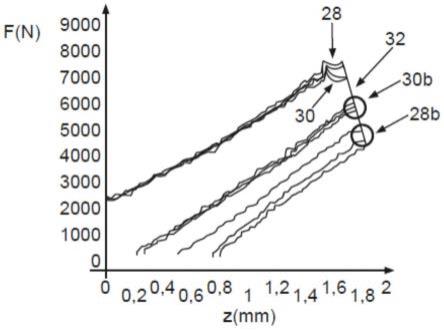
1.本发明涉及一种用于确定在装入过程期间使用的至少一个构件的质量状况的方法,其中,提供电池模块,提供具有壳体底部和分配给电池模块的接纳区域的电池壳体,其中,在接纳区域中在壳体底部上布置导热物质,将电池模块在接纳区域中放置到导热物质上并且以能预设的力压向朝壳体底部的方向指向的第一方向,使得位于电池模块和壳体底部之间的导热物质至少部分地在垂直于第一方向的第二方向上分散开。此外,本发明也涉及一种用于监控装入过程并且用于确定在装入过程中使用的构件的质量状况的控制装置。
背景技术:2.用于电动车或混合动力车的车辆电池,尤其是高压电池可如下构造:在由型材制成的框架的下侧上固定具有集成冷却通道的底板。在框架的空隙中,所谓的格架中装入单个电池模块。为了实现从电池模块到冷却底板中的热传递,在冷却底板和电池模块之间引入具有良好的导热性能的材料,所谓的缝隙填充剂。电池的装配过程设置成,能以定位的方式将缝隙填充剂涂抹到每个简单的格架中。为了缝隙填充剂将电池模块的尽可能大的面积热连结到冷却底板上,以大的力将电池模块压入被缝隙填充剂填充的格架中。此时,理想地,应在模块面积的尽可能高的浸润程度的情况下在电池模块和冷却底板之间实现尽可能小的间隙。这不仅在技术方面而且在经济性方面都是期望的,因为也由此不仅提高了车辆性能而且降低了材料成本。例如在专利文献de 10 2018 222 459 a1中描述了相似的装入过程。然而,在此可能出现,最终在这种电池模块的下侧和壳体底部之间产生的间隙宽度大小不同或者过大。也可能出现,导热物质没有理想地分布并且未充分地浸润电池模块的下侧。但是,当将这种电池模块插入电池壳体中时,至少不再能用肉眼检查,实际上是否如期望的那样进行了装入过程并且电池模块也充分好地通过导热物质连结到了冷却底板上,因为在模块和壳体底部之间的间隙处于不可见的区域中。例如,如果一个或多个电池模块没有正确地连结到冷却底板上,并且在电池制造时没有注意到,则在最坏的情况中这可能导致,最终电池在机动车运行时过热,因为不能提供充分的热导出。
3.因此期望的是,能以尽可能简单的方式评价通过这种装入过程提供的电池或者确切的说在这种装入过程期间使用的构件的质量。
4.专利文献de 37 15 077 a1描述了一种用于控制由粉末状的或颗粒状的材料压制成坯料的压制过程的方法。在此,在压制行程的进程中,根据压制距离测量压制力,并且持续地将压制力与预设的值比较。在此,根据比较结果进行控制。于是,当在利用通常的方法进行的质量检查时制成的坯料具有期望的性能时,获得压制力的期望的变化曲线。
5.与根据以上描述的方法插入壳体中的电池模块相反地,可直接在样本上进行这种质量检查,因为在所描述的压制过程中,单个构件没有相互连接,而是仅仅制造例如可在不破坏的情况下评价其的质量的单个构件,坯料。此外,与将多个构件相互连接时相比,当仅仅制造唯一的构件时,这种压制过程受到显著更低的公差要求。例如,为了在用于将电池模
块装入壳体中的装入方法中保证可重复性,例如电池模块以及同样壳体底部必须始终精确地具有相同的几何形状,并且也必须在定位和特性方面始终精确相同地提供导热物质。然而在实际中不是这种情况,使得甚至当在其变化曲线方面始终以相同的方式选择用于将电池模块压入电池壳体中的压紧力时,或者压紧力在预设的界限之内变化时,还是不能保证最终得到期望的结果。
技术实现要素:6.因此,本发明的目的在于,提供一种方法以及控制装置,其实现,以尽可能简单且可靠的方式确定至少一个在装入过程期间使用的构件的质量状况。
7.该目的通过具有根据相应的独立权利要求所述的特征的方法以及控制装置实现。从属权利要求、说明书以及附图的主题是本发明的有利的设计方案。
8.在根据本发明的用于确定在装入过程期间使用的至少一个构件的质量状况的方法中,提供电池模块,提供具有壳体底部和分配给电池模块的接纳区域的电池壳体,其中,在接纳区域中在壳体底部上布置导热物质,将电池模块在接纳区域中放置到导热物质上并且以能预设的力压向朝壳体底部的方向指向的第一方向,使得位于电池模块和壳体底部之间的导热物质至少部分地在垂直于第一方向的第二方向上分散开,作为监控参量,在装入过程的持续期间,获取在时间上的能预设的力和在装入过程期间由电池模块在时间上在第一方向上经过的位移,根据监控参量中的至少一个的至少一个特征确定所述质量状况,并且根据所确定的质量状况提供信号。
9.在此,本发明基于的认知是,以上所述的监控参量具有最终对于质量来说决定性的特征,并且因此可从中推出质量状况。通过不仅获取在时间上的能预设的力并且获取在时间上的位移,有利地实现,从多种关系及其组合中获得一个或多个特征,从这些特征中又可推出质量状况的品质。即,也就是说,不仅可获得力-位移-曲线并且通过将在力-位移-曲线上随机确定的点与一个或多个极值比较将力-位移-曲线用于确定质量状况,而且例如也可获得在时间上经过的位移的特征或者针对特定的边界条件获得的力的值或位移值的特征。然而由此也可行的是,例如从所提供的力-时间-曲线和位移-时间-曲线中获得对应的力-位移-曲线。由此,获得被评估的所考察的力变化曲线的特征不是仅仅限制在将这种力曲线与上限和下限比较上,而是优选地获得至少一个另外的特征或与此不同的特征。由此,通过分析获得的监控参量有利地实现,获得关于在这种装入过程中使用的构件的质量的结论,而不必例如在后来破坏构件。由于质量状况的评价基于可简单地实现的措施,可以非常简单且可靠的方式获得至少一个在装入过程期间使用的构件的质量状况。通过推导并分析至少一个这种特征,有利地实现,为每个装入过程单独地获得关于最终实现的质量状况的结论。
10.特别有利的是,组合地评价多个特征和曲线,因为由此可获得关于质量状况的尤其准确的结论。因此,根据本发明的另一有利的设计方案规定,获得所获取的监控参量和/或其变化曲线的多个彼此不同的特征,并且根据监控参量的多个特征确定质量状况。通过推导并分析多个这种特征,有利地实现,提高在确定质量状况时的可靠性。
11.例如,可将质量状况归类成“合格”或“不合格”。换句话说有利的是,所确定的质量状况表明,构件是合格还是不合格。这实现,以简单的方式挑选出不合格的构件,或者采取
其它应对或修正措施。根据所确定的质量状况提供的信号例如可相应地说明,构件是否合格。这种信号可通过合适的输出件输出,例如在显示屏上显示,或者如果质量状况不合格以发红光的灯的形式输出并且如果质量状况合格以发绿光的灯的形式输出。也可设想声学地输出信号的方案。
12.所描述的装入过程可为开头解释的装入过程,即,在其中,例如将具有集成的冷却通道的底板固定在由型材制成的框架的下侧上,以由此提供电池壳体。壳体底部相应地与开头所述的冷却底板对应。导热物质可为开头所述的缝隙填充剂,缝隙填充剂通常具有高的粘度并且以非常粘稠的物质或膏的形式提供。缝隙填充剂在壳体底部上被施加到对应的格架中,该格架形成或者至少提供用于容纳对应的电池模块的接纳区域,确切的说,使得在接纳区域中的整个底部面积被导热物质浸润。然而将电池模块压紧在导热物质上引起,导热物质垂直于第一方向在该面中分散开并且理想地由此几乎完全浸润模块底部。在此,可通过在位移或时间上的理论-力-变化曲线预设用于将电池模块压向壳体底部的方向的能预设的力。此时,同样可预设用于该力变化曲线的界限,不允许高于和/或低于该界限。换句话说,在进行所描述的方法时已经可假定,用于将电池模块压向壳体底部的方向的力在装入过程的持续期间在能预设的力界限之内变化。尽管如此,还可能出现的是,由壳体底部和电池模块得到的构件组件或者总地来说在装入过程期间使用的构件不能达到期望的质量状况。现在,有利地可根据对监控参量中的至少一个的至少一个特征的分析获得该质量状况。
13.在此尤其有利的是,该构件是包括电池模块、电池壳体和导热物质的组件,其中,根据利用导热物质至少部分地填充的在电池模块和壳体底部之间的间隙的最大间隙高度的特征,和/或根据通过导热物质浸润电池模块的面对壳体底部的下侧的浸润程度,确定质量状况。
14.换句话说,根据至少一个监控参量的特征,一方面可获得关于该组件的最大间隙高度的结论,而且也获得关于导热物质的浸润程度的结论。这之所以是尤其有利的,是因为这刚好是用于评价由电池模块、电池壳体和导热物质组成的构件组件的质量状况的两个重要参量。过大的间隙宽度阻碍从电池模块向壳体底部的热传递(通过该热传递通常同时也提供电池模块的冷却),由此,过大的间隙宽度损害或者不能保证充分的冷却。相同的也适用于浸润程度。例如,如果间隙足够小,但是导热物质没有充分好地分布在间隙中,使得在电池模块和壳体底部之间存在很多空气渗入和空隙,则由此也阻碍从电池模块向壳体底部的热传递,使得不再能保证充分的冷却。相应地有利的是,刚好将这两个参量用作用于评价质量状况的主要影响参量。优选地,这两个参数,即间隙宽度和浸润程度是仅有的参量,根据该参量将构件组件的质量状况分类成合格或不合格。不仅可为间隙高度而且可为浸润程度例如预设相应的界限。如果不满足该界限,则可将构件组件分类成在其质量状况方面不合格。因此,最大间隙高度不应超过预定的限值。同样,浸润程度不应低于预设的限值。又可根据监控参量中的至少一个的特征确定超过还是低于有关的限值。
15.然而尤其有利的是,通过评估力和/或位移特征,不仅仅实现,获得关于构件组件的质量状况的结论,而且例如也获得关于用于执行装入过程的设备的质量状况的结论。相应地,本发明的尤其有利的设计方案是,获得其质量状况的所述构件或第二构件是装入装置的至少一部分,并且质量状况是装入装置的所述至少一部分的磨损状态。这又基于的认
识是,例如通过评估力-时间-曲线或力-位移-曲线也可得出如下结论,即,将压紧力施加到电池模块上的机器人装配臂或龙门架或龙门架机械手具有多少机械间隙。例如可根据模块在壳体底部的方向上经过的位移通过在壳体底部的方向上施加到模块上的力的作用获得这种间隙。在此,大的间隙可推出设备或装入装置的高的磨损。这又实现,在故障之前针对性地维护装入装置,以使得由于故障引起的停机时间最少。
16.在本发明的一种尤其有利的设计方案中,作为力在时间上的变化曲线的,尤其是该变化曲线的斜率的和/或位移在时间上的变化曲线的特征和/或与位移有关的力变化曲线的特征和/或与力有关的位移(尤其是以从力的预定的力阈值开始的位移长度的形式)的变化曲线的特征,获取所述至少一个特征。由此,总共提供了多种用于确定可推出构件的质量状况的变化曲线特征的可能性。刚好在由电池模块、电池壳体和导热物质组成的构件组件方面,可通过所述变化曲线及其特征获得关于质量状况的可靠结论。在此已经发现,刚好以下特征与该构件组件的质量状况有关:一方面质量状况与在时间上的力变化曲线的斜率有关,确切的说与从在时间进程中力开始降低的时刻开始的力变化曲线的斜率有关。因此,该力变化曲线的斜率是负的。此时,在装入过程期间的力变化曲线通常如下:在此,首先以增大的压紧力将电池模块压向壳体底部的方向,其中,在该第一装入阶段期间压紧力在时间上快速增大,尤其是直至最大值,并且紧接着再次降低。此时,继续将电池模块压向壳体底部的方向,然而以逐渐降低的压紧力。如果确定的时间段结束,则结束电池模块的压紧,并且装入装置返回,也就是说压紧力降低到零,而电池模块保留在电池壳体中。但是,除了以上所述的在力降低阶段中的力的斜率之外,也可评估力和/或位移变化曲线的其它的与该构件组件的最终质量有关的特征。此外已表明,力-位移-拐点的位置与电池组件的质量状况有关。相应地有利的是,确定力-位移-拐点的位置并且将其用于评估或确定质量状况。例如,这种力-位移-拐点说明,直接在装入过程结束之前,也就是说在预设的时间段结束之后,存在怎样的力,也就是说通过装入装置作用到电池模块上的压紧力。如所描述的那样,在装入过程期间的力从达到最大力之后确定的转折点开始再次降低。在此,如此控制该降低,使得其随着电池模块在壳体底部的方向上经过的位移线性地伸延。换句话说,力随着电池模块在壳体底部的方向上的位移增加而线性降低。在预设的时间段结束之后,压紧过程结束,这意味着,电池模块经过了相应的最终-位移-长度,并且在压紧过程结束的时刻将最终-力作用到电池模块上。最终-力和最终-位移这两个参数同样与质量状况有关。相应地尤其有利的是,在装入过程的范围中为相应的电池模块获得该最终-力和最终-位移,并且在确定质量状况时进行考虑。
17.在最简单的情况中,可如此根据以上所述的监控参量及其特征确定质量状况,即,为所描述的特征设置相应的限值。例如,如果以上定义的斜率在预定的最大和最小限值之间移动,则最终可将构件组件在其质量状况方面评价成合格。相同的也适用于拐点的位置,也就是说最终-位移和/或最终-力。
18.尽管由此也不能总是正确地确定质量状况,而由此相对于现有技术至少可实现显著的改善。但是,尤其可通过由大数据方法分析所述曲线及变化曲线,提供进一步的改善,以例如也获得其它模型和关系。
19.在此,本发明的另一有利的设计方案是,通过人工智能,尤其是通过人工神经网络确定质量状况。此时,可如下非常简单地训练这种人工神经网络:首先,可进行例如已经描
述的装入过程,并且此时获取所述监控参量,并且相应地作为输入参量输送给神经网络。因此,输入参量例如描述在时间上的力变化曲线,在时间上的位移变化曲线和/或与位移有关的力变化曲线和/或与力有关的位移变化曲线。也可在此之前已经获得特征,例如上述的特征性的拐点,也就是说最终-力和/或最终-位移,以及所描述的斜率,并且作为输入参数输送到神经网络中。紧接着,可如下获得所提供的构件组件的质量状况:在缝隙填充剂或导热物质干透之后,再次拆开构件组件,也就是说拆成其单件。这伴随着构件组件的破坏。根据目前再次拆开的构件,可测量浸润程度和最大间隙高度的大小。这可相应地作为结果输送给神经网络。换句话说,与输入数据相匹配的输出数据组表示如此获得的最大间隙高度和浸润程度。可随着多次进行的装入过程一起模拟地进行该过程,以训练神经网络。借助于最终由神经网络在训练阶段之后通过在新进行的装入过程时输送所述输入参数,该输入参数可相应地作为输出数据给出最大间隙高度和浸润程度。根据给出的输出参数,可再次确定质量状况,在其中为相应的参量设定上限值和下限值,如以上已经描述的那样。如果最大间隙高度超过预设的值或者浸润程度低于预定的值,则构件组件不合格并且在所有其它情况中都合格。
20.此外,本发明的另一很大的优势在于,根据所述的力和/位移曲线也可推出装入过程的其它参数。除了装入装置的磨损状态之外,例如也可推出导热物质的粘度和暴露时间。如所描述的那样,首先将导热物质涂抹到壳体底部上,并且紧接着放置电池模块。通常,导热物质由多个在涂抹时相互混合的在涂抹之后随着时间进程硬化的组分组成。但是在单组分的导热物质的情况中,在涂抹到壳体底部上之后导热物质也随着时间进程硬化。与此伴随的是导热物质的粘度也变化。如果放置电池模块和涂抹导热物质错开很长时间,则与在涂抹导热物质之后直接将电池模块装在导热物质上时相比,导热物质例如可具有显著更大的粘滞性。相应地,在导热物质如何压紧在电池模块和壳体底部之间的方式上也有区别。由此,例如也可将导热物质涂覆到壳体底部上的涂装时刻以及压紧过程的开始用作另外的用于确定质量状况的输入参数。相反地,这种粘度性能也可从以上描述的特征中导出,例如从所述力-时间-曲线的斜率中导出。但是,导热物质的粘度不仅可受到其暴露时间(暴露时间通过以上解释的在涂抹和装上之间的时间段定义)影响,而且例如也受到环境温度确切的说进行制造的车间的车间温度影响。此时,夏天-冬天-差异可能非常显著,同样与日间时间段有关的差异也很显著。
21.相应地,本发明的另一非常有利的设计方案是,获取至少一个与监控参量不同的状态参数,根据该状态参数确定质量状况。换句话说,环境状态也可能影响最终制成的构件或构件组件的质量。由此,有利地,同样可考虑这种类型的状态参数。状态参数例如也可作为另外的输入参数输送给神经网络或其它大数据方法。由此,还能更准确地确定质量状况。
22.但是,相反地也可规定,根据对监控参量的分析和/或根据所述至少一个特征确定状态参数,例如在压紧时刻导热物质的粘度。因此,对于确定质量状况不合格的情况来说,这有利地实现了也获得这种质量状况的原因,例如由于导热物质的暴露时间过长引起过高的粘度。这又实现了,为后续的装入过程针对性地采取合适的应对措施来避免进一步的差的质量结果。
23.如所描述的那样,尤其有利的是,状态参数是在导热物质的环境中的温度,和/或状态参数是在将导热物质施加到壳体底部上和放置电池模块之间的时间段。这两者都影响
导热物质的粘度,这又影响装入过程的结果。由此,还可更准确地获得也就是说更高频地正确确定质量状况。
24.此外,知道例如也关于导热物质的粘度的结论(从中可导出所述监控参量及其变化曲线)也可用于,例如说明为什么过程例如被评价成不合格。在目前使用的方法(该方法在过程结束时例如仅仅输出合格或不合格信号)中的另一问题此外在于,不能给出进一步的关于例如为什么过程被评价成不合格的或者关于质量结果不良的可能原因的结论。其原因是,通常被评估的质量特征不允许直接推出例如必须被调整的有缺陷的过程参量。由于影响参量的数量和过程的复杂性,在结果不合格时寻找错误非常麻烦。然而,通过评估所描述的特征,也可发现例如通过导热物质过长的等待时间或者过高或过低的温度引起的可能的缺陷原因。随后,可相应地调整这种类型的不利地影响装入过程的状态参量,或者以其它方式克服这种状态参量。例如可引起注意的是,等待时间不能过长和/或进行相应的空气调整以调节温度。相反地,根据这些参量如何作用于导热物质的粘度,与例如在较低的温度时相比,例如在较高的温度时也允许更长的等待时间,或者反之亦然。此时,可利用或考虑相反地施加影响。设备的磨损状态也可能对构件的质量状况有不利影响。相应地,在评估时也可考虑设备的磨损状态作为质量状况不良的可能原因。由此,可有利地调整过程参数来实现例如更好的结果。
25.在本发明的另一有利的设计方案中规定,作为所述至少一个特征,获得在时间上的力变化曲线的频率和/或力在时间上做的功的特征。这种评估尤其允许推出装入装置的磨损状态。这种评估又可通过合适的限值方法或者大数据方法、以人工智能等的方式进行。此时,例如可将低磨损的已经维护的或者新的设备的力激励曲线与装入装置的力激励曲线比较。例如在确定的频率范围中过大的偏差或者偶然的偏差或者出现确定的不寻常的频率,暗示着磨损变大。这又实现了装入装置的及时维护。
26.此外,本发明也涉及一种用于监控装入过程并且用于确定在装入过程期间使用的至少一个构件的质量状况的控制装置,在其中,提供电池模块,提供具有壳体底部和分配给电池模块的接纳区域的电池壳体,其中,在接纳区域中在壳体底部上布置导热物质,并且电池模块在接纳区域中被放置到导热物质上并且以能预设的力压向指向壳体底部的方向的第一方向,使得位于电池模块和壳体底部之间的导热物质至少部分地在垂直于第一方向的第二方向上分散开。在此,控制装置设计成,为了监控装入过程,作为监控参量,在装入过程的持续期间,获取在时间上能预设的力和在装入过程期间由电池模块在时间上在第一方向上经过的位移,根据监控参量中的至少一个的至少一个特征确定所述质量状况,并且根据所确定的质量状况提供信号。
27.对于根据本发明的方法及其设计方案描述的优点以相同的方式适用于根据本发明的控制装置。
28.控制装置可具有数据处理装置或处理器装置,处理器装置设定成,进行根据本发明的方法的实施方式。为此,处理器装置可具有至少一个微处理器和/或至少一个微控制器和/或至少一个fpga(现场可编程逻辑门阵列)和/或至少一个dsp(数字信号处理器)。此外,处理器装置可具有程序码,程序码设定成,在通过处理器装置运行时进行根据本发明的方法的实施方式。程序码可储存在处理器装置的数据存储器中。
29.本发明也包括根据本发明的控制装置的改进方案,其具有例如已经结合根据本发
明的方法的改进方案描述的特征。出于这一原因,在此不再次描述根据本发明的控制装置的相应的改进方案。
30.本发明也包括所描述的实施方式的特征的组合。因此,本发明也包括分别具有所描述的实施方式中的多个的特征组合的实现方案,只要没有以彼此排除的方式描述这些实施方式。
附图说明
31.接下来描述本发明的实施例。其中:
32.图1示出了在根据本发明的实施例的装入过程期间具有电池壳体和电池模块的电池组件的示意性的横截面图;
33.图2示出了在装入过程期间作用到电池模块上的力的变化曲线的示意图;
34.图3示出了与在装入过程期间的与电池模块的位移有关的力变化曲线的示意图;
35.图4示出了在装入过程期间由相应的电池模块经过的位移的示意图;
36.图5示出了激励-实际-力的预设的激励-理论-力的变化曲线的,以及在装入过程期间由用于装入电池模块的装入装置所做的功的变化曲线的示意图;以及
37.图6示出了根据本发明的实施例的用于确定在装入过程期间使用的构件的质量状况的控制装置的示意图。
具体实施方式
38.以下解释的实施例是本发明的优选的实施方式。在实施例中所描述的实施方式的组件分别表示单独的、被视为彼此独立的本发明的特征,这些特征也分别彼此独立地改进本发明。因此,公开内容也应包括与所示出的实施方式的特征组合不同的组合。此外,所描述的实施方式也可通过已经描述的本发明的特征中的其它特征补充。
39.在图中,相同的附图标记分别表示功能相同的元件/部件。
40.图1示出了根据本发明的实施例的在装入过程期间的电池组件10的示意性横截面图。在此,电池组件包括电池壳体12。在该示例中,电池壳体又设计成多件式。一方面,电池壳体12具有壳体底部14。壳体底部实施成冷却底板并且在该示例中包括多个可被冷却介质穿流的冷却通道16,为清晰起见,在冷却通道中仅仅一个设有附图标记。此外,电池壳体12也包括框架18,壳体底部14在框架18上布置在下侧。在该示例中,框架18由型材制成。壳体底部14此外作为具有集成的冷却通道16的底板提供。此外,电池壳体12也可利用可选地实施成型材的分离桥接部拉伸出来,然而这在该示例中未示出。此外,组件10具有多个电池模块20,其中,在该示例中示出了三个电池模块20。在此,相应的电池模块20被插入与电池模块20对应的接纳区域22中,确切的说沿着装入方向z,在该示例中,装入方向从上向下指向并且从相应的电池模块20向着壳体底部14的方向定向。然而,在插入相应的电池模块20之前,首先将导热物质24在壳体底部14上施加到相应的接纳区域22中。紧接着,将电池模块20插入对应的接纳区域22中并且被压紧力f压向向着壳体底部14的方向的第一方向z,使得位于电池模块20和壳体底部14之间的导热物质24尤其是在垂直于第一方向z的方向上分散开。在装入过程之后,相应的电池模块20可通过相应的连接部26(在该示例中螺栓连接26)与壳体12相连接,并且由此固定在壳体上。此时,此外可使用公差调节元件,其实现在z方向
上的公差补偿。接下来,导热物质24硬化。
41.导热物质24实现了从电池模块20到冷却底板14的热导出。为了优化该热导出,有利的是,在所描述的装入过程期间如此压紧导热物质24,使得尽可能地利用导热物质24浸润电池模块的整个下侧20a,并且还使得在组件10的最终状态中提供的在有关的电池模块20的下侧20a和壳体底部14之间的间隙的高度h尽可能小。在此,低的浸润度以及空气渗入以及大的间隙高度削弱了热导出的效果。由此,可根据间隙高度h以及浸润程度确定得到的组件10的质量状况。在此,也可获得用于组件10的相应的布置区域的质量状况,其中,将相应的布置区域分配给电池模块20并且例如包括有关的电池模块20、其中包括分配给电池模块20的接纳区域22所在的壳体底部14的壳体底部区段、以及布置在壳体底部区段上的导热物质24。
42.此外,在图1中示出了在装入过程的进程中在不同时刻t1、t2、t3的三个模块20。在此,t1表示最早的时刻,t2表示稍晚的时刻,并且t3表示在装入过程结束时的最终时刻。在时刻t1时,电池模块20刚好被插入对应的接纳区域22中,并且尚未接触导热物质24。在时刻t2,电池模块20已经与导热物质24接触并且已经将导热物质垂直于z方向压紧了一些。相应地,t3示出了最后的最终状态,在最终状态中,间隙高度h最小并且导热物质24最大程度地垂直于z方向被压紧。
43.然而,现在为了能够评价如此提供的电池系统是否满足对热导出的要求,也就是说在最大允许的间隙高度h和最小允许的浸润程度方面是否合格,在已安装的或装入的状态中不再能简单地进行评价。尤其是,间隙高度h以及浸润程度不是在电池组件10的最终状态中能直接在测量技术上获取的参量。目前为止,仅仅能通过在构造好的电池上的破坏性检查在其质量方面确定装入过程实际上是否合格。在此,评估浸润程度和间隙高度,并且根据需求匹配过程参数。此外可行的是,以此为基础预测质量状况,也就是说装入过程结果是否合格,即,力-位移-曲线的变化是在确定的窗口之内。例如,如果超过确定的允许的最大力或者低于预设的最小力,则可预测到质量状况不合格。仅仅可通过以上描述的破坏性试验检查实际上是否如此。这种方式具有显著的缺点。例如,不合格的信号不能得到关于过程为什么不合格的结论。被评估的质量特征同样不能直接推出必须调整的有问题的过程参数。由于影响参量的数量以及过程的复杂性,在结果不合格时寻找错误非常复杂。在构造好电池之后几天才得到控制的结果,因为在开始评估之前,在装配之前缝隙填充剂首先必须硬化。
44.通过本发明及其实施方式,现在有利地实现,在不必破坏该组件10的情况下,获得在这种装入过程期间使用的构件,尤其是由至少一个电池模块20、壳体12和布置在壳体底部14和电池模块20之间的缝隙填充剂24组成的组件10的质量状况。为了该目的,作为监控参量,一方面获取在时间t的进程中的力f(见图2)以及在装入过程期间由模块20在时间t上在第一方向上经过的位移z,并且评估该监控参量。尤其是,从监控参量及其变化曲线以及特征性的点中可推导出其它特征,这些特征不仅与间隙高度h有关而且与浸润程度有关并且由此最终与质量状况有关。现在,接下来详细进行解释。
45.图2示出了在用于6个不同的模块组件的装入过程期间在时间t上的力f的变化曲线的示意图,在此,模块组件可分成两个不同的试验组28、30。在预定的时间(在该示例中约17秒)结束之后,压紧过程或装入过程结束。在开始时,此时施加到模块20上的力f在非常短
的时间段(约1秒长)之内非常快速地升高到其最大值上。在紧接着的过渡阶段之后,力f开始相应地在时间t的进程中连续降低。在此,在图2中分别示意性地又示出了用于相应的试验组28、30的降低的力部分的斜率28a、30a。此时已证实了,最终的质量状况以及尤其是最终的间隙高度h和浸润程度与该斜率28a、30a有关。在此,不太陡的斜率,例如在该示例中第一试验组30的斜率30a证实为更有利,并且给出更好的结果。相应地,在时间t上的力变化曲线的这种斜率28a、30a是可用于确定质量状况的特征。在最简单的情况中,可将这种获得的斜率与限值比较,或者也与两个限值,上限值和下限值比较,并且在超过或低于这些限值中的一个时,可将质量状况分类成不合格,并且否则的话分类成合格。然而尤其有利的是,为了确定质量状况,使用大数据方法,例如人工智能,例如人工神经网络。可通过所述曲线和以下还将描述的曲线以及相应的、可从该曲线中导出的特征、拐点和其它特性作为输入数据进行训练。作为有关联的输出数据,可通过破坏在其相应的间隙高度h和浸润程度方面检查相应的模块组件10,并且将相应获得的值用作训练数据。由此,最终可实现,根据作为输入数据的所描述的输入数据和以下将描述的特征,获得关于这种组件10的最终质量状况的非常普遍正确的结论。
46.图3示出了用于两个试验组28、30的力f的另一图示,现在与经过的以毫米为单位的位移z有关。如在此可看出的那样,在装入过程开始时力再次随着经过的位移距离z的增加而增加。在力f开始连续降低的时刻(例如已经针对图2进行了描述),力f根据位移z线性降低。在图3中,以32表示该线性范围。在此,力f一直降低,直至装入过程结束。当预设的时间段结束时是这种情况,如已经所述的那样,在该示例中预设的时间段为约16至17秒。在图3中,以29b和30b示出了该结束点并且结束点与从属的试验组28、30对应。在结束点(其一方面定义最终力并且另一方面定义最终位移)上,进行装入装置的位移反转。装入装置返回其初始位置中,而模块20保留在接纳区域22中。相应地,随着位移距离z减小并且压紧力f的减小到零,进行返回行程。从该线性的部分32以及对应的结束区域28b、30b中,也可再次得到关于最终的质量状况的结论。相应地,点28b、30b刚好是适合用于确定质量状况的输入参量。如同样可根据图3得到的并且在图4中还将详细说明的是,第一试验组28的电池模块20在该线性的区域32中经过比第二试验组30显著更长的位移距离δz。在此,图4示出了相应的由模块20经过的位移距离δz,一组用于第一实验组28并且一组用于第二实验组30。在此,经过的位移距离δz涉及装入过程的已定义的开始时刻和/或从这样的开始时刻开始,即,从该时刻开始超过能预设的力阈值,例如3000牛顿。在此,本发明此外基于的认识是,刚好从力f的该力阈值开始还经过的位移距离δz与得到的质量状况有关。相应地,在此也可再次设置最小限值和最大限值,为了得到的组件在其质量状况方面分类成合格,位移距离δz必须位于这两个限值之内。在此,同样再次可设想的是,将位移距离δz作为输入参数输送给学习的方法,以确定质量状况。因此,最终,尤其有利的是,根据由相应的电池模块20经过的这样的位移的位移变化确定质量状况,该位移当作用到模块20上的力f超过预定的力限值时开始并且随着装入过程的结束而结束。
47.但是,根据位移距离δz,不仅可获得在装入过程之后组件10的质量状况,而且还可得到其它结论。总地来说,也可将所述特征和变化曲线用于例如确定导热物质24的粘度,缝隙填充剂填料的暴露时间或等待时间,也就是说在将导热物质24涂覆在壳体底部14上和装上模块20之间的时间段。相反地,在此也有利的是,不仅获取所描述的监控参量,而且使
用与压紧过程的力和/或位移变化曲线组合的其它信息,例如车间温度,涂装时刻和压紧过程的开始。此外,根据特征也可获得电池托盘的公差状态和/或单个格架的平整度。优选地,在开始时测量电池壳体12的几何形状,使得开始时优选地也已知单个格架的平整度。如果出于任何原因不能实现这种测量可能性,那么因此有利地通过所述变化曲线上也存在获得壳体底部14的不平度的程度的可能性。最终有利地也实现,从所描述的曲线中获得设备状态即磨损。这之所以具有尤其大的优势,是因为例如由此可进行设备也就是说装入装置(其自动地进行电池模块20的装入和压紧)的及时维护,尤其是在设备出现故障之前和/或在设备磨损在模块组件的质量状况中显著不利之前。
48.为此,例如图5示出了在装入过程期间也在电池模块20中施加的力s的示意图,力s通过曲线34表示,所属的、预设的理论曲线36,以及在装入过程期间由设备做的功w同样作为对应的曲线38示出。在此,从力m和由模块20经过的位移距离z的乘积中得到功w。如可看出的那样,得到功w的变化曲线38的确定的波动。曲线38也包含关于设备磨损的信息。由此,对功w及其对应的时间变化曲线38的评估同样可有利地用于确定设备也就是说装入装置的质量状况。为了该目的,例如通过对变化曲线38的傅里叶分析评估尤其是在变化曲线38中存在的频率。例如可将该频率与理论频率谱或用于功曲线38的理论变化曲线比较。同样,在此又可使用人工神经网络或其它大数据方法来获得用于质量状况的设备磨损(作为另一示例)。
49.图6示出了根据本发明的实施例的用于确定构件的,例如图1中的组件10的质量状况42a、42b的控制装置40的示意图。在此,控制装置40设计成,在例如以上已经描述的装入过程期间获取监控参量44,在该示例中例如力f,位移z和时间t。
50.此外,在该示例中,也附加地获取可用的信息,以下称为状态参数46。在该示例中,该信息为在装入组件10的直接的环境中的,例如在壳体或在其中进行装入过程的加工车间之内的温度t,以及导热物质24的暴露时间δt。所获取的参量和参数44、46作为输入参数输送给控制装置40。控制装置可从被输送的数据中获得其它参量,尤其是特征48。在该示例中,特征是针对图4描述的位移长度δz,在时间上的功变化曲线38中包含的频率f(如对图5解释的那样),力变化曲线的斜率28a、30a(如对图2解释的那样),结束点28b、30b以及例如从属的最终力k0(如对图3解释的那样),以及可选的其它特征。从这些变化曲线和特征中,有利地可推出在电池模块20和壳体底部14之间的最终高度h,以及通过导热物质24浸润相应的电池模块20的下侧20a的浸润程度b。因此,根据特征48,至少近似获得间隙高度h和/或浸润程度b。紧接着,可将得到的参数,也就是说间隙高度h和浸润程度b与预设的限值比较,并且根据比较的结果将有关的模块-壳体-组件分类成合格42a或不合格42b。
51.因此,可有利地通过根据力、位移和时间自动地评估压紧过程,评价各个影响参量。在此,可监控不同参数,例如材料参数,暴露时间,设备状态确切的说设备的磨损状态,电池模块和电池托盘的平整度,等等。同样,可设想通过大数据方法分析曲线,以获得其它模型和关系。
52.总地来说示例表明,可如何通过本发明提供用于电池模块的装入过程,对于该装入过程,通过评估缝隙填充剂压紧的过程参数提供质量监控。从压紧过程的力和位移变化曲线中,尤其是与其它信息例如车间温度、涂装时刻和压紧过程的开始组合地,多种方面推出缝隙填充剂填料的粘度和暴露时间,电池托盘的公差状态,单个格架的平整度和设备状
态即磨损。由此,得到的很大优势是,在过程被评估成不合格时,在拆卸并评估电池之前已经能针对性地检查并修正过程参数,并且由此可实现显著更高的相响应速度。可针对性地调整过程参数,并且由此减少工作量。在对合格过程的监控中,可省去大部分破坏试验。可在故障之前针对性地对设备进行维护以使得停机时间最少。