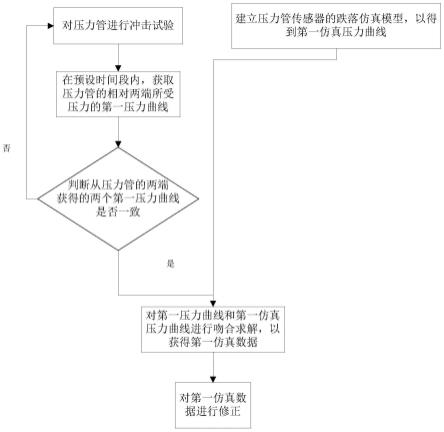
1.本发明涉及主动式弹起机罩技术领域,具体而言,涉及一种用于主动式弹起机罩的压力管传感器的压力仿真方法。
背景技术:2.随着弱势道路使用者(行人及二轮车骑行者)的交通事故及伤亡比率日益提升,针对弱势道路使用者的保护技术也普遍应用。主动式弹起机罩系统就是日益广泛应用于保护弱势道路使用者的一种技术,其通过布置在车辆前端的感知系统检测碰撞强度及类型,进而感知信号传输给ecu进行判别,当达到点爆阈值(检测到行人)便发出点火信号给执行机构;进而,执行机构动作抬升起机罩至指定区域,以减少行人头部损伤等级。乘用车主动式弹起机罩系统在应用过程中主要痛点问题为误爆,主要体现在无法准确的识别撞击到行人和撞击到其他非行人物体。因此,准确的识别行人和非行人物体成为主动式弹起机罩系统的核心问题。现在主流的压力管传感器相较于传统的单一使用加速度传感器的方法,可更好的预测行人撞击、减少误爆而应用广泛。
3.由于压力管为塑料管中填充一定压力的气体,要通过仿真实现压力信号的变化特征的准确模拟难度较大。且压力管传感器信号的区分特性与造型、布置和前端结构设计紧密相关,因此需要在乘用车开发前期建立一种准确的仿真方法,在造型、布置及前端结构定型之前达到最优设计尤为必要。
4.现有压力管的仿真方法:其一为基于材料的拉伸测试,其性能很难准确表征压力信号的特性;其二为通过整车级打击试验进行仿真标定,由于引入了外饰、泡沫的影响,标定结果也往往不理想,导致在项目开发前期对于信号的预测准确性不高,而到项目实车验证阶段暴露出设计问题,使得整改的成本较高,周期较长。
技术实现要素:5.本发明的主要目的在于提供一种用于主动式弹起机罩的压力管传感器的压力仿真方法,以解决现有技术中的压力管传感器的压力仿真方法的仿真标定的准确性不高,易导致后期整车开发成本较高的问题。
6.为了实现上述目的,本发明提供了一种用于主动式弹起机罩的压力管传感器的压力仿真方法,压力管传感器包括压力管和设置在压力管的相对两端的两个压力传感器,压力仿真方法包括:对压力管进行冲击试验的第一试验步骤;在预设时间段内,获取压力管的相对两端所受压力的第一压力曲线的第一获取步骤;建立压力管传感器的跌落仿真模型,以得到第一仿真压力曲线的第一建模步骤;对第一压力曲线和第一仿真压力曲线进行吻合求解,以获得第一仿真数据的第一求解步骤,其中,第一仿真数据包括尺寸参数组、材料参数组、性能响应参数组和接触性能参数组。
7.进一步地,第一试验步骤包括利用跌落碰撞器从多个预设高度落下并分别对压力管进行冲击试验。
8.进一步地,预设高度hi满足公式:其中,mo为撞击到人体的等效质量或标准打击器的质量,vi为打击器碰撞的相对速度,m为跌落碰撞器的质量,g为重力加速度,hi为vi对应的不同预设高度。
9.进一步地,在第一获取步骤之后,在第一求解步骤之前,压力仿真方法还包括判断从压力管的两端获得的两个第一压力曲线是否一致的判断步骤,如果是,则执行第一求解步骤,如果否,则执行第一试验步骤。
10.进一步地,第一建模步骤包括:输入压力管的尺寸参数组的初始值,以模拟压力管的形状的第一模拟步骤;输入压力管的性能响应参数组的初始值,以模拟压力管的性能响应能力的第二模拟步骤;输入压力管的材料参数组的初始值,以模拟压力管的材料的第三模拟步骤;输入压力管的接触性能参数组的初始值,以模拟压力管与跌落碰撞器之间的接触的第四模拟步骤。
11.进一步地,尺寸参数组包括压力管的长度尺寸和压力管的横截面积尺寸中的至少一个;或者,性能响应参数组包括声速、初始压力、粘性系数和阻尼系数中的至少一个;或者,材料参数组包括密度、杨氏模量、泊松比、屈服强度和切线模量中的至少一个;或者,接触性能参数组包括从面罚刚度系数、主面罚刚度系数、静态摩擦系数、动态摩擦系数和粘滞阻尼系数中的至少一个。
12.进一步地,第一求解步骤包括:在尺寸参数组、性能响应参数组、材料参数组和接触性能参数组中选取多个可调参数的参数选取步骤;设定每个可调参数的数值范围和数值个数的设定水平步骤;按照正交化的方法对所有可调参数、数值范围和数值个数进行组合,以得到正交矩阵的设定矩阵步骤;根据正交矩阵进行仿真计算,并以第一压力曲线和第一仿真压力曲线的吻合度为求解目标获得最优解。
13.进一步地,多个可调参数包括初始压力、粘性系数、阻尼系数、杨氏模量、泊松比、从面罚刚度系数、主面罚刚度系数、静态摩擦系数、动态摩擦系数和粘滞阻尼系数中的一个或多个。
14.进一步地,在第一求解步骤之后,压力仿真方法还包括对第一仿真数据进行修正的修正步骤。
15.进一步地,修正步骤包括:将压力管传感器安装至整车,并对压力管进行撞击试验的第二试验步骤;获取预设时间段内压力管的相对两端所受压力的第二压力曲线的第二获取步骤;在整车工况下,建立压力管的碰撞仿真模型,且输入第一仿真数据,以得到第二仿真压力曲线的第二建模步骤;对第二压力曲线和第二仿真压力曲线进行吻合求解,以获得第二仿真数据的第二求解步骤,其中,第二仿真数据包括尺寸参数组、材料参数组、性能响应参数组和接触参数组。
16.进一步地,在第二试验步骤之前,压力仿真方法还包括选取不同类型碰撞器的碰撞器选取步骤;第二试验步骤包括:使整车与各碰撞器以多种预设速度相对运动,以进行碰撞试验。
17.应用本发明的技术方案,通过进行压力管的跌落试验,以获得第一压力曲线,并建立压力管的跌落仿真模型,获得第一仿真压力曲线,然后以第一压力曲线为基准,使第一仿真压力曲线尽可能地与第一压力曲线吻合,这样,通过跌落仿真模型获得的第一仿真数据
可以为后期主动发动机罩的性能设计提供依据,相对于单纯的针对压力管本体材料的进行测试或直接用整车进行测试的方法而言,本实施例的仿真方法不仅可以对压力管的材料、尺寸、性能响应以及接触性能对应的参数进行求解,还减少了整车的前端外饰及泡沫等组件带来的影响,这样,不仅提升了压力管传感器仿真标定的准确性,还减少了整车试验的打击数量,以节约主动机罩系统性能开发成本。
附图说明
18.构成本技术的一部分的说明书附图用来提供对本发明的进一步理解,本发明的示意性实施例及其说明用于解释本发明,并不构成对本发明的不当限定。在附图中:
19.图1示出了本发明的实施例的压力管传感器的压力仿真方法的流程示意图;
20.图2示出了图1的压力仿真方法的第一求解步骤的流程示意图;
21.图3示出了图1的压力仿真方法的修正步骤的流程示意图;
22.图4示出了本发明的实施例的压力管传感器的结构示意图;
23.图5示出了本发明的实施例的跌落设备的结构示意图;
24.图6示出了本发明的实施例的对压力管进行撞击试验的示意图;
25.图7示出了图6的b-b向剖视图;以及
26.图8示出了本发明的实施例的第一仿真压力曲线与第一压力曲线吻合的示意图。
27.其中,上述附图包括以下附图标记:
28.101、压力管;102、压力传感器;201、跌落碰撞器;202、安装支架;203、支撑架;204、滑轨;205、支撑台;301、蒙皮;3002、防撞梁泡沫;3003、防撞梁;401、保护pdi-2腿型碰撞器;402、小动物碰撞器;403、篮球碰撞器;404、足球碰撞器;405、小鸟碰撞器;406、石子碰撞器;407、树枝碰撞器。
具体实施方式
29.需要说明的是,在不冲突的情况下,本技术中的实施例及实施例中的特征可以相互组合。下面将参考附图并结合实施例来详细说明本发明。
30.传统主动机罩在开发过程中,由于缺乏对压力管传感器高精度的仿真方法,前期不能充分识别出设计结构的风险点,导致整车测试矩阵较为巨大,且存在较多试验个数及轮次现象,导致性能开发周期长、成本高的特点。
31.因此,如图1和图4所示,本发明的实施例提供了一种用于主动式弹起机罩的压力管传感器的压力仿真方法。压力管传感器包括压力管101和设置在压力管101的相对两端的两个压力传感器102,压力仿真方法包括:对压力管101进行冲击试验的第一试验步骤;在预设时间段内,获取压力管101的相对两端所受压力的第一压力曲线的第一获取步骤;建立压力管传感器的跌落仿真模型,以得到第一仿真压力曲线的第一建模步骤;对第一压力曲线和第一仿真压力曲线进行吻合求解,以获得第一仿真数据的第一求解步骤,其中,第一仿真数据包括尺寸参数组、材料参数组、性能响应参数组和接触性能参数组。
32.上述技术方案中,通过进行压力管101的跌落试验,以获得第一压力曲线,并建立压力管101的跌落仿真模型,获得第一仿真压力曲线,然后以第一压力曲线为基准,使第一仿真压力曲线尽可能地与第一压力曲线吻合,这样,通过跌落仿真模型获得的第一仿真数
据可以为后期主动发动机罩的性能设计提供依据,相对于单纯的针对压力管101本体材料的进行测试或直接用整车进行测试的方法而言,本实施例的仿真方法不仅可以对压力管101的材料、尺寸、性能响应以及接触性能对应的参数进行求解,还减少了整车的前端外饰及泡沫等组件带来的影响,这样,不仅提升了压力管传感器仿真标定的准确性,还减少了整车试验的打击数量,以节约主动机罩系统性能开发成本。
33.具体地,本发明的实施例中,对压力管101进行冲击试验是部件类型的试验,是指直接对压力管101进行冲击,未将压力管101安装至整车,以避免其它部件影响压力管101的测试性能。
34.需要说明的是,本发明的实施例中,第一压力曲线和第一仿真压力曲线均为压力与时间的关系,即压力随着时间的变化而变化。
35.需要说明的是,如图8所示,本发明的实施例中,吻合求解是指以第一压力曲线为基准,选取与第一压力曲线较为接近的第一仿真压力曲线,即第一压力曲线和第一仿真压力曲线达到预设吻合度,这样,第一仿真压力曲线对应的跌落仿真模型的尺寸参数组、材料参数组、性能响应参数组和接触性能参数组的数值即为第一仿真数据。其中,预设吻合度优选为90%,也就是说第一压力曲线和第一仿真压力曲线的吻合度需要达到90%及其以上。
36.需要说明的是,预设吻合度是指第一压力曲线和第一仿真压力曲线的曲线峰值、曲线峰值时刻、曲线相位、曲线包络面积和曲线形状相接近的程度。
37.本发明的主动式弹起机罩系统用压力管传感器的压力仿真方法可以有效提升项目前期压力信号仿真的准确性,从而可以通过仿真实现开发前期预测设计风险、合理规划主动式弹起机罩系统整车试验,进而可实现减少试验矩阵数量和试验周期的效果。
38.具体地,本发明的实施例中,由于第一建模步骤需要建立与第一试验步骤中的部件工况一致的模型,所以先进行第一试验步骤,再进行第一建模步骤;当然,第一试验步骤和第一建模步骤之间也可以不设置先后顺序,只要先对第一试验步骤的工况进行设计,之后再进行第一试验步骤或第一建模步骤即可。
39.优选地,本发明的实施例中,压力管101内充满一定压力的气体,压力管101受到挤压或冲击后两端的传感器可以分别记录压力的变化情况。
40.如图5所示,本发明的实施例中,第一试验步骤包括利用跌落碰撞器201从多个预设高度落下并分别对压力管101进行冲击试验。
41.通过上述设置,可以通过利用跌落碰撞器201从多个预设高度落下来模拟对压力管101的不同冲击能量,这样可以采集压力管101在多个冲击能量下的多个第一压力曲线,然后选取出与多个第一压力曲线均吻合的第一仿真曲线,这样可以提高对压力管101的仿真精度,然后利用上述第一仿真曲线求解出与上述第一仿真曲线对应的尺寸参数组、材料参数组、性能响应参数组和接触性能参数组的具体数值,从而得到精确的压力管101仿真参数,进而为后期整车试验提供了准确的数据,有助于提升主动机罩误作用算法的准确性,减少系统误爆。
42.优选地,本发明的实施例中,多个预设高度包括高、中、低三种高度,以便模拟高、中、低三种冲击能量。
43.具体地,如图5所示,本发明的实施例中,冲击试验采用专用的跌落设备进行,跌落设备包括用于放置压力管传感器的支撑台205、设置在支撑台205上且间隔设置的两个安装
支架202和位于两个安装支架202之间的跌落碰撞器201;其中,每个安装支架202的朝向跌落碰撞器201的一侧设有导向槽,跌落碰撞器201的相对两端分别与两个安装支架202的导向槽滑动配合,以使跌落碰撞器201可以沿竖直方向从不同的高度落下(图5中为三个不同的预设高度)。
44.具体地,如图5所示,本发明的实施例中,跌落设备还包括宽度调节器,至少一个安装支架202的背离跌落碰撞器201的一侧设有宽度调节器,宽度调节器包括与支撑台205连接的支撑架203和相对于支撑架203沿水平方向可移动设置的滑轨204,支撑架203上设有沿水平方向布置的滑槽,滑轨204的一端在滑槽内可滑动地设置,滑槽的另一端与安装支架202连接。这样可以调节两个安装支架202之间的间隔,从而使跌落设备适用于不同质量及体积的碰撞器。
45.优选地,本发明的实施例中,宽度调节器包括沿竖直方向间隔设置的多个滑槽和分别与多个滑槽对应设置的多个滑轨204。
46.优选地,本发明的实施例中,预设高度hi满足公式:其中,m0为撞击到人体的等效质量或标准打击器的质量,vi为打击器碰撞的相对速度,m为跌落碰撞器201的质量,g为重力加速度,hi为vi对应的不同预设高度。
47.通过上述设置,可以通过同一打击器相对于压力管101的不同速度计算出在跌落试验中的同一跌落碰撞器201的不同跌落高度,从而可以模拟对压力传感器102的不同冲击能量。
48.需要说明的是,vi的速度可以为多种,优选地,vi可以为低能量强度的等效撞击速度25km/h、中能量强度的等效撞击速度32km/h、高能量强度的等效撞击速度40km/h,这样可以计算出低能量、中能量和高能量分别对应的不同高度。
49.需要说明的是,m0是人体的等效质量或标准打击器的质量,为可选取的标准值。
50.当然,在附图未示出的替代实施例中,也可以选取不同质量的跌落碰撞器201从相同的高度落下,只要可以模拟不同的冲击能量即可。将上述公式中的高度固定,通过选取不同的vi,来计算不同跌落碰撞器201的质量,即可以利用不同质量的跌落碰撞器201从同一高度落下来模拟不同的冲击能量。
51.当然,也可以使不同的跌落碰撞器201从不同的高度落下,只要可以模拟低、中和高三种冲击能量即可。
52.如图1所示,本发明的实施例中,在第一获取步骤之后,在第一求解步骤之前,压力仿真方法还包括判断从压力管101的两端获得的两个第一压力曲线是否一致的判断步骤,如果是,则执行第一求解步骤,如果否,则执行第一试验步骤。
53.通过上述设置,可以判断跌落碰撞器201撞击的是否为压力管101在自身长度方向上的中心位置,如果是,则撞击的为上述中心位置,如果否,则撞击位置偏离上述中心位置,跌落碰撞器201撞击压力管101的中心位置而产生的压力曲线可以更精确的表示压力管101的压力随时间的变化情况。这样,上述步骤可以使仿真方法能够更加精确地获得第一仿真数据,从而提升了压力管传感器仿真标定的准确性。
54.优选地,本发明的实施例中,在第一试验步骤中,选取压力管101在自身长度方向上的中心位置为跌落碰撞器201的撞击位置,若跌落碰撞器201撞击压力管101的中心位置,
理论上压力管101的两端的信号应一致。
55.需要说明的是,本发明的实施例中,两个第一压力曲线一致是指即两个第一压力曲线的峰值吻合90%及以上。
56.具体地,本发明的实施例中,第一建模步骤包括:输入压力管101的尺寸参数组的初始值,以模拟压力管101的形状的第一模拟步骤;输入压力管101的性能响应参数组的初始值,以模拟压力管101的性能响应能力的第二模拟步骤;输入压力管101的材料参数组的初始值,以模拟压力管101的材料的第三模拟步骤;输入压力管101的接触性能参数组的初始值,以模拟压力管101与跌落碰撞器201之间的接触的第四模拟步骤。
57.上述技术方案中,在建立压力管传感器的跌落仿真模型时,为尺寸参数组、性能响应参数组、材料参数组和接触性能参数组中的每个参数选择一个初始值(操作人员可以根据经验等任意选取数值),这样可以形成一个初始的压力管101跌落仿真模型,以模拟出一个初始的第一仿真压力曲线,以便于后续的求解计算。
58.进一步地,相对于单纯的针对压力管101本体材料的进行测试,本实施例的仿真方法还可以对压力管101的尺寸进行模拟,以及压力管101在撞击工况下的性能响应以及接触性能进行模拟。
59.具体地,本发明的实施例中,利用ls-dyna软件建立跌落试验工况下的压力管传感器的跌落仿真模型,即压力管101的长度、压力管101的固定位置、跌落碰撞器201的跌落高度和跌落碰撞器201的质量等与跌落试验条件一致,但是,建模软件不限于上述软件。
60.优选地,本发明的实施例利用ls-dyna软件中的梁单元模拟压力管101的截面尺寸和压力管101的长度,其中,压力管101的长度优选为1mm。当然,在附图未示出的替代实施例中,压力管101的长度也可以为其它长度。
61.需要说明的是,本发明的实施例中,性能响应是指压力管101的变形能力等。
62.具体地,本发明的实施例中,压力管101的性能响应能力采用ls-dyna软件中的define_pressure_tube卡片来进行模拟;压力管101的材料采用ls-dyna软件中的mat_plastic_kinematic材料本构来进行模拟;压力管101与跌落碰撞器201之间的接触采用ls-dyna软件中的contact_automatic_surface_to_surface_mortar来进行模拟。
63.优选地,本发明的实施例中,尺寸参数组包括压力管101的长度尺寸和压力管101的横截面积尺寸,这样可以对压力管101的尺寸进行准确模拟。
64.优选地,本发明的实施例中,性能响应参数组包括声速、初始压力、粘性系数和阻尼系数,这样可以对压力管101的变形能力进行模拟。
65.优选地,本发明的实施例中,材料参数组包括密度、杨氏模量、泊松比、屈服强度和切线模量,这样可以对压力管101的材料进行模拟。
66.优选地,本发明的实施例中,接触性能参数组包括从面罚刚度系数、主面罚刚度系数、静态摩擦系数、动态摩擦系数和粘滞阻尼系数,这样可以对压力管101与跌落碰撞器201之间的接触进行模拟。
67.通过上述设置,可以使得仿真曲线较准确地接近撞击试验中的第一压力曲线,以为后续的整车试验提供较为准确的依据。
68.如图2所示,本发明的实施例中,第一求解步骤包括:在尺寸参数组、性能响应参数组、材料参数组和接触性能参数组中选取多个可调参数的参数选取步骤;设定每个可调参
数的数值范围和数值个数的设定水平步骤;按照正交化的方法对所有可调参数、数值范围和数值个数进行组合,以得到正交矩阵的设定矩阵步骤;根据正交矩阵进行仿真计算,并以第一压力曲线和第一仿真压力曲线的吻合度为求解目标获得最优解。
69.通过上述设置,在每个可调参数的数值范围内选取多个数值,以形成多个第一仿真压力曲线,然后以第一压力曲线为基准,在多个第一仿真压力曲线中选取与第一压力曲线吻合的第一仿真压力曲线,这样,符合吻合度要求的第一仿真压力曲线所对应的参数即为最优解,这样可以得到第一仿真数据的具体数值,从而可以为后期主动发动机罩的性能设计提供依据。
70.需要说明的是,本发明的实施例中,可调参数是指尺寸参数组、性能响应参数组、材料参数组和接触性能参数组中的可以变化且对压力信号峰值、压力信号峰宽和压力信号衰减特性中的一个或多个有影响的参数。
71.需要说明的是,本发明的实施例中,在设定水平步骤中,需要给每个可调参数的数值设定一个变化范围,然后在每个可调参数的变化范围内选取多个数值,且多个数值中的相邻两个数值之间的间距相等,其中,输入尺寸参数组、材料参数组、性能响应参数组和接触性能参数组中所有参数的初始值所对应的第一仿真压力曲线与第一压力曲线之间具有差异,然后技术人员根据设计经验以及上述差异,来设计每个可调参数的数值范围和数值个数。
72.具体地,本发明的实施例中,通过设定正交矩阵,可以减少计算样本的数量,从而减少计算量。
73.具体地,本发明的实施例中,根据正交矩阵进行仿真计算是指利用迭代的方式将每个可调参数中选取的多个数值代入压力管101的跌落仿真模型中,以形成多个第一仿真压力曲线,然后从多个第一仿真压力曲线中选取与第一压力曲线吻合的一个第一仿真压力曲线,这个第一仿真压力曲线所对应的尺寸参数组、材料参数组、性能响应参数组和接触性能参数组即为第一仿真数据(最优解)。
74.具体地,本发明的实施例中,在对第一压力曲线和第一仿真压力曲线进行吻合求解时,需要使第一仿真压力曲线分别与高、中、低三种能量下的第一压力曲线进行吻合,即多个第一仿真压力曲线中选取一个能够与高能量工况下的第一压力曲线、中能量工况下的第一压力曲线、低能量工况下的第一压力曲线均吻合的一个第一仿真压力曲线。
75.优选地,本发明的实施例中,多个可调参数包括初始压力、粘性系数、阻尼系数、杨氏模量、泊松比、从面罚刚度系数、主面罚刚度系数、静态摩擦系数、动态摩擦系数和粘滞阻尼系数中的一个或多个。
76.上述技术方案中,通过选取上述参数,并对上述参数的具有数值进行改变,可以改变压力管101的压力信号峰值、压力信号峰宽和压力信号的衰减特性,这样,通过在上述参数中代入不同的数值,可以得到不同的第一仿真压力曲线,然后选取能够满足与高、中、低三个能量冲击对应的三个第一压力曲线吻合的第一仿真压力曲线,这样可以得到压力管101在跌落试验工况下的最优参数。
77.具体地,每个可调参数对压力管101的压力信号的影响如表1所示:
78.表1:每个可调参数对压力管101的压力信号的影响
[0079][0080]
通过改变上述参数可以对第一仿真压力曲线的压力信号峰值、压力信号峰宽、压力信号衰减特性进行改变,从而改变第一仿真压力曲线。
[0081]
利用前述步骤,一方面,可以逐渐缩小压力管101的参数范围,便于对后期的整车开发提供依据;另一方面,在项目开发前期,即没有整车模拟工况时,可以获得较为精确的压力管101的参数值。
[0082]
如图1所示,本发明的实施例中,在第一求解步骤之后,压力信号的仿真方法还包括对第一仿真数据进行修正的修正步骤。
[0083]
上述技术方案中,通过设置修正步骤可以对第一仿真数据进行修正,从而增加对压力管传感器仿真标定的准确性。
[0084]
如图3所示,本发明的实施例中,修正步骤包括:将压力管传感器安装至整车,并对压力管101进行撞击试验的第二试验步骤;获取预设时间段内压力管101的相对两端所受压力的第二压力曲线的第二获取步骤;在整车工况下,建立压力管101的碰撞仿真模型,且输入第一仿真数据,以得到第二仿真压力曲线的第二建模步骤;对第二压力曲线和第二仿真压力曲线进行吻合求解,以获得第二仿真数据的第二求解步骤,其中,第二仿真数据包括尺寸参数组、材料参数组、性能响应参数组和接触参数组。
[0085]
上述技术方案中,在得到部件工况下(即跌落试验下的工况)的压力管传感器的参数值后,通过模拟整车撞击工况下,来获得第二压力曲线,并输入求解出的第一仿真数据,建立压力管101在整车工况下的仿真模型,以获得第二仿真压力曲线,然后以第二压力曲线为基准,使第二仿真压力曲线尽可能地与第二压力曲线吻合,这样,可以对第一求解步骤中得出的参数值进行修正,从而使获得的第二仿真数据相比第一仿真数据更加准确,在后续的整车设计阶段为压力管传感器的设计提供依据。
[0086]
进一步地,利用本实施例的压力仿真方法可以逐渐逼近实际工况下的压力管101的最优设计参数,解决了现有技术存在的仿真结果与实际结果偏差较大的问题。
[0087]
需要说明的是,本发明的实施例中,压力管101的碰撞仿真模型是指压力管101在整车工况下的模型,以对整车工况下的压力管101进行模拟。
[0088]
需要说明的是,修正步骤是对第一仿真数据的局部微调,以对第一仿真数据进行修正。
[0089]
需要说明的是,本发明的实施例中,同理,第二求解步骤包括参数选取步骤、设定水平步骤、设定矩阵步骤以及进行仿真计算,并以第一压力曲线和第一仿真压力曲线的吻合度为求解目标获得最优解的步骤。其中,将在压力管101的碰撞仿真模型中输入第一仿真数据后,得到的第二仿真压力曲线与第一仿真数据在部件工况下的压力曲线的压力信号峰
宽会有差异,然后技术人员根据设计经验以及上述差异,来设计每个可调参数的数值范围和数值个数。
[0090]
具体地,如图7所示,本发明的实施例中,整车包括车架、覆盖于车架上的蒙皮301、位于车架前端和蒙皮301之间的防撞梁3003和位于防撞梁3003和蒙皮301之间的防撞梁泡沫3002,在防撞梁泡沫3002的朝向防撞梁3003的一侧设有安装槽,部分压力管101布置在安装槽内,且压力管101从安装槽露出的部分与防撞梁3003相连接。
[0091]
具体地,如图3所示,本发明的实施例中,由于第二建模步骤需要建立与第二试验步骤中的整车工况一致的模型,所以先进行第二试验步骤,再进行第二建模步骤;当然,第二试验步骤和第二建模步骤之间也可以不设置先后顺序,只要先对第二试验步骤的整车工况进行设计,之后再进行第二试验步骤或第二建模步骤。
[0092]
具体地,本发明的实施例中,在第二获取步骤之后,在第二求解步骤之前,压力仿真方法还包括判断从压力管101的两端获得的两个第二压力曲线是否一致的判断步骤,如果是,则执行第二求解步骤,如果否,则执行第二试验步骤。
[0093]
通过上述设置,可以判断碰撞器撞击的是否为压力管101在自身长度方向上的中心位置,如果是,则撞击的为上述中心位置,如果否,则撞击位置偏离上述中心位置,碰撞器撞击压力管101的中心位置而产生的压力曲线可以更精确的表示压力管101的压力随时间的变化情况。这样,上述步骤可以使仿真方法能够更加精确地获得第二仿真数据,从而提升了压力管传感器仿真标定的准确性。
[0094]
如图6所示,本发明的实施例中,在第二试验步骤之前,压力仿真方法还包括选取不同类型碰撞器的碰撞器选取步骤;第二试验步骤包括:使整车与各碰撞器以多种预设速度相对运动,以进行碰撞试验。
[0095]
通过上述设置,可以通过利用各碰撞器从以多种预设速度撞击到整车上,以模拟在整车工况下各碰撞器对压力管101的不同冲击能量,这样可以采集压力管101在整车工况下以及多个冲击能量下的多个第二压力曲线,然后选取出与多个第二压力曲线均吻合的第二仿真曲线,这样可以提高对压力管101的仿真精度,然后利用上述第二仿真曲线求解出与上述第二仿真曲线对应的尺寸参数组、材料参数组、性能响应参数组和接触性能参数组的具体数值,从而得到精确的压力管101仿真参数,有助于提升主动机罩误作用算法的准确性,减少系统误爆。
[0096]
优选地,本发明的实施例中,多种预设速度包括25km/h、32km/h、40km/h三种速度,以便模拟小、中、大三种冲击能量。
[0097]
如图6所示,不同类型的碰撞器包括行人保护pdi-2腿型碰撞器401、小动物碰撞器402、篮球碰撞器403、足球碰撞器404、小鸟碰撞器405、石子碰撞器406、树枝碰撞器407等,但不限于上述碰撞器。
[0098]
需要说明的是,本发明的实施例中,第二压力曲线和第二仿真压力曲线的吻合度达到吻合求解的指标为:行人保护pdi-2腿型碰撞器401或小动物碰撞器402进行试验所得到的第二压力曲线的曲线峰值、曲线峰值时刻、曲线相位、曲线包络面积、曲线形状与第二仿真曲线的吻合度≥80%;除行人保护pdi-2腿型碰撞器401和小动物碰撞器402之外的其余碰撞器进行试验所得到的第二压力曲线与第二仿真曲线的吻合度≥70%。
[0099]
需要说明的是,在主动式弹起机罩的系统开发中,高精度的压力仿真方法尤为重
要:在车辆开发前期,特别是造型及布置阶段,通过高精度仿真识别设计风险,可有效提升后期设计反复并减少性能开发周期、减少主动式弹起机罩系统的误爆率。
[0100]
从以上的描述中,可以看出,本发明上述的实施例实现了如下技术效果:通过进行压力管的跌落试验,以获得第一压力曲线,并建立压力管的跌落仿真模型,获得第一仿真压力曲线,然后以第一压力曲线为基准,使第一仿真压力曲线尽可能地与第一压力曲线吻合,这样,通过跌落仿真模型获得的第一仿真数据可以为后期主动发动机罩的性能设计提供依据,相对于单纯的针对压力管本体材料的进行测试或直接用整车进行测试的方法而言,本实施例的仿真方法不仅可以对压力管的材料、尺寸、性能响应以及接触性能对应的参数进行求解,还减少了整车的前端外饰及泡沫等组件带来的影响,这样,不仅提升了压力管传感器仿真标定的准确性,还减少了整车试验的打击数量,以节约主动机罩系统性能开发成本。
[0101]
以上所述仅为本发明的优选实施例而已,并不用于限制本发明,对于本领域的技术人员来说,本发明可以有各种更改和变化。凡在本发明的精神和原则之内,所作的任何修改、等同替换、改进等,均应包含在本发明的保护范围之内。