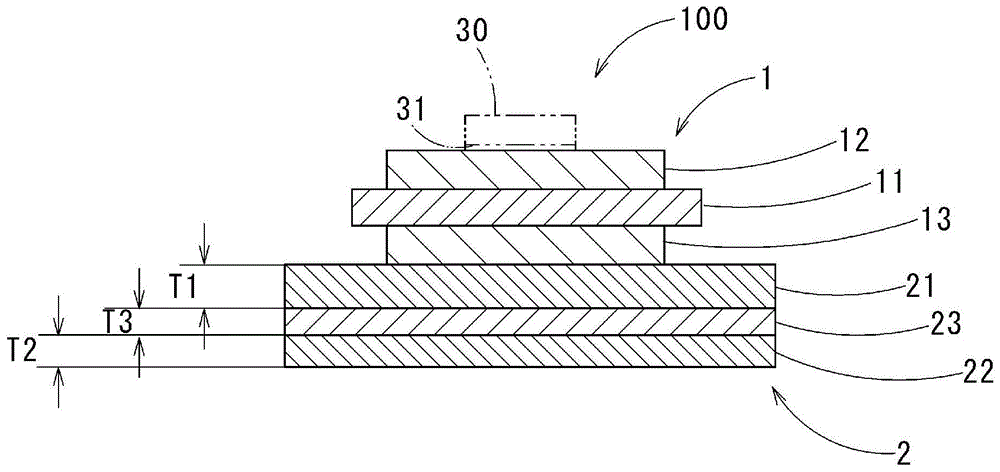
本发明涉及一种在用于控制大电流、高电压的半导体装置中使用的功率模块用基板等的绝缘电路基板接合有散热器的带散热器的绝缘电路基板。本申请基于2018年3月27日申请的日本专利申请2018-59658号要求优先权,并将其内容援用于此。
背景技术:
:已知有在由以氮化铝为代表的陶瓷基板构成的绝缘层的一个面接合有电路层,并且在另一个面隔着铝板接合有铝系的散热器的带散热器的绝缘电路基板。例如专利文献1公开的带散热器的绝缘电路基板,在由陶瓷基板构成的绝缘层的一个面接合有由纯铝板、铝合金板、纯铜板和铜合金板等中的任一个构成的电路层,在绝缘层的另一个面接合有由纯铝或铝合金的金属板构成的金属层,在该金属层上隔着铜层接合有由铝或铝合金构成的散热器。此时,绝缘层与金属层使用钎料接合,金属层与散热器在与存在于它们之间的铜层之间固相扩散接合。在这种带散热器的绝缘电路基板中,有可能发生如陶瓷基板与铝板这样热膨胀系数不同的部件的接合而导致的翘曲。为了防止这种翘曲,可考虑作为散热器的材料,使用使以铝为主成分的金属含浸于在专利文献2中公开的多孔碳化硅成型体而成的低膨胀系数的复合体。专利文献3中公开有在第1陶瓷基板的一个面接合第1金属板,在第1陶瓷基板的另一个面与第2陶瓷基板的一个面接合第2金属板,在第2陶瓷基板的另一个面接合具有多个散热片的板状散热部件而成的金属-陶瓷接合基板(带散热器的绝缘电路基板)。关于该金属-陶瓷接合基板,通过将第1陶瓷基板及第2陶瓷基板在碳制的铸模内隔开间隔地配置,使铝合金熔融金属流入铸模并冷却、固化而形成。专利文献1:日本特开2014-60215号公报专利文献2:日本特开2000-281465号公报专利文献3:日本特开2017-212316号公报关于专利文献3公开的金属-陶瓷接合基板,通过将两张陶瓷基板在铸模内隔开间隔地配置,使熔融状态的铝合金流入铸模而制造,因此所有的金属板、散热部件及散热片成为相同的铝合金。技术实现要素:本发明鉴于这种情况而完成,其目的在于抑制通过接合由与绝缘电路基板的金属层不同组成的金属构成的散热器而成的带散热器的绝缘电路基板的翘曲。本发明的带散热器的绝缘电路基板具备:绝缘电路基板,具有陶瓷基板、接合于所述陶瓷基板的一个面的电路层及接合于所述陶瓷基板的另一个面且由铝或铝合金构成的金属层;及接合于所述金属层的散热器,其中,所述散热器具有:接合于所述金属层且由铜或铜合金构成的厚度为t1的第1金属层、接合于所述第1金属层的与所述金属层相反的一侧的面的陶瓷板材、以及接合于所述陶瓷板材的与所述第1金属层相反的一侧的面且由铜或铜合金构成的厚度为t2的第2金属层,所述第1金属层的所述厚度t1为0.3mm以上且3.0mm以下,厚度比t1/t2为1.0以上。在本发明中,散热器由接合于绝缘电路基板的金属层的第1金属层、接合于所述第1金属层的陶瓷板材和接合于所述陶瓷板材的第2金属层构成。即,在由铜或铜合金构成的第1金属层与第2金属层的内侧内置有陶瓷板材,因此,能够减少该散热器的线膨胀系数,还能够减少与绝缘电路基板的线膨胀差。由此,能够抑制带散热器的绝缘电路基板的高温时与低温时的翘曲变化量。并且,将第1金属层的厚度t1设为0.3mm以上且3.0mm以下,是因为若第1金属层的厚度t1小于0.3mm则有可能散热器的散热效果降低,若厚度t1超过3.0mm则由铜或铜合金构成的第1金属层的膨胀的影响变大,该第1金属层与陶瓷板材的接合体(散热器)的线膨胀增大,因此,绝缘电路基板与散热器的接合体即带散热器的绝缘电路基板的翘曲增大。并且,若第1金属层的厚度t1小于第2金属层的厚度t1,则在加热带散热器的绝缘电路基板时有可能向绝缘电路侧以凸状翘曲,因此,将t1/t2设为1.0以上。作为本发明的带散热器的绝缘电路基板的优选方式,所述厚度比t1/t2优选为10.0以下。作为本发明的带散热器的绝缘电路基板的优选方式,所述第2金属层的所述厚度t2优选为0.3以上。作为本发明的带散热器的绝缘电路基板的优选方式,优选所述电路层由铝或铝合金构成,所述陶瓷基板由氮化铝构成,所述陶瓷板材由氮化硅构成。作为本发明的带散热器的绝缘电路基板的优选方式,优选所述金属层与所述第1金属层固相扩散接合。根据本发明,能够抑制通过接合具有金属层的绝缘电路基板和具有与绝缘电路基板的金属层不同组成的金属层的散热器而成的带散热器的绝缘电路基板的翘曲。附图说明图1为表示利用本发明的一实施方式所涉及的带散热器的绝缘电路基板的功率模块的剖视图。图2为表示从电路层侧观察上述实施方式中的带散热器的绝缘电路基板的俯视图。图3a为说明图1所示的带散热器的绝缘电路基板的制造方法的剖视图。图3b为说明图1所示的带散热器的绝缘电路基板的制造方法的剖视图。图3c为说明图1所示的带散热器的绝缘电路基板的制造方法的剖视图。具体实施方式以下,对本发明的实施方式,在参照附图的同时进行说明。[绝缘电路基板的概略结构]如图1所示,本发明所涉及的带散热器的绝缘电路基板100在绝缘电路基板1上接合散热器2而成,例如作为功率模块用基板来使用。如图1的双点划线所示,在该带散热器的绝缘电路基板100的表面(上面)搭载元件30而成为功率模块。该元件30为具备半导体的电子部件,可以选择igbt(insulatedgatebipolartransistor:绝缘栅双极型晶体管)、mosfet(metaloxidesemiconductorfieldeffecttransistor:金属氧化物半导体场效应晶体管)、fwd(freewheelingdiode:续流二极管)等各种半导体元件。此时,虽然省略图示,但是在元件30的上部设置有上部电极部,在下部设置有下部电极部,下部电极部通过焊料31等接合于电路层12的上面,由此元件30被搭载于电路层12的上面。并且,元件30的上部电极部隔着用焊料等接合的引线框等连接到电路层12的电路电极部等而制造功率模块。[绝缘电路基板的结构]绝缘电路基板1具备:陶瓷基板11、接合于陶瓷基板11的一个面的电路层12和接合于陶瓷基板11的另一个面的金属层13。陶瓷基板11为防止电路层12与金属层13之间的电连接的矩形板状的绝缘基板,例如通过氮化铝(aln)、氮化硅(si3n4)、氧化铝(al2o3)、氧化锆增韧氧化铝基板等形成,其厚度为0.2mm~1.2mm。另外,在接合于陶瓷基板11的两面的电路层12及金属层13均由铝或铝合金构成的情况下,陶瓷基板11优选由氮化铝构成。并且,陶瓷基板11的平面大小并无特别限定,在本实施方式中设定为40mm~140mm×40mm~100mm。电路层12接合于陶瓷基板11的上面(表面),使用纯度99质量%以上的纯铝或铝合金,其厚度例如为0.2mm以上且0.9mm。并且,电路层12的平面大小小于陶瓷基板11的平面大小,虽然无特别限定,但是在本实施方式中设定为36mm~136mm×36mm~96mm。金属层13接合于陶瓷基板11的下面(背面),使用纯度99质量%以上的纯铝或铝合金,在jis标准下能够使用1000系列铝,尤其能够使用1n99(纯度99.99质量%以上:所谓4n铝)。其厚度例如为0.2mm~0.9mm。并且,金属层13的平面大小小于陶瓷基板11的平面大小,虽然无特别限定,但是在本实施方式中与电路层12同样地设定为36mm~136mm×36mm~96mm。另外,电路层12及金属层13优选为相同组成、相同厚度且相同大小。[散热器的结构]散热器2接合于绝缘电路基板1,对从所述绝缘电路基板1传递的热进行散热。该散热器2包含:接合于绝缘电路基板1的金属层13的第1金属层21、接合于第1金属层21的下面(背面)的陶瓷板材23、以及接合于陶瓷板材23的下面(背面)的第2金属层22。第1金属层21由铜或铜合金构成,其厚度t1设定为0.3mm以上且3.0mm以下。并且,第2金属层22由铜或铜合金构成,其厚度t2设定为0.3mm以上且3.0mm以下。另外,若第1金属层21的厚度小于0.3mm则有可能散热器2的散热效果降低,若超过3.0mm则该第1金属层21与陶瓷板材23的接合体(散热器2)的线膨胀增大,因此,绝缘电路基板1与散热器2的接合体即带散热器的绝缘电路基板100的翘曲增大。并且,若第1金属层21的厚度小于第2金属层22,则散热器2在加热时有可能向第1金属层21侧以凸状翘曲。因此,第1金属层21的厚度t1设定为0.3mm以上且3.0mm以下,且设定为第2金属层22的厚度t2以上(与第2金属层22的厚度t2相等或比厚度t2厚)。并且,第1金属层21的厚度t1与第2金属层22的厚度t2的厚度比t1/t2优选为1.0以上且10.0以下。陶瓷板材23是为了减小散热器2与绝缘电路基板1的线膨胀差而设置,由氮化硅(si3n4)、氮化铝(aln)、氧化铝(al2o3)、氧化锆增韧铝基板等形成,其厚度t3设定为0.2mm~1.2mm。并且,第1金属层21、第2金属层22及陶瓷板材23的平面大小大于陶瓷基板11的平面大小,虽然并无特别限定,但是,均设定为相同大小,例如设定为50mm~180mm×60mm~140mm。另外,陶瓷板材23由于在其两面接合由铜或铜合金构成的第1金属层21及第2金属层22,因此,更优选由氮化硅构成。从电路层12侧观察带散热器的绝缘电路基板100时,如图2所示,陶瓷基板11大于电路层12,散热器2(第1金属层21、第2金属层22及陶瓷板材23)大于陶瓷基板11。如以上说明,散热器2成为在由铜或铜合金构成的第1金属层21与第2金属层22的内侧内置有陶瓷板材23的结构。[带散热器的绝缘电路基板的制造方法]接着,对本实施方式的带散热器的绝缘电路基板100的制造方法进行说明。关于带散热器的绝缘电路基板100的制造方法,如图3a~3c所示,具有:在陶瓷基板11接合由纯铝或铝合金构成的电路层用金属板120及金属层用金属板130的绝缘电路基板制造工序(图3a)、在陶瓷板材23接合由铜或铜合金构成的第1金属层用金属板210及第2金属层用金属板220的散热器制造工序(图3b)及接合绝缘电路基板1与散热器2的接合工序(图3c)。以下,按该工序顺序进行说明。(绝缘电路基板制造工序)首先,如图3a所示,在陶瓷基板11分别利用al-si系的钎料来接合电路层用金属板120及金属层用金属板130。具体而言,在陶瓷基板11的表面(上面)及背面(下面),分别隔着al-si系的钎料箔14层叠电路层用金属板120及金属层用金属板130,并将这些层叠体通过碳板夹持,在层叠方向施加荷载的同时在真空中加热,由此接合陶瓷基板11与电路层用金属板120及金属层用金属板130。由此,形成在陶瓷基板11的表面(上面)隔着接合部(钎焊部)接合有电路层12且在背面(下面)隔着接合部(钎焊部)接合有金属层13的绝缘电路基板1。另外,优选向层叠方向的加压力设为0.3mpa~1.5mpa、加热温度设为630℃以上且655℃以下。并且,al-si系钎料箔的厚度优选为5μm~15μm。而且,除了al-si系钎料以外,还能够使用al-ge系、al-cu系、al-mg系、al-mn系或al-si-mg系钎料。(散热板制造工序)接着,如图3b所示,在厚度t3为0.2mm~1.2mm的陶瓷板材23,分别使用ag-cu-ti系的钎料来接合厚度t1为0.3mm~3.0mm的第1金属层用金属板210及厚度t2为0.3mm~3.0mm且t1以下的第2金属层用金属板220。具体而言,在陶瓷基板23的表面(上面)及背面(下面),分别隔着ag-cu-ti系的钎料箔14,层叠第1金属层用金属板210及第2金属层用金属板220,并将这些层叠体通过碳板挟持,在层叠方向施加荷载的同时在真空中加热,由此接合陶瓷基板23与第1金属层用金属板210及第2金属层用金属板220。由此,形成散热器2,该散热器2在陶瓷板材23的表面(上面)隔着接合部(焊接部)接合有厚度t1为0.3mm~3.0mm的第1金属层21,在背面(下面)隔着接合部(焊接部)接合有厚度t2为0.3mm~3.0mm且第1金属层21的厚度t1以下的第2金属层22。并且,优选向层叠方向的加压力设为0.1mpa~1.0mpa、加热温度设为800℃~930℃。并且,ag-cu-ti系钎料箔的厚度优选为5μm~15μm。而且,除了ag-cu-ti系钎料以外,还能够使用cu-p系钎料。(接合工序)接着,将绝缘电路基板1与散热器2固相扩散接合。具体而言,如图3c所示,通过将绝缘电路基板1的金属层13层叠在散热器2上,在对这些层叠体向层叠方向加压的状态下,在真空气氛下加热为接合温度,由此,将金属层13与散热器2固相扩散接合。作为此时的加压力,例如设为0.5mpa~2.0mpa,作为加热温度设为500℃~540℃,并将该加压及加热状态维持30分钟~120分钟。由此,接合金属层13与散热器2,如图1所示,获得带散热器的绝缘电路基板100。另外,在本实施方式中,金属层13的接合面及散热器2的接合面,预先去除划痕并使其平滑后进行固相扩散接合。其中,散热器利用一张铜或铜合金的板构成时,与绝缘电路基板1的由铝或铝合金构成的金属层13的线膨胀差较大,因此,高温时的膨胀率及低温时的收缩率不同,带散热器的绝缘电路基板100的翘曲较大。相对于此,在本实施方式中,由接合于绝缘电路基板1的金属层13的第1金属层21、接合于所述第1金属层21的陶瓷板材23、以及接合于所述陶瓷板材23的第2金属层22构成散热器2。即,在由铜或铜合金构成的第1金属层21与第2金属层22的内侧内置陶瓷板材23,因此能够减小该散热器2的线膨胀系数,能够减小与绝缘电路基板1的线膨胀差。并且,第1金属层21的厚度t1为0.3mm以上且3.0mm以下,且为第2金属层22的厚度t2以上(t1≥t2),因此,在维持散热器2的散热效果的同时,能够抑制散热器2的翘曲,而且,能够进一步抑制带散热器的绝缘电路基板100的高温时与低温时的翘曲变化量。另外,细部结构并不限定于实施方式的结构,在不脱离本发明要旨的范围内,可以增加各种改变。例如,在上述实施方式中,电路层12设为由铝或铝合金构成,但并不限定于此,例如还可以由无氧铜构成。即,不限制电路层12的组成。并且,在所述实施方式中,说明了将带散热器的绝缘电路基板100作为带散热器的功率模块用基板来使用的例子,但是,该带散热器的绝缘电路基板100还能够作为led元件用基板等各种绝缘基板来使用。实施例接着,关于本发明的效果,利用实施例详细地说明,但本发明并不限于下述实施例。作为构成实施例1~18、比较例1~3及现有例的试样的绝缘电路基板,在厚度0.635mm、平面大小为120mm×90mm的陶瓷基板,通过在上述实施方式中所述的方法制造厚度0.4mm的电路层及厚度0.4mm的金属层,关于电路层及金属层,准备了表1所示组成的电路层及金属层。并且,作为构成实施例1~18及比较例1~3的试样的散热器,在厚度0.32mm、平面大小为140mm×100mm的陶瓷基板,通过在上述实施方式中所述的制造方法,制造了由无氧铜构成的第1金属层及第2金属层。关于第1金属层及第2金属层,准备了表1所示厚度的第1金属层及第2金属层。另外,关于现有例,制造了由厚度5.0mm、平面大小为140mm×100mm的一张无氧铜板构成的散热器。而且,通过在上述实施方式中所述的接合方法接合这些绝缘电路基板与散热器,对所获得的试样(实施例1~18、比较例1~3、及现有例)进行了以下实验。(翘曲变化量)针对所获得的各试样,在从30℃加热为285℃后进行冷却而成为30℃的一连串加热试验中,分别测定加热为285℃时的翘曲量及加热为285℃后进行冷却而成为30℃时的翘曲量(冷却为30℃时的翘曲量),作为翘曲变化量,确认了因温度变化而带来的各试样的变形。关于翘曲量,使用云纹式三维形状测定机(akrometrix公司制的热翘曲及变形测定机thermoireps200),将散热器的第2金属层的中央(100mm×80mm的范围)作为测定面进行了测定。更具体而言,从测定面的分布求出最小平方面,以该面为基准,求出最高点与最低点之差(绝对值)而获得了翘曲量。关于如此获得的翘曲量,根据翘曲状态设定正负。即,将测定范围的中心比由测定范围的四角形成的面更接近电路层侧的情况(第2金属层向电路层侧凸出)及测定范围的中心在由测定范围的四角形成的面上的情况设定为正值、测定范围的中心比由测定范围的四角形成的更还远离电路层侧的情况(第2金属层向散热器侧凸出)设定负值。将如此设定了正负的加热为285℃时的翘曲量及冷却为30℃时的翘曲量之差(设定了正负的加热为285℃时的翘曲量-设定了正负的冷却为30℃时的翘曲量)的绝对值设为翘曲变化量。(元件位置偏离的评价)关于元件位置偏离的评价,通过将电子部件焊接于电路层之后计测其焊接位置,并制作30个试样来确认有无发生位置偏离。然后,将发生0.2mm以上的位置偏离的状况设为不合格,发生小于0.2mm的位置偏离的状况评价为合格。然后,在针对30个试样进行的各评价中,合格比率为90%以上的状况评价为良“a”,合格比率小于90%的状况评价为不良“b”。(冷热循环可靠性的评价)并且,对实施例1~18、比较例1~3及现有例的带散热器的绝缘电路基板,执行在-50℃~175℃之间执行1000次变化的温度循环试验后,目视判定了在绝缘电路基板的陶瓷基板是否有破裂。这时,在陶瓷基板存在破裂的判定为不良“b”、在陶瓷基板不存在破裂的判定为良“a”。关于翘曲变化量、元件位置偏离的评价及冷热循环可靠性的评价,在表2表示其结果。[表1][表2]翘曲差(mm)元件位置偏离冷热循环可靠性实施例10.29aa实施例20.32aa实施例30.54aa实施例40.77aa实施例51.10aa实施例60.19aa实施例70.89aa实施例81.20aa实施例90.35aa实施例100.39aa实施例110.41aa实施例120.35aa实施例130.37aa实施例140.36aa实施例150.36aa实施例160.33aa实施例170.42aa实施例180.46aa比较例11.23ab比较例21.28ab比较例31.35ba现有例1.30bb由表2可知,在实施例1~18中,翘曲变化量为1.20mm以下,为较少,元件位置偏离及冷热循环可靠性的评价均为良“a”。因此,可知如下有效的范围:即散热器的第1金属层的厚度t1为0.3mm以上且3.0mm以下,且为第2金属层的厚度t2以上(t1≥t2)。另一方面,在比较例1及比较例2中,虽然翘曲变化量比较大但元件位置偏离的评价为良“a”,但是,所述冷热循环试验的结果,由于陶瓷基板破裂,因此评价为不良“b”。因此,可知第1金属层的厚度为4.0mm时,未能获得有效的结果。并且,在比较例3中,虽然冷热循环可靠性的评价为良“a”,但翘曲变化量为1.3mm以上,为较大,发生了元件位置偏离,因此,评价为不良“b”。因此,可知第2金属层的厚”度t2大于第1金属层的厚度t1时,未能获得有效的结果。产业上的可利用性能够抑制通过接合具有金属层的绝缘电路基板和具有与绝缘电路基板的金属层不同组成的金属层的散热器而成的带散热器的绝缘电路基板的翘曲。符号说明1绝缘电路基板2散热器11陶瓷基板12电路层13金属层14钎料箔21第1金属层22第2金属层23陶瓷板材30元件31焊料100带散热器的绝缘电路基板120电路层用金属板130金属层用金属板210第1金属层用金属板220第2金属层用金属板当前第1页12