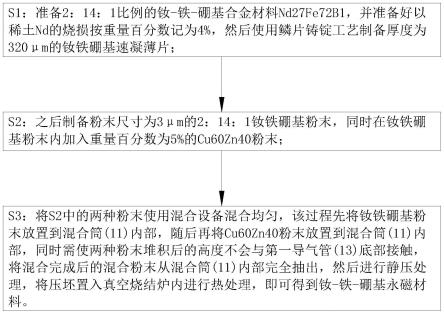
1.本发明属于永磁材料领域,具体的说是一种制备高性能钕-铁-硼基永磁材料的方法。
背景技术:2.钕-铁-硼永磁材料可与橡胶或质硬量轻的塑料等粘结材料混合,然后按照用户要求直接成型为对应形状的永磁部件。
3.公开号为cn102543343b的一项中国专利公开了铝纳米颗粒掺杂制备的高矫顽力和高耐蚀性烧结钕-铁-硼基永磁材料及制备方法,将平均粒径100-500纳米的al纳米粉末加入3-5微米钕铁硼基粉末中混合均匀,加入量为0.2-2.5%,在2.5t的磁场中取向并压制成型。
4.在钕铁硼基永磁材料制备时,需要将钕铁硼基粉末和cu80zn20粉末混合均匀,在长时间的使用观察中,发现现有的混合设备均采用搅拌叶和振动的方式进行混合,该混合方式易对钕铁硼基粉末和cu80zn20粉末造成伤害,导致混合后的钕铁硼基粉末和cu80zn20粉末颗粒出现分裂损耗的问题,因钕铁硼基粉末和cu80zn20粉末为限定好的大小进行混合加工,当钕铁硼基粉末和cu80zn20粉末的颗粒被挤碎后,无法实现有效的钕-铁-硼基永磁材料加工处理。
5.为此,本发明提供一种制备高性能钕-铁-硼基永磁材料的方法。
技术实现要素:6.为了弥补现有技术的不足,解决背景技术中所提出的至少一个技术问题。
7.本发明解决其技术问题所采用的技术方案是:本发明所述的一种制备高性能钕-铁-硼基永磁材料的方法,该高性能钕-铁-硼基永磁材料的制备方法具体包括:
8.s1:准备2:14:1比例的钕-铁-硼基合金材料nd27fe72b1,并准备好以稀土nd的烧损按重量百分数记为4%,然后使用鳞片铸锭工艺制备厚度为320μm的钕铁硼基速凝薄片;
9.s2:之后制备粉末尺寸为3μm的2:14:1钕铁硼基粉末,同时在钕铁硼基粉末内加入重量百分数为5%的cu60zn40粉末;
10.s3:将s2中的两种粉末使用混合设备混合均匀,该过程先将钕铁硼基粉末放置到混合筒内部,随后再将cu60zn40粉末放置到混合筒内部,同时需使两种粉末堆积后的高度不会与第一导气管底部接触,将混合完成后的混合粉末从混合筒内部完全抽出,然后进行静压处理,将压坯置入真空烧结炉内进行热处理,即可得到钕-铁-硼基永磁材料。
11.进一步,所述s3中提出的混合为:将钕铁硼基粉末和cu60zn40粉末放置在混合设备内部,通过该混合设备的旋转带动其内部的钕铁硼基粉末和cu60zn40粉末移动混合,同时将混合设备顶部接入高压气罐对混合设备内部吹气,使得混合设备内部的钕铁硼基粉末和cu60zn40粉末快速混合;在使用高压气罐对混合设备内部充气时,使高压气罐内部的气体间歇性的吹入到混合筒内部,使得混合设备内部的钕铁硼基粉末和cu60zn40粉末混合的
更加均匀。
12.进一步,所述s3中提出的热处理为:先以1020℃-1060℃的温度烧制1.5h-2.5h,之后再以750℃的环境热处理2h,之后再以380℃的环境进行热处理2h。
13.进一步,所述s3中提出的混合设备包括承载盘;所述承载盘顶部转动连接有混合筒;所述承载盘底部安装有电机;所述混合筒底部与电机的输出端固接;所述混合筒上转动连接有第一导气管;所述第一导气管在位于混合筒内部的中部连通有多个第二导气管;所述第一导气管中部连通有支臂;在使用时,将第一导气管顶部接入在高压气罐底部,同时使用电机带动混合筒旋转,此时混合筒会在承载盘顶部转动,同时第一导气管相对于承载盘不会转动,此时第二导气管喷出的气体会与混合筒内部不同位置处的钕铁硼基粉末和cu60zn40粉末冲击接触,使得混合筒内部的钕铁硼基粉末和cu60zn40粉末快速混合,通过使用吹气和混合筒的旋转对钕铁硼基粉末和cu60zn40粉末进行混合操作,可减少钕铁硼基粉末和cu60zn40粉末与搅拌叶轮的撞击,在保持钕铁硼基粉末和cu60zn40粉末的充分混合时,减少钕铁硼基粉末和cu60zn40粉末的颗粒破碎问题,减少损耗。
14.进一步,所述第二导气管中部连通有第三导气管;所述第三导气管端部为朝向混合筒内侧壁倾斜设置;通过在第二导气管中部设置倾斜的第三导气管对混合筒内部钕铁硼基粉末和cu60zn40粉末进行吹气,可使得混合筒内部的钕铁硼基粉末和cu60zn40粉末可更加快速的混合,同时可使得混合筒内部上下飘动的钕铁硼基粉末和cu60zn40粉末可交叉混合,提升混合的均匀度。
15.进一步,所述第二导气管端部与支臂端部之间连接有第一弹性拉绳;所述第一弹性拉绳中部连接有配重球;所述配重球位于第三导气管的端部;通过在第二导气管和支臂之间设有配重球,可在第三导气管排气时,使得配重球在混合筒内部摆动,此时摆动配重球和第一弹性拉绳可带动第一导气管和第一导气管在混合筒内部摆动,此时就可使得第二导气管摆动着喷出气体,此时第二导气管喷出的气体可进一步对混合筒内部的钕铁硼基粉末和cu60zn40粉末进行吹气混合,进一步提升混合筒内部的钕铁硼基粉末和cu60zn40粉末混合均匀度。
16.进一步,所述配重球上连接有飘带;通过在配重球上设有飘带,可在第三导气管处喷气时,飘带在配重球上摆动,此时飘带可与混合筒的内侧壁接触,使得混合筒内侧壁上粘附的钕铁硼基粉末和cu60zn40粉末被扫落,减少混合筒内侧壁上因沾附有大量的钕铁硼基粉末和cu60zn40粉末导致的浪费和混合不均匀问题。
17.进一步,所述配重球与第三导气管之间设有第二弹性拉绳;所述第二弹性拉绳一端与配重球连接,另一端与第三导气管中部内侧壁连接;通过在配重球与第三导气管之间连接有第二弹性拉绳,可使得配重球在第三导气管端口的摆动更加稳定,减少配重球脱离第三导气管端部过远的问题。
18.进一步,所述第二弹性拉绳与配重球连接处固接有弹性锥形块;通过在配重球与第二弹性拉绳接触位置处设有弹性锥形块,可在第三导气管不喷气时,配重球被第二弹性拉绳的拉扯下,堵在第三导气管的端口处,减少钕铁硼基粉末和cu60zn40粉末进入到第三导气管内部的问题,减少第三导气管被堵塞的风险。
19.进一步,所述第二弹性拉绳中部连接有多个弹性球;所述第三导气管内侧壁固接有多组喇叭状弹性瓣膜;所述弹性球直径大于喇叭状弹性瓣膜的端口直径;通过在第三导
气管内部设有喇叭状弹性瓣膜,可在弹性球被第二弹性拉绳拉扯下,弹性球间歇性的与喇叭状弹性瓣膜接触,此时会有振动产生,此时该振动会传导至配重球上,将配重球上钕铁硼基粉末和cu60zn40粉末抖落,减少因配重球上过多的钕铁硼基粉末和cu60zn40粉末沾附导致的浪费问题。
20.本发明的有益效果如下:
21.1.本发明所述的一种制备高性能钕-铁-硼基永磁材料的方法,通过使用吹气和混合筒的旋转对钕铁硼基粉末和cu60zn40粉末进行混合操作,可减少钕铁硼基粉末和cu60zn40粉末与搅拌叶轮的撞击,在保持钕铁硼基粉末和cu60zn40粉末的充分混合时,减少钕铁硼基粉末和cu60zn40粉末的颗粒破碎问题,减少损耗。
22.2.本发明所述的一种制备高性能钕-铁-硼基永磁材料的方法,通过在配重球上设有飘带,可在第三导气管处喷气时,飘带在配重球上摆动,此时飘带可与混合筒的内侧壁接触,使得混合筒内侧壁上粘附的钕铁硼基粉末和cu60zn40粉末被扫落,减少混合筒内侧壁上因沾附有大量的钕铁硼基粉末和cu60zn40粉末导致的浪费和混合不均匀问题。
附图说明
23.下面结合附图对本发明作进一步说明。
24.图1是本发明的制备方法流程图;
25.图2是本发明中混合筒的立体结构示意图;
26.图3是本发明中混合筒的剖视结构示意图;
27.图4是本发明中的导气管的结构示意图;
28.图5是本发明中第三导气管的局部结构示意图;
29.图中:1、承载盘;11、混合筒;12、电机;13、第一导气管;14、第二导气管;15、支臂;2、第三导气管;3、第一弹性拉绳;31、配重球;4、飘带;5、第二弹性拉绳;6、弹性锥形块;7、弹性球;71、喇叭状弹性瓣膜。
具体实施方式
30.为了使本发明实现的技术手段、创作特征、达成目的与功效易于明白了解,下面结合具体实施方式,进一步阐述本发明。
31.如图1所示,一种制备高性能钕-铁-硼基永磁材料的方法,该高性能钕-铁-硼基永磁材料的制备方法具体为:
32.s1:准备2:14:1比例的钕-铁-硼基合金材料nd27fe72b1,并准备好以稀土nd的烧损按重量百分数记为4%,然后使用鳞片铸锭工艺制备厚度为320μm的钕铁硼基速凝薄片;
33.s2:之后制备粉末尺寸为3μm的2:14:1钕铁硼基粉末,同时在钕铁硼基粉末内加入重量百分数为5%的cu60zn40粉末;
34.s3:将s2中的两种粉末混合均匀,之后将混合粉末静压处理,将压坯置入真空烧结炉内进行热处理,即可得到钕-铁-硼基永磁材料。
35.所述s3中提出的混合为:将钕铁硼基粉末和cu60zn40粉末放置在混合设备内部,通过该混合设备的旋转带动其内部的钕铁硼基粉末和cu60zn40粉末移动混合,同时将混合设备顶部接入高压气罐对混合设备内部吹气,使得混合设备内部的钕铁硼基粉末和
cu60zn40粉末快速混合;在使用高压气罐对混合设备内部充气时,使高压气罐内部的气体间歇性的吹入到混合筒11内部,使得混合设备内部的钕铁硼基粉末和cu60zn40粉末混合的更加均匀。
36.所述s3中提出的热处理为:先以1020℃-1060℃的温度烧制1.5h-2.5h,之后再以750℃的环境热处理2h,之后再以380℃的环境进行热处理2h。
37.实施例一
38.如图2至图4所示,本发明实施例所述的一种制备高性能钕-铁-硼基永磁材料的方法,所述s3中提出的混合设备包括承载盘1;所述承载盘1顶部转动连接有混合筒11;所述承载盘1底部安装有电机12;所述混合筒11底部与电机12的输出端固接;所述混合筒11上转动连接有第一导气管13;所述第一导气管13在位于混合筒11内部的中部连通有多个第二导气管14;所述第一导气管13中部连通有支臂15;在使用时,将第一导气管13顶部接入在高压气罐底部,同时使用电机12带动混合筒11旋转,此时混合筒11会在承载盘1顶部转动,同时第一导气管13相对于承载盘1不会转动,此时第二导气管14喷出的气体会与混合筒11内部不同位置处的钕铁硼基粉末和cu60zn40粉末冲击接触,使得混合筒11内部的钕铁硼基粉末和cu60zn40粉末快速混合,通过使用吹气和混合筒11的旋转对钕铁硼基粉末和cu60zn40粉末进行混合操作,可减少钕铁硼基粉末和cu60zn40粉末与搅拌叶轮的撞击,在保持钕铁硼基粉末和cu60zn40粉末的充分混合时,减少钕铁硼基粉末和cu60zn40粉末的颗粒破碎问题,减少损耗。
39.所述第二导气管14中部连通有第三导气管2;所述第三导气管2端部为朝向混合筒11内侧壁倾斜设置;通过在第二导气管14中部设置倾斜的第三导气管2对混合筒11内部钕铁硼基粉末和cu60zn40粉末进行吹气,可使得混合筒11内部的钕铁硼基粉末和cu60zn40粉末可更加快速的混合,同时可使得混合筒11内部上下飘动的钕铁硼基粉末和cu60zn40粉末可交叉混合,提升混合的均匀度。
40.所述第二导气管14端部与支臂15端部之间连接有第一弹性拉绳3;所述第一弹性拉绳3中部连接有配重球31;所述配重球31位于第三导气管2的端部;通过在第二导气管14和支臂15之间设有配重球31,可在第三导气管2排气时,使得配重球31在混合筒11内部摆动,此时摆动配重球31和第一弹性拉绳3可带动第一导气管13和第一导气管13在混合筒11内部摆动,此时就可使得第二导气管14摆动着喷出气体,此时第二导气管14喷出的气体可进一步对混合筒11内部的钕铁硼基粉末和cu60zn40粉末进行吹气混合,进一步提升混合筒11内部的钕铁硼基粉末和cu60zn40粉末混合均匀度。
41.所述配重球31上连接有飘带4;通过在配重球31上设有飘带4,可在第三导气管2处喷气时,飘带4在配重球31上摆动,此时飘带4可与混合筒11的内侧壁接触,使得混合筒11内侧壁上粘附的钕铁硼基粉末和cu60zn40粉末被扫落,减少混合筒11内侧壁上因沾附有大量的钕铁硼基粉末和cu60zn40粉末导致的浪费和混合不均匀问题。
42.实施例二
43.如图5所示,对比实施例一,其中本发明的另一种实施方式为:所述配重球31与第三导气管2之间设有第二弹性拉绳5;所述第二弹性拉绳5一端与配重球31连接,另一端与第三导气管2中部内侧壁连接;通过在配重球31与第三导气管2之间连接有第二弹性拉绳5,可使得配重球31在第三导气管2端口的摆动更加稳定,减少配重球31脱离第三导气管2端部过
远的问题。
44.所述第二弹性拉绳5与配重球31连接处固接有弹性锥形块6;通过在配重球31与第二弹性拉绳5接触位置处设有弹性锥形块6,可在第三导气管2不喷气时,配重球31被第二弹性拉绳5的拉扯下,堵在第三导气管2的端口处,减少钕铁硼基粉末和cu60zn40粉末进入到第三导气管2内部的问题,减少第三导气管2被堵塞的风险。
45.所述第二弹性拉绳5中部连接有多个弹性球7;所述第三导气管2内侧壁固接有多组喇叭状弹性瓣膜71;所述弹性球7直径大于喇叭状弹性瓣膜71的端口直径;通过在第三导气管2内部设有喇叭状弹性瓣膜71,可在弹性球7被第二弹性拉绳5拉扯下,弹性球7间歇性的与喇叭状弹性瓣膜71接触,此时会有振动产生,此时该振动会传导至配重球31上,将配重球31上钕铁硼基粉末和cu60zn40粉末抖落,减少因配重球31上过多的钕铁硼基粉末和cu60zn40粉末沾附导致的浪费问题。
46.工作时,将第一导气管13顶部接入在高压气罐底部,同时使用电机12带动混合筒11旋转,此时混合筒11会在承载盘1顶部转动,同时第一导气管13相对于承载盘1不会转动,此时第二导气管14喷出的气体会与混合筒11内部不同位置处的钕铁硼基粉末和cu60zn40粉末冲击接触,使得混合筒11内部的钕铁硼基粉末和cu60zn40粉末快速混合,通过使用吹气和混合筒11的旋转对钕铁硼基粉末和cu60zn40粉末进行混合操作,可减少钕铁硼基粉末和cu60zn40粉末与搅拌叶轮的撞击,在保持钕铁硼基粉末和cu60zn40粉末的充分混合时,减少钕铁硼基粉末和cu60zn40粉末的颗粒破碎问题,减少损耗。
47.通过在第二导气管14中部设置倾斜的第三导气管2对混合筒11内部钕铁硼基粉末和cu60zn40粉末进行吹气,可使得混合筒11内部的钕铁硼基粉末和cu60zn40粉末可更加快速的混合,同时可使得混合筒11内部上下飘动的钕铁硼基粉末和cu60zn40粉末可交叉混合,提升混合的均匀度;通过在第二导气管14和支臂15之间设有配重球31,可在第三导气管2排气时,使得配重球31在混合筒11内部摆动,此时摆动配重球31和第一弹性拉绳3可带动第一导气管13和第一导气管13在混合筒11内部摆动,此时就可使得第二导气管14摆动着喷出气体,此时第二导气管14喷出的气体可进一步对混合筒11内部的钕铁硼基粉末和cu60zn40粉末进行吹气混合,进一步提升混合筒11内部的钕铁硼基粉末和cu60zn40粉末混合均匀度;通过在配重球31上设有飘带4,可在第三导气管2处喷气时,飘带4在配重球31上摆动,此时飘带4可与混合筒11的内侧壁接触,使得混合筒11内侧壁上粘附的钕铁硼基粉末和cu60zn40粉末被扫落,减少混合筒11内侧壁上因沾附有大量的钕铁硼基粉末和cu60zn40粉末导致的浪费和混合不均匀问题。
48.通过在配重球31与第三导气管2之间连接有第二弹性拉绳5,可使得配重球31在第三导气管2端口的摆动更加稳定,减少配重球31脱离第三导气管2端部过远的问题;通过在配重球31与第二弹性拉绳5接触位置处设有弹性锥形块6,可在第三导气管2不喷气时,配重球31被第二弹性拉绳5的拉扯下,堵在第三导气管2的端口处,减少钕铁硼基粉末和cu60zn40粉末进入到第三导气管2内部的问题,减少第三导气管2被堵塞的风险。通过在第三导气管2内部设有喇叭状弹性瓣膜71,可在弹性球7被第二弹性拉绳5拉扯下,弹性球7间歇性的与喇叭状弹性瓣膜71接触,此时会有振动产生,此时该振动会传导至配重球31上,将配重球31上钕铁硼基粉末和cu60zn40粉末抖落,减少因配重球31上过多的钕铁硼基粉末和cu60zn40粉末沾附导致的浪费问题。
49.上述前、后、左、右、上、下均以说明书附图中的图1为基准,按照人物观察视角为标准,装置面对观察者的一面定义为前,观察者左侧定义为左,依次类推。
50.在本发明的描述中,需要理解的是,术语“中心”、“纵向”、“横向”、“前”、“后”、“左”、“右”、“竖直”、“水平”、“顶”、“底”“内”、“外”等指示的方位或位置关系为基于附图所示的方位或位置关系,仅是为了便于描述本发明和简化描述,而不是指示或暗示所指的装置或元件必须具有特定的方位、以特定的方位构造和操作,因此不能理解为对本发明保护范围的限制。
51.以上显示和描述了本发明的基本原理、主要特征和优点。本行业的技术人员应该了解,本发明不受上述实施例的限制,上述实施例和说明书中描述的只是说明本发明的原理,在不脱离本发明精神和范围的前提下,本发明还会有各种变化和改进,这些变化和改进都落入要求保护的本发明范围内。本发明要求保护范围由所附的权利要求书及其等效物界定。