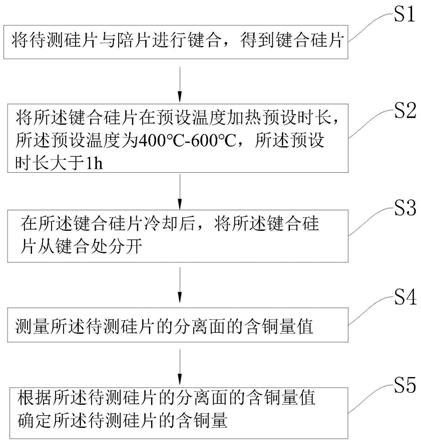
1.本发明涉及硅片测试领域,尤其是涉及一种硅片含铜量的测定方法。
背景技术:2.目前,先进集成电路的特征线宽已降低到3~7nm,并可能会继续遵循摩尔定律向更小的特征线宽发展。在这种情况下,硅片的缺陷和污染对集成电路良率带来的不利影响尤为显著,其中过渡族金属污染的危害更引起了高度重视。在先进集成电路的有源区中,微小的金属沉淀就可能导致器件失效。因此,在硅片和器件制造过程中,硅片表面的金属污染浓度都要求控制在109atoms/cm-2
以下,甚至cis(图像传感器)厂商要求控制在5*107atoms/cm-2
以下。随着薄膜淀积、图形曝光与刻蚀、离子注入等工艺的设备、化学试剂以及气源等的复杂性日益增加,金属污染的可能性有所加剧。所以,在历次发布的国际半导体技术指南(international technology roadmap for semiconductor,itrs)中,都强调有效控制金属污染对提高器件良率的重要性。
3.在硅片和器件制造过程中,金属污染会对集成电路带来恶劣的影响;主要体现在以下几个方面:1.导致集成电路器件出现漏电流(leak current),进而导致器件的失效;2.导致少数载流子寿命降低;3.金属会在带隙中形成深能级,降低p-n结的反向击穿电压,影响了器件的性能;4.金属污染会严重影响goi(gate oxide integrity,栅极氧化层的完整性),大大的降低了器件的可靠性,实验证明金属污染会严重影响goi的tzdb(time-zero dielectric breakdown,零时刻介质击穿)和tddb(time-dependent dielectric breakdown,随时间变化的介质击穿)参数。
4.铜(cu)是硅片的有害金属杂质之一。在硅片制造过程中,如果碱腐蚀、抛光、化学清洗工艺等稍有失控,就有可能带来金属cu污染。由于金属cu在硅片中具有快扩散速率及固溶度随温度急剧下降等特性,cu很容易在硅片热处理的冷却过程中形成沉淀,从而对器件的性能及可靠性带来不利影响。因此,硅片中的cu的行为一直是半导体业内关注的问题,如何准确地测量硅片体内的cu含量显得尤为重要。
技术实现要素:5.本发明旨在至少解决现有技术中存在的技术问题之一。为此,本发明在于提出一种硅片含铜量的测定方法,通过将待测硅片与陪片进行键合,然后对键合硅片进行热处理,在将待测硅片和陪片分离之后,测量待测硅片的分离面的含铜量值,可避免向待测硅片的分离面引入污染,有利于更大效率地将待测硅片内的cu扩散到待测硅片的表面,同时有利于避免移动到待测硅片的键合面上的铜重回到待测硅片体内,有利于保证测量硅片体内的cu含量的准确性。
6.根据本发明实施例的硅片含铜量的测定方法,包括以下步骤:将待测硅片与陪片进行键合;将键合后的所述待测硅片与所述陪片在预设温度热处理预设时长,所述预设温度为400℃-600℃,所述预设时长大于1h;在所述待测硅片与所述陪片冷却后,将所述待测
硅片和所述陪片从键合处分开;测量所述待测硅片的分离面的含铜量值;根据所述待测硅片的分离面的铜含量确定所述待测硅片的含铜量。
7.根据本发明实施例的硅片含铜量的测定方法,通过将待测硅片与陪片进行键合,在将待测硅片和陪片分离之后,测量待测硅片的分离面的含铜量值,一方面在热处理时,由于待测硅片和陪片键合,待测硅片与陪片的键合面被保护起来,这样可避免在热处理的环境中的cu沉积到待测硅片上;另一方面待测硅片和陪片在键合过程中产生损伤,会导致在待测硅片表面形成吸杂点,形成的吸杂区域对金属铜具有较大的束缚能,有利于更大效率地将待测硅片内的cu扩散到待测硅片的表面,同时有利于避免移动到待测硅片的键合面上的铜重回到待测硅片体内,有利于保证测量待测硅片体内的cu含量的准确性。
8.在本发明的一些实施例中,所述将待测硅片与陪片进行键合,得到键合硅片,包括:利用键合机将所述待测硅片与所述陪片对准;在利用键合机将所述待测硅片和所述陪片对准前,保证所述待测硅片和所述陪片的晶向不一致。
9.在本发明的一些实施例中,所述陪片和所述待测硅片取材于同一晶棒,在所述晶棒的长度方向上,所述陪片邻近所述待测硅片。
10.在本发明的一些实施例中,将所述键合硅片加热到预设温度的速率为0.1℃/s~50℃/s。
11.在本发明的一些实施例中,在所述键合硅片的冷却过程中,降温速率小于5℃/min。
12.在本发明的一些实施例中,所述键合硅片与所述陪片在氧气、氮气或氩气氛围下热处理。
13.在本发明的一些实施例中,在所述键合硅片冷却后,利用分片机撬动所述键合硅片以使得所述待测硅片和所述陪片在键合处分离。
14.在本发明的一些实施例中,所述测量所述待测硅片的分离面的含铜量值,包括:使用气相分解仪扫描所述待测硅片的分离面;使用等离子体质谱仪定量测试所述气相分解仪搜集的溶液。
15.在本发明的一些实施例中,根据以下公式生成所述待测硅片的分离面的含铜量值:
16.其中,n为铜原子表面密度,w为样品溶液中铜元素的浓度,v为样品溶液的体积,m为目标元素的原子量,na为阿伏伽德罗常数,s为所述待测硅片的分离面的测量面积。
17.在本发明的一些实施例中,根据以下公式生成所述待测硅片内的含铜量:
18.n
bulkcu
=n/(t/2),其中,t为所述待测硅片的厚度。
19.本发明的附加方面和优点将在下面的描述中部分给出,部分将从下面的描述中变得明显,或通过本发明的实践了解到。
附图说明
20.图1是根据本发明一个实施例的硅片含铜量的测定方法的流程示意图;
21.图2是根据本发明一个实施例的键合硅片的侧视示意图;
22.图3是根据本发明一个实施例的键合硅片的俯视示意图;
23.图4是根据本发明一个实施例的键片机的结构示意图;
24.图5是根据本发明一个实施例的硅片键合的流程示意图(第一步到第四步);
25.图6是根据本发明一个实施例的硅片键合的流程示意图(第五步到第八步);
26.图7是根据本发明一个实施例的硅片键合的流程示意图(第九步到第十一步);
27.图8是根据本发明一个实施例的热处理温度曲线的示意图;
28.图9是根据本发明一个实施例的气相分解仪的扫描流程示意图;
29.图10是在热处理过程中铜在硅片中的主要行为的示意图。
30.附图标记:
31.待测硅片10;第一氧化层11;第一旋转口12;
32.陪片20;第二氧化层21;第二旋转口22;
33.分离面30;
34.键合硅片40;
35.键合机50;上卡盘51;顶针52;下卡盘53。
具体实施方式
36.下面详细描述本发明的实施例,所述实施例的示例在附图中示出,其中自始至终相同或类似的标号表示相同或类似的元件或具有相同或类似功能的元件。下面通过参考附图描述的实施例是示例性的,旨在用于解释本发明,而不能理解为对本发明的限制。
37.下文的公开提供了许多不同的实施例或例子用来实现本发明的不同结构。为了简化本发明的公开,下文中对特定例子的部件和设置进行描述。当然,它们仅仅为示例,并且目的不在于限制本发明。此外,本发明可以在不同例子中重复参考数字和/或字母。这种重复是为了简化和清楚的目的,其本身不指示所讨论各种实施例和/或设置之间的关系。此外,本发明提供了的各种特定的工艺和材料的例子,但是本领域普通技术人员可以意识到其他工艺的可应用于性和/或其他材料的使用。
38.下面参考附图1-10描述根据本发明实施例的硅片含铜量的测定方法。
39.参照图1所示,根据本发明实施例的硅片含铜量的测定方法,可以包括以下步骤:
40.如图1所示,s1:将待测硅片10与陪片20进行键合。例如,可以通过键片机将待测硅片10和陪片20键合。在键合的过程中,参照图2所示,待测硅片10和陪片20朝向彼此的表面产生损伤,换言之,待测硅片10和陪片20的键合面(参照图2所示的分离面30)会产生损伤。在键合之后,从微观上看,待测硅片10和陪片20的键合处呈交错嵌入的形态。
41.可以理解的是,在待测硅片10和陪片20键合后,一方面可以使得待测硅片10与陪片20的键合面被保护起来,在后续的处理中有利于避免向待测硅片10的键合面引入污染;另一方面,由于待测硅片10与陪片20在键合过程中产生损伤,会增大待测硅片10的键合面处的吸杂点,可增大待测硅片10的表面对铜的束缚能,使得在后续热处理过程中、有利于更大效率地将待测硅片10内的cu扩散到待测硅片10的表面,同时进入键合面处的铜不易被释放,有利于避免移动到待测硅片10的键合面上的铜重回到待测硅片10体内,有利于提高铜含量检测的可靠性。
42.参照图1和图8所示,s2:将键合硅片40在预设温度热处理预设时长,预设温度为400℃-600℃,换言之,预设温度可以取400℃-600℃中的任一值,例如,预设温度可以为410℃、420℃、430℃、440℃、450℃、460℃、470℃、480℃、490℃、500℃、510℃、520℃、530℃、540℃、550℃、560℃、570℃、580℃、590℃等;预设时长大于1h,换言之,预设时长可以取大于1h的任意值,例如,预设时常可以为1.1h、1.2h、1.3h、1.4h、1.5h、1.6h等。可选地,可使用炉管对键合硅片40进行热处理。
43.可以理解的是,根据间隙铜的扩散公式;l2=d*t(l代表扩散长度,d代表扩散系数,t代表扩散时间),其中d与温度强相关,一般温度越高,扩散系数越大,反之亦然,但随着热处理温度变高时,可能会发生铜沉淀,为了研究热处理温度对于铜沉淀的影响,需要进一步研究铜沉淀的行为。
44.具体地,发明人在实际研究中发现,800℃是形成大量cu沉淀的临界温度;当热处理温度在800℃以下时,体内cu沉淀量极少,且随着温度升高,逐渐增加,更多的cui原子外扩散到硅片表面,在较低的温度下,cu扩散系数较小,但cu扩散系数还会受到掺杂类型,掺杂浓度的影响,实际的有效扩散系数可能更小,故在较低的温度下,尤其是对n型硅片来说,很难外扩散到表面,经研究发现在400℃以上时,n型硅片中的cui才进行外扩散运动,主要是cui会与掺杂剂磷形成复合体,故cu在n型硅片中稳定性较高,因此,通过使得热处理温度在400~600℃范围内可以适应所有类型硅片,且可以保证在不形成cu沉淀的情况下有效的进行外扩散,从而可保证待测硅片10体内的铜移动到硅片表面,换言之,可以避免在热处理时移动到待测硅片10表面的铜的减少,有利于进一步提高铜含量检测的准确性。
45.如图1所示,s3:在待测硅片10与陪片20冷却后,将键合硅片40从键合处分开;需要说明的是,由于热处理的温度在400℃-600℃之间,温度依然处于一个较低的范围,不会导致待测硅片10和陪片20融合在一起,在分离时,可施加撬转力将待测硅片10和陪片20撬开,从而避免待测硅片10和陪片20之间发生粘连,有利于进一步提高含铜量测量的准确性。
46.如图1所示,s4:测量待测硅片10的分离面30(参照图2)的含铜量值,其中,待测硅片10的分离面30也即为待测硅片10的键合面;例如,测量待测硅片10的分离面30的含铜量值,可以包括:使用气相分解仪扫描待测硅片10的分离面30;使用等离子体质谱仪定量测试气相分解仪搜集的溶液。具体地,气相分解仪原理示意图如图9所示,利用氢氟酸蒸气去除待测硅片10表面的自然氧化层,同时可使得待测硅片10表面呈疏水性,然后通过扫描液扫描待测硅片10的分离面,搜集待测硅片10的分离面上的金属铜;
47.进一步地,可根据以下公式生成待测硅片10的分离面30的含铜量值:
48.其中,n为铜原子表面密度,w为样品溶液中铜元素的浓度,v为样品溶液的体积,m为目标元素的原子量,na为阿伏伽德罗常数,s为待测硅片10的分离面的测量面积。由此,有利于准确获得待测硅片10的分离面30的含铜量值,且操作方便。
49.如图1所示,s5:根据待测硅片10的分离面30的铜含量确定待测硅片10的含铜量。具体地,根据以下公式生成待测硅片10内的含铜量:n
bulkcu
=n/(t/2),其中,t为待测硅片的厚度。可以理解的是,在热处理的过程中,待测硅片10体内的铜分别均匀的向待测硅片10的分离面30和背面,通过n
bulkcu
=n/(t/2)确定待测硅片10的含铜量,有利于较为准确地计算
出待测硅片10的含铜量。
50.需要说明的是,发明人在实际研究中发现,在晶体硅中,cu主要以间隙态铜存在硅片中,但是在经过高温热处理制程后,会以图10中的3种形态共同存在;《a》cu与点缺陷形成cu相关复合体;《b》间隙铜通过同质形核或者在缺陷上异质形核的方式,在硅片内形成cu沉淀;《c》间隙铜外扩散到硅片表面。
51.因而发明人总结,除了温度因素,间隙铜cui外扩散还受以下4个原因影响:1.cu能与表面氧化硅发生反应;2.cui阳离子会在硅片表面发生还原反应(抛光面具有疏水性和还原性);3.cu倾向于移动到硅片表面的缺陷处(应力、损伤层、悬挂键)(外部吸杂);4、cu在硅中的扩散速度快,在氧化硅中的扩散速度很慢。以上都表明cu有外扩散的驱动力,并且外扩散的cu一般存在于表面自然氧化层或硅与氧化硅的界面。
52.而相关技术中,采用低温扩散法来检测硅片内的铜含量,具体而言,通过低温(100~300℃)使得间隙铜外扩散到硅片表面,再通过气相分解仪-等离子体质谱仪(vpd-icpms)搜集待测硅片10表面的cu含量进而计算硅片体内cu含量。根据以上分析,低温扩散法具有以下缺陷:1、为保证硅片体内的cu扩散到硅片表面,故低温热处理需要足够的时间,在此过程中,环境中的cu会沉积在硅片表面,引入新的污染,导致测试cu结果不准确;2、低温扩散法一般通过室温降温,降温速度较快,间隙铜易形成cu沉淀,形成的cu沉淀无法扩散到硅片表面处,故测试结果不准确。
53.有鉴于此,根据本发明实施例的硅片含铜量的测定方法,通过将待测硅片10与陪片20进行键合,在将待测硅片10和陪片20分离之后,测量待测硅片10的分离面30的含铜量值,一方面在热处理时,由于待测硅片10和陪片20键合,待测硅片10与陪片20的键合面被保护起来,这样可避免在热处理的环境中的cu沉积到待测硅片10上;另一方面待测硅片10和陪片20在键合过程中产生损伤,会导致在待测硅片10表面形成吸杂点,形成的吸杂区域对金属铜具有较大的束缚能,有利于更大效率地将待测硅片10内的cu扩散到待测硅片10的表面,同时有利于避免移动到待测硅片10的键合面上的铜重回到待测硅片10体内,有利于保证测量待测硅片10体内的cu含量的准确性。
54.在一个示例中,在将待测硅片10与陪片20进行键合前,陪片20、待测硅片10均需要使用清洗机清洗,清洗流程如下:标准清洗溶液1(sc1:nh4oh+h2o2)-》超纯水(upw)-》稀释的氢氟酸-》超纯水(upw)-》标准清洗溶液2(sc2:hcl+h2o2)-》超纯水(upw)
–
》干燥-》臭氧成膜(形成较均匀的氧化膜),可以理解的是,在长期放置的过程中,硅会与氧气反应形成氧化膜,原本的氧化层会对后续的反应过程造成影响,因此在键合前需要对待测硅片10与陪片20进行清洗,有利于消除原来的氧化膜的不良影响,提高对待测硅片10铜含量测量的准确性。
55.在本发明的一些实施例中,参照图2和图3所示,将待测硅片10与陪片20进行键合,得到键合硅片40,包括:利用键合机50将待测硅片10与陪片20对准;在利用键合机50将待测硅片10和陪片20对准前,保证待测硅片10和陪片20的晶向不一致。可以理解的是,通过使得陪片20与待测硅片10晶向不一致,可增加待测硅片10的键合面上的吸杂点,增大待测硅片10的键合面对金属铜的束缚能,有利于进一步避免移动到待测硅片10的键合面上的铜重回到待测硅片10体内,有利于保证测量硅片体内的cu含量的准确性。
56.在本发明的一些实施例中,参照图2和图3所示,陪片20和待测硅片10取材于同一
晶棒,在晶棒的长度方向上,陪片20邻近待测硅片10。例如,在对晶棒进行切片时,陪片20可以为待测硅片10的上一片硅片或下一片硅片。由此,可以保证陪片20和待测硅片10的体内的铜含量基本一致,避免陪片20和待测硅片10的铜含量相差较大,有利于避免陪片20和待测硅片10上的铜相互扩散,保证对待测硅片10铜含量测量的准确性。当然,本发明不限于此,陪片20和待测硅片10也可以取材于不同晶棒,只要保证陪片20和待测硅片10的铜含量基本一致即可。
57.例如,在一些示例中,参照图3所示,待测硅片10具有第一旋转口12,陪片20具有第二旋转口22,在利用键合机50将待测硅片10和陪片20对准前,保证第一旋转口12和第二旋转口22错位以使得待测硅片10和陪片20的晶向不一致。由此,便于工人操作,且有利于保证待测硅片10和陪片20的晶向不一致。
58.可选地,参照图3所示,第一旋转口12和第二旋转口22之间的夹角α可以为45
°
、90
°
、135
°
或180
°
等,例如,如图3所示,第一旋转口12和第二旋转口22之间的夹角α为45
°
。由此,可进一步增大待测硅片10和陪片20之间的晶向的差异,从而可增大待测硅片10的吸杂能力,有利于避免移动到待测硅片10的键合面的铜重新回到硅片体内,提高对待测硅片10含铜量检测的准确性。
59.具体而言,在一个示例中,如图4所示,键片机包括上卡盘51和下卡盘53,上卡盘51设有顶针52,顶针52穿设于上卡盘51且相对上卡盘51可移动,具体地,将待测硅片10与陪片20进行键合可以包括如下步骤:参照图5,第一步s101,将陪片20通过真空吸力装载到上卡盘51;第二步s102,装载待测硅片10,使得待测硅片10的第一旋转口12与陪片20的第二旋转口22之间的夹角为45
°
;第三步s103,预对准;第四步s104,对准;
60.参照图6,第五步s105,下卡盘53抽真空;第六步s106,接着设置顶针52的压力,使得陪片20的中部向下形变,从而有利于保证待测硅片10和陪片20对准,有利于防止待测硅片10相对陪片20错位;第七步s107,撤去内侧上卡盘51的真空;第八步s108:撤去外侧上卡盘51的真空;
61.参照图7,第九步s109,撤去顶针52压力;第十步s110,撤去下卡盘53真空;第十一步s110,卸载键合硅片40。例如,结合图2所示,待测硅片10的表面具有第一氧化层11,陪片20的表面具有第二氧化层21,第一氧化层11和第二氧化层21通过键片机键合。
62.可以理解的是,通过利用键片机将待测硅片10与陪片20进行键合,一方面硅片的正面就可以被保护起来,在后续的处理中避免了引入污染;另一方面待测硅片10表面的第一氧化层11、陪片20与待测硅片10的晶向不一致、键合过程中产生的损伤,均会导致在待测硅片10表面形成吸杂点,形成的吸杂区域对金属铜具有较大的束缚能,使得这些金属铜不被再次释放,由此,有利于进一步保证对待测硅片10的含铜量测量的准确性。
63.在本发明的一些实施例中,参照图8所示,将键合硅片40加热到预设温度的速率为0.1℃/s~50℃/s。换言之,将键合硅片40加热到预设温度的速率可以取0.1℃/s~50℃/s中的任一值。例如,将键合硅片40加热到预设温度的速率可以取值为0.1℃/s、1℃/s、5℃/s、10℃/s、15℃/s、20℃/s、25℃/s、30℃/s、35℃/s、40℃/s、45℃/s、50℃/s等。可以理解的是,通过使得将键合硅片40加热到预设温度的速率为0.1℃/s~50℃/s,可将温升的速率控制在一个较低的值,有利于保证热处理工序的安全性。
64.在本发明的一些实施例中,参照图8所示,在键合硅片40的冷却过程中,降温速率
小于5℃/min。例如,降温速率可以为0.1℃/min、1℃/min、2℃/min、3℃/min、4℃/min、5℃/min。可以理解的是,cu在硅中具有快扩散速率以及固溶度随着热处理温度的下降急剧降低等特性,故一般铜沉淀是由过饱和度引起的化学驱动力(μ)与铜沉淀的形核势垒的比较决定的,参照以下公式:
65.μ=kbt
×
ln[c/c0(t)]
[0066]
式中c和c0(t)分别表示溶解在硅中的cui的浓度和在温度t时cu的平衡浓度,kb是波尔兹曼常数。如果化学驱动力(μ)超过了沉淀形核势垒,cu沉淀就会发生;反之就不能形成cu沉淀。
[0067]
因此,降温速率会对cu沉淀驱动力产生影响;1)若降温速率较低时,c0(t)下降得较缓慢,导致化学驱动力(μ)无法跨越cu沉淀的形核势垒,cu沉淀不会发生;2)若降温速率较快时,c0(t)下降得较快,导致化学驱动力(μ)大于cu沉淀的形核势垒,会发生cu沉淀,根据本发明实施例的硅片含铜量的测定方法,通过保证降温速率<5℃/min,有利于最大程度的减少因降温产生的cu沉淀,保证铜含量测量的准确性。
[0068]
在本发明的一些实施例中,键合硅片40在氧气、氮气或氩气氛围下热处理。可以理解的是,在相对低的温度热处理时(400~600℃),通过使得键合硅片40在氧气、氮气或氩气氛围下热处理,有利于保证热处理工序的可靠性,保证间隙铜cui在待测硅片40体内的可靠扩散。
[0069]
在本发明的一些实施例中,参照图2所示,在键合硅片40冷却后,利用分片机撬动键合硅片40以使得待测硅片10和陪片20在键合处分离。例如,分片机包括分片件,分片件可以撬动待测硅片10和陪片20键合处的边缘(参照图2中的a处)以撬动陪片20,从而使得待测硅片10和陪片20在键合处可靠分离。
[0070]
可以理解是,由于键合硅片40在相对低的温度热处理(400~600℃),待测硅片10和陪片20的氧化层(第一氧化层11和第二氧化层21)不会发生融化,同时,通过利用分片机撬动键合硅片40以使得待测硅片10和陪片20在键合处分离,可以避免待测硅片10粘连陪片20上的结构,有利于进一步保证对待测硅片10铜含量测量的准确性。
[0071]
根据本发明实施例的硅片含铜量的测定方法的其他构成以及操作对于本领域普通技术人员而言都是已知的,这里不再详细描述。
[0072]
在本发明的描述中,需要理解的是,术语“中心”、“纵向”、“横向”、“长度”、“宽度”、“厚度”、“上”、“下”、“前”、“后”、“左”、“右”、“竖直”、“水平”、“项”、“底”、“内”、“外”、“顺时针”、“逆时针”、“轴向”、“径向”、“周向”等指示的方位或位置关系为基于附图所示的方位或位置关系,仅是为了便于描述本发明和简化描述,而不是指示或暗示所指的装置或元件必须具有特定的方位、以特定的方位构造和操作,因此不能理解为对本发明的限制。
[0073]
此外,术语“第一”、“第二”仅用于描述目的,而不能理解为指示或暗示相对重要性或者隐含指明所指示的技术特征的数量。由此,限定有“第一”、“第二”的特征可以明示或者隐含地包括一个或者更多个该特征。在本发明的描述中,“多个”的含义是两个或两个以上,除非另有明确具体的限定。
[0074]
在本发明中,除非另有明确的规定和限定,术语“安装”、“相连”、“连接”、“固定”等术语应做广义理解,例如,可以是固定连接,也可以是可拆卸连接,或成一体;可以是机械连接,也可以是电连接,还可以是通信;可以是直接相连,也可以通过中间媒介间接相连,可以
是两个元件内部的连通或两个元件的相互作用关系。对于本领域的普通技术人员而言,可以根据具体情况理解上述术语在本发明中的具体含义。
[0075]
在本发明中,除非另有明确的规定和限定,第一特征在第二特征“上”或“下”可以是第一和第二特征直接接触,或第一和第二特征通过中间媒介间接接触。而且,第一特征在第二特征“之上”、“上方”和“上面”可是第一特征在第二特征正上方或斜上方,或仅仅表示第一特征水平高度高于第二特征。第一特征在第二特征“之下”、“下方”和“下面”可以是第一特征在第二特征正下方或斜下方,或仅仅表示第一特征水平高度小于第二特征。
[0076]
在本说明书的描述中,参考术语“一个实施例”、“一些实施例”、“示例”、“具体示例”、或“一些示例”等的描述意指结合该实施例或示例描述的具体特征、结构、材料或者特点包含于本发明的至少一个实施例或示例中。在本说明书中,对上述术语的示意性表述不必须针对的是相同的实施例或示例。而且,描述的具体特征、结构、材料或者特点可以在任一个或多个实施例或示例中以合适的方式结合。此外,在不相互矛盾的情况下,本领域的技术人员可以将本说明书中描述的不同实施例或示例以及不同实施例或示例的特征进行结合和组合。
[0077]
尽管已经示出和描述了本发明的实施例,本领域的普通技术人员可以理解:在不脱离本发明的原理和宗旨的情况下可以对这些实施例进行多种变化、修改、替换和变型,本发明的范围由权利要求及其等同物限定。