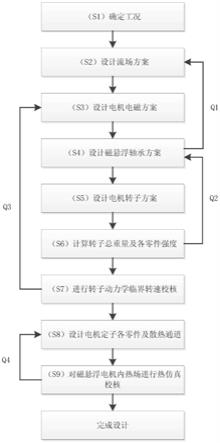
1.本发明涉及鼓风机领域,尤其涉及一种磁悬浮电机直驱离心鼓风机的设计方法。
背景技术:2.鼓风机是一种输送气体的机械设备,随着鼓风机技术的发展,基于磁悬浮技术的离心鼓风机应运而生,磁悬浮鼓风机采用磁悬浮轴承,无接触损失和机械损失,实现了高转速无级变转速调节,风机运行效率高;同时,机器采用高速永磁电机直接驱动,高效三元流叶轮直接安装在高速电动机的主轴上,整套设备集永磁同步直流电机、电驱磁悬浮轴承、高速变频、电磁滤波闭式冷却循环和自动控制一体化技术于一体,设备在运行中无任何摩擦;基于磁悬浮技术的离心鼓风机的节能、高效等性能特点,具有更好的应用前景。
3.中国发明专利申请(公开号cn110569524a,公开日:20191213)公开了一种空气悬浮高速直联鼓风机的设计方法,与现有根据经验选择设计方案比较,新方法可缩短整机设计的周期,有效避免设计过程中存在的风险,并能统筹迭代各个关键零部件涉及的高效叶轮三元流、高效高速大功率永磁电机、高速转子动力学、流固热耦合、空气动力学、箔片空气轴承弹性力学、过盈连接接触强度/刚度等技术问题,使整机产品性能、结构方面达到最优方案。
4.现有技术存在以下不足:传统的鼓风机主要依据设计人员的经验进行初始设计,而后辅以实验修正来完成最终设计;而此种方式中,对设计人员的经验提了很高的要求;同时,鼓风机设计过程中涉及到高速转子动力学和空气动力学等复杂技术,仅根据经验选择的方案不能获知鼓风机内部流场和热场等细节以进一步提高产品性能,很难达到最优解;从而容易造成产品设计周期长、鼓风效率低和振动大等问题,降低了鼓风机的性能。
技术实现要素:5.本发明的目的是:针对上述问题,提出通过按照确定流程来对鼓风机进行设计,从而避免依靠设计人员的经验,缩短了产品设计周期;同时,在设计过程中对鼓风机的内部流场和热场等细节进行精细分析并且对重要参数进行校核,从而进一步提高产品性能的一种磁悬浮电机直驱离心鼓风机的设计方法。
6.为了实现上述的目的,本发明采用了以下的技术方案:一种磁悬浮电机直驱离心鼓风机的设计方法,该方法包括以下的步骤:(s1)确定工况:确定鼓风机的出口压力、入口流量、入口温度、环境温度、湿度和工况气体属性;(s2)设计流场方案:根据鼓风机的工况,通过流体设计软件设计出流场方案,进而确定三元流离心叶轮、蜗壳和密封的结构及尺寸,以及叶轮输出功率、额定转速、最高转速、轴向力和叶轮预紧力;(s3)设计电机电磁方案:根据叶轮输出功率、额定转速和最高转速,通过电磁设计软件设计出永磁同步高速电机电磁方案;进而确定定转子硅钢片结构、定子绕组线圈排布
方式、转子磁钢材料和尺寸、电磁效率和各处损耗;(s4)设计磁悬浮轴承方案:设计出径向磁轴承定子硅钢片结构、径向磁轴承定子绕组线圈排布、径向磁轴承转子组件、轴向磁轴承定子结构、轴向磁轴承定子绕组线圈排布和推力盘结构,并计算径向磁轴承承载力和轴向磁轴承承载力;当轴向磁轴承承载力符合要求时,执行步骤(s5);否则执行步骤(s2),重新设计流场方案;(s5)设计电机转子方案:确定出电机轴结构、转子护套结构、隔磁环结构、各磁轴承和各零件间的公差;(s6)计算转子总重量及各零件强度;当转子总重量不大于径向磁轴承承载力并且各零件强度符合要求时,执行步骤(s7);否则执行步骤(s4),重新设计磁悬浮轴承方案;(s7)进行转子动力学临界转速校核;当转子动力学临界转速符合要求时,执行步骤(s8);否则执行步骤(s3),重新设计电机电磁方案;(s8)设计电机定子各零件及散热通道,包括机壳、各轴承座和连接法兰;(s9)对磁悬浮电机内热场进行热仿真校核;当电机内热场符合要求时,完成磁悬浮电机直驱离心鼓风机的设计过程;否则执行步骤(s8),重新设计电机定子各零件及散热通道。
7.作为优选,步骤(s2)设计流场方案包括:(s21)三元流离心叶轮与蜗壳的流道型线以鼓风机工况为依据,由计算流体力学软件计算得出,同时计算流体力学软件计算出叶轮输出轴功率、额定转速与最高转速;(s22)在设计出三元流离心叶轮结构后,对三元流离心叶轮选材并通过有限元分析软件对三元流离心叶轮固有频率进行计算以及对其在最高转速下进行应力分析;(s23)通过设计三元流离心叶轮背部高压区的密封结构改变流场泄漏量,同时通过改变密封在叶轮背部高压区的径向位置改变叶轮的轴向力;叶轮的预紧力通过电机对叶轮传递的扭矩计算得出,轴、叶轮的材料和轴向力皆可影响叶轮预紧力大小,并且叶轮与轴紧固的螺纹与叶轮旋转方向相反。
8.作为优选,步骤(s3)设计电机电磁方案包括:(s31)以叶轮输出功率、额定转速和最高转速所绘制的扭矩-转速曲线和功率-转速曲线为依据,由电磁设计软件计算得出基本定转子参数;(s32)根据软件计算结果设计定转子硅钢片结构、定子绕组线圈和转子磁钢材料和尺寸,然后返回软件校核;其中电磁效率及各处损耗需明确,用于为后面结构设计中的散热通道设计提供数据目标。
9.作为优选,步骤(s4)中设计磁悬浮轴承方案包括:(s41)根据步骤(s2)和(s3)中已得出的转子部分的重量乘以经验系数估算整个转子重量,再乘以安全系数确定径向磁轴承所需承载力;(s42)然后设计径向磁轴承定转子硅钢片结构及绕组线圈,并确定径向磁轴承的定转子间隙、长度、绕组线圈匝数和电流大小,最后计算此径向磁轴承承载力;(s43)根据步骤(s1)中的轴向力乘以安全系数计算轴向磁轴承所需承载力;然后设计轴向磁轴承定子硅钢片结构及、推力盘结构和绕组线圈,并确定轴向磁轴承的定子与推力盘间隙、面积、绕组线圈匝数和电流大小,最后计算此径向磁轴承承载力;其中轴承承载力大小与定转子间面积成正比、与间隙成二次方反比、与绕组线圈成二次方正比、与电流
成二次方正比,但以上规律在绕组线圈非磁饱和区内有效。
10.作为优选,执行步骤(s5)时,根据步骤(s2)、(s3)和(s4)得出的结构,设计转子上各零件的结构尺寸及公差,其中公差设计中的过盈量需要通过计算各零件在热场离心力作用下变形量及需要传递的扭矩和摩擦力确定。
11.作为优选,步骤(s6)中计算各零件强度时,需要对转子上所有零件在最高转速下进行应力分析;圆环零件可经过公式计算得出,不规则零件可通过有限元分析软件计算得出;其中,温度对材料力学性能的影响及过盈量对零件的内应力影响需要包含在计算中。
12.作为优选,执行步骤(s7)时,转子动力学临界转速的计算用于判断整个转子系统能否在全工作转速下安全稳定运行;一般有两种方式计算,第一种是传递矩阵计算,通过输出转子上所有材料的属性及转速,通过传递矩阵计算出临界转速;第二种是有限元分析法,通过有限元分析软件仿真计算转子动力学临界转速。
13.作为优选,对两种方式计算得出的临界转速结果计算平均数,再乘以经验振动区值和安全系数,得到最终的临界转速,并且得出的临界转速需不小于鼓风机的最高转速。
14.作为优选,步骤(s9)对磁悬浮电机内热场进行热仿真校核包括:(s91)用三维设计软件对电机结构建模;(s92)通过有限元分析软件中的热仿真模块对模型进行分析计算得出热场各处温度,并且得出的热场各处温度乘以安全系数后需要低于该温度区域材料最高许用温度。
15.本发明采用上述技术方案的一种磁悬浮电机直驱离心鼓风机的设计方法的优点是:通过按照确定流程来对鼓风机进行设计使得鼓风机在设计过程中有章可循,从而避免了需要依靠设计人员的经验进行设计的情况,缩短了产品设计周期;同时,在设计过程中利用相应的软件对鼓风机的内部流场和热场等细节进行精细分析模拟并且对重要参数进行校核,从而保证能够对鼓风机的内部零件进行精细化设计,以使得整机产品性能和结构方面达到最优方案。
附图说明
16.图1为本方法的流程图。
17.q1
‑ꢀ
轴向磁轴承承载力不符合要求、q2-转子总重量大于径向磁轴承承载力或者各零件强度不符合要求、q3-转子动力学临界转速不符合要求、q4-电机内热场不符合要求。
具体实施方式
18.下面结合附图对本发明的具体实施方式进行详细的说明。
19.实施例1一种磁悬浮电机直驱离心鼓风机的设计方法,该方法包括以下的步骤:(s1)确定工况:确定鼓风机的出口压力、入口流量、入口温度、环境温度、湿度和工况气体属性;(s2)设计流场方案:根据鼓风机的工况,通过流体设计软件设计出流场方案,进而确定三元流离心叶轮、蜗壳和密封的结构及尺寸,以及叶轮输出功率、额定转速、最高转速、轴向力和叶轮预紧力;
(s3)设计电机电磁方案:根据叶轮输出功率、额定转速和最高转速,通过电磁设计软件设计出永磁同步高速电机电磁方案;进而确定定转子硅钢片结构、定子绕组线圈排布方式、转子磁钢材料和尺寸、电磁效率和各处损耗;(s4)设计磁悬浮轴承方案:设计出径向磁轴承定子硅钢片结构、径向磁轴承定子绕组线圈排布、径向磁轴承转子组件、轴向磁轴承定子结构、轴向磁轴承定子绕组线圈排布和推力盘结构,并计算径向磁轴承承载力和轴向磁轴承承载力;当轴向磁轴承承载力符合要求时,执行步骤(s5);否则执行步骤(s2),重新设计流场方案;(s5)设计电机转子方案:确定出电机轴结构、转子护套结构、隔磁环结构、各磁轴承和各零件间的公差;(s6)计算转子总重量及各零件强度;当转子总重量不大于径向磁轴承承载力并且各零件强度符合要求时,执行步骤(s7);否则执行步骤(s4),重新设计磁悬浮轴承方案;(s7)进行转子动力学临界转速校核;当转子动力学临界转速符合要求时,执行步骤(s8);否则执行步骤(s3),重新设计电机电磁方案;(s8)设计电机定子各零件及散热通道,包括机壳、各轴承座和连接法兰;(s9)对磁悬浮电机内热场进行热仿真校核;当电机内热场符合要求时,完成磁悬浮电机直驱离心鼓风机的设计过程;否则执行步骤(s8),重新设计电机定子各零件及散热通道。
20.此种方式中,通过按照确定流程来对鼓风机进行设计使得鼓风机在设计过程中有章可循,从而避免了需要依靠设计人员的经验进行设计的情况,缩短了产品设计周期;同时,在设计过程中利用相应的软件对鼓风机的内部流场和热场等细节进行精细分析模拟并且对重要参数进行校核,从而保证能够对鼓风机的内部零件进行精细化设计,以使得整机产品性能和结构方面达到最优方案。
21.步骤(s2)设计流场方案包括:(s21)三元流离心叶轮与蜗壳的流道型线以鼓风机工况为依据,由计算流体力学软件计算得出,同时计算流体力学软件计算出叶轮输出轴功率、额定转速与最高转速;(s22)在设计出三元流离心叶轮结构后,对三元流离心叶轮选材并通过有限元分析软件对三元流离心叶轮固有频率进行计算以及对其在最高转速下进行应力分析;(s23)通过设计三元流离心叶轮背部高压区的密封结构改变流场泄漏量,同时通过改变密封在叶轮背部高压区的径向位置改变叶轮的轴向力;叶轮的预紧力通过电机对叶轮传递的扭矩计算得出,轴、叶轮的材料和轴向力皆可影响叶轮预紧力大小,并且叶轮与轴紧固的螺纹与叶轮旋转方向相反。
22.步骤(s3)设计电机电磁方案包括:(s31)以叶轮输出功率、额定转速和最高转速所绘制的扭矩-转速曲线和功率-转速曲线为依据,由电磁设计软件计算得出基本定转子参数;(s32)根据软件计算结果设计定转子硅钢片结构、定子绕组线圈和转子磁钢材料和尺寸,然后返回软件校核;其中电磁效率及各处损耗需明确,用于为后面结构设计中的散热通道设计提供数据目标。
23.步骤(s4)中设计磁悬浮轴承方案包括:(s41)根据步骤(s2)和(s3)中已得出的转子部分的重量乘以经验系数估算整个转
子重量,再乘以安全系数确定径向磁轴承所需承载力;(s42)然后设计径向磁轴承定转子硅钢片结构及绕组线圈,并确定径向磁轴承的定转子间隙、长度、绕组线圈匝数和电流大小,最后计算此径向磁轴承承载力;(s43)根据步骤(s1)中的轴向力乘以安全系数计算轴向磁轴承所需承载力;然后设计轴向磁轴承定子硅钢片结构及、推力盘结构和绕组线圈,并确定轴向磁轴承的定子与推力盘间隙、面积、绕组线圈匝数和电流大小,最后计算此径向磁轴承承载力;其中轴承承载力大小与定转子间面积成正比、与间隙成二次方反比、与绕组线圈成二次方正比、与电流成二次方正比,但以上规律在绕组线圈非磁饱和区内有效。
24.执行步骤(s5)时,根据步骤(s2)、(s3)和(s4)得出的结构,设计转子上各零件的结构尺寸及公差,其中公差设计中的过盈量需要通过计算各零件在热场离心力作用下变形量及需要传递的扭矩和摩擦力确定。
25.步骤(s6)中计算各零件强度时,需要对转子上所有零件在最高转速下进行应力分析;圆环零件可经过公式计算得出,不规则零件可通过有限元分析软件计算得出;其中,温度对材料力学性能的影响及过盈量对零件的内应力影响需要包含在计算中。
26.执行步骤(s7)时,转子动力学临界转速的计算用于判断整个转子系统能否在全工作转速下安全稳定运行;一般有两种方式计算,第一种是传递矩阵计算,通过输出转子上所有材料的属性及转速,通过传递矩阵计算出临界转速;第二种是有限元分析法,通过有限元分析软件仿真计算转子动力学临界转速。对两种方式计算得出的临界转速结果计算平均数,再乘以经验振动区值和安全系数,得到最终的临界转速,并且得出的临界转速需不小于鼓风机的最高转速。其中,径向磁轴承的跨距、叶轮重心到最近径向磁轴承的悬臂长度,叶轮的重量和转动惯量,轴承刚度都对临界转速有很大影响。转子各零件间内应力,轴向力等对临界转速有少量影响。
27.步骤(s8)中,设计的电机定子各零件和散热通道时需要满足定子各零件需方便拆卸,连接牢固,方便加工等要求,散热通道用于将电机定转子的热量带走。
28.步骤(s9)对磁悬浮电机内热场进行热仿真校核包括:(s91)用三维设计软件对电机结构建模;(s92)通过有限元分析软件中的热仿真模块对模型进行分析计算得出热场各处温度,并且得出的热场各处温度乘以安全系数后需要低于该温度区域材料最高许用温度。