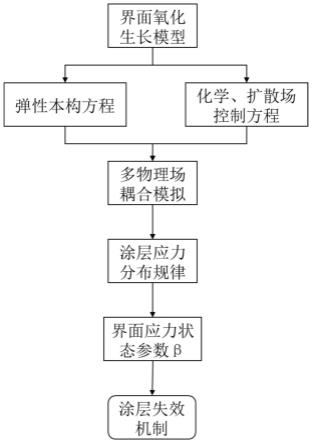
1.本发明是一种基于数值仿真的热障涂层循环氧化失效机制研究方法,用以研究热障涂层在加热-保温-冷却的工作环境下发生剥落失效的机制,属于航空航天发动机技术领域。
背景技术:2.热障涂层(tbc)是一种为满足航空发动机热端部件工作需求而诞生的高温金属保护技术,即在涡轮叶片表面涂覆具有耐腐蚀、低热导率、耐高温等性质的先进陶瓷材料,从而对高温合金基底起热防护作用,延长涡轮叶片的使用寿命。热障涂层是一种典型的多层结构,通常由四层具有特定属性和功能的材料制成。包括了陶瓷层(tc)、粘结层(bc)、氧化层(tgo)和合金基底(sub)。
3.热障涂层在服役过程中不断经历加热-保温-冷却的工作环境,陶瓷层、氧化层及粘结层由于物理参数的不匹配,在加热和冷却阶段热障涂层内部存在一定水平的热应力,在保温阶段氧化层生长而产生的热生长应力加剧了热障涂层内部的应力水平,从而引起涂层内部开裂和界面层裂,界面一旦层裂,涂层将发生剥落失效,会使叶片基体直接暴露在超过材料耐温能力的高温燃气环境中,造成叶片烧蚀、断裂。因此,必须建立热障涂层在循环氧化下的生长模型,来预测热障涂层应力演化规律,这对研究热障涂层在循环氧化下的失效机制至关重要。
4.目前对于热障涂层数值模拟研究中假设氧化层厚度均匀变化,忽略了氧化层局部非均匀生长导致的应力集中,且没有讨论界面法向应力与切向应力耦合作用与裂纹萌生之间的联系。本发明通过多物理场耦合模拟得到热障涂层在循环氧化下氧化层的生长规律及应力演化结果,并通过引入反映界面应力状态的参数,从而更加精确地分析涂层的失效机制。
技术实现要素:5.本发明要解决的技术问题为:克服现有技术的不足,提供热障涂层循环氧化下失效机制的研究方法,能够反映热障涂层在循环氧化下涂层内部及界面的应力分布及演化结果,用于分析涂层失效机制。
6.本发明解决上述技术问题采用的技术方案为:一种基于数值仿真的热障涂层循环氧化失效机制研究方法,用以研究热障涂层在加热-保温-冷却的工作环境下发生剥落失效的机制。通过建立循环氧化下余弦界面形貌的热障涂层代表性构元,模拟得到氧化层生长规律及热障涂层应力分布结果,通过引入反映界面应力状态的参数对界面裂纹进行评价,结合热障涂层循环氧化实验结果分析失效机制,实现步骤如下:
7.第一步:对氧化层生长模型进行简化假设:(1)假设氧化层生长仅在保温期间发生;(2)假设氧化层内为纯氧化铝;(3)只考虑氧化层向粘结层方向生长;(4)假设陶瓷层内的氧气扩散不受限制,即氧气扩散速率为无穷大;(5)未考虑应力对氧扩散的影响。在多物
理场耦合仿真软件中结合热障涂层循环氧化下化学扩散场、化学反应场控制方程建立氧化层生长有限元模型;
8.第二步:利用所述第一步中建立的生长有限元模型,在此基础上叠加循环热载荷(其中加热、冷却均为对流条件),结合本构关系,通过多物理场耦合仿真软件进行热障涂层循环氧化模拟,从而得到热障涂层在热力化耦合作用下的应力场分布及演化结果;
9.第三步:利用所述第二步循环氧化下的应力演化模拟得到氧化层内部、氧化层/陶瓷层界面及氧化层/粘结层界面应力分布及演化结果,结合氧化层生长规律分析氧化层内部及界面处应力分布情况,通过引入反映界面应力状态的参数β,建立了耦合界面处的法向应力与切向应力的裂纹萌生判据,即当时,界面会萌生裂纹,并与实验观测的涂层失效模式相结合,分析涂层的失效机制。至此,完成所述热障涂层循环氧化下失效机制的研究工作。
10.所述第一步中化学扩散场、化学反应场控制方程:
[0011][0012]
其中,c为氧气的浓度,n为氧化层体积分数,dc为氧扩散系数,g为化学反应速率常数,m为氧在al2o3中的摩尔浓度。
[0013]
所述第二步中本构关系:
[0014][0015]
其中,ε为应变张量,λ、μ为拉梅常数,σ为应力张量,σ
kk
为主应力之和,α
t
为热膨胀系数,t为温度,t0为初始温度,i为单位矩阵,αn为化学反应和应变的耦合系数,n为氧化层体积分数。
[0016]
所述第三步中,反映界面应力状态的参数:
[0017][0018]
其中,其中σn为法向应力,τ
xy
为切向应力,[σn]为纯拉伸模式的界面韧性,[τ
xy
]为纯剪切模式的界面韧性。
[0019]
本发明与现有技术相比的优点在于:
[0020]
(1)本发明通过多物理场耦合模拟得到热障涂层在循环氧化下的生长规律、涂层应力场分布及演化规律,从而考虑了氧化层局部非均匀生长导致的应力集中。
[0021]
(2)本发明考虑了热障涂层在经历了加热-保温-冷却过程后应力变化对涂层失效的影响。现有研究方法只关注了等温条件下氧化层生长带来的应力变化。
[0022]
(3)本发明通过引入反映界面应力状态的参数,将界面处的法向应力与切向应力与界面裂纹萌生相关联。
附图说明
[0023]
图1为本发明的一种基于数值仿真的热障涂层循环氧化失效机制研究方法实施流程;
[0024]
图2为本次举例的热障涂层有限元模型;
[0025]
图3为本次举例的氧化层生长规律模拟结果;
[0026]
图4为本次举例的氧化层/陶瓷层界面循环氧化下应力σy分布及演化模拟结果;
[0027]
图5为本次举例的氧化层内部循环氧化下应力σy分布及演化模拟结果;
[0028]
图6为本次举例的循环氧化下,氧化层/粘结层界面波峰应力σy随氧化层厚度的变化规律;
[0029]
图7为本次举例的陶瓷层内部循环氧化下应力σy分布及演化模拟结果;
[0030]
图8为本次举例的循环氧化下,陶瓷层边界波峰/波谷中心应力σy随氧化层厚度的变化规律;
[0031]
图9为本次举例的氧化层/陶瓷层界面应力状态参数β的分布规律;
[0032]
图10为本次举例的氧化层/粘结层界面应力状态参数β的分布规律。
具体实施方式
[0033]
下面结合附图,对本发明一种基于数值仿真的热障涂层循环氧化失效机制研究方法技术方案做进一步说明。如图1所示,本发明涉及一种基于数值仿真的热障涂层循环氧化失效机制研究方法,实现步骤如下:
[0034]
第一步:对氧化层生长模型进行简化假设:(1)假设氧化层生长仅在保温期间发生;(2)假设氧化层内为纯氧化铝;(3)只考虑氧化层向粘结层方向生长;(4)假设陶瓷层内的氧气扩散不受限制,即氧气扩散速率为无穷大;(5)未考虑应力对氧扩散的影响。在comsol multiphysics多物理场耦合仿真软件中结合热障涂层循环氧化下的化学扩散场、化学反应场控制方程建立氧化层生长有限元模型,如图2所示,将界面形貌拟合成正弦函数y=acos(2πx/λ),其中幅值a为15μm,波长λ为60μm,四层平均厚度分别为200μm、100μm、1μm和1200μm。模型底端y方向位移固定,左边界x方向位移固定,即v(x,y)|
y=0
=0,u(x,y)|
y=0
=0。模型右边界通过耦合约束限制相同的x方向位移。热障涂层模型的氧扩散场初始条件为:陶瓷层/氧化层界面的氧浓度为1.55mol/m3,粘结层的初始氧浓度为0mol/m3其中,化学扩散场、化学反应场控制方程如下:
[0035][0036]
其中,c为氧气的浓度,n为氧化层体积分数,dc表示氧扩散系数,g表示化学反应速率常数,m表示氧在al2o3中的摩尔浓度。
[0037]
第二步:利用所述第一步中建立的生长模型,在此基础上叠加循环热载荷,结合本构关系,通过comsol multiphysics多物理场耦合仿真软件中的固体力学、固体传热、稀物质传递以及对流扩散模块进行热障涂层循环氧化模拟,涂层的材料参数如表1所示,氧化生长参数如表2所示。循环热载荷为:加热保温45分钟(温度1000℃),冷却15分钟至室温(20℃),加热、冷却均为对流条件,从而得到热障涂层在热力化耦合作用下的应力场分布及演化结果。所述本构关系为:
[0038][0039]
其中,ε为应变张量,λ、μ为拉梅常数,σ为应力张量,σ
kk
为主应力之和,α
t
为热膨胀系数,t为温度,t0为初始温度,i为单位矩阵,αn为化学反应和应变的耦合系数,n为氧化层体积分数。
[0040]
表1
[0041][0042]
表2
[0043][0044]
第三步:利用所述第二步循环氧化模拟得到氧化层厚度(h
tgo
)及粗糙度演化规律,在本例中,界面粗糙度随着氧化层增厚而减小,如图3所示。进一步得到氧化层波峰波谷厚度变化规律,在本例中氧化层波峰厚度增长速度大于波谷厚度增长速度,从而导致了氧化层粗糙度减小,如图4所示。利用所述第二步中的循环氧化下的应力演化模拟得到氧化层内部、氧化层/陶瓷层界面及氧化层/粘结层界面应力分布及演化结果,在本例中,循环氧化下的氧化层/粘结层界面、陶瓷层边界波峰/波谷中心的拉应力σy均随着循环次数增加而增大,如图5—图8所示。结合氧化层演化规律分析氧化层内部及界面处应力分布情况,通过引入反映界面应力状态的参数,建立了耦合界面处法向应力与切向应力的裂纹萌生判据,即当时,界面会出现萌生裂纹。在本例中对于氧化层/陶瓷层界面,[σn]=200mpa、[τ
xy
]=200mpa,对于氧化层/粘结层界面,[σn]=100mpa、[τ
xy
]=200mpa,通过应力坐标变换可以计算出界面应力及相应的β值,如图9、图10所示,可知裂纹易在氧化层/陶瓷层界面波谷处及氧化层/粘结层界面波峰处萌生。至此,完成所述热障涂
层循环氧化下失效机制的研究工作。
[0045]
提供以上实例仅仅是为了描述本发明的目的,而并非要限制本发明的范围。本发明的范围由所附权利要求限定。不脱离本发明的精神和原理而做出的各种等同替换和修改,均应涵盖在本发明的范围之内。