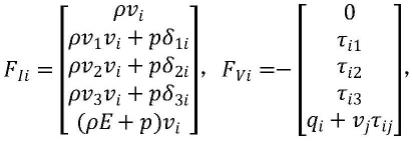
1.本发明涉及的是一种叶轮机械领域的技术,具体是一种轴流压气机篦齿封严腔优化流动性实现方法。
背景技术:2.轴流压气机是航空发动机和地面燃气轮机的重要组成部分之一,其带内环的静子叶片叶根内环处带有耐磨涂层,其与转子轮盘上加工的篦齿共同形成了篦齿封严腔,两者之间存在径向间隙,以防止转静子在工作时的刮磨。现有篦齿封严腔的几何形状较为单一,且设计方法一般是针对某几个特定的几何参数进行设计与分析,但是封严腔壁面线的几何自由度较高,现有设计方法具有局限性,目前缺乏较为有效的轴流压气机篦齿封严腔的优化几何实现方法。
技术实现要素:3.本发明针对现有篦齿封严腔的几何形状较为单一,设计方法局限性较高的问题,提出了一种轴流压气机篦齿封严腔优化流动性实现方法,通过分析篦齿封严腔内的流动特征,对封严腔内部进行分区,并对各区流动性进行针对性设计,得到优化几何结构,从而实现降低静子叶片的总压损失,同时提高其增压能力的目标。
4.本发明是通过以下技术方案实现的:
5.本发明涉及一种轴流压气机篦齿封严腔优化流动性实现方法,根据篦齿封严腔内的流动特征,将篦齿封严腔内部划分为流动控制区和速度场匹配区;然后结合实际工程约束,设计出篦齿封严腔静止上端壁的优化几何;最后通过cfd数值模拟计算对优化几何进行流动分析,并对其对于静子叶片的性能影响进行评价。
6.所述的流动控制区,具体位于近进口处、篦齿前和篦齿间,用于流动阻滞,减小泄漏损失,该流动控制区的截面形状满足:位于近进口处和篦齿间为一条直线,篦齿前为两条圆弧线,篦齿间为一条直线。
7.所述的速度场匹配区,具体位于封严腔的篦齿后和近出口处,用于控制离开封严腔的流动与主流流动的速度场相匹配以减小掺混损失,该速度场匹配区的截面形状满足:篦齿后为两条直线,近出口处为一条圆弧线。
8.所述的速度场包括径向速度、周向速度与轴向速度。
9.所述的实际工程约束是指实际加工中,因轴流压气机安全工作和制造装配需求而考虑的约束。
10.所述的cfd数值模拟计算是指:采用数值模拟方法求解雷诺平均navier-stokes方程:其中:为守恒型参数向量,为守恒型参数向量,和分别是无粘矢通量和
粘性矢通量,qi为热源项,τ
ij
为应力,δ
ij
为克罗内克符号,q为源项,q为源项,代表外作用力,wf代表这些外作用力所做的功,
11.所述的性能是指静子叶片的总压损失系数ω与压力系数c
p
。分别为和和其中:p
*
为总压,p为静压,下标in和out分别为进口和出口。这些参数通过在完成数值模拟计算后,对整个进、出口平面计算总压或静压的质量平均值而得。为了得到更优的性能,应使得总压损失系数尽可能小,压力系数尽可能高。技术效果
12.本发明通过分区的方式,根据不同区内的流动特征进行针对性设计,确保静子叶片的性能最优。本发明提高了轴流压气机篦齿封严腔的设计效率,缩短了航空发动机或地面燃气轮机的研制时间,节省了研发时间和人力成本。
附图说明
13.图1为通过优化设计方法得到的优化型篦齿封严腔几何与流动分区示意图;
14.图2为篦齿封严腔的约束示意图,其中粗线为设计对象;
15.图3为优化型篦齿封严腔内部极限流线图;
16.图4为优化设计前的原型篦齿封严腔几何及其内部极限流线图。
具体实施方式
17.如图1所示,为本实施例涉及一种轴流压气机篦齿封严腔优化流动性实现方法,其中x轴和y轴原点位于篦齿封严腔左下角;该方法包括:
18.1)确定流动控制区中靠近封严腔进口处的封严腔几何形状:靠近封严腔进口处几何的流动控制目的主要为尽可能阻碍主流通道内的流动进入封严腔,以减小泄漏流流量与泄漏损失。在本实施例中,该处的剖面形状为一条直线,其与主流之间的夹角为钝角,用于阻碍气流进入封严腔。
19.2)确定流动控制区中处于篦齿前的封严腔几何形状:篦齿前的流动从进口进入,准备通过篦齿,该区的几何需要对封严腔内的漩涡进行流动控制,尽可能减小泄漏流流量。在本实施例中,利用曲率流动控制方法,形成充满整个通道的强漩涡,达到漩涡阻滞作用,该区的几何形状由两条圆弧线构成。
20.所述的曲率流动控制方法,即通过控制流道面积的收缩与扩张和壁面曲线的曲率,来控制流动的加减速。
21.所述的两条圆弧线具体为:按顺流方向,第一条圆弧线的半径为7.28mm,圆心位于
x=76.07mm,y=20.85mm处,圆心角为69
°
,第二条圆弧线的半径为8.71mm,圆心位于x=69.92mm,y=6.09mm处,圆心角为63.97
°
。
22.3)确定流动控制区中篦齿所在位置的封严腔几何形状:篦齿所在的位置流动控制的目的同样是减小泄漏流流量,主要需要控制篦齿尖间隙尽可能小。在本实施例中,将该处的剖面形状为一条平直线,篦齿间隙值取1.1mm。
23.4)确定速度场匹配区中篦齿后的封严腔几何形状:篦齿后的流动已通过篦齿,准备通过封严腔出口进入主流。该速度场匹配区需要对封严腔内进行流动控制,使得封严腔内流动与主流流动的速度场相匹配。在本实施例中,该处的剖面形状为扩张型,由两条直线组成,篦齿封严腔的横截面积逐渐增大,以降低泄漏流的速度,达到匹配主流速度场的目的。
24.所述的两条直线之间的夹角为173.2
°
。
25.5)确定速度场匹配区中靠近封严腔出口处的封严腔几何形状:靠近封严腔出口处需更针对性地考虑封严腔出口与主流之间的掺混作用。在本实施例中,该处的剖面形状为一条圆弧线,圆弧在封严腔出口处的切线与主流方向之间呈锐角,有助于泄漏流顺畅地进入主流,减小掺混损失。
26.所述的圆弧线的半径为5.6mm,圆心位于x=8.87mm,y=20mm处,圆心角为118.8
°
。
27.6)根据上述设计方法,再根据实际工程约束,利用简单圆弧和直线方程设计出如图1所示的优化型篦齿封严腔几何。在该坐标系下,篦齿封严腔的几何形状表达式如下:在流动控制区内,近进口处的直线方程为y=0.98x-63.88(81.34≤x≤88.35),篦齿前处的两条圆弧线方程按顺流方向分别为(x-76.07)2+(y-20.85)2=7.282(73.26≤x≤81.34,y≤15.82)和(x-69.92)2+(y-6.09)2=8.712(64.16≤x≤73.26,y≥12.62),篦齿间处的直线方程为y=12.62(30.67≤x≤64.16)。在速度场匹配区内,篦齿后处的直线方程按顺流方向分别为y=-0.119x+16.27(15.73≤x≤30.67)和y=14.4(8.87≤x≤15.73)。近出口处的圆弧线方程为(x-8.87)2+(y-20)2=5.62(x≤8.87,14.4≤y≤22.7),其中:x、y的单位均为mm。
28.所述的实际工程约束包括:
29.①
壁面横向段与叶片间距离的约束,该处的壁面横向段往下不能低于篦齿高度,同时往上不能距离叶片过近,因此要求该横向段与叶片间的距离为3mm至10mm之间;
30.②
靠近进口的竖直段处,静止壁面与转动壁面间距离的约束;
31.③
靠近出口的竖直段处,静止壁面与转动壁面间距离的约束,该距离不能过小。
32.④
靠近进口的竖直段处,静止壁面与叶片之间距离的约束;
33.⑤
靠近出口的竖直段处,静止壁面与叶片之间距离的约束,该距离不能过小。
34.在对上述约束
②
至
⑤
综合考虑后,确定约束
②
处的距离需大于5mm,约束
③
处的距离需大于3mm,约束
④
与约束
⑤
处的距离均需大于3.2mm。
35.7)在完成了优化型的剖面形状后,利用cfd数值模拟计算进行流动分析。图3与图4展示了通过上述设计方法得到的优化型篦齿封严腔与优化设计前的原型篦齿封严腔内部的极限流线图。由图可见,相比于原型,优化型封严腔内部的漩涡结构在1区和2区有较大的改变。由于1区通道横截面积的扩大,单漩涡结构变为了双漩涡结构,2区内近篦齿的涡移动至封严腔进口附近,且涡结构明显增大,几乎覆盖了整个封严腔前部。相比于原型,优化型封严腔内近进口处的涡结构更能起到阻碍泄漏流的作用。对于近出口的4区和5区,原型与
优化型的涡结构差异较小。优化型的流线在近出口处与封严腔壁面贴合更加紧密,说明该几何形状起到了使泄漏流与主流的速度场更加匹配的作用,达到了减小掺混损失的目的。
36.8)对优化型对于静子叶片性能的影响进行评价。该优化型与原型在20%叶高以下的性能参数对比如表1所示。
37.表1优化型与原型的20%叶高以下性能参数对比
38.由表可见,相比于原型,优化型20%叶高以下的总压损失有了明显的降低,降低率达到12.23%,在总压损失降低的同时,叶片的增压能力也有小幅度的提升,压力系数的增长率为1.57%,说明该设计得到的优化型既可以降低总压损失,又可以提升叶片的增压能力,达到了优化设计的目的。
39.上述具体实施可由本领域技术人员在不背离本发明原理和宗旨的前提下以不同的方式对其进行局部调整,本发明的保护范围以权利要求书为准且不由上述具体实施所限,在其范围内的各个实现方案均受本发明之约束。