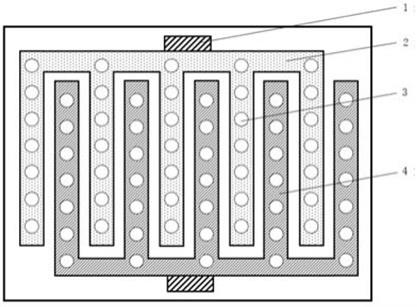
1.本发明属于微型超级电容器领域,特别涉及一种非对称三维叉梳微柱阵列电极结构超级电容器制备方法。
背景技术:2.随着mems技术的不断发展,微系统的体积不断降低,智能化程度不断提高。然而,器件的微型化对电源系统提出了极大的挑战。微能源技术作为mems系统的关键技术之一,近年来受到了各国政府的高度重视。目前,研究人员采用开展光伏、振动、温差等多源复合的微型能量收集系统以获取更高的能量密度,然而随着系统体积的微型化,薄膜锂电池、微型镍锌电池输出功率低、循环寿命短的不足逐渐凸显出来,难以实现微系统高功率输出的工作需求。
3.作为微储能技术的重要组成部分,微型超级电容器可以弥补微电池的不足,得到了各国学者的广泛关注。微型超级电容器具有体积小、储能密度高、功率密度高、循环寿命长等多种优势,在微小型电子器件、植入式传感器、智能微尘、无线传感网络、微小型飞行器等多个领域具有极强的应用前景。
4.目前而言,微型超级电容器主要集中于进一步提升其储能密度与功率密度,往往从材料与结构方面开展研究。在材料上,通过不同电极材料的复合改性,制备出具备三维结构的比表面积更高、电极活性更强的复合材料,在结构上通过制备高深宽比的三维结构电极,在增加比表面积的同时,利用特殊的微纳结构与微纳效应,改善电极材料的综合性能。在申请号为2016112187543,一种非对称超级电容器的制备方法中,以氧化亚铜为牺牲模板,通过常温搅拌,得到氢氧化钴,再通过水热法对氢氧化钴硫化得到空心硫化钴粉末,这空心结构能缩短离子的扩散距离,提高了活性物质的利用率,从而提高了材料的比电容,种以硫化钴粉末为正极,多孔碳材料为负极,组装制备得到了不对称的超级电容器;但是,仍然受限于复杂的结构加工工艺以及电极薄膜制备工艺,不能满足当前mems技术发展对微系统的体积、电容器的能量密度和功率密度的要求;目前的超级电容器仍然以梳齿电极为主,多为在平面结构内加工图形化的电极薄膜,其电极厚度依然较低,仍未实现真正的三维结构电极。此外,薄膜制备工艺中,电极材料皲裂、脱落的问题,仍然是亟待解决的关键问题。
技术实现要素:5.本发明的目的是提供一种非对称三维叉梳微柱阵列电极结构超级电容器制备方法;所述超级电容器采用icp刻蚀与激光雕刻等微纳加工工艺,设计制备出叉梳式微柱阵列电极结构,在微结构表面溅射一层金作为集流体,继而分别在正极与负极微结构表面沉积赝电容与双电层电容材料薄膜,制备出非对称式微型mems超级电容器;其特征在于,所述三维叉梳式微柱阵列电极结构的制备工艺步骤如下:(a)soi备片:选取厚度为80μm、2μm和400μm的soi片,使用uv灯、显微镜对soi片进行镜检,清洗;
(b)旋涂光刻胶:光刻胶厚度5μm
±
0.5μm;(c)光刻:光刻出微柱阵列形状,微柱直径70μm
±
0.5μm;(d)icp刻蚀:刻蚀深度80μm
±
0.5μm,刻蚀出微柱阵列,去除光刻胶;(e)磁控溅射au:厚度80nm
±
2nm;(f)激光雕刻,雕刻深度5μm
±
1μm,刻蚀出叉梳式结构,清洗。
6.所述正极材料为赝电容活性材料,包括氧化锰、氧化钌、氧化镍和聚吡咯。
7.所述正极材料通过电化学沉积工艺制备得到正电极薄膜,或正极材料与碳纳米管、石墨烯的复合共沉积制备正电极薄膜;其中,氧化锰正极薄膜的制备工艺如下:利用chi660d电化学工作站,采用恒流脉冲沉积,沉积液为乙酸锰溶液,浓度为0.2mol/l,阳极外加电流为10ma/cm2,所对应的通电时间20s,阴极外加电流为10ma/cm2,所对应的通电时间5s,沉积完成后用去离子水冲洗电极,然后放置在常温空气气氛中烘干2小时;得到正电极薄膜;该恒流脉冲电沉积工艺在mno2电极表面形成微观导电网络,提高活性物质的利用率,获得电化学性能更加优异的电极材料。
8.所述负极材料为双电层活性电极材料,包括石墨烯和碳纳米管。
9.所述负极双电层活性电极材料通过电化学沉积工艺得到电极薄膜;先用丙酮溶液清洗三维微结构,再用去离子水超声清洗15min;用丙酮溶液将碳纳米管进行氧化处理;采用电化学工作站,通过电泳沉积法制备碳纳米管电极薄膜,沉积电压为50v,沉积时间为15min,电解液为0.05mg/mlal(no3)3乙醇溶液,沉积完成后用去离子水冲洗电极,然后放置在常温空气气氛中烘干2小时。
10.所述的微型mems超级电容器,测试电解液采用6mol/l的 koh溶液和1mol/l的 lioh溶液组成的电解液。
11.本发明的有益效果在于:采用icp刻蚀、激光雕刻、磁控溅射等微纳加工工艺,设计制备出叉梳式微柱阵列电极结构,可有效提升电极比表面积,降低电子传输距离,从而降低电极阻抗,提升器件功率密度;通过分别在正极与负极微结构表面沉积赝电容与双电层电容材料薄膜,制备出非对称式微型mems超级电容器,可综合双电层电容和赝电容储能机制,可拓宽电化学稳定窗口,提升器件储能密度,所制备出的非对称式mems超级电容器可应用于物联网节点电源、个人电子产品等领域。
附图说明
12.图1为微型mems超级电容器结构示意图。
13.图2为超级电容器结构加工工艺流程图。
14.图中标号:1为电极两侧的集流体,2为叉梳正极,3为微柱阵列,4为叉梳负极。
具体实施方式
15.本发明提供一种非对称三维阵列电极结构超级电容器制备方法;下面结合附图和实施例对本发明作进一步描述:图1所示的微型超级电容器结构由叉梳正极2、叉梳负极4、电极两侧的集流体1组成。其中叉梳正极2、叉梳负极4上均有微柱阵列3排布;每个微柱直径70μm,高度60μm;微柱间距80μm,梳齿宽度80μm。
16.图2所示为超级电容器电极微结构的加工工艺流程图,主要包括icp等离子体刻蚀、溅射镀膜等工艺,具体工艺流程包括:(a),soi备片:选取soi片,可有效控制后续刻蚀工艺的刻蚀精度,保证微结构的一致性,选取厚度80μm、2μm或400μm的soi硅片,使用uv灯、显微镜对soi片进行镜检,检查有无质量问题,清洗soi片;(b),旋涂光刻胶:光刻胶厚度5μm
±
0.5μm;(c),光刻:经显影曝光,光刻出微柱阵列形状,微柱直径70μm
±
0.5μm;(d),icp刻蚀:利用等离子体刻蚀方法,刻蚀出微柱阵列,刻蚀深度80μm
±
0.5μm,去除光刻胶;(e),磁控溅射au:溅射金作为后续电极材料沉积的集流体,溅射厚度为80nm
±
2nm;(f),激光雕刻,雕刻深度5μm
±
1μm,刻蚀出叉梳式结构,清洗。
17.所述正极材料为赝电容活性材料,包括氧化锰、氧化钌、氧化镍和聚吡咯。
18.所述正极材料为赝电容活性材料,包括氧化锰、氧化钌、氧化镍和聚吡咯。
19.所述正极材料通过电化学沉积工艺制备得到正电极薄膜,或正极材料与碳纳米管、石墨烯的复合共沉积制备正电极薄膜;所述正极材料选用氧化锰的正极薄膜制备工艺如下:先用丙酮溶液清洗三维微柱,再用去离子水超声清洗15min,利用chi660d电化学工作站,采用恒流脉冲沉积方法,沉积液为乙酸锰溶液,浓度为0.2mol/l,阳极外加电流为10ma/cm2,所对应的通电时间20s,阴极外加电流为
‑
10ma/cm2,所对应的通电时间5s,沉积完成后用去离子水冲洗电极,然后放置在常温空气气氛中烘干2小时。得到正电极薄膜,该恒流脉冲电沉积工艺在mno2电极表面形成微观导电网络,提高活性物质的利用率,获得电化学性能更加优异的电极材料。
20.所述正极材料选用聚吡咯的正极薄膜制备工艺如下:采用电化学工作站,利用双电极直流阴极沉积法电沉积制备活性电极薄膜,其中硅基微结构作为阴极与工作电极,铂电极作为阳极和辅助电极;先用丙酮溶液清洗三维微结构,再用去离子水超声清洗15min,沉积液为对甲基苯磺酸钠(c7h7so3na)与聚吡咯(c4h4n)的混合溶液,其对甲基苯磺酸钠(c7h7so3na)的浓度为0.6mol/l, 聚吡咯(c4h4n)浓度为0.6mol/l,用稀硫酸调节溶液ph值为4.0,设置沉积电流密度为500 ma/cm2,沉积时间为1000秒,沉积完成后用去离子水冲洗电极,然后放置在常温空气气氛中烘干2小时。
21.所述负极材料为双电层活性电极材料,包括石墨烯和碳纳米管。
22.所述负极双电层活性电极材料通过电化学沉积工艺得到电极薄膜;先用丙酮溶液清洗三维微结构,再用去离子水超声清洗15min;用丙酮溶液将碳纳米管进行氧化处理;采用电化学工作站,通过电泳沉积法制备碳纳米管电极薄膜,沉积电压为50v,沉积时间为15min,电解液为0.05mg/mlal(no3)3乙醇溶液,沉积完成后用去离子水冲洗电极,然后放置在常温空气气氛中烘干2小时。
23.所述的微型mems超级电容器,测试电解液采用水系盐溶液,对于正极为二氧化锰薄膜,可选用6mol/l的 koh溶液和1mol/l的 lioh溶液组成的电解液。
24.所述的微型超级电容器,可采用固态电解质,进行管壳封装。
25.本发明设计采用soi硅片制备出叉梳式微柱阵列电极结构,可保证微结构刻蚀的
一致性,有效提升超级电容器电极比表面积,有利于提升微型超级电容器的储能密度与功率密度,通过分别在正极与负极微结构表面沉积赝电容与双电层电容材料薄膜,制备出非对称式微型mems超级电容器,可综合双电层电容和赝电容储能机制,可拓宽电化学稳定窗口,提升器件储能密度。
26.本发明可移植性强,电极材料可用范围广,电解液可适用于水系、有机体系以及固态电解质体系,所制备出的mems超级电容器,可与其他mems器件进行可靠集成,在个人电子产品、物联网节点等领域具有广泛的应用前景。