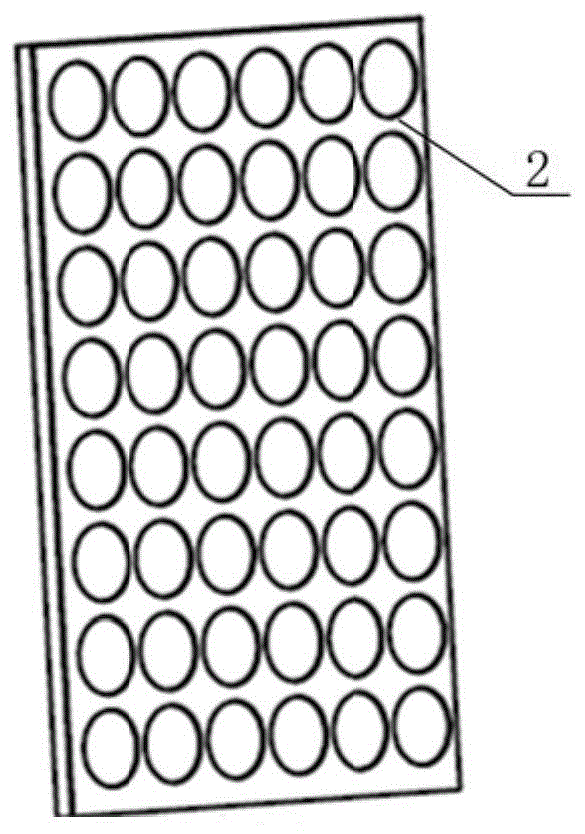
本发明涉及锂电池领域,尤其涉及一种低膨胀锂离子电池的制备工艺。
背景技术:
:锂离子电池是目前普遍认为最具优势的二次电池,具有比能量高,无记忆效应,循环寿命长等特点,广泛应用于电动汽车、航空航天等领域;锂离子电池生产制造过程中,需要经过烘烤、注液、老化、化成等工序,完成锂离子电池的激活。锂离子电池化成之后的成品电池常易出现鼓胀,主要原因可能有两种:一种是由于电极极片厚度变化导致,另一种是由于电池产气引起鼓胀。黄丽[1]进行了聚合物锂离子电池不同化成电压下产生气体的研究,研究发现化成初期形成sei膜的过程中会产生较多气体,气体的成分主要为氢气、二氧化碳、乙烯及烷烃类。目前一般采用负压抽取的方式将锂离子电池的化成过程中产生的气体排出,但由于气体的量较小且分布不均匀,负压抽取的方式不能将电池内的气体完全排出,导致成品电池出现鼓胀现象。为了消除电池的鼓胀现象,授权公告号为cn208596741u的中国实用新型专利公开了一种具有气体吸附功能的锂电隔膜,通过在锂电隔膜上涂覆具有吸附气体功能的绝缘材料,将气体吸附在绝缘材料内。此方法隔膜的孔隙率增大,气体吸附效果差;专利申请公告号为cn108615946a的中国发明专利申请文件公开了一种高镍三元体系锂离子电池的化成工艺,在注液时通入稀释过的氟气和二氧化硫,在化成过程中,sei膜中氟化锂和亚硫酸锂等的含量增加,使sei膜稳定致密,此方法注入的氟气和二氧化硫气味重,且反应效率低,成本较高,同时锂离子电池的空间利用率较大,负压对大部分的气体不易抽出,锂离子电池易出现膨胀。技术实现要素:为了解决以上问题,本发明的目的是提供一种低膨胀锂离子电池的化成工艺,能够有效地排出锂离子电池内的气体,降低成品锂离子电池的膨胀率。为实现上述目的,本发明所设计的低膨胀锂离子电池的制备工艺,包括步骤:(1)将多壁碳纳米管、碳黑、石墨烯、无水乙醇、碳酸锂混合搅拌均匀制备成浆料,通过凹版印刷将浆料涂覆在多孔硅碳负极极片表面,干燥后在多孔硅碳负极极片表面形成气体扩散层,气体扩散层上均匀分布有孔状结构;(2)将表面附着气体扩散层的多孔硅碳负极极片与正极极片经过叠片或卷绕、装配成锂离子电池;(3)将锂离子电池经烘烤、真空注液、预充电后进行化成工序,化成过程中向锂离子电池内充入氮气,通过注入氮气使化成产生的气体在锂离子电池内流动并混合均匀,最后将锂离子电池内的混合气体通过负压抽出。与现有的锂离子电池的制备工艺相比,本发明在多孔硅碳负极极片表面涂覆一层气体扩散层,气体扩散层有利于化成产生气体的传输,增大了化成产生气体的扩散传质,同时在化成过程中充入氮气,氮气的充入气流带动气体的流动,使化成产生气体和氮气充分混合,通过负压即可将电池内的气体完全排出。作为优选方案,所述气体扩散层的组成成分和重量百分比为,多壁碳纳米管15~30%、碳黑10~20%、石墨烯3~15%、碳酸锂2~5%、无水乙醇50~60%。作为优选方案,所述气体扩散层的厚度为1~4um,所述气体扩散层上的孔径为10~20um。作为优选方案,所述多孔硅碳负极的硅含量为5%~10%,孔径大小为1~10nm。作为优选方案,所述氮气充气压力为0.1~0.2mpa。作为优选方案,所述步骤(3)化成工序的具体过程为,首先采用0.05~0.5c电流对锂离子电池进行一次化成,同时向锂离子电池内充入氮气,充气压力在0.1~0.2mpa,待锂离子电池电量充至5%~40%soc时,将一次化成产生的气体和充入的氮气通过真空负压抽出;然后采用0.5~1c电流对锂离子电池进行二次化成,同时充入氮气,使锂离子电池呈现微正压状态,充气压力在0.1~0.2mpa,待锂离子电池电量充至40%~85%soc时,将二次化成产生的气体和充入的氮气通过真空负压抽出;最后以0.05~0.5c电流充到4.2v后,恒压继续充电到截止电流为0.01~0.02c,化成工序完成。作为优选方案,实现本发明较好的技术方案是:(1)按重量百分比计,将多壁碳纳米管25~30%、碳黑5%、石墨烯7~8%、碳酸锂2~3%、无水乙醇55~60%混合搅拌均匀制备成浆料,通过凹版印刷将浆料涂覆在多孔硅碳负极极片表面,多孔硅碳负极极片的孔径大小为5~10nm,干燥后在多孔硅碳负极极片表面形成厚度为1~2um的气体扩散层,气体扩散层上均匀分布有孔径为10~15um的孔状结构;(2)将表面附着气体扩散层的多孔硅碳负极极片与正极极片经过叠片或卷绕、装配成锂离子电池;(3)将锂离子电池经烘烤、真空注液、预充电后进行化成工序,化成工序的具体过程为,首先采用0.05~0.5c电流对锂离子电池进行一次化成,同时向锂离子电池内充入氮气,充气压力在0.15~0.2mpa,待锂离子电池电量充至5%~40%soc时,将一次化成产生的气体和充入的氮气通过真空负压抽出;然后采用0.5~1c电流对锂离子电池进行二次化成,同时充入氮气,使锂离子电池呈现微正压状态,充气压力在0.15~0.2mpa,待锂离子电池电量充至40%~85%soc时,将二次化成产生的气体和充入的氮气通过真空负压抽出;最后以0.05~0.5c电流充到4.2v后,恒压继续充电到截止电流为0.01~0.02c,化成工序完成。通过进一步控制多孔硅碳负极的孔径和气体扩散层的组分配比、厚度、孔径的大小使化成产生气体更好地从极片表面传输到电池内腔中,同时通过进一步控制充入氮气压力,使电池内腔的呈现微正压状态,通过负压更容易将电池内腔的气体完全排出。附图说明图1为表面附着气体扩散层的多孔硅碳负极极片的结构示意图;图2为图1的分解示意图;图中各部件标号如下:多孔硅碳负极极片1、气体扩散层2。具体实施方式为更好地理解本发明,以下将结合附图和具体实例对发明进行详细的说明。为解决现有锂离子电池排气不充分的问题,本发明提供一种低膨胀锂离子电池的制备工艺,结合图1和图2所示,首先在多孔硅碳负极极片1表面涂覆一层气体扩散层2,气体扩散层2有利于化成产生气体的传输,增大了化成产生气体的扩散传质,同时在化成过程中充入氮气,氮气的充入气流带动气体的流动,使化成产生气体和氮气充分混合,通过负压即可将电池内的气体完全排出。以下将通过具体的实施例来对本发明的锂离子电池的制备工艺的优选方式进行详细地说明。实施例1低膨胀锂离子电池的制备工艺,包括步骤:(1)按重量百分比计,将多壁碳纳米管20%、碳黑10%、石墨烯15%、碳酸锂5%、无水乙醇50%混合搅拌均匀制备成浆料,通过凹版印刷将浆料涂覆在多孔硅碳负极极片表面,多孔硅碳负极极片的孔径大小为5nm,多孔硅碳负极的硅含量为5%,干燥后在多孔硅碳负极表面形成厚度为4um的气体扩散层,气体扩散层上均匀分布有孔径为20um的孔状结构;(2)将表面附着气体扩散层的多孔硅碳负极与正极极片经过叠片或卷绕、装配成锂离子电池;(3)将锂离子电池经烘烤、真空注液、预充电后进行化成工序,化成工序的具体过程为,首先采用0.05c电流对锂离子电池进行一次化成,同时向锂离子电池内充入氮气,充气压力在0.12mpa,待锂离子电池电量充至20%soc时,将一次化成产生的气体(氢气、乙烯等气体)和充入的氮气通过真空负压抽出;然后采用0.5c电流对锂离子电池进行二次化成,同时充入氮气,使锂离子电池呈现微正压状态,充气压力在0.10mpa,待锂离子电池电量充至60%soc时,将二次化成产生的气体(氢气、乙烯等气体)和充入的氮气通过真空负压抽出;最后以0.05c电流充到4.2v后,恒压继续充电到截止电流为0.01c,化成工序完成。(4)将化成后的锂离子电池取样30支,进行厚度检测。实施例2低膨胀锂离子电池的制备工艺,包括步骤:(1)按重量百分比计,将多壁碳纳米管25%、碳黑5%、石墨烯8%、碳酸锂2%、无水乙醇60%混合搅拌均匀制备成浆料,通过凹版印刷将浆料涂覆在多孔硅碳负极极片表面,多孔硅碳负极极片的孔径大小为10nm,多孔硅碳负极的硅含量为10%,干燥后在多孔硅碳负极表面形成厚度为1um的气体扩散层,气体扩散层上均匀分布有孔径为15um的孔状结构;(2)将表面附着气体扩散层的多孔硅碳负极与正极极片经过叠片或卷绕、装配成锂离子电池;(3)将锂离子电池经烘烤、真空注液、预充电后进行化成工序,化成工序的具体过程为,首先采用0.1c电流对锂离子电池进行一次化成,同时向锂离子电池内充入氮气,充气压力在0.15mpa,待锂离子电池电量充至30%soc时,将一次化成产生的气体(氢气、乙烯等气体)和充入的氮气通过真空负压抽出;然后采用1c电流对锂离子电池进行二次化成,同时充入氮气,使锂离子电池呈现微正压状态,充气压力在0.20mpa,待锂离子电池电量充至85%soc时,将二次化成产生的气体(氢气、乙烯等气体)和充入的氮气通过真空负压抽出;最后以0.05c电流充到4.2v后,恒压继续充电到截止电流为0.02c,化成工序完成。(4)将化成后的锂离子电池取样30支,进行厚度检测。实施例3低膨胀锂离子电池的制备工艺,包括步骤:(1)按重量百分比计,将多壁碳纳米管28%、碳黑5%、石墨烯8%、碳酸锂3%、无水乙醇56%混合搅拌均匀制备成浆料,通过凹版印刷将浆料涂覆在多孔硅碳负极极片表面,多孔硅碳负极极片的孔径大小为5nm,多孔硅碳负极的硅含量为8%,干燥后在多孔硅碳负极表面形成厚度为2um的气体扩散层,气体扩散层上均匀分布有孔径为10um的孔状结构;(2)将表面附着气体扩散层的多孔硅碳负极与正极极片经过叠片或卷绕、装配成锂离子电池;(3)将锂离子电池经烘烤、真空注液、预充电后进行化成工序,化成工序的具体过程为,首先采用0.5c电流对锂离子电池进行一次化成,同时向锂离子电池内充入氮气,充气压力在0.16mpa,待锂离子电池电量充至40%soc时,将一次化成产生的气体(氢气、乙烯等气体)和充入的氮气通过真空负压抽出;然后采用0.5c电流对锂离子电池进行二次化成,同时充入氮气,使锂离子电池呈现微正压状态,充气压力在0.18mpa,待锂离子电池电量充至85%soc时,将二次化成产生的气体(氢气、乙烯等气体)和充入的氮气通过真空负压抽出;最后以0.1c电流充到4.2v后,恒压继续充电到截止电流为0.01c,化成工序完成。(4)将化成后的锂离子电池取样30支,进行厚度检测。实施例4低膨胀锂离子电池的制备工艺,包括步骤:(1)按重量百分比计,将多壁碳纳米管30%、碳黑5%、石墨烯7%、碳酸锂3%、无水乙醇55%混合搅拌均匀制备成浆料,通过凹版印刷将浆料涂覆在多孔硅碳负极极片表面,多孔硅碳负极极片的孔径大小为8nm,多孔硅碳负极的硅含量为5%,干燥后在多孔硅碳负极表面形成厚度为1um的气体扩散层,气体扩散层上均匀分布有孔径为12um的孔状结构;(2)将表面附着气体扩散层的多孔硅碳负极与正极极片经过叠片或卷绕、装配成锂离子电池;(3)将锂离子电池经烘烤、真空注液、预充电后进行化成工序,化成工序的具体过程为,首先采用0.05c电流对锂离子电池进行一次化成,同时向锂离子电池内充入氮气,充气压力在0.20mpa,待锂离子电池电量充至20%soc时,将一次化成产生的气体(氢气、乙烯等气体)和充入的氮气通过真空负压抽出;然后采用0.5c电流对锂离子电池进行二次化成,同时充入氮气,使锂离子电池呈现微正压状态,充气压力在0.15mpa,待锂离子电池电量充至60%soc时,将二次化成产生的气体(氢气、乙烯等气体)和充入的氮气通过真空负压抽出;最后以0.05c电流充到4.2v后,恒压继续充电到截止电流为0.01c,化成工序完成。(4)将化成后的锂离子电池取样30支,进行厚度检测。实施例5低膨胀锂离子电池的制备工艺,包括步骤:(1)按重量百分比计,将多壁碳纳米管15%、碳黑20%、石墨烯3%、碳酸锂2%、无水乙醇60%混合搅拌均匀制备成浆料,通过凹版印刷将浆料涂覆在多孔硅碳负极极片表面,多孔硅碳负极极片的孔径大小为1nm,多孔硅碳负极的硅含量为10%,干燥后在多孔硅碳负极表面形成厚度为3um的气体扩散层,气体扩散层上均匀分布有孔径为16um的孔状结构;(2)将表面附着气体扩散层的多孔硅碳负极与正极极片经过叠片或卷绕、装配成锂离子电池;(3)将锂离子电池经烘烤、真空注液、预充电后进行化成工序,化成工序的具体过程为,首先采用0.05c电流对锂离子电池进行一次化成,同时向锂离子电池内充入氮气,充气压力在0.10mpa,待锂离子电池电量充至20%soc时,将一次化成产生的气体(氢气、乙烯等气体)和充入的氮气通过真空负压抽出;然后采用0.5c电流对锂离子电池进行二次化成,同时充入氮气,使锂离子电池呈现微正压状态,充气压力在0.13mpa,待锂离子电池电量充至60%soc时,将二次化成产生的气体(氢气、乙烯等气体)和充入的氮气通过真空负压抽出;最后以0.5c电流充到4.2v后,恒压继续充电到截止电流为0.01c,化成工序完成。(4)将化成后的锂离子电池取样30支,进行厚度检测。对比例锂离子电池的制备工艺,包括步骤:(1)将多孔硅碳负极极片与正极极片经过叠片、装配成锂离子电池;多孔硅碳负极极片的硅含量为10%,孔径大小为1nm。(2)将锂离子电池经烘烤、真空注液、预充电后进行化成工序,化成工序采用多段式化成,首先采用0.05c电流对锂离子电池进行一次化成,一次化成后采用真空负压抽气;然后采用0.5c电流对锂离子电池进行二次化成,二次化成后采用真空负压抽气;最后以0.05c电流充到4.2v后,恒压继续充电到截止电流为0.01c时,结束化成。(3)将化成后的锂离子电池取样30支,进行厚度检测。实施例1~5和对比例得到的低膨胀锂离子电池成后厚度平均膨胀率见表1:实施例厚度平均膨胀率实施例12.2%实施例21.2%实施例31.8%实施例41.5%实施例52.1%对比例4.3%以上所述实施例仅表达了本发明的几种实施方式,其描述较为具体和详细,但并不能因此而理解为对本发明专利范围的限制。应当指出的是,对于本领域的普通技术人员来说,在不脱离本发明构思的前提下,还可以做出若干变形和改进,这些都属于本发明的保护范围。因此,本发明专利的保护范围应以所附权利要求为准。当前第1页12