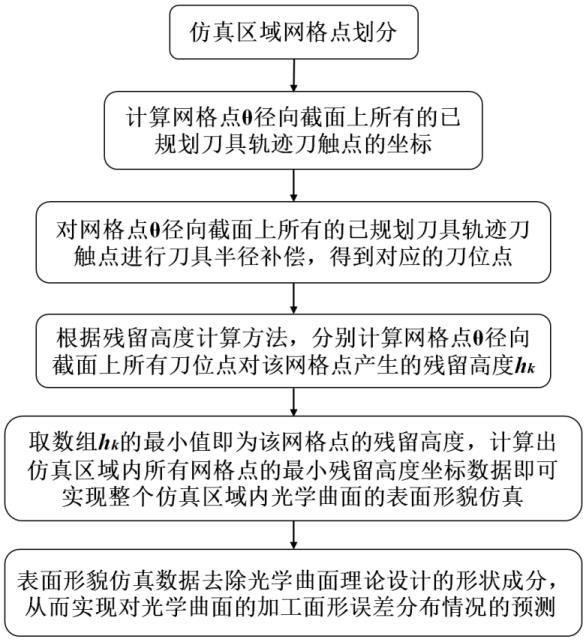
1.本发明涉及超精密加工技术领域,具体涉及一种基于超精密车削的光学曲面表面形貌仿真方法。
背景技术:2.超精密单点金刚石车削加工具有较高的加工精度和加工效率,被广泛用于光学曲面的加工制造,通过在实际加工前对超精密车削光学曲面的表面形貌进行仿真,优化车削参数,无需进行多次昂贵费时的试错实验,节约了加工成本和时间。目前,表面形貌仿真模型大都基于平面元件而言,较少基于光学曲面等进行形貌仿真,并且,很少涉及在形貌仿真中考虑已规划刀具轨迹的刀具半径补偿对形貌仿真的影响。
技术实现要素:3.本发明提供一种基于超精密车削的光学曲面表面形貌仿真方法,在形貌仿真中考虑了已规划刀具轨迹的刀具半径补偿对形貌仿真的影响,通过形貌仿真预测实际加工的表面形貌和加工面形误差,避免了进行多次昂贵费时的试错实验。
4.本发明采取的技术方案是,一种基于超精密车削的光学曲面表面形貌仿真方法,包括如下步骤:步骤(1):对仿真区域进行网格点划分,设定表面形貌仿真区域l
x
×
ly,l
x
代表仿真区域的长度,ly代表仿真区域的宽度,m
x
和my分别代表x和y方向的仿真区域分辨率,将仿真区域的中心设置为光学曲面加工的圆心,仿真区域内第(i,j)网格点的坐标表示为(x
i,j
,y
i,j
),并将网格点(x
i,j
,y
i,j
)转换为极坐标(ρ,θ),其中,ρ表示网格点(x
i,j
,y
i,j
)在极坐标系下的极径,θ表示网格点(x
i,j
,y
i,j
)在极坐标系下的极角;步骤(2):计算网格点(x
i,j
,y
i,j
)在θ径向截面上所有的刀具轨迹刀触点的极坐标半径ρk;步骤(3):对求得的网格点(x
i,j
,y
i,j
)在θ径向截面上所有的刀具轨迹刀触点(ρk,θk,zk)进行与已规划刀具轨迹模型相同的刀具半径补偿,得到网格点(x
i,j
,y
i,j
)在θ径向截面上所有的刀具轨迹刀位点(ρk',θk',zk'); 其中,θk表示在柱坐标系下刀具轨迹刀触点的极角,zk表示在柱坐标系下刀具轨迹刀触点的z坐标值,ρk'为刀具轨迹刀位点的极坐标半径,θk'为柱坐标系下刀具轨迹刀位点的极角,zk'为柱坐标系下刀具轨迹刀位点的z坐标值,k=
́
0,1,
…
,(rw/f)
́
,f为刀具进给速度, rw为工件半径;步骤(4):根据残留高度计算方法,分别计算网格点(x
i,j
,y
i,j
)在θ径向截面上所有的刀具轨迹刀位点在网格点(x
i,j
,y
i,j
)产生的残留高度hk,并且取其中最小值作为网格点(x
i,j
,y
i,j
)处的z坐标值z
i,j
;计算出仿真区域内所有网格点的最小残留高度坐标数据即可实现整个仿真区域内光学曲面的表面形貌仿真;步骤(5):将表面形貌仿真数据去除光学曲面理论设计的形状成分,从而实现对光学曲面的加工面形误差分布情况的预测。
5.进一步的,所述步骤(1)中,所述仿真区域内第(i,j)网格点的坐标(x
i,j
,y
i,j
)为:式中,i=1,2,3,
…
(l
x
/m
x
),j=1,2,3,
…
(ly/my);以及所述将网格点(x
i,j
,y
i,j
)转换为极坐标(ρ,θ)的表达式为:。
6.进一步的,所述步骤(2)中,计算网格点(x
i,j
,y
i,j
)在θ径向截面上所有的刀具轨迹刀触点经历的极坐标半径ρk的表达式为:式中,θ∈(0,2π),k=0,1,
…
(rw/f),f为刀具进给速度, rw为工件半径。
7.进一步的,所述步骤(4)中,计算网格点(x
i,j
,y
i,j
)在θ径向截面上所有的刀具轨迹刀位点在网格点(x
i,j
,y
i,j
)产生的残留高度hk的表达式为:式中,rt为刀具刀尖圆弧半径;并且取其中最小值作为网格点(x
i,j
,y
i,j
)处的z坐标值z
i,j
:z
i,j
=min(hk)。
8.进一步的,所述步骤(5)中,将表面形貌仿真数据去除光学曲面理论设计的形状成分,从而实现对光学曲面的加工面形误差分布情况的预测采用以下表达式实现:δ
i,j
=z
i,j
−zi,j
其中,δ
i,j
为网格点(x
i,j
,y
i,j
)处的加工误差,z
i,j
为步骤(4)得到的网格点(x
i,j
,y
i,j
)处的z坐标值,z
i,j
为通过光学曲面理论设计模型计算得到的网格点(x
i,j
,y
i,j
)处的z坐标。
9.本发明的有益效果是:通过对仿真区域进行网格划分,基于已规划刀具轨迹计算网格点z坐标,实现光学曲面的表面形貌仿真,并在形貌仿真中考虑已规划刀具轨迹的刀具半径补偿对形貌仿真的影响,弥补了传统形貌仿真中单一考虑基本车削参数的不足,连通了已规划刀具轨迹和形貌仿真之间的关系,使得形貌仿真结果更加贴合实际加工情况。本发明可以在车削实验前进行多次仿真预测实际加工工件的表面形貌,优化实验参数,验证已规划刀具轨迹是否满足加工要求,无需进行多次昂贵费时的试错实验。
附图说明
10.图1是本发明基于超精密车削的光学曲面表面形貌仿真方法的步骤流程图;图2是刀具轨迹和仿真网格点示意图;
图3是实例已规划刀具轨迹的刀具半径补偿示意图;图4是光学曲面加工表面形貌仿真图;图5是光学曲面加工误差预测仿真图。
具体实施方式
11.为使本发明的目的、技术方案以及优点更加清楚明白,下面结合附图和实施例对本发明作进一步详细的表述,显然,以下实施例只是为了用以解释本发明,并不用于限定性本发明,不能以此限定本发明的保护范围。
12.图1是本发明的步骤流程图,一种基于超精密车削的光学曲面表面形貌仿真方法,包括以下步骤:(1)对仿真区域进行网格点划分,设定表面形貌仿真区域l
x
×
ly,l
x
代表仿真区域的长度,ly代表仿真区域的宽度,m
x
和my分别代表x和y方向的仿真区域分辨率,将仿真区域的中心设置为光学曲面加工的圆心,仿真区域内第(i,j)网格点的坐标可以表示为(x
i,j
,y
i,j
),并将(x
i,j
,y
i,j
)转换为极坐标(ρ,θ),如图2所示;所述步骤1中设定表面形貌仿真区域l
x
×
ly,m
x
和my分别代表x和y方向的仿真区域分辨率,仿真区域内第(i,j)网格点的坐标(x
i,j
,y
i,j
)为:式中,i=1,2,3,
…
(l
x
/m
x
),j=1,2,3,
…
(ly/my);将网格点(x
i,j
,y
i,j
)转换为极坐标(ρ,θ):(2)计算网格点(x
i,j
,y
i,j
)在θ径向截面上所有的刀具轨迹刀触点经历的极坐标半径ρk;所述步骤2中计算网格点(x
i,j
,y
i,j
)在θ径向截面上所有的刀具轨迹刀触点经历的极坐标半径ρk表达式为:式中,θ∈(0,2π),k=0,1,
…
(rw/f),f为刀具进给速度,rw为工件半径;本实施例中光学曲面以非球面为例,其数学表达式为:式中,c=0.02,k=-0.1,ρ2=x2+y2;
(3)对求得的网格点(x
i,j
,y
i,j
)在θ径向截面上所有的刀具轨迹刀触点(ρk,θk,zk)进行与已规划刀具轨迹模型相同的刀具半径补偿,得到网格点(x
i,j
,y
i,j
)在θ径向截面上所有的刀具轨迹刀位点(ρk',θk',zk');在本实施例中,刀具半径补偿方法以z向近似补偿为例,如图3所示,f(ρ)为曲线方程,刀触点为点pk(ρk,zk),b点为刀具半径补偿后刀尖圆弧与曲线相切的点,由于pk点和b点相邻很近,可近似认为曲线在pk点处的斜率等于b点处的斜率,由此可得:进而可得:所以,得到刀具在z向的补偿量为:
∆
z=rt/cosφ
−
rt刀位点z坐标值为:zk'=zk+
∆
z+rt其中,rt为刀具刀尖圆弧半径。
13.(4)根据残留高度计算方法,分别计算网格点(x
i,j
,y
i,j
)在θ径向截面上所有可能的刀具轨迹刀位点在网格点(x
i,j
,y
i,j
)产生的残留高度hk,并且取其中最小值即为网格点(x
i,j
,y
i,j
)处的z坐标值z
i,j
;所述步骤(4)中计算网格点(x
i,j
,y
i,j
)在θ径向截面上所有可能的刀具轨迹刀位点在网格点(x
i,j
,y
i,j
)产生的残留高度hk:式中,rt为刀具刀尖圆弧半径;并且取其中最小值即为网格点(x
i,j
,y
i,j
)处的z坐标值z
i,j
:z
i,j
=min(hk)计算出仿真区域内所有网格点的最小残留高度坐标数据即可实现整个仿真区域内光学曲面的表面形貌仿真,如图4所示;(5)将表面形貌仿真数据去除光学曲面理论设计的形状成分,从而实现对光学曲面的加工面形误差分布情况的预测,如图5所示。
14.所述步骤(5)中将表面形貌仿真数据去除光学曲面理论设计的形状成分,从而实现对光学曲面的加工面形误差分布情况的预测采用以下表达式:δ
i,j
=z
i,j
−zi,j
其中,δ
i,j
为网格点(x
i,j
,y
i,j
)处的加工误差,z
i,j
为上述表面形貌仿真模型计算得到的网格点(x
i,j
,y
i,j
)处的z坐标,z
i,j
为光学曲面理论设计模型计算得到的网格点(x
i,j
,y
i,j
)处的z坐标。
15.以上所述实施例仅是为充分说明发明而所举的较佳的实施例,本发明的保护范围不限于此。本技术领域的技术人员在本发明基础上所作的等同替代或变换,均在本发明的保护范围之内。本发明的保护范围以权利要求书为准。