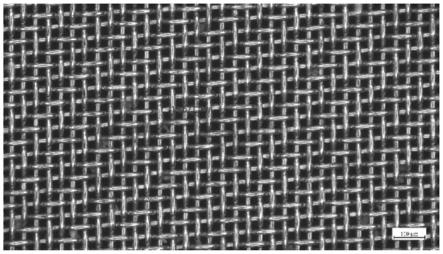
1.本发明属于燃料电池技术领域,具体涉及一种用于燃料电池的金属支撑板的制备方法。
背景技术:2.固体氧化物燃料电池是一种理想的燃料电池,不但具有燃料电池高效、环境友好的优点,而且还具有以下突出优点:(1)固体氧化物燃料电池是全固体结构,不存在使用液体电解质带来的腐蚀问题和电解质流失问题,可望实现长寿命运行。(2)固体氧化物燃料电池的工作温度为800~1000℃,不但电催化剂不需要采用贵金属,而且还可以直接采用天然气、煤气和碳氢化合物作为燃料,简化了燃料电池系统。(3)固体氧化物燃料电池排出高温余热可以与燃气轮机或蒸汽轮机组成联合循环,大幅度提高总发电效率。
3.目前的金属支撑型固体氧化物燃料电池如本技术人在先申请的中国发明专利申请《一种用于燃料电池的金属支撑板的制备方法》,其专利申请号为cn202110298584.5(申请公布号为cn113161566a)公开了一种用于燃料电池的金属支撑板的制备方法,依次包括有以下步骤:1)采用不锈钢、耐热钢、镍基合金、钴基合金、钛合金、铬基合金中的一种;2)将步骤1)中材料制成金属基板;3)在金属基板上加工直径0.005~0.5mm的微孔的孔隙,孔隙的面积占板材总面积的3~70%;4)将包含有孔隙的板材切割成所需要的尺寸;5)将阳极浆料涂覆在金属基板的上表面上,以在金属基板的上表面形成阳极层;6)将电解质浆料涂覆在阳极层的上表面上以在阳极层表面形成电解质涂层;7)将阴极浆料涂覆在电解质涂层的上表面上,以在电解质涂层的上表面形成阴极层,从而制成金属支撑板。由上述金属基板制成的金属支撑板容易变形,孔隙大小不均匀,气体流量不稳定等缺陷。
4.因此,需要对现有的用于燃料电池的金属支撑板的制备方法作进一步的改进。
技术实现要素:5.本发明所要解决的技术问题是针对上述现有技术的现状,提供一种用于燃料电池的金属支撑板的制备方法,使所制备的金属支撑板不易变形且抗拉强度高。
6.本发明解决上述技术问题所采用的技术方案为:一种用于燃料电池的金属支撑板的制备方法,其特征在于,依次包括有以下步骤:
7.1)采用目数为40~2000目的金属丝网,所述金属丝网的材质为不锈钢和/或高温合金;
8.2)根据目标金属支撑板的厚度,将步骤1)中的金属丝网进行折叠或叠放得到多层丝网,折叠或叠放的层数为2~100层;
9.3)将步骤2)中的丝网层进行轧制或者压制,然后进行烧结;
10.4)将烧结后的多层丝网进行裁剪得到金属基板;
11.5)阳极浆料涂覆在剪裁金属基板的上表面上,随后将金属基板未涂覆的下表面搁置在承烧板上,并进行干燥,从而在金属基板的上表面形成阳极层;
12.6)将电解质浆料涂覆在阳极层的上表面上,随后将金属基板未涂覆的下表面搁置在承烧板上,并进行干燥,从而在阳极层的上表面形成电解质涂层;
13.7)将阴极浆料涂覆在电解质涂层的上表面上,随后将金属基板未涂覆的下表面搁置在承烧板上,并进行干燥,从而在电解质涂层的上表面形成阴极层,从而制成金属支撑板。
14.优选地,步骤3)中的烧结温度为1000℃~1350℃,烧结保温时间为5~500min。烧结后金属支撑板具有较高的强度,同时阳极与金属支撑板之间结合紧密。阳极、电解质和阴极进行共烧结,可以提升生产效率,降低生产成本,改善金属支撑板-阳极-电解质-阴极的三个界面结合状态。
15.压制的方式有多种,但是优选地,步骤3)中的压制采用:将多层丝网下方放置支撑板,将多层丝网的上方放置陶瓷压板,陶瓷压板的上方再放置重物,支撑板为陶瓷支撑板或石墨支撑板,重物为耐热钢或者钨合金。采用耐热钢或钨合金等进行压制,可以保证网板烧结后每层网之间的结合力强并且这些材料可以重复使用,降低烧结成本。
16.进一步优选地,烧结时,将多层丝网、支撑板、陶瓷压板以及重物一起放入烧结炉中进行烧结。
17.优选地,所述金属丝网为奥氏体,或者铁素体不锈钢,或者耐热型不锈钢;所述高温合金为gh3030,或者gh4037。
18.优选地,折叠后的多层丝网中每层的目数相同。
19.具体地,在步骤5)、步骤6)和步骤7)中在干燥后均进行烧结,步骤5)中的烧结和步骤6)中的烧结所采用的烧结温度均为1050℃~1400℃,烧结时间均为10~300min,步骤7)中的烧结所采用的烧结温度为800℃~1200℃,烧结时间为5~300min,真空度为10-3
pa~102pa。
20.为了提升多层丝网的强度和透气性,叠放后的多层丝网中,各层的目数不相同,至少两层中的金属丝网的材质不同。
21.优选地,所述不锈钢的组分按照质量百分比计,包括以下组分:c:0.01~0.08%,cr:15~25%,al:0~6.0%,si:0.2~1.2%,ni:0~11%,mn:0.4~0.8%,mo:0~3%,铁:余量;所述高温合金按照质量百分比计,包括以下组分:c:0.06~0.09%,cr:15~21%,mo:0~3%,w:0~6%,al:0.1~2.2%,ti:0.1~2.5%,fe:1~5%,不可避免的杂质:小于2%,镍:余量。含有铬等元素可以保证金属支撑板在高温下具有良好的耐蚀性能和力学性能,同时保证热膨胀系数与电解质、阴极、阳极匹配。
22.优选地,所述阳极浆料包含有nio、丁酮、乙醇、三乙醇胺、淀粉、聚乙烯醇缩丁醛pvb、聚乙二醇peg及谷氨酸pht,还包括有氧化钇稳定氧化锆和sr
2-x
ca
x
fe
1.5
mo
0.5o6-δ
中的一种,其中,x=0,0.1,0.3,0.5。利于产生电池反应。
23.优选地,所述电解质浆料包括有丁酮、乙醇、三乙醇胺、聚乙烯醇缩丁醛pvb、聚乙二醇peg、谷氨酸pht,还包括有氧化钇稳定氧化锆、lagao3基电解质、ba(sr)ce(ln)o3和ceo2基固体电解质中的一种。这种电解质浆料的热膨胀系数与阳极和阴极的接近,烧结后结合较好。
24.优选地,所述阴极浆料为sr
2-x
ca
x
fe
1.5
mo
0.5o6-δ
、lsm(la
1-x
sr
x
mn03)、lscf((la,sr)(co,fe)o3)、焦绿石结构的a2ru2o
7-x
(a=pb,bi)陶瓷、ag-ydb复合陶瓷和钙钛矿结构的l型
陶瓷中的一种,前述x=0,0.1,0.3,0.5。这种阴极材料与电解质层结合紧密。
25.与现有技术相比,本发明的优点在于:该用于燃料电池的金属支撑板采用金属丝网折叠或叠放的多层丝网作为金属支撑板,其表面平整,保证阳极层均匀地覆盖在网状金属支撑板上,从而保证电解质层和阴极层也同样均匀分布,使得最终制备出的金属支撑板的抗拉强度高、变形小且易保持板材的特性。与使用金属板材的支撑板相比,密度较低,质量较轻,利于实现轻量化。此外,无需粘结剂以及涂覆处理,而金属板材制备的支撑板,需要进行多次涂层处理,成本高昂。另外,上述制备方法工艺简单,无需模具即可实现金属支撑板的大批量生产,降低生产成本,提高了生产效率。
附图说明
26.图1为金属支撑板燃料电池结构剖视图;
27.图2为实施例1中步骤1)的丝网的孔隙形貌;
28.图3为实施例1中剪切后轧制表面的形貌;
29.图4实施例1中剪切后剖切截面的形貌;
30.图5为实施例2中剪切后轧制表面的形貌;
31.图6实施例2中剪切后剖切截面的形貌;
具体实施方式
32.以下结合附图实施例对本发明作进一步详细描述。
33.实施例1:
34.如图2至图4所示,为本发明的第1个优选实施例。
35.本实施例的用于燃料电池的金属支撑板的制备方法依次包括以下步骤:
36.1)采用目数为700目的金属丝网,具体参见图2所示,金属丝网的材质为304l奥氏体不锈钢;按照质量百分比计,该不锈钢包括以下组分:c:0.015%,cr:19.2%,mn:0.6%,si:0.8%,ni:10.3%,铁:余量;
37.2)将步骤1)中的金属丝网进行折叠得到多层丝网,折叠的层数为10层;
38.3)将步骤2)中的丝网层进行轧制,然后放入真空烧结炉中,在真空度为0.1pa,烧结温度为1300℃,烧结时间为60min下进行烧结,烧结冷却后取出多层丝网;
39.4)将烧结后的多层丝网进行裁剪成110mm
×
110mm
×
0.18mm的金属基板;
40.5)阳极浆料涂覆在剪裁金属基板的上表面上,随后将金属基板4未涂覆的下表面搁置在承烧板上,并进行干燥,从而在金属基板4的上表面形成阳极层2;前述的阳极浆料包括有sr
2-x
ca
x
fe
1.5
mo
0.5o6-δ
(x=0)、nio、丁酮、乙醇、三乙醇胺、淀粉、聚乙烯醇缩丁醛pvb、聚乙二醇peg及谷氨酸pht。
41.6)将电解质浆料涂覆在阳极层2的上表面上,随后将金属基板4未涂覆的下表面搁置在承烧板上,并进行干燥,从而在阳极层2的上表面形成电解质涂层3;前述的电解质浆料包括有氧化钇稳定氧化锆电解质、丁酮、乙醇、三乙醇胺、聚乙烯醇缩丁醛pvb、聚乙二醇peg和谷氨酸pht。
42.7)将sr
2-x
ca
x
fe
1.5
mo
0.5o6-δ
(x=0)阴极浆料涂覆在电解质涂层的上表面上,随后将金属基板4未涂覆的下表面搁置在承烧板上,并进行干燥,从而在电解质涂层的上表面形成
阴极层1,从而制成金属支撑板。
43.步骤4)剪裁后在轧制表面的形貌见图3所示,剖切的形貌见图4所示。由此,可以看出,金属基板4有一定数量的孔隙,孔隙均匀,气体流量稳定。金属丝纵横分布,保证良好的强度。
44.本实施例的烧结后金属支撑板的抗拉强度150mpa,支撑板的平面度0.2mm,而使用与本实施例同样材料的金属粉末制备出的金属支撑板的抗压强度不超过50mpa,平面度在0.5mm以上。因此,采用上述多层金属丝网制备金属支撑板的抗拉强度更高。
45.实施例2:
46.本实施例与上述实施例1的区别仅在于:
47.步骤1)中所选用的金属丝网的材质不同,具体地,选用430l铁素体不锈钢丝网,丝网的目数为700目;按照质量百分比计,该不锈钢丝网包括以下组分:包括以下组分:c:0.010%,cr:17.4%,mn:0.8%,si:0.5%,铁:余量;
48.步骤2)中金属丝网采用叠放的方式,将金属丝网叠放10层,放置到刚玉板上,再将相同尺寸的刚玉板盖住叠放的丝网,刚玉板(陶瓷板)上未放置重物;
49.步骤3)将上述陶瓷板和金属丝网一起放入到推舟式烧结炉中,在露点低于-40℃的高纯氢气中,并在烧结温度为1320℃,烧结时间为40min进行烧结,烧结冷却后取出多层丝网;
50.步骤4)剪裁:将步骤3)的多层丝网采用切刀剪裁为110mm
×
110mm
×
0.45mm的金属基板;
51.前述的阳极浆料包括有氧化钇稳定氧化锆ysz、nio、丁酮、乙醇、三乙醇胺、淀粉、聚乙烯醇缩丁醛pvb、聚乙二醇peg及谷氨酸pht。前述的电解质浆料包括有氧化钇稳定氧化锆电解质、丁酮、乙醇、三乙醇胺、聚乙烯醇缩丁醛pvb、聚乙二醇peg和谷氨酸pht。阴极材料为sr
2-x
ca
x
fe
1.5
mo
0.5o6-δ
(x=0.5)。
52.本实施例中,剪裁后在轧制表面的形貌见图5,剖切的形貌见图6。由此可以看出,金属基板有较多的孔隙,孔隙均匀,气体流量稳定。金属丝纵横分布,保证良好的强度。
53.本实施例的烧结后金属支撑板的抗拉强度120mpa,支撑板的平面度0.15mm。采用上述多层金属丝网制备金属支撑板的抗拉强度更高。
54.实施例3:
55.本实施例与上述实施例2的区别仅在于:步骤1)中所选用的金属丝网的材质不同,具体地,选用fecral耐热钢丝网,丝网的目数为325目,前述耐热钢丝网,按照质量百分计,包括以下组分:c:0.08%,cr:18.7%,al:2.8%,mn:0.4%,si:1.1%,铁:余量;
56.步骤2)上述金属丝网采用叠放的形式,将金属丝网叠放6层,放置到刚玉板上,再将相同尺寸的刚玉板盖住叠放的丝网,刚玉板(陶瓷板)上放置2kg的重物;
57.步骤3)烧结温度为1340℃,烧结时间为50min;
58.步骤4)裁剪后得到金属基板的尺寸为110mm
×
110mm
×
0.53mm。
59.前述的阳极浆料包括有sr
2-x
ca
x
fe
1.5
mo
0.5o6-δ
(x=0.5)、nio、丁酮、乙醇、三乙醇胺、淀粉、聚乙烯醇缩丁醛pvb、聚乙二醇peg及谷氨酸pht。前述的电解质浆料包括有ceo2基固体电解质、丁酮、乙醇、三乙醇胺、聚乙烯醇缩丁醛pvb、聚乙二醇peg和谷氨酸pht。阴极材料为sr
2-x
ca
x
fe
1.5
mo
0.5o6-δ
(x=0.3)。
60.本实施例烧结后金属支撑板的抗拉强度120mpa,支撑板的平面度0.18mm。而使用与本实施例同样粉末材料的抗拉强度不超过50mpa,平面度在0.4mm以上。因此,采用上述多层金属丝网制备金属支撑板具有较高的抗拉强度。
61.实施例4:
62.本实施例与上述实施例2的区别仅在于:步骤1)中所选用的金属丝网的材质不同,具体地,选用fecral耐热钢丝网和304l奥氏体不锈钢丝网。其中,fecral耐热钢丝网的目数为325目,前述耐热钢,按照质量百分比计,包括以下组分:c:0.08%,cr:18.7%,al:2.8%,mn:0.4%,si:1.1%,铁:余量;304l奥氏体不锈钢丝网,丝网的目数为700目,包括以下组分:c:0.015%,cr:19.2%,mn:0.6%,si:0.8%,ni:10.3%,铁:余量;
63.步骤2)将上述fecral和304l丝网交替叠放,每种材质的丝网各5层,放置到刚玉板上,再将相同尺寸的刚玉板盖住叠放的丝网,刚玉板上放置4kg的重物;
64.步骤3)烧结温度为1320℃,烧结时间为50min;
65.步骤4)剪后得到金属基板的尺寸为110mm
×
110mm
×
0.64mm。
66.前述的阳极浆料包括有sr
2-x
ca
x
fe
1.5
mo
0.5o6-δ
(x=0.3)、nio、丁酮、乙醇、三乙醇胺、淀粉、聚乙烯醇缩丁醛pvb、聚乙二醇peg及谷氨酸pht。前述的电解质浆料包括有ba(sr)ce(ln)o3电解质、丁酮、乙醇、三乙醇胺、聚乙烯醇缩丁醛pvb、聚乙二醇peg和谷氨酸pht。
67.该实施例所制备出的金属支撑板的孔隙均匀、变形小和抗拉强度高。
68.实施例5:
69.本实施例与上述实施例2的区别仅在于:步骤1)中所选用的金属丝网的材质不同,具体地,选用高温合金(gh 3030)丝网,丝网的目数为200目,前述高温合金按照质量百分比计,包括以下组分:c:0.09%,cr:20.7%,al:0.13%,ti:0.2%,fe:1.1%,镍:余量;
70.步骤2)将上述金属丝网叠放6层,放入轧机轧制到厚度0.63mm;
71.步骤3)将轧制好的板材放入到真空烧结炉,在真空度为0.05pa,烧结温度为1310℃,烧结时间为30min下进行烧结,烧结冷却后取出丝网;
72.步骤4)裁剪后得到金属基板的尺寸为110mm
×
110mm
×
0.63mm。
73.该实施例所制备出的金属支撑板的孔隙均匀、变形小和抗拉强度高。
74.实施例6:
75.本实施例与上述实施例2的区别仅在于:步骤1)中所选用的金属丝网的材质不同,具体地,选用高温合金(gh4037)丝网,丝网的目数为400目,前述高温合金按照质量百分比计,包括以下组分:c:0.06%,cr:15.4%,mo:2.95%,w:5.90%,al:2.04%,ti:2.2%,fe:4.3%,不可避免的杂质:小于2%,镍:余量;
76.步骤2)将上述金属丝网叠放8层,放入轧机轧制到厚度为0.51mm;
77.步骤3)将轧制好的板材放入到真空烧结炉,在真空度为0.05pa,烧结温度为1290℃,烧结时间为90min下进行烧结,烧结冷却后取出丝网;
78.步骤4)裁剪后得到金属基板的尺寸为110mm
×
110mm
×
0.51mm。
79.该实施例所制备出的金属支撑板孔隙均匀、变形小和抗拉强度高。
80.实施例7:
81.本实施例与上述实施例2的区别仅在于:步骤1)中所选用的金属丝网的材质不同,具体地,选用高温合金(gh4037)丝网和434l铁素体不锈钢丝网。其中,gh4037丝网的目数为
400目,前述高温合金按照质量百分比计,包括以下组分:c:0.06%,cr:15.4%,mo:2.95%,w:5.90%,al:2.04%,ti:2.2%,fe:4.3%,不可避免的杂质:小于2%,镍:余量;434l铁素体不锈钢丝网,铁素体不锈钢丝网的目数为600目,前述铁素体不锈钢按照质量百分比计,包括以下组分:c:0.010%,cr:17.4%,mn:0.8%,si:0.5%,铁:余量;
82.步骤2)上述两种金属丝网各叠放10层,采用交替叠放的形式,放入轧机轧制到厚度为0.95mm;
83.步骤3)将轧制好的板材放入到真空烧结炉,在真空度为0.05pa,烧结温度为1290℃,烧结时间为90min下进行烧结,烧结冷却后取出丝网;
84.步骤4)裁剪后得到金属基板的尺寸为110mm
×
110mm
×
0.95mm。
85.该实施例所制备出的金属支撑板的孔隙均匀、变形小和抗拉强度高。
86.实施例8:
87.本实施例与上述实施例2的区别仅在于:步骤1)中所选用的金属丝网的材质不同,具体地,选用高温合金(gh4037)丝网和434l铁素体不锈钢丝网。其中,高温合金(gh4037)丝网的目数为400目,高温合金(gh4037)丝网按照质量百分比计,包括以下组分:c:0.06%,cr:15.4%,mo:2.95%,w:5.90%,al:2.04%,ti:2.2%,fe:4.3%,不可避免的杂质:小于2%,镍:余量;434l铁素体不锈钢丝网,丝网的目数为600目,包括以下组分:c:0.010%,cr:17.4%,mn:0.8%,si:0.5%,铁:余量;fecral耐热钢丝网,丝网的目数为325目,434l铁素体不锈钢按照质量百分比计,包括以下组分:c:0.08%,cr:18.7%,al:2.8%,mn:0.4%,si:1.1%,铁:余量;
88.步骤2)上述三种材质丝网各叠放5层,采用交替叠放的形式,放入轧机轧制到厚度0.85mm;
89.步骤3)将轧制好的板材放入到真空烧结炉,在真空度为0.05pa,烧结温度为1290℃,烧结时间为90min下进行烧结,烧结冷却后取出丝网;
90.步骤4)裁剪后得到金属基板的尺寸为110mm
×
110mm
×
0.85mm。
91.该实施例所制备出的金属支撑板的孔隙均匀、变形小和抗拉强度高。
92.实施例9:
93.本实施例与上述实施例2的区别仅在于:步骤1)中所选用的金属丝网的材质不同,具体地,金属丝网的材质为304l奥氏体不锈钢和高温合金(gh4037)丝网;其中,304l奥氏体不锈钢,按照质量百分比计,该不锈钢包括以下组分:c:0.01%,cr:17%,mn:0.6%,si:0.2%,ni:11%,铁:余量;
94.高温合金(gh4037)丝网按照质量百分比计,包括以下组分:c:0.07%,cr:21%,mo:3%,w:6%,al:2.2%,ti:2.5%,fe:5%,不可避免的杂质:小于2%,镍:余量。
95.步骤3)中的烧结温度为1350℃,烧结保温时间为5min。
96.在步骤5)、步骤6)和步骤7)中在干燥后均进行烧结,步骤5)中的烧结和步骤6)中的烧结所采用的烧结温度均为1050℃,烧结时间均为10min,步骤7)中的烧结所采用的烧结温度为800℃℃,烧结时间为5min,真空度为10-3
pa。
97.实施例10:
98.本实施例与上述实施例2的区别仅在于:步骤1)中所选用的金属丝网的材质不同,具体地,金属丝网的材质为304l奥氏体不锈钢和高温合金(gh4037)丝网;其中,304l奥氏体
不锈钢,按照质量百分比计,该不锈钢包括以下组分:c:0.07%,cr:20%,mn:0.5%,si:1.2%,ni:5%,铁:余量;
99.高温合金(gh4037)丝网按照质量百分比计,包括以下组分:c:0.08%,cr:15%,mo:2%,w:3%,al:0.1%,ti:0.1%,fe:1%,不可避免的杂质:小于2%,镍:余量。
100.步骤3)中的烧结温度为1000℃,烧结保温时间为500min。
101.在步骤5)、步骤6)和步骤7)中在干燥后均进行烧结,步骤5)中的烧结和步骤6)中的烧结所采用的烧结温度均为1400℃,烧结时间均为300min,步骤7)中的烧结所采用的烧结温度为1200℃,烧结时间为300min,真空度为102pa。
102.实施例11:
103.本实施例与上述实施例2的区别仅在于:在步骤5)、步骤6)和步骤7)中在干燥后均进行烧结,步骤5)中的烧结和步骤6)中的烧结所采用的烧结温度均为1200℃,烧结时间均为50min,步骤7)中的烧结所采用的烧结温度为900℃,烧结时间为60min,真空度为102pa。