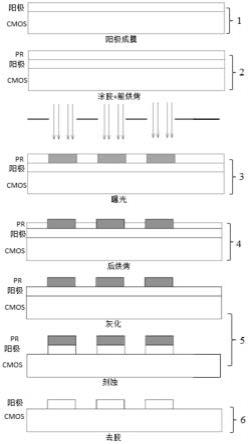
1.本发明属于硅基显示技术领域,具体涉及一种硅基微显示器件的制备方法。
背景技术:2.随着显示技术的发展,微显示的应用在蓬勃发展。因分辨率、色域、工艺可实现性考量,当下主流微显示技术为硅基微显。目前硅基微显示工艺较为复杂,工序繁多,且良率较低,故对硅基微显示器件的制备方法简化及良率提升已尤为重要及迫切。目前硅基微显示器件阳极制备工艺、像素定义层制备工艺和薄膜封装层制备工艺步骤繁多且均采用了湿法显影工艺,由于薄膜封装层的药液耐受性较差,湿法显影工艺会一定程度损伤薄膜封装层,造成后续的封装失效,影响良率。
技术实现要素:3.针对现有技术中存在的不足,本发明的目的在于提供一种硅基微显示器件的制备方法,该方法简化了阳极制备工艺、像素定义层制备工艺和薄膜封装层制备工艺,较大程度简化了工艺,节约了生产成本,且不需要进行湿法显影及硬烘,避免了湿法显影对薄膜封装层得腐蚀影响,一定程度提升了良率。
4.为实现上述目的,本发明的技术方案为:一种硅基微显示器件的制备方法,包括阳极制备工艺、像素定义层制备工艺和薄膜封装层制备工艺,所述阳极制备工艺包括:阳极成膜
→
涂胶及前烘烤
→
曝光
→
后烘烤
→
灰化
→
刻蚀
→
去胶;像素定义层制备工艺包括:像素定义层成膜
→
涂胶及前烘烤
→
曝光
→
后烘烤
→
灰化
→
刻蚀
→
去胶;薄膜封装层制备工艺包括:蒸镀
→
薄膜封装层成膜
→
涂胶及前烘烤
→
曝光
→
后烘烤
→
灰化
→
刻蚀
→
去胶;其中每个制备工艺中的灰化工艺与刻蚀工艺同腔室同步进行。
5.进一步的,所述阳极制备工艺包括:
6.步骤a.cmos硅基wafer阳极溅射成膜,得到第一基板;阳极成膜采用溅射方式成膜,膜层为ti/al/tin/ito的叠层结构,ti的厚度控制在10nm~20nm,tin厚度控制在5nm~10nm,al厚度控制在100nm~300nm,ito厚度控制在10nm~50nm;
7.步骤b.对第一基板进行涂胶及前烘烤作业,得到第二基板;对完成阳极成膜的第一基板进行光刻胶涂胶作业;
8.步骤c.对第二基板进行曝光作业,得到第三基板;对完成涂胶及前烘烤的第二基板进行曝光作业;
9.步骤d.对第三基板进行后烘烤作业,得到第四基板;对曝光后的第三基板进行后烘烤作业;
10.步骤e.对第四基板进行灰化及刻蚀作业,得到第五基板;
11.步骤f.对第五基板进行去胶作业,得到第六基板;完成灰化及刻蚀工艺后,对第五基板进行湿法光刻胶剥离,去胶液采用nmp,去胶方式为浸泡+冲洗;即完成阳极制备工艺。
12.进一步的,所述像素定义层制备工艺包括:
13.步骤1.对第六基板进行像素定义层成膜作业,得到第七基板;像素定义层成膜采用pecvd方式成膜,膜层选择sin;sin的厚度控制在150nm~200nm;
14.步骤2.对第七基板进行涂胶及前烘烤作业,得到第八基板;对完成像素定义层成膜的第七基板进行光刻胶涂胶作业;
15.步骤3.对第八基板进行曝光作业,得到第九基板;对完成涂胶及前烘烤的第八基板进行曝光作业;
16.步骤4.对第九基板进行后烘烤作业,得到第十基板;对曝光后的第九基板进行后烘烤作业;
17.步骤5.对第十基板进行灰化及刻蚀作业,得到第十一基板;
18.步骤6.对第十一基板进行去胶作业,得到第十二基板;完成灰化及刻蚀工艺后,对第十一基板进行湿法光刻胶剥离,去胶液采用nmp,去胶方式为浸泡+冲洗;即完成像素定义层制备工艺。
19.进一步的,所述阳极制备工艺的步骤b中与像素定义层制备工艺的步骤2中,光刻胶选用负性光刻胶,型号为su-8 10系列,胶厚选择1um~1.2um;前烘烤温度选择60℃
±
10℃,前烘烤时间选择10s~20s。
20.进一步的,所述阳极制备工艺的步骤和像素定义层制备工艺的步骤3中曝光机均选用nsr-i12,曝光量均为400ms
±
20ms;所述阳极制备工艺的步骤d和像素定义层制备工艺的步骤4中烘烤温度均选择150℃
±
10℃,烘烤时间均选择90s
±
10s。
21.进一步的,所述步骤e的具体操作为:对完成后烘烤后的第四基板进行灰化及干法刻蚀作业,灰化选择氧等离子方法,灰化气体选择o2,流量控制在50sccm~60sccm,source power控制在60w~70w,bias power控制在0w,压力控制在10mtorr~12mtorr,灰化时间控制在8~10s;灰化完成后,未曝光区域光刻胶完全去除,曝光区域光刻胶剩余0.78um~0.96um,此时完成图形化;对阳极干刻采用icp刻蚀模式,蚀刻气体选用bcl3、cl2、ar,bcl3的流量大小控制在60sccm~70sccm、cl2的流量大小控制在20sccm~25sccm、ar的流量大小控制在10sccm~15sccm,压力控制在10mtorr~12mtorr,source power控制在450w~480w,bias power控制在150w~160w,刻蚀时间为50s
±
2s。
22.进一步的,所述步骤5的具体操作为:对完成后烘烤后的第十基板进行灰化及干法刻蚀作业,灰化选择氧等离子方法,灰化气体选择o2,流量控制在50sccm~60sccm,source power控制在60w~70w,bias power控制在0w,压力控制在10mtorr~12mtorr,灰化时间控制在8~10s;灰化完成后,未曝光区域光刻胶完全去除,曝光区域光刻胶剩余0.78um~0.96um,此时完成图形化;对像素定义层的干刻采用icp刻蚀模式,蚀刻气体选用cf4、o2,cf4的流量大小控制在20sccm~30sccm、o2的流量大小控制在5sccm~10sccm,压力控制在5mtorr~8mtorr,source power控制在200w~2300w,bias power控制在20w~30w,刻蚀时间为90s
±
5s。
23.进一步的,所述薄膜封装层制备工艺包括:
24.s1.对第十二基板进行蒸镀作业,得到第十三基板;
25.s2.对第十三基板(13进行薄膜封装层作业,得到第十四基板;蒸镀完成后薄膜封装层成膜采用pecvd+ald方式成膜,膜层为sin/al2o3叠层结构,sin的厚度控制在500nm~1000nm,al2o3的厚度控制在20nm~50nm;
26.s3.对第十四基板进行涂胶及前烘烤作业,得到第十五基板;
27.s4.对第十五基板进行曝光作业,得到第十六基板;
28.s5.对第十六基板进行后烘烤作业,得到第十七基板;
29.s6.对第十七基板进行灰化及刻蚀作业,得到第十八基板;
30.s7.对第十八基板进行去胶作业,得到第十九基板;完成灰化及刻蚀工艺后,对第十八基板进行湿法光刻胶剥离,去胶液采用nmp,去胶方式为浸泡+冲洗;即完成薄膜封装层工艺。
31.进一步的,所述s3中对完成薄膜封装层成膜的第十四基板进行光刻胶涂胶作业,光刻胶选用负性光刻胶,型号为rfj-220系列,胶厚选择3um~3.2um;前烘烤温度选择60℃
±
10℃,时间选择10s~20s;s4中对完成涂胶及前烘烤的第十五基板进行曝光作业,曝光机选用nsr-i12,曝光量500ms
±
30ms;s5中对曝光后第十六基板进行后烘烤作业,后烘烤温度选择90℃
±
10℃,烘烤时间选择400s
±
10s。
32.进一步的,所述s6对完成后烘烤后的第十七基板进行灰化及干法刻蚀作业,灰化选择氧等离子方法,灰化气体选择o2,流量控制在50sccm~60sccm,source power控制在60w~70w,bias power控制在0w,压力控制在10mtorr~12mtorr,灰化时间控制在24~26s;灰化完成后,未曝光区域光刻胶完全去除,曝光区域光刻胶剩余2.24um~2.52um,此时完成图形化;对薄膜封装层干刻采用icp刻蚀模式,蚀刻气体选用bcl3、cl2、ar、cf4、o2,流量大小分别控制在80sccm~80sccm、15sccm~20sccm、20sccm~30sccm、40sccm~50sccm、5sccm~10sccm,压力控制在5mtorr~12mtorr,source power控制在450w~480w,bias power控制在150w~160w,刻蚀时间为240s
±
5s。
33.采用本发明技术方案的优点为:
34.本发明提供一种简化硅微显示器件阳极、像素定义层、薄膜封装层的制备方法,在定义阳极、像素定义层、薄膜封装层的图形时,在涂胶、前烘烤及曝光后,不进行湿法显影工艺,直接进行后烘烤,之后在干法刻蚀的主刻蚀前,进行灰化,定义出图形,即可完成阳极、像素定义层、薄膜封装层的图形化。此方法在硅微显示器件制备过程中,与传统工艺对比,省去了三道湿法显影工序,极大的节约了生产成本,同时,在薄膜封装层制备过程中,兼顾了薄膜封装层的药液耐受性,避免了湿法显影对薄膜封装层的腐蚀损伤,避免因薄膜封装失效造成的良率损失。
附图说明
35.下面结合附图和具体实施方式对本发明作进一步详细的说明:
36.图1为本发明阳极制备工艺示意图;
37.图2为本发明像素定义制备工艺示意图;
38.图3为本发明薄膜封装层制备工艺示意图。
39.上述图中的标记分别为:1、第一基板;2、第二基板;3、第三基板;4、第四基板;5、第五基板;6、第六基板;7、第七基板;8、第八基板;9、第九基板;10、第十基板;11、第十一基板;12、第十二基板;13、十三基板;14、第十四基板;15、第十五基板;16、第十六基板;17、第十七基板;18、第十八基板;19、第十九基板。
具体实施方式
40.在本发明中,需要理解的是,术语“长度”;“宽度”;“上”;“下”;“前”;“后”;“左”;“右”;“竖直”;“水平”;“顶”;“底”“内”;“外”;“顺时针”;“逆时针”;“轴向”;“平面方向”;“周向”等指示的方位或位置关系为基于附图所示的方位或位置关系,仅是为了便于描述本发明和简化描述,而不是指示或暗示所指的装置或元件必须具有特定的方位;以特定的方位构造和操作,因此不能理解为对本发明的限制。
41.本发明中pecvd为增强式等离子体化学气相沉积,ald为原子沉积,source power为功率,bias power为偏压功率。
42.如图1至图3所示,一种硅基微显示器件的制备方法,包括阳极制备工艺、像素定义层制备工艺和薄膜封装层制备工艺,所述阳极制备工艺包括:阳极成膜
→
涂胶及前烘烤
→
曝光
→
后烘烤
→
灰化
→
刻蚀
→
去胶;像素定义层制备工艺包括:像素定义层成膜
→
涂胶及前烘烤
→
曝光
→
后烘烤
→
灰化
→
刻蚀
→
去胶;薄膜封装层制备工艺包括:蒸镀
→
薄膜封装层成膜
→
涂胶及前烘烤
→
曝光
→
后烘烤
→
灰化
→
刻蚀
→
去胶;其中每个制备工艺中的灰化工艺与刻蚀工艺同腔室同步进行。灰化和刻蚀可同步进行,故阳极、像素定义层、薄膜封装层主工艺共19步,简化后工艺不需要进行湿法显影及硬烘,增加得灰化工艺可与刻蚀工艺同腔室同步进行;较大程度简化了工艺,节约了生产成本,且避免湿法显影对薄膜封装层得腐蚀影响,一定程度提升了良率。
43.阳极制备工艺包括:
44.步骤a.cmos硅基wafer阳极溅射成膜,得到第一基板1;阳极成膜采用溅射方式成膜,膜层为ti/al/tin/ito的叠层结构,ti的厚度控制在10nm~20nm,tin厚度控制在5nm~10nm,al厚度控制在100nm~300nm,ito厚度控制在10nm~50nm;
45.步骤b.对第一基板1进行涂胶及前烘烤作业,得到第二基板2;对完成阳极成膜的第一基板1进行光刻胶(pr)涂胶作业;光刻胶选用负性光刻胶,型号为su-8 10系列,胶厚选择1um~1.2um;此款光刻胶,在曝光区域与未曝光区域性质差别较大,未曝光区域在后烘烤时,其抗蚀剂由于溶剂的挥发,其厚度会降低30%~40%,曝光部分,由于抗蚀剂进行了光聚反应,其厚度几乎无变化。且在灰化过程中,对未曝光区域的光刻胶灰化速率为曝光区域的灰化速率的4倍~5倍,利于此性质差异进行图形化。
46.前烘烤温度选择60℃
±
10℃,时间选择10s~20s。选择此前烘烤温度与时间考量,温度过高及时间过长,易导致光刻胶溶剂挥发过多,在后烘烤时无法有效拉大曝光区域与非曝光区域膜厚差异,温度过低及时间过短,会导致光刻胶曝光特性无法固定,影响后续图形精度。
47.步骤c.对第二基板2进行曝光作业,得到第三基板3;对完成涂胶及前烘烤的第二基板2进行曝光作业,曝光机选用nsr-i12,曝光量400ms
±
20ms,曝光量决定其曝光区域光聚反应程度,如曝光量偏低,曝光区域在后烘烤及灰化时,留膜率会降低;如曝光量过大,会影响图形精度。
48.步骤d.对第三基板3进行后烘烤作业,得到第四基板4;对曝光后的第三基板3进行后烘烤作业;烘烤温度选择150℃
±
10℃,烘烤时间选择90s
±
10s,此烘烤温度及时间利于未曝光区域溶剂去除,及曝光区域驻波效应改善及光刻胶固化;在后烘烤完成后,曝光区域厚度为0.9um~1.08um,未曝光区域厚度为0.6um~0.72um。
49.步骤e.对第四基板4进行灰化及刻蚀作业,得到第五基板5;对完成后烘烤后的第四基板4进行灰化及干法刻蚀作业,灰化选择氧等离子方法,灰化气体选择o2,流量控制在50sccm~60sccm,source power(功率)控制在60w~70w,bias power(偏压功率)控制在0w,压力控制在10mtorr~12mtorr,灰化时间控制在8~10s;灰化完成后,未曝光区域光刻胶完全去除,曝光区域光刻胶剩余0.78um~0.96um,此时完成图形化;对阳极干刻采用icp刻蚀模式,蚀刻气体选用bcl3、cl2、ar,bcl3的流量大小控制在60sccm~70sccm、cl2的流量大小控制在20sccm~25sccm、ar的流量大小控制在10sccm~15sccm,压力控制在10mtorr~12mtorr,source power控制在450w~480w,bias power控制在150w~160w,刻蚀时间为50s
±
2s。
50.步骤f.对第五基板5进行去胶作业,得到第六基板6;完成灰化及刻蚀工艺后,对第五基板5进行湿法光刻胶剥离,去胶液采用nmp(甲基吡咯烷酮),去胶方式为浸泡+冲洗;即完成阳极工艺。
51.像素定义层制备工艺包括:
52.步骤1.对第六基板6进行像素定义层成膜作业,得到第七基板7;像素定义层成膜采用pecvd方式成膜,膜层选择sin;sin的厚度控制在150nm~200nm;
53.步骤2.对第七基板7进行涂胶及前烘烤作业,得到第八基板8;对完成像素定义层成膜的第七基板7进行光刻胶涂胶作业;光刻胶选用负性光刻胶,型号为su-8 10系列,胶厚选择1um~1.2um;此款光刻胶,在曝光区域与未曝光区域性质差别较大,未曝光区域在后烘烤时,其抗蚀剂由于溶剂的挥发,其厚度会降低30%~40%,曝光部分,由于抗蚀剂进行了光聚反应,其厚度几乎无变化。且在灰化过程中,对未曝光区域的光刻胶灰化速率为曝光区域的灰化速率的4倍~5倍,利于此性质差异进行图形化。
54.前烘烤温度选择60℃
±
10℃,时间选择10s~20s。选择此前烘烤温度与时间考量,温度过高及时间过长,易导致光刻胶溶剂挥发过多,在后烘烤时无法有效拉大曝光区域与非曝光区域膜厚差异,温度过低及时间过短,会导致光刻胶曝光特性无法固定,影响后续图形精度。
55.步骤3.对第八基板8进行曝光作业,得到第九基板9;对完成涂胶及前烘烤的第八基板8进行曝光作业,曝光机选用nsr-i12,曝光量400ms
±
20ms,曝光量决定其曝光区域光聚反应程度,如曝光量偏低,曝光区域在后烘烤及灰化时,留膜率会降低;如曝光量过大,会影响图形精度。
56.步骤4.对第九基板9进行后烘烤作业,得到第十基板10;对曝光后的第九基板9进行后烘烤作业,烘烤温度选择150℃
±
10℃,烘烤时间选择90s
±
10s,此烘烤温度及时间利于未曝光区域溶剂去除,及曝光区域驻波效应改善及光刻胶固化;在后烘烤完成后,曝光区域厚度为0.9um~1.08um,未曝光区域厚度为0.6um~0.72um。
57.步骤5.对第十基板10进行灰化及刻蚀作业,得到第十一基板11;对完成后烘烤后的第十基板10进行灰化及干法刻蚀作业,灰化选择氧等离子方法,灰化气体选择o2,流量控制在50sccm~60sccm,source power(功率)控制在60w~70w,bias power(偏压功率)控制在0w,压力控制在10mtorr~12mtorr,灰化时间控制在8~10s;灰化完成后,未曝光区域光刻胶完全去除,曝光区域光刻胶剩余0.78um~0.96um,此时完成图形化;对像素定义层的干刻采用icp刻蚀模式,蚀刻气体选用cf4、o2,cf4的流量大小控制在20sccm~30sccm、o2的流
量大小控制在5sccm~10sccm,压力控制在5mtorr~8mtorr,source power控制在200w~2300w,bias power控制在20w~30w,刻蚀时间为90s
±
5s。
58.步骤6.对第十一基板11进行去胶作业,得到第十二基板12;完成灰化及刻蚀工艺后,对第十一基板11进行湿法光刻胶剥离,去胶液采用nmp,去胶方式为浸泡+冲洗;即完成像素定义层工艺。
59.薄膜封装层制备工艺包括:
60.s1.对第十二基板12进行蒸镀作业,得到第十三基板13;
61.s2.对第十三基板13进行薄膜封装层作业,得到第十四基板14;蒸镀完成后薄膜封装层成膜采用pecvd+ald方式成膜,膜层为sin/al2o3叠层结构,sin的厚度控制在500nm~1000nm,al2o3的厚度控制在20nm~50nm;
62.s3.对第十四基板14进行涂胶及前烘烤作业,得到第十五基板15;对完成薄膜封装层成膜的第十四基板14进行光刻胶涂胶作业,光刻胶选用负性光刻胶,型号为rfj-220系列,胶厚选择3um~3.2um;此款光刻胶,在曝光区域与未曝光区域性质差别较大,未曝光区域在后烘烤时,其抗蚀剂由于溶剂的挥发,其厚度会降低30%~40%,曝光部分,由于抗蚀剂进行了光聚反应,其厚度几乎无变化。且在灰化过程中,对未曝光区域的光刻胶灰化速率为曝光区域的灰化速率的4倍~5倍,利于此性质差异进行图形化。
63.前烘烤温度选择60℃
±
10℃,时间选择10s~20s,选择此前烘烤温度与时间考量,温度过高及时间过长,易导致光刻胶溶剂挥发过多,在后烘烤时无法有效拉大曝光区域与非曝光区域膜厚差异,温度过低及时间过短,会导致光刻胶曝光特性无法固定,影响后续图形精度。
64.s4.对第十五基板15进行曝光作业,得到第十六基板16;对完成涂胶及前烘烤的第十五基板15进行曝光作业,曝光机选用nsr-i12,曝光量500ms
±
30ms,曝光量决定其曝光区域光聚反应程度,如曝光量偏低,曝光区域在后烘烤及灰化时,留膜率会降低;如曝光量过大,会影响图形精度。
65.s5.对第十六基板16进行后烘烤作业,得到第十七基板17;对曝光后第十六基板16进行后烘烤作业,后烘烤温度选择90℃
±
10℃,烘烤时间选择400s
±
10s;因蒸镀后温度不可高于90℃,故温度对比阳极及像素定义层调低,烘烤时间调高;此烘烤温度及时间利于未曝光区域溶剂去除,及曝光区域驻波效应改善及光刻胶固化。在后烘烤完成后,曝光区域厚度为2.7um~2.88um,未曝光区域厚度为1.8um~1.92um。
66.s6.对第十七基板17进行灰化及刻蚀作业,得到第十八基板18;对完成后烘烤后的第十七基板17进行灰化及干法刻蚀作业,灰化选择氧等离子方法,灰化气体选择o2,流量控制在50sccm~60sccm,source power控制在60w~70w,bias power控制在0w,压力控制在10mtorr~12mtorr,灰化时间控制在24~26s;灰化完成后,未曝光区域光刻胶完全去除,曝光区域光刻胶剩余2.24um~2.52um,此时完成图形化;本步骤中灰化气体选择o2,改气体可高效去除未曝光区域光刻胶;而且相关参数的设定能保证能在完全去除未曝光区域光刻胶的同时,精确控制曝光区域光刻胶厚度。
67.对薄膜封装层干刻采用icp刻蚀模式,蚀刻气体选用bcl3、cl2、ar、cf4、o2,流量大小分别控制在80sccm~80sccm、15sccm~20sccm、20sccm~30sccm、40sccm~50sccm、5sccm~10sccm,蚀刻气体的选择和流量的设定能够得到预期的刻蚀结果,使得薄膜封装层的形
貌达成;在工艺过程中,制程腔室的压力控制在5mtorr~12mtorr,source power控制在450w~480w,bias power控制在150w~160w,刻蚀时间为240s
±
5s。
68.s7.对第十八基板18进行去胶作业,得到第十九基板19;完成灰化及刻蚀工艺后,对第十八基板18进行湿法光刻胶剥离,去胶液采用nmp,去胶方式为浸泡+冲洗,实现光刻胶的剥离;即完成薄膜封装层工艺。
69.本发明提供一种简化硅微显示器件阳极、像素定义层、薄膜封装层的制备方法,在定义阳极、像素定义层、薄膜封装层的图形时,在涂胶、前烘烤及曝光后,不进行湿法显影工艺,直接进行后烘烤,之后在干法刻蚀的主刻蚀前,进行灰化,定义出图形,即可完成阳极、像素定义层、薄膜封装层的图形化。此方法在硅微显示器件制备过程中,与传统工艺对比,省去了三道湿法显影工序,极大的节约了生产成本,同时,在薄膜封装层制备过程中,兼顾了薄膜封装层的药液耐受性,避免了湿法显影对薄膜封装层的腐蚀损伤,避免因薄膜封装失效造成的良率损失。
70.以上结合附图对本发明进行了示例性描述,显然本发明具体实现并不受上述方式的限制,只要采用了本发明技术方案进行的各种非实质性的改进,或未经改进将本发明的构思和技术方案直接应用于其它场合的,均在本发明的保护范围之内。