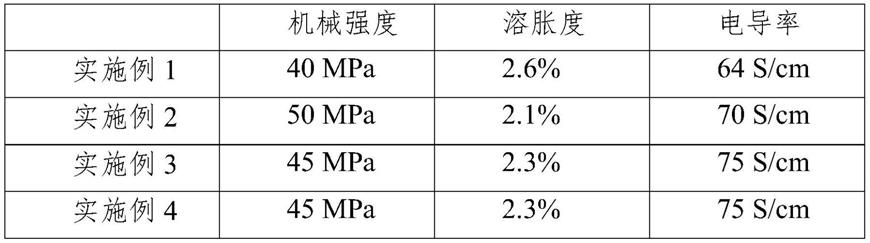
1.本发明属于质子交换膜技术领域,具体涉及一种质子交换膜的制备方法及系统。
背景技术:2.氢能是二十一世纪可持续发展的主旋律,氢能技术又是实现碳达峰及碳中和的不可或缺的洁净能源技术。在氢能技术领域中电解水是氢能上游的制氢技术,而燃料电池则是氢能领域中用氢的技术,实现了氢能应用的首尾呼应。
3.质子交换膜电解水及质子交换膜燃料电池又是应用范围最广、技术相对成熟、市场潜力最大的两个技术。而其中的质子交换膜又是这两大关键技术中的关键材料。
4.质子交换膜(pem)是一种离子传导型薄膜,其为质子的迁移和输送提供通道,同时阻隔阳极和阴极气体,防止二者混合。质子交换膜是电解水制氢及氢氧燃料电池的核心部件之一,其性能与电池的性能密切相关。在电池运行过程中,质子交换膜对电池性能的影响主要体现在面电阻上,而面电阻的大小由质子交换膜的离子电导率及质子交换膜的厚度决定,所以对于燃料电池内部使用的质子交换膜,目前超薄化及高强度化是现今质子膜发展的必然趋势。
5.目前的质子交换膜制备技术较多的是将水解前的全氟磺酸树脂进行加热熔融,然后挤出到基膜上,制备成膜后再进行水解处理得到质子交换膜。然而,这种方法有两个缺点,一是熔融挤出制备得到的质子交换膜厚度较厚,一般为100微米以上;二是,这种方法很难在质子交换膜中间加入增强层来提高膜的机械性能。另外一种目前比较常用的方法是先将全氟磺酸树脂分散到水和醇的溶剂体系中,通过将聚合物溶液直接涂布到pet等基膜上,再经过干燥及热处理后形成质子交换膜。这种方法虽然得到厚度较薄的质子交换膜,但是其很难承受在电解池或燃料电池运行过程中阴阳两极的压力差及由于吸水溶胀带来的尺寸变化。
技术实现要素:6.针对现有质子交换膜存在不能兼顾厚度和强度要求的问题,本发明提供了一种质子交换膜的制备方法及系统。
7.本发明解决上述技术问题所采用的技术方案如下:
8.一方面,本发明提供了一种质子交换膜的制备方法,包括以下操作步骤:
9.提供离型膜;
10.在离型膜上涂覆第一质子交换树脂浆料,形成第一质子交换层;
11.将增强网层的一表面覆盖于第一质子交换层上,使第一质子交换层的质子交换树脂浆料进入增强网层,加热干燥得到增强网层、第一质子交换层和离型膜的复合层;
12.将第二质子交换树脂浆料涂覆于增强网层的另一表面,形成第二质子交换层,加热干燥,收卷得到质子交换膜和离型膜复合的材料。
13.可选的,所述质子交换膜与所述离型膜的离型力为1~100g/mm。
14.可选的,所述离型膜和所述增强网层均为卷材供料,质子交换膜和离型膜复合的材料收卷得到卷材,所述第一质子交换层和所述第二质子交换层的涂覆方式各自独立地选自狭缝涂布、凹版涂布、逗号刮刀涂布和丝网印刷中的一种或多种,涂覆厚度为100~1000um。
15.可选的,所述第一质子交换树脂浆料和所述第二质子交换树脂浆料均包括质子交换树脂和溶剂,且所述质子交换树脂各自独立地选自全氟磺酸树脂、部分氟化的磺酸树脂、磺化的聚醚、磺化的聚醚醚酮、磺化的聚砜、磺化的聚醚砜、季铵盐类的阴离子交换树脂和咪唑类的阴离子交换树脂中的一种或多种;所述第一质子交换树脂浆料和所述第二质子交换树脂浆料的固含量为5~50%。
16.可选的,所述第一质子交换树脂浆料和所述第二质子交换树脂浆料中还添加有无机颗粒填料,所述无机颗粒填料的添加质量含量为0.1~10%,所述无机颗粒填料选自sio2、ceo2、mno2、mnso4、pt、pt/c中的一种或多种。
17.可选的,所述增强网层的厚度为5~200um,孔径为0.1um~1mm,强度为10~100mpa。
18.可选的,所述增强网层选自膨体ptfe、聚醚醚酮(peek)编织网和聚酯编织网中的一种或多种。
19.可选的,所述“形成第二质子交换层,加热干燥”后,还包括热处理和降温的操作。
20.另一方面,本发明提供了一种质子交换膜的制备系统,包括用于离型膜放料的第一放卷辊、用于增强网层放料的第二放卷辊、以及沿第一放卷辊送料方向依次设置的第一涂布辊、第一加热干燥装置、第二涂布辊和第二加热干燥装置,所述第二放卷辊放料的增强网层与所述第一涂布辊的放料进入所述第一加热干燥装置复合。
21.可选的,所述第一加热干燥装置包括复合辊,所述复合辊中设置有加热装置,所述第二放卷辊放料的增强网层与所述第一涂布辊的放料在所述复合辊上复合并同时进行加热烘干处理。
22.根据本发明提供的质子交换膜的制备方法,采用离型膜作为成型基体,通过在离型膜上进行第一质子交换树脂浆料的涂覆和后续的增强网层施加以及第二质子树脂浆料的涂覆,能够有效控制形成的质子交换膜的厚度,避免质子交换膜过厚,同时,增强网层的加入提高了所述质子交换膜的整体机械强度,使其满足电解池或燃料电池应用时的压力差承载要求,保证质子交换膜的尺寸稳定性;增强网层的双面涂覆提高了第一质子交换树脂浆料和第二质子交换树脂对于增强网层的填充程度,保证增强网层与第一质子交换层和第二质子交换层的一体成型效果。同时,所述离型膜在质子交换膜成型后可作为保护层以形成卷材,实现大规模连续化制备质子交换膜的目的。
附图说明
23.图1是本发明提供的质子交换膜的制备系统的结构示意图;
24.图2是本发明提供的质子交换膜的制备系统的另一结构示意图。
25.说明书附图中的附图标记如下:
[0026]1‑
第一放卷辊;2
‑
第一涂布辊;21
‑
第一涂布头;3
‑
第二放卷辊;4a
‑
复合辊;4b
‑
复合辊;5
‑
烘干装置;6
‑
第二涂布辊;61
‑
第二涂布头;7
‑
第二加热干燥装置;8
‑
热处理装置;9
‑
降温装置。
具体实施方式
[0027]
为了使本发明所解决的技术问题、技术方案及有益效果更加清楚明白,以下结合附图及实施例,对本发明进行进一步详细说明。应当理解,此处所描述的具体实施例仅仅用以解释本发明,并不用于限定本发明。
[0028]
本发明实施例提供了一种质子交换膜的制备方法,包括以下操作步骤:
[0029]
提供离型膜;
[0030]
在离型膜上涂覆第一质子交换树脂浆料,形成第一质子交换层;
[0031]
将增强网层的一表面覆盖于第一质子交换层上,使第一质子交换层的质子交换树脂浆料进入增强网层,加热干燥得到增强网层、第一质子交换层和离型膜的复合层;
[0032]
将第二质子交换树脂浆料涂覆于增强网层的另一表面,形成第二质子交换层,加热干燥,收卷得到质子交换膜和离型膜复合的材料。
[0033]
采用离型膜作为成型基体,通过在离型膜上进行第一质子交换树脂浆料的涂覆和后续的增强网层施加以及第二质子树脂浆料的涂覆,能够有效控制形成的质子交换膜的厚度,避免质子交换膜过厚,同时,增强网层的加入提高了所述质子交换膜的整体机械强度,使其满足电解池或燃料电池应用时的压力差承载要求,保证质子交换膜的尺寸稳定性;增强网层的双面涂覆提高了第一质子交换树脂浆料和第二质子交换树脂对于增强网层的填充程度,保证增强网层与第一质子交换层和第二质子交换层的一体成型效果。同时,所述离型膜在质子交换膜成型后可作为保护层以形成卷材,实现大规模连续化制备质子交换膜的目的。
[0034]
在一些实施例中,所述质子交换膜与所述离型膜的离型力为1~100g/mm。
[0035]
所述质子交换膜在具体应用时可裁切至所需尺寸后,去除所述离型膜,即可作为电解池或燃料电池的质子交换膜使用,因此,所述离型膜和所述质子交换膜之间需要具有合适的离型力,保证所述离型膜和所述质子交换膜之间的分离,同时也避免作为卷材存储时,所述离型膜和所述质子交换膜外表面的相互粘附。
[0036]
在一些实施例中,所述第一质子交换层和所述第二质子交换层的加热干燥温度为40~100℃。
[0037]
在一些实施例中,所述离型膜和所述增强网层均为卷材供料,质子交换膜和离型膜复合的材料收卷得到卷材,所述第一质子交换层和所述第二质子交换层的涂覆方式各自独立地选自狭缝涂布、凹版涂布、逗号刮刀涂布和丝网印刷中的一种或多种,涂覆厚度为100~1000um。
[0038]
在一些实施例中,所述第一质子交换树脂浆料和所述第二质子交换树脂浆料均包括质子交换树脂和溶剂,且所述质子交换树脂各自独立地选自全氟磺酸树脂、部分氟化的磺酸树脂、磺化的聚醚、磺化的聚醚醚酮、磺化的聚砜、磺化的聚醚砜、季铵盐类的阴离子交换树脂和咪唑类的阴离子交换树脂中的一种或多种;所述第一质子交换树脂浆料和所述第二质子交换树脂浆料的固含量为5~25%。所述溶剂可选自水或其他有机溶剂。
[0039]
在一些实施例中,所述第一质子交换树脂浆料和所述第二质子交换树脂浆料中还添加有无机颗粒填料,所述无机颗粒填料的添加质量含量为0.1~10%,所述无机颗粒填料
选自sio2、ceo2、mno2、mnso4、pt、pt/c中的一种或多种。
[0040]
加入的无机颗粒填料对于所述质子交换膜具有保湿和抗氧化的作用。
[0041]
在一些实施例中,所述增强网层的厚度为5~200um,孔径为0.1um~1mm,强度为10~100mpa。
[0042]
在一些实施例中,所述增强网层选自膨体ptfe、聚醚醚酮(peek)编织网和聚酯编织网中的一种或多种。
[0043]
在一些实施例中,所述“形成第二质子交换层,加热干燥”后,还包括热处理和降温的操作。
[0044]
在一些实施例中,所述热处理的处理温度为140~250℃,处理时间为10min~2h,以使所述质子交换膜中的质子交换树脂产生交联。热处理和降温操作后,所述第一质子交换层和所述第二质子交换层的厚度为3~40um。
[0045]
在一些实施例中,所述降温操作的处理温度为40~100℃。
[0046]
在一些实施例中,所述质子交换膜的厚度为5~100um。
[0047]
如图1和图2所示,本发明提供了一种质子交换膜的制备系统,包括用于离型膜放料的第一放卷辊1、用于增强网层放料的第二放卷辊3、以及沿第一放卷辊1送料方向依次设置的第一涂布辊2、第一加热干燥装置、第二涂布辊6和第二加热干燥装置7,所述第二放卷辊3放料的增强网层与所述第一涂布辊2的放料进入所述第一加热干燥装置复合。
[0048]
所述质子交换膜的制备系统用于上述的质子交换膜的制备方法的实施。
[0049]
通过所述第一放卷辊1进行离型膜的放料,所述第一放卷辊1放料的离型膜进入所述第一涂布辊2进行第一质子交换层的涂覆,涂覆有第一质子交换层的离型膜与所述第二放卷辊3放料的增强网层一同进入所述第一加热干燥装置,将增强网层附着于第一质子交换层上,并通过所述第一加热干燥装置加热去除溶剂,然后在第二涂布辊6处进行所述第二质子交换层的涂布,在所述第二加热干燥装置7处进行第二质子交换层的加热干燥,得到质子交换膜与离型膜的复合材料。
[0050]
在一些实施例中,所述第一涂布辊2处设置有第一涂布头21,所述第二涂布辊6处设置有第二涂布头61。
[0051]
在一实施例中,所述质子交换膜的制备系统还包括有热处理装置8和降温装置9,所述热处理装置8和所述降温装置9间隔设置于所述第二加热干燥装置7的送料方向下游,所述热处理装置8用于对干燥后的质子交换膜进行进一步的热处理,所述降温装置9用于对热处理后的质子交换膜进行冷却降温。
[0052]
如图1所示,在一实施例中,所述第一加热干燥装置包括复合辊4a和烘干装置5,所述第二放卷辊3放料的增强网层与所述第一涂布辊2放料的带有第一质子交换层的离型膜在所述复合辊4a上复合,复合后的物料传送至所述烘干装置5进行加热烘干处理。
[0053]
图1所示的质子交换膜的制备系统中,将所述增强网层与所述第一质子交换层的复合操作和干燥操作分为两个不连续的步骤进行,容易由于第一质子交换层干燥收缩,导致增强网层、第一质子交换层和离型膜的收缩程度存在差异,进而出现膜材卷曲或膜层分离的问题。
[0054]
为了解决上述的技术问题,如图2所示,在优选的实施例中,所述第一加热干燥装置包括复合辊4b,所述复合辊4b中设置有加热装置,所述第二放卷辊3放料的增强网层与所
述第一涂布辊2的放料在所述复合辊4上复合并同时进行加热烘干处理。
[0055]
在本实施例中,将所述第二放卷辊3放料的增强网层和所述第一涂布辊2放料的带有第一质子交换层的离型膜同时置于复合辊4b上,通过复合辊4b对离型膜、第一质子交换层和增强网层产生一定的张力,同时,通过所述加热装置对所述复合辊4b进行加热,进而在张力的条件下使第一质子交换层干燥成型,进而可以避免由于第一质子交换层收缩而导致膜层分离或膜材卷曲的问题。
[0056]
在一些实施例中,所述第二加热干燥装置7采用与所述第一加热干燥装置相同的结构。
[0057]
以下通过实施例对本发明进行进一步的说明。
[0058]
实施例1
[0059]
本实施例用于说明本发明公开的质子交换膜的制备方法,采用如图2所示的系统进行制备,包括以下操作步骤:
[0060]
(1)在容量瓶中分别加入一定量的全氟磺酸树脂溶液,通过加入水及醇类调节到固含量范围在10%,将其作为第一涂布头和第二涂布头的全氟磺酸树脂浆料。
[0061]
(2)在第一涂布头处控制湿膜涂布厚度在200微米厚度。
[0062]
(3)在复合辊处将从第二放卷辊放出的5微米厚增强网层与全氟磺酸树脂浆料复合,全氟磺酸树脂浆料渗透进入增强网层。
[0063]
(4)40℃进行干燥热处理10min。
[0064]
(5)第二涂布头涂布200微米湿膜厚度。
[0065]
(6)先在涂布机内采用40℃进行干燥热处理,接着进入140℃进行热处理,随后进入60℃的降温处理,最后得到透明的增强型质子交换膜,质子交换膜厚度10微米。
[0066]
实施例2
[0067]
本实施例用于说明本发明公开的质子交换膜的制备方法,采用如图2所示的系统进行制备,包括以下操作步骤:
[0068]
(1)在容量瓶中分别加入一定量的全氟磺酸树脂溶液,通过加入水及醇类调节到固含量范围在10%,将其作为第一涂布头和第二涂布头的全氟磺酸树脂浆料。
[0069]
(2)在第一涂布头处控制湿膜涂布厚度在200微米厚度。
[0070]
(3)在复合辊处将从第二放卷辊放出的5微米厚增强网层与全氟磺酸树脂浆料复合,全氟磺酸树脂浆料渗透进入增强网层。
[0071]
(4)60℃进行干燥热处理10min。
[0072]
(5)第二涂布头涂布200微米湿膜厚度。
[0073]
(6)先在涂布机内采用40℃进行干燥热处理,接着进入250℃进行热处理,随后进入100℃的降温处理,最后得到透明的增强型质子交换膜,质子交换膜厚度10微米。
[0074]
实施例3
[0075]
本实施例用于说明本发明公开的质子交换膜的制备方法,采用如图2所示的系统进行制备,包括以下操作步骤:
[0076]
(1)在容量瓶中分别加入一定量的全氟磺酸树脂溶液,通过加入水及醇类调节到固含量范围在10%,将其作为第一涂布头和第二涂布头的全氟磺酸树脂浆料。
[0077]
(2)在第一涂布头处控制湿膜涂布厚度在300微米厚度。
[0078]
(3)在复合辊处将从第二放卷辊放出的5微米厚增强网层与全氟磺酸树脂浆料复合,全氟磺酸树脂浆料渗透进入增强网层。
[0079]
(4)60℃进行干燥热处理10min。
[0080]
(5)第二涂布头涂布300微米湿膜厚度。
[0081]
(6)先在涂布机内采用40℃进行干燥热处理,接着进入250℃进行热处理,随后进入100℃的降温处理,最后得到透明的增强型质子交换膜,质子交换膜厚度15微米。
[0082]
实施例4
[0083]
本实施例用于说明本发明公开的质子交换膜的制备方法,采用如图2所示的系统进行制备,包括以下操作步骤:
[0084]
(1)在容量瓶中分别加入一定量的全氟磺酸树脂溶液,通过加入水及醇类调节到固含量范围在15%,将其作为第一涂布头和第二涂布头的全氟磺酸树脂浆料。
[0085]
(2)在第一涂布头处控制湿膜涂布厚度在200微米厚度。
[0086]
(3)在复合辊处将从第二放卷辊放出的5微米厚增强网层与全氟磺酸树脂浆料复合,全氟磺酸树脂浆料渗透进入增强网层。
[0087]
(4)60℃进行干燥热处理10min。
[0088]
(5)第二涂布头涂布200微米湿膜厚度。
[0089]
(6)先在涂布机内采用40℃进行干燥热处理,接着进入250℃进行热处理,随后进入100℃的降温处理,最后得到透明的增强型质子交换膜,质子交换膜厚度15微米。
[0090]
实施例5
[0091]
本实施例用于说明本发明公开的质子交换膜的制备方法,采用如图2所示的系统进行制备,包括以下操作步骤:
[0092]
(1)在容量瓶中分别加入一定量的全氟磺酸树脂溶液,通过加入水及醇类调节到固含量范围在20%,将其作为第一涂布头和第二涂布头的全氟磺酸树脂浆料。
[0093]
(2)在第一涂布头处控制湿膜涂布厚度在1000微米厚度。
[0094]
(3)在复合辊处将从第二放卷辊放出的80微米厚增强网层与全氟磺酸树脂浆料复合,全氟磺酸树脂浆料渗透进入增强网层。
[0095]
(4)60℃进行干燥热处理10min。
[0096]
(5)第二涂布头涂布1000微米湿膜厚度。
[0097]
(6)先在涂布机内采用60℃进行干燥热处理,接着进入250℃进行热处理,随后进入100℃的降温处理,最后得到透明的增强型质子交换膜,质子交换膜厚度100微米。
[0098]
对比例1
[0099]
本对比例用于对比说明本发明公开的质子交换膜的制备方法,包括实施例1中大部分操作步骤,其不同之处在于:
[0100]
不设置所述增强网层。
[0101]
性能测试
[0102]
对上述制备得到的质子交换膜进行如下性能测试:
[0103]
机械强度测试:采用astm d638测试方法,用标准裁刀将质子膜裁剪成哑铃状,将其装在拉力测试仪上,用5mm每分钟的速度去拉膜的一端,直到膜断裂,根据在拉力测试过程中检测到的拉力变化及形变量计算得到拉伸强度。
[0104]
溶胀度测试:将质子膜裁剪成3
×
4cm的长方形,放置于80摄氏度的热水中浸泡1小时后拿出,测试其长宽的变化,其长宽方向的尺寸变化率即为其溶胀度。
[0105]
电导率测试:将质子膜裁剪成1
×
2cm的长方形,将其放置于scribner的membrane test system设备中,测试其在70%湿度80摄氏度的离子电导率。
[0106]
得到的测试结果填入表1。
[0107]
表1
[0108][0109][0110]
从表1的测试结果可以看出,相比于对比例1提供的质子交换膜,采用本发明提供的制备方法制备得到的质子交换膜在相同的厚度下,具有较高的机械强度,同时也具有较低的溶胀度。
[0111]
以上所述仅为本发明的较佳实施例而已,并不用以限制本发明,凡在本发明的精神和原则之内所作的任何修改、等同替换和改进等,均应包含在本发明的保护范围之内。