则电池模组端板设计完成;若第二仿真分析模型不满足第二约束条件,则返回步骤s4。
10.进一步地,所述步骤s1中的第一约束条件包括约束端板上的螺栓安装孔的六自由度。
11.进一步地,所述步骤s2中的优化区域为端板上除螺栓安装孔周边区域外的其余区域。
12.进一步地,所述步骤s2中的优化目标为寻求优化区域的最小重量。
13.进一步地,所述步骤s2中的第二约束条件包括端板内侧在加载最大膨胀力作用时,其最大mises应力低于端板材料抗拉强度;端板的最大变形量小于设定值。
14.进一步地,所述步骤s3中的第一优化结果包括显示优化区域中适合开设减重孔的区域及权重。
15.进一步地,所述步骤s1中的第一仿真分析模型的控制参数包括材料密度、杨氏模量、泊松比、应力应变曲线和膨胀力等效压力。
16.进一步地,所述步骤s2中的优化目标的控制参数包括优化区域和减重孔的开槽方向。
17.进一步地,所述步骤s3中的优化分析的控制参数包括优化迭代次数和优化终止条件。
18.进一步地,所述步骤s4中的减重孔的控制参数包括减重孔的形状和挤压铝的最低控制宽度。
19.本发明通过建立数模,设定优化区域和优化目标,利用最大膨胀力和最大形变量进行约束,设定迭代优化次数和终止条件,然后设计减重孔形状和挤压铝最低控制宽度,最后校核完成端板设计,为电池模组提高能量密度比提供优化理论支撑,本发明提供了一种在满足对端板强度的约束条件下,对端板进行轻量化设计的端板设计方式,可靠性高且易于实现。
20.上述说明仅是本发明技术方案的概述,为了能够更清楚了解本发明的技术手段,而可依照说明书的内容予以实施,并且为了让本发明的上述和其他目的、特征和优点能够更明显易懂,以下特举较佳实施例,并配合附图,详细说明如下。
附图说明
21.图1为本发明提供的电池模组端板设计方法的示意图。
22.图2为本发明中的第一仿真分析模型的示意图。
23.图3为本发明中的优化区域的示意图。
具体实施方式
24.为更进一步阐述本发明为达成预定发明目的所采取的技术手段及功效,以下结合附图及较佳实施例,对本发明详细说明如下。
25.请参阅图1,本发明的电池模组端板设计方法包括以下步骤:
26.步骤s1:根据电池模组端板和侧板的数模建立第一仿真分析模型,设置约束电池模组端板和侧板的第一约束条件;
27.具体地,请一并参阅图2,由于电池模组的端板和侧板是对称结构,因此建模时只取模型的一半并设置对称边界条件。为达到本发明的设计目的,端板的内侧均布加载最大膨胀力时所对应的压力,该压力在附图1中以箭头的方式示出。第一仿真分析模型的控制参数包括材料密度、杨氏模量、泊松比、应力应变曲线和膨胀力等效压力,第一约束条件包括约束端板上的螺栓安装孔的六自由度,即螺栓安装孔在六个自由度上都不能移动或转动,在附图1中以三角的标注示出。
28.步骤s2:输入优化区域及优化目标,设置用于约束优化目标的第二约束条件;
29.具体地,请一并参阅图3,优化区域为端板上除螺栓安装孔周边区域外的其余区域,优化目标为寻求优化区域的最小重量,以追求电池模组轻量化设计和更高的能量密度比,优化目标的控制参数包括优化区域和减重孔的开槽方向。第二约束条件包括端板内侧在加载最大膨胀力作用时,其最大mises应力低于端板材料抗拉强度,即要求端板强度足够,材料不会失效;端板的最大变形量小于设定值,即要求端板不挤压到周边零部件。
30.步骤s3:根据第一约束条件和第二约束条件,使用分析软件对第一仿真分析模型、
优化区域和优化目标进行优化分析,得到第一优化结果;
31.具体地,优化分析的控制参数包括优化迭代次数和优化终止条件,第一优化结果包括显示优化区域中适合开设减重孔的区域及权重,在本实施例中,采用有限元优化分析软件optistruct进行优化分析,第一优化结果将在该软件上以图示的形式示出,以颜色及颜色的深浅显示优化区域内是否需要设置减重孔以及减重孔的覆盖区域和面积。
32.步骤s4:根据第一优化结果在优化区域内设置减重孔,然后在第一仿真分析模型的基础上根据设置的减重孔建立第二仿真分析模型;
33.具体地,减重孔的控制参数包括减重孔的形状和挤压铝的最低控制宽度,在本实施例中,减重孔的设计需要从工艺层面上进行考量,在得到第一优化结果后,需根据第一优化结果的图示决定在哪些区域进行开孔,同时从工艺角度上对减重孔的形状和角度进行设计,另外,还需要避免其厚度过薄,若其厚度小于挤压铝的最低控制宽度,则即使可以通过软件的分析模拟,在实际生产中也无法对其进行生产。
34.步骤s5:根据第二约束条件,使用分析软件对第二仿真分析模型进行校核分析,判断第二仿真分析模型是否满足第二约束条件,若第二仿真分析模型满足第二约束条件,则电池模组端板设计完成;若第二仿真分析模型不满足第二约束条件,则返回步骤s4。
35.具体地,由于减重孔的形状和位置均为人工参考仿真结果设计,因此还需要对人工设计过减重孔的端板重新建模,建立第二仿真分析模型,导回分析软件根据第二约束条件进行分析核校。若不如此做,则端板可能能够满足轻量化设计,但不能满足最基本的强度要求,也就无法投入使用。若经过核校,第二仿真分析模型满足第二约束条件,则电池模组端板设计完毕;若经过核校,第二仿真分析模型不能满足第二约束条件,则表明端板在满足轻量化设计的前提下未满足强度要求,需返回步骤s4重新设计减重孔,随后再进行核校,直到满足第二约束条件为止。
36.综上,本发明通过建立数模,设定优化区域和优化目标,利用最大膨胀力和最大形变量进行约束,设定迭代优化次数和终止条件,然后设计减重孔形状和挤压铝最低控制宽度,最后校核完成端板设计,为电池模组提高能量密度比提供优化理论支撑,本发明提供了一种在满足对端板强度的约束条件下,对端板进行轻量化设计的端板设计方式,可靠性高且易于实现。
37.以上,仅是本发明的较佳实施例而已,并非对本发明作任何形式上的限制,虽然本发明已以较佳实施例揭露如上,然而并非用以限定本发明,任何熟悉本专业的技术人员,在不脱离本发明技术方案范围内,当可利用上述揭示的技术内容作出些许更动或修饰为等同变化的等效实施例,但凡是未脱离本发明技术方案内容,依据本发明的技术实质对以上实施例所作的任何简单修改、等同变化与修饰,均仍属于本发明技术方案的范围内。