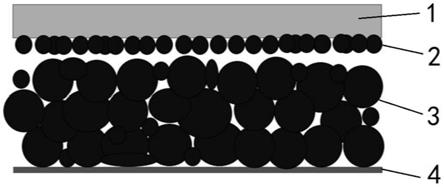
1.本发明涉及锂离子电池技术领域,尤其涉及一种锂离子电池用隔膜及快充型锂离子电池的制备方法。
背景技术:2.为了提高离子电池的快充性能,主要人们主要从包含石墨的负极方面进行改善。另外,目前快充型电极表面常发生析锂现象,析锂的主要原因是高倍率的情况下,由于极化原因li
+
不能快速嵌入近石墨层,从而导致负极极片表面易发生析锂现象。可通过减少石墨的粒径和增加表面的不定型碳的含量提高动力学性能从而减少极化,达到倍率性能的提高。但是这类功率型石墨具有首效低,克容量低的劣势。因此,全部采用这种负极会降低能量密度。
3.为克服上述问题,现有的方法一般是采用双层涂布的方法制备负极,其底层涂布大颗粒石墨,表层涂布功率型石墨,该方法既保持电极的能量密度,又使电极达到一定的功率能力。但是,采用双层涂布技术时,需定制特殊的涂布模头,其制造成本高,且对涂布的过程参数要求苛刻。如需严格控制涂布速度,同时还存在可加工温度区间狭窄,涂布不同石墨颗粒之间切换困难等问题。以上缺陷均降低了生产的产能、提高了加工成本。
技术实现要素:4.为解决上述技术问题,本发明的目的是提供一种锂离子电池用隔膜及快充型锂离子电池的制备方法,本发明的技术直接可以在现有工艺产出的极片上通过简单的热压复合工艺达到与双层涂布工艺同样的效果,对生产产能和加工成本无影响。
5.本发明的第一个目的是提供一种锂离子电池用隔膜,包括隔膜基体以及位于隔膜基体一侧表面的连续的石墨层,石墨层具有多个间隔设置的岛状结构,石墨层包括粘结剂和石墨颗粒,石墨颗粒的粒径分布为d50在1
‑
8μm之间。
6.优选地,石墨颗粒的分布为d50 2
‑
5μm之间。
7.进一步地,石墨层的厚度为4
‑
20μm,石墨粒径分布d50为3μm时,最优化厚度为6μm。可采用喷涂方式将石墨颗粒喷涂至隔膜基体表面。
8.进一步地,粘结剂占石墨层总重的1
‑
5%,石墨颗粒占石墨层总重的95
‑
99%。在石墨层中,石墨颗粒均匀分布于粘结剂中。
9.进一步地,粘结剂包括pvdf(聚四氟乙烯)、cmc/sbr(羧甲基纤维素钠/丁苯橡胶)、paa(聚丙酸)、pva中的一种或几种。优选地,粘结剂为pvdf。
10.进一步地,锂离子电池用隔膜中还可包括导电剂,导电剂占石墨层总重的5%以下。
11.进一步地,导电剂选自碳黑,碳纳米管,石墨烯等。
12.进一步地,锂离子电池用隔膜中还包括分散助剂,分散助剂占石墨层总重的2%以下。
13.进一步地,分散助剂采用pva(聚乙烯醇)。
14.进一步地,隔膜基体的材质选自pe、pp和pi中中的一种或几种。
15.进一步地,隔膜基体的厚度为5
‑
20微米。
16.本发明的第二个目的是提供一种快充型锂离子电池的制备方法,包括以下步骤:
17.(1)制备本发明的上述锂离子电池用隔膜;
18.(2)将锂离子电池用隔膜的石墨层与负极极片贴合,根据石墨层内粘结剂含量和隔膜材料及不同热压后剥离力的需求,选择适当的压力(1
‑
20ton/mm2)压力及70
‑
95℃下进行热压复合,以使得负极极片与隔膜复合。
19.进一步地,在步骤(2)中,负极极片包括负极活性物,负极活性物与石墨层贴合。
20.进一步地,负极活性物选自含有石墨的单一或含有硅碳,lto等材料的复合体系。
21.进一步地,负极活性物为石墨,石墨的粒径大于涂层中的石墨颗粒的粒径。通常情况下,负极活性物所选的石墨的粒径为10
‑
30μm。通过本发明的工艺可以达到负极极片具有紧密结合的双层石墨材料的结构。
22.本发明在隔膜对负极面涂覆了小颗石墨材料涂层,从而在保持了一定的电池的能量密度的同时改善电池倍率和循环性能。
23.在常温25摄氏度时,soc0%
‑
soc80%的充电时间在48分钟之内,或充电倍率在1c以上可充电的电池一般认为是“快充型锂离子电池”。
24.借由上述方案,本发明至少具有以下优点:
25.本发明的锂离子电池用隔膜中采用含小颗粒功能性石墨颗粒的石墨层,充分利用小颗粒石墨颗粒的超高倍率性优点,大幅度改善了快充型电极表面的析锂现象,提升快充型锂离子电池的循环,倍率性能及安全性能。
26.本发明的快充型锂离子电池在制备过程中,采用热压复合工艺将上述锂离子电池用隔膜和负极极片复合,达到隔膜上的小颗粒功率型石墨颗粒与原有负极极片上的负极活性物紧密结合的负极双层涂布的效果,从而制备超高功率性能的快充型锂离子电池。通过隔膜与热压复合工艺的结合的方法实现双层涂布效果,不仅具有比原有同时在负极表面涂布双层不同粒径的石墨涂布工艺简单,涂布均一,可操作性高的优点。同时,也达到了隔膜和负极极片的紧密结合的效果,从而从两个方面达到动力学的改善,大大提高了快充型锂离子电池的功率性能。
27.上述说明仅是本发明技术方案的概述,为了能够更清楚了解本发明的技术手段,并可依照说明书的内容予以实施,以下以本发明的较佳实施例并配合详细附图说明如后。
附图说明
28.图1是含小颗粒石墨层的隔膜与负极的贴合示意图;
29.附图标记说明:
[0030]1‑
隔膜基体;2
‑
功率型石墨材料;3
‑
大颗粒人造石墨;4
‑
铜箔。
具体实施方式
[0031]
下面结合实施例,对本发明的具体实施方式作进一步详细描述。以下实施例用于说明本发明,但不用来限制本发明的范围。
[0032]
对比例1
[0033]
商用20μm厚的材质为pppp隔膜。
[0034]
实施例1
[0035]
一种含小颗粒石墨层的隔膜,制备方法如下:
[0036]
将功率型石墨材料2,具体选择石墨a:d50为3μm,粒径分布1
‑
5μm、pvdf与水制备成溶液后。采用喷涂方式,均匀喷涂在20μm厚的隔膜基体1表面,以在隔膜基体1的一侧表面形成连续的石墨层,石墨层中具有多个间隔分布的岛状结构。其中,石墨层中,功率型石墨材料2、pvdf占石墨层总质量的质量分数依次为95%、5%。隔膜基体1材质为pp隔膜,石墨层的厚度为8μm。
[0037]
实施例2
‑6[0038]
一种含小颗粒石墨层的隔膜,制备方法如下:
[0039]
将功率型石墨材料(石墨a:d50为3μm,粒径分布1
‑
5μm或石墨b:d50为6μm,粒径分布2
‑
10μm)、pvdf,导电剂superp与水制备成溶液a或溶液b,采用喷涂方式,均匀喷涂在20μm厚的隔膜表面,以在隔膜的一侧表面形成连续的石墨层,石墨层中具有多个间隔分布的岛状结构。其中,石墨层中,功率型石墨材料、pvdf、导电剂占石墨层总质量的质量分数依次为95%、3%、2%。隔膜材质为pp隔膜。石墨层的厚度见表1。
[0040]
表1隔膜涂层厚度与相应负极表
[0041][0042]
利用实施例的隔膜制备快充型锂离子电池,步骤如下:
[0043]
采用1ah软包电池设计,正极材料为三元622材料,负极包括铜箔4以及位于铜箔4一侧表面的负极活性层,其中负极活性层包括大颗粒人造石墨3(粒径为d50 15μm)。
[0044]
另利用对比例1的隔膜按照常规方法组装成锂离子电池。
[0045]
叠片过程中,将隔膜基体1上带有石墨层的一面与负极活性层紧密贴合(图1),之后采用热压化成过程,通过加压8ton/mm2和80℃下加热60秒,将隔膜基体1与负极紧密结合,达到双层涂布效果。
[0046]
测试以上制备的锂离子电池的常温循环寿命。循环性能通过两种不同充电,相同放电情况下(cc 1c至2.5v)的循环寿命对比来体现本发明对锂离子电池快充性能的改善。
[0047]
充电方式一:充电:cc/cv 0.5c至4.3v,0.05c截止,soc0
‑
80%充电时间96min。
[0048]
充电方式二:快速充电:2c,9min
‑
1.5c,8min
‑
1c,18min
‑
0.5c至4.3v,0.05c截止,soc0
‑
80%充电时间35min。结果如表2所示:
[0049]
表2不同锂离子电池的电学性能
[0050][0051][0052]
由表2可看出,实施例1
‑
6均较对比例1在常温普通充电上改善不明显,在快充循环性能上均有显著提升,加入导电剂对性能有提升(实施例1和实施例3)。进一步地,石墨大小及涂层厚度的影响分析如下:
[0053]
(1)石墨层厚度
[0054]
石墨a:d50为3μm,粒径分布2
‑
10μm时,对比实施例2至4,随着涂布厚度的增加(4μm、8μm、20μm),锂离子电池的电学性能上升后又下降。当厚度为8μm时,即石墨层厚度约为石墨a的d50值的2.5倍(3
×
2.5=8.5μm)左右时,达到性能最佳值。
[0055]
石墨b:d50为6μm,粒径分布2
‑
10μm时,涂层厚度越薄,电池性能更优。
[0056]
(2)石墨颗粒大小影响
[0057]
对比实施例4和实施例6,涂层相同厚度20μm时,涂层中选择小颗粒石墨的电学性能优于涂层中选择大颗粒石墨的电学性能。
[0058]
为了提高高能量密度快充体系的倍率性能,目前技术为双层涂布工艺。本发明开发了一种在隔膜表面涂覆功率型石墨材料的技术,充分利用小粒径的石墨具有良好的功率性,抑制高倍率析锂性能,大大拓展高倍率下充电的性能窗口,进而减少充电时间,保持优良的循环性能。同时本方法具有工艺简单,可制造性高的特点。
[0059]
以上仅是本发明的优选实施方式,并不用于限制本发明,应当指出,对于本技术领域的普通技术人员来说,在不脱离本发明技术原理的前提下,还可以做出若干改进和变型,这些改进和变型也应视为本发明的保护范围。