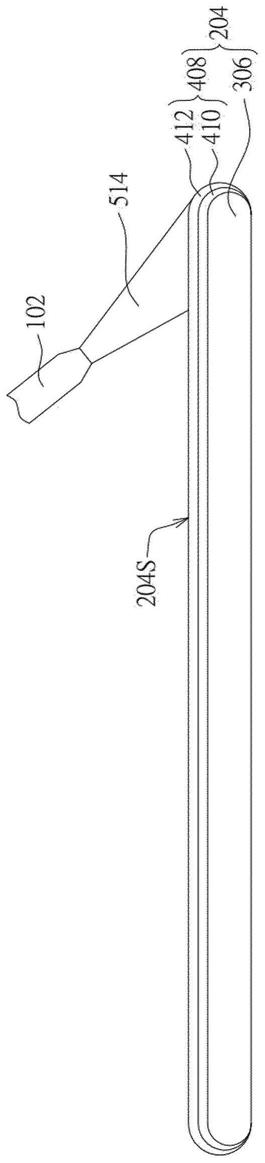
1.本发明涉及一种半导体制作工艺,且特别是涉及一种晶片斜边清洗制作工艺。
背景技术:2.在半导体制作工艺中,可利用电化学电镀(electro chemical plating,简称ecp)制作工艺形成铜金属层。然后,可进行晶片斜边清除(ebr)制作工艺将晶片边缘残余的铜通过例如是过氧化氢(h2o2)与硫酸(h2so4)的水溶液化学调剂进行清洗,以避免晶片边缘残余的铜在尔后的化学机械研磨过程中剥离而伤害金属表面,影响后续制作工艺。
技术实现要素:3.本发明是有关于一种半导体制作工艺。
4.根据本发明的一概念,提出一种半导体制作工艺,其包括第一供力步骤及第二供力步骤。第一供力步骤是对供应至晶片的晶片表面上的清洗液提供第一固定离心力。第二供力步骤是对供应至晶片表面上的清洗液提供第二固定离心力。第二供力步骤是在第一供力步骤之后。第二固定离心力是大于第一固定离心力。
5.根据本发明的另一概念,提出一种半导体制作工艺,其包括在第一时段期间进行第一旋转步骤与清洗液供应步骤,及然后在第二时段期间进行第二旋转步骤与清洗液供应步骤。第一旋转步骤是以第一固定转速旋转晶片。清洗液供应步骤是供应清洗液至晶片的晶片表面上。第二旋转步骤是以第二固定转速旋转晶片。第二固定转速是快于第一固定转速。
6.为了对本发明的上述及其他方面有更佳的了解,下文特举实施例,并配合所附的附图详细说明如下:
附图说明
7.图1为本发明一实施例的半导体制作工艺的示意图;
8.图2为本发明一实施例的半导体制作工艺的时序图;
9.图3为比较例及实施例中经清洗后的晶片的示意图。
具体实施方式
10.以下以一些实施例做说明。需注意的是,本发明并非显示出所有可能的实施例,未于本发明提出的其他实施态样也可能可以应用。再者,附图上的尺寸比例并非按照实际产品等比例绘制。因此,说明书和图示内容仅作叙述实施例之用,而非作为限缩本发明保护范围之用。另外,实施例中的叙述,例如细部结构、制作工艺步骤和材料应用等等,仅为举例说明之用,并非对本发明欲保护的范围做限缩。实施例的步骤和结构各项细节可在不脱离本发明的精神和范围内根据实际应用制作工艺的需要而加以变化与修饰。以下是以相同/类似的符号表示相同/类似的元件做说明。
11.请参照图1,其绘示半导体制作工艺的示意图。喷嘴102可设置在晶片(晶圆片)204上并邻近晶片204的边缘,用以供应清洗液514至晶片204的晶片表面204s(可包括晶片侧壁表面及邻近晶片侧壁表面的上晶片表面)上。一实施例中,喷嘴102的位向可如图1所示配置成来自喷嘴口的清洗液514可朝往晶片204的晶片侧壁表面的方向射出。
12.晶片204可包括半导体基板306及含金属的膜408在半导体基板306上。半导体基板306例如包括硅(例如硅晶片)或其它合适的半导体材料。含金属的膜408可包括金属或其氧化物、氮化物等。例如,含金属的膜408可包括金属层410。金属层410可例如以沉积或涂布等方式形成。含金属的膜408也可包括金属氧化层412在金属层410上。金属氧化层412可为金属层410的表面经氧化之后所形成的层,例如为自然氧化层,或以沉积、涂布等方式形成。一实施例中,金属层410包括铜,金属氧化层412包括氧化铜,用以清洗铜/氧化铜的清洗液514可包括过氧化氢(h2o2)与硫酸(h2so4)的水溶液(亦即过氧化氢、硫酸与水的混合溶液)。但本发明不限于此。其它实施例中,含金属的膜408其金属可包括钴或其它合适的金属种类,用以清洗(或蚀刻)含金属的膜408的清洗液514(或蚀刻液)可以对应选择合适的溶液。图1中是显示清洗液514所供应至其上的晶片表面204s包括金属氧化层412的表面。但能理解,在一些情况中,例如当金属层410上没有形成金属氧化层412,或金属氧化层412经清洗步骤(例如移除步骤)被去除而露出下方的金属层410时,清洗液514所供应至其上的晶片表面204s是包括金属层410的表面。
13.图2绘示半导体制作工艺的时序图。请同时参照图1及图2。实施例中,半导体制作工艺为晶片边缘和斜角上薄膜的去除制作工艺。半导体制作工艺包括在从时间点t1至时间点t2的第一时段p1期间进行清洗液供应步骤与第一供力步骤,以使持续供应至晶片204上的清洗液514以一固定的较慢流速离开晶片204。清洗液供应步骤是供应清洗液514至晶片204上。一实施例中,第一供力步骤是对晶片204上的清洗液514提供第一固定离心力f1,由此使清洗液514能以较慢流速(例如径向流速)离开晶片204。一实施例中,第一固定离心力f1可由以第一转速r1旋转晶片204的第一旋转步骤造成。第一转速r1可为固定的转速(即第一固定转速)。一实施例中,第一转速r1为100~400rpm。较慢流速使得清洗液514能待在晶片204上较长的时间。能通过较慢流速使清洗后的含金属的膜408具有较大的斜边宽度。一实施例中,较慢流速的清洗液514能停留在晶片204上较久的时间,有效率地移除在金属层410上较为刚硬的金属氧化层412,由此露出金属层410,或者,可有效率地溶解金属层410(例如铜)。
14.然后,在第二时段p2期间进行清洗液供应步骤与第二供力步骤,以使持续供应至晶片204上的清洗液514以一固定的较快流速离开晶片204。一实施例中,第二供力步骤是对晶片204上的清洗液514提供第二固定离心力f2,第二固定离心力f2是大于第一固定离心力f1,由此使清洗液514能以较快流速(例如径向流速)离开晶片204,也能避免清洗液514倒流至晶片204的内部而影响不欲被清洗液514清洗/移除的区域。一实施例中,第二固定离心力f2可由以第二转速r2旋转晶片204的第二旋转步骤造成。第二转速r2可为固定的转速(即第二固定转速)。第二转速r2快于第一时段p1期间进行的第一旋转步骤的第一转速r1。一实施例中,第二转速r2对于第一转速r1的比值(r2/r1)为大于1,且为小于或等于4。亦即,1<r2/r1≤4。较慢流速之后所使用的较快流速使得清洗液514能待在晶片204上较短的时间。一实施例中,较快流速能造成清洗后的含金属的膜408具有较陡峭的斜边或较窄的斜边宽度(例
如图3所示的斜边宽度ew)。在第二时段p2之后,可对晶片204进行化学机械研磨步骤。由于含金属的膜408具有较窄的斜边宽度,因此能改善化学机械研磨步骤可能发生的金属剥落颗粒(例如铜颗粒)及颗粒造成材料层表面刮损的制作工艺问题。
15.实施例中,半导体制作工艺可包括加速时段a,在第一时段p1与第二时段p2之间。加速时段a可为时间点t2至时间点t3之间的时段。第二时段p2可为时间点t3至时间点t4之间的时段。一实施例中,加速时段a期间可进行清洗液供应步骤与力增强步骤。力增强步骤是将提供至晶片204上的清洗液514的离心力从第一固定离心力f1增强至第二固定离心力f2,例如从第一固定离心力f1线性增强至第二固定离心力f2。一实施例中,离心力的增强是由将晶片204的转速从第一转速r1等加速至第二转速r2的加速步骤造成。
16.一实施例中,第一时段p1、第二时段p2及加速时段a期间,能设定喷嘴102以固定不变的流量持续不断提供清洗液514。一实施例中,在第一时段p1之前,晶片204可从静止状态等加速至第一转速r1,待转速达到第一转速r1后才提供清洗液514至晶片204上,提供清洗液514的起始时间点可对应图2的时间点t1。一实施例中,清洗液514可在第一时段p1及第二时段p2期间提供,而在加速时段a期间不提供清洗液514至晶片204上。第一时段p1与第二时段p2可独立为1秒至10分钟。一实施例中,举例来说,第一时段p1为2秒至1分钟,第二时段p2为2秒至5分钟。
17.图3绘示根据比较例及实施例中经清洗后的晶片的示意图。请同时参照图2及图3。一比较例中,是在时间点t1至时间点t4期间仅使用单一转速rc旋转晶片204,转速rc大于第一转速r1且小于第二转速r2,以此方式清洗晶片204后造成的斜边宽度标示为cw。实施例中,先以固定的第一转速r1,然后以快于第一转速r1的固定的第二转速r2旋转晶片204,以此方式清洗晶片204后造成的斜边宽度标示为ew,其窄于比较例的斜边宽度cw。一些实施例的斜边宽度ew相较于比较例的斜边宽度cw缩减约10%。根据实施例的半导体制作工艺形成具有较窄斜边宽度ew的含金属的膜408,能改善后续化学机械研磨步骤可能发生的金属剥落颗粒(例如铜颗粒)及颗粒造成材料层表面刮损的制作工艺问题。或是增加晶片表面上有效管芯的面积。
18.根据以上,实施例中,是使持续供应至晶片上的清洗液以一固定的较慢流速离开晶片,然后以一固定的较快流速离开晶片。以此方式进行边缘金属层去除的制作工艺,能形成具有较窄斜边宽度的含金属的膜(例如铜膜),能改善后续化学机械研磨步骤可能发生的金属剥落颗粒(例如铜颗粒)及颗粒造成材料层表面刮损的制作工艺问题。或是增加晶片表面上有效管芯的面积。
19.综上所述,虽然结合以上实施例公开了本发明,然而其并非用以限定本发明。本发明所属技术领域中具有通常知识者,在不脱离本发明的精神和范围内,可作各种的更动与润饰。因此,本发明的保护范围应当以附上的权利要求所界定的为准。