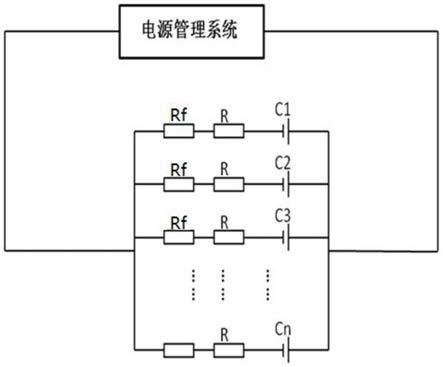
1.本发明涉及充电电池领域,具体涉及一种扣式电池制造中的并联充放电装置及充放电方法。
背景技术:2.电池制造过程中,在完成电池的组装后,需要进行化成、分容的充放电过程。传统电池制造过程中的电池充放电采用单回路控制方式,对于规模较大的制造企业,这种每个电池配备一个回路式的充放电模式给企业带来巨大的成本负担。并联充放电方式可以将单点单回路控制提升为单点多回路控制,从而降低电池制造过程中的设备投入成本、占地成本、和管理成本。然而,对于包括扣式电池在内的小容量电池而言,由于电池内阻的差异,简单的并联充放电方式会导致通过并联支路的电流有较大的差异,进而造成各充放电电池电压有较大的差异,而达成出厂需要的电池一致性过程需要较长的时间,时间成本过大。
3.对于小型电池的多路电池组并联充电,如何保持充电的一致性;放电时,由于电池内阻很小,当电池组间存在比较大的电压差时,则会在电池组之间形成较大的环流,而该电池组间较大的环流会对电池组产生不良影响,甚至损坏,如何降低并联放电的环流对电池的影响;理论上,对于单体电池而言,其本身就是一个并联体,因此如何在上述问题、制造成本、电池组系统偏差容许范围之间找到优化平衡是本发明方案的基点。
技术实现要素:4.为解决上述问题本发明提供了一种扣式电池制造中的多路电池并联充放电装置及充放电方法,采用taper型充电模式,通过对并联支路中配置串联配阻电阻,以控制充电时流经各并联支路电池电流的均衡性和一致性;并且配置的串联配阻电阻也能够在出现短路的意外情况下起到分流的作用,在放电时亦能够有效降低并联支路回路中产生的环流影响;本发明方法还配置了限流电阻以保障系统线路在电流超限的情况下阻断并联支路;本发明方法提供的电路使充放电的单点控制变成多点统一控制,设计的系统简单、安全、高效,极大地降低控制系统成本。
5.为实现上述目的,本发明的技术方案如下,一种扣式电池制造过程中的电池并联充放电装置,包括电源管理系统和若干组并联的充放电支路。
6.上述的一种扣式电池制造过程中的电池并联充放电装置,电源管理系统与若干组并联的充放电支路串联连接。
7.上述的一种扣式电池制造过程中的电池并联充放电装置,每一组充放电支路包括串联连接的电池、配阻电阻r、和限流电阻rf。
8.上述的一种扣式电池制造过程中的电池并联充放电装置,各组充放电支路中配阻电阻r的阻值等同。
9.上述的一种扣式电池制造过程中的电池并联充放电装置,配阻电阻r的阻值为各充放电支路中电池平均内阻的к倍,к介于2~10之间。
10.上述的一种扣式电池制造过程中的电池并联充放电装置,各充放电支路中限流电阻rf阻值等同。
11.上述的一种扣式电池制造过程中的电池并联充放电装置,限流电阻rf中允许的最大通过电流是电池标示的最大放电电流的1~10倍。
12.上述的一种扣式电池制造过程中的电池并联充放电装置,限流电阻rf中允许的最大通过电流是电池标示的最大放电电流的3~8倍。
13.上述的一种扣式电池制造过程中的电池并联充放电装置的充电方法,电源管理系统以恒流的方式启动充电,待电池充电达到一定电压后改为恒压充电,当充电电流降为截止电流时,停止充电。
14.上述的一种扣式电池制造过程中的电池并联充放电装置的放电方法,所述电源管理系统恒流的方式启动放电,待放电电池容量降到10%soc后,改为恒流放电,当回路电压降至截止电压时,停止放电。
15.本发明提供的方法对于平衡电池内阻的原理如下:
16.假设存在电池内阻偏差
±
20%的某n个电池采用本发明提供的方法充电,设并联支路中的配阻电阻r为5倍的电阻均值,且其阻值偏差为
±
1%,则:
[0017][0018]
即通过本发明提供的方法充电,可使原本电池内阻偏差为
±
20%的电池组的偏差降至实际偏差的
±
4.2%,进而满足系统偏差要求。
[0019]
本发明的有益效果是:
[0020]
对于小型电池而言,由于电池内阻差异,并联充电时,流经各并联支路的电流差异较大。本发明设计的各并联支路配置的串联电阻,可有效平衡流经各并联支路的电流,保障充放电流的一致性。当某个或某几个并联支路出现短路的情况下,各并联支路配置的限流电阻可保证其它并联支路照常充放电,使其不受影响。本发明方法巧妙地在可行解决方案、制造成本、电池组系统偏差容许范围之间找到平衡,提供的电路使充放电的单点控制变成多点统一控制,设计的系统简单、安全、高效,极大地降低控制系统成本。
附图说明
[0021]
图1电池并联充放电装置框图。
具体实施方式
[0022]
为了使本发明解决的技术问题、技术方案、及有益效果更加清楚明白,以下结合附图及实施例,对本发明进行进一步详细说明。应当理解,此处所描述的具体实施例仅用以解释本发明,并不用于限定本发明。
[0023]
图1为本发明电池组并联充电装置提供的一实施例结构框图,参阅图1,电源管理系统与若干组并联充放电支路串联连接。并联的充放电支路包括n组充放电支路,所述n组充放电支路由第一充放电支路、第二充放电支路、第三充放电支路、
……
、第n充放电支路并联连接。其中n为自然数,且n≥1,即n也为充电支路的组数。
[0024]
其中,第一充放电支路包括串联的配阻电阻r、限流电阻rf和电池c1、第二充放电
支路包括串联的配阻电阻r、限流电阻rf和电池c2、第三充放电支路包括串联的配阻电阻r、限流电阻rf和电池c3、
……
、第n充放电支路包括串联的配阻电阻r、限流电阻rf和电池cn。
[0025]
所述电源管理系统控制充放电的方式、启动、终止。所述配阻电阻r用于平衡各支路的充放电电流,并平衡各支路两端的放电电压,所述限流电阻rf用于限制各支路可承受的最大电流。
[0026]
实施例1
[0027]
扣式电池制造过程中的电池并联充放电装置是电源管理系统和20组并联的充放电支路串联连接。20支容量为70mah的单体电池并联,20支电池的内阻值在200mω
±
20%区间,每个并联充放电支路串联一个电阻为1ω配阻电阻r和一个限阻电流rf为0.5a限流电阻。所述电源管理系统以1c恒流(0.07a)的方式启动充电,待电池充电达到90%电池带电量指标(以下称soc)后改为恒压(4.2v)充电,充电10分钟后停止充电,测试并记录通过各支路的电流。放电时,所述电源管理系统以1c恒流(0.07a)的方式启动放电,待放电电池容量降到10%soc后,改为0.2c恒流(0.0014a)放电,当回路电压降至截止电压(2.75v)时,停止放电,记录各支路电池释放的电池容量(见表1)。
[0028]
实施例2
[0029]
扣式电池制造过程中的电池并联充放电装置是电源管理系统和20组并联的充放电支路串联连接。20支容量为70mah的单体电池并联,20支电池的内阻值在200mω
±
20%区间。所述电源管理系统以1c恒流(0.07a)的方式启动充电,待电池充电达到90%soc后改为恒压(4.2v)充电,充电10分钟后停止充电,测试并记录通过各支路的电流。放电时,所述电源管理系统以1c恒流(0.07a)的方式启动放电,待放电电池容量降到10%soc后,改为0.2c恒流(0.0014a)放电,当回路电压降至截止电压(2.75v)时,停止放电,记录各支路电池释放的电池容量。
[0030]
由表1可见,较之实施例2,实施例1支路中串联配置电阻后,流经各支路的电流均衡性很好,充放电容量偏差也小。整个装置完成充电时间为83分钟,完成放电时间为69分钟;实施例2中,整个装置完成充电时间为102分钟,完成放电时间为74分钟。采用本发明提供的方法的实施例1能够在更短的时间内完成充放电,与简单的并联充电相比,完成充电的时间可减少18%。
[0031]
表1
[0032]