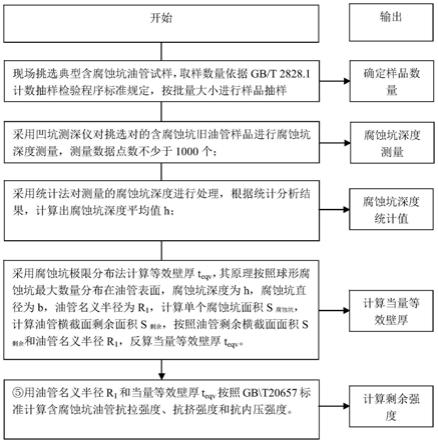
1.本发明属于石油管材新方法技术领域,具体涉及一种含腐蚀坑油管剩余强度的确定方法。
背景技术:2.油管损坏是油气田开发过程中常见的问题之一,目前国内陆上油田每年因腐蚀报废油管高达20多万吨,并且随着开采年限不断增加,报废油管数量不断上升,报废原因大部分由于油管腐蚀。
3.为了降低油管采购成本,提高经济效益,油田开展了旧油管回收修复工作。为确保修复后的旧油管入井使用安全,目前采用api spec5ct标准对旧油管进行检测判定。api spec 5ct标准是新油管质量是否合格的判定标准,应用该标准可以保证修复的旧油管下井应用安全可靠性,但同时也提高了旧油管非正常判废的比例。
4.旧油管修复判废比例取决于设定的判定依据,而目前的判定依据只是根据经验,定性的分析给出的一个参考。依据的指标太严,就会导致大量旧油管报废,造成浪费;如果依据的指标太宽,将增大下井后失效的风险,影响安全生产,失去修复的意义。如何通过旧油管的技术特征的数据来确定剩余强度指标,并提供具体的量化数据来进行修复具有很重要的现实意义。
技术实现要素:5.有鉴于此,本发明提供一种含腐蚀坑油管剩余强度的确定方法,为旧油管修复的提供量化标准。
6.为解决现有技术存在的问题,本发明所采用的技术方案为:一种含腐蚀坑油管剩余强度的确定方法步骤为:
7.1)按批量大小现场挑选典型含腐蚀坑油管试样若干根;
8.2)采用凹坑测深仪对挑选好的含腐蚀坑油管样品进行腐蚀坑深度测量,测量数据点数不少于1000个;
9.3)采用统计法对测量的腐蚀坑深度进行处理,根据统计分析结果,计算出腐蚀坑深度平均值h;
[0010][0011]
式中:m——腐蚀坑个数;
[0012]
h——腐蚀坑深度;
[0013]hi
——第i个腐蚀坑深度;
[0014]
4)采用腐蚀坑极限分布法计算等效壁厚t
eqv
,按照球形腐蚀坑最大数量分布在油管表面,腐蚀坑直径为b,计算单个腐蚀坑面积s
腐蚀坑
,计算油管横截面剩余面积s
剩余
,按照油
管剩余横截面面积s
剩余
和油管名义半径r1,反算当量等效壁厚t
eqv
;
[0015][0016][0017]s剩余
=s
管体-ns
腐蚀坑
=π(2r
1-t
eqv
)t
eqv
ꢀꢀꢀꢀ
公式4
[0018][0019]
式中:
[0020]
b——腐蚀坑直径;
[0021]
h——腐蚀坑深度;
[0022]
r1——油管名义半径;
[0023]
t——油管名义壁厚;
[0024]
r2——腐蚀坑半径;
[0025]
α1——腐蚀坑在油管上对应的圆心角的一半;
[0026]
α2——腐蚀坑圆心角的一半;
[0027]
h1——腐蚀坑弦高;
[0028]s管体扇
——腐蚀坑对应油管扇形面积;
[0029]s腐蚀坑扇
——腐蚀坑扇形面积;
[0030]s腐蚀坑
——腐蚀坑面积;
[0031]s管体
——管体横截面积;
[0032]s剩余
——单个腐蚀坑对应管体剩余横截面积;
[0033]
n——油管横截面上极限腐蚀坑数量;
[0034]
t
eqv
——含腐蚀坑油管当量等效壁厚;
[0035]
5)根据油管名义半径r1和当量等效壁厚t
eqv
,按照gb\t20657标准计算旧油管抗拉强度、抗挤强度和抗内压强度。
[0036]
与现有技术相比,本发明包括以下有益效果:
[0037]
1、本发明建立了以概率统计方法和腐蚀坑极限分布法为依据的含腐蚀坑油管剩余强度的确定方法,可以对腐蚀坑油管剩余强度指标进行量化确定提供了一种新的方法。
[0038]
2、本发明考虑了批量腐蚀坑油管腐蚀坑随机分布的影响,明确了旧油管当量等效壁厚在剩余强度指标中的重要地位,提出了根据当量等效壁厚确定旧油管剩余强度指标。通过大量的实验表明,该方法确定的旧油管剩余强度可靠性高,与试验值吻合程度高。
附图说明
[0039]
图1为含腐蚀坑油管剩余强度的确定方法的流程图;
[0040]
图2腐蚀坑油管示意图;
[0041]
图3腐蚀坑示意图;
[0042]
图4计算参数示意图;
[0043]
图5计算参数腐蚀坑面积示意图;
[0044]
标记说明:1油管;2腐蚀坑。
具体实施方式
[0045]
为了使本发明的目的、技术方案及优点更加清楚明白,以下结合附图及实施例,对本发明进行进一步详细说明。应当理解,此处所描述的具体实施例仅仅用以解释本发明,并不用于限定本发明。
[0046]
本发明是在腐蚀坑统计学基础上,采用腐蚀坑极限分布法预测旧油管剩余强度,解决旧油管的判定标准制定面临的问题。
[0047]
实施例1:本实施例提供φ88.90mm
×
6.45mmp110含腐蚀坑油管剩余强度的确定方法,如图1和图2所示:
[0048]
1、现场挑选典型含腐蚀坑油管,规格为φ88.90mm
×
6.45mmp110,旧油管数量依据gb/t 2828.1计数抽样检验程序标准规定样品挑选38根;
[0049]
2、采用凹坑测深仪对挑选样品进行腐蚀坑深度测量,共计测量3440个腐蚀坑数据;
[0050]
3、采用统计法统计腐蚀坑深度,通过对油管样本腐蚀坑深度统计分析,腐蚀坑深度平均值为h=1.94mm,如图3所示。
[0051][0052]
m——腐蚀坑个数;
[0053]
h——腐蚀坑深度;
[0054]hi
——第i个腐蚀坑深度;
[0055]
采用腐蚀坑极限分布法计算等效壁厚t
eqv
,即按照球形腐蚀坑最大数量分布在油管表面,任意取一腐蚀坑,腐蚀坑深度为h=1.94mm,腐蚀坑直径b任意取值,结果取等效当量壁厚最小的情况,油管半径为r=44.45mm,采用公式9-公式13计算单个腐蚀坑面积损失s
腐蚀坑
=2.985mm2,计算油管横截面面总损失s
剩余
=1461.6mm2,按照油管剩余横截面面积和油管名义半径r1,反算当量等效壁厚t
eqv
=5.58mm,如图4和图5所示。
[0056][0057][0058][0059][0060]
[0061][0062][0063][0064][0065][0066][0067]s剩余
=s
管体-ns
腐蚀坑
=π(2r
1-t
eqv
)t
eqv
ꢀꢀꢀ
公式13
[0068][0069]
式中:
[0070]
b——腐蚀坑直径;
[0071]
h——腐蚀坑深度;
[0072]
r1——油管名义半径;
[0073]
t——油管名义壁厚;
[0074]
r2——腐蚀坑半径;
[0075]
α1——腐蚀坑在油管上对应的圆心角的一半;
[0076]
α2——腐蚀坑圆心角的一半;
[0077]
h1——腐蚀坑弦高;
[0078]s管体扇
——腐蚀坑对应油管扇形面积;
[0079]s腐蚀坑扇
——腐蚀坑扇形面积;
[0080]s腐蚀坑
——腐蚀坑面积;
[0081]s管体
——管体横截面积;
[0082]s剩余
——单个腐蚀坑对应管体剩余横截面积;
[0083]
n——油管横截面上极限腐蚀坑数量;
[0084]
t
eqv
——含腐蚀坑油管当量等效壁厚。
[0085]
5、采用油管名义半径r1和当量壁厚t
eqv
=5.58mm按照gb\t20657标准计算旧油管抗拉强度、抗挤强度和抗内压强度。
[0086]
实施效果:通过本方法确定了φ88.90mm
×
6.45mm p110含腐蚀坑旧油管抗拉强度为1108kn,达到额定值的87%;抗内压强度为95.2mpa,达到额定值的98%;抗挤强度下降69.6mpa,达到额定值的75%,使得量化指标可以为不同的工况提供了明确的参考。
[0087]
本发明的内容不限于实施例所列举,本领域普通技术人员通过阅读本发明说明书而对本发明技术方案采取的任何等效的变换,均为本发明的权利要求所涵盖。