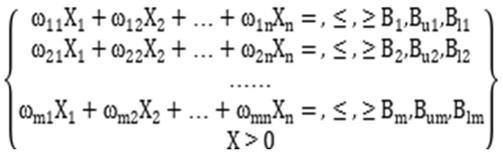
1.本发明涉及钢铁生产技术领域,特别是涉及一种炼钢合金化窄成分控制方法。
背景技术:2.普通的碳钢不能满足抗锈蚀、耐酸、耐磨、耐热等工艺或性能要求,在炼钢过程中,向钢水中投入不同种类的合金元素和剂量,能使钢具有某些特定的优良性能,这个过程即为炼钢的合金化操作,炼钢过程中的合金化操作是钢铁冶炼中的一个非常重要的工序,如何保证在满足钢种窄成分控制的前提下,最大限度地减少所投入合金的费用,降低炼钢合金成分,是钢铁行业降本增效,提高经济效益和市场竞争力的重要途径。
3.炼钢冶炼过程实质上是固(废钢、造渣料及炉衬等)、液(铁水和熔融炉渣)、气(炉气、吹入的氧气)三相组元共同参与的物质与热量传递的过程,影响合金料收得率的因素复杂多变,国内大多数的钢铁企业合金化操作作业中合金料的加入仍然依靠操作工人凭借经验,按照冶炼标准选择合金的种类和加入量,有些钢厂甚至分钢种制定固定的合金种类和计入量,导致合金料加多造成浪费或少加导致钢种成分控制不合格。近年来,随着用户对钢种质量的要求越来越苛刻,传统的人工加入合金调整成分已经越来越难以满足生产和市场的要求。为了解决合金脱料优化控制方面的问题,宝钢从国外引进转炉合金控制模型,但各方面因素限制导致合金模型的的应用效果不是十分理想,如不能计算最小成本的合金投入量,不能由操作工选择不同合金元素参与模型计算,尤其是模型计算没有考虑到合金料市场价格变动的情况。而国内炼钢企业在合金优化加料控制方法或模型投入更少,因此,针对我国钢铁企业开发一项冶炼终点合金优化加料模型显得尤为重要。
技术实现要素:4.本发明针对上述技术问题,克服现有技术的缺点,提供一种炼钢合金化窄成分控制方法,包括:(1)通过生产设备采集多组电路炼钢中与出钢量相关的各项参数信息,所述参数信息包括废钢的重量、废钢成分、铁水成分、铁水重量、终点钢水成分、成品成分、终点温度、出钢量、钢种成分控制中限、各类合金的加入量信息;(2)将所述步骤(1)采集的参数信息作为自变量和应变量,并利用这些数据信息一部分作训练样本,一部分作检验样本;(3)建立三层bp神经网络,利用所述步骤(2)的训练样本输入到三层bp神经网络中,对bp神经网络进行自学习训练,利用所述步骤(2)的检验样本对神经网络的预算结果进行验证,用预测的出钢量与实际的出钢量进行对比,直至预测值与实际值的相对误差足够小或接近为0%,从而确定三层神经网络的隐含层节点个数以及隐含层的权值和阈值;(4)将终点钢水成分、成品成分、终点温度、出钢量、各类合金的加入量信息作为自变量样本,计算相应的合金元素收得率;(5)利用统计原理,对所述步骤(4)的自变量样本和计算得到的合金收得率进行统
计分析,得到各合金元素收得率与终点碳含量、终点温度的拟合方程,用于对合金料中合金元素的收得率进行预算;(6)通过物料平衡原理计算待预测炉次各合金元素的需求量,考虑各合金料市场实时价格,利用最优化原理,预算出不同合金配比的加料模式,以总合金加料成本作为判定依据,从而确定最优的合金加料模式。
5.本发明进一步限定的技术方案是:前所述的一种炼钢合金化窄成分控制方法,采集的参数信息均通过生产erp系统直接获取,采集200-300组参数信息作为数据库。
6.前所述的一种炼钢合金化窄成分控制方法,从数据库中筛选出与出钢量相关的参数,废钢的重量、废钢成分、铁水成分、铁水重量、终点钢水成分、各类合金的加入量作为自变量,出钢量作为应变量,构成bp神经网络的训练样本。
7.前所述的一种炼钢合金化窄成分控制方法,建立三层bp神经网络,包括输入层、隐含层、输出层,其中所述步骤(2)中的自变量构成输入层节点,隐含层节点数通过训练网络获得,出钢量作为输出层。
8.前所述的一种炼钢合金化窄成分控制方法,选取250组数据作为神经网络的训练样本,剩下的50组数据作为检验样本,验证神经网络训练的有效性,训练之初选定隐含层节点数以及各节点连接的权值和阈值;然后将250组训练样本输入到三层神经网络对模型进行训练,得到隐含层节点数和各节点连接的权值和阈值,将50组检验样本的自变量输入神经网络对网络进行验证,将预算得到的出钢量与实际值进行比较,根据预算值与实际值的误差大小重新调整隐含层节点数和各节点连接的权值和阈值;重复进行上述操作,直到预算值与实际值误差足够小或为零,确定此时的隐含层节点数以及各节点连接的权值和阈值大小,得到训练好的满足现场的三层 bp神经网络。
9.前所述的一种炼钢合金化窄成分控制方法,利用统计样本拟合合金元素收得率与终点 钢水温度、终点钢水碳含量,得到合金元素收得率与终点钢水温度、终点钢水碳含量的二次 函数关系:其关系式为:合金元素收得率为:其中,t
终
、c
终
分别为冶 炼终点钢水温度和钢水碳含量;ω[i]
规格中限
为钢种元素i控制中限;ω[i]
终点残余
为终点钢水元素i 含量;x1、x2、xn分别为合金料x1、x2、xn加入量;ω
in
为合金料xn中元素i的含量;q
出钢量 为出钢量。
[0010]
前所述的一种炼钢合金化窄成分控制方法,合金料的加入对出钢量产生影响,因此需 对合金i的需求量进行调整,调整为: 合金元素i需求量其中δq为钢水增重, 元素i整量。
[0011]
前所述的一种炼钢合金化窄成分控制方法,利用最优化原理进行炼钢过程中各限制条 件下最优成本时各合金料的加入量,该问题可描述为:求:
其中:z为加入合金料总成本,cj为第j种合金单价;ω
ij
为第j种合金中第i种元素的含量; bi为钢种第i种元素需求量;b
ui
为钢种第i中元素需求量上限值;为钢种第i中元素需求量 下限值。
[0012]
前所述的一种炼钢合金化窄成分控制方法,采用计算机编译语言visual basic对最优化合金加料模型的计算逻辑以及原始参数设定进行计算机编程,形成便捷用户界面,运用到现场。
[0013]
本发明的有益效果是:(1)本发明运用了bp神经网络算法预算出钢量,通过统计分析原理拟合合金元素收得率与终点碳含量、终点温度的方程,从而从物料平衡角度建立了钢水合金化最后加料预测模型,采用精确采集炼钢冶炼过程相关生产数据作为变量,以实现最优化的炼钢窄成分控制,提高炼钢生产效率和产品质量的目的;(2)本发明具有出钢量和合金收得率预报能力,利用三层神经网络在线对出钢量进行精准预测,大量统计数据样本对各合金元素收得率进行预测;(3)本发明可以方便地对各参数进行人工地设定,如各元素目标、上下限成分、成品成分、收得率、合金设定投入量等;(4)本发明可实时变化加料模式,无论合金料市场价格变动,始终保证合金加料成本最优;(5)本发明由于合金采购价格随市场波动情况较大,具体经济效益需根据当日市场合金价格通过模型计算得到。
附图说明
[0014]
图1为本发明中电炉炼钢窄成分控制的流程图;图2为本发明中出钢量bp神经网络训练学习流程示意图。
具体实施方式
[0015]
实施例1本实施例提供的一种炼钢合金化窄成分控制方法,如图1,包括以下步骤:(1)通过生产设备采集多组电路炼钢中与出钢量相关的各项参数信息,所述参数信息包括废 钢的重量、废钢成分、铁水成分、铁水重量、终点钢水成分、成品成分、终点温度、出钢量、 钢种成分控制中限、各类合金的加入量信息;采集的参数信息均通过生产erp系统直接获取, 采集300组参数信息作为数据库,因炼钢冶炼数据采集存在误差,选取的数据过少,不具有 代表性,不利于神经网络训练的误差稳定,相反,选取的数据过多也会影响网络训练的效率;(2)从数据库中筛选出与出钢量相关的参数,废钢的重量、废钢成分、铁水成分、铁水重量、 终点钢水成分、各类合金的加入量作为自变量,出钢量作为应变量,构成bp神经网
络的训练 样本;(3)建立三层bp神经网络,如图2,包括输入层、隐含层、输出层,其中步骤(2)中的自 变量构成输入层节点,隐含层节点数通过训练网络获得,出钢量作为输出层,选取250组数 据作为神经网络的训练样本,剩下的50组数据作为检验样本,验证神经网络训练的有效性, 训练之初选定隐含层节点数以及各节点连接的权值和阈值;然后将250组训练样本输入到三层神经网络对模型进行训练,得到隐含层节点数和各节点连 接的权值和阈值,将50组检验样本的自变量输入神经网络对网络进行验证,将预算得到的出 钢量与实际值进行比较,根据预算值与实际值的误差大小重新调整隐含层节点数和各节点连 接的权值和阈值;重复进行上述操作,直到预算值与实际值误差足够小或为零,确定此时的隐含层节点数以及 各节点连接的权值和阈值大小,得到训练好的满足现场的三层bp神经网络;(4)将终点钢水成分、成品成分、终点温度、出钢量、各类合金的加入量信息作为自变量样 本,计算相应的合金元素收得率,(5)利用统计原理,对步骤(4)的自变量样本和计算得到的合金收得率进行统计分析,得 到各合金元素收得率与终点碳含量、终点温度的拟合方程,用于对合金料中合金元素的收得 率进行预算;影响合金元素收得率的因素有很多,出钢是否下渣、钢水的氧化性、钢水终点温度、挡渣机 故障,是否下渣、钢水终点碳、锰含量以及合金工责任心等主观客观因素均会影响到合金料 的收得率,而最主要的影响因素就是钢水氧化性和钢水终点温度,合金元素收得率与终点钢 水温度、终点钢水碳含量的二次函数关系:其关系式为:合金元素收得率为:其中,t
终
、c
终
分别为冶 炼终点钢水温度和钢水碳含量;ω[i]
规格中限
为钢种元素i控制中限;ω[i]
终点残余
为终点钢水元素i 含量;x1、x2、xn分别为合金料x1、x2、xn加入量;ω
in
为合金料xn中元素i的含量;q
出钢量 为出钢量;:合金料的加入对出钢量产生影响,因此需对合金i的需求量进行调整,调整为: 合金元素i需求量其中δq为钢水增重, 元素i整量(如自然脱碳量);(6)通过物料平衡原理计算待预测炉次各合金元素的需求量,考虑各合金料市场实时价格, 利用最优化原理,预算出不同合金配比的加料模式,以总合金加料成本作为判定依据,从而 确定最优的合金加料模式, 利用最优化原理进行炼钢过程中各限制条件下最优成本时各合金料的加入量,该问题可描述 为:求:为:求:其中:z为加入合金料总成本,cj为第j种合金单价;ω
ij
为第j种合金中第i种元素
的含量; bi为钢种第i种元素需求量;b
ui
为钢种第i中元素需求量上限值;为钢种第i中元素需求量 下限值;采用计算机编译语言visual basic对最优化合金加料模型的计算逻辑以及原始参数设定(合金 料成分,合金料市场价格等)进行计算机编程,形成便捷用户界面,运用到现场。
[0016]
原始炉次信息:炉号1321263,铁水重98t、废钢重16.4t、渣钢3t、铁水成分c:4.86、si:0.42、mn:0.112。
[0017]
成品控制要求:c:0.22%-0.25%、s≤0.8%、mn:0.45%-0.55%。
[0018]
过程加料信息:烧结矿720kg、石灰3000kg、白云石3900kg。
[0019]
出钢量预结果:104.2t;实际出钢量:103.2t,预算相对误差0.97%。
[0020]
合金元素收得率预算:mn:92.3%、si:91.2%、c:82.5%。
[0021]
合金料加入量预算:硅锰673.4kg、硅铁193.8kg、碳粉133.8kg,合金成本预算吨钢43.1元/吨。
[0022]
成品成分:c:0.23%、s≤0.23%、mn:0.52%,最大相对误差4%。
[0023]
实施例2原始炉次信息:炉号1321375,铁水重101t、废钢重15.6t、渣钢3t、铁水成分c:4.23、si:0.44、mn:0.12。
[0024]
成品控制要求:c:0.22%-0.25%、s≤0.8%、mn:1.25%-1.35%。
[0025]
过程加料信息:烧结矿1600kg、石灰3400kg、白云石3100kg、镁球300kg。
[0026]
出钢量预结果:107.0t;实际出钢量:107.3t,预算相对误差0.28%。
[0027]
合金元素收得率预算:mn:91.2%、si:90.8%、c:80.5%。
[0028]
合金料加入量预算:硅锰2124.8kg、硅铁153.2kg、碳粉249.3kg,合金成本预算吨钢110.4元/吨。成品成分:c:0.23%、si≤0.4%、mn:1.25%,最大相对误差3.8%。
[0029]
除上述实施例外,本发明还可以有其他实施方式。凡采用等同替换或等效变换形成的技术方案,均落在本发明要求的保护范围。