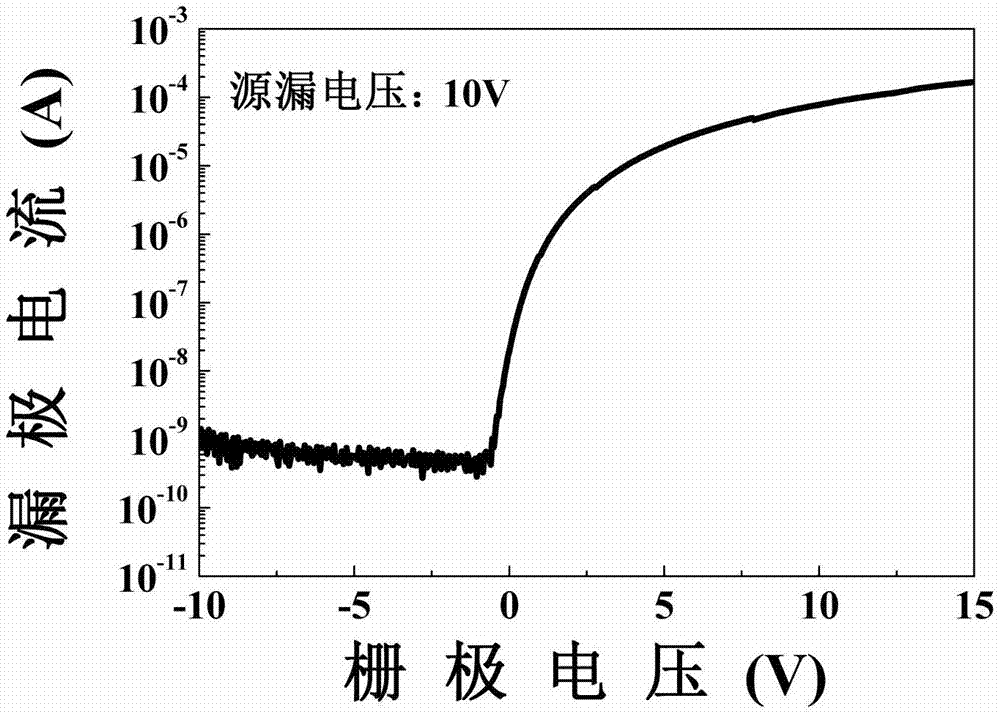
本发明涉及薄膜晶体管
技术领域:
,具体是一种以锌锡铝钾氧化物为沟道层的薄膜晶体管及其制备方法。
背景技术:
:薄膜晶体管(tft)作为有源矩阵有机发光二极管显示(activematrixoriganiclight-emittingdiode,amoled)技术中的核心元件,其包括基底、沟道层、绝缘层、栅极、源极和漏极等几个重要组成部分。目前,基于透明非晶氧化物半导体(taos)薄膜作为沟道层的氧化物tft,凭借其迁移率高、可见光透明性好以及均匀性优良等特点成为最具潜力应用于amoled的新一代tft技术。在氧化物tft中,基于铟嫁锌氧化物(in-ga-zn-o,igzo)材料的沟道层tft的研究已取得了一些实质性的进展,但考虑到in、ga的消耗与日聚增,价格持续上涨,开发不含in、ga的新型taos沟道层材料是本领域的重点研究方向。锌锡氧化物(zn-sn-o,zto)具备良好的环境稳定性、高的可见光透过率、易形成平整的非晶薄膜以及组成元素丰富等优点,有潜力用于制备不含in、ga的高迁移率氧化物沟道层材料。然而,zto中天然存在着氧空位及金属离子间隙等缺陷,其作为tft沟道层时载流子浓度过高,导致tft常工作于耗尽模式且呈现出高的关态电流,从而产生大的能耗。尽管本研究领域目前将一些低负电性的元素(例如,la、al、hf、w、si、b、li、s、ba等)引入到zto材料中,以通过抑制zto材料中氧空位的形成来降低其电子载流子浓度,最终降低ztotft的关态电流。然而,研究表明zto材料的电子迁移率也会随上述掺杂元素含量的增加被减小,导致tft的饱和迁移率急剧被降低;此外,由于上述这些低负电性元素的离子往往为高价态(+3价~+6价),很难通过改变高价态杂掺元素含量对zto材料载流子浓度实现精确调控,使得高价态元素的掺杂在降低tft关态电流的同时,器件开态电流也被大幅度的降低,导致tft呈现出较低的开关比。因此,能否对zto薄膜的载流子浓度实现精确调控已成为研制兼具低关态电流、高饱和迁移率、高的开关比以及工作于增强模式的ztotft器件的关键。技术实现要素:为了解决现有技术中存在的上述技术问题,本发明提供一种低成本且兼具良好电学性能及低能耗的以锌锡铝钾氧化物为沟道层的薄膜晶体管及其制备方法。一种以锌锡铝钾氧化物为沟道层的薄膜晶体管的制备方法,包括如下步骤:(1)将zn(c2h3o2)2·5h2o、sncl2·2h2o、alcl3·6h2o和kcl·3h2o溶于乙二醇中,以乙醇胺作为稳定剂,50-80℃下搅拌24-48小时形成透明的前驱体溶液;(2)将所得的前驱体溶液静置老化后,在玻璃基底上浸渍提拉镀膜,将提拉结束后的湿膜放入烘箱内,在200-250℃温度下预处理20-60分钟,然后经350-500℃退火1-5小时,得到锌锡铝钾氧化物沟道层;(3)结合掩膜,利用真空热蒸发的方法在步骤(2)所得锌锡铝钾氧化物沟道层上制备源电极和漏电极;(4)采用浸渍提拉工艺,在包含源电极和漏电极的锌锡铝钾氧化物沟道层上用溶有聚四乙烯苯酚的有机溶液制备pvp绝缘层;(5)结合掩膜,利用真空热蒸发的方法在pvp绝缘层上面制备栅电极,即得以锌锡铝钾氧化物为沟道层的薄膜晶体管。所述步骤(1),其中乙醇胺与乙二醇体积之比为(0.1:100-1:100)。所述步骤(1),其中前驱体溶液浓度为0.2-0.6m,zn(c2h3o2)2·5h2o、sncl22h2o、alcl3·6h2o、kcl·3h2o中锌离子、锡离子、铝离子、钾离子的摩尔比为1:2:0.07:0.1。所述步骤(2)中,在玻璃基底上浸渍提拉镀膜,其提拉速度为0.1-0.5mm/s。通过提拉速度为0.1-0.5mm/s的渍提拉镀膜,从而制备了表面平整(薄膜的平均粗糙度和方均根粗糙度均低于1nm)、厚度均匀的锌锡铝钾氧化物薄膜,这有利于沟道层与绝缘层间良好界面的形成,有助于提升器件的饱和迁移率。所述步骤(2)中,前驱体溶液在玻璃基底上浸渍提拉、烘箱内烘烤及退火的次数均为2-4次。通过控制浸渍提拉、烘箱内烘烤及退火的次数,从而形成了致密的锌锡铝钾氧化物薄膜,降低了因半导体沟道层中缺陷态对电子载流子捕获或散射造成器件饱和迁移率劣化的影响。所述步骤(3)中,采用真空热蒸发的方法,具体操作步骤是:以氧化铝为掩膜制备源电极、漏电极,控制热蒸发电流为65a,热蒸发电压为60-80v,且最终得到的薄膜晶体管的源电极和漏电极均为金属铝电极。以获得与锌锡铝钾氧化物沟道层欧姆接触的源电极和漏电极。所述步骤(4)中,聚四乙烯苯酚溶液浓度为75mg/ml,有机溶剂为无水乙醇或丙酮;浸渍提拉工艺中控制提拉速度为1.0mm/s,提拉2次,提拉后于70-120℃中烘烤60分钟。此条件下可以制备得到具备较低漏电流密度、表面平整(薄膜的平均粗糙度和方均根粗糙度均低于1nm)、厚度均匀、致密的绝缘层,这不仅有利于降低器件的漏电流,还劣化了因半导体沟道层/绝缘层界面处的缺陷态对电子载流子捕获或散射造成器件饱和迁移率恶化的影响。所述步骤(5)中,利用真空热蒸发的方法在pvp绝缘层上面制备栅电极,是以氧化铝为掩膜制备栅电极,并控制热蒸发电流为65a,热蒸发电压为60-80v,且制备得到的薄膜晶体管的栅电极为金属铝电极。这样获得的栅电极具备低电阻率(<10-6ω·cm)的优势,有助于减少栅电极与源电极、漏电极间的rc信号延迟。对制备过程进行控制,使最终得到的薄膜晶体管的沟道层为厚度45-80nm的锌锡铝钾氧化物薄膜;绝缘层为厚度160nm的聚四乙烯苯酚薄膜;源电极、漏电极及栅电极均为厚度为80-120nm的金属铝薄膜。上述厚度的控制,是在保证薄膜晶体管器件具备高性能、低能耗的前提下,尽可能的降低其厚度,以满足器件小型化发展的趋势。目前,低成本的溶胶凝胶法制备tft的氧化物沟道层近年来受到了研究人员的青睐。然而,相比传统溅射法而言,基于溶胶凝胶法制备氧化物沟道层的tft器件迁移率普遍偏低,而在240hz的8k4k超高清电流驱动的amoled显示中要求tft的迁移率至少需30cm2/vs以上,且基于溶胶凝胶法工艺的tft还存在漏电流过高的问题,因此,如果能够改善沟道层材料本身的性能,有利于促进基于溶胶凝胶法制备氧化物tft器件性能的提升。考虑到铝离子以及钾离子与氧的结合能力要高于锌或锡离子与氧的结合能力,理论上来讲,铝和钾共掺杂对zto体系的氧空位缺陷(提供电子载流子)能起到一定抑制效果。由于铝离子和钾离子分别为高金属价态(+3价)和低金属价态(+1价),铝和钾共掺杂可通过改变高金属价态铝离子(al3+)的掺杂含量对zto材料中的氧空位缺陷浓度起到粗调,通过调整低金属价态钾离子(k1+)的掺杂含量对zto材料中的氧空位缺陷浓度起到微调,以实现对zto薄膜的电子载流子浓度的精确调控。更值得一提的是铝离子以及钾离子的外层电子结构对方向的变化不敏感,将其引入非晶zto材料中,有望在分子比较无序的状态下使材料兼具比较高的电子迁移率。此外,铝元素以及钾元素无毒、来源丰富、价格低廉,还可以作为zto薄膜非晶态结构的稳定剂。上述优点使得锌锡铝钾氧化物材料如果被用作tft沟道层有望为基于低成本溶胶凝胶法制备兼具良好电学性能(tft的饱和迁移率>30cm2/vs、关态电流<10-9a、亚阈值摆幅<0.20v/decade以及开关比>106)及低能耗(tft具备接近于零且正的阈值电压以及漏电流<10-10a)的氧化物tft提供解决方案。与现有技术相比,本发明创造的技术效果体现在:本发明以锌锡铝钾氧化物材料作为沟道层,以有机聚四乙烯苯酚(pvp)材料作为绝缘层,以铝作为源、漏、栅电极,在普通玻璃基底上制备了顶栅共面结构的tft。本发明中,沟道层及介质层均采用溶胶凝胶法的浸渍提拉工艺来制备,源、漏、栅电极采用真空热蒸发的方法制备。最终得到了一种具有较高饱和迁移率62.3cm2/vs,较低亚阈值摆幅0.09v/decade,接近于零的阈值电压0.23v,较低的关态电流(<10-9a),较低的漏电流(<10-10a),开关比大于106以及工作于增强模式的锌锡铝钾氧化物薄膜晶体管。本发明为低成本制备高性能、低能耗的氧化物薄膜晶体管提供了可行性方案。附图说明图1是实施例1所得的以锌锡铝钾氧化物为沟道层的薄膜晶体管的转移特性曲线图。图2是实施例1所得的以锌锡铝钾氧化物为沟道层的薄膜晶体管的漏电流曲线图。具体实施方式下面结合具体的实施方式来对本发明的技术方案做进一步的限定,但要求保护的范围不仅局限于所作的描述。实施例1一种以锌锡铝钾氧化物为沟道层的薄膜晶体管,使用玻璃作为基底,以锌锡铝钾氧化物薄膜作为沟道层,以有机pvp薄膜作为绝缘层,以铝薄膜作为源电极、漏电极以及栅电极,制备顶栅共面结构的tft,并通过如下方法制备:(1)将分析纯的zn(c2h3o2)2·5h2o、sncl2·2h2o、alcl3·6h2o和kcl·3h2o溶于乙二醇中,以乙醇胺作为稳定剂,70℃下搅拌30小时形成透明的前驱体溶液,其中前驱体溶液浓度为0.2m,zn(c2h3o2)2·5h2o、sncl2·2h2o、alcl3·6h2o和kcl·3h2o中锌离子、锡离子、铝离子、钾离子的摩尔比为1:2:0.07:0.1,乙醇胺与乙二醇体积之比为0.2:100;(2)将所得的前驱体溶液静置72h老化后,在玻璃基底上以0.1mm/s的速度浸渍提拉镀膜,将提拉结束后的湿膜放入烘箱内,在250℃温度下预处理30分钟,然后经400℃退火4小时,前驱体溶液在玻璃基底上浸渍提拉、烘箱内烘烤及退火的次数均为3次,得到60nm厚的锌锡铝钾氧化物沟道层;(3)在沟道层上用宽长比为400μm/40μm的氧化铝掩膜制备120nm厚的金属铝薄膜作为源电极和漏电极,控制热蒸发电流为65a,热蒸发电压为80v,且最终得到的薄膜晶体管的源电极和漏电极均为金属铝电极;(4)将步骤(3)所得的含源、漏电极层的沟道层浸入pvp丙酮前驱体溶液,经提速为1.0mm/s的提拉涂覆后,置于温度为120℃的烘箱中烘烤60min,重复提拉涂覆以烘烤操作2次,形成厚度为160nm的有机pvp薄膜,作为绝缘层;所述pvp丙酮前驱体溶液是将sigma-aldrich公司的pvp粉末溶于丙酮溶剂中进行搅拌,得到浓度为75mg/ml的pvp丙酮前驱体溶液;(5)采用真空热蒸发的方法,在步骤(4)所得的绝缘层上,辅以氧化铝掩膜制备120nm厚的金属铝薄膜作为栅电极以氧化铝为掩膜制备栅电极,并控制热蒸发电流为65a,热蒸发电压为80v,且制备得到的薄膜晶体管的栅电极为金属铝电极,即得以锌锡铝钾氧化物为沟道层的薄膜晶体管。本实施例中,基于锌锡铝钾氧化物沟道层的tft器件的转移曲线如图1所示。可以得出,该器件工作于增强模式,具有较高饱和迁移率62.3cm2/vs,较低亚阈值摆幅0.09v/decade,接近于零的阈值电压0.23v,较低的关态电流(<10-9a)以及大于106开关比。从图2可以看出,该器件还具备有较小漏电流(<10-10a),说明该器件具备较低的能耗。实施例2一种以锌锡铝钾氧化物为沟道层的薄膜晶体管,使用玻璃作为基底,以锌锡铝钾氧化物薄膜作为沟道层,以有机pvp薄膜作为绝缘层,以铝薄膜作为源电极、漏电极以及栅电极,制备顶栅共面结构的tft,并通过如下方法制备:(1)将分析纯的zn(c2h3o2)2·5h2o、sncl2·2h2o、alcl3·6h2o和kcl·3h2o溶于乙二醇中,以乙醇胺作为稳定剂,50℃下搅拌24小时形成透明的前驱体溶液,其中前驱体溶液浓度为0.35m,zn(c2h3o2)2·5h2o、sncl2·2h2o、alcl3·6h2o和kcl·3h2o中锌离子、锡离子、铝离子、钾离子的摩尔比为1:2:0.07:0.1,乙醇胺与乙二醇体积之比为0.1:100;(2)将所得的前驱体溶液静置72h老化后,在玻璃基底上以0.3mm/s的速度浸渍提拉镀膜,将提拉结束后的湿膜放入烘箱内,在200℃温度下预处理20分钟,然后经350℃退火1小时,前驱体溶液在玻璃基底上浸渍提拉、烘箱内烘烤及退火的次数均为2次,得到50nm厚的锌锡铝钾氧化物沟道层;(3)在沟道层上用宽长比为400μm/40μm的氧化铝掩膜制备80nm厚的金属铝薄膜作为源电极和漏电极,控制热蒸发电流为65a,热蒸发电压为60v,且最终得到的薄膜晶体管的源电极和漏电极均为金属铝电极;(4)将步骤(3)所得的含源、漏电极层的沟道层浸入pvp丙酮前驱体溶液,经提速为1.0mm/s的提拉涂覆后,置于温度为70℃的烘箱中烘烤60min,重复提拉涂覆以烘烤操作2次,形成厚度为160nm的有机pvp薄膜,作为绝缘层;所述pvp前驱体溶液是将sigma-aldrich公司的pvp粉末溶于无水乙醇溶剂中进行搅拌,得到浓度为75mg/ml的pvp无水乙醇前驱体溶液;(5)采用真空热蒸发的方法,在步骤(4)所得的绝缘层上,辅以氧化铝掩膜制备100nm厚的金属铝薄膜作为栅电极以氧化铝为掩膜制备栅电极,并控制热蒸发电流为65a,热蒸发电压为55v,且制备得到的薄膜晶体管的栅电极为金属铝电极,即得以锌锡铝钾氧化物为沟道层的薄膜晶体管。本实施例中,以锌锡铝钾氧化物为沟道层的薄膜晶体管器件工作于增强模式,具有较高饱和迁移率51.7cm2/vs,较低亚阈值摆幅0.19v/decade,接近于零的阈值电压0.37v,较低的关态电流(<10-9a)、较小漏电流(<10-10a)以及大于106开关比。实施例3一种以锌锡铝钾氧化物为沟道层的薄膜晶体管,使用玻璃作为基底,以锌锡铝钾氧化物薄膜作为沟道层,以有机pvp薄膜作为绝缘层,以铝薄膜作为源电极、漏电极以及栅电极,制备顶栅共面结构的tft,并通过如下方法制备:(1)将分析纯的zn(c2h3o2)2·5h2o、sncl2·2h2o、alcl3·6h2o和kcl·3h2o溶于乙二醇中,以乙醇胺作为稳定剂,80℃下搅拌48小时形成透明的前驱体溶液,其中前驱体溶液浓度为0.6m,zn(c2h3o2)2·5h2o、sncl2·2h2o、alcl3·6h2o和kcl·3h2o中锌离子、锡离子、铝离子、钾离子的摩尔比为1:2:0.07:0.1,乙醇胺与乙二醇体积之比为1:100;(2)将所得的前驱体溶液静置72h老化后,在玻璃基底上以0.5mm/s的速度浸渍提拉镀膜,将提拉结束后的湿膜放入烘箱内,在250℃温度下预处理60分钟,然后经500℃退火5小时,前驱体溶液在玻璃基底上浸渍提拉、烘箱内烘烤及退火的次数均为4次,得到80nm厚的锌锡铝钾氧化物沟道层;(3)在沟道层上用宽长比为400μm/40μm的氧化铝掩膜制备120nm厚的金属铝薄膜作为源电极和漏电极,控制热蒸发电流为65a,热蒸发电压为80v,且最终得到的薄膜晶体管的源电极和漏电极均为金属铝电极;(4)将步骤(3)所得的含源、漏电极层的沟道层浸入pvp丙酮前驱体溶液,经提速为1.0mm/s的提拉涂覆后,置于温度为120℃的烘箱中烘烤60min,重复提拉涂覆以烘烤操作2次,形成厚度为160nm的有机pvp薄膜,作为绝缘层;所述pvp丙酮前驱体溶液是将sigma-aldrich公司的pvp粉末溶于丙酮溶剂中进行搅拌,得到浓度为75mg/ml的pvp丙酮前驱体溶液;(5)采用真空热蒸发的方法,在步骤(4)所得的绝缘层上,辅以氧化铝掩膜制备120nm厚的金属铝薄膜作为栅电极以氧化铝为掩膜制备栅电极,并控制热蒸发电流为65a,热蒸发电压为80v,且制备得到的薄膜晶体管的栅电极为金属铝电极,即得以锌锡铝钾氧化物为沟道层的薄膜晶体管。本实施例中,以锌锡铝钾氧化物为沟道层的薄膜晶体管器件工作于增强模式,具有较高饱和迁移率66.9cm2/vs,较低亚阈值摆幅0.16v/decade,接近于零的阈值电压0.15v,较低的关态电流(<10-9a)、较小漏电流(<10-10a)以及大于106开关比。将实施例1-3所得的以锌锡铝钾氧化物为沟道层的薄膜晶体管的饱和迁移率、亚阈值摆幅、阈值电压进行对比:饱和迁移率亚阈值摆幅阈值电压实施例162.3cm2/vs0.09v/decade0.23v实施例251.7cm2/vs0.19v/decade0.37v实施例366.9cm2/vs0.16v/decade0.15v以上数据可说明,本发明为低成本制备高性能、低能耗的氧化物薄膜晶体管提供了可行性方案最后,应当指出,以上实施例仅是本发明较有代表性的例子。显然,本发明的技术方案并不限于上述实施例,还可以有许多变形。本领域的普通技术人员能从本发明公开的内容直接导出或联想到的所有变形,均应认为是本发明的保护范围。当前第1页12