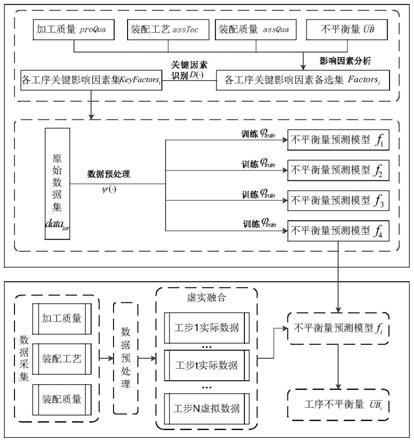
1.本发明属于航空发动机制造领域,涉及一种面向装配过程的低压转子多工序不平衡量预测方法。
背景技术:2.不平衡量是引起低压转子振动的主要原因,严重时会影响到航空发动机的运转可靠性与使用寿命。然而低压转子不平衡量受零件加工质量、装配工艺、装配质量等多因素协同影响,使得其在装配过程中的预测面临影响因素多、互相耦合且作用机理不明确等问题,这导致装配过程中不平衡量难以预测。文献“航空发动机转子同轴度和不平衡量双目标优化装配方法”提出了一种基于神经网络的转子不平衡量预测方法。该方法在根据多级转子结构特点及堆叠装配工艺明确不平衡量的误差源的基础上,建立了基于bp神经网络的多级转子不平衡量预测网络,实现了转子初始不平衡量的识别。但是该方法是在转子装配前对转子不平衡量进行预测,仅仅考虑了零件加工质量和部分装配工艺,忽略了装配过程中各因素对不平衡的影响,预测精确度较低,具有一定的局限性。
3.发明目的
4.为解决目前低压转子初始不平衡量波动大,一次成功率低的问题,本发明提出了面向装配过程的不平衡量半实物仿真模型,主要解决以下两个问题:
5.(1)各工序不平衡量关键影响因素识别。针对各工序初始不平衡量影响因素众多、影响关系黑箱且强耦合的问题,提出基于复杂网络的不平衡量关键影响因素识别方法,采用复杂网络对各工序不平衡量影响因素的关联关系建模,然后基于所建立的关联关系模型采用熵权
‑
topsis模型对其中的关键影响因素进行识别。
6.(2)面向装配过程的不平衡量预测。针对低压转子不平衡量与其关键影响因素复杂耦合以及双向时序作用关系,本发明在对各装配工序不平衡量关键影响因素识别的基础上,构建以双向lstm网络为预测模型的半实物仿真模型,实现装配过程中低压转子各工序不平衡量的预测。
技术实现要素:7.为实现装配过程中对不平衡量的预测,本发明提出了一种面向装配过程的低压转子多工序不平衡量预测模型,通过对低压转子结构和装配工艺分析形成不平衡量关键影响因素备选,然后利用复杂网络构建因素间的关联关系模型对各工序不平衡量的关键影响因素进行识别,以所识别关键影响因素为输入,利用双向lstm构建低压转子不平衡量预测模型对各工序不平衡量进行预测,最后建立低压转子半实物仿真模型实现装配过程中不平衡的预测。由于是在综合考虑了不平衡量形成过程中的各种因素的基础上对关键影响因素进行的识别,并且利用虚实融合的方式解决了装配过程中后序工步未进行所导致的输入数据不完备的问题,因此实现了装配过程中对不平衡量的预测并保证了其预测精度。
8.本发明解决其技术问题所采用的技术方案:一种面向装配过程的低压转子多工序
不平衡量预测方法,其特点是包括以下步骤:
9.步骤一、通过分析低压转子的结构以及装配工艺形成各工序不平衡量关键影响因素备选集,用公式:
10.factors
i
={proqua
i
,asstec
i
,assqua
i
} (1)
11.式中,factors
i
表示第i个工序不平衡量关键影响因素备选集,proqua
i
是第i个工序所涉及到的零件加工质量,asstec
i
是第i个工序所涉及到的装配工艺,assqua
i
是第i个工序所涉及到的装配质量;
12.步骤二、根据工序不平衡量关键影响因素备选集中各影响因素间的相互作用关系利用复杂网络构建影响因素关联关系模型g
i
(factors
i
,e
f
);
13.步骤三、根据关联关系模型g
i
(factors
i
,e
f
)计算各因素的度中心性、聚集系数、介数中心性、接近度中心性、离心度中心性、特征向量中心性、平均邻居度七个因素重要度指标形成属性原始矩阵x。上述各指标计算公式如下:
14.度中心性:
15.聚集系数:
16.介数中心性:
17.接近度中心性:
18.离心度中心性:ec(i)=maxd
ij
(6)
19.特征向量中心性:
20.平均邻居度:
21.步骤四、根据形成属性原始矩阵x进行标准化得到矩阵,然后采用熵权
‑
tiopsis模型计算各因素重要度,并根据重要度变化趋势确定阈值,实现各工序不平衡量关键影响因素识别。
22.各指标的权重计算公式如下式:
[0023][0024]
[0025]
其中,如果p
ij
=0,则定义
[0026]
各因素重要度计算公式如下:
[0027][0028]
其中:
[0029][0030]
步骤五、根据关键影响因素随工步的变化情况分为随工序变化和随工步变化两类的关键影响因素,以工序所包含的工步数为时间步,每一时间步的输入识别出的关键影响因素中由随工序变化和随工步变化两部分组成,构建基于双向lstm的不平衡量预测模型。
[0031]
步骤六、构建以不平衡量预测模型为核心的不平衡量半实物仿真模型。该模型输入是将各工步以虚实结合的方式输入,即将已进行工步的实测数据与未进行的工步的理论数据相结合输入到训练好的网络中即可得到该工序不平衡量的预测值。其输入如下式:
[0032][0033]
其中,x
i
为半实物仿真模型的输入,每一工步的输入是由从加工质量、装配质量、装配工艺识别出关键影响因素组成,x
t
中当前工步前为实测值,之后的为理论值。
[0034]
本发明的有益效果
[0035]
在关键影响因素识别阶段,综合考虑了不平衡量识别过程中所涉及到的各类因素,并且采用了一种客观定量的方法,避免了人为主观因素的影响;在预测模型建立阶段,利用双向lstm在处理双向时序上的优势建立不平衡量预测模型,挖掘了装配过程中的双向时序上的关系,提供了不平衡量预测的准确率;在利用半实物仿真模型预测不平衡量预测模型时,输入采用了虚实结合的方式,解决了装配过程中后序工步未进行导致的输入数据缺失的问题。
附图说明
[0036]
图1实现预测过程
[0037]
图2双向lstm的不平衡量预测模型
[0038]
图3半实物仿真模型
具体实施方式
[0039]
首先分析低压转子的结构特征以及装配工艺,形成了各工序不平衡量关键影响因素的备选集,如下式:
[0040]
盘鼓装配阶段:
[0041]
proqua1=(iub
i pd perp
i as
i atr
i csr
i tsr
i rcy
i rsr
i rph
i rhs
i
)
ꢀꢀꢀ
(14)
[0042]
式中:
[0043]
proqua1——盘鼓装配工序不平衡量加工质量影响因素;
[0044]
iub
i
——第i级盘鼓初始不平衡量;
[0045]
pd——第i级盘鼓上下止口配合端面平行度;
[0046]
prep
i
——第i级盘鼓配合止口处端面相对于旋转轴的端面跳动度;
[0047]
as
i
——第i级盘鼓配合止口处柱面实际尺寸;
[0048]
atr
i
——第i级盘鼓配合止口处柱面全跳动度;
[0049]
csr
i
——第i级盘鼓配合止口处柱面表面粗糙度;
[0050]
tsr
i
——第i级盘鼓配合止口处端面表面粗糙度;
[0051]
rcy
i
——第i级盘鼓配合轴承安装处转轴的圆柱度;
[0052]
rsr
i
——第i级盘鼓配合轴承安装处转轴的表面粗糙度;
[0053]
rhp
i
——第i级盘鼓配合轴承安装处转轴端面的平面度;
[0054]
rhs
i
——第i级盘鼓配合轴承安装处转轴端面的表面粗糙度。
[0055][0056]
式中:
[0057]
asstec1——低压转子不平衡量盘鼓安装工序不平衡量装配工艺影响因素集;
[0058]
iph
i
——第i级盘鼓安装相位;
[0059]
hte
i
——盘鼓加热温度;
[0060]
ete
i
——装配环境温度;
[0061]
——第i级盘鼓装配中第j个螺栓拧紧力矩;
[0062]
——第i级盘鼓装配中第j个螺栓拧紧顺序。
[0063]
assqua1=(raca dca cspl dim)
ꢀꢀꢀ
(16)
[0064]
式中:
[0065]
asstua1——低压转子不平衡量盘鼓安装工序不平衡量装配质量影响因素集;
[0066]
raca——旋转轴的同轴度;
[0067]
dca——盘鼓间的同心度;
[0068]
cspl——盘鼓止口接触面不平行度;
[0069]
dim——盘鼓过盈配合的过盈量。
[0070]
叶片装配阶段:
[0071][0072]
式中:
[0073]
proqua
2,3
——第i级叶片安装工序不平衡量加工质量影响因素;
[0074]
——盘鼓装配完成后形成的不平衡量;
[0075]
——第i级盘鼓第j个叶片重量矩;
[0076]
——第i级盘鼓第j个叶片弯矩;
[0077]
——第i级盘鼓第j个叶片扭矩;
[0078]
——第i级盘鼓第j个叶片实际尺寸;
[0079]
bsr
ij
——第i级盘鼓第j个榫头表面粗糙度;
[0080]
——第i级盘鼓第j个榫头直线度;
[0081]
——第i级盘鼓第j个榫槽实际尺寸;
[0082]
dsr
ij
——第i级盘鼓第j个榫槽表面粗糙度;
[0083]
——第i级盘鼓第j个榫槽直线度。
[0084]
pub
i
——第i级叶片组不平衡量。
[0085][0086]
式中:
[0087]
asstec
2,3
——低压转子不平衡量叶片安装工序不平衡量装配工艺影响因素集;
[0088]
——第i级盘鼓第j个叶片安装顺序;
[0089]
binf
ij
——第i级盘鼓第j个叶片安装力。
[0090][0091]
式中:
[0092]
asstua
2,3
——低压转子不平衡量叶片安装工序不平衡量装配质量影响因素集;
[0093]
pcl
i
——第i级盘鼓第j个叶片的装配间隙。
[0094]
不平衡量校正正阶段:
[0095][0096]
式中:
[0097]
proqua4——低压转子不平衡量校正工序不平衡量加工质量影响因素;
[0098]
——低压转子平衡前的初始不平衡量。
[0099]
asstec4=(bsn bsw
i bsp
i
)
ꢀꢀꢀ
(21)
[0100]
式中:
[0101]
asstec4——低压转子不平衡量校正工序装配工艺影响因素集;
[0102]
bsn——平衡螺钉的数量;
[0103]
bsw
i
——第i个平衡螺钉的质量
[0104]
bsp
i
——第i个平衡螺钉的安装位置。
[0105]
然后根据各因素间的相互作用关系利用复杂网络建立因素间的关联关系模型,并计算各因素在复杂网络里的固有属性,形成固有属性原始矩阵x。
[0106]
根据矩阵x利用熵权
‑
topsis模型计算各因素综合重要度。首先根据矩阵x利用熵权法计算出各属性占综合重要度的权重,同时利用topsis方法计算各因素的属性与理想值的距离,然后根据计算的权重以及与理性值距离计算获得各因素的综合重要度。最后根据重要度的变化趋势获得各工序不平衡量的关键影响因素,部分结果如下表:
[0107]
表1二级叶片装配工序不平衡量关键影响因素重要性排序结果
[0108][0109]
以二级叶片装配为例介绍建立不平衡量预测模型过程。其中盘鼓初始不平衡量、二级叶片组不平衡量为随工序改变的关键影响因素,叶片重量矩、安装位置、装配间隙为随工步改变的影响因素,因此该工序预测模型的输入如下式。此外由于二级叶片有60片,因此该双向lstm网络的时间步为60。然后对该网络进行训练获得不平衡量预测模型。
[0110][0111]
其中ub1代表盘鼓初始不平衡量,ulg2是二级叶片组不平衡量,是二级叶片组不平衡量,分别是叶片重量矩、安装位置、装配间隙。
[0112]
以训练所获得的预测模型为核心构建不平衡量半实物仿真模型。由于参装零件在装配前已经确定,因此装配过程中预测不平衡量时加工质量的数据均为实际值x
pq
;在第t个工步进行时采集相应的装配工艺数据当工步完成后采集装配质量数据形成该工步的输入数据将该工步之前的实际数据与之后的理论数据相融合,形成输入数据x
i
={x1,x2,
…
,x
n
};将融合后的数据输入到所建立的该工序不平衡量预测模型中预测第t个工步完成后该工序的不平衡量
[0113]
本发明综合考虑了不平衡量各类影响影响因素,并利用双向lstm在挖掘双向时序非线性关系的优势来构建半实物仿真模型,最后采用了虚实结合的方式实现了装配过程中不平衡量的预测,能够为低压转子的装配提供一定的指导,提高一次装配成功率。