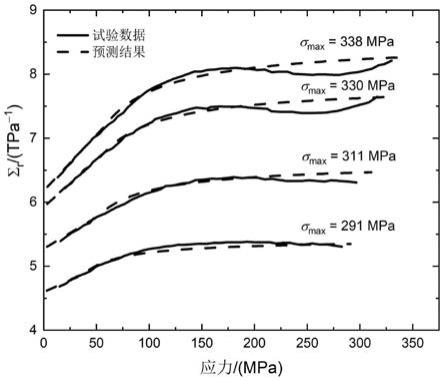
1.本发明涉及复合材料疲劳损伤预测技术领域,尤其涉及一种通过切线模量预测纤维增强陶瓷基复合材料疲劳损伤的方法。
背景技术:2.纤维增强陶瓷基复合材料具有耐高温、耐腐蚀、低密度、高比强以及高比模等优点,相比高温合金,纤维增强陶瓷基复合材料能够承受更高的温度,减少冷却气流,提高涡轮效率,目前已经应用于航空发动机燃烧室、涡轮导向叶片、涡轮壳环以及尾喷管等。
3.为了保证纤维增强陶瓷基复合材料在飞机和航空发动机结构中使用的可靠性与安全性,国内外研究人员将纤维增强陶瓷基复合材料性能评估、损伤演化、强度与寿命预测工具的开发作为纤维增强陶瓷基复合材料结构部件适航取证的关键。为了确保纤维增强陶瓷基复合材料结构使用过程中的可靠性与安全性,需要对其疲劳损伤及耐久性开展深入的研究,目前尚未建立通过切线模量预测纤维增强陶瓷基复合材料疲劳损伤的方法。
技术实现要素:4.本发明的目的在于提供一种通过切线模量预测纤维增强陶瓷基复合材料疲劳损伤的方法,本发明提供的方法通过切线模量能够准确预测纤维增强陶瓷基复合材料疲劳损伤。
5.为了实现上述发明目的,本发明提供以下技术方案:
6.本发明提供了一种通过切线模量预测纤维增强陶瓷基复合材料疲劳损伤的方法,包括以下步骤:
7.(1)根据基体随机碎断模型确定基体裂纹间距;
8.(2)根据总体载荷承担准则,得到卸载和重新加载过程中在峰值应力处的完好纤维承担载荷;
9.根据断裂力学界面脱粘准则,利用所述卸载和重新加载过程中在峰值应力处的完好纤维承担载荷,得到界面脱粘长度、卸载界面反向滑移长度和重新加载新界面滑移长度;
10.(3)根据卸载与重新加载过程的纤维滑移机理,利用所述步骤(1)中基体裂纹间距以及步骤(2)中卸载和重新加载过程中在峰值应力处的完好纤维承担载荷、界面脱粘长度、卸载界面反向滑移长度和重新加载新界面滑移长度,得到卸载和重新加载过程中纤维增强陶瓷基复合材料的应力-应变关系方程;
11.(4)根据所述步骤(3)中卸载和重新加载过程中纤维增强陶瓷基复合材料的应力-应变关系方程,得到卸载和重新加载过程中纤维增强陶瓷基复合材料的切线模量,以此预测纤维增强陶瓷基复合材料疲劳损伤;
12.所述步骤(1)与步骤(2)无时间顺序限定。
13.优选地,所述步骤(1)中基体裂纹间距如式1所示:
[0014][0015]
其中,lc为基体裂纹间距,l
sat
为饱和基体裂纹间距,σm为基体轴向应力,σr为基体开裂特征应力,m为基体威布尔模量。
[0016]
优选地,所述步骤(2)中卸载和重新加载过程中在峰值应力处的完好纤维承担载荷根据式2得到:
[0017][0018]
其中,σ
max
为疲劳峰值应力,vf为纤维体积含量,φ为完好纤维承担载荷,σ
fc
为纤维特征强度,mf为纤维威布尔模量。
[0019]
优选地,所述步骤(2)中界面脱粘长度如式3所示:
[0020][0021]
其中,ld为界面脱粘长度,rf为纤维半径,vm为基体体积含量,ef为纤维弹性模量,em为基体弹性模量,ec为复合材料弹性模量,ρ为剪滞模型参数,τi为界面剪应力,γi为界面脱粘能,σ为名义应力。
[0022]
优选地,所述步骤(2)中卸载界面反向滑移长度如式4所示:
[0023][0024]
其中,ly为卸载界面反向滑移长度,φu为卸载完好纤维承担应力,σu为卸载应力。
[0025]
优选地,所述步骤(2)中重新加载新界面滑移长度如式5所示:
[0026][0027]
其中,lz为重新加载新界面滑移长度,φr为重新加载完好纤维承担应力,σr为重新加载应力。
[0028]
优选地,所述步骤(3)中卸载过程中纤维增强陶瓷基复合材料的应力-应变关系方程如式6所示:
[0029][0030]
其中,ε
unloading
为卸载应变,lc为基体裂纹间距,αc为复合材料热膨胀系数,αf为纤维热膨胀系数,δt为测试温度与制备温度差值。
[0031]
优选地,所述步骤(3)中重新加载过程中纤维增强陶瓷基复合材料的应力-应变关系方程如式7所示:
[0032][0033]
其中,ε
reloading
为重新加载应变。
[0034]
优选地,所述步骤(4)中卸载过程中纤维增强陶瓷基复合材料的切线模量如式8所示:
[0035][0036]
其中,所述σu为卸载切线模量,δεu为卸载应变差;
[0037]
所述δεu由式9确定:
[0038][0039]
优选地,所述步骤(4)中重新加载过程中纤维增强陶瓷基复合材料的切线模量如式10所示:
[0040][0041]
其中,所述σr为重新加载切线模量,δεr为重新加载应变差;
[0042]
所述δεr由式11确定:
[0043][0044]
其中,σ
min
为疲劳谷值应力。
[0045]
本发明提供了一种通过切线模量预测纤维增强陶瓷基复合材料疲劳损伤的方法,具体是根据总体载荷承担准则,得到卸载和重新加载过程中在峰值应力处的完好纤维承担载荷,基于此根据断裂力学界面脱粘准则得到界面脱粘长度和滑移长度(包括卸载界面反向滑移长度和重新加载新界面滑移长度),同时根据基体随机碎断模型确定基体裂纹间距,在此基础上获得卸载和重新加载过程中纤维增强陶瓷基复合材料的应力-应变关系方程,进而得到卸载和重新加载过程中纤维增强陶瓷基复合材料的切线模量,以此预测纤维增强陶瓷基复合材料疲劳损伤。本发明提供的方法通过切线模量能够准确预测纤维增强陶瓷基复合材料疲劳损伤。
附图说明
[0046]
图1为本发明中试验与理论预测的纤维增强陶瓷基复合材料迟滞回线对比图;
[0047]
图2为本发明中试验与理论预测的纤维增强陶瓷基复合材料切线模量对比图。
具体实施方式
[0048]
本发明提供的通过切线模量预测纤维增强陶瓷基复合材料疲劳损伤的方法中涉及的各项符号、含义及其获取方法汇总于表1中,以下具体实施方式中,除特殊说明外,各个方程或者关系式中的符号含义、获取方法均以表1的内容为准,不再一一赘述。
[0049]
表1通过切线模量预测纤维增强陶瓷基复合材料疲劳损伤的方法中参数说明
[0050]
[0051][0052]
注:表1中复合材料表示纤维增强陶瓷基复合材料,纤维表示纤维增强陶瓷基复合材料中的纤维,基体表示纤维增强陶瓷基复合材料中的基体,轴向指的是应力加载方向,界面指的是基体/纤维界面。
[0053]
基于表1的说明,对本发明提供的通过切线模量预测纤维增强陶瓷基复合材料疲劳损伤的方法的具体实施过程进行如下说明:
[0054]
(1)根据基体随机碎断模型确定基体裂纹间距;
[0055]
(2)根据总体载荷承担准则,得到卸载和重新加载过程中在峰值应力处的完好纤维承担载荷;
[0056]
根据断裂力学界面脱粘准则,利用所述卸载和重新加载过程中在峰值应力处的完好纤维承担载荷,得到界面脱粘长度、卸载界面反向滑移长度和重新加载新界面滑移长度;
[0057]
(3)根据卸载与重新加载过程的纤维滑移机理,利用所述步骤(1)中基体裂纹间距以及步骤(2)中卸载和重新加载过程中在峰值应力处的完好纤维承担载荷、界面脱粘长度、卸载界面反向滑移长度和重新加载新界面滑移长度,得到卸载和重新加载过程中纤维增强陶瓷基复合材料的应力-应变关系方程;
[0058]
(4)根据所述步骤(3)中卸载和重新加载过程中纤维增强陶瓷基复合材料的应力-应变关系方程,得到卸载和重新加载过程中纤维增强陶瓷基复合材料的切线模量,以此预测纤维增强陶瓷基复合材料疲劳损伤;
[0059]
所述步骤(1)与步骤(2)无时间顺序限定。
[0060]
本发明根据基体随机碎断模型确定基体裂纹间距。在本发明中,所述基体裂纹间距优选如式1所示:
[0061][0062]
其中,lc为基体裂纹间距,l
sat
为饱和基体裂纹间距,σm为基体轴向应力,σr为基体开裂特征应力,m为基体威布尔模量。
[0063]
在本发明中,饱和基体裂纹间距是基体裂纹间距的稳定值;本发明优选采用式1所示公式,能够获得不同应力下的基体裂纹间距。
[0064]
本发明根据总体载荷承担准则,得到卸载和重新加载过程中在峰值应力处的完好纤维承担载荷;根据断裂力学界面脱粘准则,利用所述卸载和重新加载过程中在峰值应力处的完好纤维承担载荷,得到界面脱粘长度、卸载界面反向滑移长度和重新加载新界面滑移长度。
[0065]
在本发明中,所述卸载和重新加载过程中峰值应力处的完好纤维承担载荷优选根据式2得到:
[0066][0067]
其中,σ
max
为疲劳峰值应力,vf为纤维体积含量,φ为完好纤维承担载荷,σ
fc
为纤维特征强度,mf为纤维威布尔模量。
[0068]
本发明优选采用上述方式获得卸载和重新加载过程中峰值应力处的完好纤维承担载荷,考虑了纤维随机断裂过程,峰值应力处预测的完好纤维承担应力更加准确。
[0069]
在本发明中,所述界面脱粘长度优选如式3所示:
[0070][0071]
其中,ld为界面脱粘长度,rf为纤维半径,vm为基体体积含量,ef为纤维弹性模量,em为基体弹性模量,ec为复合材料弹性模量,ρ为剪滞模型参数,τi为界面剪应力,γi为界面脱粘能,σ为名义应力。
[0072]
本发明优选采用上述方式获得界面脱粘长度,考虑了纤维断裂对界面脱粘的影响,预测的界面脱粘长度更加准确。
[0073]
在本发明中,所述卸载界面反向滑移长度优选如式4所示:
[0074][0075]
其中,ly为卸载界面反向滑移长度,φu为卸载完好纤维承担应力,σu为卸载应力。
[0076]
本发明优选采用上述方式获得卸载界面反向滑移长度,考虑了纤维断裂对界面反向滑移长度的影响,预测的卸载界面反向滑移长度更准确。
[0077]
在本发明中,所述重新加载新界面滑移长度优选如式5所示:
[0078]
[0079]
其中,lz为重新加载新界面滑移长度,φr为重新加载完好纤维承担应力,σr为重新加载应力。
[0080]
本发明优选采用上述方式获得重新加载新界面滑移长度,考虑了纤维断裂对重新加载新界面滑移长度的影响,预测的重新加载新界面滑移长度更准确。
[0081]
本发明根据卸载与重新加载过程的纤维滑移机理,利用所述基体裂纹间距以及卸载和重新加载过程中在峰值应力处的完好纤维承担载荷、界面脱粘长度、卸载界面反向滑移长度和重新加载新界面滑移长度,得到卸载和重新加载过程中纤维增强陶瓷基复合材料的应力-应变关系方程。
[0082]
在本发明中,所述卸载过程中纤维增强陶瓷基复合材料的应力-应变关系方程优选如式6所示:
[0083][0084]
其中,ε
unloading
为卸载应变,lc为基体裂纹间距,αc为复合材料热膨胀系数,αf为纤维热膨胀系数,δt为测试温度与制备温度差值。
[0085]
本发明优选采用上述方式获得卸载过程中纤维增强陶瓷基复合材料的应变,考虑了纤维断裂对复合材料卸载应变的影响,预测的卸载过程中纤维增强陶瓷基复合材料的应变更准确。
[0086]
在本发明中,所述重新加载过程中纤维增强陶瓷基复合材料的应力-应变关系方程优选如式7所示:
[0087][0088]
其中,ε
reloading
为重新加载应变。
[0089]
本发明优选采用上述方式获得重新加载过程中纤维增强陶瓷基复合材料的应变,考虑了纤维断裂对复合材料重新加载应变的影响,预测的重新加载过程中纤维增强陶瓷基复合材料的应变更准确。
[0090]
在本发明中,所述卸载过程中纤维增强陶瓷基复合材料的切线模量优选如式8所示:
[0091][0092]
其中,所述σu为卸载切线模量,δεu为卸载应变差;
[0093]
所述δεu由式9确定:
[0094][0095]
其中,σ
max
为疲劳峰值应力。
[0096]
本发明优选采用上述方式获得卸载过程中纤维增强陶瓷基复合材料的切线模量,考虑了多种损伤机制,例如,基体开裂、界面脱粘和纤维断裂,获得的切线模量能更准确反应复合材料内部的损伤。
[0097]
在本发明中,所述重新加载过程中纤维增强陶瓷基复合材料的切线模量如式10所示:
[0098][0099]
其中,所述σr为重新加载切线模量,δεr为重新加载应变差;
[0100]
所述δεr由式11确定:
[0101][0102]
其中,σ
min
为疲劳谷值应力。
[0103]
本发明优选采用上述方式获得重新加载过程中纤维增强陶瓷基复合材料的切线模量,考虑了多种损伤机制,例如,基体开裂、界面脱粘和纤维断裂,获得的切线模量能更准确反应复合材料内部的损伤。
[0104]
在本发明中,上述技术方案涉及的公式中,剪滞模型参数(ρ)优选通过剪滞模型计算得到,所述剪滞模型优选为bhe剪滞模型。本发明对所述计算方式没有特殊要求,采用本领域技术人员熟知的方式即可。
[0105]
本发明提供的技术方案适用于对纤维增强陶瓷基复合材料裂纹张开位移进行预测,所述纤维增强陶瓷基复合材料具体可以为编织陶瓷基复合材料;在本发明的实施例中,具体是以编织sic/sic陶瓷基复合材料为测试样品。
[0106]
下面将结合本发明中的实施例,对本发明中的技术方案进行清楚、完整地描述。显然,所描述的实施例仅仅是本发明一部分实施例,而不是全部的实施例。基于本发明中的实施例,本领域普通技术人员在没有做出创造性劳动前提下所获得的所有其他实施例,都属于本发明保护的范围。
[0107]
实施例1
[0108]
本实施例以编织sic/sic陶瓷基复合材料为测试样品,并通过切线模量预测纤维增强陶瓷基复合材料疲劳损伤:
[0109]
提供参数:vf=0.35,rf=7.5μm,ef=200gpa,em=300gpa,αf=3
×
10-6
/℃,αm=4
×
10-6
/℃,τi=40mpa,γi=5j/m2,mf=5,σ
fc
=2.0gpa;
[0110]
该复合材料的制备温度为1020℃,测试温度为20℃,则δt=-1000℃;
[0111]
然后根据式1~11得到纤维增强陶瓷基复合材料的切线模量,进而实现纤维增强陶瓷基复合材料疲劳损伤的预测。
[0112]
图1为本发明中试验与理论预测的纤维增强陶瓷基复合材料迟滞回线对比图,图1中实线为实际测试数据,虚线为采用本方案预测结果;由图1可知,采用本发明提供的方法预测的迟滞回线与实验数据相吻合。图2为本发明中试验与理论预测的纤维增强陶瓷基复合材料切线模量对比图,图2中实线为实际测试数据,虚线为采用本方案预测结果;由图2可知,采用本发明提供的方法预测的不同峰值应力下的切线模量与试验数据相吻合。综上可知,采用本发明方法能够准确预测纤维增强陶瓷基复合材料疲劳损伤。
[0113]
以上所述仅是本发明的优选实施方式,应当指出,对于本技术领域的普通技术人员来说,在不脱离本发明原理的前提下,还可以做出若干改进和润饰,这些改进和润饰也应视为本发明的保护范围。