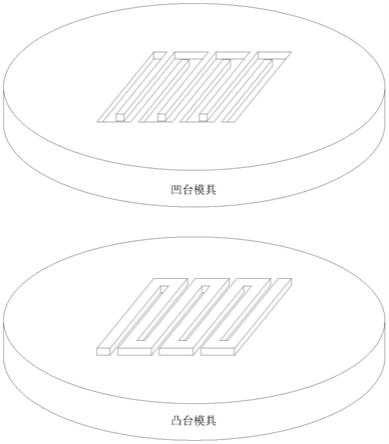
1.本发明涉及薄膜制作技术,特别涉及低压微区薄膜制作技术。
背景技术:2.毫米级别以下的微区加热技术是气味识别、环境检测、红外发射及生物芯片等领域的基础技术,是近年来相关领域国内外研究的热点之一。与采用高压脉冲大电流只要瞬时达到点火温度的点火桥技术不同,局部微区热板温度要在较短的时间内升高,还要稳定均匀的维持在200℃~800℃一段时间,同时得满足低能耗要求,对材料和热设计甚至是供电电路设计都是一种挑战。
3.早期的方案是用高熔点金属做电阻膜材料(如钨膜、钽膜或铂膜等),采用闭膜或悬梁臂的热设计结构,直流供电。闭膜式热板是先在硅基衬底淀积一层二氧化硅(sio2)薄膜,再淀积一层金属,然后光刻出图形主体和pad区,再在主体区盖一层氮化硅(si3n4)薄膜,pad连接外电路,这样既减小了热流失也起到了调制应力的作用,增强了结构稳定性。后来随着半导体工艺的提升,发展出了悬臂梁式热设计方案,对闭膜式方案中二氧化硅与基板接触的方式进行了改进,将电阻膜主体区域外二氧化硅刻蚀成细梁,相应区域硅基板背面刻蚀梯形槽,将薄膜主体区域悬空,这样完全切断了背部热耗散途径,进一步减少了热量流失,降低了功耗。但这种方案的一大缺陷是结构不稳定,悬梁在热应力作用下易断裂。
4.电阻膜的制作工艺和形状设计需要考虑加热过程中温度分布的均匀性。如果电阻膜排布不均匀则易引起温度不均,造成热板温度局部集中并产生热点,这将降低器件应用性能,如嗅觉探测灵敏度下降、红外收发器噪点增多等。因此,金属电阻膜的制作工艺多采用真空蒸发、磁控溅射或电子束蒸发技术。其中,真空蒸发方式要求金属熔点较低,以便于在真空室中将金属气化,常见满足此条件的金属是铝和铜,真空蒸发方式的缺点是电阻膜的厚度、晶粒大小和均匀度的控制稍差,因而不易控制加热电阻的阻值。相较而言,磁控溅射和电子束蒸发技术对金属膜生长速度、均匀度的控制要好得多,但其成本也高不少。无论采用真空蒸发、磁控溅射或电子束蒸发技术,在制作金属电阻膜时都需要掩膜板,否则就需要进行光刻和刻蚀,从成本方面考虑,上述热板制作方式受制于昂贵设备和严苛的工艺环境、高纯化学试剂及精密光刻掩膜板等,不利于成本的降低,同时,半导体工艺固有的较长制造周期也不利于由快速迭代应用所驱动的微区热板技术的探索和升级。此外,电阻膜形状设计方面需要考虑各向同性和自相似的形状排布,以降低温度梯度,使加热过程中温度分布均匀。
5.实际加热应用中,加热电阻膜的供电设计也是考虑的重点之一,与同样作为加热应用的点火桥不同(点火桥是一种瞬时高热激发器,只需要瞬时高温能够触发高能燃药即可,其脉冲电压约30v~40v,甚至在100v以上),微区加热多采用约20v直流电压供电,功耗较大,一般上百毫瓦,功耗较大的原因是采用磁控溅射生长的金属薄膜厚度一般在几十至几百纳米,电阻较大的缘故,由于这些电压与目前主流低压电路不兼容,因此原则上设计专门的供电芯片及pcb板上的外围供电电路对点火或稳定加热效果最好,但增加了设计成本
和pcb板面积,成本不易控制。
技术实现要素:6.本发明的目的是要解决目前如微区热板中所采用的较小较薄的电阻膜制作成本高、工艺复杂的问题,提供了一种电阻膜制作方法,采用的技术方案是:
7.电阻膜制作方法,包括以下步骤:采用金属箔通过冲压方式制备电阻膜,所述电阻膜为条状,线条宽度为100微米~10毫米,厚度为1微米~100微米。
8.具体的,为说明电阻膜的形状,则所述电阻膜的形状排布具有各向同性或自相似性,所述各向同性是指在二维平面内各方向分布相同,所述自相似性是指局部形状与整体形状相似。
9.进一步的,为说明金属箔的材料,则所述金属箔采用具有延展性的金属箔。
10.具体的,为详细说明冲压方式,则所述采用金属箔通过冲压方式制备电阻膜是指:将金属箔置于凸台模具与凹台模具之间,通过凸台模具与凹台模具咬合,利用切削力将金属箔切削成所需形状的电阻膜。
11.再进一步的,为提高冲压方式制备电阻膜时的成功率,则所述凸台模具中的凸台高度大于等于凹台模具中凹陷厚度,为进一步提升成功率,则所述凸台模具中的凸台高度为凹台模具中凹陷厚度的2倍至5倍。
12.具体的,为提供一种凸台模具上的凸台高度,则所述凸台模具中,其凸台高度不小于200μm。
13.再进一步的,为提高冲压方式制备电阻膜时的成功率,则所述将金属箔置于凸台模具与凹台模具之间具体为:将金属箔置于两层具有摩擦力的纸之间,再将其置于凸台模具与凹台模具之间;
14.或,在凸台模具与凹台模具咬合咬合过程中,将金属箔绷紧。
15.具体的,为说明金属箔的材料,则所述金属箔采用导电铜胶带。
16.本发明的另一目的是要解决目前微区热板制作成本高、工艺复杂的问题,提供了一种微区热板制作方法,所采用的技术方案是:
17.微区热板制作方法,包括以下步骤:采用上述方式制备电阻膜,并将电阻膜置于散热基板中心。
18.具体的,为提高所制备的微区热板的散热能力,则所述散热基板表面涂覆有一层高导热绝缘胶,且电阻膜贴附于该高导热绝缘胶上。
19.本发明的有益效果是,在本发明方案中,通过上述电阻膜制作方法,其提出以金属箔为加工原料,以冲压工艺一次成形完成电阻膜的制作,不仅工艺成本极低,形状灵活多变,且一次成形的电阻膜致密均匀,可作为较理想的发热单元。其一大优点是一次成型,而非多次冲压再组装;另一大优点是适应性好,相比传统真空蒸发、磁控溅射成膜等需要合适的基底材料,不仅需要耐一定高温,其表面还要对金属原子有一定附着力,本发明生成电阻膜的方案不需要依附于基底,一次性冲压成形的电阻膜可以置于任何基底上发挥其功能,且相较于传统的如真空蒸发及磁控溅射等采用多工序、精细加工方式制作电阻膜,本发明在不改变性能的基础上,极大的降低了环境要求和制作成本,也具有更好的温度均匀性和稳定性。所制备的电阻膜既可以用于本发明中的微区热板发热,也可用于贴片微天线信号
传导中所使用的电阻膜(不同于最新公开的冲压法制蜂窝基站天线的低频带辐射元件,其应用对象是较厚的金属片零件,且需要组装的方式装配,非常精密复杂)。
附图说明
20.图1是本发明实施例1中所采用的冲压模具的结构示意图。
21.图2是本发明实施例2中金属箔放置于凹台模具和凸台模具之间的方式。
22.图3是本发明实施例3提供的条状电阻薄膜不同的形状设计的示意图。
23.图4是本发明实施例4中提供的微区热板以及与受热体装配示意图。
具体实施方式
24.下面结合实施例及附图,详细描述本发明的技术方案。
25.本发明的电阻膜制作方法,包括以下步骤:采用金属箔通过冲压方式制备电阻膜,所制作的电阻膜为条状,线条宽度为100微米~10毫米,厚度为1微米~100微米。
26.为说明电阻膜的形状,则电阻膜的形状排布可具有各向同性或自相似性,各向同性是指在二维平面内各方向分布相同,如圆环或平面螺旋等,所述自相似性是指局部形状与整体形状相似,如hilbert形等,这些形状可使电阻膜中的金属条分布均匀,从而提升所制备电阻膜加热时的均匀性。
27.为说明金属箔的材料,则金属箔优选为采用具有延展性的金属箔。
28.为详细说明冲压方式,则采用金属箔通过冲压方式制备电阻膜可以为:将金属箔置于凸台模具与凹台模具之间,通过凸台模具与凹台模具咬合,利用切削力将金属箔切削成所需形状的电阻膜。
29.为提高冲压方式制备电阻膜时的成功率,则凸台模具中的凸台高度大于等于凹台模具中凹陷厚度,为进一步提升成功率,则凸台模具中的凸台高度为凹台模具中凹陷厚度的2倍至5倍。
30.为提供一种凸台模具上的凸台高度,则凸台模具中,其凸台高度不小于200μm。
31.为提高冲压方式制备电阻膜时的成功率,则将金属箔置于凸台模具与凹台模具之间具体优选为:将金属箔置于两层具有摩擦力的纸之间,再将其置于凸台模具与凹台模具之间;或,在凸台模具与凹台模具咬合过程中,将金属箔绷紧。这样即可使凸台模具与凹台模具咬合过程中金属箔不易因凸台模具与凹台模具的咬合而移动,从而提升制备时的成功率。电阻膜还可以采用导电铜胶带制备,即金属箔采用导电铜胶带,由于导电铜胶带一面是具有摩擦力的垫纸,则在凸台模具与凹台模具咬合过程中导电铜胶带也不易因凸台模具与凹台模具的咬合而移动,从而不需如上述金属箔一般置于两层具有摩擦力的纸之间。
32.本发明的微区热板制作方法,包括以下步骤:采用上述方式制备电阻膜,并将电阻膜置于散热基板中心。
33.为提高所制备的微区热板的散热能力,则散热基板表面可涂覆有一层高导热绝缘胶,且电阻膜贴附于该高导热绝缘胶上。
34.实施例1
35.参见图1,图1为本发明实施例1中所采用的冲压模具的结构示意图,实际操作时,可将凹台模具置于下方,将凸台模具置于上方,图形向下凸起。凹台模具上的凹陷形状为电
阻膜所需图形模具,凸台模具上的凸台为电阻膜图形,其与凹台模具上凹陷形状对应的电阻膜图形完全一致,凸台高度大于等于凹陷厚度(如考虑成功率则凸台高度可以设置成凹模板厚度的两倍到5倍,凸台高度大于等于凹陷厚度时,可提高凹台模具和凸台模具的咬合精度,进而提高制备成功率)。电阻膜图形线宽200μm,间距200μm。本例中按照冲压法制作电阻膜:将金属箔平整放置于凹台模具和凸台模具中间,然后凹台模具和凸台模具按照电阻膜图形(凸台与凹陷)完全对准进行咬合,随后凹台模具和凸台模具分开,去除成型的金属电阻膜。使用的金属箔面积应能够完整覆盖电阻膜图形(凸台与凹陷),金属箔可以是铜箔、锡箔、铝箔或金箔等。凹台模具和凸台模具上的电阻膜图形可按需要设计成其他图形,如矩形螺旋或圆形螺旋等。按照本例的冲压方法,金属电阻条宽度可以窄至100μm,厚度可以为几微米~数十微米,无需洁净工艺间,单人操作数分钟即可制作一个电阻条。
36.实施例2
37.附图2是本发明实施例2中金属箔放置于凹台模具和凸台模具之间的方式,由于金属表面的摩擦力小以及有一定延展性,直接冲压容易导致金属箔因摩擦力小而拉扯撕裂,不易使线宽很小的电阻膜完整成型,为提高冲压制作特定形状电阻膜的成功率,采用了在将金属箔包裹在两层纸中间,纸质不宜太厚,最好摩擦力大,光滑的塑料纸是起不到作用的。也可以采用压合过程中使金属箔绷紧的方法,以减小切削滑动,纸质不宜过厚的原因是纸的厚度也有几十微米,若两张加起来已经接近凸台的高度,则成型的电阻膜不能够完好地脱落,甚至没有完全切开,从而导致电阻膜制作失败。
38.本实施例2中提高金属箔冲压成功率还可以选用导电铜胶带,待冲压出电阻膜图形后,在去离子水、有机溶剂浸泡以剥离背面垫纸。
39.实施例3
40.附图3是本发明实施例3提供的条状电阻薄膜不同的形状设计的示意图,即冲压模具图形。这些图形均是自相似图形,以提高加热区温度均匀性。其中b图形可以由a图重构得到,a图短边长度相等,长边长度2倍于短边,c图形由b图重构而成,重构方法如下:
41.将a等比缩小1/2为a0,将a0向右镜像,距离是基本单元短边长度,得a1,同样地,将a1镜像并沿中心逆时针旋转90
°
,得a2,同样地,将再a2向镜像得a3,连接a0,a1,a2,a3得b。同理c可由b图按上述重构方法得到。上述重构方法可以无限进行下去,根据实际需求和模具加工精度选择合适的重构次数。
42.实施例4
43.附图4是本发明实施例4中提供的微区热板以及与受热体装配示意图。首先在散热基板上涂敷高导热绝缘胶,然后将冲压成型的金属电阻膜平整铺在其上。待胶体固化后,将受热体置于其上(接触或留有空隙)。本例的关键在于刷在基板上的导热胶的厚度要均匀适中,太厚容易散热不及时,热量局部堆积,太薄则容易使高温下的电阻膜脱落,电阻膜要平整地粘结在基板上,不能有架空,否则容易使电阻膜熔断,微区热板报废。本例中的基板形状可以为圆形、方形或多边形等,材质可以是pcb或陶瓷或聚乙烯树脂等。
44.综上所述,本发明公开了一种低成本、易于批量生产的微热板技术,并给出了实例,与传统的微热板制作方式不同的是,本发明采用冲压的方式制作电阻膜,使用高导热绝缘胶粘结的方式固定电阻膜,冲压模具制作成本低,可灵活更换各种形状的模具,制作出电阻膜形状各异的微热板,有助于微热板性能的提升,提高各类基于微热板器件性能。