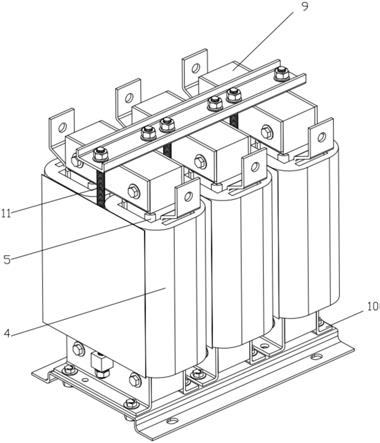
1.本实用新型涉及电抗器领域,尤其是指一种单相双柱电抗器线圈结构。
背景技术:2.电抗器也叫电感器,一个导体通电时就会在其所占据的一定空间方位产生磁场,但是,通电长直导体的电感较小,所产生的磁场不强,因此实际的电抗器是导线绕制螺线管形式,称为空心电抗器;有些电抗器应用不同,一般需要其具有更大的电感,就会在螺线管中心插入铁心,称为铁心电抗器。一般采用目前市场上应用的大功率单相电抗器由于受制作工艺限制,都采用双柱结构,如本技术附图1所示,每个心柱1上套装有线圈绕组,采用铝箔绕制,绕组的头尾均用母排2焊接引出,其过度连接都采用外部母排连接工艺,这种工艺的弊端有:整体外形尺寸过大;过度母排连接点温升高;连接母排2同拉杆螺柱3间容易发生短路、导电等问题,存在绝缘处理难等缺点。
技术实现要素:3.有鉴于此,本实用新型提供了一种新型的单相双柱电抗器线圈结构。
4.为实现上述目的,本实用新型提供如下技术方案:
5.一种新型单相双柱电抗器线圈结构,包括两个绕组线圈、两个心柱,所述绕组线圈分别套装在电抗器的两个心柱上,每个绕组线圈均具有初始端头与尾部,所述绕组线圈的初始端头用母排焊接引出,绕组线圈的尾部不焊接并预留有预留段,所述两个预留段直接焊接连接,所述绕组线圈的外层缠绕一层玻璃纤维丝带层,所述玻璃纤维丝带层外包覆有聚酰亚胺薄膜层。
6.具体的,所述预留段的长度≤200mm。
7.具体的,所述玻璃纤维丝带层的宽度≤50mm,厚度≤3mm。
8.具体的,所述新型单相双柱电抗器线圈结构的绕组线圈包括绝缘预浸材料层与铝带层,所述绝缘预浸材料层位于铝带层与铝带层之间。
9.本实用新型的有益效果在于:本实用新型所述的新型单相双柱电抗器线圈结构简单,整体尺寸小;在生产过程中,将两个独立绕组线圈套装在双柱电抗器的两个心柱上,双绕组线圈过度连接采用预留铝箔进行直接焊接的工艺,最后再外包绝缘层,这种直接预留处理并直接焊接的工艺,省去外连接母排,极大的节省了原料成本,原料成本较之前下降5%,整体结构更加紧凑;同时避免了母排接触点的温升以及母排同拉杆螺柱间的绝缘问题,使用上安全性更高。
附图说明
10.为了更清楚地说明本实用新型实施例或现有技术中的技术方案,下面将对实施例或现有技术描述中所需要使用的附图作简单地介绍,显而易见地,下面描述中的附图仅仅是本实用新型的一些实施例,对于本领域普通技术人员来讲,在不付出创造性劳动的前提
下,还可以根据这些附图获得其他的附图。
11.附图1所示为现有技术的单相双柱电抗器线圈结构;
12.附图2所示为本实用新型所述的新型单相双柱电抗器线圈结构;
13.附图3所示为多组新型单相双柱电抗器线圈结构;
14.本实用新型附图标记:
15.4、线圈绕组,5、心柱,6、初始端头,7、尾部,8、母排,9、上铁轭,10、下铁轭,11、拉杆螺柱。
具体实施方式
16.下面将结合本实用新型实施例中的附图,对本实用新型实施例中的技术方案进行清楚、完整地描述,显然,所描述的实施例仅仅是本实用新型一部分实施例,而不是全部的实施例。基于本实用新型中的实施例,本领域普通技术人员在没有做出创造性劳动前提下所获得的所有其他实施例,都属于本实用新型保护的范围。
17.下面将结合说明书附图对本实用新型做进一步描述。
18.本实用新型提供如下技术方案:
19.如附图2、3所示,本实用新型新型单相双柱电抗器线圈结构,包括两个绕组线圈4和铁心,铁心包括两个心柱5、上铁轭9、下铁轭10。所述绕组线圈4分别套装在电抗器的两个心柱5上,每个绕组线圈4均具有初始端头6与尾部7,所述绕组线圈的初始端头6用母排8焊接引出,绕组线圈4的尾部不焊接并预留有预留段,所述两个预留段直接焊接连接,所述绕组线圈的外层缠绕一层玻璃纤维丝带层,所述玻璃纤维丝带层外包覆有聚酰亚胺薄膜层。这样的结构设计使得所述新型单相双柱电抗器线圈结构更加简单,整体尺寸更小。
20.具体的,所述预留段的长度≤200mm为佳,所述玻璃纤维丝带层的宽度≤50mm,厚度≤3mm。这样能够确保在相对的低成本下获得高强度的电抗器线圈结构。
21.具体的,所述新型单相双柱电抗器线圈结构的绕组线圈包括绝缘预浸材料层与铝带层,所述绝缘预浸材料层位于铝带层与铝带层之间。具体的,在本实施例中,所述绝缘预浸材料为绝缘预浸布,所述绝缘预浸布包括一层聚酰亚胺薄膜层和一层耐热纤维非纺织布,所述聚酰亚胺薄膜层的厚度不大于0.05mm。所述每层铝带之间通过绝缘预浸布层层间隔,经过固化处理后,绝缘预浸布将每层铝带都牢固的粘结在一起,使得所述线圈绕组形成一个稳固的整体,提高整体的机械强度,结构稳定性更高。
22.本实用新型还提供一种如以上所述的新型单相双柱电抗器线圈结构的生产工艺,下面通过两个具体实施例对本工艺做出详细描述。
23.实施例1
24.所述新型单相双柱电抗器线圈结构的生产工艺包括如下步骤:
25.(1)备至所需材料:采用铝带作为绕组线圈材料,并将其吊装在箔绕机的料架上,将心轴在箔绕机上固定好;准备玻璃纤维丝带与聚酰亚胺薄膜,所述玻璃纤维丝带的厚度为1.5mm,宽度为25mm;准备焊接用母排,并将其表面做清洁处理;选取模芯,套在心轴上备用,为了方便脱模,可在模芯外包覆一层聚酰亚胺薄膜,所述薄膜的厚度为0.05mm;备制绝缘预浸材料,并将所述绝缘预浸材料套装在卷绕机上,确保绝缘预浸材料与铝带在同一条直线上,将铝带与绝缘预浸材料一端经过辅助的导向压紧装置引至绕线机的心轴位置并调
整好待用。所述绝缘预浸材料与铝带的绕制方式与实施例1相同,在此不再赘述。
26.(2)绕制绕组线圈:按照所需的匝数在模芯上绕制铝带形成绕组线圈,将铝带的初始端头拉出,用所述母排焊接引出,将铝带的尾部预留形成预留段,将所述预留段的尾部直接焊接在一起。所述预留段的尾部的铝带与母排在焊接时采用氩弧焊,电流为300~450a,铝焊条的直径为2mm,焊点的深度为0.3mm
±
0.05mm,焊点直径为0.8mm。本实施例中,线圈匝数为11圈,一般的,具体的线圈匝数要依据线圈的型号规格确定。
27.在本实施例中,所述铝带的尾部与母排焊接时,氩气流量为6l/min,焊接的最大电流值不高于450a,焊接的坡口角度为35
±
0.5
°
。为保证焊接的成品率,焊前将焊接坡口及其两侧5mm范围内进行严格清理,此范围内不得有水、油、锈、氧化物等。坡口处不允许有包砂、裂纹、疏松等铸造缺陷。如有以上缺陷,必须按焊补工艺进行补焊后,方可进行焊接。需要注意的是,焊接过程中保证形成的焊缝一致。
28.(3)熔融固化步骤:将步骤(2)所制备的绕组线圈放入熔炉内进行固化处理,熔炉内的温度为165℃
±
5℃,维持恒温5小时,固化完成后出炉自然冷却。
29.(4)绝缘处理:在步骤(2)所制得的绕组线圈外层缠绕一层厚度为1.5mm的玻璃纤维丝带,在玻璃纤维丝带外层缠绕一层厚度为0.15mm的聚酰亚胺薄膜。具体的,将步骤(3)制得的绕组线圈用磨光机磨掉焊接处的尖角毛刺,所述磨光机的转速小于1500r/min,用钢刷等辅助工具刷去焊接表面的氧化物,同时擦干铝带上的焊渣,然后再完成玻璃纤维丝带层与聚酰亚胺薄膜层的包覆,最后用502胶水固定。
30.本实用新型所述的新型单相双柱电抗器线圈,尤其是在多组电抗器线圈结构时,省掉了尾端母排的设置,结构简单,整体尺寸小。在生产过程中,将两个独立绕组线圈套装在双柱电抗器的两个心柱上,双绕组线圈过度连接采用预留铝箔进行直接焊接的工艺,最后再外包绝缘层,这种直接预留处理并直接焊接的工艺,省去外连接母排,减少了母排的用量,节约了原材料,节省了安装成本,极大的节省了整体的原料成本,原料成本较之前下降5%,整体结构也更加紧凑;同时能够避免传统电抗器普遍存在的母排接触点的温升以及母排同拉杆螺柱11间的绝缘问题,使用上安全性更高。
31.实施例2
32.所述新型单相双柱电抗器线圈结构的生产工艺包括如下步骤:
33.(1)备至所需材料:采用铝带作为绕组线圈材料,并将其吊装在箔绕机的料架上,将心轴在箔绕机上固定好;准备玻璃纤维丝带与聚酰亚胺薄膜,所述玻璃纤维丝带的厚度不大于3mm;准备焊接用母排,并将其表面做清洁处理;选取模芯,套在心轴上备用;备制前述绝缘预浸材料,并将所述绝缘预浸材料套装在卷绕机上,确保绝缘预浸材料与铝带在同一条直线上,将铝带与绝缘预浸材料一端经过辅助的导向压紧装置引至绕线机的心轴位置并调整好待用。具体的,将绝缘预浸材料作为内层,铝带作为外层,用绝缘预浸材料将各个层的铝带隔开,绝缘预浸材料与铝带同时绕制形成所述绕组线圈。
34.(2)绕制绕组线圈:按照所需的匝数在模芯上绕制铝带形成绕组线圈,将铝带的初始端头拉出,用所述母排焊接引出,将铝带的尾部预留形成预留段,将所述预留段的尾部直接焊接在一起,所述预留段的尾部在焊接时采用氩弧焊,电流为450a,铝焊条的直径为2.5mm,焊点的深度为0.2mm
±
0.05mm,焊点直径为0.7mm。为保证焊接的成品率,焊前将焊接坡口及其两侧5mm范围内进行严格清理,此范围内不得有水、油、锈、氧化物等。坡口处不允
许有包砂、裂纹、疏松等铸造缺陷。如有以上缺陷,必须按焊补工艺进行补焊后,方可进行焊接。需要注意的是,焊接过程中保证形成的焊缝一致。
35.(3)熔融固化步骤:将步骤(2)所制备的绕组线圈放入熔炉内进行固化处理,熔炉内的温度为165℃
±
5℃,维持恒温6小时,固化完成后出炉自然冷却。固化可以选择在自然环境温度下固化,也可以在30~50℃的环境下进行固化干燥。
36.(4)绝缘处理:在步骤(2)所制得的绕组线圈外层缠绕一层厚度为1.5mm的玻璃纤维丝带,在玻璃纤维丝带外层缠绕一层厚度为0.15mm的聚酰亚胺薄膜。具体的,将步骤(3)制得的绕组线圈用磨光机磨掉焊接处的尖角毛刺,所述磨光机的转速小于1500r/min,用钢刷等辅助工具刷去焊接表面的氧化物,同时擦干铝带上的焊渣,然后再完成玻璃纤维丝带层与聚酰亚胺薄膜层的包覆,最后用502胶水固定。
37.对所公开的实施例的上述说明,使本领域专业技术人员能够实现或使用本实用新型。对这些实施例的多种修改对本领域的专业技术人员来说将是显而易见的,本文中所定义的一般原理可以在不脱离本实用新型的精神或范围的情况下,在其它实施例中实现。因此,本实用新型将不会被限制于本文所示的这些实施例,而是要符合与本文所公开的原理和新颖特点相一致的最宽的范围。