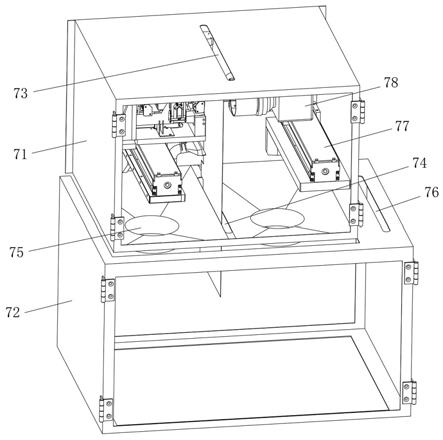
1.本发明涉及锂离子动力电池领域,特别指适用于锂离子动力电池极耳裁切除尘工艺的一种极耳裁切除尘装置及其极耳裁切除尘工艺。
背景技术:2.锂电池lithium battery是指电化学体系中含有锂包括金属锂、锂合金和锂离子、锂聚合物的电池。锂电池大致可分为两类:锂金属电池和锂离子电池。锂电池是一种充电电池,它主要依靠锂离子在正极和负极之间移动来工作。一般采用含有锂元素的材料作为电极的电池,是现代高性能电池的代表。随着国家大力推动新能源发展,各行各业对锂离子动力电池的需求日益增长,锂离子动力电池的组成结构中电芯是其核心部件,电芯一般由正负极片相互交错叠合而成。电芯组成结构包括上下交错叠合的多片正负极片,正负极片之间通过隔膜进行隔离绝缘。目前国内技术比较先进的锂电池设备主要掌握在国外设备供应商手中,国内高端锂电叠片设备目前主要依靠进口。
3.锂离子电池的电芯一般由正负极片交错叠合后形成,因此在电芯制造过程中首先需要先将单片的极片制造完成。目前,市场上极片的来料大部分为带状卷料,由于电芯内部极片为单片状结构,在电芯制成前需要将单片极片制成,在单片极片制成过程中涉及几个工艺制成段,包括极片带导出工艺、极耳裁切工艺及极片裁切工艺。
4.针对极耳裁切工艺,存在以下技术难点问题需要解决:1、极耳裁切过程中会产生粉末,极易残留在极片表面,而极片对表面洁净度要求极高,因此需要解决极片带表面因极耳裁切导致的残余物或颗粒粘附导致污染的问题;2、极片带在极耳裁切过程中产生的片状废料需要在裁切的同时导出,以免残留在极片带表面,因此需要解决极耳裁切废料的自动取出问题。
技术实现要素:5.本发明要解决的技术问题是针对上述现有技术的不足,提供一种实现了极耳自动裁切及裁切除尘及极耳裁切废料自动导出,有效地提升了极耳裁切效率及表面洁净度的极耳裁切除尘装置及其极耳裁切除尘工艺。
6.本发明采取的技术方案如下:一种极耳裁切除尘装置,包括第一箱体、第二箱体、极片入槽、极片过渡槽、除尘罩、极片出槽及极耳裁切组件,其中,上述第一箱体及第二箱体上下间隔设置,两者内部为安装空间;上述极片入槽开设在第一箱体上;上述极片过渡槽及极片出槽分别开设在第二箱体上,且极片过渡槽位于第一箱体与第二箱体连接部位,极片出槽位于第二箱体与第一箱体未连接部位;上述除尘罩设置于第一箱体与第二箱体连接处,且贯通第一箱体与第二箱体的内部空间;上述极耳裁切组件设置在第一箱体内,极耳裁切组件包括间隔设置的极耳裁切平台部件及极耳裁切部件。
7.优选的,所述极耳裁切部件包括极耳裁切直线模组及极耳裁切激光器,其中,上述极耳裁切直线模组水平设置在第一箱体内;上述极耳裁切激光器设置在极耳裁切直线模组
的输出端上。
8.优选的,所述极耳裁切平台部件包括极耳裁切承载部件,极耳裁切承载部件包括极耳承载直线模组、极耳承载座、极耳承载支板、平台旋转电机、旋转盘及极耳平台支板;上述极耳承载直线模组水平设置在第一箱体内;上述极耳承载座连接在极耳承载直线模组上;上述极耳承载支板水平设置在极耳承载座的顶部;上述平台旋转电机竖直设置在极耳承载支板上,且输出端朝下设置;上述旋转盘水平连接在平台旋转电机的输出端上,旋转盘为圆形盘体结构,旋转盘的周沿间隔设置有至少两个安装位;上述极耳平台支板连接在上述安装位上,并竖直向下延伸。
9.优选的,所述极耳裁切平台部件还包括极耳裁切除尘部件,极耳裁切除尘部件包括极耳裁切除尘罩及导尘管,其中,上述极耳裁切除尘罩固定设置在极耳平台支板上,并向下延伸至安装位内侧,且吸尘口朝外设置;上述导尘管连接在极耳裁切除尘罩的出尘口上。
10.优选的,所述极耳裁切平台部件还包括极耳导出部件,极耳导出部件包括导出支座、推极耳部件、导极耳部件及吸极耳部件,其中,上述导出支座设置在旋转盘的下方,导出支座上开设有导出空间;上述推极耳部件设置在导出支座的侧部,且延伸至导出支座的导出空间的外侧,从外侧将裁切后的极耳推入导出空间内;上述导极耳部件设置在导出空间内,导极耳部件将推入的极耳向内侧导出;上述吸极耳部件设置在导出空间的内侧,并与导出空间连通。
11.优选的,所述推极耳部件包括导出气缸、导出滑杆及导出推块,其中,上述导出气缸设置在导出支座的内侧,且输出端朝外设置;上述导出滑杆为l状结构,导出滑杆的一端连接在导出气缸的输出端上,另一端延伸至导出支座的导出空间的外侧;上述导出推块连接在导出滑杆的另一端,并朝导出空间延伸。
12.优选的,所述导极耳部件包括导出电机、导出轴、导出齿轮、导出轮,其中,上述导出轴包括两根,两根导出轴沿平行间隔地设置在导出空间内,并与导出空间的内侧壁可转动地连接,导出轴的一端穿过导出空间延伸至导出支座的侧部;上述导出齿轮包括两个,两个导出齿轮分别套设在两根导出轴的一端端部,且两个导出齿轮相互啮合连接;上述导出电机设置在导出支座的侧部,且输出端与一根导出轴连接;上述导出轮包括两个,两个导出轮分别套设固定在两根导出轴上,且两个导出轮上下对应设置,两者之间留有间隙空间。
13.优选的,所述吸极耳部件包括极耳导出罩及极耳导出管,其中,上述极耳导出罩设置于导出支座的内侧,且吸口与导出空间连通;上述极耳导出管连接于极耳导出罩的内侧的出料口上。
14.优选的,所述极耳裁切平台部件还包括平台吸尘罩及料带吸尘罩,其中,上述平台吸尘罩设置于上述旋转盘的安装位的下侧,平台吸尘罩的上部设有吸尘空间,该吸尘空间的两侧开口,以便极耳平台支板进出;上述料带吸尘罩设置于极耳导出支座的下方,料带吸尘罩的吸尘开口朝外侧设置。
15.本发明的有益效果在于:本发明针对现有技术存在的缺陷和不足自主研发设计了一种实现了极耳自动裁切及裁切除尘及极耳裁切废料自动导出,有效地提升了极耳裁切效率及表面洁净度的极耳裁切除尘装置及其极耳裁切除尘工艺。本发明应用于锂离子动力电池的极片制成工艺中的极耳裁切工艺段。
16.本发明在完成自动裁切极耳的同时,还具备多级除尘功能,极大的保证了极耳裁切过程中极片带表面的洁净度。本发明整体采用上下两层分层隔离式设计,通过上下间隔设置的第一箱体和第二箱体形成独立的上下空间,极片带从第一箱体的极片入槽进入第一箱体内,在第一箱体内完成极耳裁切后,经极片过渡槽进入第二箱体,并经第二箱体上部开设的极片出槽从第二箱体内导出。同时,在第一箱体内设置有极耳裁切组件,极耳裁切组件包括左右间隔设置的极耳裁切部件和极耳平台部件,极片带从两者之间的间隙空间竖直向下穿过时,经极耳平台部件承载极片带的一侧后,经极耳裁切部件从另一侧在极片带的边沿裁切极耳槽。具体地,本发明的极耳裁切部件采用激光裁切原理,通过极耳裁切直线模组控制极耳裁切激光器运动调整裁切位置后,利用极耳裁切激光器在极片带边沿裁切连续的极耳槽。本发明的极耳平台部件整体包括极耳裁切承载部件、极耳裁切除尘部件和极耳导出部件,其中,极耳裁切承载部件以极耳承载直线模组作为动力,驱动极耳承载在及其顶部水平设置的极耳承载支板整体直线运动。特别地,本发明在极耳极耳承载支板下方可转动地连接有旋转盘,旋转盘为圆形盘体结构,其周沿均匀间隔地设置有多个安装位,安装位上竖直连接有向下延伸的极耳平台支板,旋转盘经上方的平台旋转电机驱动而带动多块极耳平台支板旋转运动,以实现轮换式更换极片带裁切过程中的承载平台,当其中一块极耳平台支板旋转至靠近极耳裁切激光器,并与极耳裁切激光器的激光发射方向垂直平面时,此极耳平台支板为工作状态,即用于承载极耳裁切过程中极片带的一侧;在极耳裁切过程中,同步的实现极耳平台支板的轮换式旋转更换,避免同一块极耳平台支板长时间承载极片带时,其表面积累的污染物二次污染极片带表面;同时旋转出工作状态的极耳平台支板经设置于旋转盘下方的平台吸尘罩内,通过平台吸尘罩内产生的真空负压将极耳平台支板表面的残留物进行吸尘清洁,为适应极耳平台支板的旋转轮换式结构,平台吸尘罩顶部的吸尘空间两侧设计为开放结构,以避免极耳平台支板进出吸尘空间时出现运动干涉。同时,本发明设计的极耳裁切除尘部件可同步完成极耳裁切过程中的实时除尘,通过在极耳平台支板的内侧设置极耳裁切除尘罩包覆极耳平台支板外沿后,利用极耳裁切除尘罩产生的真空负压将极耳裁切过程中产生的污染物同步实时的吸出,并经其内侧连接的导尘管向外导出。另外,针对极耳裁切过程中产生的片状废料,本发明在极耳平台支板下方设计了极耳导出部件,极耳导出部件通过推极耳部件、导极耳部件及吸极耳部件分别实现了废料的推入、滚动导出及真空吸出;极耳导出部件整体以上部开设有导出空间的导出支座作为承载载体,推极耳部件的导出气缸推动连接于其输出端上,并延伸至导出空间外侧的导出滑杆带动连接于其上的导出推块将极片带边沿裁切后的竖直状态的片状废料水平推入导出空间内极耳导极耳部件的两导出轮之间,通过设置于导出支座侧方的导出电机驱动导出轴旋转时,利用导出轴上套设的导出齿轮驱动上方的导出轴同步旋转,而两根导出轴同步旋转的同时带动两导出轮旋转滚动,将推入两者之间的片状废料向内侧方向推入至吸极耳部件的极耳导出罩内,通过真空负压将片状废料自动吸出。另外,为保证极片带表面洁净度,本发明在导出支座的下方还设置了料带吸尘罩,沿着导出支座侧部竖直向下拉出的极片带在经过料带吸尘罩时进一步进行表面除尘清洁。
附图说明
17.图1为本发明极耳裁切机构的立体结构示意图之一。
18.图2为本发明极耳裁切机构的立体结构示意图之二。
19.图3为本发明极耳裁切机构的立体结构示意图之三。
20.图4为本发明极耳裁切组件的立体结构示意图之一。
21.图5为本发明极耳裁切组件的立体结构示意图之二。
22.图6为本发明极耳裁切组件的立体结构示意图之三。
23.图7为本发明极耳裁切组件的立体结构示意图之四。
24.图8为本发明极耳裁切组件的立体结构示意图之五。
25.图9为本发明极耳裁切组件的立体结构示意图之六。
26.图10为图7中i处放大结构示意图。
具体实施方式
27.下面将结合附图对本发明作进一步描述:如图1至图10所示,本发明采取的技术方案如下:一种极耳裁切除尘装置,包括第一箱体、第二箱体、极片入槽、极片过渡槽、除尘罩、极片出槽及极耳裁切组件,其中,上述第一箱体及第二箱体上下间隔设置,两者内部为安装空间;上述极片入槽开设在第一箱体上;上述极片过渡槽及极片出槽分别开设在第二箱体上,且极片过渡槽位于第一箱体与第二箱体连接部位,极片出槽位于第二箱体72与第一箱体未连接部位;上述除尘罩设置于第一箱体与第二箱体连接处,且贯通第一箱体与第二箱体的内部空间;上述极耳裁切组件设置在第一箱体内,极耳裁切组件包括间隔设置的极耳裁切平台部件及极耳裁切部件。
28.所述极耳裁切部件包括极耳裁切直线模组77及极耳裁切激光器78,其中,上述极耳裁切直线模组77水平设置在第一箱体71内;上述极耳裁切激光器78设置在极耳裁切直线模组77的输出端上。
29.所述极耳裁切平台部件包括极耳裁切承载部件,极耳裁切承载部件包括极耳承载直线模组79、极耳承载座710、极耳承载支板711、平台旋转电机712、旋转盘713及极耳平台支板714;上述极耳承载直线模组79水平设置在第一箱体71内;上述极耳承载座710连接在极耳承载直线模组79上;上述极耳承载支板711水平设置在极耳承载座710的顶部;上述平台旋转电机712竖直设置在极耳承载支板711上,且输出端朝下设置;上述旋转盘713水平连接在平台旋转电机712的输出端上,旋转盘713为圆形盘体结构,旋转盘713的周沿间隔设置有至少两个安装位;上述极耳平台支板714连接在上述安装位上,并竖直向下延伸。
30.所述极耳裁切平台部件还包括极耳裁切除尘部件,极耳裁切除尘部件包括极耳裁切除尘罩715及导尘管716,其中,上述极耳裁切除尘罩715固定设置在极耳平台支板714上,并向下延伸至安装位内侧,且吸尘口朝外设置;上述导尘管716连接在极耳裁切除尘罩715的出尘口上。
31.所述极耳裁切平台部件还包括极耳导出部件,极耳导出部件包括导出支座717、推极耳部件、导极耳部件及吸极耳部件,其中,上述导出支座717设置在旋转盘713的下方,导出支座717上开设有导出空间;上述推极耳部件设置在导出支座717的侧部,且延伸至导出支座717的导出空间的外侧,从外侧将裁切后的极耳推入导出空间内;上述导极耳部件设置在导出空间内,导极耳部件将推入的极耳向内侧导出;上述吸极耳部件设置在导出空间的
内侧,并与导出空间连通。
32.所述推极耳部件包括导出气缸722、导出滑杆723及导出推块724,其中,上述导出气缸722设置在导出支座717的内侧,且输出端朝外设置;上述导出滑杆723为l状结构,导出滑杆723的一端连接在导出气缸722的输出端上,另一端延伸至导出支座717的导出空间的外侧;上述导出推块724连接在导出滑杆723的另一端,并朝导出空间延伸。
33.所述导极耳部件包括导出电机718、导出轴719、导出齿轮720、导出轮721,其中,上述导出轴719包括两根,两根导出轴719沿平行间隔地设置在导出空间内,并与导出空间的内侧壁可转动地连接,导出轴719的一端穿过导出空间延伸至导出支座717的侧部;上述导出齿轮720包括两个,两个导出齿轮720分别套设在两根导出轴719的一端端部,且两个导出齿轮720相互啮合连接;上述导出电机718设置在导出支座717的侧部,且输出端与一根导出轴719连接;上述导出轮721包括两个,两个导出轮721分别套设固定在两根导出轴719上,且两个导出轮721上下对应设置,两者之间留有间隙空间。
34.所述吸极耳部件包括极耳导出罩725及极耳导出管726,其中,上述极耳导出罩725设置于导出支座717的内侧,且吸口与导出空间连通;上述极耳导出管726连接于极耳导出罩725的内侧的出料口上。
35.所述极耳裁切平台部件还包括平台吸尘罩727及料带吸尘罩728,其中,上述平台吸尘罩727设置于上述旋转盘713的安装位的下侧,平台吸尘罩727的上部设有吸尘空间,该吸尘空间的两侧开口,以便极耳平台支板714进出;上述料带吸尘罩728设置于极耳导出支座717的下方,料带吸尘罩728的吸尘开口朝外侧设置。
36.一种极耳裁切除尘装置的极耳裁切除尘工艺,包括如下工艺步骤:s1、入料:极片带经极片入槽进入第一箱体内;s2、极耳裁切:步骤s1中导出的极片带进入极耳裁切机构内,并经极耳裁切机构在极片带的一侧边沿裁切极耳槽,并进行裁切除尘及极片带除尘,裁切掉落的片料经极耳裁切机构导出回收;s3、出料:步骤s2中完成极耳裁切的极片带经过渡槽进入第二箱体内,并从第二箱体上开设的极片出槽导出。
37.所述步骤s2中极片带竖直向下进入极耳裁切机构内的极耳裁切平台部件及极耳裁切部件之间,并以竖直连接于旋转盘安装位的极耳平台支板承载极片带一侧后,经另一侧的极耳裁切激光器在极片带上进行极耳裁切,并通过旋转盘旋转实现极耳平台支板的轮换;且极耳裁切时同步进行裁切吸尘,旋转出来的极耳裁切平台支板进行吸尘清洁,极耳裁切完后的极片带在极耳裁切下方经料带吸尘罩进行表面吸尘清洁。
38.优选的,所述步骤s2中极耳裁切后形成的片状废料经推极耳部件推入至导极耳部件的两个导出轮之间,通过旋转导出轮将极耳辊入吸极耳部件内,经吸极耳部件吸出。
39.进一步,本发明设计了一种实现了极耳自动裁切及裁切除尘及极耳裁切废料自动导出,有效地提升了极耳裁切效率及表面洁净度的极耳裁切除尘装置及其极耳裁切除尘工艺。本发明应用于锂离子动力电池的极片制成工艺中的极耳裁切工艺段。
40.本发明在完成自动裁切极耳的同时,还具备多级除尘功能,极大的保证了极耳裁切过程中极片带表面的洁净度。本发明整体采用上下两层分层隔离式设计,通过上下间隔设置的第一箱体和第二箱体形成独立的上下空间,极片带从第一箱体的极片入槽进入第一
箱体内,在第一箱体内完成极耳裁切后,经极片过渡槽进入第二箱体,并经第二箱体上部开设的极片出槽从第二箱体内导出。同时,在第一箱体内设置有极耳裁切组件,极耳裁切组件包括左右间隔设置的极耳裁切部件和极耳平台部件,极片带从两者之间的间隙空间竖直向下穿过时,经极耳平台部件承载极片带的一侧后,经极耳裁切部件从另一侧在极片带的边沿裁切极耳槽。具体地,本发明的极耳裁切部件采用激光裁切原理,通过极耳裁切直线模组控制极耳裁切激光器运动调整裁切位置后,利用极耳裁切激光器在极片带边沿裁切连续的极耳槽。本发明的极耳平台部件整体包括极耳裁切承载部件、极耳裁切除尘部件和极耳导出部件,其中,极耳裁切承载部件以极耳承载直线模组作为动力,驱动极耳承载在及其顶部水平设置的极耳承载支板整体直线运动。特别地,本发明在极耳极耳承载支板下方可转动地连接有旋转盘,旋转盘为圆形盘体结构,其周沿均匀间隔地设置有多个安装位,安装位上竖直连接有向下延伸的极耳平台支板,旋转盘经上方的平台旋转电机驱动而带动多块极耳平台支板旋转运动,以实现轮换式更换极片带裁切过程中的承载平台,当其中一块极耳平台支板旋转至靠近极耳裁切激光器,并与极耳裁切激光器的激光发射方向垂直平面时,此极耳平台支板为工作状态,即用于承载极耳裁切过程中极片带的一侧;在极耳裁切过程中,同步的实现极耳平台支板的轮换式旋转更换,避免同一块极耳平台支板长时间承载极片带时,其表面积累的污染物二次污染极片带表面;同时旋转出工作状态的极耳平台支板经设置于旋转盘下方的平台吸尘罩内,通过平台吸尘罩内产生的真空负压将极耳平台支板表面的残留物进行吸尘清洁,为适应极耳平台支板的旋转轮换式结构,平台吸尘罩顶部的吸尘空间两侧设计为开放结构,以避免极耳平台支板进出吸尘空间时出现运动干涉。同时,本发明设计的极耳裁切除尘部件可同步完成极耳裁切过程中的实时除尘,通过在极耳平台支板的内侧设置极耳裁切除尘罩包覆极耳平台支板外沿后,利用极耳裁切除尘罩产生的真空负压将极耳裁切过程中产生的污染物同步实时的吸出,并经其内侧连接的导尘管向外导出。另外,针对极耳裁切过程中产生的片状废料,本发明在极耳平台支板下方设计了极耳导出部件,极耳导出部件通过推极耳部件、导极耳部件及吸极耳部件分别实现了废料的推入、滚动导出及真空吸出;极耳导出部件整体以上部开设有导出空间的导出支座作为承载载体,推极耳部件的导出气缸推动连接于其输出端上,并延伸至导出空间外侧的导出滑杆带动连接于其上的导出推块将极片带边沿裁切后的竖直状态的片状废料水平推入导出空间内极耳导极耳部件的两导出轮之间,通过设置于导出支座侧方的导出电机驱动导出轴旋转时,利用导出轴上套设的导出齿轮驱动上方的导出轴同步旋转,而两根导出轴同步旋转的同时带动两导出轮旋转滚动,将推入两者之间的片状废料向内侧方向推入至吸极耳部件的极耳导出罩内,通过真空负压将片状废料自动吸出。另外,为保证极片带表面洁净度,本发明在导出支座的下方还设置了料带吸尘罩,沿着导出支座侧部竖直向下拉出的极片带在经过料带吸尘罩时进一步进行表面除尘清洁。
41.本发明的实施例只是介绍其具体实施方式,不在于限制其保护范围。本行业的技术人员在本实施例的启发下可以作出某些修改,故凡依照本发明专利范围所做的等效变化或修饰,均属于本发明专利权利要求范围内。