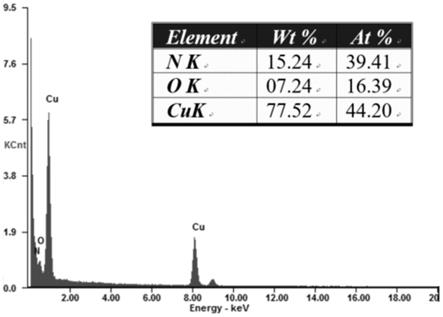
1.本发明涉及纳米化合物复合材料领域,具体涉及一种氧化亚铜复合材料及其制备方法和应用。
背景技术:2.复合材料是由两种或两种以上不同性质的材料通过物理或化学的方法在宏观或微观上组成的新性质材料,在化学、生命、材料、物理、电子等领域具有广泛的应用。原位生长得到的复合材料往往具有更好的催化活性,然而原位生长的实现是十分困难的,并且常为薄膜材料,这限制了它的应用。因此,有必要开发新方法来原位构筑复合材料。
3.铜氧化物具有价格低廉、制备方法简单易行、氧化还原性质丰富且化学稳定性好等优点,最近关于铜氧化物的研究取得了较大的进展,包括不同形貌、不同结构的铜氧化物的设计合成,另外,作为3d过渡金属的铜元素具有丰富的电子态结构,将铜氧化物与其他材料复合在一起,能够构筑特殊的电子态结构,得到的复合材料极具研究意义。氮化铜具有特殊的电子结构、较高的化学稳定性和较好的导电性,因而在可再生能源领域受到广泛关注。然而,氮化铜的合成往往涉及到氨气钢瓶的使用,而氨气具有刺激性气味,对人体具有较大的危害性,长时间使用氨气也有一定的危险。
技术实现要素:4.因此,本发明要解决的技术问题在于现有对难以合成氧化亚铜和氮化铜复合材料的问题,从而提供一种氧化亚铜复合材料及其制备方法和应用。
5.为此,本发明采用如下技术方案:
6.本发明提供一种氧化亚铜复合材料的制备方法,包括如下步骤:
7.s1:将氧化亚铜和尿素,碱充分混合,加热进行反应;
8.s2:将反应后的产物洗涤后烘干,得到所述氧化亚铜复合材料。
9.进一步地,所述氧化亚铜和尿素,碱的摩尔比为1:5-25:5-25。
10.步骤s1中,所述加热反应温度为180-200℃,反应时间为4-10h;
11.步骤s2中,所述烘干温度为70-90℃,烘干时间为8-16h。
12.优选地,所述氧化亚铜由如下工艺制得:
13.将五水硫酸铜溶于超纯水中,加入十六烷基三甲基溴化铵和抗坏血酸,混合后升温搅拌反应;然后加入氢氧化钠溶液至溶液变为亮黄色,加热搅拌静置,得到黄色的悬浊液;将悬浊液交替使用超纯水和无水乙醇在离心得到的深橙色固体;将深橙色固体进行干燥,得到棕黄色固体氧化亚铜。
14.进一步地,所述五水硫酸铜和十六烷基三甲基溴化铵、抗坏血酸的摩尔比为1:5:5。
15.优选地,所述碱为氢氧化钠和氢氧化钾中的至少一种
16.本发明还提供一种氧化亚铜复合材料,由上述制备方法制得。
17.本发明还提供上述氧化亚铜复合材料的应用,具体为应用于锂空气电池的正极催化剂。
18.本发明技术方案,具有如下优点:
19.(1)本发明通过原料和反应时间的控制,为氧化亚铜原位合成氮化铜得到复合材料提供了一种方便可行的新方法;由于所使用的尿素的量有限,其产生的氨气量少且可控,不使用氨气钢瓶,实验条件要求更低,操作简单便捷,安全系数高。
20.(2)本发明得到的氧化亚铜复合材料,是一种内部为球形、外部为立方体的核壳结构材料,其结构稳定,具有广阔的应用前景。
21.(3)本发明得到的氧化亚铜复合材料,其应用于锂空气电池反应中,氧化亚铜的氮化对其锂空气电池催化活性的提升有重要作用,而复合材料的构筑不仅可以进一步提升其催化活性,同时可以提高材料性能的稳定性。由于原位形成的复合材料的界面效应,相比于机械复合的复合材料,其催化活性提升更为明显提升。
附图说明
22.为了更清楚地说明本发明具体实施方式或现有技术中的技术方案,下面将对具体实施方式或现有技术描述中所需要使用的附图作简单地介绍,显而易见地,下面描述中的附图是本发明的一些实施方式,对于本领域普通技术人员来讲,在不付出创造性劳动的前提下,还可以根据这些附图获得其他的附图。
23.图1为本发明实施例1得到的氧化亚铜复合材料的扫描电子显微镜能谱仪测试结果;
24.图2为本发明试验例1中,实施例1和对比例1-3得到的粉末的x射线衍射图;
25.图3为本发明试验例1中,实施例1和对比例1-3得到的粉末的扫描电子显微镜图;
26.图4为本发明试验例1中,实施例1和对比例1-3得到的粉末的透射电子显微镜图;
27.图5为本发明试验例2中,实施例1和对比例1-3得到的粉末为正极催化剂的锂空气电池在100ma/g电流密度、2.5-4.4v电压范围内的放电-充电曲线图;
28.图6为本发明试验例2中,实施例1和对比例1-3得到的粉末为正极催化剂的锂空气电池在200ma/g电流密度、2.5-4.4v电压范围内的放电-充电曲线图;
29.图7为本发明试验例2中,实施例1和对比例1-3得到的粉末为正极催化剂的锂空气电池在500ma/g电流密度、2.5-4.4v电压范围内的放电-充电曲线图;
30.图8为本发明试验例2中,实施例1和对比例1-3得到的粉末为正极催化剂的锂空气电池的容量保持率;
31.图9为本发明试验例2中,实施例1和对比例1-3得到的粉末为正极催化剂的锂空气电池的循环稳定性。
具体实施方式
32.提供下述实施例是为了更好地进一步理解本发明,并不局限于所述最佳实施方式,不对本发明的内容和保护范围构成限制,任何人在本发明的启示下或是将本发明与其他现有技术的特征进行组合而得出的任何与本发明相同或相近似的产品,均落在本发明的保护范围之内。
33.实施例中未注明具体实验步骤或条件者,按照本领域内的文献所描述的常规实验步骤的操作或条件即可进行。
34.实施例1
35.本实施例提供一种氧化亚铜复合材料,其制备方法具体如下:
36.(1)氧化亚铜的合成
37.将0.16g氢氧化钠固体溶于20ml超纯水中,搅拌溶解,形成透明澄清溶液备用。将0.1g五水合硫酸铜加入装有200ml超纯水的烧杯中,搅拌溶解,随后加入7.33g十六烷基三甲基溴化铵、0.36g抗坏血酸,升温至60℃,搅拌30分钟。随后,将配制好的氢氧化钠溶液加入烧杯中,溶液逐渐变为亮黄色,加热搅拌十分钟后静置,得到黄色的悬浊液。将冷却后的悬浊液交替使用超纯水和无水乙醇在8000rpm条件下离心洗涤三次,每次5分钟。将得到的深橙色固体放入真空干燥箱,60℃干燥12小时,得到棕黄色固体,即氧化亚铜。
38.(2)氧化亚铜的氮化
39.将步骤(1)得到的氧化亚铜称量0.1431g,与0.3003g尿素、0.2g氢氧化钠混合均匀,放入25ml反应釜中,置于200℃烘箱中,反应6小时。将得到的固体使用超纯水洗涤3次后,放置于80℃的烘箱中烘干12小时,到深褐色固体,即所述氧化亚铜复合材料,如图1所示,对得到的氧化亚铜复合材料扫描电子显微镜能谱仪测试,可以看出o元素和n元素的摩尔比为1:2,因而可知上述氧化亚铜复合材料中氧化亚铜和氮化铜的摩尔比为1:2。
40.实施例2
41.本实施例提供一种氧化亚铜复合材料,其制备方法具体如下:
42.将实施例1步骤(1)得到的氧化亚铜称量0.1431g,与0.6006g尿素、0.4g氢氧化钠混合均匀,放入25ml反应釜中,置于180℃烘箱中,反应7小时。将得到的固体使用超纯水洗涤3次后,放置于80℃的烘箱中烘干12小时,到深褐色固体,即所述氧化亚铜复合材料。
43.实施例3
44.本实施例提供一种氧化亚铜复合材料,其制备方法具体如下:
45.将实施例1步骤(1)得到的氧化亚铜称量0.1431g,与0.3003g尿素、0.28g氢氧化钾混合均匀,放入25ml反应釜中,置于190℃烘箱中,反应4小时。将得到的固体使用超纯水洗涤3次后,放置于90℃的烘箱中烘干16小时,到深褐色固体,即所述氧化亚铜复合材料。
46.实施例4
47.本实施例提供一种氧化亚铜复合材料,其制备方法具体如下:
48.将实施例1步骤(1)得到的氧化亚铜称量0.1431g,与1.5015g尿素、1g氢氧化钠混合均匀,放入25ml反应釜中,置于200℃烘箱中,反应9小时。将得到的固体使用超纯水洗涤3次后,放置于80℃的烘箱中烘干8小时,到深褐色固体,即所述氧化亚铜复合材料。
49.实施例5
50.本实施例提供一种氧化亚铜复合材料,其制备方法具体如下:
51.将实施例1步骤(1)得到的氧化亚铜称量0.1431g,与0.3003g尿素、0.14g氢氧化钾、0.1g氢氧化钠混合均匀,放入25ml反应釜中,置于180℃烘箱中,反应10小时。将得到的固体使用超纯水洗涤3次后,放置于70℃的烘箱中烘干10小时,到深褐色固体,即所述氧化亚铜复合材料。
52.对比例1
53.本对比例使用实施例1步骤(1)中制得的氧化亚铜。
54.对比例2
55.本对比例和实施例1的区别在于,将步骤(2)改为,将步骤(1)得到的氧化亚铜称量0.1431g,与0.3003g尿素、0.2g氢氧化钠混合均匀,放入25ml反应釜中,置于200℃烘箱中,反应12小时。将得到的固体使用超纯水洗涤3次后,放置于80℃的烘箱中12小时,即可得到黑褐色固体。
56.对比例3
57.本对比例取对比例1和对比例2得到的粉末,以摩尔比为1:2的比例充分混合。
58.试验例1
59.将对比例1得到的粉末记为c-1,对比例2得到的粉末记为c-2,实施例1得到的粉末记为c-3,对比例3得到粉末记为c-4,对c-1、c-2、c-3和c-4进行检测,如图2-4。
60.从图2可以看出,c-1和c-2均只具有一组衍射峰,分别对应氧化亚铜和氮化铜,表明它们各自是氧化亚铜和氮化铜的纯相;而c-3、c-4具有氧化亚铜、氮化铜两组衍射峰,这表明c-3、c-4是由二者组合而成,为氧化亚铜和氮化铜的复合材料。
61.图3中,(a)、(b)、(c)和(d)分别对应c-1、c-2、c-3和c-4的扫描电子显微镜图,可以看出,(a)表明,c-1为圆球形;(b)表明,c-2为近立方体的形貌;而在(c)中,c-3的形貌介于c-1和c-2之间,是一种由球形向正方体的过渡形貌;(d)则表明,c-4是由圆球形和立方体形混合而成,表明了其是由c-1和c-2混合得来的。
62.图4中,(a)、(b)、(c)和(d)分别对应c-1、c-2、c-3和c-4的透射电子显微镜图,可以看出,(a)表明,c-1表现为具有核壳结构的球形;(b)表明,c-2表现为具有核壳结构的立方体,说明经过长时间的尿素处理,氧化亚铜已经完全转变为氮化铜;而在(c)中,c-3则是内部为球形、外部为立方体的核壳结构,这表明短时间的尿素处理仅仅使具外部的氧化亚铜发生氮化,转变为氮化铜,而内部仍然保持为氧化亚铜结构,这证明了c-3是氧化亚铜和氮化铜复合而成的;(d)则表明,c-4同时存在核壳结构的圆球形和立方体,再次印证了它是由c-1和c-2混合而来。
63.试验例2
64.将试验例1中的c-1、c-2、c-3和c-4粉末作为锂空气电池的正极催化剂,具体方法如下:将所得到的粉末与炭黑、萘酚锂以质量比3:6:1称重混合,加入nmp作为溶剂混合均匀,涂布在碳纸上,放置于120℃真空干燥箱中烘干12小时。将烘干后的碳纸裁剪为直径为12mm的圆片,以锂片为负极,与传统的cr2032型扣式锂空气电池电池模块组装,即可得到后续测试所需要的锂空气电池。
65.对得到的锂空气电池做性能测试,如图5-9所示。
66.图5是以c-1、c-2、c-3和c-4为正极催化剂的锂空气电池分别在100ma/g电流密度下、2.5-4.4v的电压范围内进行测试的放电-充电曲线图,它们的放电比容量分别为5794.9、6529.2、10845.8、7131.6mah/g;将电流密度增加至200ma/g进行测试,如图6所示,c-1、c-2、c-3和c-4作为正极催化剂的锂空气电池的放电比容量分别为4521.6、5044.7、8867.6、5617.8mah/g;在图7中,进一步增加测试电流密度至500ma/g,四种锂空气电池的放电比容量为2753.7、4057.8、7288.0、4574.2mah/g。由图5-7,比较c-1和c-2,材料氮化后,其对于锂空气电池的催化活性有所提升,但提升程度并不明显;比较c-3、c-4与c-1、c-2,可以
发现其锂空气电池催化活性大幅提升,这说明材料复合对其性能有促进作用;比较c-3和c-4,发现c-3的催化活性提升更明显,这说明原位复合相比于普通的复合更具有优势。
67.在图8中为材料的锂空气电池容量保持率,当电流密度增加到200ma/g时,c-1、c-2、c-3、c-4的容量保持率分别为78%、78%、82%、79%;当电流密度进一步增大至500ma/g时,c-1的容量保持率仅为48%,c-2下降至62%,c-3维持在67%,而c-4则在64%。比较c-1与c-2、c-3、c-4可以发现,氮化铜对于容量保持率的提升有着作用。而c-3、c-4的容量保持率优于c-2,这表明复合材料的重要作用,c-3又优于c-4,这表明原位复合的重要作用。
68.图9是以c-1、c-2、c-3和c-4为正极催化剂的锂空气电池的循环稳定性测试结果,测试条件为:100ma/g的电流密度进行截容量测试,容量限制为500mah/g。可以看出,c-1和c-2分别可以稳定循环94和100圈,c-4则稳定循环105圈,略有提升;而c-3可以保持稳定循环154圈,其循环稳定性提高了50%。
69.由图5-9可知,氧化亚铜的氮化对其锂空气电池催化活性的提升有重要作用,而复合材料的构筑不仅可以进一步提升其催化活性,同时可以提高材料性能的稳定性。由于复合材料的界面效应,c-3表现出优秀的锂空气电池性能,相比于机械复合的c-4,其催化活性明显提升。
70.显然,上述实施例仅仅是为清楚地说明所作的举例,而并非对实施方式的限定。对于所属领域的普通技术人员来说,在上述说明的基础上还可以做出其它不同形式的变化或变动。这里无需也无法对所有的实施方式予以穷举。而由此所引伸出的显而易见的变化或变动仍处于本发明创造的保护范围之中。