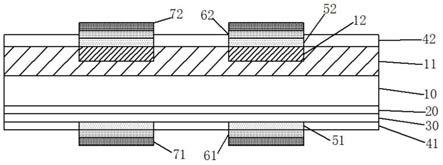
1.本发明涉及一种晶硅太阳能电池。
背景技术:2.晶硅太阳能电池是在硅衬底上通过扩散、注入等方式形成pn结,在结的两端,与电极接触。为了提高电池效率,电极处需要在降低电阻和复合两方面得以改进。在降低电阻方面,目前p型电池正面以及n型电池正、背面仍然采用以含有银粉、玻璃粉的浆料通过丝网印刷、高温烧结工艺来形成金属
‑
硅的接触。由于在微观上接触面复杂,光生载流子通过局部隧穿等方式被收集进入电极,多个界面间的散射与局部热效应,都会对载流子传输效率存在损害,表现为接触电阻高。同时,为提高晶硅电池效率,电池中发射极层的厚度不断减薄,从几百纳米发展至小于100纳米的极薄发射极层,此时形成无短路、低漏电的欧姆接触对于电池性能是最关键的。对于传统银浆,要使银颗粒之间充分融合形成良好电通道以获得低的传导电阻,烧结温度不能低,而促使银颗粒形成金属
‑
硅接触的同时,也加剧向硅基底深处的扩散,在玻璃体与硅反应的共同作用下,硅片表面被腐蚀出尺寸不一的亚微米、微米级的四面锥体结构。当这些锥体微结构接近或穿透pn结时,漏电大量产生,光伏效应被破坏。这种破坏尤其对于隧穿型电极接触结构是致命的,对于n型正面的电极接触,由于采用的是银铝浆,微观四面锥体的存在对pn结是严重危害。
3.中国专利cn112133769a中公开了一种太阳能电池,其利用金属硅化物作为电极材料与硅基底形成欧姆接触,而电流传输由接触部位之上的第二层金属层承担。该专利的思路直接来自于半导体器件浅发射极电极接触时所用的方法。但是,无论是该专利中提到的两层金属沉积后的共退火工艺,或者是相对更优的两层金属分别沉积和退火的工艺,都无法解决一个难点,即上层传导用金属(即第二金属层)对下层接触区域反应而形成的穿刺、渗透等破坏效应,引起金属电极接触区域附近半导体结的失效,包括pn结或高低结。这种反应型破坏来自第二层金属材料沉积和退火工艺。所有的金属电极薄膜在沉积或退火工艺中,局部温度可以达到数百摄氏度,当沉积或退火温度升高至300℃以上时,金属薄膜间的互扩散,甚至相变就会进行;直接与硅相接触的第一层金属层在硅片中本身只有几十纳米到一百纳米左右的厚度,第二层金属层直接沉积并后续退火处理时,第一层金属层中的硅、金属成分与第二层金属层中的金属成分都会扩散和反应,这不仅引起金属成分向硅片纵深扩散,而且也改变了不同金属层、金属层与硅之间的接触电阻。
4.另外,中国专利cn102365751b公开了一种具有金属触点的硅太阳能电池,其在局部多孔硅结构上形成的金属硅化物作为硅层接触点,金属硅化物之上直接沉积第二层金属,该专利的方案同样也会存在上层金属与下层硅化物互扩散的问题。
技术实现要素:5.为解决现有技术的缺陷,本发明的目的在于提供一种晶硅太阳能电池,包括:硅衬底,形成于硅衬底之上的介质隧穿层,形成于介质隧穿层之上的掺杂导电层,以及栅线电
极;所述栅线电极包含:形成于掺杂导电层之上的第一金属层,形成于第一层金属层之上的介质导电层,以及形成于介质导电层之上的第二金属层;所述第一层金属层与掺杂导电层在界面处形成金属硅化物或以金属
‑
硅为主要成分的多元化合物;所述介质导电层为金属氮化物、碳化物、硼化物、磷化物或金属氮氧化物。
6.优选的,所述介质导电层为tin、ga
x
n
y
、al
x
n
y
、ni
x
n
y
、co
x
n
y
、tic、ti
x
b
y
、tio
x
n
y
、gao
x
n
y
、alo
x
n
y
、nio
x
n
y
或coo
x
n
y
。
7.优选的,所述以金属
‑
硅为主要成分的多元化合物,其主要成分选自金属i
‑
硅
‑
锡
‑
氧、金属i
‑
硅
‑
锡
‑
氧
‑
氟、金属i
‑
硅
‑
锌
‑
氧、金属i
‑
硅
‑
锌
‑
氧
‑
铝、金属i
‑
硅
‑
锌
‑
氧
‑
镓、金属i
‑
硅
‑
镓
‑
氧、金属i
‑
硅
‑
镉
‑
氧、金属i
‑
硅
‑
铜
‑
铝
‑
氧中的一种或几种;所述金属i选自镁、钴、钛、镍、钨、钒、锰、钼、铪、锆中的一种或几种。
8.优选的,所述第一金属层含有镁、钴、钛、镍、钨、钒、锰、钼、铪、锆中的一种或几种;所述第二金属层含有铝、铜、钨、锡、镍、锌、铅中的一种或多种。所述第一层金属层也可与直接采用金属硅化物。
9.优选的,所述金属硅化物选自硅化镁、硅化钴、硅化钛、硅化镍、硅化钨、硅化钒、硅化锰、硅化钼、硅化铪、硅化锆中的一种或几种。
10.优选的,所述掺杂导电层为掺杂多晶硅层或多晶导电氧化物薄层;所述多晶导电氧化物薄层选自氧化锡、掺氟氧化锡、氧化锌、掺铝氧化锌、掺镓氧化锌、氧化镓、氧化镉、氧化铟、掺锡氧化铟、cualo2中的一种。
11.优选的,所述介质隧穿层选自sio2、sin
x
、al2o3、sio
x
n
y
、sic、tio2、moo3、zro2、mgo、hfo、v2o5中的一种或两种。
12.优选的,所述介质导电层的厚度小于500nm;所述掺杂导电层的厚度小于1微米;所述第一层金属层的厚度小于2微米。
13.优选的,所述掺杂导电层的掺杂极型与硅衬底同型或异型;所述介质隧穿层和掺杂导电层在硅衬底的正面和/或背面,在硅衬底同一面的介质隧穿层和掺杂导电层为整面结构或局部结构。
14.优选的,所述硅衬底为n型单晶硅,掺杂导电层为n型掺杂层;介质隧穿层和掺杂导电层在硅衬底的背面;介质隧穿层和掺杂导电层为整面结构或局部选择性图案结构;掺杂导电层外侧(远离硅衬底一侧)设有钝化介质层或透明导电层。
15.优选的,所述硅衬底为n型单晶硅;硅衬底的正面和背面都设有介质隧穿层和掺杂导电层,硅衬底正面的掺杂导电层为局部p型重掺杂层(p++),硅衬底背面的掺杂导电层为n型掺杂层,硅衬底靠近p型重掺杂层的一侧为p型轻掺杂层(p+);所述硅衬底正面的介质隧穿层和掺杂导电层为局部选择性图案结构,硅衬底背面的介质隧穿层和掺杂导电层为整面结构或局部选择性图案结构;所述硅衬底正面掺杂导电层外侧及p型轻掺杂层外侧设有钝化减反膜或透明导电层,硅衬底背面掺杂导电层外侧(远离硅衬底一侧)设有钝化介质层或透明导电层。
16.优选的,所述硅衬底为p型单晶硅,掺杂导电层为p型掺杂层;介质隧穿层和掺杂导电层在硅衬底的背面,介质隧穿层和掺杂导电层为整面结构或局部选择性图案结构,掺杂
导电层外侧(远离硅衬底一侧)设有钝化介质层或透明导电层。
17.优选的,所述硅衬底为p型单晶硅,掺杂导电层为n型重掺杂层(n++), 介质隧穿层和掺杂导电层在硅衬底的正面,介质隧穿层和掺杂导电层为整面结构或局部选择性图案结构,硅衬底靠近介质隧穿层和掺杂导电层的一侧为n型轻掺杂层(n+),掺杂导电层外侧及n型轻掺杂层外侧设有钝化介质层或透明导电层。
18.优选的,所述硅衬底为p型单晶硅,掺杂导电层为n型掺杂层;介质隧穿层和掺杂导电层在硅衬底的背面,介质隧穿层和掺杂导电层为整面结构或局部选择性图案结构,掺杂导电层外侧(远离硅衬底一侧)设有钝化介质层或透明导电层。
19.优选的,所述硅衬底为p型单晶硅,硅衬底正面和背面都设有介质隧穿层和掺杂导电层,硅衬底正面的掺杂导电层为局部n型重掺杂层(n++),硅衬底背面的掺杂导电层为p型掺杂层,硅衬底靠近n型重掺杂层的一侧为n型轻掺杂层(n+);所述硅衬底正面的介质隧穿层和掺杂导电层为局部选择性图案结构,硅衬底背面的介质隧穿层和掺杂导电层为整面结构或局部选择性图案结构,硅衬底正面掺杂导电层外侧及n型轻掺杂层外侧设有钝化介质层或透明导电层,硅衬底背面掺杂导电层外侧(远离硅衬底一侧)设有钝化介质层或透明导电层。
20.优选的,所述硅衬底为n型单晶硅;硅衬底的正面由内至外依次设有前表面n+掺杂层和减反射层;硅衬底背面设有介质隧穿层、多个n型和多个p型掺杂导电层区域,掺杂导电层与硅衬底构成异质结,且n型和相邻p型掺杂导电层区域之间通过沟槽实现电隔离。
21.优选的,所述硅衬底为n型单晶硅;硅衬底的正面由内至外依次设置有前表面n+掺杂层和减反射层;硅衬底背面设有介质隧穿层、多个n型和多个p型掺杂导电层区域,掺杂导电层与硅衬底构成异质结,且n型和相邻p型掺杂导电层区域之间通过本征多晶硅实现电隔离。
22.优选的,所述硅衬底为n型单晶硅;硅衬底背面设有多个n型和多个p型掺杂导电层区域,相邻区域之间电隔离,且掺杂导电层与硅衬底构成同质结,硅衬底背面p型掺杂导电层局部区域为p型重掺杂(p++),其余区域为p型轻掺杂区域(p+)。
23.优选的,所述硅衬底为n型单晶硅;硅衬底的正面由内至外依次设有前表面n+掺杂层和减反射层;硅衬底背面设有介质隧穿层、多个n型和多个p型掺杂导电层区域,相邻区域之间电隔离,且掺杂导电层与硅衬底构成异质结,硅衬底背面p型掺杂导电层局部区域为p型重掺杂(p++),其余区域为p型轻掺杂区域(p+)。
24.本发明的优点和有益效果在于:本发明对晶硅光伏电池的电极接触部分进行改进,一是取代成本很高的银电极材料和高温烧结工艺,在大大降低生产成本的同时,也拓宽了低成本金属应用于晶硅光伏电池的可能性;二是与薄膜结构做金属接触时,包括异质结结构的电接触时,控制了金属扩散深度,杜绝了穿刺引起的复合增加甚至是电池的失效。
25.本发明提供了一种三层结构的复合电极接触方式:第一金属层
‑
介质导电层
‑
第二金属层;其中第一金属层用于与晶硅薄膜或氧化物导电薄膜结合,第一金属层与硅衬底之间能以准二维的生长模式,在形成良好欧姆接触的同时,对金属接触区的深度进行很好的控制,这就能适应各种轻掺杂半导体结;在第一金属层之上,是介质导电层(介质导电层也可以称为阻挡层、隔离层或隔绝
层),该介质导电层同时具有较好的导电性以及阻挡金属扩散的性能;在介质导电层之上是第二金属层,第二金属层为电流传输层。介质阻挡层本身的在具有较好导电率的同时,由于其含有n、o、c等杂质原子,能有效堵塞金属互扩散的通道,特别是金属膜的晶界位错等部位,故第一金属层上的介质导电层可以有效保护已经形成的第一金属层
‑
硅接触不被第二金属层破坏,这就保证了可以适应不同的器件工艺场合。第一层金属层与掺杂导电层在界面处形成的硅化物为多元硅化物时,可以调节其退火温度、与硅的接触势垒,有利于去匹配不同的发射极接触和电池工艺。本发明的三层结构不仅可以避免传统银浆、银铝浆在电极形成的高温烧结过程中形成的穿刺问题,从而为高效电池结构的优化拓宽了空间,而且不再用昂贵的银作为电接触的载体,可有效降低晶硅电池成本。
26.本发明的电极结构,结合钝化接触的思路,把一般都在使用的重掺非晶硅层这一重掺结构范围扩大。目前结合隧穿钝化思路的电极接触都配合掺杂多晶硅层,多晶硅层与硅表面之间是一层介质隧穿层。此类结构可以有效降低金属接触界面的少子复合,增加少子寿命,提高整个光伏设备的开压和效率。其中多晶硅层负责光电流的收集,传导至电极接触处。为了提高横向传输性能,多晶硅层使用重掺。但其重掺性能提高的同时,其光透过性也会随之下降。这对含有重掺非晶硅层结构的双面电池的使用是不利的。若减薄多晶硅层会对导电性有负面影响,不可能无限减薄。因此,透明导电材料的应用具有潜在优势。尽管目前透明导电薄膜成本仍然偏高,但低成本且性能优越的透明导电薄膜一直被开发和进步中。本发明的上述多层电极结构也可以与透明导电层配合。
27.本发明结合上述复合电极结构,还给出了若干种高效晶硅电池的结构设计。
附图说明
28.图1是实施例1的示意图;图2是实施例2的示意图;图3是实施例3的示意图;图4是实施例4的示意图;图5是实施例5的示意图;图6是实施例6的示意图;图7是实施例7的示意图;图8是实施例8的示意图。
具体实施方式
29.下面结合附图和实施例,对本发明的具体实施方式作进一步描述。以下实施例仅用于更加清楚地说明本发明的技术方案,而不能以此来限制本发明的保护范围。
30.本发明提供一种晶硅太阳能电池,包括:硅衬底,形成于硅衬底之上的介质隧穿层,形成于介质隧穿层之上的掺杂导电层,以及栅线电极;所述栅线电极包含:形成于掺杂导电层之上的第一金属层,形成于第一层金属层之上的介质导电层,以及形成于介质导电层之上的第二金属层;所述第一层金属层与掺杂导电层在界面处形成金属硅化物或以金属
‑
硅为主要成分的多元化合物;
所述介质导电层为金属氮化物、碳化物、硼化物、磷化物或金属氮氧化物;具体的:所述介质导电层为tin、ga
x
n
y
、al
x
n
y
、ni
x
n
y
、co
x
n
y
、tic、ti
x
b
y
、tio
x
n
y
、gao
x
n
y
、alo
x
n
y
、nio
x
n
y
或coo
x
n
y
;所述以金属
‑
硅为主要成分的多元化合物,其主要成分选自金属i
‑
硅
‑
锡
‑
氧、金属i
‑
硅
‑
锡
‑
氧
‑
氟、金属i
‑
硅
‑
锌
‑
氧、金属i
‑
硅
‑
锌
‑
氧
‑
铝、金属i
‑
硅
‑
锌
‑
氧
‑
镓、金属i
‑
硅
‑
镓
‑
氧、金属i
‑
硅
‑
镉
‑
氧、金属i
‑
硅
‑
铜
‑
铝
‑
氧中的一种或几种;所述金属i选自镁、钴、钛、镍、钨、钒、锰、钼、铪、锆中的一种或几种;所述第一金属层含有镁、钴、钛、镍、钨、钒、锰、钼、铪、锆中的一种或几种;第一层金属层也可与直接采用金属硅化物;所述第二金属层含有铝、铜、钨、锡、镍、锌、铅中的一种或多种;所述金属硅化物选自硅化镁、硅化钴、硅化钛、硅化镍、硅化钨、硅化钒、硅化锰、硅化钼、硅化铪、硅化锆中的一种或几种;所述掺杂导电层为掺杂多晶硅层或多晶导电氧化物薄层;所述多晶导电氧化物薄层选自氧化锡、掺氟氧化锡、氧化锌、掺铝氧化锌、掺镓氧化锌、氧化镓、氧化镉、氧化铟、掺锡氧化铟、cualo2中的一种;所述介质隧穿层选自sio2、sin
x
、al2o3、sio
x
n
y
、sic、tio2、moo3、zro2、mgo、hfo、v2o5中的一种或两种;所述介质导电层的厚度小于500nm;所述掺杂导电层的厚度小于1微米;所述第一层金属层的厚度小于2微米;所述掺杂导电层的掺杂极型与硅衬底同型或异型;所述介质隧穿层和掺杂导电层在硅衬底的正面和/或背面,在硅衬底同一面的介质隧穿层和掺杂导电层为整面结构或局部结构。
31.本发明的具体实施例如下:实施例1:如图1所示,一种晶硅太阳能电池,包括n型单晶硅衬底10;硅衬底10背面一侧从硅衬底开始依次为介质隧穿层20、掺杂导电层30、钝化介电层41,其中,介质隧穿层20可以是厚度为2nm的热氧化层,掺杂导电层30可以是厚度为180nm的掺杂氧化锌透明导电层,钝化介电层41可以是厚度为80nm的氮化硅膜;背面钝化介电层41上(远离硅衬底),通过丝网印刷方式依次印刷第一金属层51、金属介质层61、第二金属层71,采用分步退火工艺;其中,第一层金属层51为硅化钛浆料,通过2次退火实现第一金属层51与掺杂导电层30在界面形成金属硅化物,第一次退火温度为260℃
‑
360℃,退火时间为3min,第二次退火温度为500℃
‑
650℃,退火时间为30s,第二次退火在印刷完金属介质层61后进行;金属介质层61为氮化钛浆料;第二金属层71为金属铝浆料,通过烧结工艺与掺杂多晶硅层接触形成完整的钝化接触,设置烧结最高温度为500℃
‑
600℃,烧结时间为20s
‑
40s;硅衬底10的正面设有掺磷掺杂层11,并且可以通过激光选择性掺杂工艺形成局部图案化n型重掺杂区域12;硅衬底之上还设有钝化介电层42,钝化介电层42可以是氮化硅层、氧化硅层、碳化硅、氮氧化硅、氧化铝、氮氧化铝、碳氮化硅中的一种或几种的组合叠层;
钝化介质层42之上为正面复合电极结构,正面电极结构包括依次印刷的正面第一金属层52、正面金属介质层62、正面第二金属层72,同样采用分步退火工艺;其中,正面第一层金属52为硅化钨浆料,第一次退火温度为260℃
‑
360℃,退火时间为3min,第二次退火温度为700℃
‑
900℃,退火时间为30s,第二次退火在印刷完正面金属介质层62后进行;正面金属介质层62为氮化钛浆料;正面第二金属层72为金属锡包铜浆料,通过退火工艺与硅层接触形成完整的钝化接触,设置退火最高温度为200℃
‑
400℃,烧结时间为20s
‑
40s。
32.实施例2:如图2所示,一种晶硅太阳能电池,包括n型单晶硅衬底10;硅衬底10背面一侧从硅衬底开始依次为介质隧穿层21、掺杂导电层31、钝化介电层41,其中,介质隧穿层21可以是厚度为1.6nm的氧化硅层,掺杂导电层31可以是厚度为200nm的掺磷多晶硅层,钝化介电层41可以是厚度为85nm的氮化硅膜;背面钝化介电层41上(远离硅衬底),通过丝网印刷方式依次印刷第一金属层51、金属介质层61、第二金属层71,通过一步退火法形成界面金属硅化物;其中,第一金属层51为硅化镍浆料,烘箱温度设置为240℃,时间为50s;金属介质层61为氮化钛浆料,烘箱温度设置为250℃,时间为30s;第二金属层71为金属铝浆料,烘箱温度设置为280℃,时间为30s;通过一步退火工艺与掺杂多晶硅层接触形成完整的钝化接触,退火温度为400℃
‑
500℃,时间为30s
‑
50s,保证第一金属层与掺杂多晶硅层形成良好的欧姆接触;硅衬底10正面一侧从硅衬底开始一次为介质隧穿层22、掺杂导电层32、钝化介电层42,正面的介质隧穿层22和掺杂导电层32为选择性局部图案结构,钝化介电层42在掺杂导电层32和正面硅衬底之上;正面一侧的硅衬底靠近介质隧穿层22为p+掺杂层11,可以是硼掺杂层,介质隧穿层22可以是厚度为1.8nm的隧穿热氧化层,掺杂导电层32可以是厚度200nm掺硼多晶硅层,钝化介电层42可以是氮化硅层、氧化硅层、碳化硅、氮氧化硅、氧化铝、氮氧化铝、碳氮化硅中的一种或几种的组合叠层;正面钝化介电层42上(远离硅衬底),对应掺杂导电层图案化区域,通过丝网印刷方式依次印刷第一金属层52、金属介质层62、第二金属层72,其中,第一层金属52为硅化镍浆料,烘箱温度设置为240℃,时间为50s;金属介质层62为氮化钛浆料,烘箱温度设置为250℃,时间为30s;第二层金属层72为金属铝浆料,烘箱温度设置为280℃,时间为30s;通过一步退火工艺与掺杂多晶硅层接触形成完整的钝化接触,退火温度为400℃
‑
500℃,时间为30s
‑
50s。
33.实施例3:如图3所示,一种晶硅太阳能电池,包括p型单晶硅衬底10;硅衬底10背面一侧从硅衬底开始依次为介质隧穿层20、掺杂导电层30、钝化介电层41,其中,介质隧穿层20可以是厚度为1.6nm的隧穿热氧化层,掺杂导电层30可以是厚度为160nm的掺锡氧化铟透明导电层,钝化介电层41可以是氮化硅层、氧化硅层、碳化硅、氮氧化硅、氧化铝、氮氧化铝、碳氮化硅中的一种或几种的组合叠层;背面钝化介电层41上(远离硅衬底),通过丝网印刷方式依次印刷第一金属层51、金属介质层61、第二金属层71,采用分步退火工艺;其中,第一金属层51为硅化钨浆料,通过2次退火实现第一金属层51与掺杂导电层30在界面形成金属硅化物,第一次退火温度为260℃
‑
360℃,退火时间为3min,第二次退火温度为700℃
‑
900℃,退火时间为30s,第二次退火在印刷完金属介质层61后进行;金属介质层61为氮化钛浆料;第二金属层71为金属锡包铜浆料,通过退火工艺与掺杂多晶硅层接触形成完整的钝化接触,设置
退火最高温度为200℃
‑
400℃,烧结时间为20s
‑
40s;硅衬底10的正面设有掺磷掺杂层11,并且可以通过激光选择性掺杂工艺形成局部图案化n型重掺杂区域12;硅衬底之上还设有钝化介电层42,钝化介电层42可以是氮化硅层、氧化硅层、碳化硅、氮氧化硅、氧化铝、氮氧化铝、碳氮化硅中的一种或几种的组合叠层;钝化介质层42之上为正面复合电极结构,正面电极结构包括依次印刷的正面第一金属层52、正面金属介质层62、正面第二金属层72,同样采用分步退火工艺;其中,正面第一层金属为硅化钨浆料,第一次退火温度为260℃
‑
360℃,退火时间为3min,第二次退火温度为700℃
‑
900℃,退火时间为30s,第二次退火在印刷完正面金属介质层62后进行;正面金属介质层62为氮化钛浆料;正面第二金属层72为金属锡包铜浆料,通过退火工艺与硅层接触形成完整的钝化接触,设置退火最高温度为200℃
‑
400℃,烧结时间为20s
‑
40s。
34.实施例4:如图4所示,一种晶硅太阳能电池,包括p型单晶硅衬底10;硅衬底10正面一侧从硅衬底开始依次为介质隧穿层21、掺杂导电层31、钝化介电层41;正面的介质隧穿层21和掺杂导电层31为选择性局部图案结构,可以使用掩膜法工艺制备,钝化介电层41在掺杂导电层31和正面硅衬底之上;其中,介质隧穿层21可以是厚度为1.6nm的隧穿热氧化层,掺杂导电层31可以是厚度为150nm掺磷多晶硅层,正面一侧的硅衬底靠近介质隧穿层21为n+型掺杂层11,钝化介电层41可以是氮化硅膜;正面钝化介电层41上(远离硅衬底),对应掺杂导电层图案化区域,通过丝网印刷方式依次印刷第一金属层51、金属介质层61,电镀第二金属层71,通过一步退火法形成界面金属硅化物;其中,第一金属层51为硅化钴浆料,烘箱温度设置为260℃,时间为50s;金属介质层61为氮化钴浆料,印刷金属介电层61后进行退火工艺,设置退火温度为700
‑
850℃,设置时间为30s
‑
50s;通过电镀方式沉积第二金属层71,第二金属层71可与是金属镍;最后通过退火工艺形成完整的钝化接触,设置退火温度为200℃
‑
300℃,时间为3min;硅衬底10背面一侧从硅衬底开始依次为介质隧穿层22、掺杂导电层32、钝化介电层42,其中,介质隧穿层22可以是厚度为1.6nm的氧化硅层,掺杂导电层32可以是厚度为200nm的掺磷多晶硅层,钝化介电层42可以是厚度为85nm的氮化硅膜;背面钝化介电层42上(远离硅衬底一面),同样通过丝网印刷方式依次印刷第一金属层52、金属介质层62,电镀第二金属层72,通过一步退火法形成界面金属硅化物;其中,第一金属层52为硅化钴浆料,烘箱温度设置为260℃,时间为50s;金属介质层62为氮化钴浆料,印刷金属介电层后进行退火工艺,设置退火温度为700
‑
850℃,设置时间为30s
‑
50s;通过电镀方式沉积第二金属层72,第二金属层72可以是金属镍;最后通过退火工艺形成完整的钝化接触,设置退火温度为200℃
‑
300℃,时间为3min。
35.实施例5:如图5所示,一种晶硅太阳能电池,包括n型单晶硅衬底3;n型单晶硅衬底3的正面由内至外依次设置有前表面n+掺杂层2和减反射层1,在n型单晶硅衬底3的背面设置有介质遂穿层4,介质遂穿层4外侧设有掺杂导电层,掺杂导电层包括多个n+掺杂导电层区5和多个p+掺杂导电层区8,掺杂导电层上设有背面钝化层,第一开膜区域设有栅线复合电极,栅线复合电极包括:形成于掺杂导电层5上的第一栅线电极,以及形成于掺杂导电层8上的第二栅线电极;第一栅线电极、第二栅线电极包括:第一金属层6,介质层9,以及第二金属层7(第
一栅线电极)、第二金属层10(第二栅线电极);实施例5的电池结构通过如下步骤制备:1)硅衬底选择n型单晶硅片,并进行一次清洗单面制绒处理,清洗时间为30min;2)使用pecvd设备在硅衬底背面沉积介质遂穿层,工艺温度为300℃
‑
400℃;(隧穿层可以使用化学氧化或热氧化生长为薄氧化物膜;隧穿层也可以使用pecvd或ald沉积形成氧化物、氮化物、碳化物、氮氧化物或碳氧化物的薄膜,例如氧化铝、氮化铝、氮氧化铝等);3)使用ald设备在介质隧穿层上沉积掺杂导电层,工艺温度为300℃
‑
400℃,厚度约为50um
‑
100um;4)用掩膜工艺使掺杂导电层形成多个n型和多个p型掺杂导电层区域;5)使用激光工艺在n型和p型掺杂导电层间形成沟槽实现电隔离,激光采用532nm或者355nm光源,激光功率10
‑
60w,扫描速度15
‑
30m/s;6)使用低压高温扩散炉对硅片进行正面磷扩散形成n型掺杂区,扩散温度控制在850℃
‑
950℃,扩散时间10min
‑
30min,结深为0.01
‑
0.1um;7)使用pecvd设备在硅衬底正背面沉积氮化硅钝化膜,膜厚为60
‑
80nm,折射率为1.8
‑
2.5;8)使用激光开槽设备对硅衬底背表面栅线区域进行开槽,沉积第一金属层;9)第一金属层上沉积介质导电层10nm;10)介质导电层上印刷第二层金属层,烧结后形成良好的欧姆接触,烧结温度为500
‑
700℃,时间长度为30秒
‑
2分钟。
36.实施例6:如图6所示,一种晶硅太阳能电池,包括n型单晶硅衬底8;硅衬底8的正面由内至外依次设置有前表面n+掺杂层2和减反射层1,在n型单晶硅衬底8的背面设置有介质遂穿层9,介质遂穿层9外侧设有掺杂导电层7,掺杂导电层7包括多个n+掺杂导电层区和多个p+掺杂导电层区,掺杂导电层7上设有背面钝化层,第一开膜区域设有栅线复合电极,栅线复合电极包括:形成于n+掺杂导电层上的第一栅线电极,以及形成于p+掺杂导电层上的第二栅线电极;第一栅线电极、第二栅线电极包括:第一金属层4,介质层5,以及第二金属层3;实施例6的电池结构通过如下步骤制备:1)硅衬底选择n型单晶硅片,并进行一次清洗单面制绒处理,清洗时间为30min;2)使用pecvd设备在硅衬底背面沉积介质遂穿层,工艺温度为300℃
‑
400℃;(隧穿层可以使用化学氧化或热氧化生长为薄氧化物膜;隧穿层也可以使用pecvd 或ald沉积形成氧化物、氮化物、碳化物、氮氧化物或碳氧化物的薄膜,例如氧化铝、氮化铝、氮氧化铝等);3)使用ald设备在介质隧穿层上沉积掺杂导电层,掺杂导电层为本征多晶硅,工艺温度为300℃
‑
400℃,厚度约为50um
‑
100um;4)用掩膜工艺使多晶硅层形成多个n型和多个p型掺杂导电层区域,区域之间的部分不掺杂,保持本征多晶硅6状态实现电隔离;5)使用低压高温扩散炉对硅片进行正面磷扩散形成n型掺杂区,扩散温度控制在850℃
‑
950℃,扩散时间10min
‑
30min结深为0.01
‑
0.1um;6)使用pecvd设备在硅衬底正背面沉积氮化硅钝化膜,膜厚为60
‑
80nm,折射率为
1.8
‑
2.5;7)使用激光开槽设备对硅衬底背表面栅线区域进行开槽,沉积第一金属层;退火温度为300
‑
400℃,时间30分钟;8)第一金属层上沉积介质导电层,厚度15nm;9)介质导电层上印刷第二金属层,烧结后形成良好的欧姆接触,烧结温度为500
‑
700℃,时间长度45秒。
37.实施例7:如图7所示,一种晶硅太阳能电池,包括n型单晶硅衬底3;硅衬底3的正面由内至外依次设置有前表面n+掺杂层2和减反射层1,在硅衬底3的背面设置掺杂导电层,并在硅衬底3直接掺杂形成同质结;掺杂导电层包括多个n型掺杂导电层区域8和多个p型掺杂导电层区域5,且n型掺杂导电层区域8和相邻p型掺杂导电层区域5之间电隔离;第一栅线电极对应n型掺杂导电层区域8;第二栅线电极对应所述p型掺杂导电层区域5;在背表面p型掺杂导电层区域5(p+掺杂层)中设置有p++重掺杂区6;第一栅线电极、第二栅线电极包括:第一金属层7,介质层4,以及第二金属层10(第二栅线电极)和第二金属层11(第一栅线电极);实施例7的电池结构通过如下步骤制备:1)硅衬底选择n型单晶硅片,并进行双面制绒处理,清洗时间约为30min;2)利用掩膜工艺在p区中心位置(电极正上方区域)离子注入硼;3)进行rca清洗,去除金属离子和表面损伤;4)使用低压高温扩散炉在硅衬底背面进行硼扩散,扩散温度控制在850℃
‑
950℃,扩散时间10min
‑
30min,结深为0.01
‑
0.2um;5)使用pecvd设备在硅衬底背面沉积氮化硅膜,膜厚为60
‑
80nm;6)使用激光开槽设备对基体背表面n型bsf区域进行开槽,激光采用532nm或者355nm光源,激光功率10
‑
60w,扫描速度15
‑
30m/s;7)使用低压高温扩散炉对硅片进行双面磷扩散,扩散温度为800
‑
1100℃,扩散时间为10
‑
50min;8)使用pecvd设备在硅衬底正面沉积氮化硅钝化膜膜,膜厚80
‑
100um;9)使用激光开槽设备对硅衬底背表面栅线区域进行开槽,沉积第一金属层;10)第一金属层上沉积介质导电层;11)介质导电层上印刷第二金属层,烧结后形成良好接触,烧结温度为600
‑
900℃,时间长度3
‑
10秒。
38.实施例8:如图8所示,一种晶硅太阳能电池,包括n型单晶硅衬底3;在n型单晶硅衬底3的正面由内至外依次设置有前表面n+掺杂层2和减反射层1,在n型单晶硅衬底3的背面设置有介质遂穿层4,介质遂穿层4表面设有掺杂导电层,并与硅衬底3构成异质结;掺杂导电层包括多个n型掺杂导电层区域8和多个p型掺杂导电层区域5,且n型掺杂导电层区域8和相邻所述p型掺杂导电层区域5之间电隔离;第一栅线电极对应所述n型掺杂多晶硅区域;第二栅线电极对应所述p型掺杂多晶硅区域;在背表面p型掺杂导电层区域5(p+掺杂层)中设置有p++重掺杂区6;第一栅线电极、第二栅线电极包括:第一金属层7,介质层9,以及第二金属层10(第二栅线电极)和第二金属层11(第一栅线电极);
实施例8的电池结构通过如下步骤制备:1)硅衬底选择n型单晶硅片,并进行一次清洗制绒处理,清洗时间为30min;2)使用pecvd设备在硅衬底背面沉积介质遂穿层,工艺温度为300℃
‑
400℃;(隧穿层可以使用化学氧化或热氧化生长为薄氧化物膜;隧穿层也可以使用pecvd 或ald沉积形成氧化物、氮化物、碳化物、氮氧化物或碳氧化物的薄膜,例如氧化铝、氮化铝、氮氧化铝等);3)使用ald设备在介质隧穿层上沉积掺杂导电层,工艺温度为300℃
‑
400℃,厚度约为50um
‑
100um;4)用掩膜工艺使掺杂导电层形成多个n型和多个p型掺杂导电层区域;5)使用激光工艺在n型和p型间形成沟槽实现电隔离,激光采用532nm或者355nm光源,激光功率10
‑
60w,扫描速度15
‑
30m/s;6)使用喷涂或者激光工艺使p+型掺杂层栅线区域形成p++重掺;7)使用低压高温扩散炉对硅片进行正面磷扩散形成n型掺杂区,扩散温度控制在850℃
‑
950℃,扩散时间10min
‑
30min结深为0.01
‑
0.1um;8)使用pecvd设备在硅衬底正背面沉积氮化硅钝化膜,膜厚为60
‑
80nm,折射率1.8
‑
2.5;9)使用激光开槽设备对硅衬底背表面栅线区域进行开槽,沉积第一金属层;10)第一金属层上沉积介质导电层;11)介质导电层上印刷第二金属层,烧结后形成良好的欧姆接触,烧结温度为600
‑
900℃,时间长度3
‑
10秒。
39.以上所述仅是本发明的优选实施方式,应当指出,对于本技术领域的普通技术人员来说,在不脱离本发明技术原理的前提下,还可以做出若干改进和润饰,这些改进和润饰也应视为本发明的保护范围。